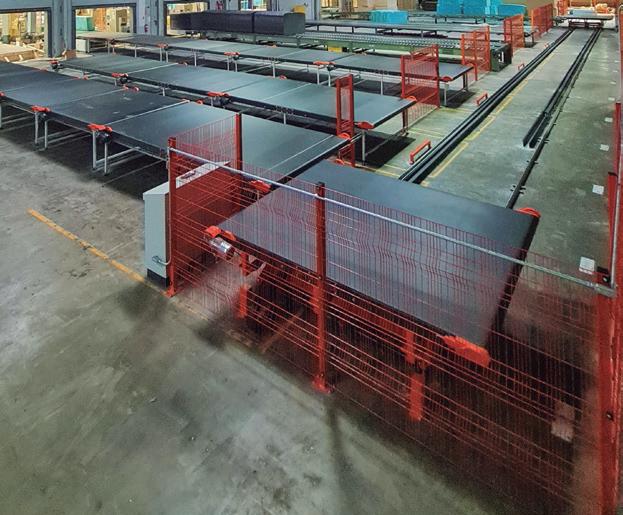
3 minute read
MattressTek continues momentum in automation
It’s been a busy few months for British machinery and conveyor manufacturer MattressTek, with installations of full production lines in the UK and US, including its hot glue lamination and foam processing shuttle transfer lines.
Directors Shaun Peel and Michael Birtwistle discuss the extent of their pursuits and how it has enhanced the way manufacturers make their products, increase volume, improve efficiency and save time.
Continuing success with big names in the mattress and bed manufacturing field, they have installed the seventh full automation conveyor line for a customer in America, as well as bespoke individual machines and partial lines to fit into existing production at factories all across the UK.
Having grown their team to meet the demand, they have been humbled to receive recommendations from the lines they have installed this year, including orders for rolling, packing, stitching, stamping/labelling and transportation systems to move components including foam blocks and rolled foam buns around vast factories and facilities. One of these involved transporting foam blocks from a saw to multiple lines of conveyors, using three straight-line belt conveyors on a track – their ‘Shuttle’ conveyor. A similar line was also installed for a processor in Lancashire to load rolled foam used in almost all aspects of the automotive industry into a compressor.
Examples of their work to enhance automation, streamlining how products are made, as well as ensuring reduced risk to operators, with regard to health and safety, were the design and installation of downward incline conveyors to replace a factory that was sliding divan beds down wooden planks rested precariously on a staircase. This ensured minimal health and safety risks, reduction of labour of, and by, operators, and damage to the product and site, as well as increasing capacity and speeding up transportation.
Another case study that they have been working on, which is also available to look at on the automation page of their website, is the full installation of an automated line to layer foam and pocket spring components, glue and press them together, before stuffing them into a fire sock, stitching the seam with a sock closer, stuffing them into an outer cover before closing that seam, then centre aligning them, ready to be stacked. This has increased production and efficiency by 95%, allowing them to process more than 450 mattresses on each 8-hour shift, and ensuring reduced operator involvement, accuracy of alignment and ease of transportation for the divan based to the lower level of the facility for loading in the logistics area.
They have also been working to redevelop the RollPack machine whereby foam and spring mattresses can be fed into a press, before being spun into paper and wrapped ready for rotation at 90 degrees and raised for positioning on a pallet. They have plans for a similar machine, ideal for manufacturers of rolled and boxed mattresses.
Technical director Shaun explains: “We have been honoured to be recommended by current customers, to both their internal teams and other departments, as well as their network of fellow manufacturers, in the foam processing and transportation world, which has led to us designing and fulfilling orders of bespoke machines here in the UK and across the US and Europe.”
Fellow Director Michael adds: “With automation becoming the logical and sensible thing to consider and incorporate into production, regardless of the sector of manufacturing, to ensure efficiency and streamlining of production, whilst maximising capacity and volume, we are proud to be a British business leading the way in the mattress and bed making and foam processing worlds.”
As a finalist in the International Trade category of The Manufacturer TMMX Awards, and Insider North West International Trade Awards having made it to the second stage of the Innovation and Under £20m Company of the Year categories, the company says: “We have increased our marketing presence exponentially in the past year and to be a finalist in these awards, to further get our brand and range our into the industry, is credit to the hard work of the whole team in ensuring we can provide reliable, robust and efficient machines, designed and build to meet the needs of our customers and help them to optimise production.”
