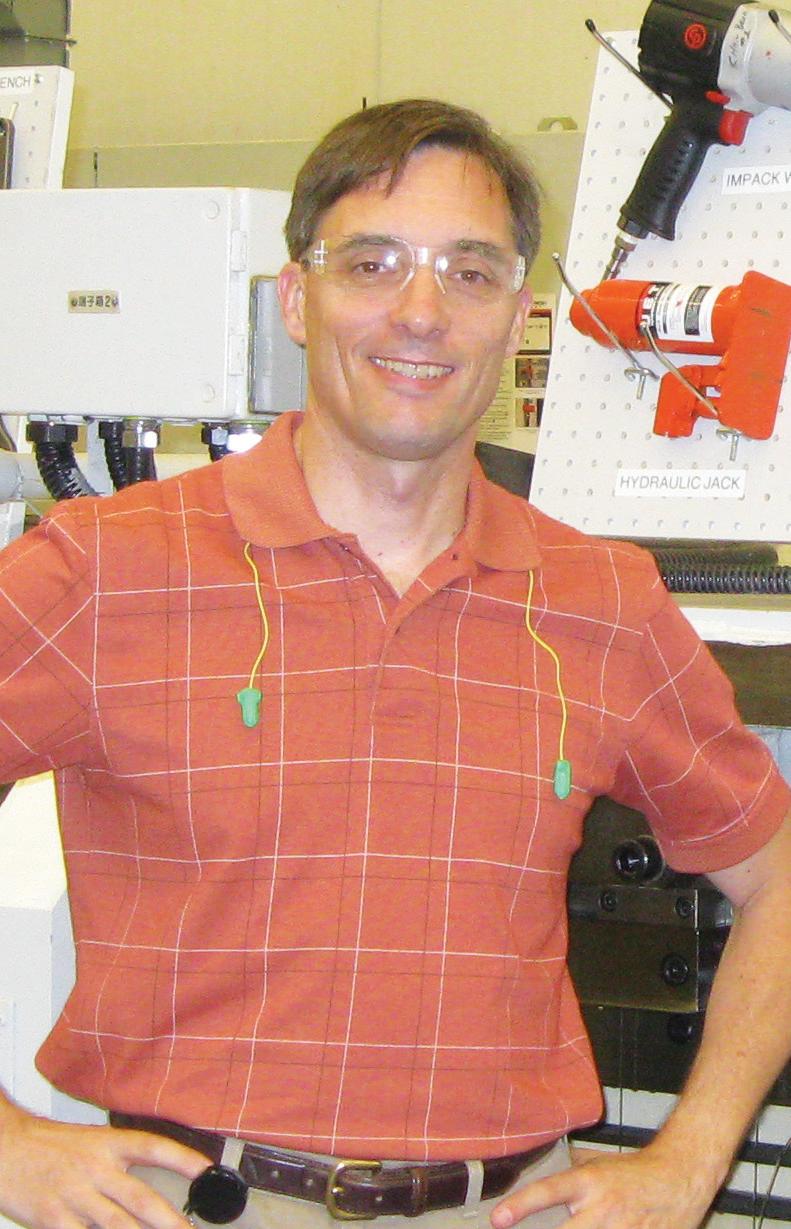
2 minute read
Business Operations
By Mike Leigh
Executive Summary:
Advertisement
Organizations are complex – but process improvement does not have to be overly so.
Send your questions or comments to Mike@ OpXSolutionsllc.com
Define standards to improve processes
I’ve spent the past 15 years helping organizations and their leaders improve their processes. The types of challenges they face, and the problems they are trying to fix are infinite. However, I’ve learned over the years that most problems can be reduced or eliminated by focusing on one simple concept – using standards.
A continuous improvement colleague of mine, Mark Rosenthal, wrote a blog post called Troubleshooting by Defining Standards, which succinctly explained what I had learned through the years. In his article, he describes how organizations can ask themselves a series of questions to help troubleshoot and improve a process. This methodology can be used for almost any process issue in an organization.
When evaluating and trying to improve a process, ask yourself these questions. You must answer “YES” before moving to the next question.
1) Is there a clear standard for the outcome? Can everyone clearly describe a “good” vs. a “bad” outcome? If not, then it’s likely the quality of your product or service will be inconsistent. If the answer is “NO,” then establish a standard for what a “good” outcome looks like that everyone understands.
2) Is there a clear standard for the method that will achieve
the standard results? Without a standard method, you can’t be certain your process will produce a good result and there will be greater variation in how employees execute the process. If the answer is “NO,” establish a clear sequence of steps to be performed.
3) Are the standard conditions required for success present?
Do the employees have the required tools, fixtures, materials, machines, environmental conditions, etc. to successfully execute the standard method? Too often
I see employees do “workarounds” to try and be successful when the organization has not provided the conditions they need. If the answer is “NO,” establish and provide the necessary conditions for success. 4)Is there variation in execution? If the answer to the previous three questions is “YES” and there are still problems, then there could be a training issue, or some other unforeseen factor that is impacting successful execution. Study the process to understand the root cause of the variation and correct it.
If you get to this point, your process is most likely working. But what if you want or need to get better? Simply reset your standard for your new expectations and start again at the top. Process improvement does not have to be overly complex. Follow these steps to clarify your challenges and focus your efforts for the results you need.