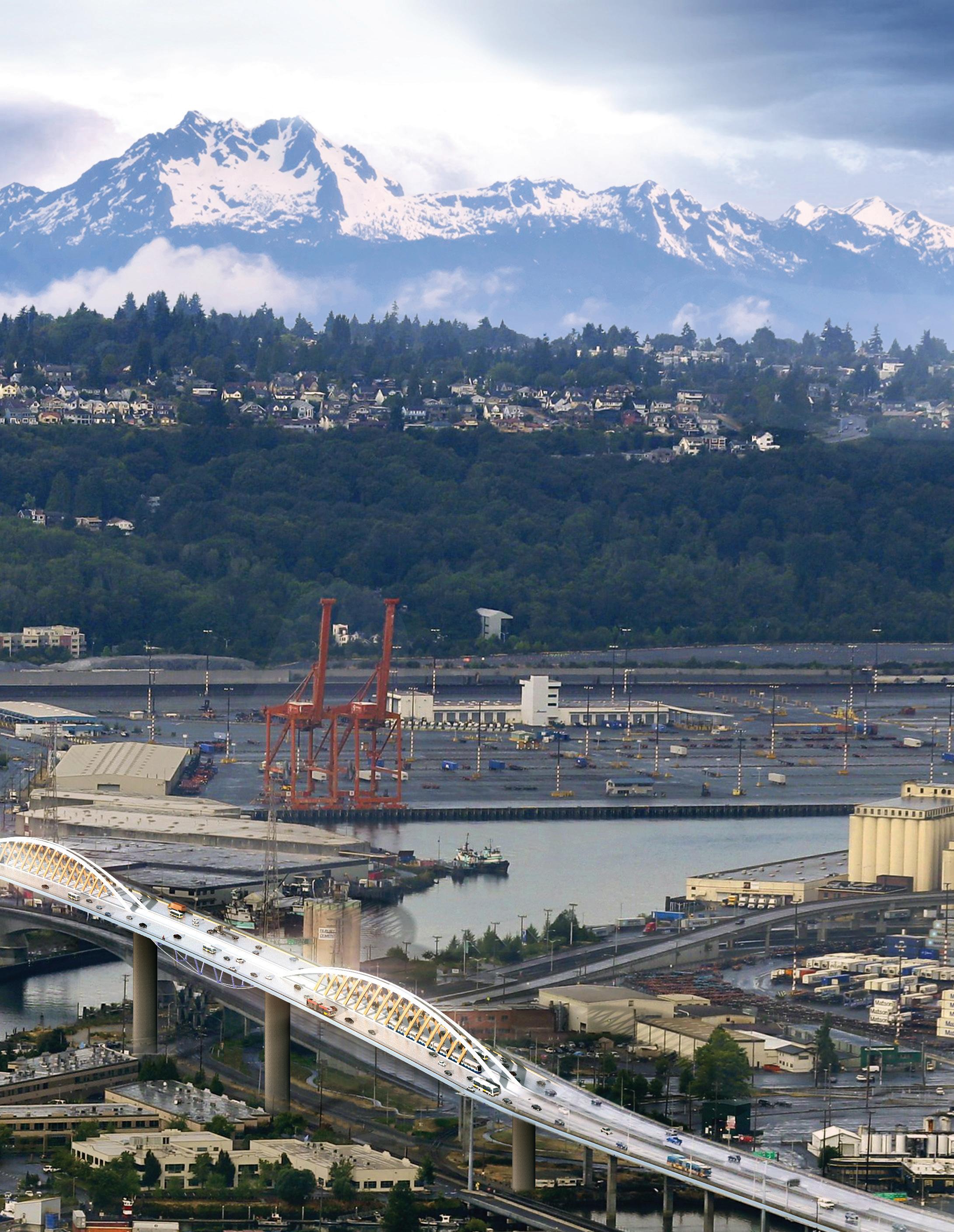
23 minute read
APPENDIX
Activity
1 NTP, MOBILIZATION & DESIGN - Same for All Options
2 NTP 3 ON SITE MOBILIZATION 4 DESIGN [Demolition] 5 DESIGN [Demolition - Approval] 6 DESIGN [New Bridge] 7 DESIGN [New Bridge - Approval]
8 DEMOLITION - Same for All Options
9 EQUIPMENT [Procurement] 10 EQUIPMENT [Design, Fabrication, Delivery, Assemblt, Test & commissioning] 11 DEMOLITION [Edge & Median Barriers] 12 DEMOLITION [Deck Overhangs] 13 DEMOLITION [Back Spans - Unbalanced Segments] 14 DEMOLITION [Main Spans - Balanced Cantilever Segments] 15 DEMOLITION [Main Piers 16 & 17 - Pier Heads] 16 DEMOLITION [Main Piers 16 & 17 - Piers] 17 DEMOLITION [Main Piers 16 & 17 - Pile Caps] 18 DEMOLITION [Main Piers 16 & 17 - Foundations] - It is assumed that existing Piles can be reused 19 DEMOLITION [Transition Piers 15 & 18 - Pier Heads] 20 DEMOLITION [Transition Piers 15 & 18 - Piers] 21 DEMOLITION [Transition Piers 15 & 18 - Pile Caps] 22 DEMOLITION [Transition Piers 15 & 18 - Foundations] - It is assumed that existing Piles can be reused
23 MASS TIMBER / STEEL OPTION - Single Deck Section 130 ft wide
24 SUBSTRUCTURES [Main Piers 16 & 17 - Foundations] - It is assumed that existing Piles can be reused 25 SUBSTRUCTURES [Main Piers 16 & 17 - Pile Caps] 26 SUBSTRUCTURES [Main Piers 16 & 17 - Piers] 27 SUBSTRUCTURES [Main Piers 16 & 17 - Pier Heads] 28 SUBSTRUCTURES [Transition Piers 15 & 18 - Foundations] - It is assumed that existing Piles can be reused 29 SUBSTRUCTURES [Transition Piers 15 & 18 - Pile Caps] 30 SUBSTRUCTURES [Transition Piers 15 & 18 - Piers] 31 SUBSTRUCTURES [Transition Piers 15 & 18 - Pier Heads] 32 DECK STEEL STRUCTURE [Fabrication & Delivery to site] 33 DECK STEEL STRUCTURE [Back Spans Assembly] 34 DECK STEEL STRUCTURE [West Back Span Delivery to Erection Site] 35 DECK STEEL STRUCTURE [West Back Span Partial Lifting & Underslung Arch Assembly] 36 DECK STEEL STRUCTURE [West Back Span Final Lifting] 37 DECK STEEL STRUCTURE [East Back Span Delivery to Erection Site] 38 DECK STEEL STRUCTURE [East Back Span Partial Lifting & Underslung Arch Assembly] 39 DECK STEEL STRUCTURE [East Back Span Final Lifting] 40 DECK STEEL STRUCTURE [Main Span Assembly] 41 DECK STEEL STRUCTURE [Main Span Delivery to Erection Site] 42 DECK STEEL STRUCTURE [Main Span Final Lifting] 43 DECK CONCRETE SLAB 44 MASS TIMBER 45 FINISHING WORKS
46 MASS TIMBER / STEEL OPTION - SUBSTANTIAL COMPLETION
47 CIP CONCRETE OPTION - Twin Deck Box Section 65 ft wide each
