THE STATE OF MINING IN ONTARIO
> The evolving narrative of critical minerals
> The world of mining is changing
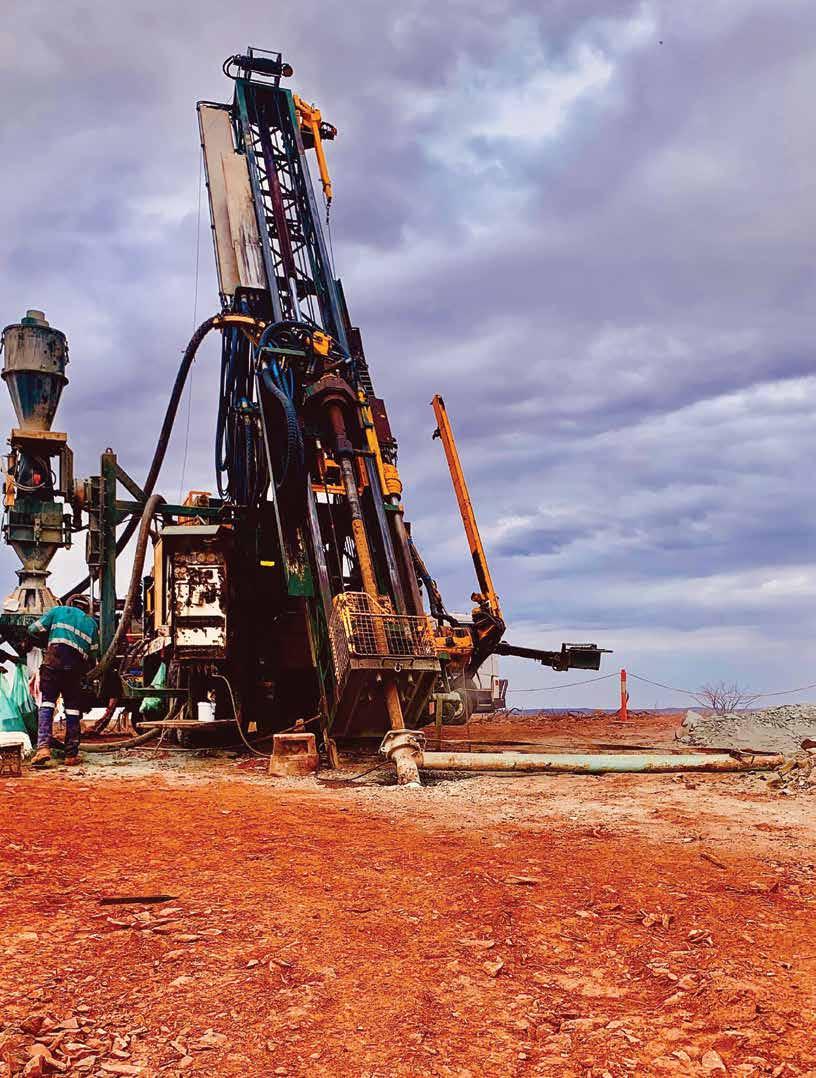
- UNLOCKING CANADA’S MINING POTENTIAL
- UNDERSTANDING INSURANCE DYNAMICS IN MINING

> The evolving narrative of critical minerals
> The world of mining is changing
- UNLOCKING CANADA’S MINING POTENTIAL
- UNDERSTANDING INSURANCE DYNAMICS IN MINING
MINING IN ONTARIO
21 Navigating challenges and embracing opportunities in 2025.
24 Top critical mining projects in Ontario.
29 Alamos Gold expands Ontario footprint with Magino mine acquisition.
31 Dynasty Gold expands Thundercloud project.
34 From green dreams to strategic imperatives: The evolving narrative of critical minerals.
ESG/INTERNATIONAL MINING
36 Energy transition brings mining beneficiation into focus: Who wins?
TECHNOLOGY, EQUIPMENT, AND MAINTENANCE
19 Optimizing ventilation systems for underground mines.
38 Artificial Intelligence: How computer vision is shaping more productive and sustainable mining.
41 Sustainability and tailings management: The role of control valves in sustainable mining.
43 A revolutionary new lubricant can prevent hydrogen wear.
48 Inertial navigation paves the way for resilient mining.
TRAINING AND WORKFORCE
51 Increasing employee retention with robotic demolition machines.
53 Securing the future of Canadian mining: Attracting and retaining talent in a changing landscape.
55 Pay attention: The world of mining is changing.
60 Measuring success from conveyor maintenance and safety training.
HISTORY OF MINING
57 Mining and the idea of Canada.
4 EDITORIAL | Trumpy with a chance of tariffs.
6 FAST NEWS | Updates from across the mining ecosystem.
10 LAW AND REGULATORY | Unlocking Canada’s mining potential: Strategies to attract investment in the sector.
14 MIN(E)D YOUR BUSINESS | Understanding insurance dynamics in mining.
16 MIN(E)D YOUR BUSINESS | Attracting investment into Canadian mining projects.
Tamer Elbokl, PhD
n another recent interview on CBC Radio’s Labrador Morning, I mentioned that I was not surprised to see Trump slap on tariffs on steel and aluminum, as tariffs have been a talking point for months. The forecast has been “Trumpy with a chance of tariffs” for a while. This is déjà vu from what happened in 2018. Since its election in November, this U.S. administration has been threatening tariffs on Canada, Mexico, and on so many other countries.
Tariffs on steel imports to the U.S. will “trickle down” the supply chain, impacting the mining sector in Canada. Canada is a major producer of iron ore and nickel (in Sudbury, Ont. and Labrador), which are major components in steel manufacturing, so the Canadian mining sector will eventually see some upheaval. The silver lining is to diversify our markets.
For the mining sector in Canada, uncertainty will dominate the forecast for the next few weeks. Following a short-lived standoff between the two allies, the U.S. and Canada have agreed to postpone the global imposition of 25% tariffs on each other’s imports for 30 days, as of Feb. 3, 2025.
For Ontario, mining is a cornerstone of the province’s economy and plays a pivotal role in Canada’s natural resources sector. Ontario is Canada’s largest producer of nonfuel minerals, accounting for approximately 25% of the country’s total mineral production. The province’s mining sector is at a critical juncture, with its success closely tied to U.S. trade policy. While the province has the resources and expertise to lead in critical mineral production, tariffs could undermine its competitive advantage, disrupt supply chains, and deter investment. Policymakers in both Canada and the U.S. must tread carefully, ensuring that trade disputes do not derail North America’s ambitions to build a secure and sustainable mining and manufacturing ecosystem.
Ontario’s mining industry will need to work closely with the federal government to push for exemptions or alternative trade agreements that safeguard its access to the U.S. market. Collaboration with American automakers and policymakers will also be key in reinforcing the importance of Ontario’s minerals in strengthening North America’s clean energy transition.
How can we alleviate the impact of tariffs on the mining sector in Canada and specifically Ontario? We need to adopt some proactive measures. The regulatory approval process for projects related to non-renewable natural resources should be led by the provinces and their regulatory bodies. Canada’s current regulatory approval processes for building large projects is a mix of overlapping federal and provincial oversight. Regulatory overlap creates uncertainty. Eliminating regulatory overlap is one way to improve efficiency. The federal government must respect that provinces are competent regulators and capable of ensuring environmental protection associated with development of their resources within their borders. In my opinion, the federal government should completely opt out of the mining permitting and regulatory processes. Read the law column on page 10 of this February/March issue for more insight.
Additionally, articles on pages 21 to 35 provide updates on mining in Ontario. Flip to pages 51 to 62 for articles on latest topics related to training and workforce in mining as well as history of mining in Canada.
If you are planning to attend the Prospectors and Developers Association of Canada (PDAC) 2025 convention in Toronto, Mar. 2-5, please visit our booth # 808 to pick up a hardcopy of this issue.
Finally, our April issue will tie-in BEVs, mine electrification, and de-carbonization. Editorial contributions can be sent to the Editor in Chief until Mar. 7, 2025.
FEBRUARY/MARCH 2025
Vol. 146 – No . 1
69 Yonge St., Ste. 200, Toronto, ON M5E 1K3 Tel. (416) 510-6789 Fax (416) 510-5138 www.canadianminingjournal.com
Editor in Chief
Dr. Tamer Elbokl telbokl@canadianminingjournal.com
News Editor Joseph Quesnel jquesnel@canadianminingjournal.com
Production Manager Jessica Jubb jjubb@northernminer.com
Manager of Product Distribution Allison Mein 416-510-6789 ext 3 amein@northernminergroup.com
Publisher & Sales
Robert Seagraves 416-510-6891 rseagraves@canadianminingjournal.com
Sales, Western Canada George Agelopoulos 416-510-5104 gagelopoulos@northernminer.com
Toll Free Canada & U.S.A.: 1-888-502-3456 ext 2 or 43734
Circulation Toll Free Canada & U.S.A.: 1-888-502-3456 ext 3
President, The Northern Miner Group Anthony Vaccaro
Established 1882 Canadian Mining Journal provides articles and information of practical use to those who work in the technical, administrative and supervisory aspects of exploration, mining and processing in the Canadian mineral exploration and mining industry. Canadian Mining Journal (ISSN 0008-4492) is published nine times a year by The Northern Miner Group. TNM is located at 69 Yonge St., Ste. 200, Toronto, ON M5E 1K3. Phone (416) 510-6891.
Legal deposit: National Library, Ottawa. Printed in Canada. All rights reserved. The contents of this magazine are protected by copyright and may be used only for your personal non-commercial purposes. All other rights are reserved and commercial use is prohibited. To make use of any of this material you must first obtain the permission of the owner of the copyright. For further information please contact Robert Seagraves at 416-510-6891.
Subscriptions – Canada: $51.95 per year; $81.50 for two years. USA: US$64.95 per year. Foreign: US$77.95 per year. Single copies: Canada $10; USA and foreign: US$10. Canadian subscribers must add HST and Provincial tax where necessary. HST registration # 809744071RT001.
From time to time we make our subscription list available to select companies and organizations whose product or service may interest you. If you do not wish your contact information to be made available, please contact us via one of the following methods: Phone: 1-888-502-3456 ext 3; E-mail: amein@northernminergroup.com
Mail to: Allison Mein, 69 Yonge St., Ste. 200, Toronto, ON M5E 1K3 We acknowledge the financial support of the Government of Canada.
“MAXIMIZE SAFETY AND PRODUCTIVITY BY PROVIDING REAL-TIME AIR QUALITY DATA AND EMERGENCY MESSAGES ON A LARGE DISPLAY THAT INTEGRATES WITH ANY NETWORK.”
Eliminate guesswork and know with confidence when it’s safe to move about the mine.
SuperBrite™ Marquee Display provides fail-safe, real-time data by ensuring only current information is displayed – preventing unsafe old data from display when network is off-line. Easily integrated into wireless or Ethernet network and written to directly from any Vigilante AQS™ or Zephyr AQS™ stations, SCADA, DCS, PLC or HMI control system.
The Canadian Mining Journal is honouring the life of mining giant Don MacLean on Jan. 11, 2024. The Journal is pleased to hear MacLean was inducted into the Canadian Mining Hall of Fame in October 2024.
Don Maclean is best known for founding his namesake mobile equipment manufacturing company in 1973 and over the past five decades of growth and product development, as well as helping to revolutionize safety in the underground mining industry globally. His legacy of safety innovation and service will live on through the employees of the company who will continue his lifelong mission of making the underground environment a safer place for miners.
MacLean Engineering pioneered the design and production of the scissor bolter to enhance the safety and efficiency of underground mining. They addressed the need for reliable ground support in challenging environments. There’s also the rubber-tire Long Tom pneumatic drill, the Blockholer and various electric vehicles.
He was also a man of contrasts; country music yet classical, jazz and Piaf, too; mucking about in the barn; but also dressing up. He was known for sporting fedoras that would draw praise on the streets.
January 2025 saw two important milestone agreements regarding the Ring of Fire in the Far North of northwestern Ontario. The Ring of Fire is an area rich in mineral deposits about 540 km northeast of Thunder Bay.
Fifteen First Nation groups and the federal Impact Assessment Agency of Canada finalized terms of reference for the conduct of the regional assessment in the Ring of Fire Area.
This marks yet another announcement on the long journey in securing Indigenous support for developing the mineral-rich region.
This latest step involves the formation of a working group involving the Impact Assessment Agency of Canada and community members from 15 First Nations in the region. The working group will now submit its final report within 30 months from now. This represents two and a half calendar years of waiting some observers in the mining world are concerned about given long running delays and problems in moving ahead on the historic project.
The Ontario government also announced a historic investment in roads and electricity transmission infrastructure for First Nations in the Ring of Fire region.
The Ontario government and Aroland First Nation signed an agreement to invest in key infrastructure for the Ring of Fire area in the far reaches of Northern Ontario. The first part of the investment is for upgrading Anaconda and Painter Lake Roads, which are important connections on the road to the Ring of Fire, as well as major new investments in infrastructure and energy transmission in the region.
Thunder Gold intersected high-grade gold from surface over broad intervals at its Tower Mountain property in Ontario, sending shares to a 12-month high.
The company reported drill results from 13 shallow holes, totalling 753.5 metres. These were done on its flagship property, 50 km from Thunder Bay, from late November to early December 2024.
CEO Wes Hanson called the results “the most significant drill hole results at Tower Mountain in 50 years.” He underlined the potential to match grades found along the western Tower Mountain Intrusive Complex (TMIC) contact.
MAKE YOUR MINE MORE EFFICIENT AND PROFITABLE.
In today’s challenging mining environment, maximizing productivity and cutting costs are critical. The right lubricant choice is essential to your success. Petro-Canada Lubricants offers a comprehensive range of products, including PRODURO™, DURON™, HYDREX™, and our specialized greases and open gear lubricants, all designed to enhance effi ciency and reliability in off-road applications. Choose Petro-Canada Lubricants for superior performance and peace of mind.
Ready to take your operations to the next level? Challenge us to show you the savings! Contact the Petro-Canada Lubricants team today and unlock potential with our Cost Savings Calculator.
petrocanadalubricants.com
Nova Scotia may open the province to uranium mining given recent encouraging remarks from Nova Scotia Premier Tim Houston.
The province has maintained a moratorium on uranium mining since 1981. However, in response to concerns over the expected U.S. tariffs on Canadian goods, Premier Houston raised possibilities over local natural resource development. Nova Scotia has imposed a ban on uranium mining.
The Mining Association of Nova Scotia has been a long advocate for uranium mining in the province. Nova Scotia’s mining and quarrying industry employs 5500 Nova Scotians, mainly in rural areas. The premier has not explicitly said he will left the moratorium on uranium mining, but many are interpreting his willingness to re-visit resource bans as an invitation to re-evaluate uranium mining.
Delivering fit-for-purpose solutions across the entire project life cycle
We are a world leader, boasting decades of experience delivering fit-for-purpose solutions across the minerals and mining industry.
No matter your commodity, we are positioned to serve as your trusted advisors on the ground reducing your supply chain risk. We invest in the latest equipment, continual training and ensure industry requirements are met at the global, regional, and local level.
Fortuna Mining reported record production of precious metals for the fourth quarter and full year 2024 from its five operating mines abroad. For the full year of 2024, Fortuna produced a record 369,637 ounces of gold and 3.7M ounces of silver for a record 455,958 gold equivalent ounces, including lead and zinc by-products. Fortuna is a Canadian mid-tier producer of precious metals with mining assets abroad.
Fortuna also released ambitious exploration plans in 2025. The mining company has a total mineral exploration budget of $41.0 million for 2025, compared to an estimated $44.0 million invested in 2024. Brownfields represents 53 percent, and greenfield initiatives, including $8.3 million for Diamba Sud, represents 47 percent of this year’s budget.
Artemis Gold announced the successful completion of its first gold and silver pour at the Blackwater mine in British Columbia. The company has targeted commercial production in the second quarter of this year. In December 2024, Artemis postponed first gold to January 2025 due to delays in final commissioning of the wet plant. Issues with the control circuit configuration and a lack of vendor specialists during the holidays caused the delay.
BMO Capital Markets noted, “Yesterday’s first gold pour at Blackwater is a positive, if expected, milestone after holiday startup delays.”
“Targeting commercial production in Q2 2025, Artemis stands out as a new, sizeable mine with the potential to produce ~500,000 oz/year in a top jurisdiction.”
Kirkland Lake Discoveries identified extensive gold mineralization now that it has completed its fall 2024 drill program at the Hargreaves shaft and the Jo zone on the Goodfish-Kirana claim group. Drilling teams completed a total of five diamond drill holes aggregating at 1,187 metres. The properties are located near the town of Kirkland Lake in northeastern Ontario.
The gold producer announced it had intersected anomalous gold at both the Jo Zone and Hargreaves shaft with highlights including: Jo zone (KLD24-27): Extensive gold mineralization across 37 metres throughout the drill hole independent of rock type, including intervals of 4.5 metres at 0.621 g/t gold, 13.66 metres at 0.287 g/t gold, 1.2 metres at 3.82 g/t gold, 5.6 metres at 0.894 g/t gold, 5.23 metres at 1.035 g/t gold and 7.29 metres at 1.334 g/t gold.
The Centre for Excellence in Mining Innovation (CEMI) – a Sudbury-based research initiative dedicated to accelerating technological innovation within the mining sector – has signed an agreement with DIGITAL to collaborate on fostering technical innovation and securing global opportunities for Canada’s mining sector and for mining technologies. Digital is known as an innovative tech cluster that has been expanding its mining portfolio significantly since 2018.
The memorandum of understanding signed between the two organizations intends to enhance the competitiveness, environmental performance, and profitability of the mining sector within Canada.
By David Hunter, Bernard Roth,
Canada is facing an investment and productivity crisis, and its onerous and lengthy regulatory approval processes are compounding the problem. There is a common misconception that shortening regulatory approval process timelines must come at the expense of environmental oversights and affected Indigenous groups. Canadian regulatory approval processes can and should be implemented in a way that allows projects to proceed in a timely manner, without sacrificing necessary environmental requirements and Indigenous interests.
Canada’s regulatory approval processes have been negatively impacting investment because they create uncertainty for investors and negatively affect the financial viability of proposed major projects. Investors will pursue a project if the net present value (NPV) exceeds the cost, but the longer the project timeline stretches, the more the NPV is eroded by inflation and the opportunity costs of foregoing other investments. Consequently, the longer a project timeline stretches, the higher the required return on investment to justify the delay. In a competitive global economy, regulatory delay is a significant barrier to investment.
The harm caused by Canada’s regulatory approval processes is not a matter of conjecture, it is supported by data. The chart below demonstrates that investors view investing in Canada as higher risk than the U.S. and Australia, which are Canada’s major competitors for mining and oil and gas investments. This perceived uncertainty is being reflected by fewer dollars being invested. For example, Canada’s estimated global share of min-
ing investment has fallen precipitously. In 2015, Canada accounted for 12% of global mining investment but this figure nearly halved to 7% in 2023.
Economic theorists have understood the positive correlation between investment and productivity for a long time. When investment stalls, productivity suffers. Relative to the U.S., Canada is second to last amongst G7 countries when it comes to productivity decline in recent decades.
Further, Canada’s relatively stagnant mining industry appears to conflict with its commitments to decarbonize the economy. Canada is rich in many critical minerals necessary to build a robust low-carbon economy, including copper, manganese, platinum, uranium, lithium, cobalt, indium, tellurium, and rare earth elements (REEs). Fatih Birol, the executive director of the International Energy Agency (IEA), has suggested he prefers that Canada be a world leader in critical mineral production because “there is rule of law, there is transparency, and there is accountability of government.” The problem with the IEA is that it has also suggested that there should be no investment in new
oil and gas production to achieve net-zero. Canada’s federal regulatory process has been used to curtail investment in the development of Canada’s natural resources. This comes at a significant cost to Canada’s economy and productivity.
