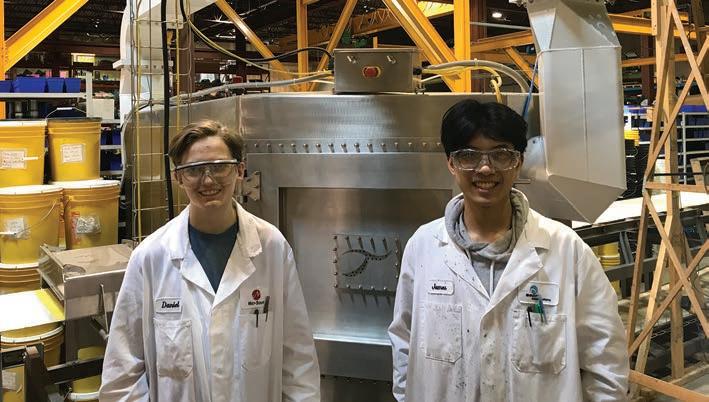
4 minute read
Microwave processing of ore
Finding innovative solutions that lower energy use in mining processes will reduce greenhouse gas emissions, improve productivity, and help the mining industry become more competitive. Microwave technology is an emerging process which can help improve the energy efficiency of mines not only in Canada but around the world.
A B.C.-based mineral processing company, Sepro Mineral Systems, is developing this cutting-edge technology for crushing and sorting pre blasted ore and is performing commercial bench and pilot scale test work for customers. Sepro are the world’s experts in microwave-assisted comminution and sorting.
Comminution or particle-size reduction is the crushing and grinding of rocks. It is typically the first stage of mineral processing. This stage liberates minerals from one another before separation and is one of the most energy-intensive processes in the mining industry. Comminution consumes 50% to 70% of the energy used in mineral processing and can be as little as 1% efficient as significant energy is lost to heat, vibration, and noise.
The technology combines microwave-assisted comminution and multi-sensor ore sorting and selectively targets valuable minerals via differential heating of the valuable and gangue phases causing microfractures along the phase boundaries. This allows for a reduction in ore competency and an increase in the liberation of the valuable mineral phases. The treated ore can then be sorted using multisensor sorting.
Research and development have been conducted since March 2020 as part of the “Crush it challenge!” The national competition was launched in 2018 by Natural Resources Canada for applicants to develop the best comminution energy breakthrough. In June 2022, Sepro and its partners won the $5-million grand prize. Sepro collaborated with several partners such as Gillian Holcroft from CMIC (Canada Mining Innovation Council) ReThink Mining, and Glencore Canada. Their cleantech solution, CanMicro, exceeded the challenge guidelines, reaching 46% energy savings across several commodities and improving mill throughput.
According to the Minister of Energy, Jonathan Wilkinson, “Improving energy efficiency supports increased productivity and decreased costs at mining sites, while also reducing environmental impacts and harmful emissions.”
Commercial bench scale test work has been performed for clients since May 2021. Most ores being tested are from Canada, but testing has been done on ores from around the world.
In the last year, the microwave heating behaviour database has been expanded from 45 to over 90 unique materials rang- ing from ores, concentrates, and tailings. The database is one of the largest pertaining to the microwave treating of ores. Treated commodities include nickel, copper sulphides, lead and zinc sulphides, gold sulphides, some PGE (platinum group elements) and REE (rare earth elements), and kimberlites. The treatment of nickel and sulphide ores has been particularly successful. Ores with too many reflective metallic phases are not suitable for microwave treatment.
Microwaves can theoretically transmit energy to heat microwave-absorbing materials in a few seconds in a continuous process. When ores are treated by microwaves, valuable minerals usually heat more easily than waste minerals. Materials with semi-conducting properties, such as sulphides and different metal oxides, heat very well in response to microwaves. Ores containing these minerals include chalcopyrite, pentlandite, galena, pyrite, pyrrhotite, and magnetite.
Silicates and carbonates and other gangue minerals typically do not respond to microwaves. Some minerals, like silica, are microwave transparent, which means that the microwaves pass through them, and nothing happens. Other highly magnetic materials are too conductive, and microwaves will be reflected off them.
Ore texture is also important. Ores responsive to microwaves are well-dispersed throughout a non-heating gangue yield improved mineral liberation and reduced ore competency. Ores with a coarser texture such as a veiny texture tend to respond well to microwave-assisted sorting.
As ores are usually composed of several phases containing different microwave properties, some phases heat while others do not. This unique heating behaviour creates thermal stress and fractures along grain boundaries of target and waste minerals. These microfractures reduce the need to grind the ore as finely, preventing the loss of valuable minerals to fines and reducing slimes. The thermal expansion of mineral grains gives rocks containing valuable minerals a thermal signature.
The sorting algorithm uses this heating
CONTINUED ON PAGE 36 information to reject barren rocks prior to grinding. The result is reduced ore competency and improved mineral liberation after grinding, which allows for a coarser grind compared to untreated ores.
Even with limited mineralogical data, the extensive database of microwave responses for various ores allows staff to assess the potential benefits for projects.
First, a bench-scale evaluation is conducted on an ore sample. This evaluation includes two phases of testing. In the first testing phase, a microwave heating test is performed using a bench-scale microwave unit. This test is used to establish a microwave heating behaviour curve.
Chemical and mineralogical analysis is performed on the sample, and this data is compared with the database to determine the amenability of the ore. If the sample responds positively, it moves on to the second phase of testing.
Next, comparative downstream pro ing, gravity concentration, flotation, and cyanide leaching. Using the test data, a customized testing plan is created. ducted since the 1990s, so it is a modern technology with no working process. In the last five to 10 years, there has been increasing interest in going from bench testing to using tech on an industrial scale.
The main issue of working with the technology is the fundamental understanding of how well the material can be treated by microwaves.
Adjacent industries like food processing and cannabis have more homogenous materials. In mining, there are many diverse types of rocks with different shapes, particle size, and mineralogy, which makes testing much more complicated.
In terms of safety, microwave technology uses non-ionizing radiation which does not cause cancer. However, if the microwaves escaped, employees could be burnt. To prevent this, the microwaves are encased in a steel box. For pilot scale testing, attenuation tunnels contain choke pins to prevent the microwaves from escaping.
Some of the benefits include increased mill throughput, enhanced mineral recovery, and improved concentrate grades. There is less milling capacity required and less fine tailings to pump and manage. Other benefits include the potential to increase the grind size, reduce the loss of valuable minerals to fines and reducing slimes, improved flotation and leaching recoveries and reduced reagent use.
The coarser grind size, improved mineral liberation, and higher ore grade can improve downstream processes, such as gravity concentration, flotation, cyanidation, dewatering, and tailings management. Other benefits of microwave treatment include reduced water use and