48 SUBSTRUCTURES [Main Piers 16 & 17 - Foundations] - It is assumed that existing Piles can be reused 49 SUBSTRUCTURES [Main Piers 16 & 17 - Pile Caps] 50 SUBSTRUCTURES [Main Piers 16 & 17 - Piers] 51 SUBSTRUCTURES [Main Piers 16 & 17 - Pier Heads] 52 SUBSTRUCTURES [Transition Piers 15 & 18 - Foundations] - It is assumed that existing Piles can be reused 53 SUBSTRUCTURES [Transition Piers 15 & 18 - Pile Caps] 54 SUBSTRUCTURES [Transition Piers 15 & 18 - Piers] 55 SUBSTRUCTURES [Transition Piers 15 & 18 - Pier Heads] 56 DECK CONCRETE STRUCTURE [E/B - Balanced Cantilever Segments over Main Pier 16 - 1U&D] 57 DECK CONCRETE STRUCTURE [E/B - Form Travellers Assembly & Commissioning] 58 DECK CONCRETE STRUCTURE [E/B - Balanced Cantilever Segments at Main Pier 16] 59 DECK CONCRETE STRUCTURE [E/B - Back span Unbalanced Segments at Transition Pier 15] 60 DECK CONCRETE STRUCTURE [E/B - Balanced Cantilever Segments at Main Pier 17 - 1U&D] 61 DECK CONCRETE STRUCTURE [E/B - Form Travellers Assembly & Commissioning] 62 DECK CONCRETE STRUCTURE [E/B - Balanced Cantilever Segments over Main Pier 17] 63 DECK CONCRETE STRUCTURE [E/B - Back span Unbalanced Segments at Transition Pier 18] 64 DECK CONCRETE STRUCTURE [W/B - Balanced Cantilever Segments over Main Pier 16 - 1U&D] 65 DECK CONCRETE STRUCTURE [W/B - Form Travellers Assembly & Commissioning] 66 DECK CONCRETE STRUCTURE [W/B - Balanced Cantilever Segments at Main Pier 16] 67 DECK CONCRETE STRUCTURE [W/B - Back span Unbalanced Segments at Transition Pier 15] 68 DECK CONCRETE STRUCTURE [W/B - Balanced Cantilever Segments at Main Pier 17 - 1U&D] 69 DECK CONCRETE STRUCTURE [W/B - Form Travellers Assembly & Commissioning] 70 DECK CONCRETE STRUCTURE [W/B - Balanced Cantilever Segments over Main Pier 17] 71 DECK CONCRETE STRUCTURE [W/B - Back span Unbalanced Segments at Transition Pier 18] 72 DECK CONCRETE STRUCTURE [E/B & W/B - Form Travellers Disassembly] 73 DECK CONCRETE STRUCTURE [Longitudinal CIP Stitch between E/B & W/B] 74 FINISHING WORKS
75 CIP CONCRETE OPTION - SUBSTANTIAL COMPLETION
76 PRECAST CONCRETE OPTION - Twin Deck Box Section 65 ft wide each
77 SUBSTRUCTURES [Main Piers 16 & 17 - Foundations] - It is assumed that existing Piles can be reused 78 SUBSTRUCTURES [Main Piers 16 & 17 - Pile Caps] 79 SUBSTRUCTURES [Main Piers 16 & 17 - Piers] 80 SUBSTRUCTURES [Main Piers 16 & 17 - Pier Heads] 81 SUBSTRUCTURES [Transition Piers 15 & 18 - Foundations] - It is assumed that existing Piles can be reused 82 SUBSTRUCTURES [Transition Piers 15 & 18 - Pile Caps]
WEST SEATTLE BRIDGE REPLACEMENT (MASS TIMBER / STEEL vs. CIP CONCRETE vs. PRECAST CONCRETE)
Start End Months M1 M2 M3 M4 M5 M6 M7 M8 M9 M10 M11 M12 M13 M14 M15 M16 M17 M18 M19 M20 M21 M22 M23 M24 M25 M26 M27 M28 M29 M30 M31 M32 M33 M34 M35 M36 M37 M38 M39 M40 M41 M42 M43 M44 M45 M46 M47 M48 M49 M50 M51 M52 M53 M54
0.00 11.00 11.00 0.00 0.00 0.00 1.00 1.00 0.00 0.00 2.00 2.00 1.00 3.00 2.00 0.00 10.00 10.00 1.00 11.00 10.00
0.00 18.00 18.00 0.00 1.00 1.00 1.00 6.00 5.00 2.00 4.00 2.00 3.00 6.00 3.00 4.00 8.00 4.00 6.00 12.00 6.00 12.00 14.00 2.00 14.00 16.00 2.00 16.00 18.00 2.00 18.00 18.00 0.00 12.00 13.00 1.00 13.00 15.00 2.00 15.00 17.00 2.00 17.00 17.00 0.00
