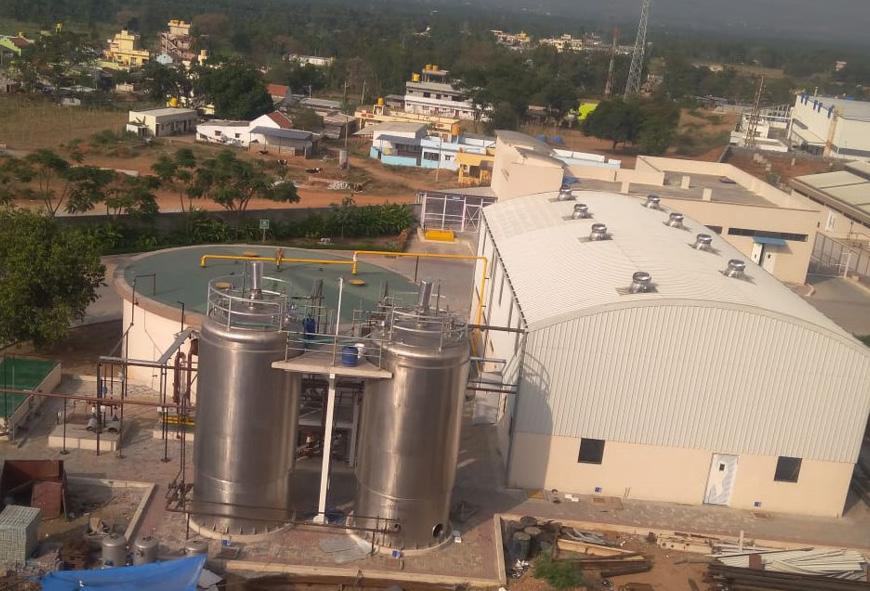
27 minute read
Biogas production from pharmaceutical
Biogas production from pharmaceutical Waste
Mailhem Environment Private Limited has designed and constructed an anaerobic treatment plant for one of the bulk drug manufacturers, capable of treating fermentation broth samples containing high levels of BOD, COD & TSS. In this case, the split between biomass retention time and hydraulic retention time is critical to the success of anaerobic treatment: a M-UASB reactor (our indigenous reactor) followed by an external sludge separation system with biomass re-circulation. This solution offers the advantages of High organic loading capacity & highly settleable granular biomass with ease to operate & maintain. Other advantages are the small footprint and the lower anaerobic effluent TSS values, facilitating the aerobic post-treatment
Anthem Bio-sciences Pvt Ltd manufactures drugs using Soya Flour, Peptone, Tetrose and Cultures like - Yeast, Fungus as a primary raw material. Fermentation is the core process used to con-
Sr. No Tests Unit Sample – 01 Without Solvent Sample – 02 With Solvent
1 Total Solids %
2 Total Volatile Solids @ 550°C
3
COD
4 BOD (@ 27°C, 3 days) 5 Total Kjeldahl Nitrogen as (N) 6 Total Organic Carbon 11 . 9580 10 . 3362
10 . 5715 8 . 8298
17 . 6268 41 . 7078
7 . 5803 20 . 2405
1 . 0996 0 . 8617
4 . 7471 9 . 8171
vert these raw materials into drugs intermediate. However, this process generates massive amount of fermentation waste, which can cause damage to the environment due to the high organic load. In this regard, Anthem Bio-sciences had approached us to design a suitable upstream treatment process prior treating it in their effluent treatment plant.
We have the technology and expertise to offer turnkey solutions for treating in-situ process waste. Subsequently, the challenge was taken up by our R&D unit to study the process waste and design the biological treatment by setting up a pilot-scale plant. The objective of the study was to maximize the recovery of biogas while maintaining an optimal retention time.
WORKING PRINCIPLE
1. The fermented waste broth requires pre-treatment to prepare it for the anaerobic
Biogas Magazine | Edition 19 | 13 treatment process for the generation of biogas. Conditioning of the feed slurry occurs in the slurry tank via a recirculation step that mixes it with recycled anaerobic effluent. . Furthermore, the pH-value and temperature are regulated and nutrients are dosed as needed to achieve optimal anaerobic biomass growth conditions in the M-UASB reactor.
2. The conditioned feed slurry is then pumped to the M-UASB reactor in constant, continuous flow A special Influent distribution system ensures that the Influent is equally distributed over the entire reactor surface area. Thus, the Influent passes through a dense anaerobic granular biomass bed, where the biological conversion process occurs, transforming the organic waste’s COD load (Chemical Oxygen Demand) to biogas.
3. Our experts modified the indigenous design of the M-UASB reactor’s to allow for a longer contact time between bacteria and organic material. The M-UASB anaerobic digester is specially designed with internal baffles, partitions and launders (proprietary) for anaerobic treatment. The sludge blanket is comprised of microbial granules which are small agglomerations of microorganisms that resist being washed out in the up flow due to their weight. The microorganisms in the sludge layer degrade organic compounds. As a result, biogas is produced that is primarily composed of methane and carbon dioxide. Without the assistance of any mechanical components, the rising bubbles mix the sludge. Sloped walls deflect material that reaches the top of the M-UASB downwards as clarified effluent/overflow.
4. Our propriety moules, which are internally installed at the top of the reactor, separates the treated slurry from the produced biogas.
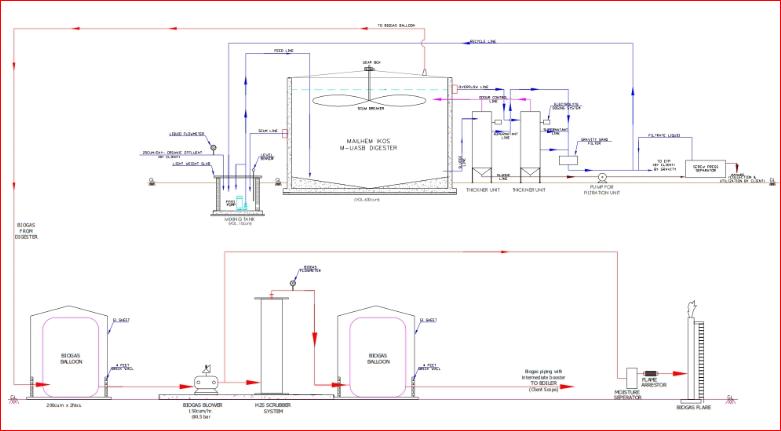
The biomass settles to the bottom of the reactor, whiles portion of the treated effluent is recycled, and the rest is processed to separate solids and liquid digestate. The digestate solids will be transported to a sludge drying area for further processing into organic manure, while the liquid digestate will be treated in an Effluent Treatment Plant
Treatment Capacity
Biogas Magazine | Edition 19 | 14 is chemically scrubbed as a treatment procedure under controlled conditions, and is used as a source of energy for capital consumption, specifically boiler and cooking application. vol%) which can be used for heating, upgrading to natural gas quality, or co-generation of electricity and heat. Digestion installations are technologically simple with low energy and space requirements.
The anaerobic process is an excellent method for the treatment of such high strength fermentation broths.
The focus was to generate biogas from the waste at the fermentation unit, which could replace or offset the
Up to 25 cum/day
Type of Effluent
Fermentation Broth after process
Nature
Water base, thick slurry
Biogas Produced
Biogas Equivalent to LPG
Water Required
Area Required
Approx. 2250 -2500 cum per day at calorific value of 4800 - 5200 kcal /cum
Approx.1000 – 1125 Kg per day of LPG
Approx. 20 CUM / day
1500 sq. m.
(ETP). 5. Biogas is collected and piped to a biogas balloon. It The generated biogas is a mixture of methane (55-75 vol%) and carbon dioxide (25-45
Sameer Rege
CEO
Mailhem Environment Pvt. Ltd.
processing industry’s demand for grid electricity and LPG for thermal energy.

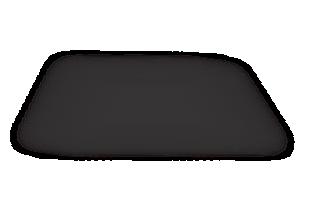
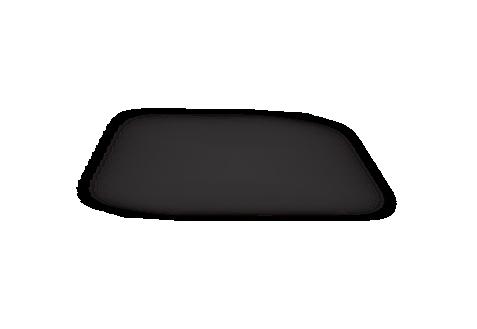

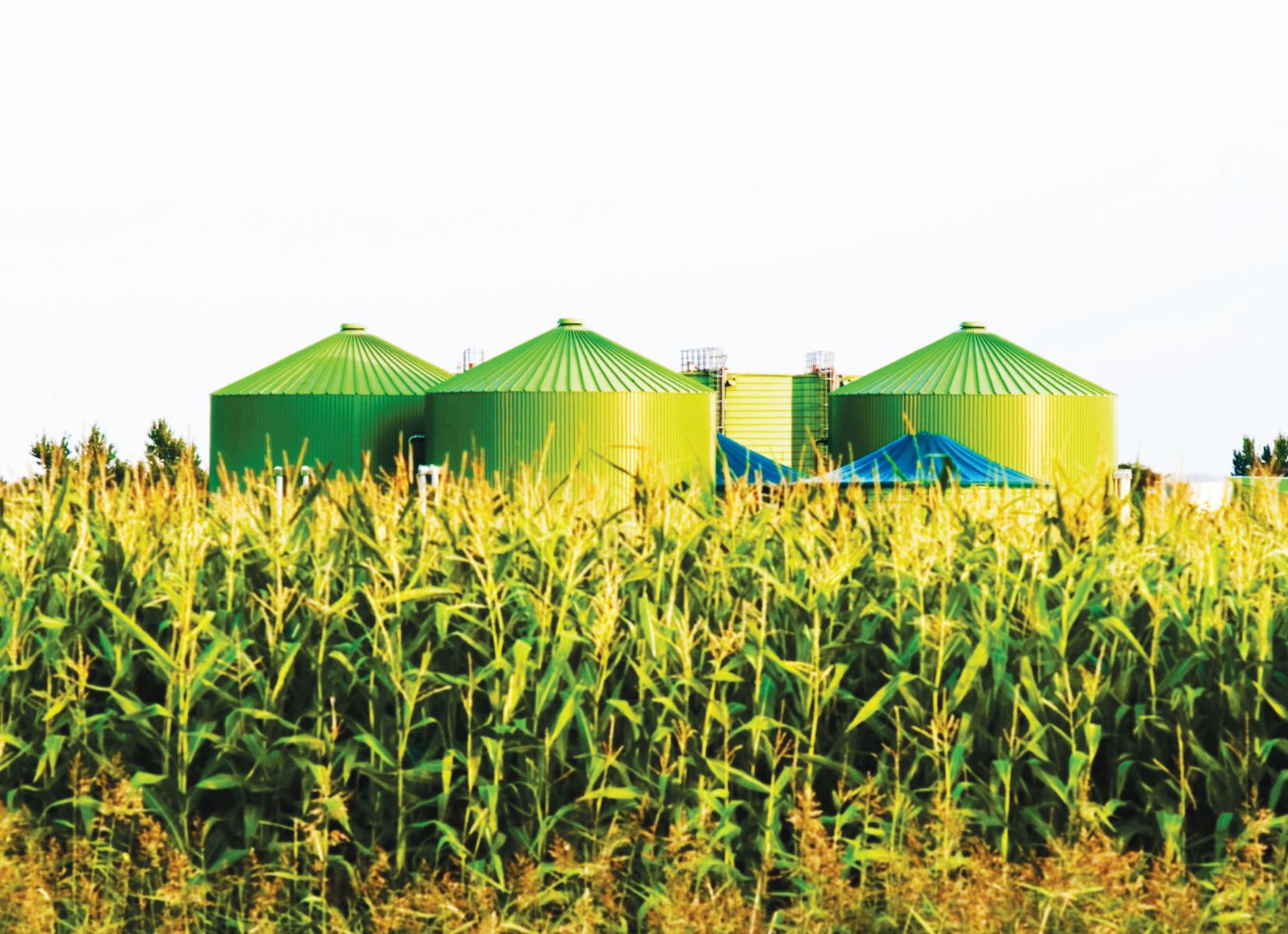
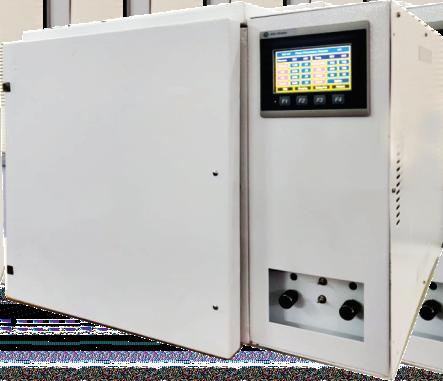
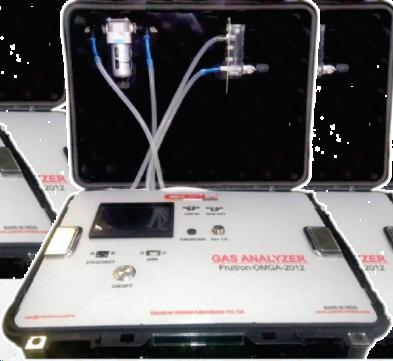
Food waste depackaging and separation functions and recent industry advances
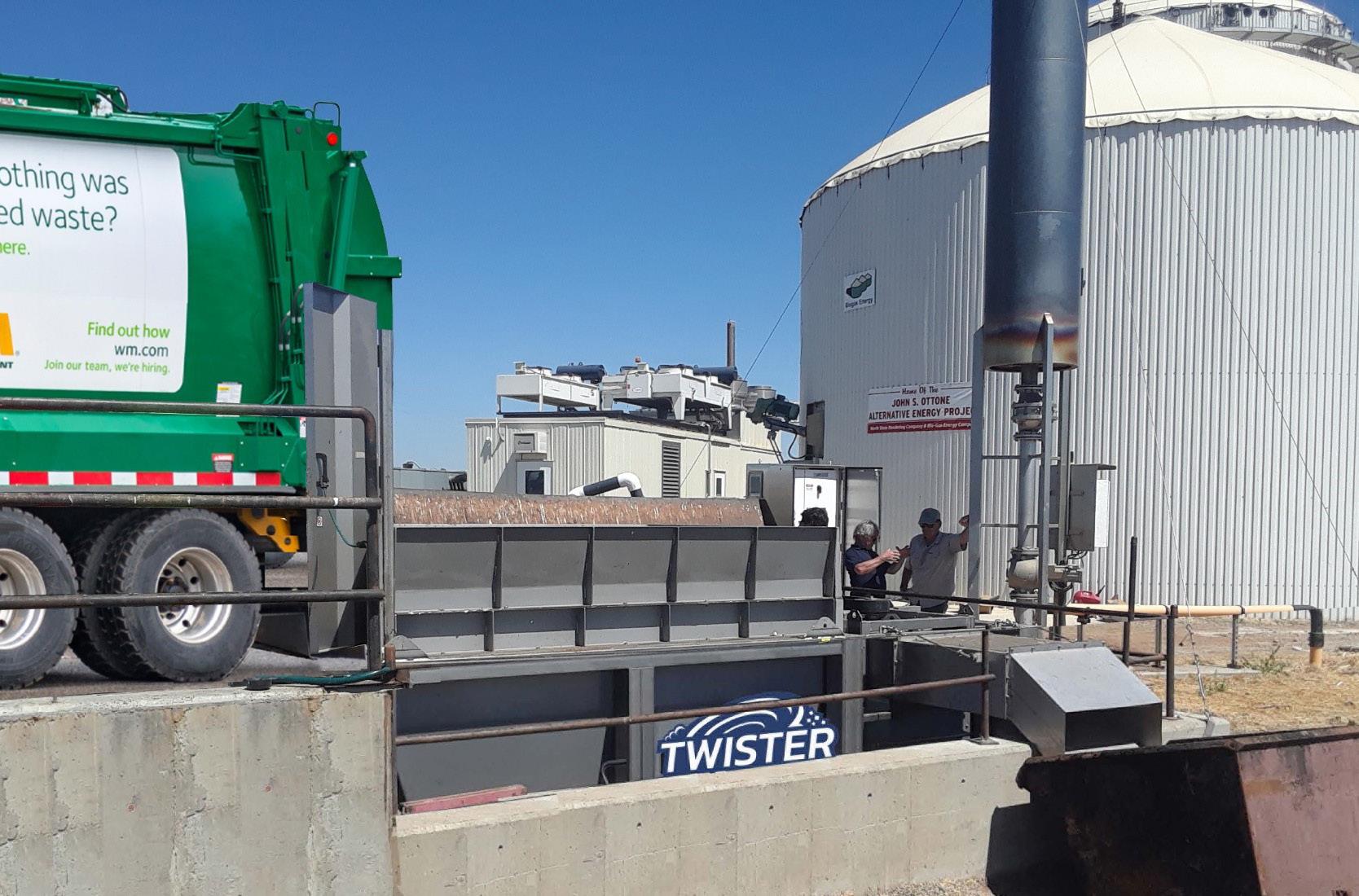
This article discusses the requirements of a good food waste depackager and separator. We describe the equipment’s functions and introduce a novel technology for increasing the purity of the output stream It accomplishes this through the use of fewer moving parts, less energy, and a smaller system footprint.
