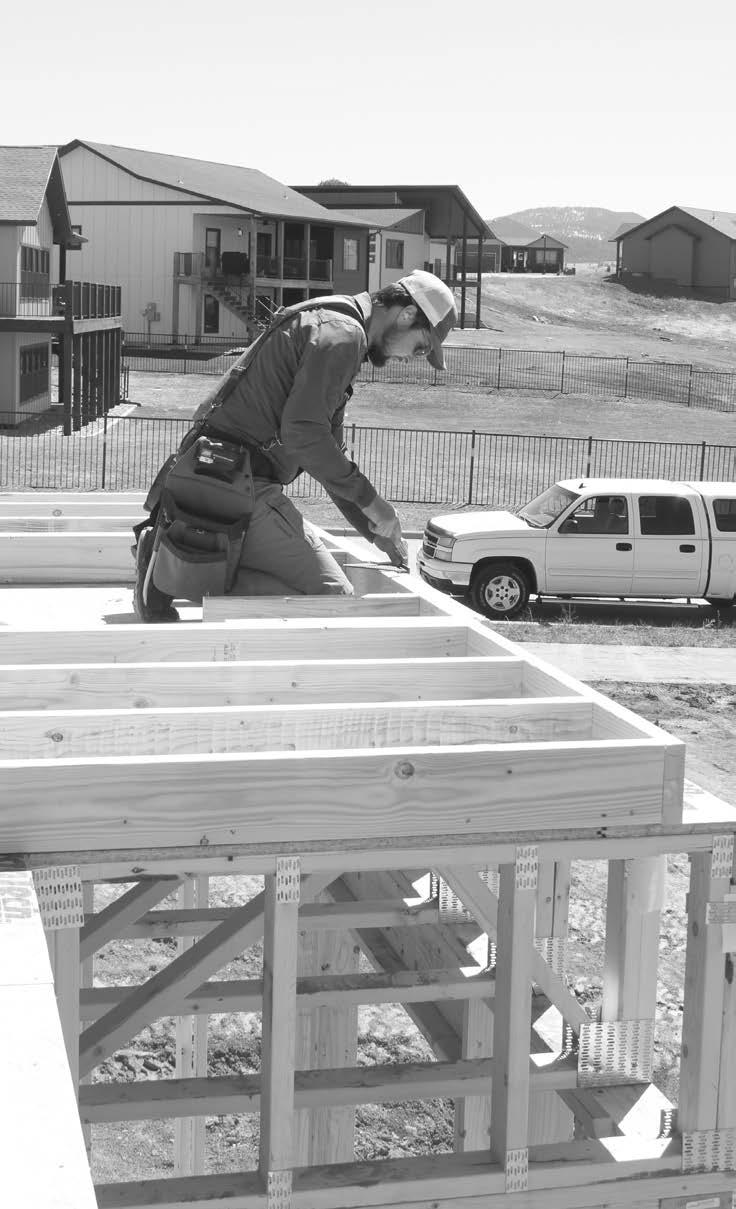
4 minute read
Construction costs, worker shortages major factors in tight housing market
B y t om l aW rence Special to The Pioneer
There are thousands of parts needed to build a home, and many of them will cost more this year than last.
Advertisement
Duane Bickett of Sioux Falls, who serves as the South Dakota Home Builders state representative, said there has been some good news. Lumber prices jumped dramatically in 2020-21 as lumber mills slowed or even ceased production during the COVID-19 pandemic.
“Well, it’s dropped, the lumber futures have dropped considerably from what they were probably in mid- to late 2021, probably when they hit their peak, and kind of declined a little bit through last year,” Bickett said.
But that is a double-edged sword, he said. As consumption declines, manufacturers reduce their inventory and that keeps prices from dropping a lot.
“It keeps it high because then they are only supplying what the demand is going to buy,” he said.
Bickett, who is building homes in Hill City right now, said with the price of steel rising, some equipment purchases were delayed. He hopes to see reports of more purchases of trailers and dump trucks. That really slowed down when the cost of raw materials spiked, Bickett said.
Construction
age,” he said, and they are looking to build or buy a house. All these factors create increased demand for available houses, he said.
Rettig said for years, there always were 50-75 homes on the market in Yankton. Now, there are fewer than 10.
“People have been saying, ‘The bubble’s going to burst, the bubble’s going to burst, the bubble’s going to burst,’” he said. “And it’s not bursting.”
I think we’re going to see some softening of prices because demand will decrease. So as demand comes down, we’ll see some softening.”
Rettig said as people realize 6.5 percent interest rates are realistic, and decide they want to own a home, he predicts more houses will be built in the next few years.
“We are planning, our company is planning, for a five- to seven-year boom,” he said.
Bickett remains optimistic, and encourages potential home-buyers to share that feeling.
“What we’re trying to show through the home builders association is, there’s still a way to build a house,” he said. “The interest rates are going to come down again. Refinancing is always an option. So if your family is ready and you need a home, or you’re transferring or you’re doing whatever that is, there’s still homes available. We’re still building them.
“I don’t see any need for doom and gloom,” Bickett said. “We’re going to be in kind of a lull for part of this year, but they’re already predicting, the economists are, that the housing market will pick up by the end of 2023. We’re going to keep working.”
The Associated General Contractors of America released an analysis of government data on Jan. 18. It said while the cost of lumber, steel and diesel fuel led to lower costs for construction materials and services in December, that could change.
“Contractors are optimistic about the construction outlook for 2023, yet they are expecting very different market conditions for the coming year than what they experienced last year,” Stephen E. Sandherr, the association’s chief executive officer, said in a Jan. 4 release. “Even as market demand evolves, contractors will continue to be confronted by many of the challenges they faced in 2022, including the impacts of supply chain problems and labor shortages.”
Ken Simonson, the association’s chief economist, said contractors listed the cost of materials as a major concern. More than 1,000 contractors responded to the survey.
While construction prices dropped 1.8 percent in December, they were up 7.2 percent in all of 2022, higher than the 6.5 percent increase in the consumer price index. The price of fuel, lumber and steel declined at the end of 2022, but other costs spiraled up, including the price of ready-mix concrete, copper and brass shapes, hot-rolled coil, used for construction steel and paint. from Pg 8
Lee Rettig, who is in charge of new homes sales and chief marketing officer of K Construction in Yankton, said housing costs have risen 30 to 40 percent, with the price of lumber skyrocketing in 2020. Lumber that sold for $320 per 1,000 linear feet jumped to $1,700 per 1,000 linear feet.
Lumber plants on the West Coast slowed production or shut down completely. Large companies like Lowe’s and Home Depot snapped up much of the available lumber, driving up costs for builders, Rettig said.
“Just getting products was a factor,” he said.
Rettig said with lumber, metal products, plastic, wiring and other items, building a house is a complex matter. There are, he tells people, “10,000 moving pieces in a house,” and the price of all of them can fluctuate.
Lumber prices have returned to nearly their previous level, Rettig said. Mills are once again turning out product to build homes, but there is still some competition for it.
Another reason for the spike in housing costs was the labor market. Many people stayed home at the depths of the COVID-19 pandemic — and some didn’t return to work, Rettig said. When companies went to hire people to place roof trusses, operate shingle-making machines or build and install cabinets, they had to raise wages to find workers.
Companies are now paying $18 an hour for entry-level carpenters, up from $10 to $12 per hour a couple years ago. It’s good for the workers — but it adds to the price of a home, Rettig said.
All this “spooked” many home buyers and home builders, he said. Some of the largest national home builders “literally walked away from contracts,” Rettig said.
“They had to, they couldn’t afford to build the houses because the cost of everything was so unstable,” he said.