11.00 34.00 23.00 18.00 19.00 1.00 19.00 21.00 2.00 21.00 23.00 2.00 23.00 24.00 1.00 17.00 18.00 1.00 18.00 20.00 2.00 20.00 22.00 2.00 22.00 24.00 2.00 11.00 23.00 12.00 17.00 25.00 8.00 24.00 25.00 1.00 25.00 27.00 2.00 27.00 27.00 0.00 25.00 26.00 1.00 26.00 28.00 2.00 28.00 28.00 0.00 17.00 23.00 6.00 23.00 25.00 2.00 25.00 25.00 0.00 28.00 32.00 4.00 31.00 33.00 2.00 30.00 34.00 4.00 34.00 34.00 0.00
18.00 44.00 26.00 18.00 19.00 1.00 19.00 21.00 2.00 21.00 23.00 2.00 23.00 26.00 3.00 19.00 20.00 1.00 20.00 22.00 2.00 22.00 24.00 2.00 24.00 27.00 3.00 26.00 28.00 2.00 28.00 29.00 1.00 29.00 37.00 8.00 32.00 38.00 6.00 27.00 29.00 2.00 29.00 30.00 1.00 30.00 38.00 8.00 33.00 39.00 6.00 26.00 28.00 2.00 28.00 29.00 1.00 29.00 37.00 8.00 32.00 38.00 6.00 27.00 29.00 2.00 29.00 30.00 1.00 30.00 38.00 8.00 33.00 39.00 6.00 36.00 40.00 4.00 39.00 41.00 2.00 40.00 44.00 4.00 44.00 44.00 0.00
8.00 40.00 32.00 18.00 19.00 1.00 19.00 21.00 2.00 21.00 23.00 2.00 23.00 26.00 3.00 17.00 18.00 1.00 18.00 20.00 2.00
NTP
ON SITE MOBILIZATION
DESIGN [Demolition] DESIGN [Demolition ‐Approval]
NTP, MOBILIZATION & DESIGN ‐Same for All Options
DESIGN [New Bridge] DESIGN [New Bridge ‐Approval]
DEMOLITION ‐Same for All Options
EQUIPMENT [Procurement]
EQUIPMENT [Design, Fabrication, Delivery, Assemblt, Test & commissioning] DEMOLITION [Edge & Median Barriers] DEMOLITION [Deck Overhangs] DEMOLITION [Back Spans ‐Unbalanced Segments] DEMOLITION [Main Spans ‐Balanced Cantilever Segments] DEMOLITION [Main Piers 16 & 17 ‐Pier Heads] DEMOLITION [Main Piers 16 & 17 ‐Piers] DEMOLITION [Main Piers 16 & 17 ‐Pile Caps] DEMOLITION [Main Piers 16 & 17 ‐Foundations] ‐It is assumed that existing Piles can be reused DEMOLITION [Transition Piers 15 & 18 ‐Pier Heads] DEMOLITION [Transition Piers 15 & 18 ‐Piers] DEMOLITION [Transition Piers 15 & 18 ‐Pile Caps] DEMOLITION [Transition Piers 15 & 18 ‐Foundations] ‐It is assumed that existing Piles can be reused
MASS TIMBER / STEELOPTION ‐Single Deck Section 130 ft wide
SUBSTRUCTURES [Main Piers 16 & 17 ‐Foundations] ‐It is assumed that existing Piles can be reused
SUBSTRUCTURES [Main Piers 16 & 17 ‐Pile Caps] SUBSTRUCTURES [Main Piers 16 & 17 ‐Piers] SUBSTRUCTURES [Main Piers 16 & 17 ‐Pier Heads] SUBSTRUCTURES [Transition Piers 15 & 18 ‐Foundations] ‐It is assumed that existing Piles can be reused SUBSTRUCTURES [Transition Piers 15 & 18 ‐Pile Caps] SUBSTRUCTURES [Transition Piers 15 & 18 ‐Piers] SUBSTRUCTURES [Transition Piers 15 & 18 ‐Pier Heads] DECK STEEL STRUCTURE [Fabrication & Delivery to site] DECK STEEL STRUCTURE [Back Spans Assembly] DECK STEEL STRUCTURE [West Back Span Delivery to Erection Site] DECK STEEL STRUCTURE [West Back Span Partial