Improved recycling technology for plastic is long overdue. The public is becoming more aware of the environmental damage that plastic packaging causes. Despite its unmatched ability to keep food fresh and safe to eat, plastic is losing popularity with the public. Boris Johnson, the UK Prime Miinister, stated “Plastic recycling does not work” (BBC October 2021). The good news is that a new generation of this vital plastic recycling technology has emerged wherein clogging and component wear issues have also been addressed.
Continue reading to learn about the capabilities of this equipment , how it could be improved, and how one company is addressing the issue through a case study in India.
Depackaging and separator functions
Fig. 1 - The compact Twister accomplishes depackaging and separation activities in one unit.
The purpose of this equipment is to open all bags and containers and separate the organic material. The challenge has evolved to include doing so in the most environmentally friendly manner possible while producing distinct plastic, organic, and inert outputs.
Food waste depackagers and separators serve a variety of functions and are designed to automatically separate organic material from the following:
● source-separated food and green waste from household kerbside collections,
● the organic fraction of municipal solid waste (known as “residual waste” or “black bag” waste) which is, generated by trommel screening,
● pre-consumer organic food waste such as catering waste from the hospitality industry’s kitchens, company canteens, educational, insti-
Fig. 1
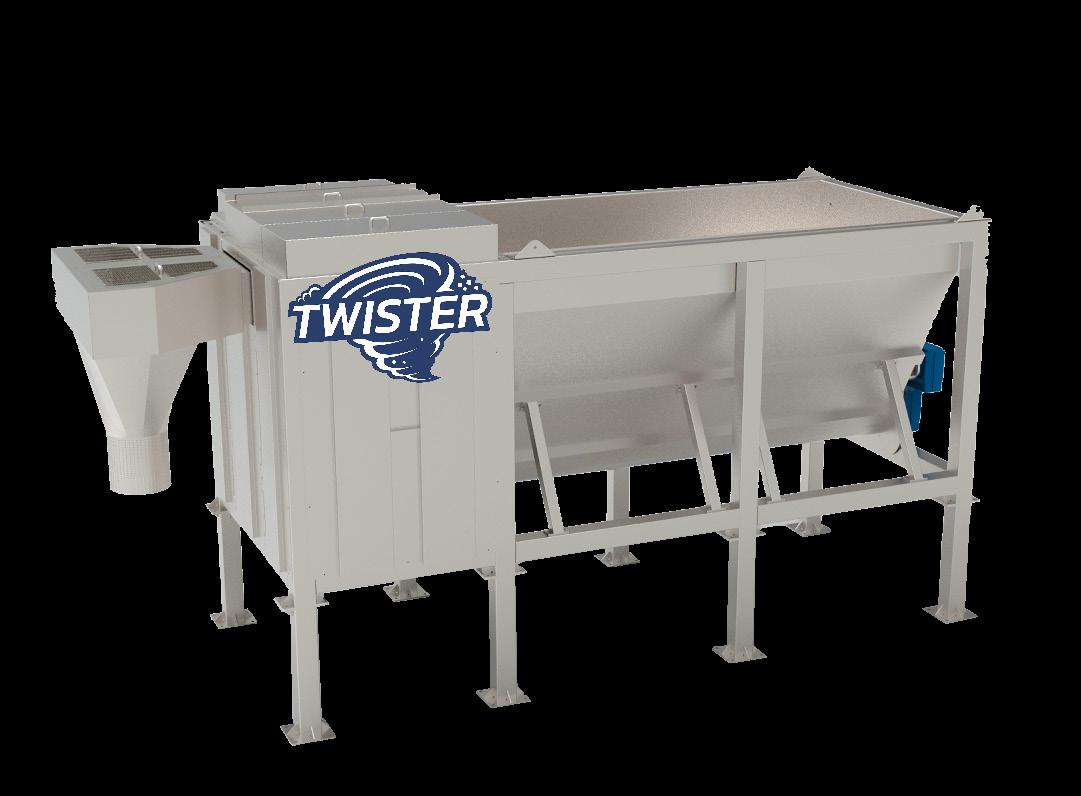
tutions, cruise ships, prisons etc.
● the food processing industry, and cess food waste organic content for feeding an anaerobic digesters, or for composting in windrow or in-vessel
● inedible food from supermarkets, and the food distribution logistics industry.
Why depackage and seprate? The market drivers
Depackaging and separation are driven by national waste management treatment hierarchies, which impose on the waste sector the following obligations:
● minimising waste, ● reduce what’s unavoidable, ● in that sequence, reuse and recycle, and ● beyond that, energy extraction is the fall-back choice, with landfill being the least desirable of all.
In practice, as the water content is already high in food, the preferred option is to pro-
Opening every bag pack and packet
A decent depackager/ separator must handle packaged food waste and be capable of opening each bag, package and packet. That is a tough challenge for the equipment. Consider for a moment the huge variety of materials, shapes and sizes available for food packaging today. That is an extremely difficult task for any machine. Not only must , each container be opened, but it must also be completely emptied. Above all, it must remain free from clogs and blockages after hundreds of hours of operations.
The industry is motivated to create separators that generate a clean, contamination-free organic paste, “pulp” or “soup” that may be pumped or transported into a treatment process to maximize value and energy of the material. Additionally, it must do it in accordance with the local “waste hierarchy”. Not to mention the necessity for environmental stewardship.
Secondary functions of a food waste separator
The secondary role of a food waste separator organic output stream are to:
● the greatest extent feasible, avoid the inclusion of insoluble non-organic pollutants in the organic fraction, including inert materials such as stones, grit, sand, silt, and clay, metal pieces, and plastics. Maintain the water content to provide a fluid viscosity in the organic fraction output suitable for onward conveyance and, if digested, to meet the water content requirements of the anaerobic digestion process which it feeds, ● prevent being damaged by the presence of occasional “unexpected items” such as the cutlery, and crockery accidentally dropped into food waste bins.
Perhaps too little attention has been devoted in the past to the removal of inert materials ranging in size from stones to clay particles. Even in small quantities these contaminants can accumulate in anaerobic digestion tanks. Once digester efficiency detoriates as a result of excessive inert
material accumulation, emptying and cleaning the digester can be dangerous, costly, and time consuming. This has a detrimental effect on the energy output.
The imperative of avoiding microplastics in the environment
A new requirement has been introduced in response to scientific and public concerns over plastic pollution and its possibly disastrous effects on the health of the world’s oceans, and eventually on humans. This function is necessary to avoid generation of microplastics (small chips and granules of plastic).
Tiny plastic particles have the potential to be re-concentrated in oceans in ways that pose a threat to species .
Microplastics (little bits of plastic) wash ashore in the intertidal zone, gradually breaking into smaller pieces. As a result, plastic accumulates on vulnerable beaches. It’s difficult to say that after food waste separation, any microplastic can be tolerated. As a result, users of this equipment now have an added responsibility to minimise microplastics. When used as a digestate fertilizer, it is spread on the land and eventually washes into the sea over geological time.
Low microplastics in current food waste separator technology
Biogas Magazine | Edition 19 | 18 To avoid blockages, first generation separation technologies reduced particle size. However, a significant amount of microplastic particles were produced. As a result the latest depackagers/separators avoid hammering paddle-smashing, and shredding. This results in energy saving. Aditionally, the larger surface area of tiny plastic particles retained more water. Thus, a higher-grade plastic output results from less destructive processing, more acceptable for recycling or as an RDF. So, the days of discarding this material should now be gone. continue to remove plastic after the digester. They must, as a significant amount of food tends to adher to the plastic generated by early separation machinery. However , separating plastic and grit after the digester is not a smart idea. It results in inefficient digester operation, due to elevated substrate viscosity, a greater tendency for hard crust to form on the digester surface, inefficient mixing and grit, sand, and silt buildup in the digester.
Eventually, when build-up reaches a certain point the
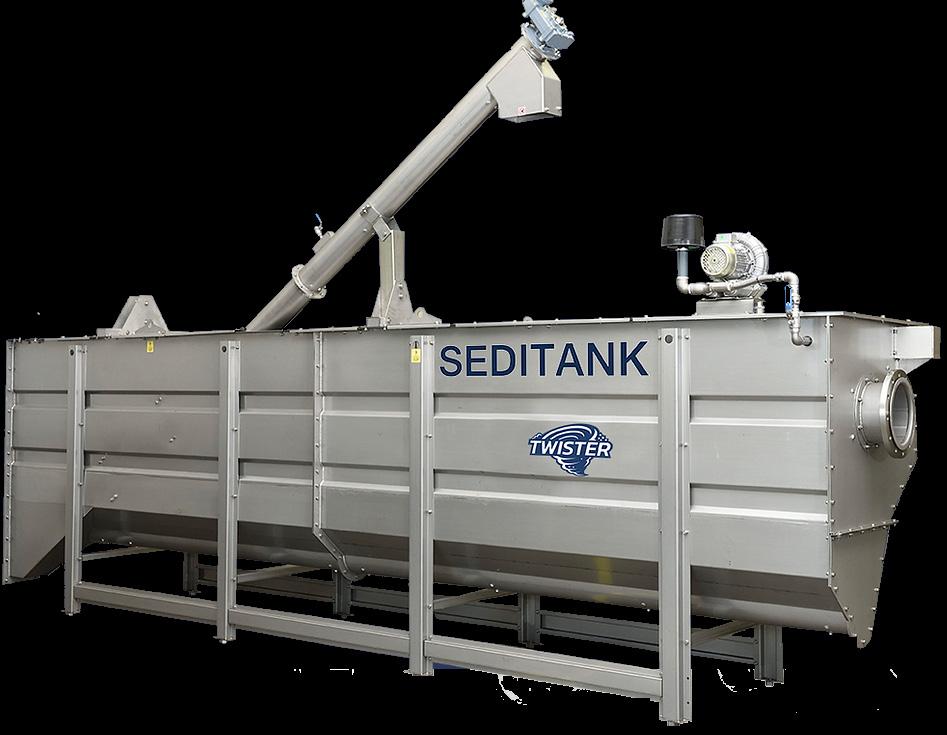
Separation of plastics before the digester is the future
While reducing microplastic content is crucial, it is also critical to maintain organic content. AD operators require the entire calorific content of food waste to genetate biogas. For this reason, many digestion tank must be shut down and dug out. That entails heavy cleaning costs and the loss of biogas output. Additionally, when digester availability declines, power companies may see a decrease in the price they pay for each unit of electricity.
The Drycake Twister™ Food Depackaging and Separator System
Recent generation of depackager/separators that aims to meet all of these requirements is the Drycake TwisterTM high-speed vortex depackaging and separator system, which can be supplemented by SeditankTM and CleanpressTM units as needed. This is a technology that will soon be operational in an Indian trash facility.
As the third generation of Drycake’s unique vertical cyclonic separation technique, it is primarily designed to provide a depackaged food waste substrate suited for AD plants.
The Twister operates on the principle of a separation vortex.
The system consists of a feed hopper with an upper screw auger to prevent material from bridging and a lower screw auger to feed the machine.
The unit debags in the hopper, requiring no preliminary size reduction. A vortex is formed in the screening drum by the action of an integral turbine. This simultaneously forces the organics through a screen while the packaging is ejected for discharge.
Flexing and vibration in the air of the high-speed vortexcontribute to the cleaning ef-
Biogas Magazine | Edition 19 | 19 fect while the organic fraction is transferred to an optional separate unit, called a Seditank which removes inert materials and any small plastics/ microplastics
Case study: Bangalore Airport, Genia Global and Adverio Waste Systems work together on innovative move toward sustainable management of air transport infrastructure
Bangalore Airport is the third-largest airport in India and is known for its innovation and high standard of sustainability. It has launched a new project to repurpose food waste and reduce energy consumption.
The facility will process the airport’s 15,000t of biowaste per year, producing 2.25 million Nm3/year of biomethane and 14,625MWh of total energy.
This energy will be used to generate electricity with its 500kW generator motor and also to make vehicular biomethane (CNG) for airport vehicles.
To do this a new anaerobic digestion plant and biogas upgrading facility will be built on site to process the waste generated at the airport and in flight.
Twister technology was selected for the duty of depackaging garbage prior to entering the digester by the engineering firm Adverio Waste Systems in collaboration with the biogas system provider. The rationale cited was its capacity to produce an organic outlet of excellent quality. The model employed for this project has the capacity to process 5 T/hr of biowaste The project is scheduled to be completed in late 2022 Genia Global intends to apply this model to multiple other airports across the globe.