Canada’s current regulatory approval processes for building large projects is a mix of overlapping federal and provincial oversight. Regulatory overlap creates uncertainty. Eliminating regulatory overlap is one way to improve efficiency.
Over the past decade, the federal government has involved itself in the approvals process for major projects like mines. This needs to change. The federal government should accept that provinces have strong environmental assessment and protection regimes, and its intervention is not needed to ensure high environmental standards are met.
The Impact Assessment Act (IAA) is the federal government’s primary tool to assess the impacts of major projects. Enacted in 2019, the IAA was supposed to offer streamlined regulatory timelines while maintaining stringent environmental and social standards. However, it was challenged by the province of Alberta as being ultra vires federal powers. Alberta’s challenge was motivated by the federal government’s use of the IAA to try to force the adoption of caps on climate change emissions. In reference to the Impact Assessment Act, the Supreme Court of Canada (SCC) ruled against the federal government and held that most of the IAA was unconstitutional. The Supreme Court’s decision brought into question the federal government’s jurisdiction to impose emissions caps on industry in a province.
As a result of the SCC’s ruling, some changes to the IAA were enacted in June 2024. The IAA reference decision does not bar the federal government from designing environmental legislation but emphasizes that any contemplated federal environmental legislation must respect the division of powers under the constitution. However, constitutional litigation is unlikely to solve the problem because the problem is not a legal one; it is a political one. To borrow a western idiom, legislation can continue to be amended, and lawyers can argue about constitutional jurisdiction until the cows come home, but what is truly needed is an attitude adjustment that sees the federal government respect that provinces are competent regulators and capable of ensuring environmental protection associated with the development of their resources within their borders.
The regulatory approval process for projects related to non-renewable natural resources should be led by the provinces and their regulatory bodies. Regulatory bodies are specialized in particular areas of the law and have the expertise and institutional knowledge necessary to adjudicate regulatory approval processes. Provincial governments and their regulatory bodies can implement requirements that are as stringent as those of the federal government and its regulatory bodies. The issue damaging Canada’s ability to attract capital to develop its resources is not overly stringent or restrictive environmental or social requirements, it is the uncertainty created by duplication in regulation and the perception that at the federal level, Canada is not interested in developing some of its most signifi-
cant resources. Legislative changes and constitutional challenges are unlikely to be an answer to the problem because they just bring more delay and continue the uncertainty. Again, what is needed is a change in attitude. The regulatory approval processes can be efficient without jeopardizing Canada’s environmental and social goals. Continuous conflict between the federal and provincial governments is highly unproductive.
Through various iterations of legislative change over past 30 years, the federal government has always had the ability to defer to provincial regulatory processes and accept their results in the interests of providing timely decisions and regulatory certainty. The federal government has recently indicated that it wants to change its approach, to achieve these objectives, but only in relation to what it considers to be “clean growth projects.” To be effective in creating the certainty needed to attract investment in Canada’s mining industry, the federal government can not be selective in its efforts to streamline its regulatory process. Regulatory certainty requires that all provinces and projects be subject to the same process.
Nowhere is this regulatory inefficiency more apparent than in process to permit a new mine in Canada, which involves both federal and provincial regulators under the IAA and provincial environmental assessment acts, such as B.C.’s Environmental Assessment Act. The duplication of regulatory oversight across a broad range of social, ethical, cultural, and economic impacts, in addition to environmental, health, and safety considerations, has left Canada with a process that can extend to 15 years. Recent recognition of the importance of securing domestic sources for the critical minerals essential for technologies like electric vehicles, renewable energy systems, and advanced electronics has drawn much needed attention from political and industry leadership. Presently, the Mining Association of British Columbia (MABC) is advocating for a new permitting strategy aimed at reducing mine permitting timelines to seven years. A key element of MABC’s strategy is convening joint project tables to streamline and align federal and provincial permitting and authorization processes for designated projects. Recently, both the provincial New Democratic Party and the Conservative Party have made commitments to expedite B.C.’s mine permitting process, reflecting a growing consensus of the need for a more efficient and streamlined permitting approval processes.
The importance of Indigenous equity partnerships
Indigenous partners can be important to the success of major projects in Canada. Affected Indigenous groups can significantly delay the regulatory approval process, but partnering with them on project development can significantly expedite the regulatory approval process and advance economic reconciliation. Successful business operations in Canada depend on the ability to adapt to the evolving relationship between federal and provincial governments and Indigenous partners, including First Nations communities.
Economic reconciliation, broadly speaking, is an initiative to include Indigenous peoples, communities, and businesses in economic activities. In Alberta and B.C., many Indigenous
groups are working together with industry to develop large projects as equity partners. Mining projects are well-suited to achieving economic reconciliation because they are geographically confined, allowing for the identification of a limited number of the most affected Indigenous groups to become partners in development.
The reconciliation process remains a priority for the Canadian government, which has demonstrated a willingness to take significant steps to address the matter. Increasingly, First Nations’ communities are seeking equity ownership rather than jobs, training opportunities and profit-sharing traditionally offered through impact benefit agreements (IBAs). Equity ownership is increasingly viewed by Indigenous communities as representing a step towards true economic self-determination.
Canadian courts have found that First Nations’ communities have inherent rights to lands demonstrated to be part of their traditional territories; however, First Nations’ communities have historically faced challenges in monetizing these rights. Recent government programs, such as loan guarantees, are addressing this gap by enabling First Nations to access capital for equity investments. These measures are instrumental in ensuring they can participate fully in major projects in their territory as equity stakeholders.
In its 2024 budget, the Canadian federal government announced a pledge to establish and fund a national Indigenous loan guarantee program up to $5.0 billion through a newly formed, wholly owned subsidiary of the Canada Development Investment Corporation: the Canada Indigenous Loan Guarantee Corporation. This initiative aims to provide First Nations’ communities with the financial tools necessary to participate as equity stakeholders in major projects, with the intent of fostering economic reconciliation and enhancing regulatory certainty.
Similarly, B.C.’s three-year fiscal plan, published in 2024, highlights the importance of meaningful project involvement and ownership opportunities for First Nations’ communities. To support this, B.C. introduced the First Nations Equity Framework in 2024, intended to facilitate participation projects through various mechanisms, including equity loan guarantees.
The First Nations Equity Framework establishes a First Nations Equity Financing special account, initially funded with $19.0 million to address capacity needs and provincial program costs for various projects. Additionally, the B.C. government has authorized guarantees for equity loans, capped at $1.0 billion to help First Nations’ communities acquire equity stakes in priority projects. Other provinces with loan guarantee programs in place include Alberta, Saskatchewan, and Ontario, through the Alberta Indigenous Opportunities Corporation, the Saskatchewan Indigenous Investment Finance Corporation, and the Aboriginal Loan Guarantee Program, respectively.
Equity partnerships, often structured as limited partnerships or joint ventures, provide First Nations’ communities with greater control, equity, and financial benefits compared to traditional IBAs. Limited partnerships are often the preferred model owing to potential tax advantages under Section 87 of the Indian Act. For example, income earned by an Indigenous
partner through a limited partnership connected to reserve lands may be tax-exempt because of its flow-through income structure, which enhances the financial viability of such arrangements. This structure is particularly effective when part of the business is conducted on-reserve, leveraging the tax exemptions to maximize net benefits. By contrast, lump-sum payments or revenue sharing from IBAs are fully taxable, diminishing their overall value.
While equity partnerships present substantial opportunities, several challenges remain. A notable issue is the ambiguity surrounding the legal status of “bands” under Canadian law, which contributes to uncertainty in partnership arrangements. As part of the reconciliation process, certain First Nations’ communities now possess the legal authority to exercise ownership over traditional lands, grant land rights and licences, manage natural resources and enact laws on those lands.
When pursuing Indigenous equity partnerships, one of the most difficult issues is to identify the groups to partner with. Project equity can be diluted, along with its effectiveness, if participation is too broad. This is a major challenge to linear infrastructure projects that can affect dozens of groups but is far less of an issue for mining projects that are able to be far more focused in their partnership arrangements. Mining projects can more realistically use economic reconciliation by adding equity to the benefits they offer to achieve informed consent from the most affected groups.
Ultimately, equity partnerships with Indigenous groups represent a valuable approach to resource development, combining economic reconciliation with long-term financial benefits and enhanced project certainty. By addressing challenges such as regulatory overlaps and providing robust financial support mechanisms, these partnerships can significantly advance Canada’s goals for inclusive growth and sustainable development.
Canada’s investment and productivity crises are being compounded by inefficient regulatory approval processes for major projects. Investors are wary of investing in Canada because there is too much uncertainty regarding project approvals and timelines relative to other comparable jurisdictions. As timelines increase, the economic viability of projects decreases, and investment dwindles. There are two primary changes that can make Canada more competitive internationally. First, the federal government needs to accept that provinces and their regulatory bodies can ensure the protection of the environment in the development of their natural resources. Second, project proponents can pursue Indigenous equity partnerships as a tool to both smooth the regulatory approval process and advance economic reconciliation.
David Hunter is a partner in Dentons Canada LLP’s corporate group. Bernard Roth is a partner in Dentons Canada LLP’s energy regulation group. Mary Su is an associate in Dentons Canada LLP’s corporate group. The authors would like to thank articling student, Ben Kriwokon, for his significant contribution to this article.
Mining incidents that capture headlines tend to cause an immediate reaction within the insurance industry, leading to proposed coverage changes that impact mining companies during their next insurance renewal cycle. Current trending topics shaping this landscape include business interruption volatility, accurate property values, waiting periods, heap leach and tailing facilities, underground exposure, strikes, riots, civil commotion, and malicious damage coverage.
Commodity price cycles are an area of concern for insurers in mining. The fluctuating exposure makes it difficult to determine appropriate premiums. Insurers do not want to be in a position of deploying capital at a fixed premium only to have the business interruption exposure double six months later because of a higher commodity price — without receiving adequate premium for the increased exposure that they are now at risk for. As such, although business interruption volatility and commodity price caps are not new to the mining industry, insurers are now pushing to have at least one of them included in the policy wording.
Mining companies should be reviewing the commodity prices
reported on the business interruption worksheets they provided to insurers as part of the underwriting submission, particularly if there is a business interruption volatility clause on the property and business interruption policy. A business interruption volatility clause applies a cap, typically a percentage, to the declared business interruption values either on a monthly or annual basis or both.
Mining companies should stress test the business interruption volatility percentage/commodity cap applied to their policy to ensure it is within their company’s risk appetite. If the insured requires a higher cap, this should be raised with their insurance broker to discuss with the markets who can provide options with the applicable premium associated with the increased coverage, and vice versa if a lower cap is required.
Another area of concern for insurers has been the accuracy of declared property values. This being due to a mix of inflation and insurers realizing losses that were higher than expected because replacement costs were higher than those declared by companies in their statement of values. As a result, insurers began pushing for margin clauses to be added to property policies and requiring updated property appraisals.
A margin clause limits the amount recoverable from a loss to a specific percentage of the property values declared at policy
inception. The intent of this clause is like a co-insurance clause where the insurers want the declared values to be as accurate as possible. If a mining company has had a recent property appraisal and has continued to apply credible indexes to their declared values, then typically a margin clause can be avoided.
The application of business interruption waiting period deductibles varies from policy to policy. Mining companies should be reviewing these thoroughly to ensure they understand and agree with what their company has accepted as risk retention on their balance sheet. For example, some waiting period language requires mining companies to deplete their inventory or stockpile prior to the commencement of the waiting period.
From some insurer’s perspective, once the inventory has been depleted that is when the business loss starts. However, from a mining company’s perspective that inventory or stockpile has a purpose, potentially for blending or to cover a production outage that is due to a turnaround.
If the mining company uses the stockpile during the business interruption waiting period, is this covered under the insurance policy? How is it credited in the insurance claim? Is the production cost to build the inventory back to where it was prior to the loss covered?
These are discussions mining companies should be having with their insurance broker prior to a loss to ensure there is understanding of how the policy responds and if changes to the policy wording are required.
The Çöpler mine disaster in Türkiye (2024), where a landslide occurred on a heap leach pad, has renewed insurer focus on these structures. Heap leaching, widely used in mining, involves stacking low-grade ore or waste material for extraction. While cost-effective, these facilities present unique risks because of their reliance on structural integrity, environmental safeguards, and effective governance.
Prior to offering any substantial limits for heap leach pads, insurers are required to review documentation, such as up to date third party engineering reports, including any recommendations and the mining company’s response to those recommendations and action plans, governance practices, safety measures, and technical guidelines.
A similar approach is applied to tailings management facilities, following several failures over recent years. Whether it be for property and business interruption coverage or environmental liability coverage, insurers need sufficient documentation to provide them with comfort surrounding the risk before they deploy any meaningful capacity.
As a result of claims history and the higher risk exposure, underground insurance coverage for mining operations is often difficult to secure and is typically subject to sub-limits when obtained. Coverage for underground floods, particularly for mines that are situated under a sizable water table, comes at a high premium cost if insurers are willing to offer it at all. To achieve any meaningful property and business interruption capacity, mining companies must provide sufficient documentation demonstrating best-in-class operations. Key evidence includes ground control procedures, maintenance plans, fire protection measures, redundancy or spare capacity for
critical equipment (notably de-watering systems), capital expenditures, and third-party engineering reviews.
Historically, strikes, riots, civil commotion, malicious damage, and terrorism coverage was offered under a property and business interruption insurance policy (typically with a sublimit). However, the recent increase in incidents and claims has prompted reinsurers to exclude these risks from property treaties. This has led to insurers removing such coverage from property and business interruption policies. For mining companies seeking protection, stand-alone coverage is available through the terrorism and political violence market. This market offers broader coverage than was previously provided under standard property and business interruption policies.
The Canadian mining insurance market is becoming more favourable for property, machinery breakdown, and business interruption coverage, as well as claims-free risks. There are new markets entering the mining space and increased capacity being offered by markets who have been long term players.
Canada is home to world-class mining operations with some of the highest standards in safety and environmental protection, and this continues to inspire confidence among insurers. If a Canadian mining company has operations outside of Canada, it should evidence to insurers that Canadian standards are also being applied to their mines abroad. Insurers tend to approach risks outside of Canada and the U.S. with caution because of different levels of mining standards.
Thorough, up-to-date documentation — particularly thirdparty engineering reports — is key to achieving meaningful mining coverage. Companies are advised to provide a comprehensive underwriting package well in advance of renewal (60 to 90 days before the policy renewal date).
In the unfortunate instance when a claim does occur, providing notice to the insurers as soon as it is evident that there may be an insurance claim is key to starting a positive claims process. This allows insurers time to properly respond and send adjusters to the location of the incident to gather relevant information to support the claim. Mining companies should develop a factual timeline of the events leading up to the claim, a root cause analysis of the incident, and a timeline of events that followed the loss. This factual storyline should strengthen a mining company’s position when negotiating a claim settlement.
Insurance is a relationship-driven industry. Mining companies should prioritize in-person meetings during renewal cycles and throughout the year to build rapport with insurers. Claims discussions typically go more smoothly when there has been rapport built between the individuals at the table, and with both parties wanting to continue the relationship they have developed over the years. Given the small size of the mining insurance community, maintaining strong ties with brokers, adjusters, risk managers, and service providers is fundamental to successful placements and claims handling.
As senior vice-president of risk management, Katherine Dawal brings her risk management expertise to the Complex Risk Solutions Group of NFP in Canada, with a specialization in mining.
By
With the globalization of investment dollars, the regulatory framework for a mineral exploration or mining project plays a key factor in the analysis both foreign and domestic investors make: Can a project get off the ground? Will permits be obtainable on a timely basis or at all? Who can object and what does that mean? And, perhaps most importantly, will the process be predictable? A regulatory system that functions as a patchwork as opposed to being harmonized lacks certainty and risks alienating capital.
“If you cannot grow it, you have to mine it” — the reality is simple, but the regulations are not.
Canada and its provinces acknowledge the importance of predictability in creating a well-functioning and regulated mining sector, including by publishing high-level strategies on critical mineral projects in their respective jurisdictions. The implementation of these government strategies requires significant action to achieve the desired results in a timely manner. This article considers the current regulatory and legal issues in Canada that may impact the ability of companies conducting mineral exploration, development, or production activities to attract investment.
Provinces govern exploration and extraction of mineral resources — they have their own legislation relating to operating and permitting mines, staking claims, and conducting other mineral exploration and development activities, and are generally the jurisdictional level which regulates business. All provinces other than Prince Edward Island further have developed strategies related to critical minerals, though some are clearly more welcoming than others of projects.
Saskatchewan has rich deposits of potash and uranium, along with 27 of the 34 critical minerals identified by the government of Canada, as well as gold. The provincial government has strongly supported the increase in exploration, development, and production, and specifically has set a goal to account for 15% of Canadian mineral exploration spending and double the number of critical minerals being produced by 2030. A 2023 survey of mining companies by the Fraser Institute indicated that Saskatchewan, followed by Quebec and then Manitoba, are the top Canadian jurisdictions for investment. Similarly, when assessing policy factors alone, Saskatchewan came out on top. British Columbia, discussed below, scored among the lowest of any Canadian jurisdiction. Saskatchewan is a jurisdiction that has been vocal about its priorities in promoting mineral projects, and both the industry and the investment community have clearly listened.
While well-known as a leading oil and gas producer, Alberta, like the rest of Canada, has deposits of critical minerals, including those produced as byproducts rather than targeted minerals. At present, there are no critical minerals mines in Alberta; however, the province has established the Minerals Strategy and Action Plan to enhance its profile as a possible producer and supplier of critical minerals on the world stage. One of Alberta’s priorities has been the establishment of more publicly available geoscientific information to attract investments by providing pre-exploration information. Further, Alberta identified the need for clarity and predictability when it comes to regulation and is attempting to streamline laws in this space through the Mineral Resource Development Act, which, among other things, has given authority to the Alberta Energy Regulator over minerals just as it did over oil, gas, and coal.
Ontario and Quebec have standing policies related to development of minerals and specifically critical and strategic minerals, and have, as discussed below, enticed exploration activities through tax credits. Ontario and the federal government have attempted to unlock the opportunity that the Ring of Fire region holds, but advancing projects in this area is complex, and has so far proven elusive. Ontario has an existing geological dataset that is publicly available to assist with pre-exploration activities, and Quebec is not only enhancing its geoscientific data but has also noted that it plans to use technology to make the dataset more meaningful. Quebec has noted a priority on acquiring new geoscientific knowledge and information as key to supporting exploration and specifically outlines that its data indicates that every dollar invested in such knowledge generates an average of five dollars in exploration work, in addition to reducing the risks for mineral exploration companies. Quebec has signalled its willingness to prioritize investment in the natural resources sector by promoting exploration, development, and production activities, with visible success, and establishing provincial tax credits for Quebec taxpayers on critical minerals exploration in the province. For context, Ontario currently boasts 36 active mining operations, and B.C. has 25 operating mines or quarries, while Quebec’s government notes that there are approximately 200 active mines, quarries, and sandpits located in the province, which include 20 metal mines.