Lifting & Underslung Arch Assembly] DECK STEEL STRUCTURE [West Back Span Final Lifting] DECK STEEL STRUCTURE [East Back Span Delivery to Erection Site] DECK STEEL STRUCTURE [East Back Span Partial Lifting & Underslung Arch Assembly] DECK STEEL STRUCTURE [East Back Span Final Lifting] DECK STEEL STRUCTURE [Main Span Assembly] DECK STEEL STRUCTURE [Main Span Delivery to Erection Site] DECK STEEL STRUCTURE [Main Span Final Lifting]
DECK CONCRETE SLAB
MASS TIMBER
FINISHING WORKS
MASS TIMBER / STEEL OPTION ‐SUBSTANTIAL COMPLETION
CIP CONCRETE OPTION ‐Twin Deck Box Section 65 ft wide each
SUBSTRUCTURES [Main Piers 16 & 17 ‐Foundations] ‐It is assumed that existing Piles can be reused
SUBSTRUCTURES [Main Piers 16 & 17 ‐Pile Caps] SUBSTRUCTURES [Main Piers 16 & 17 ‐Piers] SUBSTRUCTURES [Main Piers 16 & 17 ‐Pier Heads] SUBSTRUCTURES [Transition Piers 15 & 18 ‐Foundations] ‐It is assumed that existing Piles can be reused SUBSTRUCTURES [Transition Piers 15 & 18 ‐Pile Caps] SUBSTRUCTURES [Transition Piers 15 & 18 ‐Piers] SUBSTRUCTURES [Transition Piers 15 & 18 ‐Pier Heads] DECK CONCRETE STRUCTURE [E/B ‐Balanced Cantilever Segments over Main Pier 16 ‐1U&D] DECK CONCRETE STRUCTURE [E/B ‐Form Travellers Assembly & Commissioning] DECK CONCRETE STRUCTURE [E/B ‐Balanced Cantilever Segments at Main Pier 16] DECK CONCRETE STRUCTURE [E/B ‐Back span Unbalanced Segments at Transition Pier 15] DECK CONCRETE STRUCTURE [E/B ‐Balanced Cantilever Segments at Main Pier 17 ‐1U&D] DECK CONCRETE STRUCTURE [E/B ‐Form Travellers Assembly & Commissioning] DECK CONCRETE STRUCTURE [E/B ‐Balanced Cantilever Segments over Main Pier 17] DECK CONCRETE STRUCTURE [E/B ‐Back span Unbalanced Segments at Transition Pier 18] DECK CONCRETE STRUCTURE [W/B ‐Balanced Cantilever Segments over Main Pier 16 ‐1U&D] DECK CONCRETE STRUCTURE [W/B ‐Form Travellers Assembly & Commissioning] DECK CONCRETE STRUCTURE [W/B ‐Balanced Cantilever Segments at Main Pier 16] DECK CONCRETE STRUCTURE [W/B ‐Back span Unbalanced Segments at Transition Pier 15] DECK CONCRETE STRUCTURE [W/B ‐Balanced Cantilever Segments at Main Pier 17 ‐1U&D] DECK CONCRETE STRUCTURE [W/B ‐Form Travellers Assembly & Commissioning] DECK CONCRETE STRUCTURE [W/B ‐Balanced Cantilever Segments over Main Pier 17] DECK CONCRETE STRUCTURE [W/B ‐Back span Unbalanced Segments at Transition Pier 18] DECK CONCRETE STRUCTURE [E/B & W/B ‐Form Travellers Disassembly] DECK CONCRETE STRUCTURE [Longitudinal CIP Stitch between E/B & W/B]
FINISHING WORKS
CIP CONCRETE OPTION ‐SUBSTANTIAL COMPLETION
SUBSTRUCTURES [Main Piers 16 & 17 ‐Foundations] ‐It is assumed that existing Piles can be reused
SUBSTRUCTURES [Main Piers 16 & 17 ‐Pile Caps] SUBSTRUCTURES [Main Piers 16 & 17 ‐Piers] SUBSTRUCTURES [Main Piers 16 & 17 ‐Pier Heads] SUBSTRUCTURES [Transition Piers 15 & 18 ‐Foundations] ‐It is assumed that existing Piles can be reused SUBSTRUCTURES [Transition Piers 15 & 18 ‐Pile Caps]