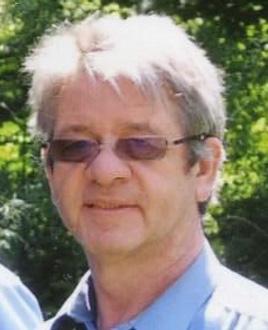
Mark Vanderbeken
Chairman and Founder
The TWISTER De-packager
Online Biogas Magazine | Edition 19 | 20 Biogas Training


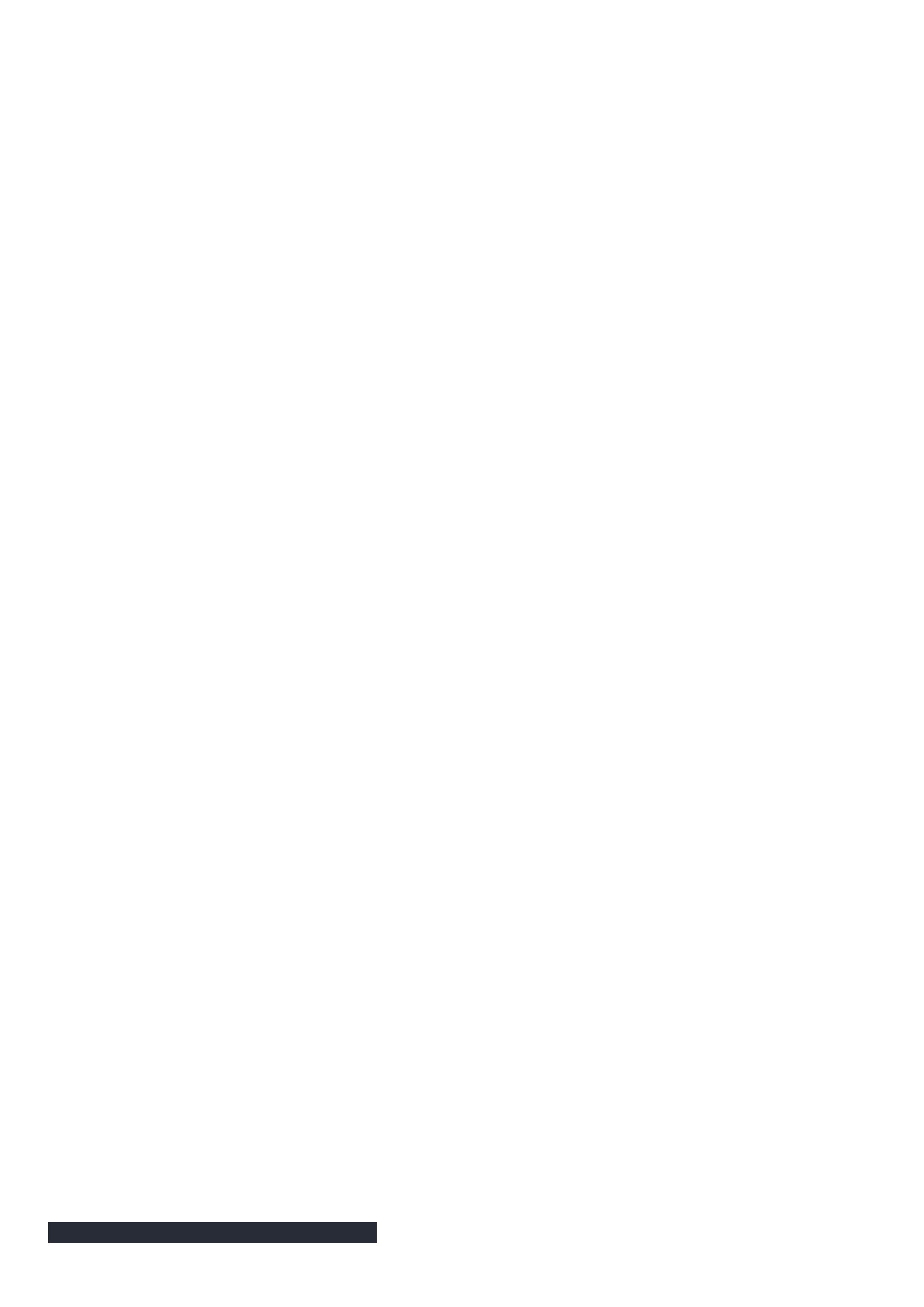
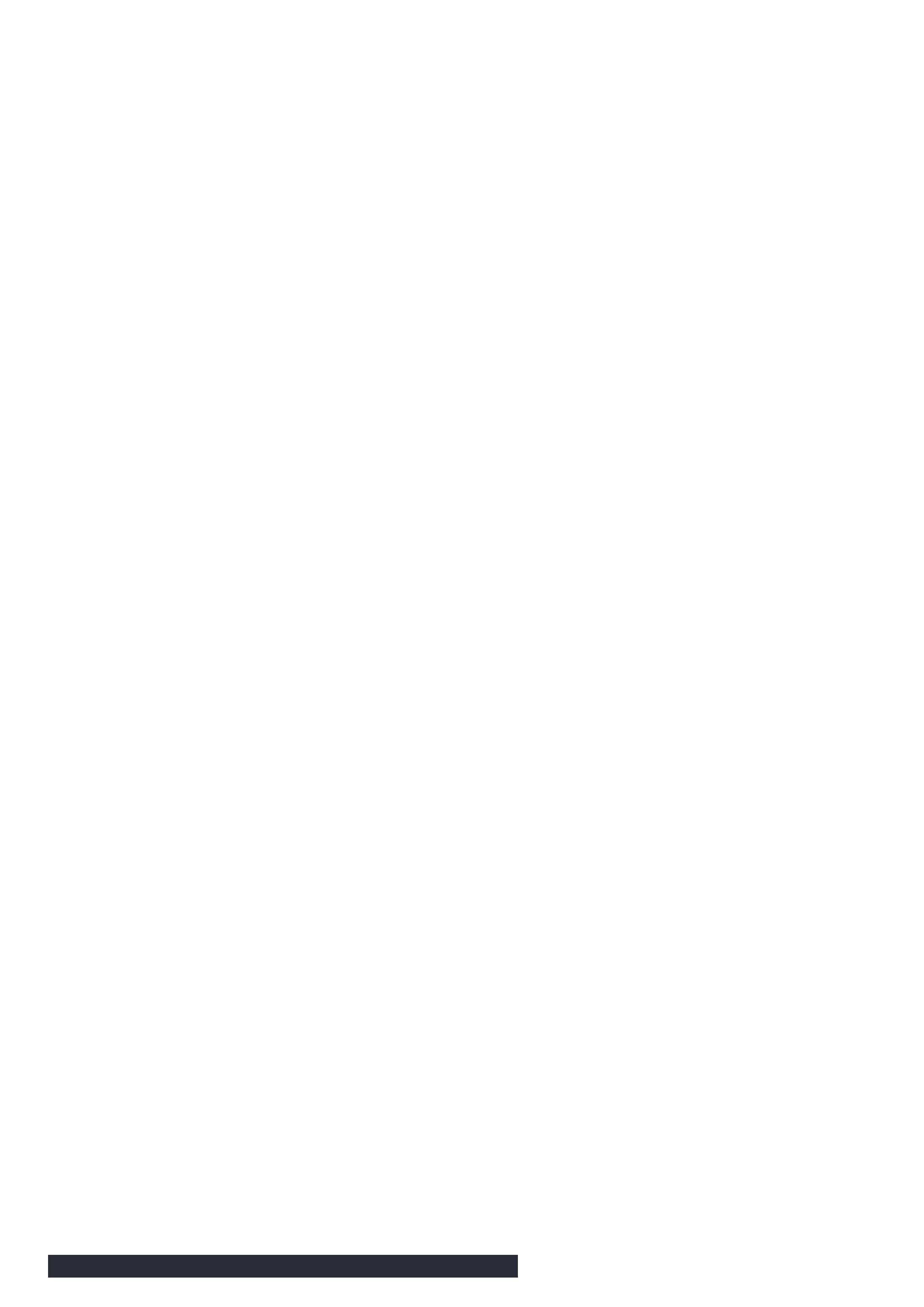

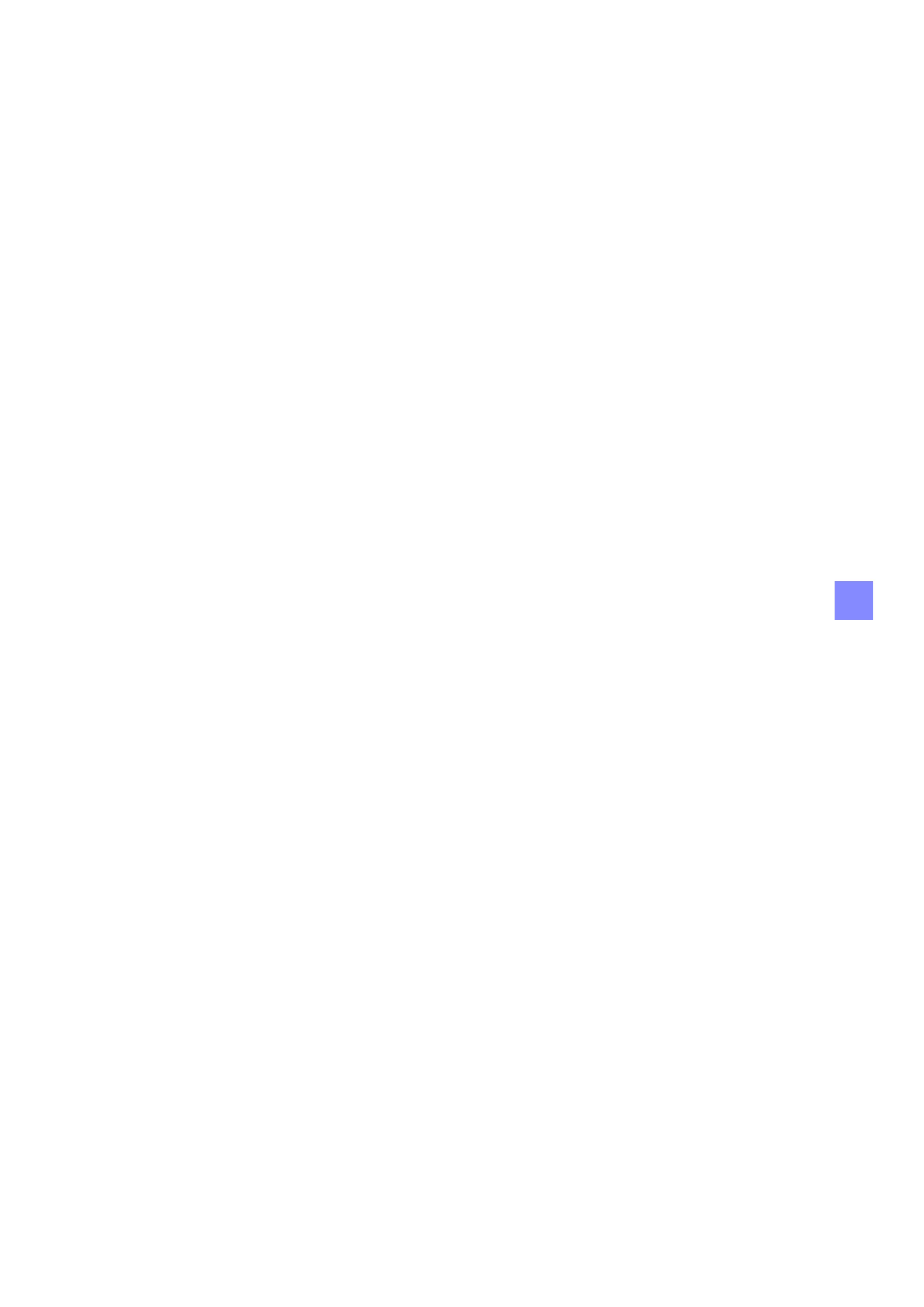