B.C. published its “Phase 1” critical minerals strategy in January 2024, highlighting key priority areas, including infrastructure development. Development projects like the North Coast Transmission Line and Northwest B.C. Highway Corridor Improvements Project are needed to support critical mineral development and to enable electrification of mining projects in line with the province’s CleanBC plan. The province has also been focused on ensuring that the administration of the Mineral Tenure Act (MTA) is in line with its duty to consult. In September 2023, the Supreme Court of British Columbia held that the province’s online staking system for mineral claims was contrary to the province’s duty to consult Indigenous groups when registering mineral claims under the MTA within their traditional territories, which has the potential to impact Indigenous rights prior to any consultation occurring. While the MTA was constitutional, the court found that the administration of the tenure system was not. As such, the court sus-
pended its declaration for 18 months to allow the design of a system for the registration of claims. On January 7, 2025, the province announced its draft Mineral Claims Consultation Framework, designed to address the court order. Under the new framework, mineral claims will not be automatically registered on application but instead will be subject to a prior consultation process by the provincial government with potentially affected First Nations. Claim registrations may be subject to conditions or rejection based on the consultation process. The framework remains subject to several questions, including what protections there will be, if any, related to the intellectual property of explorers and miners, who will be obligated to disclose their claim areas prior to having any rights to the mineral claims or the land under which they exist. The province is also committed to modernising the MTA in line with the United Nations Declaration on the Rights of Indigenous People. The government has stated that it intends to engage with industry and First Nations regarding the modernization.
While mining activities are regulated at the provincial level, the federal regulatory environment is complex and includes Canada’s import and export laws (both generally and specifically for certain mined materials, such as the Import of Rough Diamonds Act), transportation laws, the environmental protection regime, which goes beyond the impact assessment process and includes navigable waters legislation, fisheries, migratory birds, and other areas. Beyond navigating the litany of regulations that might apply to a mining project, a significant source of uncertainty introduced because of this regulatory approach is uncertainty of timing — in short, delays.
These delays are exacerbated when federal and provincial processes are not harmonized, including with respect to the environmental assessment processes. While Canada and the B.C. are party to the Impact Assessment Cooperation Agreement between Canada and B.C., not all provinces have thus far entered into such cooperation agreements. Addressing parallel permitting requirements with environmental assessments continues to be a challenge, with duplication and inefficiencies common issues.
The length of time it takes to move through the review process can take 12 to 15 years, and the Minister of Energy and Natural Resources has noted that he believes it can be reduced to five, through conducting reviews for various permits concurrently instead of consecutively, increasing staffing to reduce backlogs, and supporting the development of infrastructure. Should the political willpower to achieve this timeline continue to exist, investors can hope for more efficient returns as projects would be able to become revenue generating much faster.
Since 2009, with the adoption of a national security regime, the federal government has used its authority under the Investment Canada Act (ICA) to review, alter, or prevent transactions that it views as injurious (or potentially injurious) to Canada’s national security. In 2022, the federal government put miners who rely on investments from China on edge, with the forced divestiture of three minority investments in Canadian companies involved in lithium mineral projects, two of whom had no projects in
Canada, which were held by Chinese investors. It appears that each investor may have been closely tied to, subject to influence from, or compellable to comply with extrajudicial direction from the People’s Republic of China (PRC). While the federal government never explicitly alleged publicly that these investors have any connections to the PRC, the government’s statement announcing these national security decisions included a direct electronic hyperlink to the government’s Critical Minerals Policy, which only applies to SOEs and investors that could be influenced or compelled by foreign governments.
Over the past several years, the federal government has refined its position on investment from China as well as increased its powers more generally through amendments to the ICA, which effectively allow the imposition of interim mitigation measures while a review is ongoing and will require pre-closing filings for investments in certain enumerated sectors, which we expect will include operations related to “critical minerals.” A pattern has emerged of lengthy reviews that can be well more than the 200-day period provided for in the ICA, and failures of deals either because of the length of time or possibly the requirements for approval being floated by government officials during their discussions with the applicants. This trend includes Solaris Resources Inc. abandoning its prospective $130 million minority investment by Zijin Mining Group, which a cynical observer might assume at least partially informed Solaris’ decision to exit Canada and relocate to Switzerland. A recent successful transaction, being Paladin Energy’s $1.14 billion takeover of Fission Uranium, demonstrates the circumstances in which overseas buyers with ties to China might be approved. Reuters reports that Paladin, an Australian company holding a Namibian project that was partially financed through an investment from a Chinese company, agreed not to use Chinese sourced finance to fund the project, or sell the uranium directly or indirectly to any Chinese customer other than China General Nuclear Power Group. Similarly, Canada’s approval of the sale of Pan American Silver’s La Arena project in Peru to a subsidiary of Zijin Mining Group was in part predicated on an agreement where the intention is to supply North American markets with the copper concentrate that will be produced.
Attracting Chinese or state sourced financing for Canadian companies will remain challenging for the foreseeable future. Investors will need to engage in a review process that may take seven to nine months, or potentially longer, and enter Westernfriendly restrictions on future sales and operations, while maintaining a Canadian decision-making structure.
Where Canada has been able to promote mining industry investments in an effective way, it has done so by promoting domestic capital through flow-through financing options, which allow tax deductions for certain exploration expenses incurred by mining companies to be transferred to investors, thereby reducing the real dollar cost of the investment. In addition to the flow-through deductions, the mineral exploration tax credit
(METC) provides investors with an added 15% non-refundable tax credit for early exploration, which is deductible from taxes payable. Other measures include a critical mineral exploration tax credit (CMETC) which effectively increases the METC tax credit to 30% if the company in question is primarily exploring for designated critical minerals, including copper, lithium, and nickel, and a clean technology manufacturing investment tax credit, which applied to investments in eligible property used in critical mineral extraction and processing.
In addition, the provinces may offer additional tax credits which apply to provincial income tax, and Quebec notably allows investors to deduct up to 120% of the cost of certain exploration expenditures, and Ontario has an Ontario focused flow-through share tax credit for mineral exploration projects in Ontario which provides a 5% credit.
Importantly, the METC and CMETC are not permanent features — the METC is currently slated to expire on March 31, 2025, and the CMETC is currently slated to expire on March 31, 2027.
Canada and its provinces, as jurisdictions for investment, have identified the priority areas and laws that would make it more attractive for mining investors, specifically policies aimed at increasing data available to exploration companies, incentivizing investment through the tax system, and reducing regulatory delay in the regulatory process for development stage and production stage mineral projects. The actual implementation of those policies is mixed. At present, different provinces are at different stages in creating a predictable environment for mining capital, and the federal government has not committed to permanent tax incentives for domestic capital, or found a replacement for the China-based capital that it has rejected as forming part of the funding needed for domestic critical minerals projects. Companies seeking to attract investors need to be realistic about the risks involved on a jurisdictional level, which vary based on both the province or territory the project is based in and on what the anticipated funding sources are. For exploration level projects seeking domestic capital, Canada’s flowthrough regime provides attractive options. For other projects, Saskatchewan’s objectives in aggressively increasing the number of projects, or Quebec’s history of shepherding projects from exploration through to production, might create attractive conditions for foreign investors (from the U.S. or the E.U.) wanting to take advantage of the stability of those jurisdictions in comparison to other international sources of minerals.
Mining is both Canada’s history and future. The competitiveness of our industry for investment will be tied to efficient regulation and a tax system that incentivizes exploration, and at present, there are some successes but many more opportunities to enhance mining activities in Canada.
Sasa Jarvis is a partner, mining, capital markets & securities; Cory Kent is an office management partner, based in Vancouver; and Sharon Singh is a partner and co-head of environment and Indigenous at McMillan LLP.
An underground mine’s ventilation system is an intricate series of drifts and raises connected to a main backbone designed to deliver fresh air throughout the mine while safely exhausting contaminated air to the surface. As mines expand deeper underground and further laterally, the ventilation system must work even harder to push fresh air to where it is needed. This increased demand could lead to higher costs — whether from installing larger fans, adding more equipment, or perhaps constructing a new vent raise, which could easily range from $200 to $300 million. With operational costs under constant scrutiny, mining companies are looking for smarter, more cost-effective solutions. Implementing ventilation control strategies offers a viable option for reducing energy consumption without compromising air quality. Given that ventilation accounts for roughly 50% of an underground mine’s overall energy consumption, implementing the right strategies could extend the system’s capacity, ensuring fresh air where it is required, essentially maximizing efficiency, and making the most of existing infrastructure.
Three key strategies for optimizing mine ventilation
Controlling fresh and exhaust air fans efficiently can significantly improve ventilation performance and reduce costs. Here
are three key strategies:
1) Scheduling: Fresh air requirements during regular operations are generally based on mobile diesel equipment airflow requirements or heating and cooling conditions. However, when blasting occurs, additional contaminants enter the airflow, requiring a clearing period that forces personnel to remain on the surface for two or more hours, cutting into valuable production time. By strategically scheduling and increasing
main fan airflow using variable speed drives (VSD s) on the main surface fans and remotely controlled starters on auxiliary fans, the blast clearing period can be reduced by up to 50%. This allows personnel to return underground sooner and resume mining operations more quickly.
2) Telemetry: Equipping personnel and mobile equipment with radio-frequency identification (RFID) tags allows for realtime tracking of underground activity per location by control room operators. These tags communicate via wireless signals, requiring additional
then provide the precise or general tag location, allowing auxiliary fans, when equipped with normal starters, two-speed starters or, in some cases, VSDs, to adjust airflow based on equipment type or operational needs in specific headings.
3) Environmental monitoring: Installing sensors throughout the underground mine to track airflow, temperature, and parts per million (ppm) concentrations from contaminants produced by diesel or other equipment enhances ventilation control. Regulations dictate airflow requirements based on diesel equipment horsepower and the presence of contaminants such as carbon monoxide (CO), diesel particulate matter (DPM), nitrogen oxides (NOx) and other hazardous gases. By monitoring air quality continuously, ventilation systems could be programmed to increase fresh air flow automatically when hazardous gases reach critical levels, ensuring a safer work environment.
No matter which ventilation control strategy is implemented, investing in automation enhances worker health and safety while optimizing infrastructure and equipment. The capital cost must be weighed carefully against potential energy savings, the fresh air requirements of different mine areas, production impacts, and the projected end-of-mine life.
Depending on the selected strategies, additional expertise in ventilation or automation may be required to support system upgrades.
Before implementing ventilation automation, a comprehensive assessment of current mining operations and infrastructure is essential to determine feasibility. Key factors to consider include the following:
Energy consumption: Estimating the ventilation system’s current energy use based on the total fan horsepower.
Mine plan: Evaluating long-term development leading to endof-mine life.
Operational schedules: Reviewing shift changes and blasting schedules to identify efficiency opportunities.
Ventilation model: Ensuring fresh air is available when and where it is needed.
Integrating ventilation control strategies is a proven way to lower operating costs, extend equipment efficiency, and gain deeper insights into system performance. It also enhances health and safety by reducing hazardous contaminants and improving real-time tracking of personnel and equipment using telemetry.
By taking a strategic approach, mining companies can achieve a more efficient, cost-effective, and safer underground environment.
Mark Lafontaine is BBA’s Sudbury office director.
ince joining the Ontario Mining Association (OMA) in the autumn of 2024 as president, I have had some time to reflect on its remarkable century-long commitment to bolstering the province’s mining industry. What strikes me is that we find ourselves at an inflection point in 2025 — one marked by unprecedented geopolitical and market challenges, as well as once-in-a-generation opportunities.
Factors such as rising global conflicts, post-pandemic renewal, and geopolitically driven trade defence measures, as well as growing demand for responsibly mined minerals linked to the energy transition, are reshaping the landscape of our sector. Recent global events and an emphasis on Environmental, Social and Governance (ESG) performance indicators have only reinforced Ontario’s competitive advantages: Vast mineral wealth, rule of law, a stable government, respect for human rights, a robust health and safety culture, a diverse ecosystem of service providers, and ample sources of clean energy position the province as a leading mining destination. Ontario was listed as this year’s lowest-risk jurisdiction globally in the MJI World Risk Report, a comprehensive evaluation of mining investment risk featuring assessments of 117 jurisdictions globally. The OMA is seizing this moment to engage proactively with the provincial government and key stakeholders to build on our advantages and carve out pathways for economic growth, placing the spotlight on the mining sector’s pivotal role in Ontario’s economy and ability to drive innovation.
The critical minerals strategy roadmap to success Ontario government has commendably prioritized the implementation of its Critical Minerals Strategy (CMS), which aims to establish the province as a leader in the sustainable production of essential minerals. These metals and minerals are vital for clean energy technologies, the digital economy, defence systems, and advanced manufacturing, among other sectors. The CMS goals are closely aligned with those in the “Driving Prosperity Phase 2” document, which aims to retool the automotive sector for electric vehicle production and facilitate the development of the battery supply chain. Additionally, they align with insights from the Critical Minerals Talent Strategy, released by the Ontario Vehicle Innovation Network, which serves as a roadmap to leverage Ontario’s skilled workforce for building a comprehensive electric vehicle supply chain. The findings in the Advanced Manufacturing Council’s 2024 Final Report further emphasize how Ontario can maintain its manufacturing leadership. This synergetic strategic vision is crucial
for optimizing our complete supply chain — from mining to manufacturing — thereby enhancing economic resilience, creating jobs, and boosting Ontario’s innovation capacity and leadership within the global clean technology landscape. It also underpins Ontario’s newly announced plan to accelerate strategic resource development to build a revitalized Canada-U.S. alliance, dubbed “Fortress Am-Can,” which aims to foster global stability, security, and long-term prosperity.
As Ontario makes clear our ambition to supply allied nations with critical minerals and be a global player in the clean technology market, the OMA applauds the commitment to facilitate electric vehicle infrastructure and production within the province. The investment of over $50 billion in downstream manufacturing over the past few years signals unwavering federal and provincial governmental support. However, existing gaps in funding upstream mining development pose significant challenges that we must collectively address to maintain Ontario’s competitive edge and harness our ability to lead.
While considerable momentum has been building for downstream manufacturing, it is crucial not to overlook the upstream mining operations fundamental to sustaining this growth. To paraphrase Canada Nickel CEO, Mark Selby, just as the farm-totable experience begins with seeding the crop, every step in our supply chain is essential for cultivating sustainable growth and success. While continued growth in the mining sector is critical for our economy, security, and environment, Ontario’s mines and smelters are currently grappling with significant challenges that threaten their profitability and long-term viability in an increasingly competitive market.
Our province is facing intense rivalry from international competitors in base metals markets, particularly given that Indonesia, the world’s leading nickel supplier, maintained ample supply through the second half of 2024, fuelled by a surge in Chinese smelting projects. As Indonesia continues to ramp up its nickel smelting capacity with 44 operations — as of September 2024, a staggering increase from just a decade prior — Ontario’s mines and smelters find themselves in a precarious position. As our major producers compete for global capital for local investment, de-risking new projects or expansions will require a whole-of-government approach to secure those necessary
investments in innovation, operational improvements, and mine life extension. This plan should feature diversified support mechanisms such as competitive energy pricing, strategic tax incentives, and concierge regulatory approvals to fortify the entire mining production spectrum.
The urgency of this initiative is intensifying, especially given the looming threat of potential US tariffs and retaliatory federal measures, which could raise the cost of doing business in Ontario. The challenges are compounded by the geographical remoteness of mining operations in Northern Ontario, which makes attracting talent difficult. Although the mining sector is a lead employer in the North, few employed in the sector are originally from the North, and some are recruited internationally. This means the sector must contend with attracting workers to the Northern region while competing with employers in more accessible locations, closer to where the bulk of the workforce resides. Housing pressures — and costs, even for modular housing — as well as lack of access to healthcare, education, digital connectivity, other essential infrastructure and certain cultural supports in Northern Ontario impede growth in the mining sector, once again highlighting the urgent need for a comprehensive, whole-of-government approach to find solutions. To truly support the industry, current strategies must be bolstered by investments that not only focus on advanced manufacturing but also enhance upstream exploration, mining operations, and processing facilities.
Elevating all commodities, with an emphasis on gold and key strategic minerals
We strongly believe that these government investments will yield significant benefits for all commodities mined in Ontario, particularly for strategically important minerals like gold. Gold serves as a vital hedge against inflation, currency devaluation, and economic uncertainty, especially in today’s unpredictable geopolitical climate. Gold also plays a crucial role in driving innovation and facilitating the transition to a green economy. It is an essential component in modern technologies, used in conductors, switch contacts, soldered joints, and various electronics like smartphones and televisions. In the medical field, gold is transforming diagnostic tools and treatments because of its biocompatibility and chemical stability. Additionally, its applications are expanding in defence and aerospace technologies. Gold mining can be a significant contributor to decarbonizing local economies in other ways. Ontario gold mines have been key in adopting innovative technologies to further decarbonization goals, often serving as the initial catalyst in bringing clean energy systems to remote locations. While the outlook for gold remains optimistic, Ontario mines are currently facing significant challenges, including a lack of a robust workforce pipeline for mining careers, rising labour costs, regulatory uncertainty, and other prevalent industry issues that the CMS seeks to remedy.
Recognizing these challenges, the OMA has proposed that gold be added to Ontario’s critical minerals list, following the precedent set by China and Japan, which are leading the world in recognizing gold as a critical mineral. Meanwhile, we continue to
underscore that Ontario must adopt an inclusive and whole-of-government approach across the mining production spectrum to uplift not just critical minerals, but also other commodities that remain central to Ontario’s economy. This collaborative strategy is crucial not only for enhancing employment opportunities and contributing to GDP, but also for fostering positive relationships with Indigenous communities and enabling us to build out the “Fortress Am-Can” strategic alliance.
Ontario’s mining sector stands poised for growth but requires strategic interventions to bridge the funding gap for upstream exploration, operations (including deep-level mining), and processing of critical minerals. In our 2025 pre-budget recommendations, we stressed the need to strike a better balance when it comes to supporting mineral development to ensure a successful battery and EV production future. Our submission encompasses enhancing geoscience data, bolstering domestic processing abilities and creating resilient local supply chains, reforming regulatory frameworks, and promoting innovation within the industry. Establishing a new Am-Can Critical Mineral Security Alliance is a positive start by the government, but this initiative must bear significant investments in upstream mine development and deliver on expanding processing capacity in the province to ensure the “Made in Ontario” supply chain can deliver on the increasing global demand for critical minerals.
Another significant component in strengthening Ontario’s mining sector is building economic development opportunities with Indigenous partners. We appreciate that the provincial government remains committed to implementing Resource Revenue Sharing (RRS) agreements, but there is a pressing need to broaden the geographic scope of these agreements to engage more Indigenous communities proximate to operating mines. For these agreements to be successful, it is so important for government to support Indigenous communities at every stage of RRS implementation to ensure that communities do not face financial and capacity constraints to a meaningful participation. To truly foster these partnerships, the government also needs to have a coordinated and expedited process to create more certainty with consultation procedures and accommodation, thus helping to reduce risk and move towards strategic mineral development while advancing economic reconciliation.
Furthermore, it is essential to tackle the lack of a robust workforce pipeline required to sustain current mining operations in Ontario and grow production of minerals and metals, in particular critical minerals, required to meet the 21st century demand and the energy transition. In April 2023, the OMA partnered with the Ontario Labour Market Partnerships (OLMP) program to address local economic and employment challenges in the mining sector. This partnership resulted in a
comprehensive labour market assessment and the implementation of a multi-partner information campaign aimed at improving workforce perception among Ontario youth (ages 16 to 28) regarding careers in mining. To date, results of the sustained, coordinated “This is Mine Life” (TIML) campaign have been outstanding. Both for the total reach of over 14 million and the level of engagement — both online and in-person — from youth and their career influencers, including educators, guidance counsellors, and parents. This level of engagement has been amplified with the significant enthusiasm and collaboration from our industry partners and career ambassadors representing our member companies. Moving forward, the OMA aims to sustain the TIML campaign, leveraging its successes and harnessing continued support for further initiatives from government, industry, and non-profit organizations that share similar mandates to address the labour shortage across the mining industry in Ontario and attract investment and people to Northern Ontario.