PRECAST CONCRETE OPTION ‐Twin Deck Box Section 65 ft wide each
Activity
83 SUBSTRUCTURES [Transition Piers 15 & 18 - Piers] 84 SUBSTRUCTURES [Transition Piers 15 & 18 - Pier Heads] 85 PRECAST YARD [Setting & Ready to Start] 86 PRECAST YARD [Production - About 300 Segments - 4 Short-Line Moulds] 87 DECK CONCRETE STRUCTURE [E/B - Balanced Cantilever Segments over Main Pier 16 - 1U&D] 88 DECK CONCRETE STRUCTURE [E/B - Segments 1U&D - CIP Stitches with Pier Head] 89 DECK CONCRETE STRUCTURE [E/B - Lifting Frames Assembly & Commissioning] 90 DECK CONCRETE STRUCTURE [E/B - Balanced Cantilever Segments at Main Pier 16] 91 DECK CONCRETE STRUCTURE [E/B - Back span Unbalanced Segments at Transition Pier 15] 92 DECK CONCRETE STRUCTURE [E/B - Balanced Cantilever Segments at Main Pier 17 - 1U&D] 93 DECK CONCRETE STRUCTURE [E/B - Segments 1U&D - CIP Stitches with Pier Head] 94 DECK CONCRETE STRUCTURE [E/B - Lifting Frames Assembly & Commissioning] 95 DECK CONCRETE STRUCTURE [E/B - Balanced Cantilever Segments over Main Pier 17] 96 DECK CONCRETE STRUCTURE [E/B - Back span Unbalanced Segments at Transition Pier 18] 97 DECK CONCRETE STRUCTURE [E/B - Lifting Frames Disassembly] 98 DECK CONCRETE STRUCTURE [E/B - Mid Main Span & Back Spans CIP Stitches] 99 DECK CONCRETE STRUCTURE [W/B - Balanced Cantilever Segments over Main Pier 16 - 1U&D] 100 DECK CONCRETE STRUCTURE [W/B - Segments 1U&D - CIP Stitches with Pier Head] 101 DECK CONCRETE STRUCTURE [W/B - Lifting Frames Assembly & Commissioning] 102 DECK CONCRETE STRUCTURE [W/B - Balanced Cantilever Segments at Main Pier 16] 103 DECK CONCRETE STRUCTURE [W/B - Back span Unbalanced Segments at Transition Pier 15] 104 DECK CONCRETE STRUCTURE [W/B - Balanced Cantilever Segments at Main Pier 17 - 1U&D] 105 DECK CONCRETE STRUCTURE [W/B - Segments 1U&D - CIP Stitches with Pier Head] 106 DECK CONCRETE STRUCTURE [W/B - Lifting Frames Assembly & Commissioning] 107 DECK CONCRETE STRUCTURE [W/B - Balanced Cantilever Segments over Main Pier 17] 108 DECK CONCRETE STRUCTURE [W/B - Back span Unbalanced Segments at Transition Pier 18] 109 DECK CONCRETE STRUCTURE [W/B - Lifting Frames Disassembly] 110 DECK CONCRETE STRUCTURE [W/B - Mid Main Span & Back Spans CIP Stitches] 111 DECK CONCRETE STRUCTURE [Longitudinal CIP Stitch between E/B & W/B] 112 FINISHING WORKS
113 PRECAST CONCRETE OPTION - SUBSTANTIAL COMPLETION WEST SEATTLE BRIDGE REPLACEMENT (MASS TIMBER / STEEL vs. CIP CONCRETE vs. PRECAST CONCRETE)
Start End Months M1 M2 M3 M4 M5 M6 M7 M8 M9 M10 M11 M12 M13 M14 M15 M16 M17 M18 M19 M20 M21 M22 M23 M24 M25 M26 M27 M28 M29 M30 M31 M32 M33 M34 M35 M36 M37 M38 M39 M40 M41 M42 M43 M44 M45 M46 M47 M48 M49 M50 M51 M52 M53 M54