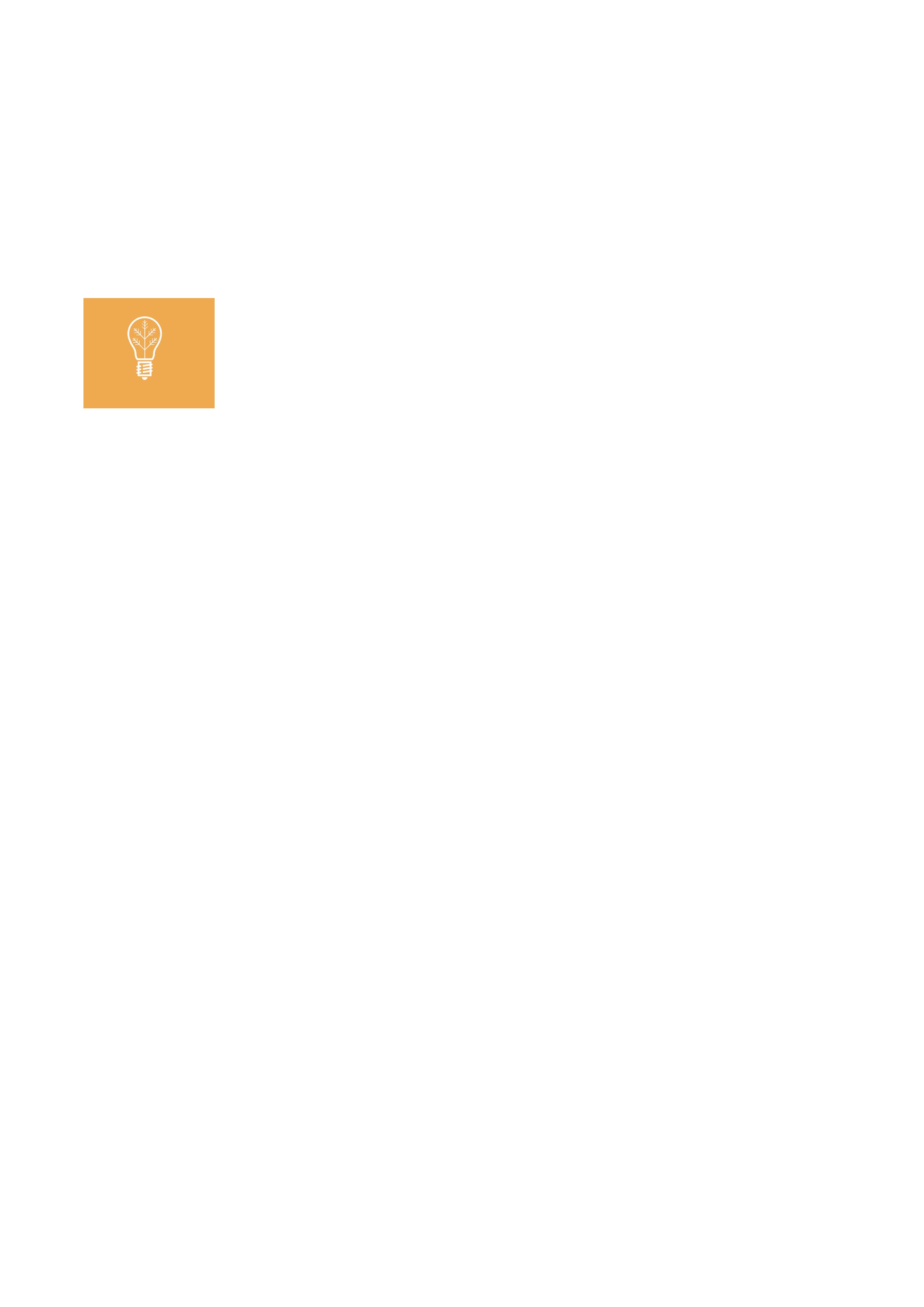

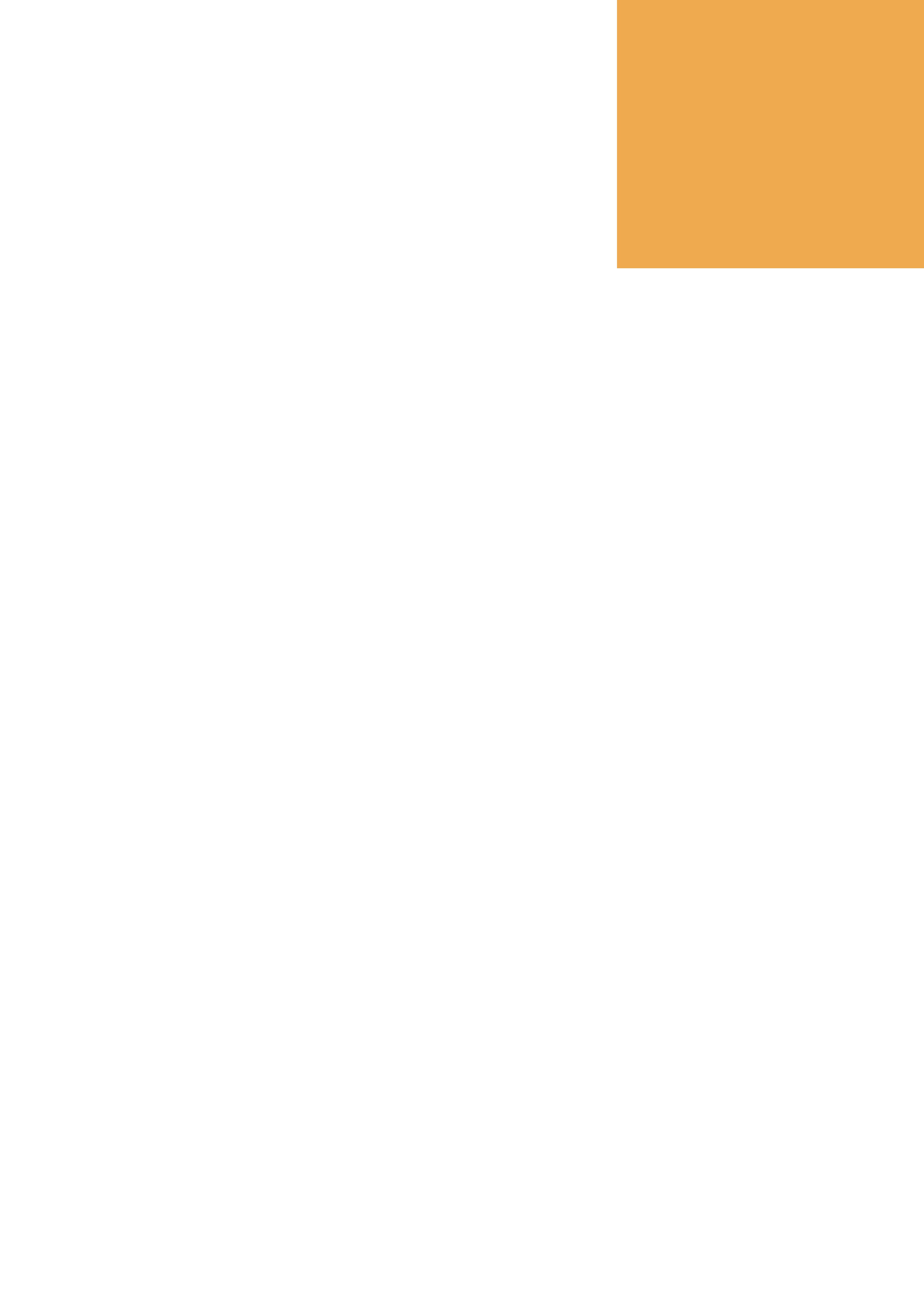
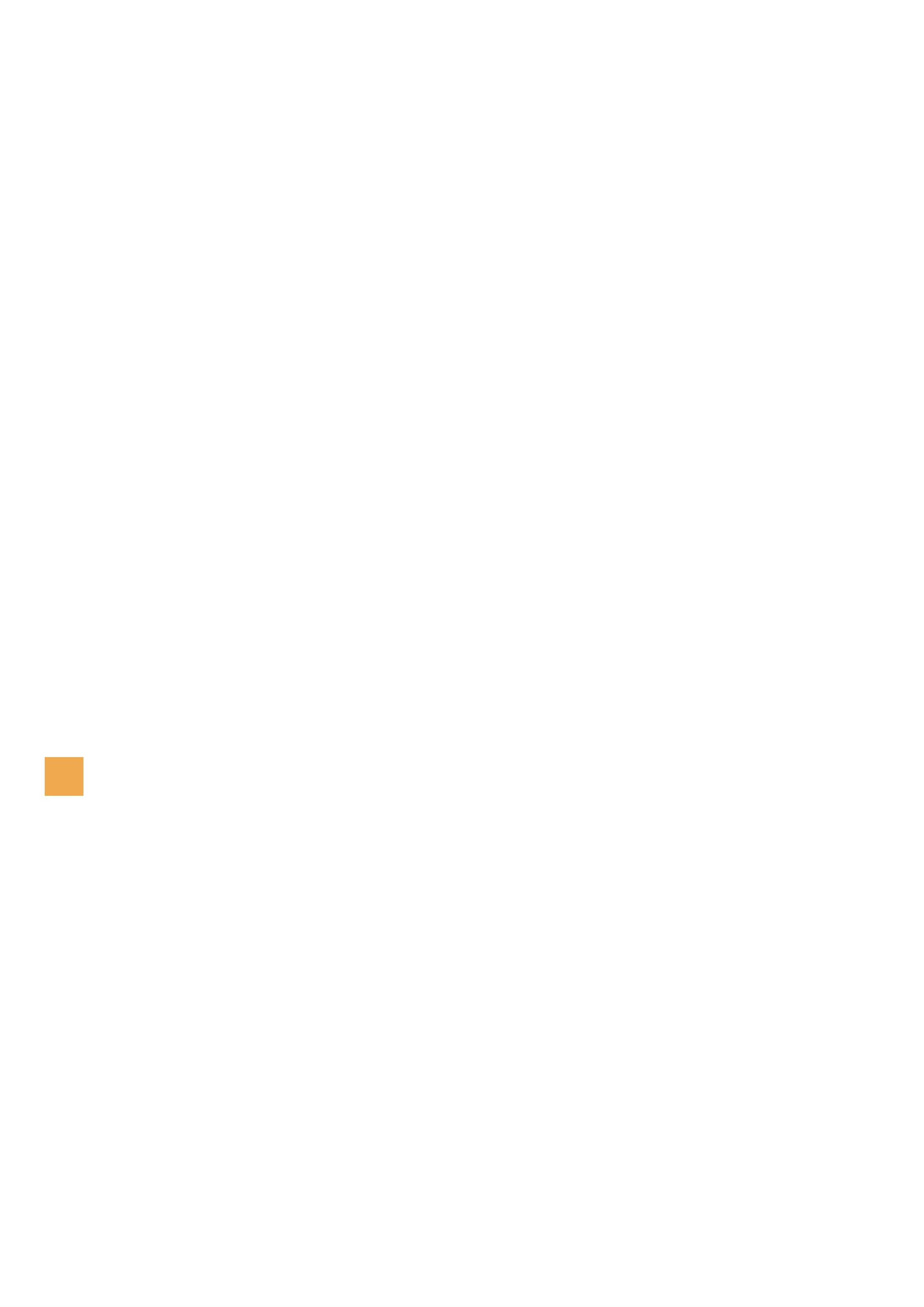
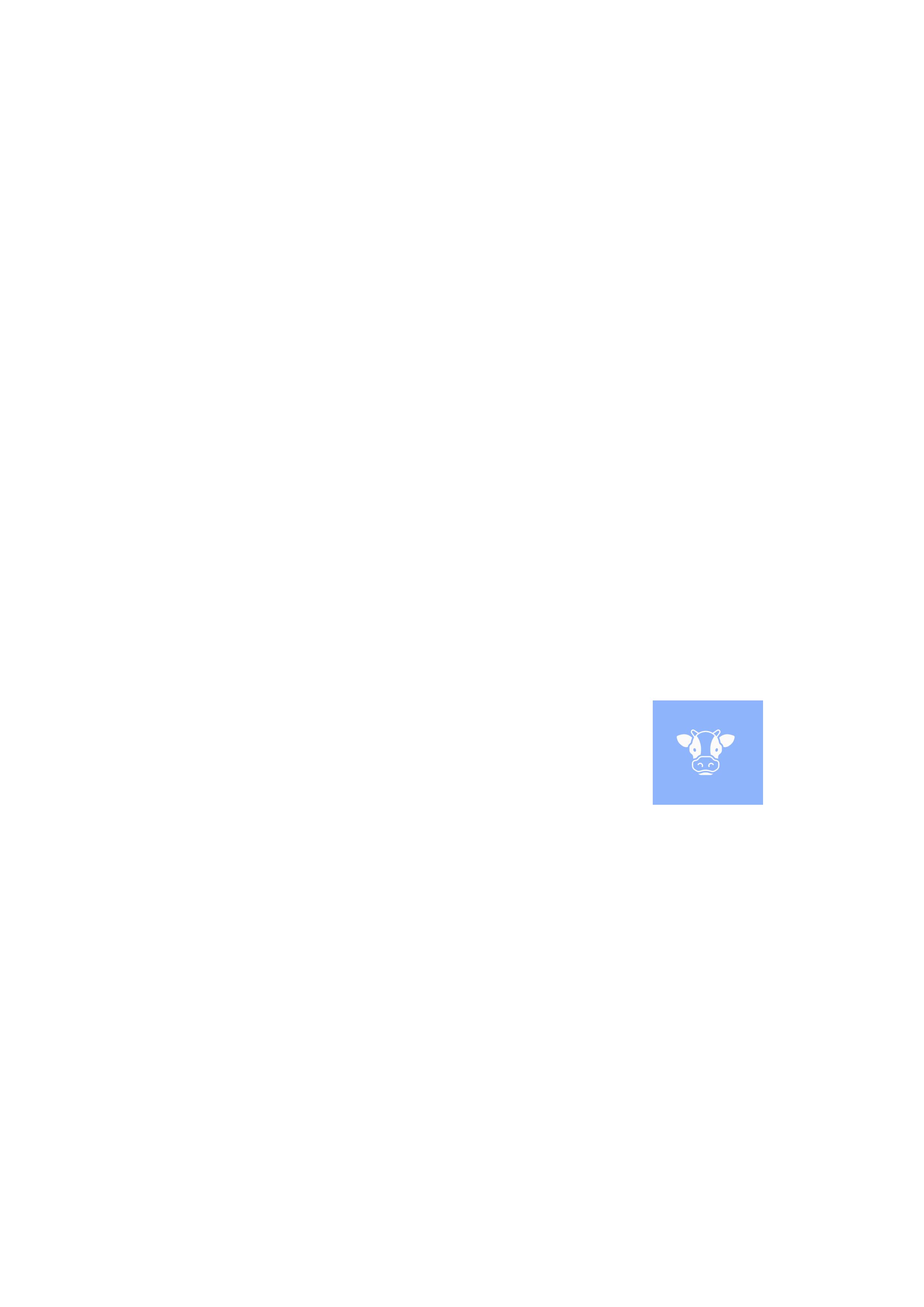
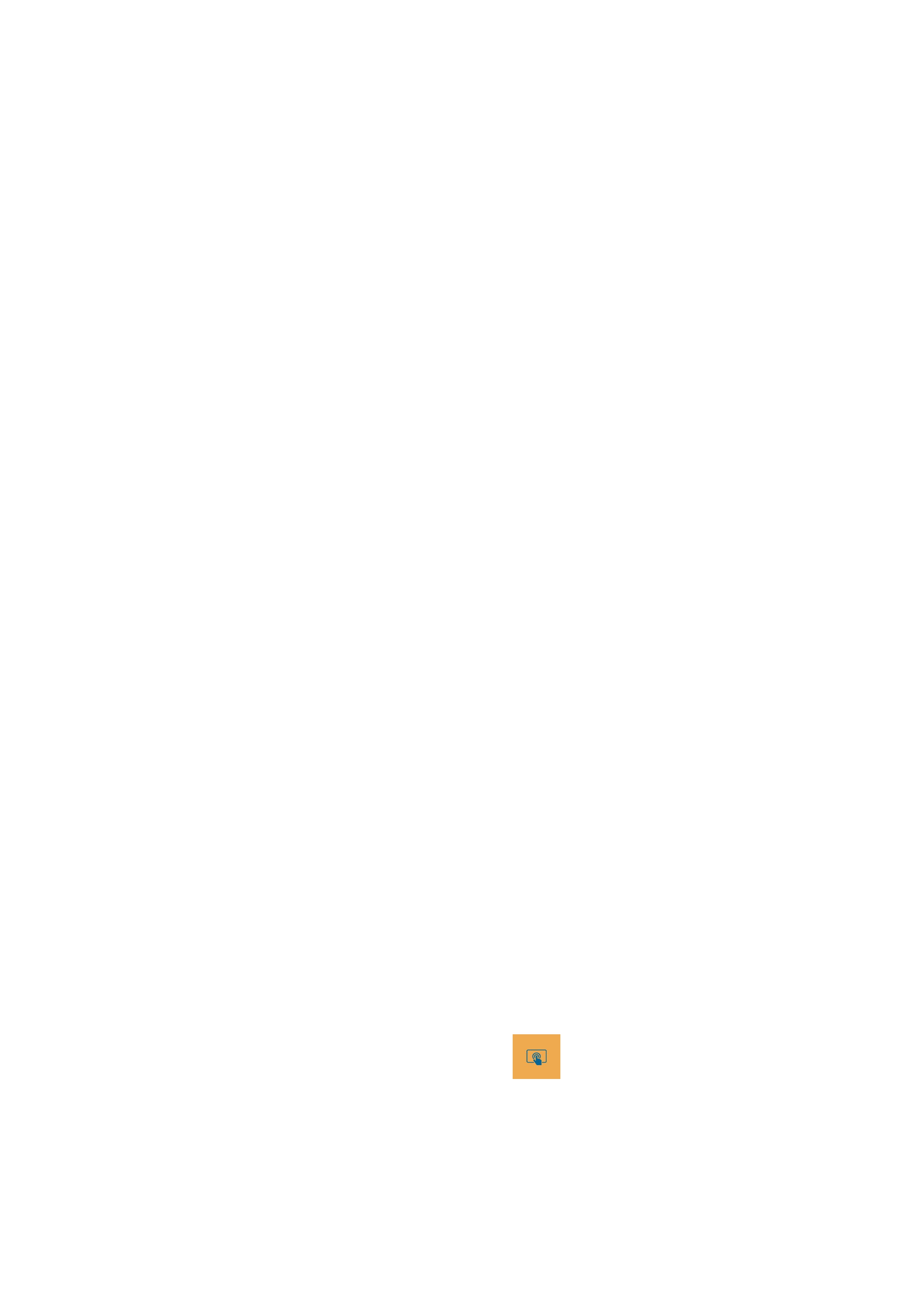
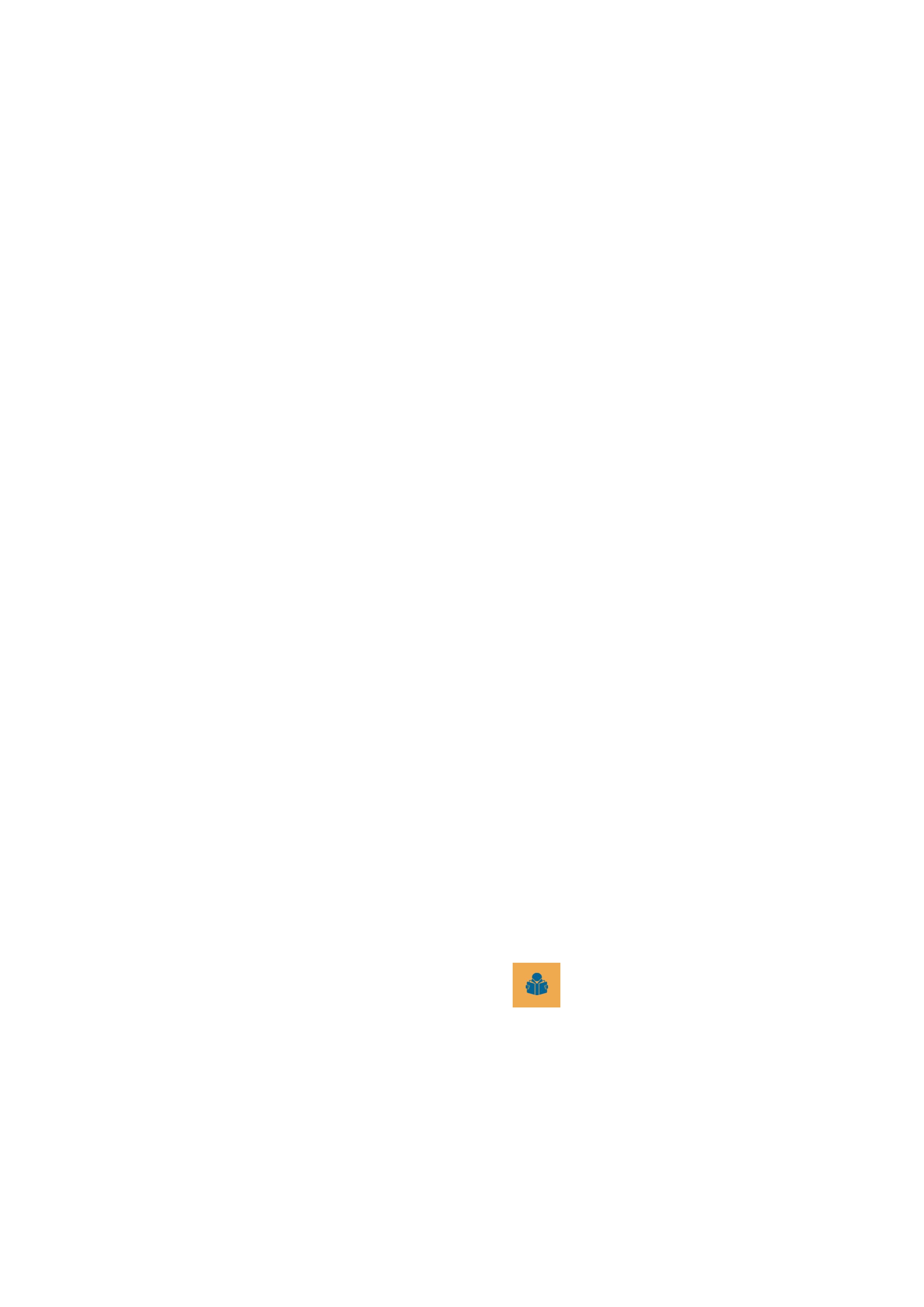
Book your Seats Now!