To maintain Ontario’s position as a global leader in mining, we must adopt a multi-faceted and sustained approach to develop a workforce that is not only aware of the mining industry’s opportunities and challenges but is also passionate about its role in shaping the future of this sector. The transition from a student
Ontario not only attracts but also retains a workforce equipped to excel and maintain our global leadership position in mining. Achieving this goal will necessitate ongoing collaboration and resource sharing among industry leaders, government agencies, educational institutions, and organizations with aligned objectives and a view to a concerted, generational-spanned, long-term approach to bridging the labour gap and creating a robust pipeline of talent that will support continued growth and innovation in Ontario’s mining industry.
As the state of mining in Ontario evolves and the government stresses the need to develop critical minerals, it becomes evident that a collaborative approach across all government levels is crucial for successful implementation of the CMS. National and subnational governments, stakeholders, civil society, and Indigenous communities must be single-minded in purpose to develop our upstream natural resources in a responsible fashion with benefits to local communities, or risk losing control of our supply chains, failing to meet our energy transition objectives, and undermining our national interests.
This concern about unmet objectives and missed opportunities is heightened
by the current competitive dynamics of the global marketplace, which poses significant challenges, including potential international tariffs and the pressing need to secure a reliable domestic supply of critical minerals within North America. To secure Ontario’s position as a key player in the global supply chain, it is essential to cultivate a robust and inclusive mining sector by forging strategic partnerships with Indigenous leaders, facilitating accessible educational programs, modernizing the regulatory framework, creating incentives for investment, and committing to ongoing research and development.
Seeding the way forward
The OMA is dedicated to collaborating with the government to achieve these vital objectives. The trajectory of Ontario mining depends on swift and strategic action —cultivating the seeds sown through the CMS will catalyse a resilient and innovative industry. By developing a robust supply chain anchored in a strong mining base, Ontario stands to not only boost its economic outlook and create safe, well-paying jobs but also set a global standard for responsible mining practices.
| NYSE:SKE www.skeenagoldsilver.com
The surging demand for electric vehicles (EVs) is breathing new life into Ontario’s mining industry. Several critical strategic mineral mines will produce the minerals required to manufacture EV batteries and renewable energy storage for the North American market.
The following are the top critical strategic minerals’ (CSM) mining projects in the development phase:
Canada Nickel is a Toronto-based company that is advancing the next generation of net-zero carbon nickel-cobalt projects with plans to supply the critical mineral to Canada’s EV battery industry. The company’s Crawford nickel sulphide project is the second largest nickel resource and reserve globally, with 3.8 million tonnes of proven and probable nickel contained. The project is expected to be the third largest nickel sulphide operation globally with an annual production of 48,000 t/y nickel, 800 t/y cobalt, 1.6 million t/y iron, and 76,000 t/y chrome during its peak 27-year period, and a total of 1.6 million tonnes of nickel over the project’s 41-year lifespan.
Located in the Timmins Nickel District and covering 900 km2, the project will be a large scale, open pit, bulk tonnage, nickel sulphide operation with the potential for zero carbon production. Canada Nickel’s feasibility study (FS), completed in Nov. 2023, showed that the project has a $3.5 billion after-tax net present value (NPV) (8%), an internal rate of return (IRR) of 17%, increasing to $3.69 billion after-tax NPV (8%), an IRR of
18%, and an initial capital expenditure of $2.70 billion.
The FS also showed that over the project’s lifecycle, it is projected to generate more than $89 billion in revenue, $9.93 billion in federal and provincial income tax, and $3.69 billion in provincial mining taxes, from a total investment of
The company is developing its PAK lithium project, which contains one of North America’s highest-grade, large-tonnage, hard-rock lithium resources in the form of a rare low-iron spodumene and ranks as the second largest lithium deposit in Ontario by size. In March 2024, Frontier Lithium
Located in the Great Lakes Region and covering 270 km2, the PAK project will develop a fully integrated lithium mining and processing operation featuring two primary deposit areas: the PAK deposit and the Spark deposit. The proposed mine site will include two open pits, rock storage areas, a concentrator plant com
The project has received a total of $6.1 million from the Critical Minerals Infrastructure Fund for a mine access road and power transmission line infrastructure (two investments for two projects). The project has the potential to become North America’s lowest-cost lithium chemical production facility.
In 2023, Frontier Lithium conducted a pre-FS which showed that its PAK lithium project will deliver a post-tax NPV (8%) of $2.2 billion, a post-tax IRR of 24.1%, with a capital expenditure of $608 million for phase 1 (the mill and mine) and $749 million for phase 2 (the refinery).
All environmental baseline studies for the mine and mill were completed in Nov. 2024, with final reports expected over the next couple of months. The company continues exploration drilling, regional mapping, and technical de-risking of the integrated flowsheet.
International Lithium Corp. (ILC) is a Canadian lithium exploration company that acquires and advances lithium properties and critical mineral projects.
CREDIT: INTERNATIONAL LITHIUM
The company’s Raleigh Lake project is a relatively small lithium deposit consisting of spodumene. The project is unique in that it contains a significant and highly concentrated rubidium deposit within but separate from the lithium deposit in the mineral microcline. The resource estimate for the lithium in spodumene is approximately six million tonnes at 0.6% Li2O or 600,000 tonnes of spodumene concentrate.
Located 25 km west of Ignace, the project consists of a proposed open pit mining operation, with a mine life of nine years and an expected production rate of 56,000 t/y of spodumene concentrate. The mining of the spodumene will eventually unearth the self-contained rubidium deposit consisting of approximately 1,400 tonnes of Rb2O.
The results of the preliminary economic assessment (PEA) reported in Dec. 2023 that the project had a post-tax NPV (8%) of $342.9 million, a post-tax IRR of 44.3%, and a capital expenditure of $111.9 million. The PEA was based solely on the production of spodumene concentrate and does not consider the
economics of the rubidium deposit.
Currently, ILC is moving forward with its FS. Phase 1 metallurgical test work proved lithium recoveries were above 81%. Phase 2 metallurgical test work will consist of collecting a bulk sample and optimizing the results as determined in Phase 1.
ILC says because there is no large capital investment required for infrastructure development for the project, much of the work generally required for an FS does not need to be conducted for this project. However, the company has made an application to convert its mining claims into mining leases, and it has begun the baseline environmental work required for the submission of a mining permit application.
According to ILC, the lithium market will factor in any decisions regarding production at the Raleigh Lake project. The project can be fast tracked to production owing to its location within existing infrastructure. Once a decision to proceed with production is made, the mine will take approximately two years to fully permit and construct. If a decision was made in 2025 to proceed, production would commence in 2027 or 2028.
Northern Graphite: Bissett Creek project
Northern Graphite is a Canadian junior mining company engaged in the production, exploration, and development of mineral resource properties. The company is focused on producing natural graphite and upgrading it into high-value products including anode material for lithium batteries and EVs, fuel cells, and graphene.
Northern Graphite’s goal is to become an integrated, mine-tobattery producer of graphite by expanding production at its existing mine, bringing a second mine onstream in 2026, and advancing two large scale projects towards development while also developing down-stream capacity to produce anode material for lithium batteries and EVs.
Northern Graphite is the only significant producer of natural graphite in North America and its Bissett Creek graphite project is the only graphite project in the province. Graphite is the largest component of lithium batteries used in EVs. Once in production, Bissett Creek will be a main supplier of graphite to Northern Graphite’s planned battery anode material plant in Baie-Comeau, Que. The plant, located with easy access to North America’s gigafactory belt, will process graphite from the company’s mines into 200,000 t/y of battery anode material,
enough to supply four 50 gigawatt gigafactories, and build 2.5 million lithium batteries.
Located between North Bay and Ottawa, the project will be built as a staged, two-phase development that is synced to market demand, and will have a mine life of 23 years. The project has 1.2 million tonnes of graphite in measured and implied resources, initial production will be 44,000 t/y in phase 1, with a capital expenditure of $155 million.
Northern Graphite completed its FS, and all permits are expected to be received, pending funding, in 2025. The company expects to make a construction decision sometime in 2025, with a construction start date of 2026 and first production anticipated in 2027.
Our commitment to you, our customers, is guided by three words; SAFETY, SERVICE, and INNOVATION. We are constantly moving forward creating products of the highest quality and providing you with the services which make the impossible possible. Our ability to provide our customers a complete range of complementary products and services ensures quality, efficiency and availability resulting in reduced costs, reduced lead times and increased customer satisfaction! From our Engineers to our Technical Sales Representatives we work tirelessly with you to ensure your safety is at the forefront. We will be with you every step of the way.
CANADA LOCATIONS
Sudbury, ON, CANADA (705) 525-0101
Rouyn Noranda, QC, CANADA (819) 797-3866
GLOBAL HEAD QUARTERS Pittsburgh, PA, USA (412)-963-9071
For more information on our portfolio of diverse and complementary brands visit us at www.jennmar.com
Rock Tech Lithium: Georgia Lake lithium project
Rock Tech Lithium is another Canadian mining company that develops lithium properties. The company’s focus is to develop and optimize battery-grade lithium hydroxide monohydrate with a goal to create a closed-loop lithium production system.
The mining and processing operation of Rock Tech’s Georgia Lake lithium project will produce 6% lithium concentrate for a planned lithium hydroxide converter in Red Rock. The operation will use a combination of open pit and underground mining over five deposits, with mineral processing that involves crushing, dense media separation, and flotation.
The project is located 160 km northeast of Thunder Bay. The project covers 67.28 km2 and will include open pit mining, underground mining, a concentrator, a water treatment plant and a tailings storage facility. The project has a mine life of nine years and an expected production rate of one million t/y of lithium concentrate.
The results of Rock Tech’s pre-FS completed in Nov. 2022 demonstrated mineral reserves totaling 7.33 million tonnes at an average grade of 0.82% Li2O and a recovery rate of 80%, a post-tax NPV (8%) of $190 million, a post-tax IRR of 35.6%, and total capital expenditures of $378 million.
The project was awarded conditional approval of funding for up to $1.4 million under the Critical Minerals Infrastructure Fund for its Fairloch Lake access road project, which involves constructing a new 10-kilometre access route from the TransCanada Highway to Rock Tech’s Georgia Lake Mine.
Rock Tech has plans for a drilling program across its six deposits, including its newly discovered East Conway. The primary goal of this program is to expand the overall mineral resource, upgrade the resource classification to measured and indicated, and integrate the findings into a future definitive feasibility study (DFS).
The company is working on further engineering and permitting activities for this project which is required to progress to the next stage and prepare for eventual construction and operation.
Rock Tech expects to decide on this project by the end of 2025. If approved, construction of the project is expected to occur between 2025 and 2027, with first production anticipated in 2028, in line with its planned converter commissioning.
One last Canadian exploration and development mining company in this report is Tartisan Nickel Corp., which is also focused on mining battery metals.
The company’s flagship project is its wholly owned Kenbridge nickel project. Totaling 42,73 km2, it is located in the Kenora Mining District in the northwestern corner of Ontario. The project is focused on nickel, copper, and cobalt.
The results of Tartisan’s PEA, dated July 2022, were based on an underground operation. With an initial nine year mine life and operating at 1,500 t/d, it would use conventional processes to produce a nickel/copper concentrate. The measured, indicated, and inferred mineral resource estimate to date, both potentially open pit and underground mining potential totals, are 146 million lb of nickel, 78 million lb of copper, and two million lb of cobalt. The expected capital expenditure is $134 million.
Tartisan’s 2025 drilling program expects to bring one million tonnes of inferred nickel at 1% into the indicated category as well as test significant geophysical anomalies indicated from the 2021-2022 drilling program results. The company also plans to drill deeper below the 900-metre level.
A magnetotellurics (MT) mobile airborne survey is scheduled to be flown over the Kenbridge nickel project in May 2025. The results of this survey should promote additional drilling targets and a better overall understanding of the newly acquired land. Tartisan anticipates a post-2025 drilling update to the mineral resource estimation (MRE) which should improve overall project economics and mine life. Environmental metallurgical work should be completed by spring 2025.
Diane L.M. Cook is a freelance mining writer.
Alamos Gold was formed in 2003 through the merger of Alamos Minerals and National Gold. The company seized on key acquisitions during the gold price trough from 2015 to 2017, securing Young-Davidson in Ontario, Lynn Lake in Manitoba, and Island Gold.
Last summer, Alamos Gold announced the acquisition of Argonaut Gold and its past-troubled Magino mine in northern Ontario in an all-share deal valued at US$325 million to become Canada’s third-largest gold producer. The acquisition gives Alamos a fourth long-life producing asset in addition to its two mines in Ontario — Young-Davidson and Island — and Mulatos in Mexico. The company also has the Lynn Lake development project in Manitoba, which received federal environmental approval in 2023, as well as others in Turkey and Oregon.
The Island Gold District is comprised of the adjacent Island Gold and Magino mines, two long-life operations with a large mineral reserve and resource base and significant exploration upside. Island Gold is an underground mine and one of Canada’s highest grade and lowest cost gold mines. Magino is a large open pit mining operation located within 300 metres of the Island Gold deposit. The combination of Island Gold and Magino will create one of the largest and lowest-cost gold mines in Canada.
From the transaction, Alamos hopes to create US$515 million in cost-savings over about two decades of production from Island Gold and Magino mines. Alamos plans to use Magino’s larger mill and tailings facilities instead of Island’s.
“Through our acquisition of Argonaut, we have further
enhanced our unique positioning as a Canadian focused, intermediate gold producer, with growing production and declining costs. The integration of Magino and Island Gold is expected to unlock significant synergies using shared infrastructure. Together, they will create one of the largest and lowest cost gold mines in Canada with significant longer-term expansion potential supported by their long mine lives and ongoing exploration success,” said John McCluskey, president and CEO of Alamos Gold.
Mr. McCluskey explained that after the addition of Magino mine, the company did not have to build a new mill for the phase 3+ expansion. There was also no need for tailings lift for the existing tailings facility, which saved about US$20 million in costs.
In 2024, the company invested $19 million for exploration at Island Gold, up from $14 million in 2023. The company’s goal was to define new mineral reserves and resources in proximity to existing production horizons and infrastructure.
Combined with lower costs, the company achieved a record free cash flow of $106.9 million in the second quarter (Q2) of 2024, up more than 300% from the first quarter of the same year.
Soaring gold prices helped Alamos deliver a record revenue of $332.6 million in Q2, a 27% year-on-year increase. “We remain well-positioned to achieve full-year guidance and deliver significant production growth at declining costs over the next several years,” said McCluskey.
The third quarter (Q3) marked the first reporting period with the Magino mine under Alamos ownership. During Q3 of 2024, Alamos delivered record production of 152,000 oz. of gold. The company attributed the production boost to the Magino gold mine
as well as the added production from the Mulatos mine in Mexico.
Alamos Gold plans to release its fourth quarter and year-end 2024 financial results after market close on Feb. 19, 2025.
Phase 3+ expansion also continues in the Island Gold project. The company reported recent progress on the shaft sink, with the shaft past a depth of 800 metres in Nov. 2024, doubling its depth from the end of the second quarter. This is more than halfway from its goal of 1,373 metres. Completion of the shaft will drive production higher, costs significantly lower, and allow Alamos to unlock additional highgrade resources at depth.
According to Mr. McCluskey, completion of the phase 3+ expansion in 2026 is expected to push the company’s annual production rate closer to 700,000 oz. per year and decrease the all-in sustaining costs to $1,150 per oz.
“The addition of Magino mine compliments the company’s strong growth profile and has enhanced our strong outlook, increasing our near-term production rate by approximately 20% to 600,000 oz. per year, and providing longer-term growth opportunities
through expansions of the Island Gold District. We are making excellent progress on our growth projects with the phase 3+ expansion more than halfway complete,” McCluskey said.
Island Gold has established itself as one of the highest-grade and fastest growing deposits in the world, with the main structure open laterally and down-plunge, and significant high-grade results being intersected within emerging and yet to be defined zones in proximity to the main structure.
Over the past year, the drilling program at Island Gold has been one of the most successful in terms of the magnitude of high-grade intercepts across the lateral extent of the main deposit and within the numerous newly defined hanging wall and footwall zones. In 2024, company drilling teams completed 50,416 metres of underground exploration drilling in 185 holes, relative to a goal of 41,000 metres. Alamos also completed 9,849 metres of surface exploration drilling in 11 holes. McCluskey expects this to drive a ninth consecutive year of growth in combined mineral reserves and resources, with grades also increasing over that time frame.
Dynasty Gold has two gold assets in the most desirable mining camps in North America. The first is the Thundercloud property, which is in the Archean Manitou-Stormy Lakes Greenstone Belt in Western Ontario, 47-km southeast of Dryden, and has a geological setting similar to the Abitibi Belt but much less explored. Dryden is a resource-based town with excellent infrastructure necessary for mining operations. Several large scale mining operations in the area include New Gold’s Rainy River mine, Evolution Mining’s Red Lake Gold mine (150 km to the north), as well as the Canadian Malartic Hammond Reef deposit by Agnico Eagle and First Mining Gold’s Springpole deposit. Dynasty’s second property is Golden Repeat, which is strategically located in the prolific Midas region of Elko County, Nevada.
The company is advancing its 100%-owned high-grade Thundercloud gold project, acquired from Teck Resources in 2021. Notable deposits in the area include the Rainy River mine, Hammond Reef deposit to the south, and the Goliath deposit to the north. Kenorland’s ground adjoins Thundercloud to the north. The project is connected to highways, rail, and power.
The first bonanza drill hole results, released in Jan. 2023, returned 8.4 g/t gold over 73.5 metres, from its four-hole maiden drilling at the Pelham zone. Another hole returned 6.0 g/t over 34.5 metres. Both holes are within 250 metres of surface. These are the best drill intersections reported in the area, putting it on the map as an “Emerging Gold Camp.” In 2023 and 2024, the company continued to intersect many high-grade and/or long-intercepts within 200 metres from surface. For example, 70.5 metres of 3.2 g/t, including 11.0 g/t over 12 metres; lower grade, longer intercept of 1.0 g/t over 163.5 metres, including 8.8 g/t over 7.5 metres; and 94.5 metres at 1.61 g/t, including 42 metres of 3.03 g/t. These results attracted Rob McEwen, who is now the largest shareholder, owning 9.7% of Dynasty Gold.
The 2-km mineralized zone in Pelham zone is associated with pyritic veining within an east-west trending structure.
Currently, only 400 metres have been drilled producing a string of impressive hits. A three-dimensional resource model was generated based on the drill data and Teck’s historical data of a total of 17,000 metres of drilling. At a 3.03 g/t cut-off, the model produces 232,000 oz. gold at 8.04 g/t; and at 0.5 g/t cut-off, it is 439,000 oz. at 2.14 g/t, open pit resource of which 85% is in measured and indicated category. Most of the mineralized zone (80%) remains undrilled.
Crew (geologists and geo-technicians) outside core logging workshop.
In 2024, a new mineralized zone was discovered by drilling 1 km south of the Pelham zone. The first hole ever drilled in this area returned 6 metres of 2 to 3 g/t gold, within a wide zone of 22.5 metres at 0.8 g/t, 6 metres from surface, opening a new exploration area. This drill hole was designed to target induced polarization (IP) chargeability high, similar geophysical features were found to correlates to high-grade gold in the Pelham zone. The company believes that this new mineralized zone could be another Pelham zone. Roman Shklanka, PhD, a mining veteran and a director at Dynasty Gold, believes that the Pelham zone and the new zone belong to one big mineralized system, pending further drilling to connect both zones.