Big Furniture Magazine #4 The installation of our machines in full automated production lines has fed our already established growth and we have been able to document these innovations through case studies, which are now included on our website.
www.mattresstek.co.uk/automation
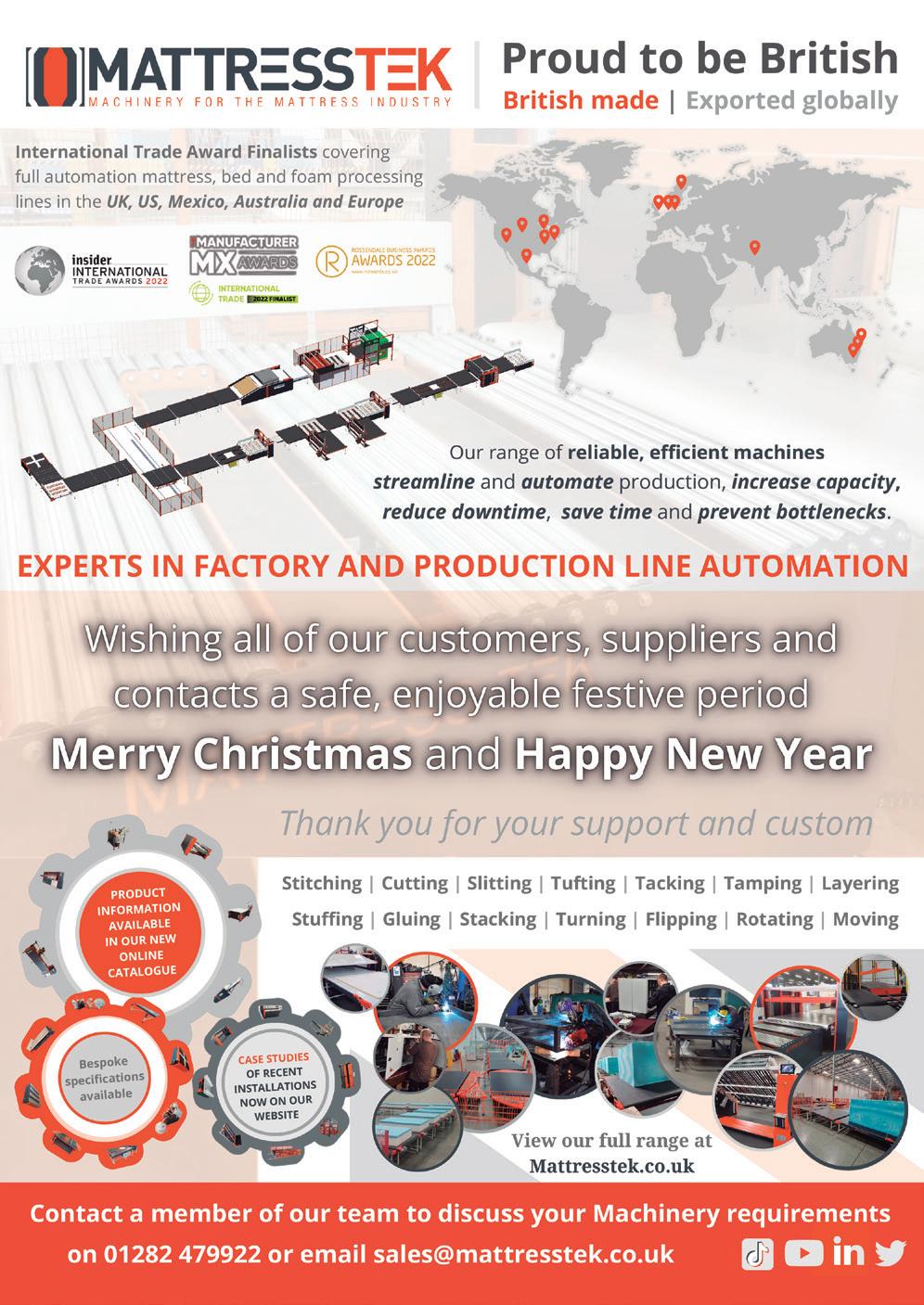