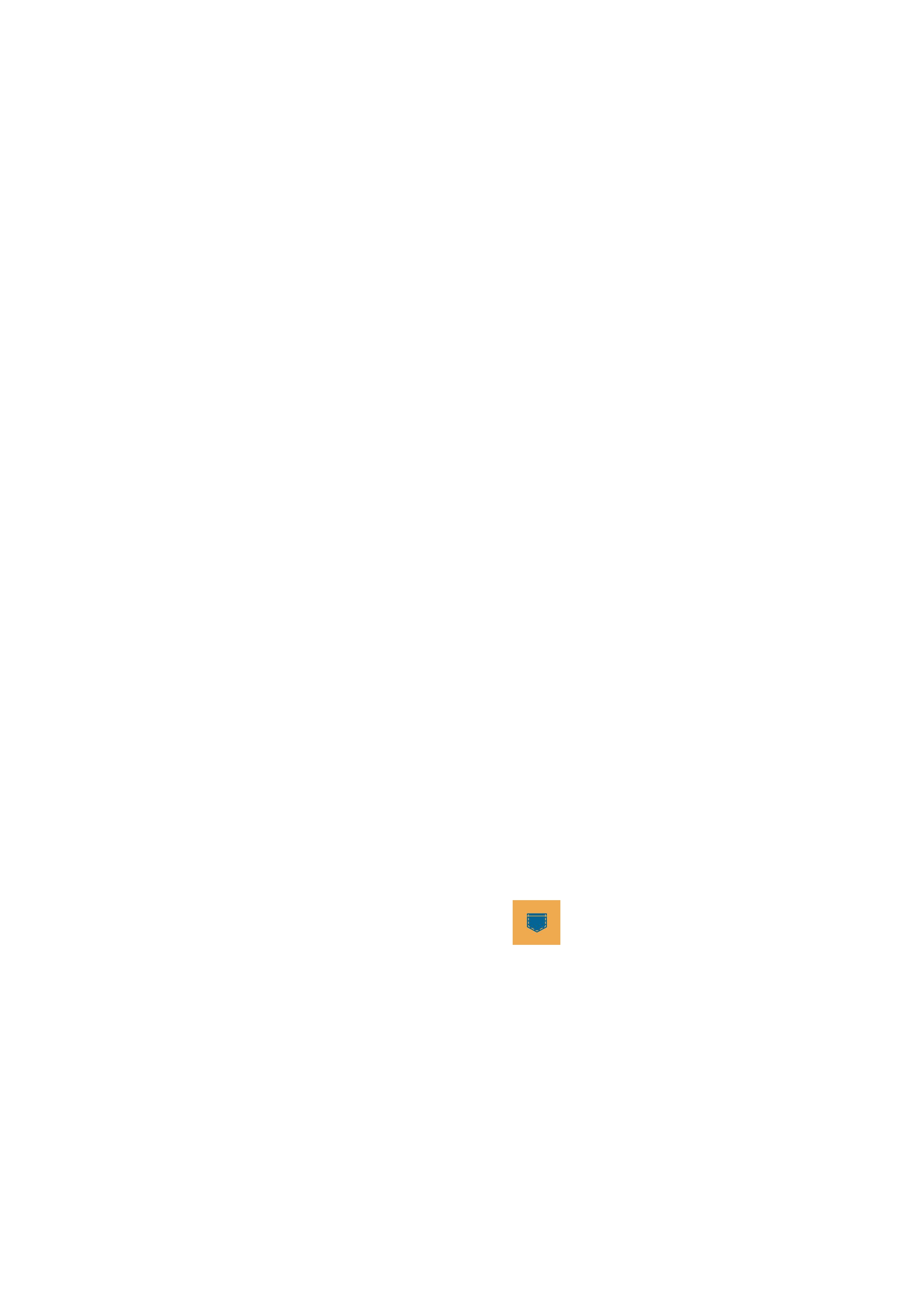
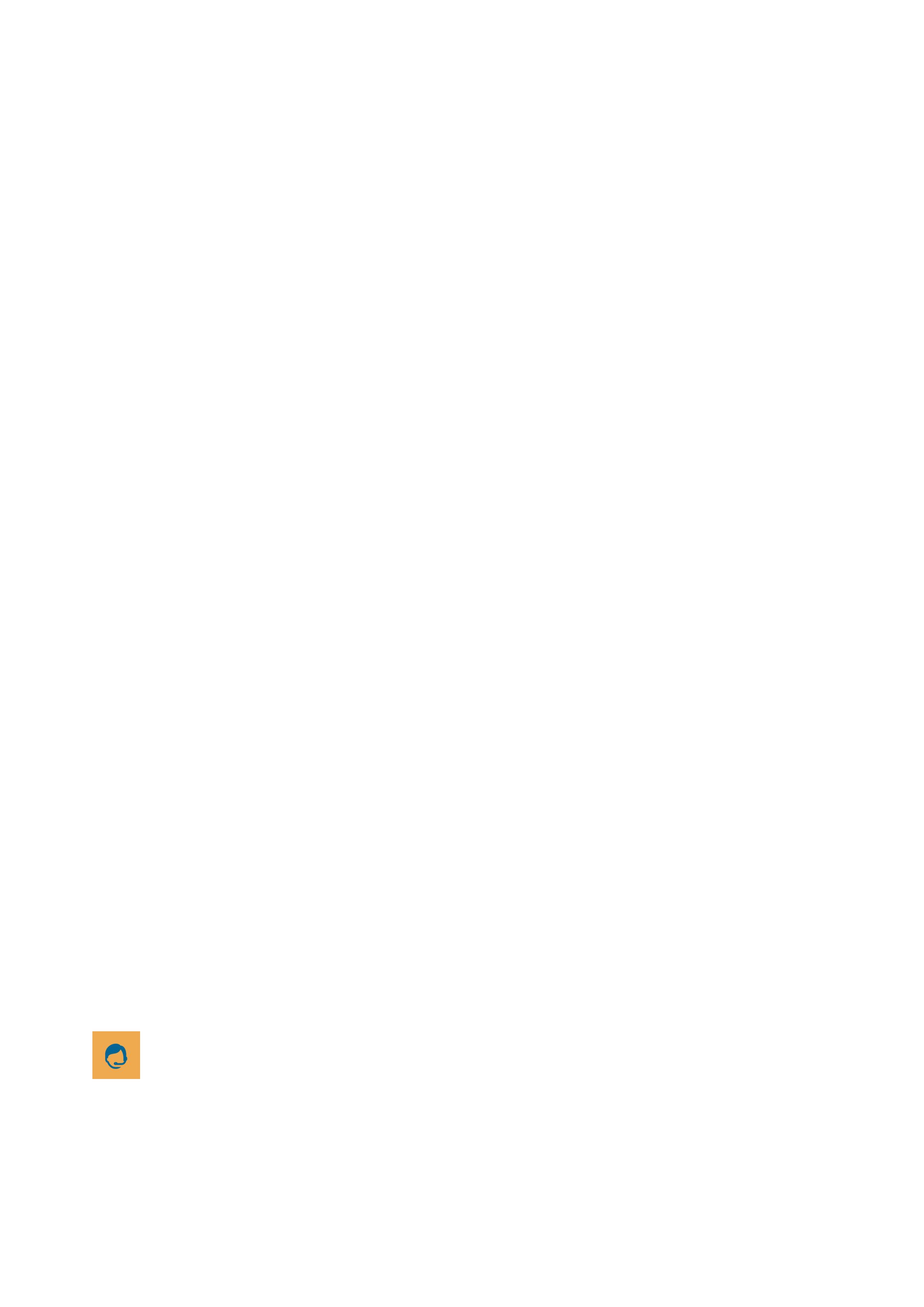
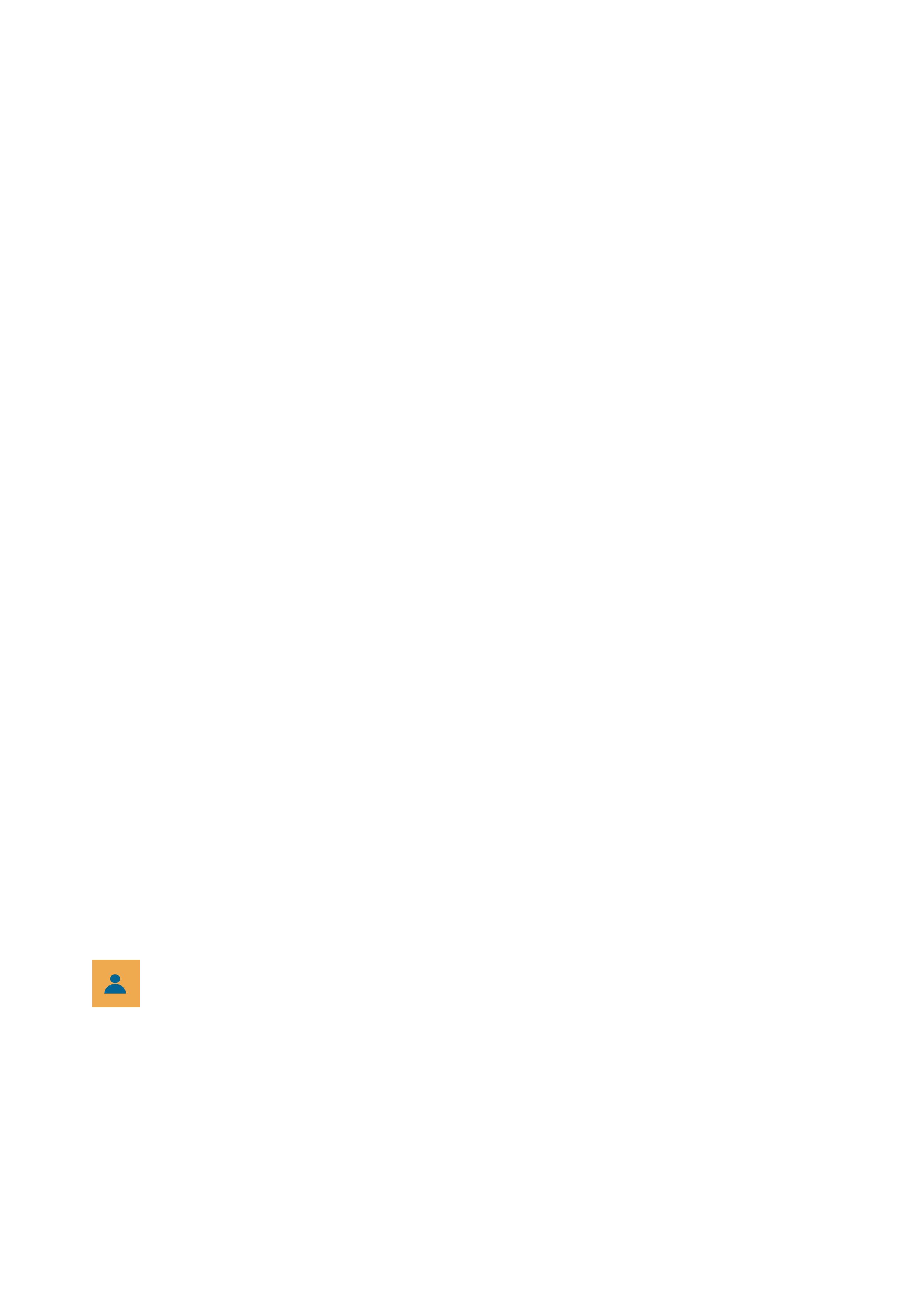
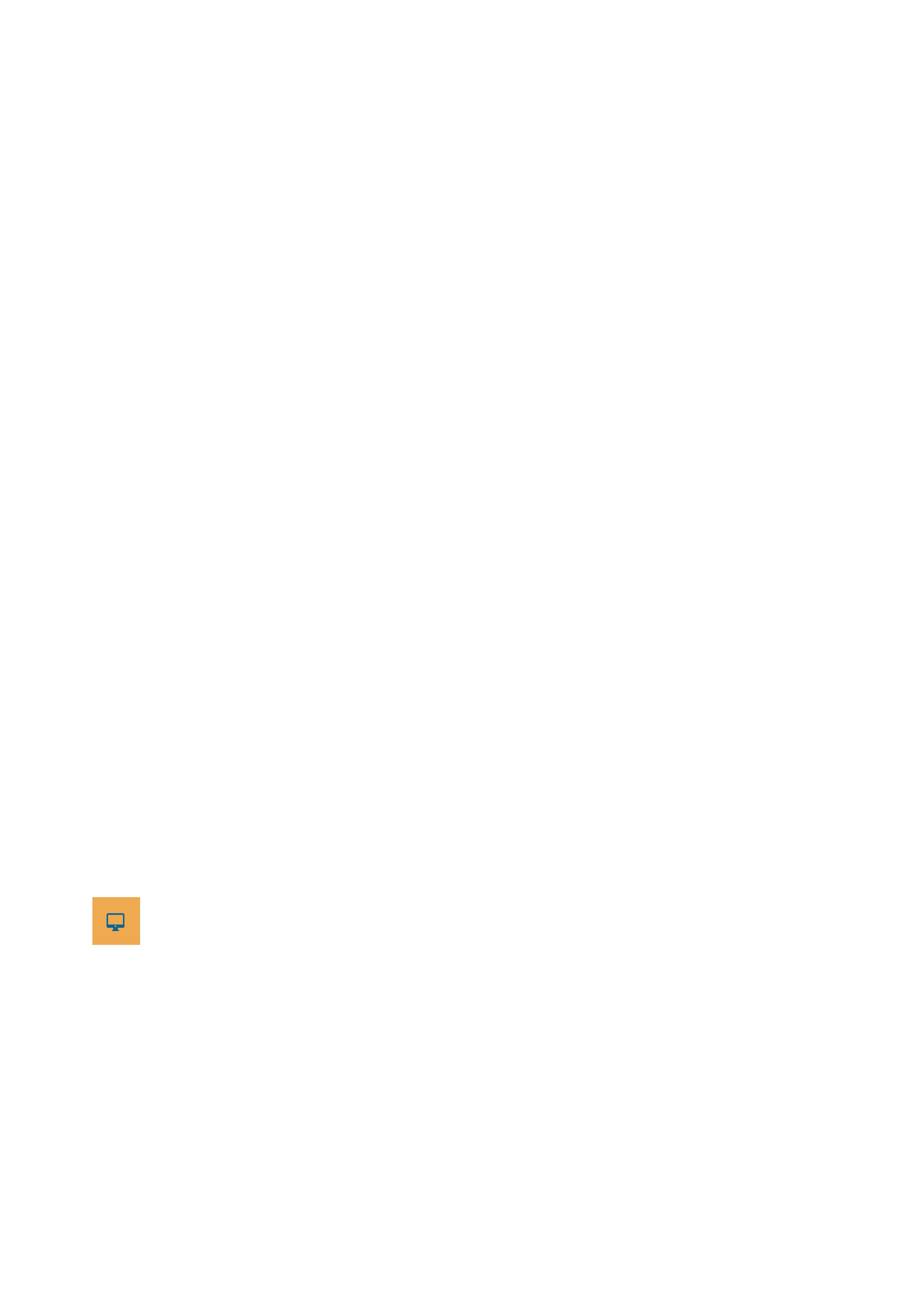
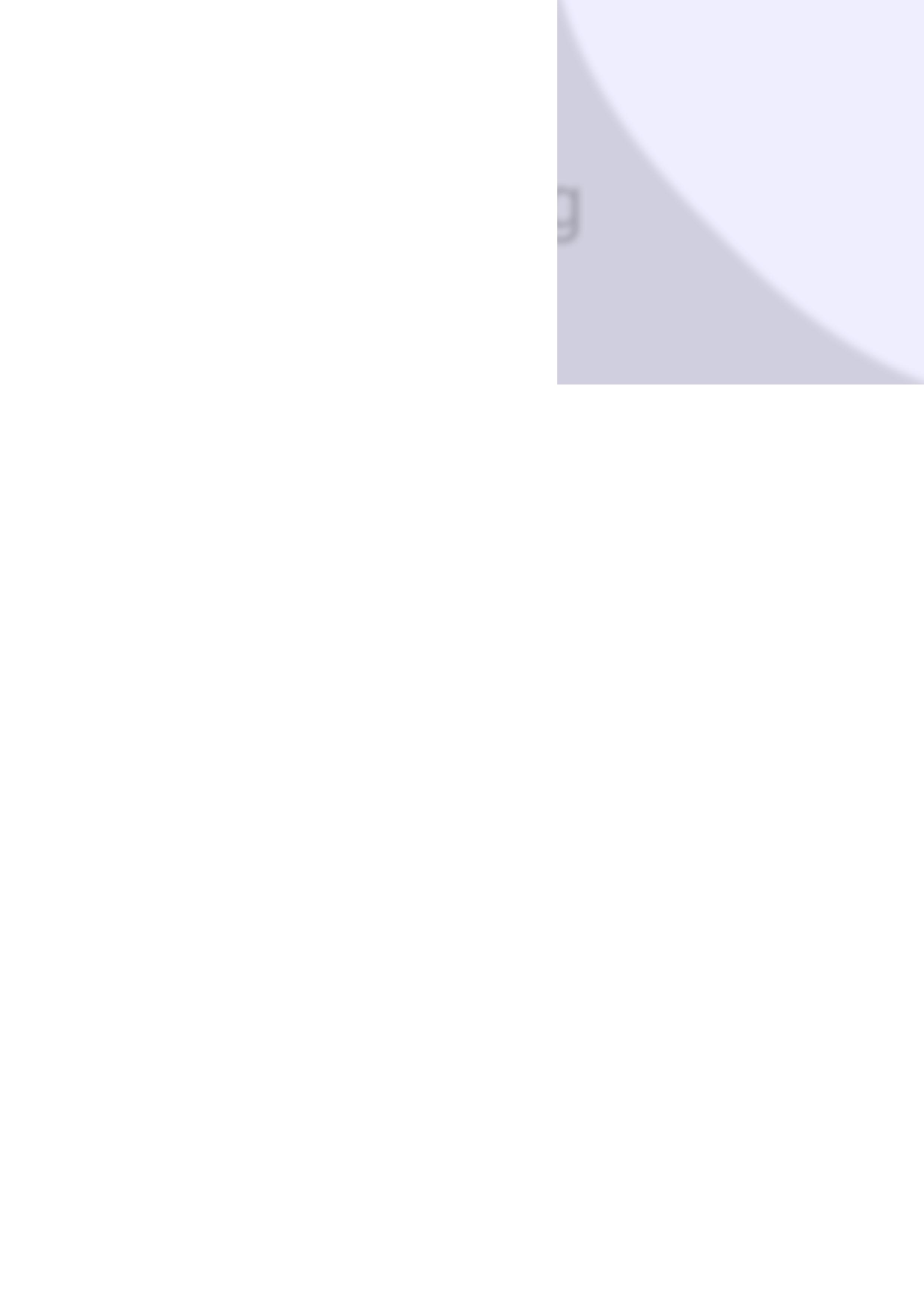

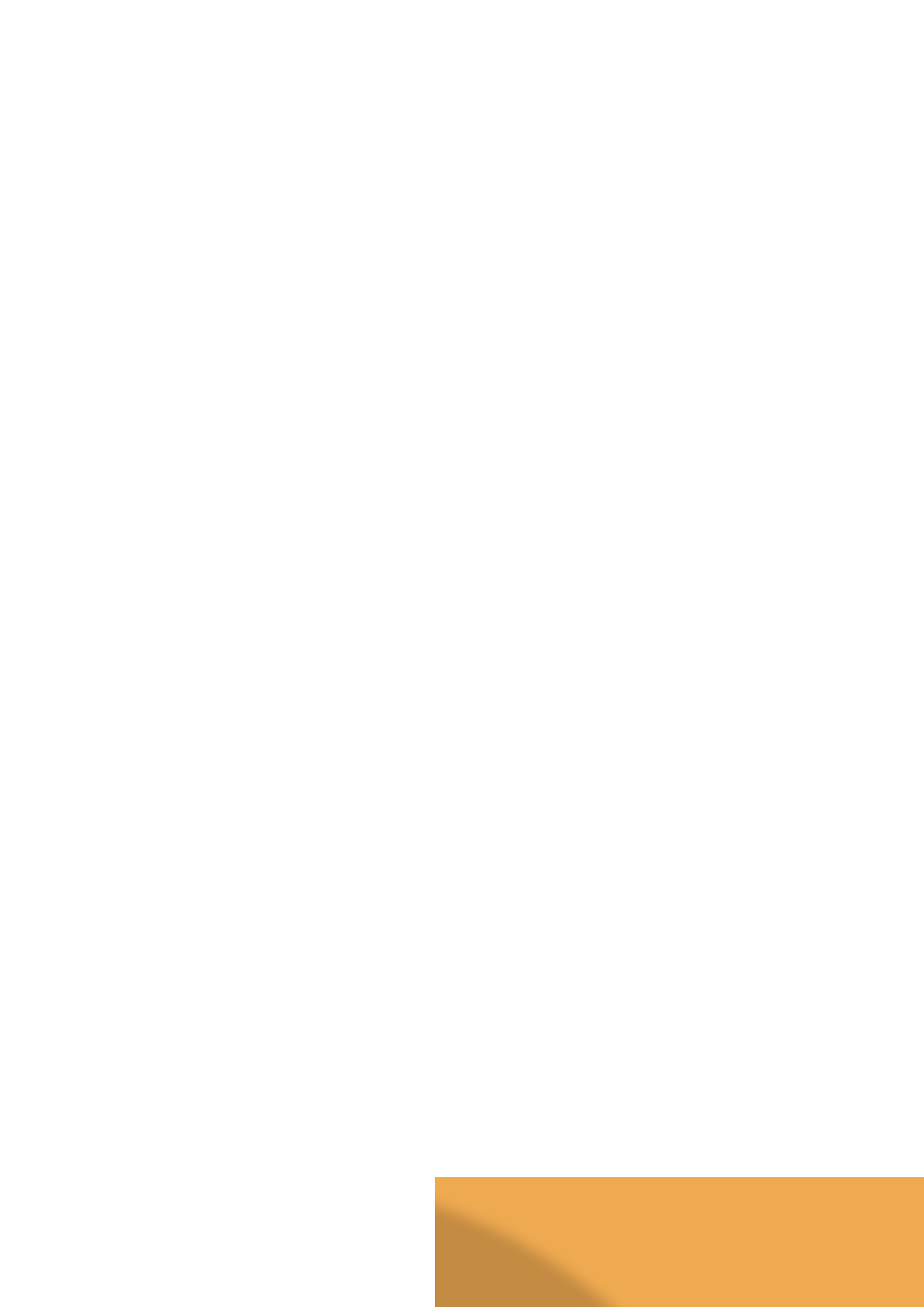
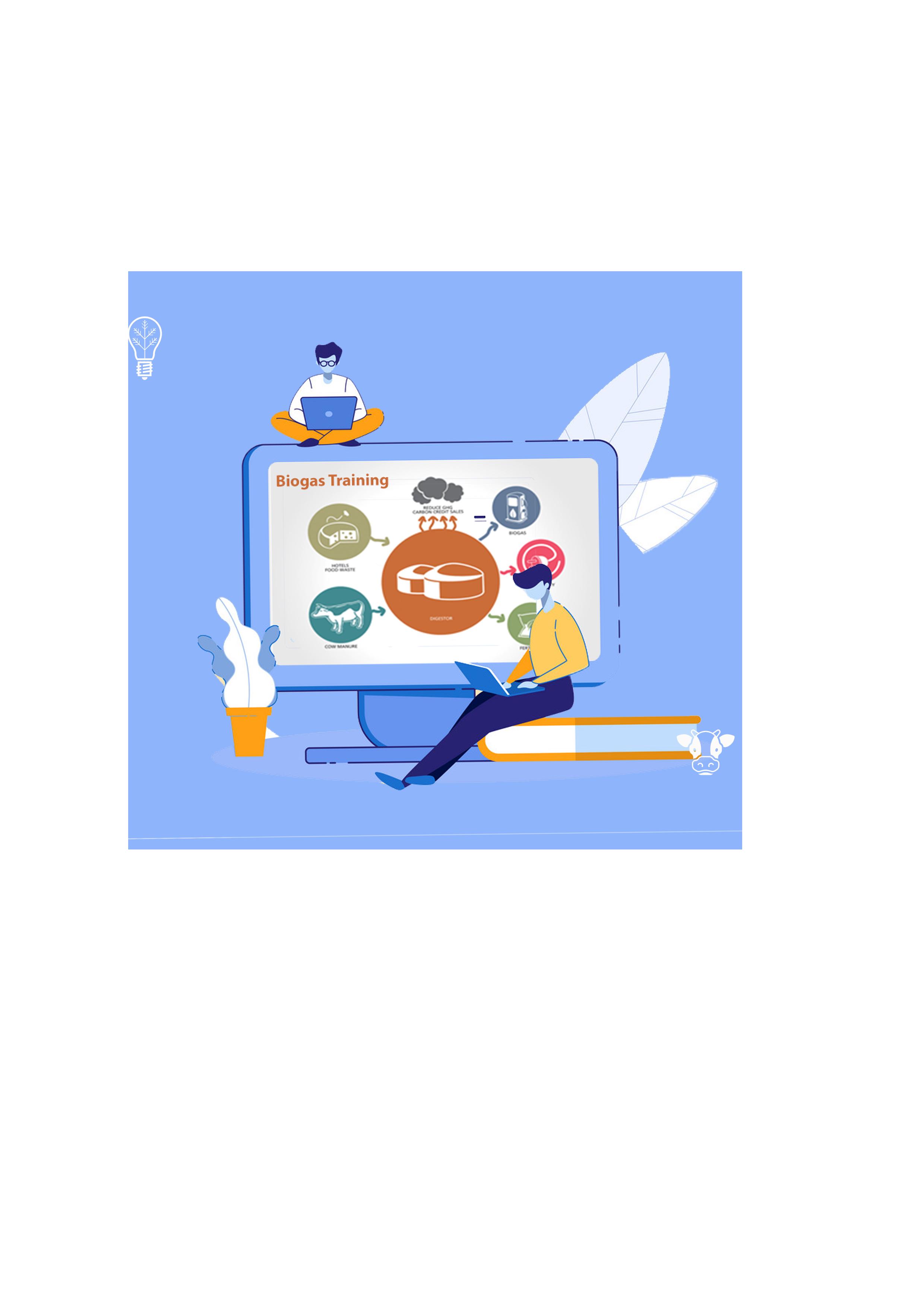
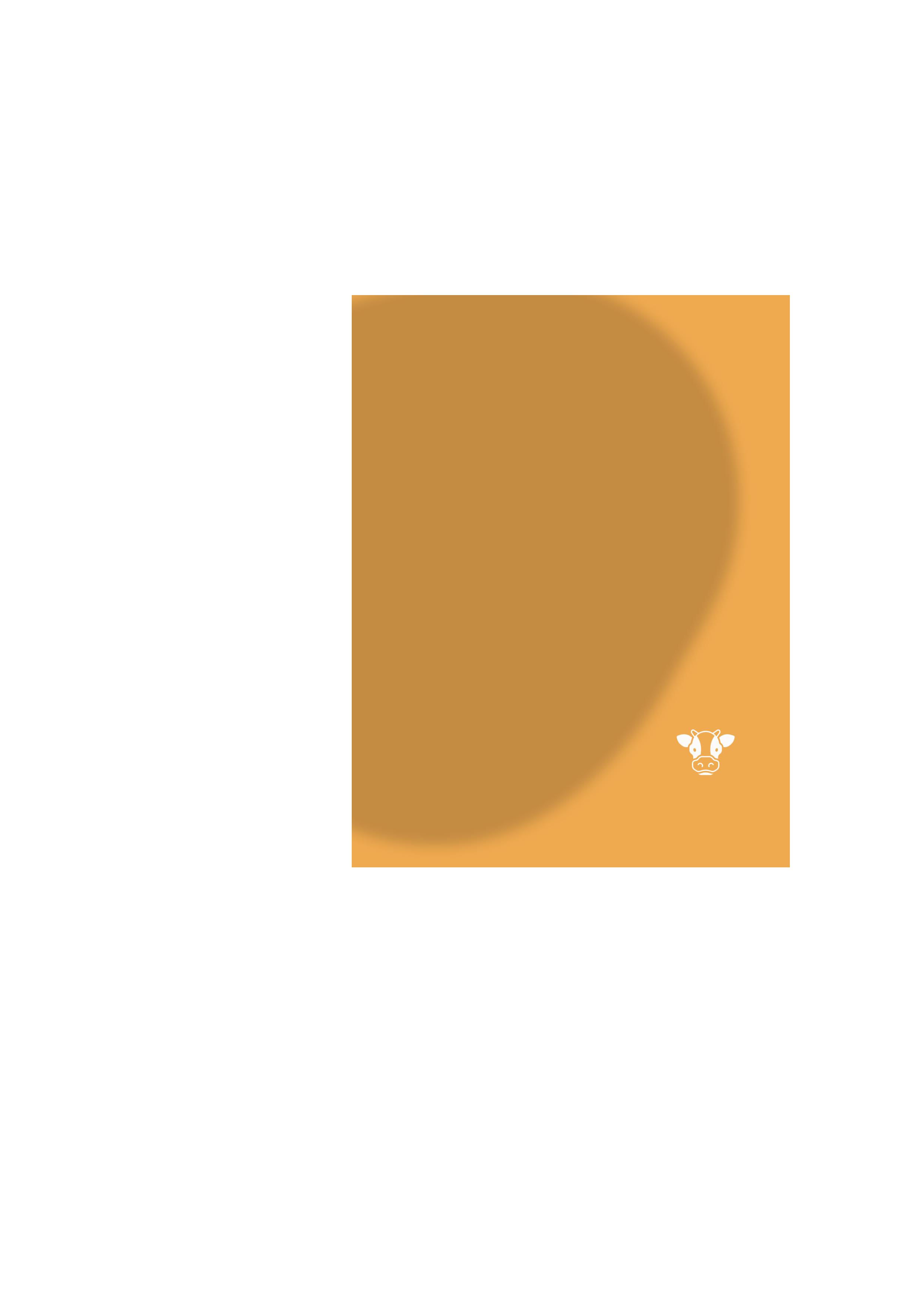
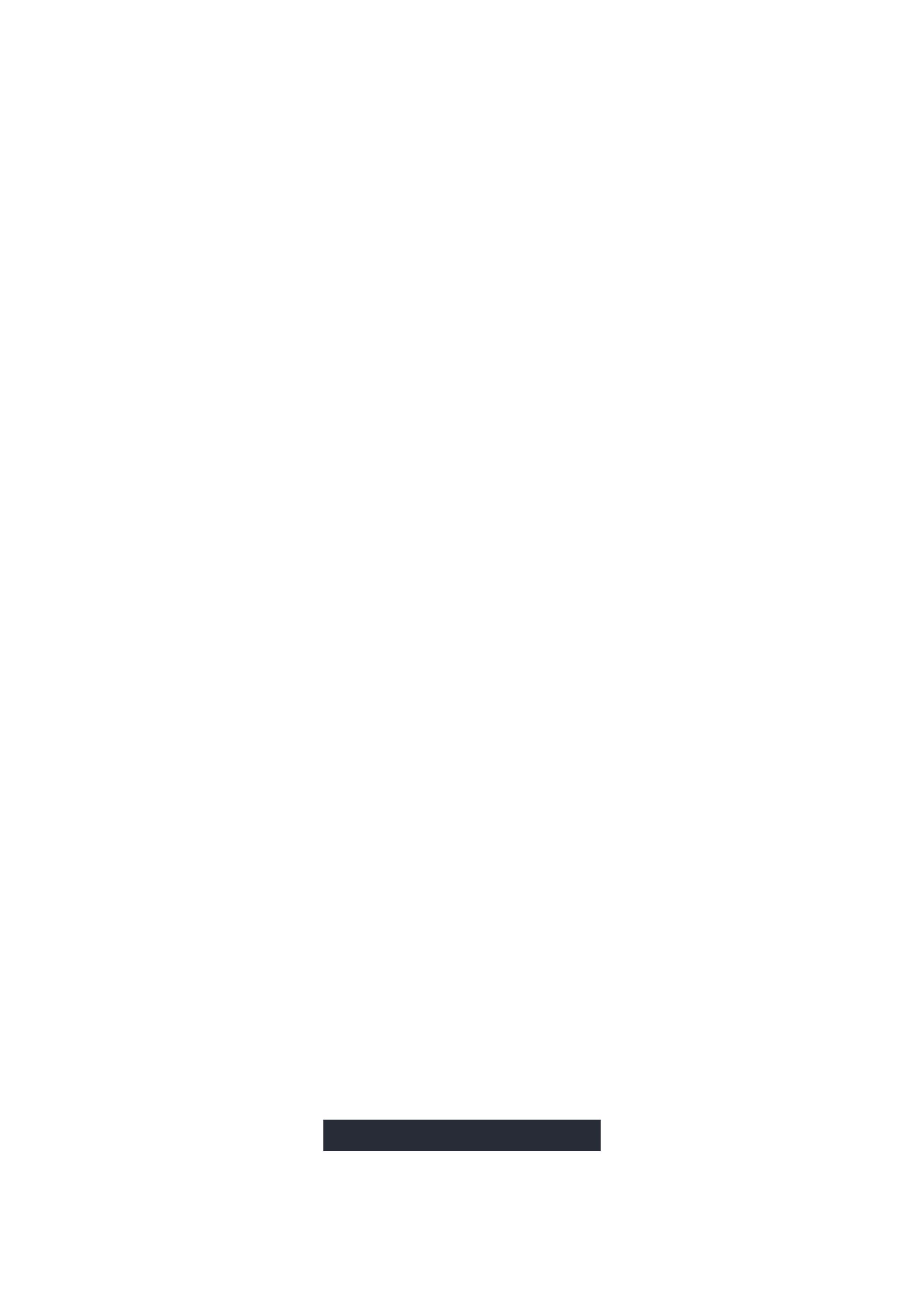
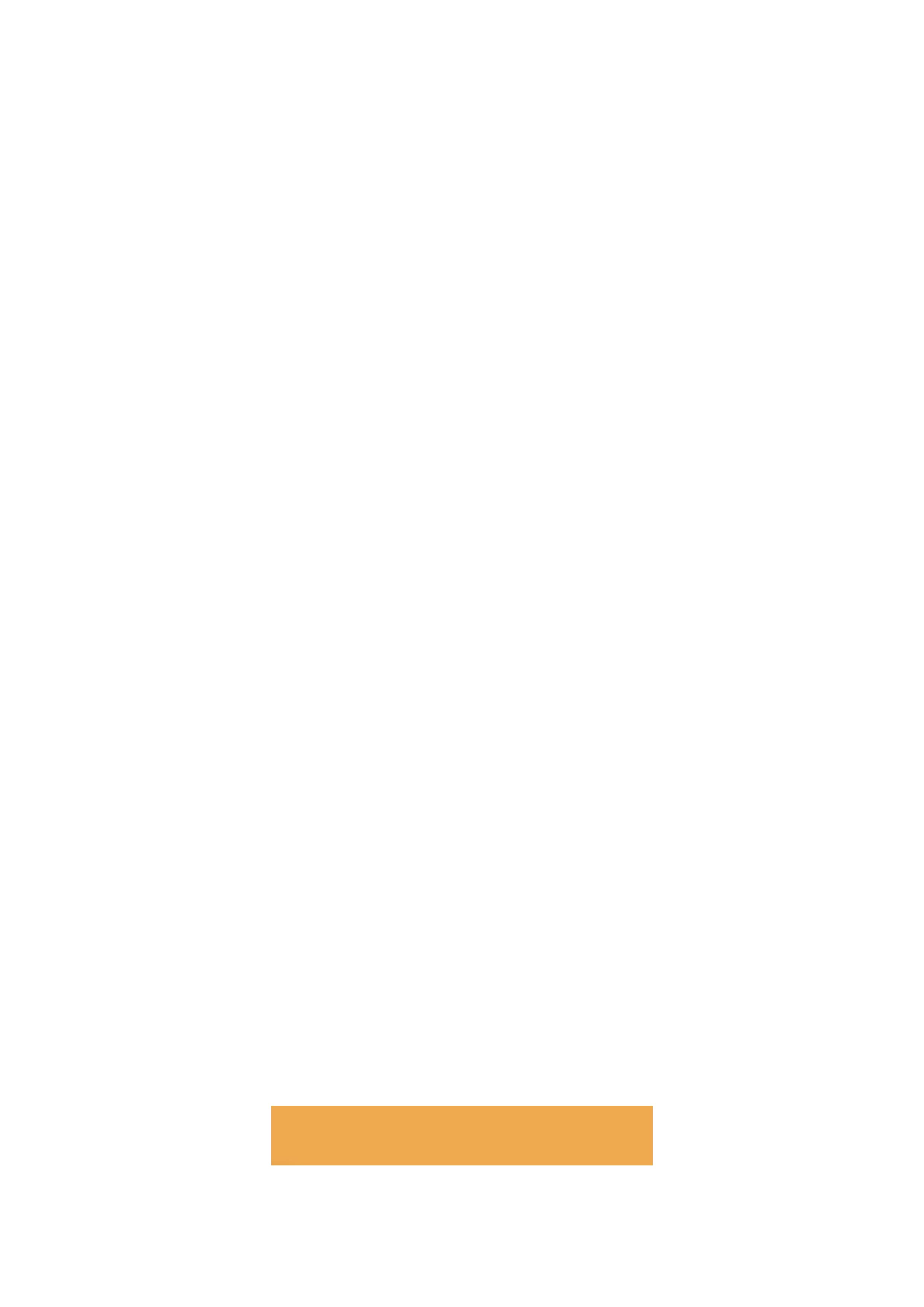
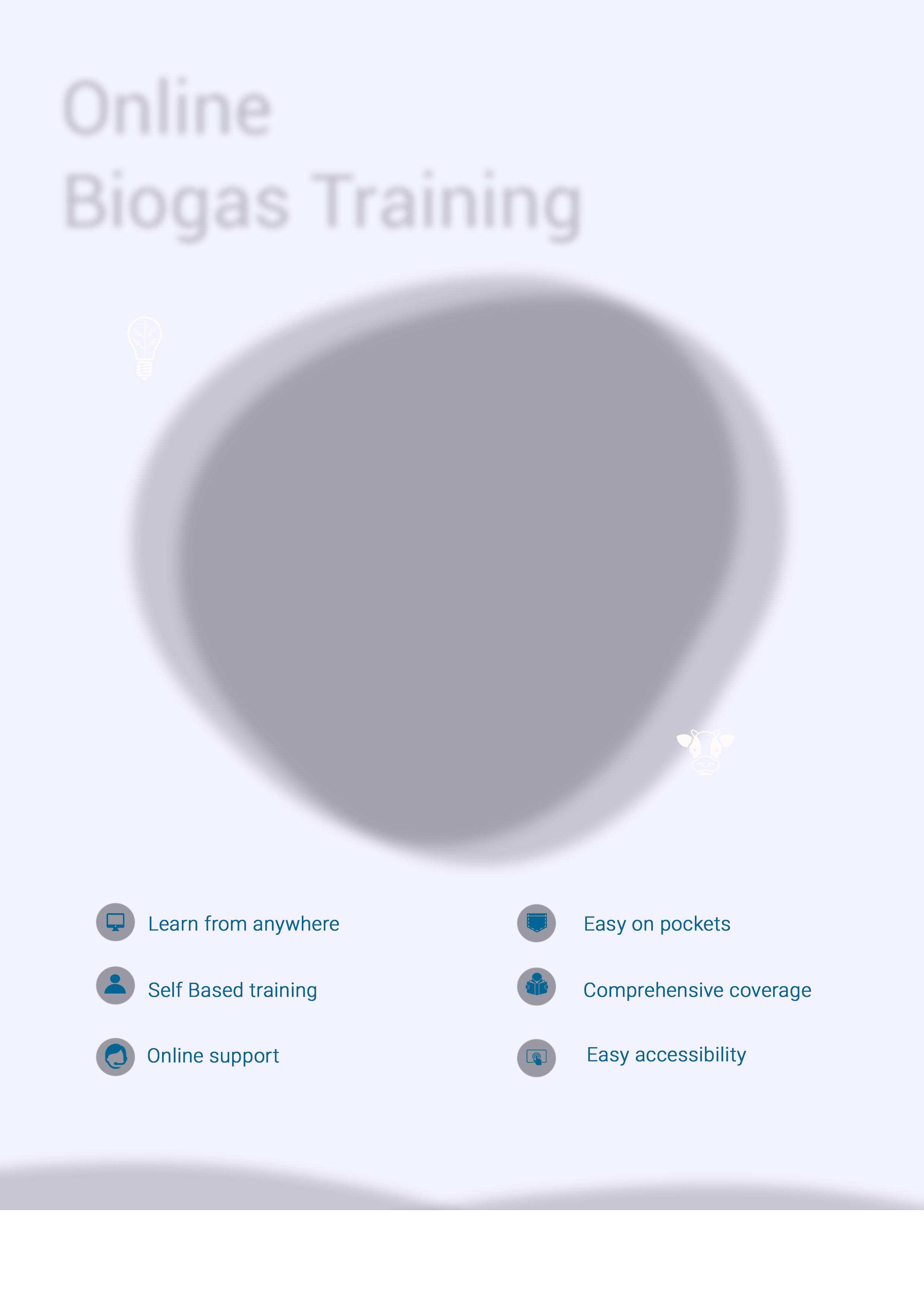