20.00 22.00 2.00 22.00 25.00 3.00 8.00 20.00 12.00 20.00 30.00 10.00 26.00 27.00 1.00 26.75 27.00 0.25 27.00 28.00 1.00 28.00 32.00 4.00 30.00 32.00 2.00 27.00 28.00 1.00 27.75 28.00 0.25 28.00 29.00 1.00 29.00 33.00 4.00 31.00 33.00 2.00 32.50 33.50 1.00 33.00 35.00 2.00 26.00 27.00 1.00 26.75 27.00 0.25 27.00 28.00 1.00 28.00 32.00 4.00 30.00 32.00 2.00 27.00 28.00 1.00 27.75 28.00 0.25 28.00 29.00 1.00 29.00 33.00 4.00 31.00 33.00 2.00 32.50 33.50 1.00 33.00 35.00 2.00 35.00 37.00 2.00 36.00 40.00 4.00 40.00 40.00 0.00
SUBSTRUCTURES [Transition Piers 15 & 18 ‐Piers] SUBSTRUCTURES [Transition Piers 15 & 18 ‐Pier Heads]
PRECAST YARD [Setting & Ready to Start]
PRECAST YARD [Production ‐About 300 Segments ‐4 Short‐Line Moulds] DECK CONCRETE STRUCTURE [E/B ‐Balanced Cantilever Segments over Main Pier 16 ‐1U&D] DECK CONCRETE STRUCTURE [E/B ‐Segments 1U&D ‐CIP Stitches with Pier Head] DECK CONCRETE STRUCTURE [E/B ‐Lifting Frames Assembly & Commissioning] DECK CONCRETE STRUCTURE [E/B ‐Balanced Cantilever Segments at Main Pier 16] DECK CONCRETE STRUCTURE [E/B ‐Back span Unbalanced Segments at Transition Pier 15] DECK CONCRETE STRUCTURE [E/B ‐Balanced Cantilever Segments at Main Pier 17 ‐1U&D] DECK CONCRETE STRUCTURE [E/B ‐Segments 1U&D ‐CIP Stitches with Pier Head] DECK CONCRETE STRUCTURE [E/B ‐Lifting Frames Assembly & Commissioning] DECK CONCRETE STRUCTURE [E/B ‐Balanced Cantilever Segments over Main Pier 17] DECK CONCRETE STRUCTURE [E/B ‐Back span Unbalanced Segments at Transition Pier 18] DECK CONCRETE STRUCTURE [E/B ‐Lifting Frames Disassembly] DECK CONCRETE STRUCTURE [E/B ‐Mid Main Span & Back Spans CIP Stitches] DECK CONCRETE STRUCTURE [W/B ‐Balanced Cantilever Segments over Main Pier 16 ‐1U&D] DECK CONCRETE STRUCTURE [W/B ‐Segments 1U&D ‐CIP Stitches with Pier Head] DECK CONCRETE STRUCTURE [W/B ‐Lifting Frames Assembly & Commissioning] DECK CONCRETE STRUCTURE [W/B ‐Balanced Cantilever Segments at Main Pier 16] DECK CONCRETE STRUCTURE [W/B ‐Back span Unbalanced Segments at Transition Pier 15] DECK CONCRETE STRUCTURE [W/B ‐Balanced Cantilever Segments at Main Pier 17 ‐1U&D] DECK CONCRETE STRUCTURE [W/B ‐Segments 1U&D ‐CIP Stitches with Pier Head] DECK CONCRETE STRUCTURE [W/B ‐Lifting Frames Assembly & Commissioning] DECK CONCRETE STRUCTURE [W/B ‐Balanced Cantilever Segments over Main Pier 17] DECK CONCRETE STRUCTURE [W/B ‐Back span Unbalanced Segments at Transition Pier 18] DECK CONCRETE STRUCTURE [W/B ‐Lifting Frames Disassembly] DECK CONCRETE STRUCTURE [W/B ‐Mid Main Span & Back Spans CIP Stitches] DECK CONCRETE STRUCTURE [Longitudinal CIP Stitch between E/B & W/B]
FINISHING WORKS
PRECAST CONCRETE OPTION ‐SUBSTANTIAL COMPLETION
Bridge Dimensions
Total Deck Length Main Span Back Span Total Deck Width No. of carriageways
Total Deck Area
408 180 130 15.5 2
12,648
m m m m No.