With a fully funded 2025 exploration program, Dynasty Gold plans to be on the ground in the spring, when weather permits, to start drilling in the newly discovered zone. Additional drilling is also planned at the Pelham zone to delineate the ~2-km mineralization. It is exciting that 95% of the property remains undrilled, leaving a large area to explore and build up the resources.
Ivy Chong is president and CEO of Dynasty Gold Corp.
Harlsan Pty Ltd, a leading supplier of premium drilling equipment since 1992, continues to deliver innovative solutions that enhance drilling efficiency, globally. Recently, they shared impressive productivity gains achieved by their customers, supported by compelling performance data.
Our gear is world-leading, and we offer game-changing reliability and robust efficiency,” says Matt Bevan, General Manager of Harlsan. Based in Western Australia, the company leverages extensive experience both on-site and in the equipment design space, to improve operations, team safety, and profitability. He continues: “Putting Harlsan gear on your rig will drive up productivity and output – we have the data to support this”.
Choosing an RC drilling supplier can be challenging, with varying priorities such as service, price, and quality. To showcase their edge, Harlsan recently shared examples of their reliable, low-maintenance equipment in action. (Detailed case studies are available at harlsan.com.au/case-studies.)
In one instance, a major global industry player faced maintenance issues with their rig setup, including top swivel failures, blockages, and downtime. Harlsan was brought in to help and they introduced an efficient, simplified bottom swivel design, reducing costs and non-productive time. The Harlsan Flotec® hydraulic blow down system, which clears blockages with a simple switch, resolved drill string blockages swiftly and minimized interruptions.
Smooth, continuous operations resumed. Rigorous performance comparisons conducted by this customer revealed significant advantages with a Harlsan setup:
• 31% more drilling hours
• 93.85% equipment availability
• 15-fold decrease in lost shifts
• Maintenance hours cut by over 50%
• 94% reduction in head maintenance hours.
Encouraged by these outcomes, they transitioned all their rigs to Harlsan setups.
Rig setup optimization is critical for maximizing productivity. Harlsan Director Harley Hollier emphasizes the importance of reliability: “Our customers know what it means to have a rig down, and we do too. Reliability drives the bottom line.” Harlsan’s equipment undergoes rigorous checks (including, for example, hardened and calibrated master gauges to ensure thread precision) – one of the reasons they have cemented their reputation for reliability and efficiency.
A standout example is Harlsan’s Wearlok ® wear bend, designed for durability and ease of maintenance. Its extended wear-life reduces the need for frequent checks, while a simple two-bolt removal mechanism makes maintenance far simpler, minimizing time spent at height. The results are reduced non-productive time, improved team safety, and longer service intervals.
Customers consistently cite Harlsan’s exceptional service, premium products,
and innovative solutions as key reasons for their loyalty. The global RC drilling industry’s evolving demands require adaptable and practical equipment - a hallmark of Harlsan’s approach.
“By closely collaborating with our customers and applying our in-field expertise, we are able to deliver practical and reliable solutions to enhance operational efficiency”, explains Harley, who brings over 20 years of experience optimizing rig performance and tailoring solutions.
Harlsan also believes that tradition shouldn’t stand in the way of innovation— there’s always a better way to do things. The management- and design teams work together with customers, developing practical solutions that will reduce costs and non-productive time, with minimized rig changes.
Manufactured in Australia and shipped globally, Harlsan’s products continue to enhance operational efficiency worldwide. Matt Bevan and Harley Hollier will attend the PDAC event in Toronto this March. For inquiries, email info@harlsan.com.au or visit their website: harlsan.com.au.
Harley Hollier, Director at Harlsan outlined the ease of shifting to a Harlsan setup: “We work closely with customers every step of the way to ensure a seamless implementation. Feedback from the field is that our game-changing setup is simple to integrate and continues to increase operational reliability.
Matt Bevan, General Manager of Harlsan, explained, “Our world class equipment and innovative engineering solutions have always come together to optimize customers’ rig profitability. But now we have also gone one step further, making ongoing maintenance quicker, safer and easier.
Harlsan’s full setup is proving that drilling efficiency can be achieved, regardless of ground type, bringing significant cost-savings, and improved rig reliability.
Over the past few years, the discourse around critical minerals has largely been framed as a cornerstone of the electric vehicle (EV) revolution and the broader energy transition. Governments and industries emphasized their role in creating greener economies, fostering innovation, and combating climate change. However, in the last six months, this narrative has undergone a gradual shift. Conversations once dominated by sustainability and clean energy are increasingly infused with themes of national security, geopolitical strategy, and economic sovereignty.
This evolution reflects the growing realization that critical minerals are not just essential for a sustainable future but are also pivotal to the stability and competitiveness of nations in an increasingly fragmented global milieu. As tensions escalate between major powers and supply chains face unprecedented vulnerabilities, governments are reconsidering their approach to these resources. Countries like Canada and the U.S. are no longer merely talking about critical minerals as a pathway to EVs or renewable energy systems but as a means of safeguarding strategic industries, defending against supply chain disruptions, and supporting defense capabilities and readiness.
What is driving this shift in focus, and how is it shaping policy decisions and investments, and what does it mean for the mining sector, particularly in resource-rich regions like Ontario? Does this new framing elevate the critical minerals agenda? Or does it risk sidelining the green energy narrative in favour of heightened geopolitics? As governments pivot their rhetoric and strategies, the question arises: How does this redefinition of critical minerals impact their role in shaping the future?
In Ontario, critical minerals have taken centre stage in discussions about both economic resilience and national security. Premier Doug Ford has emphasized the province’s pivotal role in ensuring a stable supply of these resources, vital for advanced technologies, clean energy, and defense applications. Through initiatives like “Fortress Am-Can,” Ford aims to accelerate the development of resources in regions like the Ring of Fire, positioning Ontario as a strategic partner in the Canada-U.S. critical minerals alliance. Speaking to the broader implications, Ford has highlighted that Fortress Am-Can can achieve energy security to power economic growth for both nations, underscoring the importance of reducing reliance on countries that do not share democratic values or align with national security priorities. Furthermore, Ford has not shied away from addressing trade tensions, proposing retaliatory measures such as restricting critical mineral exports to the U.S. in response to potential tariffs. “We have to retaliate hard against our friends south of the border, which is unfortunate,” Ford remarked, emphasizing Ontario’s readiness to safeguard its economic interests. These statements reflect a growing alignment in Ontario’s policy rhetoric with themes of security, sovereignty, and strategic collaboration, reshaping the narrative around critical minerals beyond the energy transition.
At the federal level, Canada’s approach to critical minerals has evolved over recent months. Initially framed within the context of the energy transition and the push for electrification, the narrative has shifted toward emphasizing supply chain localization and national security. This change reflects growing geopolitical tensions and the recognition of vulnera-
bilities in global supply chains. Natural Resources Minister Jonathan Wilkinson has also described the strategic importance of these resources as being strategic assets that contribute to Canada’s prosperity and national security. Similarly, Innovation, Science, and Industry Minister François-Philippe Champagne has reinforced this focus by implementing policies aimed at protecting Canada’s critical mineral sectors from foreign state-owned enterprises. He has stressed the need for continued direct foreign investment, while guarding against threats to our national security, and our critical minerals supply chains. These statements highlight how the federal government is prioritizing strategic autonomy and economic resilience, shifting from a focus on green energy to a broader agenda that aligns with global security concerns. This pivot marks a recalibration of priorities, aiming to ensure Canada’s critical minerals are leveraged not only for climate goals but also to strengthen the nation’s geopolitical standing.
Ontario’s critical minerals sector stands at a pivotal juncture, with its significance extending beyond the EV industry to encompass broader economic and national security concerns. While the EV market remains a substantial driver of demand for these minerals, other sectors are rapidly emerging as key consumers. Energy storage, for instance, is poised to experience significant growth. According to McKinsey & Company, the global battery energy storage systems market is expected to reach between $120 billion and $150 billion by 2030, more than doubling its current size.
Beyond energy storage, critical minerals are essential for the development of advanced defense technologies, telecommunications infrastructure, and renewable energy systems. This diversification underscores the strategic importance of Ontario’s mineral resources in bolstering both economic resilience and national security. As global demand for these minerals intensifies, Ontario is well-positioned to leverage its rich deposits to meet the needs of various high-growth industries, ensuring a prosperous and secure future for the province. What remains to be seen is how
this shift in narrative will impact public opinion and support for the mining sector and critical minerals which has been dealing with an image problem for decades. Will the shift in focus from cleaner and greener future to sovereignty and self-preservation resonate more deeply with the public? While traditional environmental and social concerns surrounding mining persist, the emphasis on national security and economic independence might redefine how communities perceive the value of
mineral development. If effectively communicated, this narrative could not only reinforce industry support but also encourage more widespread acceptance of the sector’s role in shaping a secure, sustainable future. In fact, the renewed pressure that comes with this shift in message might just be the catalyst for accelerating the development of new mining projects across Ontario.
Steve Gravel is the manager of the Centre for Smart Mining at Cambrian College.
Reliable measuring results for extreme process conditions
Whether level, limit level, density, interface or mass flow: Radiation-based process instrumentation delivers precise measuring results in industrial production and handling processes, and that even under the most difficult operating conditions. Flexibility through detector variety: You can choose between different types of detectors. Detector can thus be optimized for widely different applications becoming the specialist for your particular measuring task.
Advantages
Simple mounting and operation
Maintenance-free operation
Easy adjustment
Self-monitoring and diagnosis
Developed acc. to IEC 61508
Compact device with integrated inputs for temperature or belt speed
Electronics
4 … 20 mA/HART
Profibus PA
Foundation Fieldbus
Display and adjustment module
PLICSCOM
VEGACONNECT and DTM
VEGA Tools app Housings
Aluminium
Energy is on the minds of policymakers worldwide. In South Africa, while we may be at the first stage of failure of loadshedding, the government and broader society continue to keep a watchful eye on the energy supply. It is ironic, or perhaps opportune, that loadshedding occurred at a time when the world began pivoting away from fossil fuels to cleaner forms of energy in earnest and despite machinations of a revision to fossil fuels, this trend looks to continue here and abroad. With South Africa remaining the continent’s highest energy user, its first-mover approach to clean fuels has seen it secure a seat among the continent’s clean energy leaders. But this is no time to rest on proverbial laurels.
On the international stage, the primary pivot has been driven by decarbonization, the declining cost of clean energy such as solar and wind power, and ESG becoming part of the status quo from a corporate governance perspective.
A notable impact of the world’s changing energy supply mix is seen through ramifications on the mining sector, which is responsible for providing the commodities needed to manufacture the materials that underpin the transition to cleaner energy, such as batteries, turbines, and solar panels. Africa is a crucial player in this regard. It houses 55% of the world’s cobalt, 47.6% of manganese (with South Africa leading the way), 21.6% of natural graphite, and just under 6% of global copper, and nickel reserves. Large lithium deposits can also be found in countries such as Zimbabwe and the Democratic Republic of Congo. Coincidently, mining is at its core an energy intensive industry as well. The extraction and processing facets, coupled with logistics and supply chain (often to and from some of the remotest regions on the continent) means that mining is, simultaneously, essential to the production of sustainable energy solutions while being one of the largest likely users thereof.
In the past, foreign mining companies were focused on extracting minerals from the continent, with surrounding communities and the broader national interest of African countries being second tier considerations. Today, there is growing recognition that the mining industry can no longer adopt an explore, extract, and export mindset. The shadow of these practices continues to fall over the industry despite marked attempts to shake this bad actor mantel by making concerted and tangible differences. Real beneficiation and environmental, social, and governance (ESG) are now firmly part of any conversation, with mining companies expected to engage with and benefit the communities surrounding their operations.
Mining companies are not solely responsible in this respect. The communities and the governments that host them play crucial roles in moderating how mining can benefit local communities and the state while at the same time supporting and
creating the enabling environment which would enable the realization of a truly reciprocal and mutually beneficial relationship. The question of who wins as the world transitions to a just energy supply is therefore the wrong question. Winning denotes that there is to be a loser. To create the sustainable energy and mining future we all desire, there can be no losers, and the focus should be a matter of balance.
Real beneficiation starts with authenticity and treating communities with respect
To speak about beneficiation means thinking about whether the mining sector and governments have been successful in the past. The general answer is no, though there are outliers. The Royal Bafokeng Nation in the North West is one, with the Debswana agreement between the Botswanan government and De Beers being another. However, a cursory study of mining’s history in places ranging from Cote d’Ivoire and the Democratic Republic of Congo to South Africa itself suggests that too few benefited as minerals were extracted from the continent.
A vital starting point for true beneficiation is whether the mining company involved is authentic in its intentions to spread the benefit of its operations beyond the confines of the mining site fence and if it has a vision of what real beneficiation looks like. If a mining operator only approaches ESG and beneficiation to tick the necessary boxes, long-term sustainable beneficiation is stranded at the starting line.
The mining companies that have beneficiation rights have been those that are highly intentional in collaborating with the local community. They recognize not just the public relations and reporting value of beneficiation, but the visceral operational benefits of building beyond the life cycle of the mine.
One benefit is protection from bad actors within the community who represent the greatest threat to operational continuity
and employee safety. For example, in South Africa, the phenomena of the construction and other extortion type-mafias thrive best in communities where they are allowed to operate and spread misinformation, a push-and-pull dynamic.
Based on our clients’ experience, if a local community is given a real seat at the table where decisions are made around a particular project, are treated with respect, and provided with real and tangible opportunities, the community will endeavour to expel these bad actors. The costs of associating with extortionists are far higher than working with mining operators, who, in a best-case scenario, show themselves to be genuine actors.
A separate benefit is enhanced labour relations. A workforce that can objectively see the work done by a mining firm to improve their standard of living is far more willing to listen at the negotiation table than those who feel neglected and exploited.
For example, a mine requires transport infrastructure to move people and materials in and out of the facility. Expanding this infrastructure by a fraction above the needed cost can make an exponential difference in the lives of those who work and live around a mine. Real beneficiation at its heart is as much about building relationships and trust as it is about sharing the benefits of built infrastructure.
Creating an enabling environment for beneficiation should be the role of the state As much as beneficiation occurs between local communities and mining operators, government attitudes and policies are crucial in whether beneficiation is successful at a national and industry level.
From a policy perspective, the state has the tricky task of balancing regulation and creating an enabling environment for foreign and local investment. The more heavy-handed a state is from a regulatory perspective, the easier it will be for investors and mining companies to look for calmer waters. However, a laissez-faire approach will invite abuses because of the nefarious and creeping nature of unchecked power.
Furthermore, a government may put in place legislation and policy that is outstanding in theory but never enforce or
implement it as envisaged. Zimbabwean law, for example, is based on sound jurisprudence, but enforcement and implementation are either non-existent, piecemeal, or skewered to suit specific interests.
Africa’s influence in the global mining industry is expected to grow in line with mineral needs to drive the energy transition. If African states are to make the most of this opportunity, governments should seek to collaborate with the mining industry and their constitu-
ance, shared interest, and creating an environment where all parties can benefit simultaneously.
The 2025 Mining Indaba theme: “Futureproofing African mining, today,” highlights the pivotal role of Africa in shaping the global energy transition.
Tyron Theessen and Megan Jarvis are partners at Webber Wentzel. Different versions of this article might
Learning Center provides online, around-the-clock access to a variety of training modules, webinars and Zoom sessions.
We also offer an extensive curriculum of in-person classes conducted by factory-trained professionals. All are provided to mitigate cleanup costs, potential risks to workers, premature equipment failure, and unexpected downtime.
Like diamonds, the mining industry is under immense pressure. The demand for the mining industry to continually boost safety and productivity is ever-growing, and one small slowdown can cost millions in revenue. To put this in perspective, only a 2% improvement in margin for the top mining players worldwide would drive over $19 billion in new mining profits.
Economic pressures aside, global warming is also challenging mines to stay sustainable while also maintaining profitability, a challenging feat to accomplish. According to ABB, 30% of mines are falling short of their decarbonization goals.
The demands for productivity and sustainability make keeping tabs on efficiency and safety of the utmost priority. But manual 24/7 monitoring of complex processes, large equipment, and dynamic environments is time-consuming, prone to error, and dangerous. Luckily, artificial intelligence (AI)powered automation and computer vision can resolve these challenges and accelerate the progress of mines.
Computer vision is poised to transform the industry by providing real-time, visual insights into the entire mining lifecycle all the way from mineral processing to worker safety and site security. It elevates productivity, safety, and sustainability
across the entire value chain to proactively address issues as they happen and offer optimization opportunities. Computer vision is undoubtedly the future of mining.
At a high level, computer vision is a subtype of AI that detects objects, people, and events in real-time, providing actionable data to improve operations. Leveraging neural networks and machine learning (ML), computer vision allows computers to analyze and understand the environment around them. The technology can be easily integrated with existing cameras and complements the sensor and machine vision technology already present in the mining market, such as temperature and pressure sensors, robotics, and advanced machinery.
Because computer vision gathers real-time data that is more accurate than what manual monitoring can achieve, it is both resource and cost-effective over time. It helps operators address slowdowns, resolve safety violations, detect anomalies, and target inefficiencies immediately. Computer vision is the “practical” subset of AI that leaders across all industries are using to see transformative impact and ROI from.
Computer vision transforms logistics, health and safety, environmental monitoring, and site security of mines — boosting productivity and sustainability. It allows mines to keep up with the industry’s demands, while remaining profitable and scalable.
Because of the constant safety concerns, labour shortages, environmental pressures, and tight timelines faced by the mining industry, computer vision is truly revolutionary.
Drilling and excavating
An unplanned drill and excavator downtime on mine sites is detrimental for profitability and productivity. One small slowdown or machine breakdown can cost thousands in lost revenue, but this is where computer vision comes in.
Computer vision can detect worn or broken drill bits and shovel teeth, monitor drill and excavator activity, and track drill and excavator performance in real-time — boosting pro-
data, eliminating manual bottlenecks and better allocating resources. This in turn helps reduce unnecessary emissions.
But how? Computer vision can monitor truck cycle timing, detecting any queues or idle trucks without loads. It can track ore and waste dumps to ensure no valuable ore is placed in a waste dump and vice versa. It can detect the loading (and misloading) of haul trucks, alerting management if any ore is placed incorrectly. It can prevent collisions between trucks, personnel, and equipment in busy open pit mines by tracking truck paths, identifying hazards in real-time, and alerting drivers or triggering autonomous braking.
Computer vision can also track machine status to resolve any slowdowns or breakdowns. It ensures key processes like haul, muck, and load activity are optimizing ore clearance and offers suggestions for future improvements through predictive and prescriptive analytics.
The technology provides real-time alerts for any bottlenecks, delays, or machine and labour slowdowns, so operators can
ing operations, when valuable ore is gathered and separated
Computer vision can surveil conveyor belts in real-time and alert for any mechanical failures, tears, blockages, and spills. It vent unnecessary downtime and processing from being
slowed. Particle size distributions can be analyzed, preventing any oversized pieces from being passed further along in the mineral processing process.
Computer vision provides real-time alerts for any processing issues, so mines don’t forfeit precious time (and revenue). It automates inefficiency identification, so productivity is maximized and processing workflows streamlined.
Mining jobs are some of the most dangerous and injury-prone, so monitoring workers’ safety is essential. Furthermore, investors and customers are prioritizing environmental, social, and governance (ESG) factors more than ever before, with employee safety being a key focus.
Maintaining workforce safety while also scaling operations can be complex, but computer vision offers a solution. This technology can ensure personal protective equipment (PPE) compliance by automatically monitoring gear and alerting management of any workers not adhering to correct safety protocols. This can be done in tandem with facial blurring to protect worker privacy, solely alerting management to visit the scene and address any issues as quickly as possible.