Contact Us: M: +91 7838447489 , +91 9289126306 E: vishal@biogas-india.com | service@biogasindia.com
From a sceptic to a pioneer
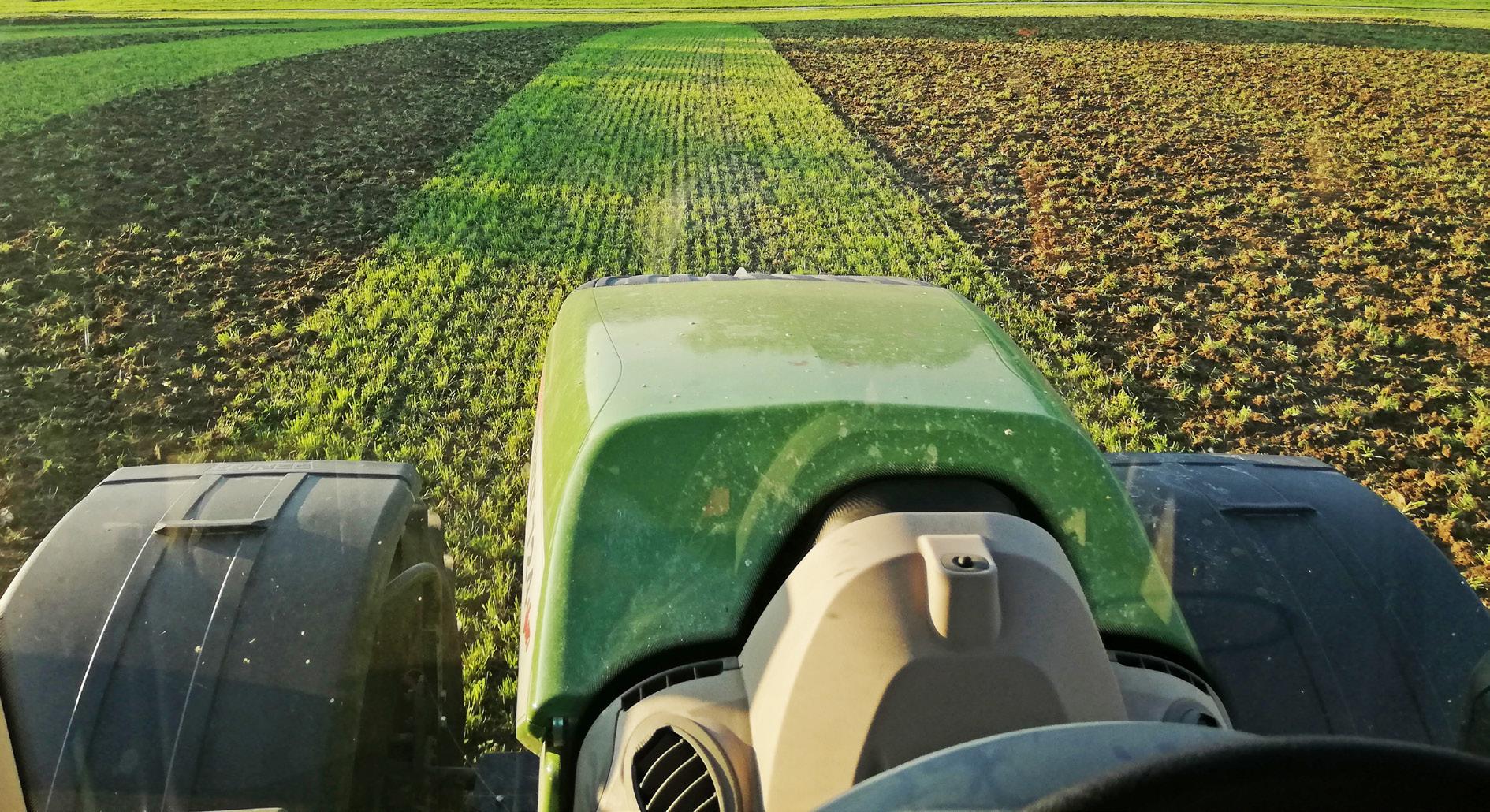
Hans Grötzinger is a passionate crop, biogas and organic farmer. He discovered renewable agriculture while searching for better soil fertility and stability in view of the climate change. He applies some of the measures mentioned under this term, but not all of them. He focuses on humification, a well-balanced supply of nutrients and organic fertilization. - By Christian Dany
Hilling in the Lower Bavarian district of Landshut: Hans Grötzinger sticks a spade into the soil of his field. “The chunks in the soil are good,” he explained. “They maintain the soil structure so that the soil won’t become too muddy when it rains. Below the chunks is the fine soil.” He then digs more than 30 centimeters below the surface. There is no visible cultivated layer, which is no wonder, as the organic farmer Grötzinger stopped using a plough three years ago.
