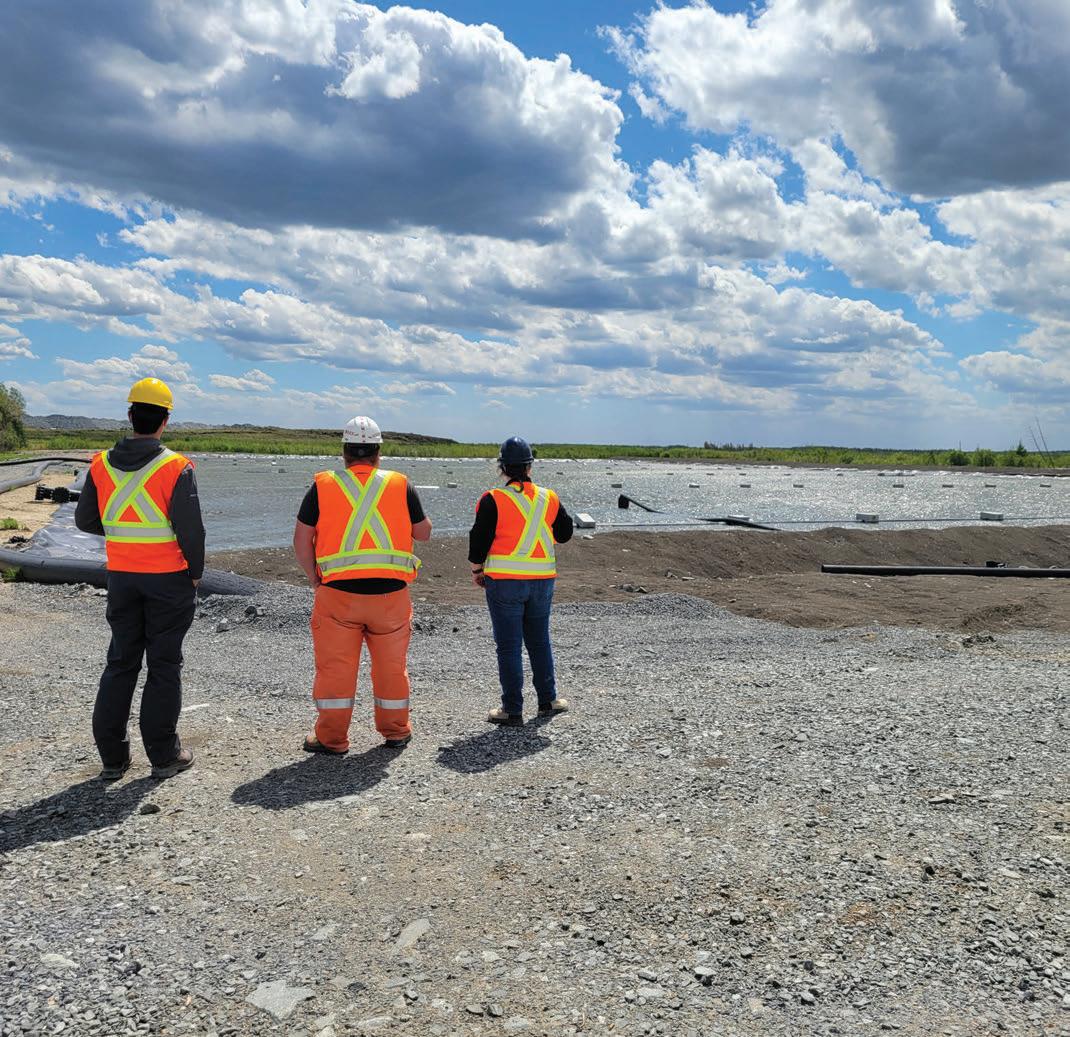
5 minute read
Five things you need to know about modern 'passive' bioreactors
A modern in-ground BCR operating in Ontario treating water from a tailings pond. CREDIT: MAVEN WATER & ENVIRONMENT
By Monique Simair
Biochemical reactors (BCRs) have a longstanding history in the environmental field; however, they have only been recently employed as a tool in water treatment of the mining sector. As this field of technology continues to grow, bioreactors are gaining interest in the world of “passive” water treatment and the technology is modernizing at a rapid rate. These passive bioreactors are built into the ground and designed with the intention to require little operator intervention. There are more than a dozen names and acronyms in use to describe different bioreactors depending on the style or brand of system. The generic term “BCR” will be used here for simplicity, this includes types such as mixed-media reactors and gravel bed bioreactors (GBBRs). Here are five things that you should know about modern in-ground BCRs.