m2
Summary of Quantities (Balanced Cantilever Option)
Top Slab Thickness Average Deck Depth Web Thickness Average Bottom Slab Thickness Bottom Slab Width
Average Cross-Section Area
Total Deck Cross-Section Volume Volume of Diaphragms
Total Deck Volume
250 7,750 500 825 7,500
17.81
14,535 465
15,000
mm mm mm mm mm
m2 m 3 m 3 m 3
Quantity
1.0 Concrete Volume 2.0 Prestressing Tonnage 3.0 Reinforcement Tonnage
Value
15,000 Unit
m3
750 t 2,550 t
13,912,800.00
18,333,477.69
Varies from 11 250 mm at pier to 4 250 at midspans
Varies from 1400 mm at pier to 250 at midspans `
Remark
Calculated assuming 50 kg/m 3 of concrete Calculated assuming 170 kg/m 3 of concrete
Summary of Quantities (Steel and MT Timber Arch and Underslung Deck)
No. Quantity
1.0 Steelwork Tonnage
Value
9,552 t Unit Remark
Calculated assuming 0.5 t/m2 of deck for 120 m span
Main Spam 1380 130 179400 1.31774177 Direct Cost - Superstructure Foundations Substructure Add for LRT width Job Overhead Corporate G&A & Profit
Total [Seattle, 2020]
Cost premium, relative to Baseline 1
MT-Steel Design
123,021,756 23,420,000 6,875,000 incl. 25,500,000 26,822,513
MT-Steel Design (new location)
$ 123,021,756 $ 23,420,000 $ 6,875,000 incl. $ 20,500,000 $ 26,822,513
Baseline 1 (CIP)
64,312,500 27,125,000 7,980,000 17,978,325 33,000,000 22,559,374
205,639,270 19% 200,639,270 16% 172,955,199 Baseline 2 (PC)
68,670,000 27,125,000 7,980,000 23,463,025 30,000,000 23,585,704
180,823,728 5%
Cost Estimates
150,000,000 37,500,000 38,250,000 225,750,000
382,075,000 CIP
Steel
1.692469546 timber
deck temp. works Relocate RR & Road
PC Segm Superstructure only
19,620.00 1,650,000.00 5,610,000.00 CY LB LB
21,014,125.00 4,237.76 9,677.78 1.00 1.00 LB MBF CY LS LS
19,620.00 1,650,000.00 5,610,000.00 CY LB LB 136,142.00 SF
2,500.00 5.00 1.25 49,050,000.00 8,250,000.00 7,012,500.00 64,312,500.00
174,200.00 SF
$ 4.50 $ 1,600.00 $ 1,000.00 $ 10,000,000.00 $ 2,000,000.00 $ 94,563,562.50 $ 6,780,416.00 $ 9,677,777.78 $ 10,000,000.00 $ 2,000,000.00 $ 123,021,756.28
136,142.00 SF
3,500.00 5.00 1.25 68,670,000.00 8,250,000.00 7,012,500.00 83,932,500.00
West Seattle Bridge Replacement Narrative (Lane Construction)
General Information
This assessment is relevant only to the structural unit of the main bridge spanning over the river (the “main bridge”). No consideration has been given to any improvements associated with the approach span portion of the bridge.
Our general approach when examining options for the future of the West Seattle Bridge included consideration of two fundamental types of structures. Given the limited time available to consider the various options, a scope including a broader cross-section of bridge types was not reasonably possible.
We have assumed the current West Seattle Bridge foundations and substructure columns as being inadequate to receive additional loads related to LRT deck widening and have therefore approached the project with the view that these components would be part of the replacement structure.
To establish a baseline, we initially produced a cost estimate associated with replacement of the compromised superstructure and substructure of the main bridge utilizing a cast in place concrete segmental design (Baseline 1). This would be very similar to the existing structure type, however, for an equal comparison, we matched the width of the mass timber steel bridge and included structural provisions for LRT and bicycle lanes. Some changes would be included with the replacement structure, and of course, any new structure would be fully compliant with current design standards. The general type of structure would mirror that which currently serves the local community; however, the approaches would need to be widened to accommodate LRT and bicycle lanes.
Our second cost analysis was focused on replacing the West Seattle Bridge with a reimagined mass timber and steel composite design (MT-Steel Design). As noted above, the foundations and substructure columns would be replaced. salvaged from the current structure and utilized for construction of the new span atop the existing works. From a schedule perspective, keeping the existing foundations and substructure would afford significant time savings in the overall replacement schedule. This is a key component to a fast track delivery for either of the new bridge options contemplated herein.
The bridge type developed by B+H utilizing the composite mass timber and steel arch design proves to be less economical than the concrete baseline structure. However, given the fact that many components can be pre-fabricated and positioned for installation concurrent with the performance of bridge substructure operations, significant economies in the schedule are achievable and these efficiencies serve to offset the more expensive direct cost of the mass timber and steel arch alternative design. The following narrative provides some additional information regarding the types of construction we have reviewed, and offers additional details on how some of the work may be carried out.
Removal of Existing Main Span Bridge
Demolition of a cast-in-place segmental structure is a complex undertaking and significant engineering analysis must be carried out to ascertain the safest and most stable sequence. Essentially, the bridge must be demolished in the exact reverse sequence used during construction. These types of bridges must be “de-constructed” following a specific staged plan. From our past experience, we envision the following general operation.
As a preliminary activity, to reduce the maximum required lifting capacity of the lowering equipment, edge and median barrier sections will be cut in advance. Overhang deck sections (through to the most exterior longitudinal post-tensioning tendons are encountered) will be cut in advance as well.
The existing bridge main span deconstruction would then commence with the 80 ft long out of balance deck section at each backspan. These segments will be supported by means of temporary towers and removed with the aid of a crane positioned on the approaches or at ground level.
Then, the segments of the remaining balanced cantilever deck sections will be removed simultaneously on either side of the cantilever itself. After lowering equipment has been firmly attached to the deck and segments have been secured to their spreader beams, wire cutting operations would be carried out to free these elements from the rest of the structure. Once cut free, the segments would be lowered to the ground on to lowbed trailers (in backspans) or to the river on barges (in the main span) for secondary transport to a demolition area established on site.
The first main span segment removal will include a section of deck 2 typical segments in length plus the mid-span closure segment. Only after the lowering equipment has been firmly attached to the deck, wire cutting operations would be carried out. The central section would be lowered to a barge below and staged on trailers for final transfer to a demolition area established on site.