Computer vision can prevent safety breaches by monitoring hazardous zones as well. If workers enter restricted or unsafe areas, real-time alerts can be sent to mine operators to resolve breaches before they have the chance to potentially escalate. Fires, spills, and leaks can also be detected in real-time to proactively address safety and environmental hazards.
Computer vision’s automated monitoring allows mines to get real-time alerts for any issues that occur to keep their workers protected and comfortable.
As sustainability and ESG demands rise, tracking the environmental health on and around mine sites is important for protecting workers’ safety, wildlife, and the mines’ reputations. Mines are also facing stricter environmental regulations than ever before, requiring immediate compliance to continue operations.
Computer vision can help tackle these pressures. This technology can monitor and count fauna to keep tabs on the environmental health around a mine site. It can also lower a mine’s environmental footprint by automating key sustainability processes like waste monitoring and energy management to reduce emissions and resource usage.
For example, it can detect any water discharge anomalies to prevent pollution and costly fines. By tracking the distribution of tailings material, any unplanned accumulations can be identified to protect the dam wall.
Computer vision provides real-time alerts for any environmental issues so they can be promptly addressed, and mines can stay productive.
Mine sites are large, targets of theft, and difficult to keep tabs on at all times. Traditional manual monitoring is both expensive and prone to error.
Thankfully, computer vision can help automate and protect site security, monitoring a mine site’s perimeter and sending real-time alerts for any unauthorized breaches or theft, so security can quickly respond to issues. Cameras placed around a mine site perimeter can detect any security breaches, and cameras placed around restricted areas and precious resources can alert for any pilfering and theft.
Computer vision’s real-time insights secure sites and valuable materials, while also protecting worker safety and keeping ESG goals a priority.
Computer vision is key for mining enterprises of all sizes because it is practical. It shows leaders what is happening in their business as it happens — acting as a digital superintendent. It offers the actionable data needed to make immediate sustainability and operational improvements and stay ahead in such a competitive industry.
Building successful computer vision solutions is complex and time intensive, but end-to-end platforms exist where you can build, deploy, and manage applications in one place. Furthermore, if mining enterprises do not have the engineering talent to build solutions themselves, some computer vision providers will take over the entire process — constructing and deploying solutions for a mine’s unique needs and environment. Computer vision is the future of mining, and it is here to stay.
By Maria Aguirre
In the pursuit of sustainable mining, water recovery and tailings reclamation have emerged as crucial elements. Mining companies, stakeholders, and sustainability researchers are focusing on innovative solutions to recover water used in mining processes and restore lands affected by mineral extraction and tailings. This year, MIT hosted the inaugural “Tailings Sustainability Innovation Summit,” bringing together mine operators and academic researchers to share projects, advance research, and collaborate on solutions to this critical environmental challenge, a challenge increasingly viewed as an opportunity for sustainable progress.
The mining industry is optimistic about recent advancements in sustainable innovation, with coarse particle flotation technology emerging as a promising development. Coarse particle flotation offers several benefits to standard mineral processing, including early gangue rejection and reduced energy requirements owing to less grinding. By targeting larger particles, it significantly reduces tailings settling time, making water recovery faster and more efficient. However, managing coarser tailings presents new challenges in fluid control. The high solids content and increased viscosity of coarse tailings require specialized solutions for effective management. This adds to the already complex control applications in tailings management, especially those involving thickeners, which are essential for recovering process water and managing tailings. These systems are among the most abrasive in the mining industry, often leading developers to avoid using control devices in their designs. While this approach may minimize costs, it can significantly reduce the overall effectiveness of tailings management solutions.
A common issue in thickener underflow discharge control and other systems dealing with coarse and mid-tailings is severe erosion of the control devices, such as valves and orifice plates. These devices are critical to the proper operation of systems that play a vital role in water and mineral recovery. Applications that handle tailings containing 55% to 80% solids (w/w) and densities as high as 5000 cP are particularly prone to failure if discharge flow control requirements are not properly analyzed and addressed. Constant failures of control devices can lead to significant water loss, which is critical to the process and must be recovered.
In thickeners, discharge control is especially challenging because the same control device often manages both the thickener’s water recovery and overflow conditions. In the case of an overflow — owing to external factors like environmental changes — the valve must have sufficient flow capacity to prevent choking and allow the tailings not to overflow. This requires a wide range of controllability. As the system cannot be choked, control devices (such as valves) are often sized to handle maximum flow capacity, which leads to normal operation occurring at very low percentages of the valve’s total range. Operating in this low percentage range accelerates wear on internal components, especially when handling abra-
sive media. This is one of the primary reasons why failures in these control devices are so common.
The ideal control valve for such applications should be able to maintain flow within a recommended range, reducing the exposure of internal components to high levels of erosion while also providing enough capacity to prevent choking under maximum operating conditions. To achieve this, selecting a control device that offers an equal percentage or similar flow capacity in relation to the percentage of opening is ideal. This helps center the flow and ensures that only replaceable components are exposed to the abrasive media.
It is important to understand that these processes are inherently abrasive, meaning erosion is not only expected but should also be planned for. Using equipment in these processes that does not account for erosion, especially
equipment that exposes non-wearable components to harsh conditions, can result in reduced equipment lifespan and longer downtimes owing to the need for frequent replacements.
Figure 4 compares the performance of a control knife gate valve and a pinch valve. The pinch valve, when modulating from 15% to 20%, experienced weekly failures owing to high velocities and cavitation caused by the significant differential pressure across the valve (see Figure 3). As shown in Figure 4, the pinch valve’s performance degrades as the percentage of opening increases; the control curve begins to flatten out, and the valve can no longer provide the required maximum flow capacity (operation point 5). This reinforces the need for careful valve selection in these challenging applications. The control knife gate valve, on the other hand, offers linearity and is designed with internal components that ensure it provides the necessary maxi-
mum flow capacity while maintaining control within the recommended range and a higher wear resistance since it moves away from the use of solely elastomers, as with the pinch valve.
Sustainable mining requires careful attention to the design and selection of control valves for water recovery and tailings management. As mining operations continue to push for more efficient and environmentally friendly processes, control devices must be chosen that balance effective flow control with the ability to withstand the abrasive nature of mining tailings.
By Leyla Alieva and Sergei Mamykin
There is a widespread belief that four major wear mechanisms contribute to the damage and deterioration of industrial machine parts: adhesive, abrasive, corrosive, and surface fatigue. This report explains the presence of another no less important, if not more, mechanism that is largely underreported: hydrogen wear.
As hydrogen is the most abundant element in nature, its significance as a leading factor in the premature failure of machine components cannot be ignored. Studies have shown that at least three of the four wear mechanisms mentioned above (adhesive, abrasive, and surface fatigue) will contain the underlying effects of hydrogen wear whenever there is metalto-metal contact with a temperature gradient, even on a micro level.
This report provides a detailed understanding of the hydrogen wear phenomenon, its causal effects in mechanical failures, and how it has presented the wind turbine industry, which is important for the green transition, with a substantial problem.
While knowledge of the hydrogen wear phenomenon is far from commonplace, what is even less known is the remarkable new solution in the guise of NEOL’s revolutionary copper filming lubricant technology. Its unique and environmentally friendly properties not only protect machine components from hydrogen wear with none of the downsides of traditional approaches such as ZDDP but also extend the lifespan and operational performance of industrial applications.
Furthermore, as emerging hydrogen technologies become a potential key source of sustainable energy solutions, this report presents a compelling case for how this revolutionary lubricant’s ability to take advantage of the hydrogen wear mechanism could have far-reaching consequences in the enablement of future technologies.
The hydrogen wear phenomenon
The wear of machinery is found in almost every industry where two surfaces meet and move against each other. This naturally occurring phenomenon is a significant cause of mechanical failure and requires extensive maintenance, time, and cost in the repair or replacement of damaged parts.
The science behind hydrogen wear can be traced back to the 1960s, when Dmitry N. Garkunov made two startling discover-
ies while investigating mechanical failure in aircraft’s landing gears. First, he discovered that during friction, copper ions were being selectively transferred into the crystalline grid of iron forming a thin film. Second, he found that hydrogen was the primary cause of metal surface deterioration.
These two discoveries, which were consequently named “the wearlessness effect” and “hydrogen wear of metals,” marked the beginning of a revolutionary new approach towards antiwear protection and the potential to extend the lifespan of machine applications.
At this point, it is important to distinguish the substantial differences between hydrogen embrittlement and hydrogen wear.
The phenomenon of hydrogen embrittlement, which has been well-known for over a century, is a reduction in the ductility of a metal because of absorbed hydrogen. It usually manifests itself in terms of singular sharp cracks. This process typically occurs owing to contact in hydrogenous media and is promoted by high temperatures, atmospheric pressure, high loads and deformation, and cathodic processes. As such, hydrogen embrittlement is a common issue for steelmakers.
In contrast, hydrogen wear only occurs during sliding and rolling contacts that are found in rotating machinery such as gears and hydraulics. The high contact pressures cause a higher rate of hydrogen absorption, and therefore, an abnormally high concentration of hydrogen. As hydrogen invades the surface it increases internal pressure and causes cracks to form. Through repeated cyclic stresses, these cracks grow and eventually produce the formation of wear particles.
Unlike hydrogen embrittlement, where a different law of hydrogen distribution applies, the phenomenon of hydrogen wear creates an unusual pattern of failure.
Dr. Sergei Mamykin, a global leader in the study of hydrogen wear, defines this pattern of failure as the “self-organized destruction in the material’s top layer during friction; it is characterized by a considerable non-equilibrium of processes and by joint impact of co-factors that contribute to absorption of hydrogen in the top layer and destruction of this layer.”
Additionally, if hydrogen is adsorbed on the friction surface and driven by a temperature gradient, it can diffuse deep into the surface and concentrate there, making the top layers fragile and provoking more intense deterioration.
Factors that determine the intensity of hydrogen absorption include the composition and state of the medium, the treatment of the metal surface, its chemical composition, its atomic structure, its stresses and deformations (in particular, deformations of the metal lattice which raises its energy level), the hydrogen saturation time, and the conditions of hydrogen desorption from metal.
Further research has shown that hydrogen wear has increasingly become a significant factor in the wear of machine parts in a vast array of industries, including mining, transportation, aviation, farming, chemical production, and microbiological production equipment.
Another significant factor is that hydrogen imparts higher fragility to products of hardened steel, especially those used under alternating loads such as crankshafts, piston rings, cylinders of internal combustion engines, and bolted joints.
In some cases, hydrogen impact during friction determines the service life of the friction part. This last point has significantly changed our understanding of the nature of friction and wear. The thermal, electrical, and magnetic effects of friction, all of which control the hydrogen concentration in metals, are now proven to be factors that determine deterioration.
Additionally, during desorption and lubrication, hydrogen can occupy numerous adsorption centres and enters the top layer in much larger quantities — its concentration in steel rises rapidly to a level above equilibrium. At the same time, defects become more numerous with deformation. This effect will go on until internal pressure finally causes the destruction of steel along all emerging and interconnected cracks.
While hydrogen wear is not as well-documented as hydrogen embrittlement, it is no less important in understanding how hydrogen invades the metal surface of machine parts, and how this invasion leads to premature failures.
Hydrogen wear gearbox failures in wind turbines
When metal surfaces connect with each other, they generate heat and pressure, causing particles to separate. This provides gaps that allow hydrogen atoms to infiltrate the metal, pushing out its own particles and causing the deterioration of machine parts.
An example of this can be witnessed in the wind turbine industry. Mechanical wear in large multi-megawatt (MW) wind turbines has become an increasingly serious issue over the last decade. Investigations have found widespread gearbox failures in wind turbines that have occurred in less than five years of operation, so much so that operators now consider it the single most expensive failure mode for all wind turbine components.
This is a serious problem. The global wind turbine sector is growing exponentially. In 2022, the Global Wind Energy Council forecasted 1,221 GW of new capacity to be built worldwide from 2023-2030, yet there is already talk of a “graveyard of gearboxes” in the wind turbine sector.
Research is ongoing to determine the causes of this high failure rate, but it is generally concentrated on the amount of energy required to remove hydrogen ions from either water or from the base oil. When one considers the sheer size of turbines, the amount of torque that goes through their gearboxes, and the power that flows through their blades, the energy is extreme. Consequently, cracks have appeared on the inner ring of high-speed shafts and high-speed intermediate shafts of bearings. If left ignored, these cracks will extend to the gearbox itself and eventually lead to premature failures.
When examining this phenomenon closely, researchers concluded that three factors appear to be working together: non-metallic inclusions, sliding, and hydrogen. However, as the wear phenomenon occurs below the surface, it is impossible to detect with the naked eye, and by the time it reaches the surface, the damage is done.
Researchers have called this phenomenon “white etching cracking” (WEC), and although they agree that its exact cause remains unclear, many suggest that lubricants may play a significant role.
Tellingly, their description of WEC is near-identical to the description of hydrogen wear.
The description of white etching cracking is near-identical to hydrogen wear phenomenon.
CREDIT: NEOL
A 2020 report by ExxonMobil speculated on the activity of hydrogen in the subsurface zone and concluded that it was most likely the result of a complex interaction between several mechanical, electrical, operational, and chemical factors. Even so, the report admitted that “the scale of this tribochemical reaction — the chemical changes that occur to a lubricant and a lubricated surface when separated by a thin tribofilm, generated as a result of interactions between lubricant additives and
lubricated surfaces — is not well-understood.”
Thorsten Süling, European EB/OEM manager of ExxonMobil, posited that “it is possible to select gear oils that do not contribute to the phenomenon.”
Given the fact that many wind turbine gearboxes are not achieving their expected 20-year design life, and around 60% of the industry’s gearbox failures are caused by the WEC phenomenon, it is unsurprising that wind turbine operators and OEMs are conducting extensive investigations on how to fix the problem.
The research conducted into the hydrogen wear of metals and the wearlessness effect has long concluded that evolutionary discoveries of “the wearlessness effect” and “hydrogen wear of metals” simply identified the cause of two different phenomena; that is, why ions are transferred in the process of friction and what causes metal surfaces to deteriorate in machines.
However, by combining these two discoveries together, the double detection of the wear-free effect and the hydrogen wear in tribological engineering uncovered both the cause and solution for mechanical wear.
Dr. Sergei Mamykin, who has been developing revolutionary copper filming technology for more than 30 years, defines the wear-free effect as “a type of friction that can be described as a non-oxidizing thin metal film (servovite film) that emerges spontaneously in the contact area; the film possesses low shear resistance and cannot accumulate dislocations through deformation. On top of this film, an additional protective film (surf film) can be formed, entering in a chemical bond with it; the latter film is made of degradation products left from hydrocarbon lubricants.”
Furthermore, as friction units are manufactured, Mamykin found that the selective transfer effect helped to reduce their weight and dimensions by 15% to 20% thanks to greater load capacity of their friction pairs, and to significantly increase the efficiency of respective machinery while simultaneously reducing consumption of energy, increasing reliability, and extending the service life and overhaul periods of these machines.
In operational terms, this would allow operators to significantly decrease the costs of labour, time, and energy spent on maintenance and repair.
Lubricant additives based on copper ions (Cu2+) have been widely known for more than five decades. Professor Garkunov, who first discovered the hydrogen wear of metals, discovered the effect of friction and wear reduction by copper films, and that layering occurs when the copper particles were compressed between two friction bodies.
Garkunov and other researchers also found that the copper film does not oxidize, and material can be transferred to the counter body. Consequently, a copper–copper sliding interface is formed.
The effect of wear reduction by copper tribofilms has been demonstrated by many experiments, including both tribometers and real applications. In 2016, scientists led by Matthias Scherge at the MicroTribology Center in Karlsruhe, Germany, added copper ions as an additive to fully formulated engine oils. The copper additive was in colloidal form, with an inner core of Cu2+ atoms covered by surfactants to form stable reverse micelles that are completely dispersible in the base oil.
The tribological performance was then investigated using atomic force microscopy, a microtribometer, a pin-on-disk tribometer in combination with continuous and high-resolution wear measurements with radio nuclide technique, and high pressure stressing in a thrust roller bearing test rig.
The results were revelatory. First, laboratory tests and tribological investigations confirmed that this innovative stable copper additive delivers long-lasting reduction in friction, protection against wear, and extended service-life. Second, the mechanism and function of copper tribofilms involved a threestep process: an instantaneous reduction in the coefficient of friction, the formation of a solid lubricant composed of copper monolayers, and plastic flow of the copper tribofilm combined with mechanical intermixing and tribochemical reactions. Furthermore, near surface polymerization of monomers from the base oil led to a protective top layer that helps to shift the systems towards hydrodynamic lubrication and prevents further attacks of oxygen.
The test results provided additional proof of “self-sustained friction reduction and wear protection.” Building on the work of Garkunov and other researchers, the following conclusions were reached:
• The protective and friction-reducing action of copper-based additives can be extended to the tribological regime at ultralow wear rates.
• When severe wear is examined under artificially extreme four-ball machine test conditions, thick films are necessary to protect the surfaces; while in real-world and representative ultra-low wear regimes, thin films provide sufficient protection.
Friction is often only associated with the process of wear, but when paired with the selective transfer of copper ions, it becomes an evolutionary process and, as a result, the destruction of surfaces becomes secondary.
Owing to the exchange of energy and matter between the friction surface and the external environment, as well as the collective behaviour of copper ions, the developmental nature of friction is revealed in the form of a thin copper film that coats the metal parts, protecting the friction surfaces from wear. And because friction creates a protective film, it can no longer destroy it. Simply put, the system has become self-organizing.
This is where NEOL’s unique copper filming technology comes into play. This revolutionary lubricant technology can solve the issue of hydrogen wear while lowering friction and reducing other mechanisms such as adhesive, abrasive, and surface fatigue wear. As soon as hydrogen finds metal-to-metal contact, it starts causing wear, but rather than allowing uncontrolled hydrogen invasion to the friction surface, NEOL’s additive technology first uses its properties to “polish” the friction surface at the elementary level. The hydrogen wear is then terminated with copper ions. Copper ions are embedded in the crystal lattice of iron or iron-containing alloys, thereby “heal-
ing” damaged areas. They gradually form an even copper film covering an entire surface, at which point, continued hydrogen wear and other wear mechanisms will virtually cease.
This results in a significant increase in the efficiency and longevity of machinery — iron being the most abundant metal in machine components — while substantially decreasing expenditure on maintenance and replacements, plus a considerable reduction in fuel consumption. Additionally, copper filming technology means there is no longer a dependence on toxic phosphorous and sulfur compounds which have traditionally been used as anti-wear agents by the global lubricants industry, mainly as ZDDP (zinc dialkyldithiophosphate).
ZDDP has been the world’s most popular lubricant oil additive since it was patented in 1944. Cheap to produce, its multifunctional additives are used in engine oils, transmission fluids, hydraulic fluids, greases, gear oils, and many other applications. While commonly known as zinc, it is the phosphorus and sulfur compounds in ZDDP that do all the hard work in reducing wear and controlling oxidation.
However, while ZDDP has been proven to extend machine longevity, its negative effects on the environment have become a critical issue. Additionally, zinc-induced neurotoxicity has been shown to play a role in neuronal damage and death associated with traumatic brain injury, stroke, seizures, and neurodegenerative diseases.
In stark contrast, NEOL’s proprietary additive package is based on oil soluble organic copper salts. This unique composition contains ultra-low to no SAPS (sulfated ash, phosphorus, and sulfur) and does not require a high base content. As a result, used NEOL oil is easily recyclable and, in some cases, fully biodegradable.