1 IT’S NOT JUST PASSIVE OR ACTIVE
There are many approaches to designing in-ground BCRs. Designs must be matched not only to what is being treated, but also to site-specific objectives. Although a “walk away” method is sought after in water treatment, it is usually more reasonable to set a goal of operating as passively as possible. With BCRs, design measures can be put in place to adjust operations as needed, hence the modern language term “semi-passive” (as opposed to completely passive). Flexible operating modes can be adjusted depending on site specific variability, such as seasonality, flows, chemistries, and so on. These factors require modern in-ground BCRs to be supplemented with nutrients and other reagents as needed. Systems are also plumbed with the ability to flow water in different directions, making it possible to clean the system when necessary.
2 SOMETIMES TEMPERATURE MATTERS, SOMETIMES IT DOESN’T
Some constituents are directly transformed by the microbes in the BCR (such as cyanide, thiocyanate, ammonia, biological oxygen demand, nitrite, nitrate, and sulphate). For this reason, the treatment of these constituents is temperature dependent. This means that the BCR must be sized accordingly. Although cold temperature bioreactors for these constituents may need to be sized larger, there are several examples of BCRs operating with water barely above freezing. In contrast, many metals and metalloids are treated indirectly in BCRs by the bacteria using coupled biogeochemical processes. This means the microbes create compounds in the BCR, which in turn treat the water. Under the right conditions, microbes can create stockpiles of these treatment compounds in the BCR (which we can measure and track). This ‘stockpiling’ of materials makes it possible to design and operate BCRs effectively in cold temperatures when treating metals and metalloids, with change in temperature having little effect.
3 THE “BLACK BOX” IS OPEN AND UNDERSTOOD
One of the greatest misconceptions that remains is that BCRs are a “black box.” BCRs are more complex than conventional physical and chemical water treatment due to their biological component. However, they are not purely biological. BCRs function through coupled reactions including physical, chemical, microbiological, and biogeochemical reactions. These must all be considered when selecting appropriate substrates and reagents for a system. The use of reagents should be purposeful and targeted. For example, the electron stoichiometry of the system should be calculated to ensure adequate treatment can be achieved. A BCR design should include not only the the hydrology and list of components, but the reactions of the reagents and components, lifespan, and how treatment can be manipulated and augmented as needed. Whether active or passive, BCRs are most manageable when the components are separated into a series of purposeful units. Separating treatment functions allows each aspect to be adjusted as needed depending on site-specific changes over time. The microbial component of a system is also no longer a mystery. Commercial fee for service genomic-based microbiology profiling has been available in Canada since 2012, with a handful of providers now in operation across North America.
4 PILOTING HAS PURPOSE
Pilot-scale testing should be purposeful, not exploratory. The BCR design should be sufficient to explain how the system works and how it is expected to react under a range of conditions including expectations of what happens when chemistries, flows, or temperatures change. A semi- passive or passive system such as a BCR must incorporate this sort of flexibility into the design elements, whereas active treatment systems use reagents, heat, and electricity to manage these changes. For this reason, passive and semi-passive BCRs require somewhat longer site-specific pilot-scale testing than active treatment does. A pilot-scale testing program should be specifically designed to address regulatory questions or site-specific aspects. These might include aspects that affect construction, operation, and bonding costs. The BCR pilot-testing program can be run onsite or at a dedicated temperature-controlled facility, depending on the project needs. Pilot-testing should evaluate the ability of the system to respond to site-specific changes and to test the limits of the system under critical scenarios. Furthermore, a pilot-scale test should find out the limits of the system and what it can recover from. For this reason, pilot-scale testing is often best done in modular test units (not built into the ground), to enable rapid testing and replacement of units if needed. This process allows for a site-specific operating plan, maintenance schedule, and adaptive management plan to be customized for the site and system design.
5 THINK BEYOND TREATMENT
Modern BCR design and operation goes beyond just thinking of treatment. A few additional points to consider are:
> Does the operating plan have internal monitoring points and parameters to assess if it is operating as intended?
> How will the BCR be monitored and managed long term? Will local personnel be trained? Is it set up for remote monitoring and management?
> How does the BCR fit into the site-wide water management strategy and mine life cycle?
> What happens to the treated constituents? Where do they go? What is their form? How stable are they? Under what conditions are they at risk of re-releasing? Does the BCR design take these aspects into account?
> Have the BCR design and operating plans incorporated hydrologic and chemistry changes through the mine life cycle in addition to the lifespan of the BCR?
> Can the BCR be readily modified or adapted if there are unexpected changes in the water quality, water volumes, or water quality objectives?
> Can the BCR be retrofitted or modified to incorporate emerging technology?
> Are there performance guarantees or other fee structures that align the technology provider with performance outcomes?
Knowledge about BCR design and operation has changed greatly in recent years and is being applied at mine sites across North America. It is critical that your BCR design and management is up to date on technology advancements that can help save time and money on the design, permitting, and operation of these systems.
Dr. Monique Simair is a globally recognized leader in passive and semi-passive water treatment for the mining sector, including bioreactors, constructed wetlands, in situ treatment, and contaminant source control methods. She is the founder and CEO of Maven Water & Environment (www.mavenwe.com) and can be contacted at monique@mavenwe.com.