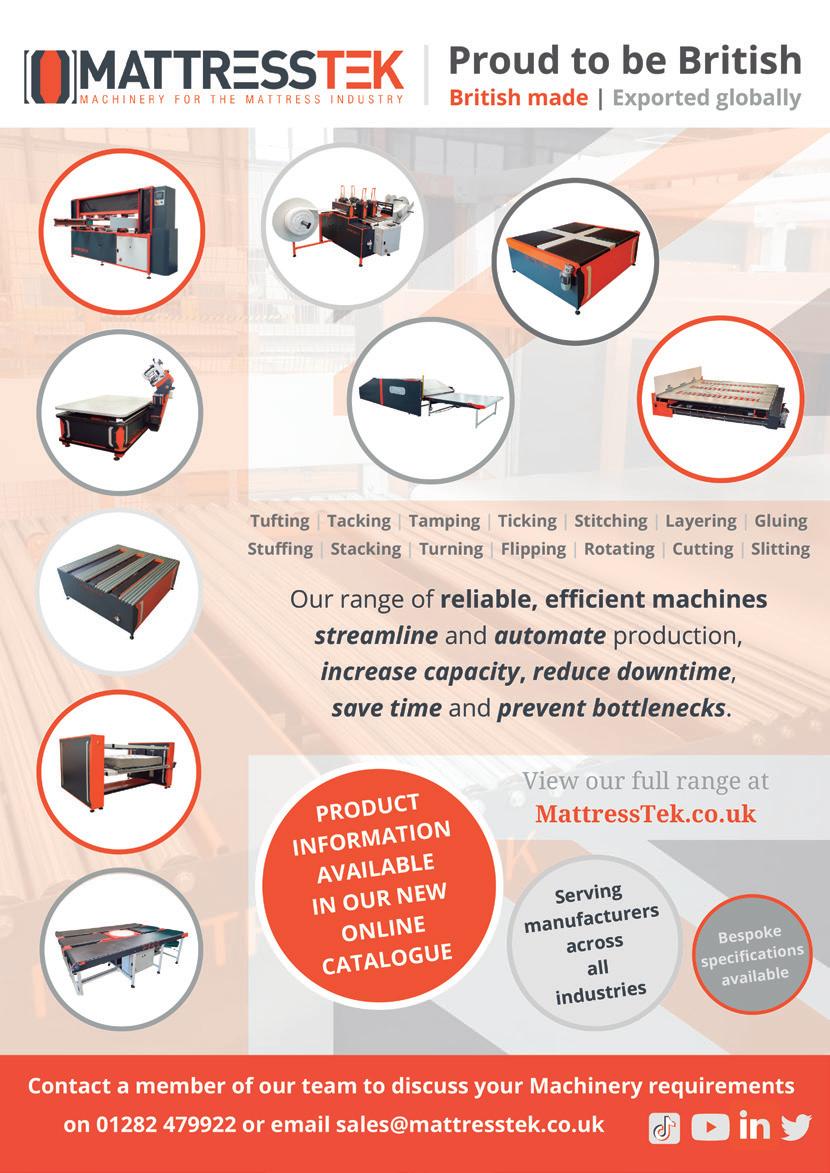
3 minute read
How recent investments are driving the MattressTek machine
FEATURES
How recent investments are driving the Mattress Tek machine
MattressTek Directors, Shaun Peel and Michael Birtwistle, talk about why automation is the way forward and how the company has affirmed itself as a force for growth.
With over 40 years worth of combined experience, made up of a mix of designers and engineers, Lancashire-based mattress machinery manufacturer, MattressTek, has maintained its positioning as a provider of quality, robust and reliable production lines for the bed industry and beyond.
Innovation and problem solving are at its core, which has seen the company invest in a number of areas across the business of late. Shaun Peel, Technical Director at the brand, shares an insight into the importance of continually developing with its focus on helping manufacturers to streamline and automate their production lines.
“We have cemented ourselves as one of the leaders in the making of machines for the mattress industry, and our range has proven popular with clients and big brands in the UK, US, Mexico, Europe and Australia.
“There are a whole host of machines needed to help manufacturers to make their products to a high quality - positioning, stuffing, stitching, sewing, spring unbaling, gluing, turning, flipping, inspecting and packing. Automation is literally the way forward.
“Our machines meet those needs and allow seamless production, ensure efficiency, reduce downtime and increase the number of products made. Automating the process also helps to deal with the labour lag the industry is currently facing.”
MattressTek has recently developed its Stacker and Stuffer machines, as well as 90/180 degree turning and flipping inspection and straight-line belt and roller driven conveyors, which can be made to suit bespoke requirements and be added into existing production lines.
Fellow Director, Michael Birtwistle said: “We have refined and developed our machines, with regard to design and the hardware and technology, to adapt them to fit into limited space at factories, as well as incorporating sensors to flag up when material runs out, threads break and bottlenecks occur.
Shaun explains: “We have seen growing demand for machines such as the Hot Glue Bridge, which applies glue and layers mattress filling components before they are pressed together by the Tamping machine.
“Along with our extensive range of stitching and panel cutting machines, and our offering of conveyors, we have been refining our machines for unbaling and unwrapping pocket spring beds, as well as those that can compress and roll springs and complete mattresses, as we meet the ever-innovative approach to packing compact mattresses.
“We have also invested in a Material Resource Planning system to streamline, track and plan production and resourcing, which will support the sustained global export of our range.”
MattressTek has also revamped their website, where the brand has gone all out to help customers with more resources and product information. The refreshed website, mattresstek. co.uk, features a downloadable catalogue and a more interactive and accessible layout and design to provide solutions to issues that manufacturers face.
Shaun said: “We have added the full range of machines and conveyors and really considered the information customers want to know, as well as videos of machines in operation and in situ on a production line.”
And that’s not all. Over the past 12 months, MattressTek has been busy expanding its physical presence too, all in line with its rapid growth.
“We have built a store for the fabrication and build part of the site and have completed construction of a meeting room space to welcome customers and conduct internal meetings,” Shaun said.
Michael added: “Growth has been pretty rapid, attributable to the development of existing products and processes, along with the introduction of new machines. We look forward to our next phase of growth.”