NEOL’s additive is also a highly effective detergent keeping machines free of the sludge deposits and varnish that plagues modern engines, compressors, turbines, and hydraulic systems. This makes it an environmentally friendly alternative and completely safe for use with modern catalytic converters and diesel particulate filters.
ZDDP-free, ultra-low to no-SAPS (sulfated ash, phosphorus, and sulfur) copper filming technology makes lubricants environmentally friendly.
To prove the effectiveness of its unique properties, NEOL evaluated the performance of CuGlide powered oil formulation packages in a series of real-world applications. One test study involved a one-year trial of full-synthetic ISO VG 220 industrial gear oil in a well-worked Sandvik CG820i gyratory crusher
during mining operations. Phase one consisted of a 1,500-hour pilot test. This was followed by a second phase of using the industrial gear oil in the crusher for more than 5,000 hours to
CREDIT: SANDVIK
test the longevity of its lubrication and cleaning properties.
It was important to have two extensive testing phases to fully evaluate the oil’s performance on the 244-tonne gyratory crusher, which had a 525-kW motor, a 1,200-L oil charge, and was capable of processing up to 4,000 tonnes of material an hour. It also allowed NEOL to appraise the viscosity, acid control, wear protection, and the detergency properties of the oil under long-term, heavy in-service conditions.
The one-year field test delivered exceptional results. The industrial gear oil proved to have excellent viscosity control at 40°C and 100°C while also offering thermal and oxidative stability. There was no increase in in-service oil acidity, with the lubricant providing oxidation and corrosion protection, and no degradation in performance.
The gyratory crusher’s gear parts that were subjected to high load, stress, and hot temperatures did not wear during contact. Additional oil analysis also showed there was no iron, chromium, or nickel detected. The lubricant helped to effectively clean the gyratory crusher’s gear parts and restore efficiency, as previously immoveable remnants and engine debris were washed out. Furthermore, during the pilot test phase, there were six filter changes that revealed particles of metal and bronze shavings also washed out of the crusher.
Overall, the industrial gear oil delivered a robust level of protection, worked as a detergent, and offered long-term lubrication. This allowed operators to run the equipment more efficiently while saving on maintenance costs.
Another test study involved a 500-hour standard service interval field trial on three CAT 777E haul trucks equipped with Caterpillar C32 V-12 engines in an open cast mining operation.
The objective was to assess engine lubricant performance and quantify operating savings, particularly in fuel consumption, for mining operators. Additionally, the innovative formulation aimed to solubilize and remove harmful deposits, repair engine wear, and extend engine life, thereby reducing total cost of ownership (TCO) and enhancing productivity.
The trial deployed CuGlide powered no-SAPS synthetic 10W40 HDDEO formulation in the three trucks, with each vehicle having accumulated 28,000 to 33,000 hours of service. The lubricant consisted of a unique blend of additives, including a highly concentrated additive package (~300 ppm copper), performance polymers, pour point depressants, and a mix of API Group-III, PAO, and ester base oils.
Previously, the trucks had been using a market-leading SAE 15W-40 oil with various additives. Despite satisfactory operational conditions, NEOL sought to explore the potential benefits of its unique additives in these heavily utilized vehicles.
The field trial yielded remarkable results and demonstrated the efficacy of CuGlide powered lubricant in enhancing engine performance. Oil analysis revealed minimal wear, efficient removal of lead-containing deposits, and excellent control of oxidation and nitration.
In terms of operational costs, fuel consumption data indicated potential annual savings ranging from $83,000 to $178,000 per truck, contributing significantly to reducing TCO. Drivers also reported improved vehicle acceleration and speed, highlighting the rejuvenating effects of the oil on engine components.
By delivering improved efficiency, protection, and productivity, the copper filming technology allowed operators to optimize engine performance and mitigate operational costs in harsh mining environments, indicating a radical advancement in asset management that could generate profitability for other mining operators.
The untold possibilities of the copper filming technology to prevent and reverse the effects of hydrogen wear and other wear mechanisms not only has far-reaching consequences for the industries of today but also extends to the emerging industries of tomorrow.
For some time now, hydrogen has been recognized as one of the most promising carriers of non-fossil energy on the pathway to net-zero. The transportation industry, one of the largest fuel consumers of the global energy market, is investigating hydrogen as a potential future solution in providing clean, reliable, safe, and affordable energy for our planet.
The obvious advantages of hydrogen — its abundance, energy density, and ease of transportation — also make it a serious contender to replace our deep-rooted addiction of fossil fuels. However, as hydrogen technologies emerge, the processing, storing, and utilization of hydrogen in a safe and sustainable manner requires high production expenditure, being almost triple the cost compared to fossil fuels. For this very reason, the protection and maintenance of hydrogen technology is paramount.
Leyla Alieva is CEO and co-founder of NEOL Copper Technologies. Dr. Sergei Mamykin is a tribologist and copper filming technology developer at NEOL Copper Technologies.
A version of this article has been published previously in Lube Magazine. However, this version has been updated, modified, and made exclusive to the Canadian Mining Journal.
Since the late 1990s, the earthmoving sector has been utilizing GPS technology for advanced machine guidance and process optimization. By receiving signals from a network of satellites orbiting the Earth, GPS receivers mounted on mining machinery can provide real-time positioning information, enabling operators to pinpoint and monitor the exact location of all equipment.
Nonetheless, relying solely on GPS comes with setbacks. For one, GPS is only suitable when the equipment has a clear view of the sky with decent satellite coverage to provide positioning information. This means underground mining must rely on alternative navigation methods. Projects in open-pit mines are also susceptible to multipath GPS signals.
Further, GPS is vulnerable to ionospheric scintillation, where the signal waves are disrupted by small-scale irregularities in the ionosphere. This issue is most severe in sub-equatorial regions and at auroral latitudes, which covers much of Canada — the fourth largest nation by mine production volume.
Mining operators often leverage a myriad of technologies consisting of GPS and other redundant solutions, such as an inertial navigation system (INS). An INS uses a variety of environmental sensors, including accelerometers and gyroscopes, to detect and measure the change in motion of an object. Using this sensor data, the INS can determine the position of the object relative to its starting point — a process known as “dead-reckoning.”
When mounted onto a mining vehicle, this presents several fundamental advantages. Firstly, an INS can provide updates at a higher rate than GPS. This allows it to output data much faster and provide orientation data, roll, pitch, and heading, which the traditional GPS system is incapable of achieving.
INS can also operate in GPS-denied environments. Mine sites are often located in distant, rugged terrains with dust, low light, and unideal weather conditions with signal interruptions. By applying the principle of dead-reckoning and data fusion to estimate position, an INS makes for a reliable technology when GPS positioning information is unavailable.
A combination of GPS and INS data can ensure position, velocity, and attitude estimates of higher accuracies and better dynamic performance. In a real-world example, a bulldozer can have INS units mounted on the chassis and on the blade, with GPS antennas mounted to the cab. The INS units can measure the angle, tilt, depth, and motion of the blade, while the GPS captures real-time positioning data around the dozer’s location, blade position, and the surrounding terrain. All this information would be sent back to the control centre, allowing managers to make strategic decisions over time that would drastically improve efficiencies and yield.
A combination of INS and GPS data can advance the automation capability of certain types of mining equipment, such as autonomous haulages. This means an autonomous, connected fleet where machines can communicate with one another to perform tasks with minimal human intervention onsite, greatly improving safety.
Across the mining industry, the market for INS equipment is broadening. Manufacturers and system integrators often face trade-offs between a unit’s cost and performance. Where a system provides superior performance, its power consumption and cost often come across as unattainable for mining operators; whereas a system that sits within budget constraints may not achieve the precision and accuracy required to carry out the job effectively.
A less perceptible but increasingly important attribute is the system’s size and weight. Mining operators are trending towards the adoption of smaller, lighter systems that can optimize the use of space in every vehicle’s junction box. Further, with the proliferation of drones and uncrewed air systems used for tasks such as surveying and mapping, having a reliable navigation unit that does not weigh down the overall system is critical.
Advanced Navigation recently rolled out the Certus MINI series. Available in three variants, the series includes a GNSSaided Certus MINI D and Certus MINI N INS, while Certus MINI A functions as an attitude and heading reference system (AHRS).
Certus MINI D features dual-antenna GNSS heading, allowing it to deliver superior accuracy in heading, position, and velocity. With a maximum weight of 0.055 kg, the series fills a critical gap in the market for a dual-antenna INS in a lightweight and compact size. This level of miniaturization owes to a breakthrough algorithmic technology. This software-enhanced hardware delivers navigation data superior to outputs based on traditional filter methods, offering new levels of performance for miniature INS in GPSchallenged environments.
Certus MINI is the ideal solution for surface drilling OEMs and integrators seeking precise rig alignment. Best-inclass accuracy provides precise alignment even in deep pits where multipath errors occur, and a ruggedized design delivers durability and reliability in harsh mining conditions.
Designed with flexibility in mind, the series is easily integrated into existing and new system builds with simple plugand-play connectivity, minimizing development time and costs.
Additionally, by operating on the L1/ L5 multi-constellation GNSS, the Certus MINI series offers leading capabilities in interference immunity, position accuracy, and multipath resistance.
For mining operators deploying landbased vehicles, this value-driven breakthrough unlocks new possibilities for those using lightweight airborne platforms, such as drones.
Recently, Advanced Navigation entered an agreement with UK-based NILEQ to co-develop a resilient INS solution, integrating NILEQ’s absolute positioning technology — suited for a multitude of airborne platforms.
NILEQ’s patent-pending technology is underpinned by the use of novel neuromorphic sensors to derive and match terrain fingerprints. The sensing technology captures data of the changing terrain as an airborne system flies across it and matches it to an existing database of the Earth’s surface.
The concluding solution is set to enable systems, such as uncrewed air systems, to secure an absolute position fix over land with a solution that is passive and
resistant to electronic interference. The solution is expected to enable faster and easily repeatable mining surveys carried out on low-cost drones. This is suitable for large-scale projects, such as site-mapping and infrastructure inspection. It also enhances the safety of beyond visual line of sight (BVLOS) operations, allowing drones to navigate dangerous or inaccessible areas, such as unstable terrains, high walls, or underground tunnels where GPS is not available. Advanced Navigation and NILEQ will validate the
system in an airborne demonstration planned in Australia this year.
Inertial navigation is a tested and proven method for maintaining resilient positioning on mine sites when GPS is unavailable. Mine operators should pay special attention to advancements in this technology as they will be pivotal to commercial success.
Chris Shaw is the CEO and co-founder of Advanced Navigation.
INTRODUCING AN EASY WAY TO PROTECT YOUR WORKERS AS WELL AS PROTECT YOUR INVESTMENT INTO YOUR
Many industries, including mining, struggle to attract and retain employees in the aftermath of the 2020
“great resignation” and mass retirements. Part of this has to do with the health risks workers take every day. From dust exposure to nerve damage to hand-arm vibration syndrome, younger individuals entering the workforce have seen the outcome of working in these industries long term. They are looking for safer alternatives that protect them and allow them to use the most up-to-date technology.
Successful companies think outside the box and supplement their crews with technologically advanced equipment capable of supporting zero-carbon mining initiatives. Modern robotic demolition machines help boost employee recruitment efforts and increase long-term employee retention by offering a safer, more sustainable way to get the job done.
Employee recruitment
Cutting-edge technology can be a powerful recruitment tool. When it comes to safety, for example, manual labour workforces are well-aware that quality of life and length of career can be significantly affected by injuries and silica dust exposure.
They look for employers who show care for their employees and keep to the highest safety standards to protect their futures.
Companies who invest in mechanization reduce the amount of dangerous and hard manual labour workers must perform, which is a powerful benefit. A young employee may consequently see mining as a long-term profession with a realistic way to remain in the industry for the duration of their career.
Technologically advanced equipment also attracts younger workers. For one company, including advanced robotic equipment in their fleet reduced the median age of their 300-strong workforce to just 25 years old. The machines allowed them to do more work with fewer people and increased productivity 17% over three years.
Employee retention
Another thing mining operations need to consider is the general age of their workforce and how long those workers will stay in the industry. In 2023, the median worker age was 42.1 years with 40% of miners being 45 years old and older. Many have worked in the industry their whole lives and are looking for ways to remain in their positions for the rest of their
careers. However, long-term use of handheld breakers, jacklegs, stopers, and ad-hoc bar and arms have been linked to several chronic injuries. These injuries can hold employees back and even take them out of their positions for good.
Remote-controlled machines physically distance employees up to 300 metres away from strong vibrations as well as harmful silica dust. They also help prevent one of the most common causes of serious work-related injury and death — falling debris. A remote-controlled unit allows operators to remain a safe distance from the rock face and other hazards. This provides peace of mind for workers and project managers and allows employees to extend their careers. The same company that lowered the median age of their workforce also saw a cut in turnover by 10%.
The advantages of demolition robots
Recruitment and retention changes as time goes on and can become a challenge if companies are not keeping up with the newest equipment options. Being able to support workers throughout their working career helps attract new employees and keep current employees longer. Modern mining has many exciting challenges in store for the new generation of technologists who will need creative solutions to supply the world’s
ever-growing demand of metals in support of green technologies and more. By investing in robotic demolition machines, mining companies can thrive in today’s competitive environment while preparing for the future, staying ahead of the competition.
Jeff Keeling is the vice-president of sales and marketing at Brokk Inc. He works closely with regional sales managers to develop and grow the Brokk brand in key segments across the U.S. and Canada.
By Antoine Mindjimba
As Canada’s metals and mining industry grapples with the demand challenges of the energy transition, it must also address the urgent need to modernize its workforce. Alarmingly, recent data has shown that workforce considerations have fallen out among the Top 10 Risks and Opportunities for mining leaders heading into 2025. This shift in priorities among mining companies is concerning, especially when the sector faces significant challenges in attracting and retaining the talent necessary for its future success.
The consequences of neglecting workforce modernization could jeopardize Canada’s position as a global mining leader, with potential economic setbacks and reduced competitiveness looming large.
The mining industry must recognize that long-term success hinges on its ability to attract, train, and retain a skilled and motivated workforce which will require a fundamental shift in how the sector approaches talent management.
Embracing technology for upskilling
The rapid advancement of technology, particularly in artificial intelligence (AI) and automation, presents a unique opportu-
nity. According to polling data from the EY 2024 Americas Metals & Mining Forum, 36% of attendees identified AI and machine learning (ML) as the most significant advent to influence operations in the next five years. Integrating these tools strategically will allow companies to enhance their workforce rather than replace it. Upskilling programs that align with technological advancements will be key. For instance, AI or virtual reality (VR) simulations can fill training gaps, offering real-time opportunities to improve skills and, ultimately, safety on-site.
Moreover, the adoption of technology may help address the sector’s aging workforce by making mining jobs more attractive to younger generations. By showcasing the industry’s commitment to innovation and sustainability, mining professionals can appeal to tech-savvy prospective candidates who might otherwise overlook the sector. This approach positions mining as a forward-thinking industry that values leveraging cutting-edge technologies.
Research indicates that tailored nudges, such as using engaging and inclusive language in job descriptions, can significantly increase applications from underrepresented groups.
Mining companies could adopt this strategy to reach younger and more diverse talent pools.
The next generation of mining workers prioritizes work-life balance, mental health, and workplace safety, and emphasizes the need to produce with consideration to the planet, future generations, and sustainably. The sector must adapt to these shifting priorities or risk being left behind. Data by the Canadian Mining Industry Human Resources Council found that 70% of young people would “definitely not” or “probably not” work in the mining sector. This statistic underscores the need for a fundamental industry rebrand for all its stakeholders. Companies must align their organizational values with employee priorities. Inclusive leadership that embraces diversity, and fosters belonging with employees across generations, to create a performing culture, will be crucial. This approach not only attracts talent but also enhances employee engagement and retention.
To achieve this, mining companies should consider adopting policies that promote work-life balance and mental health. This includes offering flexible work arrangements, providing access to mental health resources, and creating a supportive work environment that prioritizes employee well-being to help them unleash their full potential. By demonstrating a genuine commitment to these values, mining companies can build a positive reputation that resonates with potential employees and sets them apart from competitors. Just as elite athletes rely on mental and physical fitness for peak performance, mining companies must foster a culture that promotes resilience and well-being to sustain long-term success.
In today’s diverse workplace, a one-size-fits-all strategy is outdated. The mining sector must develop tailored leadership strategies that accommodate both remote and on-site workers. Flexible work arrangements, purpose-driven environments, and corporate
cultures that prioritize growth, lifelong learning are increasingly sought after. For example, rotating early career engineers through different disciplines can help avoid pigeonholing and improve retention. Additionally, skills maps can articulate growth opportunities within roles, supporting upskilling for role changes, rotations, and certifications. By continuously engaging with talent, companies can draw a clear path forward for their workers to embrace a long-term career in mining with possibilities of upward mobility.
Furthermore, mining companies should invest in robust succession planning to ensure a smooth transition of knowledge and skills from retiring employees to the next generation. This involves creating structured mentorship programs and offering leadership development opportunities. By prioritizing career development and setting employees up for success, mining companies can cultivate a loyal and motivated workforce that is well-equipped to navigate future challenges. Introducing structured feedback loops — where employees can regularly share their career aspirations and receive actionable guidance — can significantly enhance engagement and retention.
The future of mining companies hinges on the dedicated individuals who keep the industry moving forward. The field depends on a motivated, highly trained, and supported workforce to grow, and its future depends on its ability to attract, train, and retain this next mining generation.
Canadian miners must begin implementing these strategies for 2025 and beyond. Embracing technology for upskilling, realigning organizational values with emerging employee priorities, and offering flexible work arrangements and career development opportunities are essential steps. By doing so, the sector can secure its incoming talent pipeline and achieve long-term, sustained success.
Mining leaders must act now to implement these strategies, securing not only their workforce but also the sector’s future amid global shifts toward sustainability and innovation.
Antoine Mindjimba is an EY Canada partner and the people consulting leader for mining and metals at EY Canada, based in Toronto.
The global mining industry continues to build momentum and prepares itself for what appears to be a remarkable technological transformation. Executives are facing unprecedented pressure to find sustainable and creative methods to drive shareholder value and enhance productivity while improving the safety of the workforce — all during a time of global political instability, low commodity prices, and a generation of new workers that are motivated by non-traditional incentives. This transformation is not only reshaping the landscape of employment and skill requirements for mine workers, but also it is reframing the relationship between the external technology ecosystem and global mining operators. In this era of transformation, the pace of technological change is unprecedented and as I have mentioned before, I believe the side that pays attention and learns the fastest will win. Those unaware or choose not to pay attention to this technological revolution risk the inability to compete and sustain operations in this new world.
As an example of paying attention, I was invited to participate in the 2025 MIT AI Negotiation Competition earlier this year. Recognizing that artificial intelligence (AI) and large language models (LLMs) are transforming the way we work, live, and communicate, this competition was rooted in having teams creatively prompt and counter-prompt ChatGPT in a realistic negotiation scenario. In each round, the bots negotiate with each other, yielding scores for value creation, value claiming, subjective value, and efficiency. This competition, utilizing a platform that was created only two years ago, serves as an example of the unprecedented rate of technological change. If there are any skeptics thinking this is an interesting example, but believe AI has limited applications in mining, I would encourage you to spend the time to check out tech ventures such as MinersAI (minersai.com), RadiXplore (radixplore.com), Elemission (elemission.ca), and Ideon (ideon. ai). If you are not familiar with these ventures, I would argue that you are not paying attention.
