
4 minute read
Three ways vibrating screen diagnostics help your bottom line
The new year is a perfect time to consider it
Vibration analysis helps operations achieve maximum productivity levels through real-time data analysis – information that producers can use to optimize screening performance and increase their production.
CREDIT: HAVER & BOECKER NIAGARA
The start of the year offers an opportunity to consider how new practices and technology can help your bottom line. In 2022, you may have read articles from Haver & Boecker Niagara in the Canadian Mining Journal on several topics, including an in-depth look at vibrating screen diagnostics and how the technology can maximize plant productivity. An article in the June/July issue gave information on how partnering with a technical OEM for equipment monitoring through diagnostic tools (in addition to regular service) results in a comprehensive service program designed to optimize plant flow, boost production, and increase profits, keeping the heart of an operation at optimum health. Finally, in October, we discussed how the development of the double eccentric screen and other screening technology provides operations with innovative and cost-effective ways to increase profits and efficiency.

Vibration analysis can help detect abnormalities that are impossible to spot visually before they cause catastrophic failure. Even small irregularities can reduce screen performance or lead to expensive future
breakdowns. CREDIT: HAVER & BOECKER NIAGARA
As you start off the new year, consider some quick tips on diagnostics technology, which has reached the point where it is possible to monitor vibrating screen performance to unprecedented levels of detail in real-time. Mining and aggregates producers need reliable equipment. Unplanned maintenance and inefficient equipment can reduce productivity and negatively affect profits. That is why more and more turn to diagnostics to prevent issues with operational efficiency. Innovative vibration analysis technology uses advanced diagnostics to help operations achieve maximum productivity.
Some systems have eight tri-axial sensors that fasten to key areas of a vibrating screen to detect and wirelessly transmit data to an industrial-grade tablet on-site. Measurements from these systems can include orbit, acceleration, deviations, and other important data points that indicate the condition of the machine. The instantaneous information can reveal irregularities that result in diminished performance, decreased efficiency and possible safety risks. The data
can be transmitted to a vibrating screen manufacturer’s trained engineers to analyze and interpret it. They report the results to the producer, including recommendations to improve vibrating screen efficiency.
While everyone agrees that efficiency is a good thing, consider the following specific ways vibration analysis can benefit your bottom line from the start of 2023:
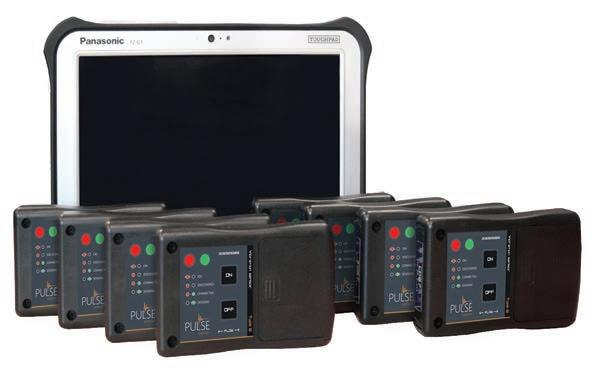
1.Greater safety
Experienced producers know a safe environment is a productive one. Vibration analysis provides the information needed to keep machines running properly and safely. Thanks to the technology’s Wi-Fi capabilities, sensors transmit the collected information to technicians’ tablets as they stand a safe distance from the machine, collecting and monitoring screen performance data out of harm’s way.
2.Less downtime
Vibration analysis can help detect abnormalities that are impossible to spot visually before they cause catastrophic failure. Even small irregularities can reduce screen performance or lead to expensive future breakdowns. Vibration analysis allows producers to manage performance problems before they occur through preventative maintenance.
Consider the example shared in a previous article about a B.C. producer that worked with an OEM to conduct a vibra-
Diagnostics technology has reached the point where it is possible to monitor vibrating screen performance to unprecedented levels of detail in realtime. Innovative vibration analysis technology uses advanced diagnostics to help operations achieve maximum
productivity. CREDIT: HAVER & BOECKER NIAGARA
tion analysis on a vibrating screen that appeared to be healthy. The resulting data indicated a problem early, which saved the producer money in downtime and repair costs.
3.Better productivity
Vibration analysis helps operations achieve maximum productivity levels through real-time data analysis; i.e., information that producers can use to optimize screening performance and increase their production. Additionally, some vibration analysis setups save time by including multiple sensors, allowing for a comprehensive look at the machine at the same time compared to options that have one sensor that must be moved to multiple parts of a machine for a full reading. When every minute counts, the productivity gained, and time saved with the multiple sensors is a significant consideration for producers. The systems also store a vibrating screen’s historical data for easy comparison over time and insightful troubleshooting.
Diagnostic tools like vibration analysis can do wonders for improving and maintaining vibrating screen performance and reducing maintenance costs and downtime. Beginning the new year with considerations such as these will allow producers to have a holistic view of their operation and to be more aware of areas that, with a few changes, may drive significant increases in revenue while minimizing costs. Look for a manufacturer able to provide a diagnostics system along with the expertise needed to make recommendations to improve productivity, efficiency, and your bottom line. CMJ
Wilm Schulz is the parts and service manager at Haver & Boecker Niagara, a leading provider in screening, pelletizing, and mineral processing plants and systems.
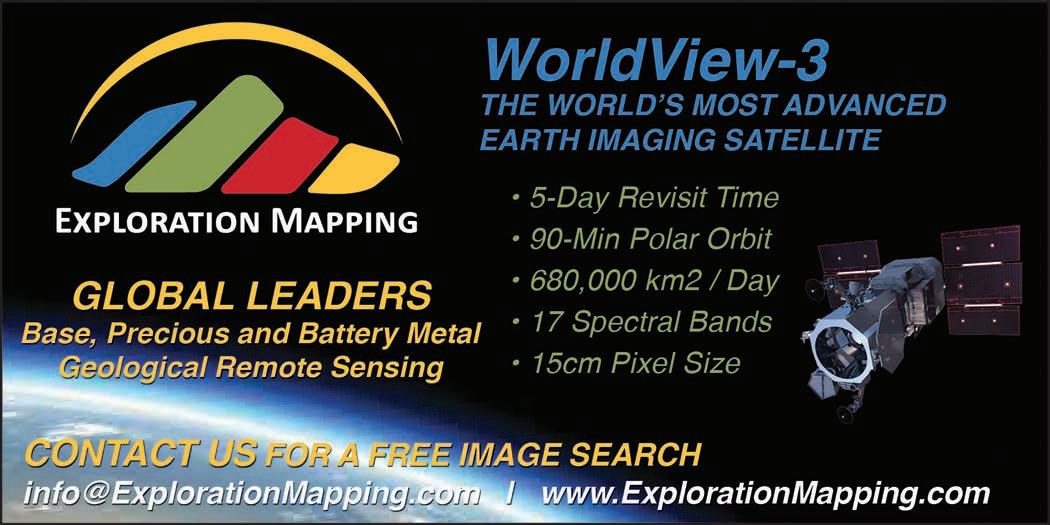