Demolition will then proceed with removal of deck segments working back towards the main pier. We will follow the general joint layouts used in the original construction but may vary this approach in certain locations where larger elements may be handled. This approach will enable us to reduce the number of closures required in the channel.
To expedite joint preparation, separate dedicated work crews will carry out limited joint precutting activities several segments back from the leading tip of the cantilever. To further mitigate the need for channel closures, we will be utilizing four separate deconstruction teams, one situated on each side of the center channel and on each structure (Eastbound and Westbound). Segments which have been cut free (one on each cantilever on each side of the channel) will be also lowered concurrently to maximize the benefit of each
channel closure. We will continue our operations in this manner as we progress towards the main piers until the entire bridge superstructure has been safely removed.
Secondary Demolition at On-Site Facility For maximum efficiency, we would plan to establish a concrete breaking crushing operation on site to handle the larger concrete elements which have been removed from the existing structure. Maintaining the theme of environmental vigilance, our staff will look for any opportunities to recycle products that are derived from the deconstruction operations. We currently forecast that at least 30 thousand tons of recycled concrete can be utilized on site or sold for use in other regional construction and endeavors. All reinforcing and prestressing steel which is recovered from bridge demolition activities will also be sold for recycling purposes. Any materials which must be disposed of off-site will be handled through properly licensed and approved locations.
Mass Timber – Steel Design - Arch Composite
Side Spans Construction Sequence
Since the concept design for the side spans includes and under deck truss system to support the overall span, the construction of the sides spans on either side of the primary river crossing would be staged in two primary phases.
The first stage would address the assembly at ground level of the main bowstring structural steel element of the under-deck support. We have envisioned assembly of the structural steel frame without the installation of the tension cables in this first phase. Once the primary steel frame had been completely assembled within a separate supporting framework, the overall bow string frame would be raised vertically on for short towers to facilitate installation of the tension cables. Once the cables were installed, they will be stressed to their prescribed forces to provide adequate support for the total deck assembly at this stage of the construction sequence.
Then, utilizing a multi-strand heavy lift jacking system attached to the upper area of the bridge columns, the entire span will be lifted vertically into its final position at deck level. Once secured to its permanent fixation points, the jacking system will be removed, movement joints installed at connection with approaches and remaining concrete riding surface of the deck would be cast in place at this location.
The same system will be utilized for the bowstring spans on either side of the primary arched main span crossing. As pointed out earlier, with much of this pre-assembly work being permitted to take place concurrent with new foundation and pier activities, a considerable amount of time can be saved on the overall project schedule.
Main Span Construction Sequence
Again, to take advantage of schedule time savings through overlapping activities, pre-assembly of the main span would also be undertaken while new pier activity was underway. We foresee the main span steel arch, along with its side cantilevered roadway portion, being pre-assembled on the ground in a staging area specially prepared for this activity. Speed of assembly will be greatly improved, and overall safety of the workforce enhanced, as the primary assembly activities would all take place directly at ground level.
Once all pre-assembly operations have been completed and the tops of the main span support piers prepared to receive the new main span structure, the preassembled span would be loaded onto a specially outfitted barge utilizing multi axle self-propelled modular transporters (SPMT’s). Once the main span structure was properly positioned and stabilized on the barge, the SPMT’s would be driven off and returned to the staging area.
Following receipt of approval for any necessary waterway channel closures, the barge carrying the preassembled main span would be floated into position in between the existing bridge columns. A multi-strand heavy lift jacking system, similar to that used to raise the side span preassemblies, would then vertically hoist the main span arch and cantilevered roadway structure vertically into its final service position. Once permanently positioned onto its support bearings and the lifting system removed, work will continue in place at deck level to pour the concrete riding surface for the structure.
Baseline 1, Cast-in-Place Segmental Bridge
Another alternative we have investigated for the West Seattle Bridge replacement is to cast the segments in their final position in the structure with the same methodology originally used. This would essentially be the bridge type that is currently in place on site and is what we have considered as the “base line structure” in our analysis.
Cast-in-place construction proves to be very advantageous when large, very heavy segments are encountered. Instead of handling the segments in a completely precast state, with cast-in-place methodology, only materials have to be transported during construction, thus influencing the type and size of required equipment. The commonly used method for casting segments in place is with the use of a traveling form system, known as form travelers. Form travelers are moveable forms supported by steel cantilever trusses attached to previously completed segments. The usual production rate for a form traveler is one segment every week.
Balanced cantilever erection will probably be the most commonly used method for constructing segmental bridges. It solves problems such as environmental or existing traffic constraints. Conversely, the linear nature of cast-in-place construction yield slower overall production rates. For a project requiring fast-track construction, this bridge type is less preferable. When balanced cantilever cast-in-place construction is used, a minimum of two form travelers is required. The segment production rate for form travelers is usually one segment every week per traveler. Therefore, to approach more reasonable production capacities, a total of eight form travelers would be required.
B+H | SMEC | RBG | LANE | DCI
MATTHIAS OLT
Design Director, Architecture, USA B+H Architects matthias.olt@bhadvancestrategy.com 206.679.0922