In the spirit of paying attention, I want to highlight three emergent themes that are core contributors to “winning” in the mining industry — each taken from a unique perspective: a mining operator, a technology company, and an association/enabling intermediary. Each of these entities have different challenges, and therefore each define winning in different ways.
First, from the perspective of Canadian mining operators, one of the challenges of winning continues to lie in attracting and retaining talent. As outlined by the Mining Industry Human Resources Council of Canada (MiHR), our country will need more than 100,000 new mine workers by 2029. However, it is not simply a workforce numbers problem. Mining operators have enhanced their talent recruitment and retention strategy to engage and train resources that are capable and confident of assessing, procuring, utilizing, and integrating emerging technologies within mining operations. With this, the new world of work is driving the new world of training and development.
At a practical level, what does this look like? How do operators build both competency and confidence in a meaningful way that is cost effective and can accommodate the ever-changing nature of new technologies that are poised to transform the industry? One method is virtual reality (VR). In a 2022 study published by PwC, it was found that utilizing VR as a learning tool, trainees were able to learn four times faster than traditional classroom methods and were 275% more confident to apply skills learned after training. Obviously, there are nuances related to the appropriate application of VR, but the results demonstrate the role that VR can play in the future of education. Furthermore, over the past ten years, NORCAT has heavily invested in developing and deploying both VR and augmented reality (AR)-based learning programs to inform the future of training and development. In a recent multi-year research study conducted in partnership with the Future Skills Centre in Canada, our results closely echoed the aforementioned study. As an example, trainees participating in our VR pre-operational circle check training program indicated improved know-how and
confidence in completing the pre-operational check from an average baseline score of 41% to a post-training score of 96%.
Given the labour market requirements, coupled with the pressures to expedite technology adoption, it is critical that mining operators understand the opportunities to incorporate learning technologies to augment existing methods of training and development. In a 2022 study conducted by McKinsey, nearly 50% of mining employees were likely to leave their current job because of the lack of career development. To advance in one’s career — especially in an industry undergoing a technology transformation — on-going learning and development will be critical, and tools such as VR and AR will be key enablers to make this happen both effectively and efficiently. There are now countless studies validating the educational benefits associated with VR and AR that did not exist two years ago. Pay attention. These technologies will help operators win the battle to attract, educate, and advance the career opportunities of their workers.
Next, mining operators historically have invested in in-house R&D teams charged with proprietary IP and product development to build bespoke solutions that would provide a competitive advantage throughout their mining supply chain. However, over the past thirty years, an analysis conducted in partnership with MIT indicated that mining companies’ R&D expenditures declined approximately 45% as a percentage of revenue from 1994 to 2024 on the part of twenty of the leading global mining operators. Mining companies industry-wide have gradually divested themselves from large in-house tech-oriented R&D functions while over the same period emerging technologies in data, automation, electrification, and ore characterization among others, promise to increase mining productivity, safety, and value creation. Simply put, mining operators have evolved from builders of technology to buyers of technology.
With that, one of the foundational trends that is driving technology procurement, adoption, and diffusion in the mining industry is the elevated investment from mining supply, service, and technology companies to educate mine operators on both the fundamentals and intricacies of the emerging technologies they are selling. For example, TesMan, based in Sudbury, Ont., has developed and deployed remote loading and cleaning technology that is defining a new underground mining method. This method not only reduces cycle times and improves productivity, but it also removes the mine worker away from the face. As part of their growth strategy, TesMan has conducted numerous workshops and case studies collectively engaging integrators, operators, workers, and intermediaries to educate and build confidence on the merits of their solution. Similarly, Ideon Technologies, headquartered in Vancouver, B.C., has developed a solution that reduces geologic uncertainty using muon-based technology. A key aspect of their go-to-market strategy is rooted in educating and providing simulations for prospective customers on how muon tomography works and how it compares with conventional methods in the marketplace.
These concepts, simulations, case studies, and workshops are not new, but what is new, is the sophistication and rate of emerging technology development and the elevated importance
to ensure the market clearly understands the technology, the value proposition, and the integration/adoption pathway within operations. The well-known metaphor “raising the tide so all boats can rise” is more important than ever in the age of rapid digital transformation, and an increasing amount of this responsibility is falling directly on supply, service, and technology companies. Tech companies like TesMan and Ideon are paying attention and therefore winning the battle for deployment of their technology.
Last, the on-going perception challenges facing the Canadian mining industry have continued to contribute to the declining interest and enrolment in mining related programs among younger generations. In a 2021 study published by MiHR, 70% of young people between the ages of 15 to 30 indicated they would not or probably not be interested in a career in mining. Mining engineering enrolment and graduation rates have been declining in recent years, with a 50% decrease from 2014 to 2022. Of the approximate 90,000 engineering students enrolled in Canada, only 2,200 are enrolled in mining-related fields. Canada is not alone as similar trends exist in other mining jurisdictions including both Australia and the U.S.
However, there is reason for optimism. Initiatives such as the “This is Mine Life” campaign by the Ontario Mining Association are starting to reverse this trend. This program, designed to shift the perceptions of Ontario youth to consider a career in mining, has deployed multiple resources, including in-person workshops, podcasts, on-line content/videos, and social media campaigns, and it has a total reach of over 14 million in the last 18 months. Furthermore, this initiative has been focused on engaging Indigenous Peoples and women — two populations that present significant opportunities to support the future of the Canadian mining industry. The question becomes, what more can be done to engage and inspire these groups to consider a career in the mining industry?
A 2019 U.S.-based study published by Bell et al. in the Journal of Quarterly Economics, highlighted the importance of role models for young people and the influence they have on downstream career selection. The comprehensive study presents evidence on a variety of factors that determine who becomes an inventor by tracking the lives of inventors in the U.S. from birth to adulthood. Controlling multiple variables, the study reveals that exposure to innovation during childhood is a critical factor that determines who becomes an inventor and the types of innovations they pursue. Using this study as a proxy, it is more important than ever for our industry to build on and pay attention to the existing platforms, such as the “This is Mine Life” and “Women in Mining” initiatives, coupled with First Nations’ mining engagement programs, to ensure that existing mine workers within these demographics can engage with and share stories about their experiences in the mining industry and ultimately serve as role models. The research shows that role models are one of, if not “the” most important, factor(s) our industry needs to engage these populations.
Don Duval is the CEO of NORCAT.
For me, every January begins with another trip through the key events of Canadian history since 1867, courtesy of a course I have taught for nearly 20 years at Memorial University of Newfoundland. As I write, I just stepped out of a class on Confederation, where we examine all the reasons that four tenuously related colonies decided to become the nation we call Canada. As most teachers do, I covered off some key factors that produced a new political union: political gridlock and instability in the two Canadas (present-day Ontario and Quebec), fears of an attack from the U.S., dreams of a transcontinental nation, and the mania for railroads that might knit British North America together as a powerful, integrated industrial economy.
There is one important inspiration for Confederation that often gets left out of standard textbooks and classrooms: gold mining. This part of the story can be traced back to 1858, when the SS Otter arrived at San Francisco with 800 oz. of gold from the Fraser River and sparked a rush northward among miners who were working the increasingly unproductive gold deposits of the Sierra Nevada. As with most nineteenth century gold rushes, even a whisper of a new deposit draw thousands of individual miners. Indeed, nearly 30,000 American miners passed through Victoria or Esquimault before taking a ferry to the mainland and overland trails to the new gold deposits. It was a diverse group, not only White Americans but also Black miners (see the Canadian Mining Journal: vol. 144, no. 8), Australian, Chinese, and European fortune-seekers, all descending upon the lands of Indigenous groups such as the Stó꞉lō and Nlaka’pamux. With no central authority or laws, different factions attempted to sort mining claims on their own (sometimes with violent and deadly confrontations), while Indigenous communities defended important salmon fishing areas and their own gold diggings. In response to the chaos,
and the prospect of losing the territory to the U.S., the British Parliament created the brand-new colony of British Columbia in the Hudson’s Bay Company lands, planting the seed for what would soon become a transcontinental nation.
The enthusiasm for B.C. gold only accelerated with a new rush in 1861, as prospectors pushed outward from the Fraser River to make the next big strike in the Cariboo region. Because it was a mountainous and remote region of the interior, Governor James Douglas ordered that a road be built between Yale, a town that arose with the Fraser gold rush, and Bakerville, the centre of the new gold rush, 350 km to the north. Cariboo gold production hit its peak in 1864, though mining continued in fits and starts for another couple of decades.
Despite the tenuous nature of the Cariboo rush, some colonial politicians saw it and the Fraser River rush as symbols of the wealth-generating potential of a new transcontinental nation. On Feb. 8, 1865, George Brown, speaking before the Legislative Assembly of the Province of Canada, described B.C. as “the land of golden promise,” and suggested, “if the mind stretches from the western bounds of civilization through those great north-western regions, which we hope ere long will be ours, to the eastern slope of the Rocky Mountains, what vast sources of wealth to the fur trader, the miner, the gold hunter, and the agriculturist, lie there ready to be developed. Exactly a month later, Fitzwilliam Chambers argued to same legislature that the idea of a transcontinental nation “points to the vast commercial enterprises yet to be engaged in upon the Pacific shores, to the rich gold fields of Columbia and the fertile shores of Vancouver.”
More important than the musings of politicians was the fact that gold mining provided the economic basis for the settlement and early establishment of colonial authority over what is now mainland B.C. Prior to 1858, there were very few
non-Indigenous people inhabiting the region, mainly traders and merchants associated with the fur economy. The gold rush era brought sudden change to the mainland, and it is difficult to imagine B.C. entering Confederation in 1871 (or the other Canadian colonies making entreaties for B.C. to join) without the rapid settlement and road development program that had occurred over the previous thirteen years. Ironically, it was Ottawa’s promise to assume B.C.’s debt, a good portion of which was generated building roads to the gold mining interior, that convinced the westernmost colony to join Confederation. But it was the lure of B.C.’s riches, and the desire to link such a far-lung British colonies to its counterparts further east, that cemented the
bers of the crew working on the road to Barkerville. Governor Frederick Seymour sent two small colonial militia groups to confront the Tŝilhqot’in, but they did not know the land well, and
Prior to his execution, Klatassin declared that “we meant war, not murder.”
Recognizing that the Tŝilhqot’in acted to defend their homeland through warfare rather than criminal acts, B.C. Premier Christy Clark apologized for the hangings in 2014. Four years later, Prime Minister Justin Trudeau also apologized and took the further step of exonerating the convicted Chiefs. Also in 2014, the Tŝilhqot’in won title to 1700 km2 of their traditional territory through a ruling of the Supreme Court of Canada, the first time a Canadian court has recognized Indigenous title to land. In some ways, the Tŝilhqot’in court decision brought the story of gold mining and Confederation full circle, recognizing that Canada’s gold-hued national dreams of the 1860s had not erased the pre-existing First Nations that had inhabited the area since time immemorial.
is a professor in the History Department at Memorial University of Newfoundland and the co-author (with Arn Keeling) of “Mining Country: A History of Canada’s Mines and Miners,” published by James Lorimer and Co. in 2021. His new book, “The Price of Gold: Mining, Pollution and Resistance in Yellowknife” (also co-authored with Arn Keeling), will be released with McGill-Queen’s University
Are you just checking the boxes by doing required training hours, or is your goal to get a return on your investment? There can be huge improvements in production, maintenance labour, risk avoidance, and cashflow by training employees on how to safely control fugitive materials in bulk material handling and then implementing changes. Unfortunately, half measures do not get half results, so training alone will not be sufficient. Following through on what has been learned is the key.
Training should be robust enough to break the “We have always done it that way” mentality and encourage creativity in problem solving with safety at the forefront of the design. Companies that place a priority on safety — and address fugitive material problems seriously — benefit from fewer safety incidents, less regulatory oversight, and higher productivity and profits.
The online Martin Foundations Learning Centre draws from the collective knowledge and expertise gathered over nearly 80 years solving bulk handling challenges. Aimed at apprentice technicians and experienced engineers alike, the non-commercial information is offered at no charge and is accessible by computer, tablet, or smartphone. An extension of the Foundations training curriculum, the Learning Centre uses a mix of text, photos, videos, webinars, online events, and live experts available to answer questions.
Everyone operating, cleaning, or maintaining conveyors should be trained in the hazards of belt conveyors and bulk material handling. Operators and cleaning crews should have a basic understanding of what normal conveyor operation is and what the common problems are, so they can be aware that there are ways to reduce day-to-day problems such as spillage and belt wander.
Basic training includes topics such as guarding, identifying problems, and safe work practices. Appropriate safety training emphasizes how the belt can store elastic energy even when Lock-Out Tag-Out procedures are followed, and why additional securing of the belt is required. Further, with the retirement of many experienced operators and mechanics — and the difficulty in finding new workers — it becomes critical that new employees understand the basics of conveyor design and operation.
The engineering and maintenance staff should be additionally trained in fundamental conveyor design concepts, so they can analyze cause-and-effect relationships. Quite often the visible signs of poor conveyor operation are not the root cause of the problem. For example, using guide rollers to force the belt to track does not address the fundamental reason for the belt mistracking and usually results in belt edge damage.
85% of conveyor maintenance is a result of fugitive materials escaping from transfer points.
2014 Pit and Quarry Conveyor University Handbook – MSHA quote in chapter 10
Maintenance personnel should receive advanced conveyor training.
CREDIT: MARTIN ENGINEERING
Sometimes training is on a specific piece of equipment with the goal of creating trainers who can educate the rest of the maintenance department. This approach works well with certain types of equipment but ends up with one or two motivated and well-versed technicians who can troubleshoot.
A mechanic trained in installing problem solving components will run into a myriad of physical constraints. First, the original conveyor design and subsequent modifications can make it impossible to install equipment according to the manufacturer’s instructions without a complete redesign. Second, often structural obstructions or conveyor arrangements do not allow enough room for installation, clear views for inspection, or access for safe and easy maintenance access according to industry standards.
Conveyor design training for engineers and mechanics is critical so they can diagnose problems with an understanding of fundamental design methods. Systems are incrementally modified over time to minimize problems when belt speed and capacity exceed the original design specifications. No two conveyors are identical and even twin conveyors side by side can act differently. So, adhering to standard design methods allows one technician to make these slight adjustments and another technician to recognize the intentions even without the prior technician present.
Training alone rarely results in meaningful actions to improve conveyor performance. When management understands the clear links between safety, cleanliness, and productivity, it is much easier to turn training into results. There are many variations of how this can work, but most success stories have the following common threads:
• Basic training in conveyor hazards and the methods for controlling fugitive materials.
• Training in conveyor design fundamentals and the root causes of common problems.
• Management participation in the training to show support.
• A pilot program and measured results.
• A long-term plan implemented from a successful pilot program.
A walkdown of one or two “problem belts” and a review of goals the day before the training help the instructor focus on site-specific problems and management’s expectations. The survey and interview usually take a few hours to half a day. The goal is for the instructor to have actual examples to show the class their problems are not necessarily unique. An experienced teacher will most likely have examples showing similar problems and their solutions.
The first day typically starts with reviewing the typical problems and getting the class to talk about their specific challenges. The class identifies a couple of problem conveyors and the class splits into small teams. Each team can look at the same problem or select different ones. Photos and videos of the issues are taken to be used in the problem-solving discussions. The rest of day one and the start of day two review basic design principles that relate to the problem conveyors. The discussion centers on possible root causes and solutions. Once the teams reach an agreement on a way forward, they prepare a short presentation with the help of the instructor, using their actual conveyor problems and the knowledge they gained. The presentations may also include an estimate of the cost of the proposed solutions.
Management’s role
At the end of day two, management is invited to listen to the team presenta-
tions and solutions. By participating in the class presentations, management shows a commitment to making improvements and has an opportunity to ask questions. The trainees, by making the presentations, show the knowledge they gained and support for the proposed solutions. The photos, videos, and inspection sheets help shed light on issues and solutions crews experience every day. It is critical at this step that the managers who attend the presentations have the authority to act on the proposals and are willing to commit to a pilot program to prove the theoretical results can be turned into reality.
One or more conveyors are selected for a trial program. While it is normal to select the “worst” conveyor, keep in mind that half measures do not get half results, so consider the project’s scope. Once a conveyor has been selected, detailed proposals for retrofit can be obtained. An experienced person from the selected equipment supplier should overview the designs, offer feedback, and supervise the installation. Either outside contractors or in-house personnel can be used. Sufficient downtime must be allocated to properly modify the conveyor.
Measuring results from improvements is important but relatively easy to do. Photos and videos of before and after must be taken. Dust levels are measured using common instrumentation, spillage can be measured by placing buckets or trays in appropriate locations, and carryback is measured by placing a tarp under several return idlers close to the discharge pulley. The collected fugitive materials are weighed for comparison after the conveyor has been modified. Dust and spillage sampling locations should be marked so the tests can be accurately repeated after retrofitting and an improvement percentage can be calculated.
The length of time for collecting samples can vary from a day to a week and should give a good representation of the average or typical operating environment and weather conditions. It is
important to keep the dust monitor running even if the conveyor is running empty, as maximum fugitive dust levels are often detected when running conveyors empty long enough that the carryback dries out and becomes airborne. Usually, the results of the pilot program are immediately noticeable, but there is a temptation to assume the problem has been fixed and to revert to delaying maintenance without follow-up maintenance, causing the results to deteriorate. Therefore, the test period should extend to the next scheduled maintenance shutdown with periodic inspections and adjustments made by the equipment supplier in the interim to ensure optimum efficiency.
To demonstrate the benefit of safety to a company’s bottom line, the U.S. Occupational Safety and Health Administration (OSHA) created the online tool “$afety Pays,” which uses company-specific economic information to assess the potential economic impact of occupational injuries on that firm’s profitability. The program estimates direct costs (claim cost estimates provided by the National Council on Compensation Insurance) and indirect costs (provided by the Stanford University Department of Civil Engineering) and weighs them against financial details supplied by the company.
Conclusion
Experience has shown that the motivation to act developed in the classroom often defaults back to prior habits.
Sometimes it is a lack of funding, an understaffed maintenance department or a “runtill-broke” mentality. The pressure to get back into production overwhelms the training that emphasizes the understanding of the root causes of inefficiency and injuries such as fugitive materials. A production-at-all-costs approach
means the problems and safety concerns never go away, and employees just must accept the poor performance and added risks, which demoralizes them. It is incumbent upon management to take the safety and maintenance training as seriously as the staff, listen to the concerns of employees, and fix the problem correctly the first time. As research has shown, companies that prioritize safety, training, and updating equipment enjoy fewer safety incidents, less regulatory oversight, higher productivity, and greater long-term profits.
R. Todd Swinderman is president emeritus of Martin Engineering.
SERVICES
Mineral Exploration
Aerial Construction
Drill Moves
Airborne
Geophysics
Lake Sampling
Thermography
Photogrammetry
Terrain Analysis
FLEET
AS 350 Series (5-6 passengers)
D, BA, BA+, B2, SD2, B3
Bell 212HP BLR (14 passengers)
Multiple drone platforms
Infrared and long range cameras
SERVICES
Mineral
Aerial
Drill
Airborne
Geophysics
Lake
Photogrammetry
Terrain Analysis
And much more...
FLEET
AS 350 Series (5-6 passengers)
BA+, B2, SD2, B3
The new DR411i combines exceptional productivity with innovative iSeries technology.
With Sandvik’s new DR411i, you’ll reap the benefits from a compact drill that’s powerful, precise and productive. Paired with the innovative, data-driven technology the iSeries is known for, it’s as intelligent as it is capable. Making anyone adding it to their operation look pretty smart. Discover how the new DR411i drill from Sandvik can increase your productivity, visit rocktechnology.sandvik