
4 minute read
Creating value from waste through tailings reprocessing
Creating value from waste Metso discusses why tailings reprocessing is key to the mining sector’s future
By Niclas Hällevall
For some time already, ore reserves have been depleting with mines going deeper. Huge volumes of waste, or tailings, are being generated with the growing need to process more and more ore. And recent devastating tailings dam failures have brought safety and environment concerns to the forefront, thereby increasing the pressure to search for alternatives. There have also been stronger regulatory compliances affecting the social licence to operate in many regions.
Though the industry has been taking positive steps to become more responsible towards local community welfare with optimum utilization of natural resources, many significant challenges still remain.
Metso has launched a new tailings management concept catering to these needs. It offers miners a sustainable way to handle tailings and a new value-creation model through the easy reprocessing of tailings.
Need for a future ready solution There are millions of tons of tailings being discharged today and billions lying in legacy dams. In fact, a lot of operational and closed tailings facilities have residual mineral values, or secondary metals that might not have been of interest in earlier times.
As their orebodies are continuously shrinking, mining companies are looking for viable opportunities to reprocess existing waste. With the advent of novel technologies, mining companies are now figuring out ways to extract valuable metals from tailings.
It is well known by the mining industry that the cost of tailings management and reclamation are also becoming increasingly significant factors for sustainable and economically viable mining and long-term survival.
While water scarcity has been a driver towards considering dry tailings technology in the past, the question now is around responsible use of resources.
“At Metso, we are challenging the conventional way of thinking, while changing the industry view around tailings management in mining. Our emphasis is to include reprocessing of tailings as part of the overall solution,” says Rodrigo Gouveia, vice-president, Tailings Management Systems at Metso.
In practice, it is about making the right choice. Mining companies do not just want the most technically suitable equipment to dewater tailings, they want a future ready solution that is able

to transform legacy practices and takes the end-of-mine strategy to a new level.
Maximizing value from waste With progressive technology and a more environment friendly vision, mining companies have been exploring effective waste management methods to handle mine tailings. Driven by both stored mineral value and reclamation, reprocessing offers an interesting proposition for long-term tailings management.
“In some gold, copper, iron and coal mines, it’s impressive how rich those tailings are,” Gouveia says. “We have conducted studies recently that tell us that in some cases reprocessing one unit of tailings to collect the valuable material can be up to three times more cost-effective than processing virgin material.”
Metso believes that this in a way helps mining companies to reduce possible water losses as well as clean up the existing tailings dams or eliminate them completely, while providing an opportunity to convert mine waste to value.
“Reprocessing is not only a means to sustainability, it’s a huge business opportunity at the same time,” Gouveia says.
With reprocessing, the mining industry can set the agenda to transform tailings ponds from a liability into an asset.

Metso offers complete solution for reprocessing of tailings dams through its expertise in comminution and beneficiation solutions. A standard method of reprocessing involves dragging tailings from an existing dam back to the concentrator and using required mineral processing solutions to liberate the valuable metals. The discarded tailings are then dewatered and dry stacked, and the water recycled within the plant or properly disposed back to nature.
Gouveia adds: “Sustainable and productive mining solutions like reprocessing helps in creating a shared value for mining companies, local communities and the entire ecosystem.”
Metso firmly believes that within a few years, dry tailings will be the new standard in the mining industry. And a disruptive practice like reprocessing can virtually eliminate the need for tailings ponds in the coming years, as well as lowering the risk of dam failures and groundwater contamination.
Making the right choice A conventional view is still dominating the discussion around smarter and efficient management of mine tailings. The way tailings are handled can have a longterm impact on the mines’ economic
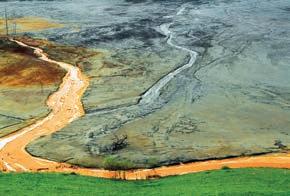

efficiency as well as on the ecology.
Designing and commissioning a future-proof tailings management system requires a totally new mindset.
“As futuristic organizations, we should embrace competitive and viable solutions that not only enhance productivity but create a positive difference to the environment and natural resources,” Gouveia says.
Treating tailings ponds as a potential source for converting “waste to value” would surely help in changing the way the mining industry has been perceived all these years. “It is time to replace the old and negative risk-avoidance position with a new value creation model,” Gouveia says.
With reprocessing technology, Metso commits to bring a step change in managing large volume of tailings, while ensuring efficient, sustainable and economical operations. CMJ
Niclas Hällevall is vice-president, Processing Systems, at Metso.
Top left: Metso’s dewatering technology, including its VPX filter, which can recover up to 90% of water from tailings. CREDIT: METSO Top and bottom right: Tailings images, including dry-stacking of coal tailings at bottom right. CREDIT: METSO/SHUTTERSTOCK
#TheMetsoWay