Another interesting factor is the test with a one meter long soil probe: it can easily be pushed into the soil as far as it will go. 37-year old Grötzinger then inspects a field of fiveweek-old oat plants dispersed with buckwheat and goosegrass. “The buckwheat is from the previous catch crop and the goosegrass shows there is good nutrient availability,” he explains. We then see a demonstration of renewable agriculture live when his brother, Josef, works the remnants of a catch crop blend into the soil with a seedbed cultivator.
Grötzinger’s father Josef switched to organic farming in the Naturland Association as early as 1989. “We were a mixed farm, with dairy cattle and bullock fattening,” said Grötzinger. The quadrangle-shaped farmhouse lies on the main street of the village, just like some of the other farms. But most of the approximately 500 inhabitants live in the adjacent residential area. There are some large industrial companies nearby. Employment opportunities have accelerated structural change.
The smaller farms closed down about 30 or 40 years ago. Grötzinger himself also did not follow a predestined course of life. After his apprenticeship in agriculture, he no longer enjoyed working in that profession. “For five years, I worked as a paramedic. I wasn’t really interested in dairy cattle,” he said.
But when the special permit for livestock breeding expired, he experienced a turnaround: “We would have needed more pasture, but were a little too penned between the road and the Bina River,” said Grötzinger. He enrolled in the organic agricultural college
in Landshut-Schönbrunn and graduated as a master of agriculture. He later gave up livestock breeding and revolutionized the business: “We have a lot of clover grass in the crop rotation. That can be optimally utilized in the biogas plant. I have good technical skills, which is just what we needed,” said Grötzinger, who has two sons.
The biogas plant, which has an electric capacity of 210 kilowatts (kWel) was set up along the lines of the build-owner model in 2010 with connected load. A 100 kWel CHP unit for flexible operation was added in 2016. Grötzinger: “We operate a little according to the temperature.” That means full power, particularly in October and November, when grain maize is being dried, and in winter to ensure a guaranteed supply of heat for the seven households connected to the heating grid. In return, power is reduced in mid-summer. Grötzinger wants his plant to run as much as possible on residues which it does: The main component of the feedstock is grass silage made of grass clover and catch crops, 32 to 35 percent of it consists of sloped floor deep litter manure, which he buys in addition. Only 15 percent of it is maize silage. of linseed: “If it works, we’ll expand it.” He ventures into unusual farming methods in other ways, too: He cultivates spelt, oats, grain maize and even sweet maize, of which the cobs are picked and sold as barbecue maize.
Biogas plant as a nutrient supplier
On the organic farm, the biogas plant fulfills the important function of a “nutrient plant”. In return for the manure he buys, Grötzinger partly returns digestate as fertilizer and partly receives a nutrient input. He also cooperates with other biogas plants, from which he gets grass clover in exchange for the digestate. The Lower Bavarian considers cooperation an important aspect at many levels: In a community of five farmers, he tests and develops the cultivation Grötzinger sells around two thirds of the field crops as cash crop, one third goes into the biogas plant. “Reallocation and consolidation of the farm holdings resulted in a great infrastructure,” he says. Most of the farm boundaries have been readjusted and 80 percent of the fields are less than 2.5 kilometers away. They have an average size of about 4 hectares. And besides that, crop production benefits from the loess soils in this area. Crop and energy farmers also have about 20 hectares of grassland, many of which are wildflower meadows along the Bina River. Grötzinger farms a total of 150 hectares, a large part of which is leased land.
The basis of Grötzinger’s crop rotation is clover grass. He says that well-planned crop rotation will ensure a clean, healthy plant stock; for example, as a prevention against stone blight in wheat. Catch crops are planted after each primary crop to ensure that
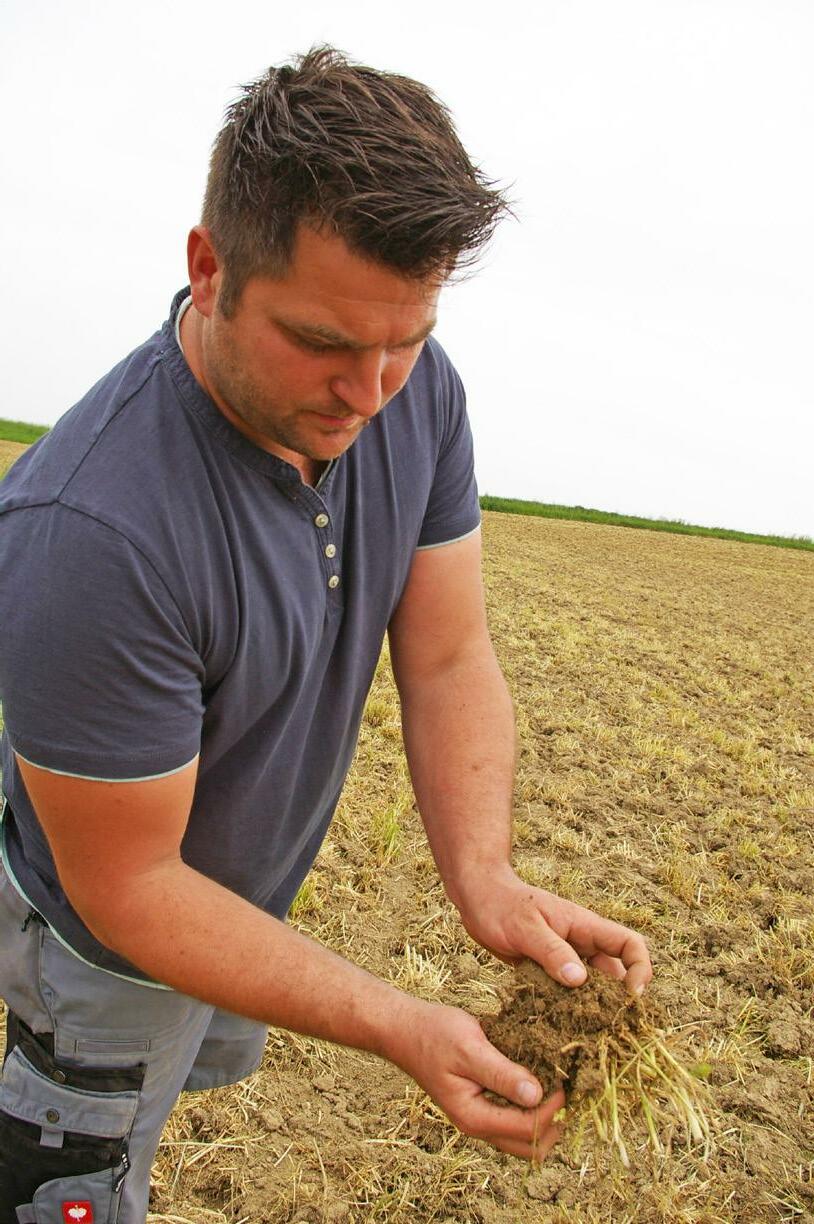
the soil is always covered. For example, he grows vetch rye or Landsberger mixture, which generally consists of vetches, scarlet clover and Italian ryegrass.
This mixture regularly brings the organic farmer a harvest of more than 30 tons of fresh matter per hectare with about 28 percent of dry substance. “That’s about half a maize harvest and there is also a cash crop on top of that.” The additional revenue and the humification more than make up for all the work and the hours spent on the tractor. Grötzinger has his own seed blending unit with which he can also make individual mixtures. Besides that, he also puts in more undersown crops when he plants grain and maize: for example, white clover, rye-grass or grain legumes.
Retting instead of ploughing
So far, not so good. “Even with good yields and good agricultural practice, the problems did not decrease, they rather tended to increase,” said Grötzinger. The yields were not stable enough, especially during dry periods. So he took a closer look at new forms of agriculture and how to brace himself for the climate change. He considers the enrichment of humus as the most important task for the future because of its capability to retain water and nutrients. “We have been planting
Biogas Magazine | Edition 19 | 23 catch crops for a long time now. We also used to have solid manure. We had 2.8 to 3.5 percent of humus, but did not manage to get more than that,” he said, looking back. He found solutions in principles that today are summed up as “renewable agriculture”. He changed the inversion and soil sampling methods and also organic fertilization.
He has been tilling the soil without a plough for about 4 years now, as it did more to destroy the life and structure of the soil than enhance it: “Ploughing interferes with the development of bacteria. Further down, there are anaerobic bacteria that are brought to the surface, which you can smell.” Instead of doing that, Grötzinger removes the crop residue and puts it into the surface retting. Later, he stirs the soil with a cultivator at a depth of about 15 centimeters and then compacts it with a Cambridge-type roller.
Anything that has a thick sward, like clover grass and Landsberger mixture, is cut right down to the roots,” he explained. The rotary tiller, that he leases, cuts to a depth of 3 to 5 centimeters. “If there are straw and maize stubbles, green rye and whole crop silage, we use a blade cultivator because it consumes less diesel.” The special hydraulic cultivator with adjustable depth can also cut plants to that depth. “That’s how I put organic material into the soil with maximum soil conservation,” said Grötzinger. He refrains from using retting control, like enzymes or the like: “It needs time. The material stays in there for three to ten days. The more there is, the longer it takes for the organic matter to be converted.” The chisel ploughing is followed by rolling. He says that is important to ensure that the CO2 is retained in the soil rather than being outgassed. And besides that, the soil retains its resistance to heavy loads much faster.
“If left for a few weeks, the soil becomes porous and compaction is reduced. We hardly ever need a rotary harrow, even though our soil is heavy.” Although this kind of tillage requires several cycles, it uses up less diesel: “We only use between 2 and 4 liters of diesel per hectare for each flat cultivating and rolling cycle.” The annual consumption is 28,000 liters, which is about 2,000 liters less than when he was still using a plough.
Fertilization according to Albrecht/Kinsey
The changing tillage methods go hand in hand with soil analyses according to the Albrecht/Kinsey method, which is applied to create a balanced proportion of nutrients in the soil and adequate levels of trace elements. Grötzinger explained the theory of “scar-
city despite abundance”: “Today, you have to eat ten times more salad than after World War II to absorb the same amount of trace elements. This method will provide us with food items that are simply more nutritious.” The farmer, who comes from Hilling, works with the agricultural retailer Josef Hägler and with Geobüro Christophel, and supervises the soil samples of other operating farms in the region.
The Albrecht/Kinsey method primarily focuses on the cation exchange capacity, which is a measure of the quantity of nutrient cations that occurs in interchangeable form and that is thus accessible to plants (for example Ca2+, Mg2+, K+). It also used to examine the interaction of nutrient contents, for which there are special ratios, such as the carbon:nitrogen ratio: “Within two years, we adjusted the C:N ratio to 9:1 (10:1 would be ideal). We started off at 5:1,” said Grötzinger, “That’s too tight for most of the farms, no matter whether they have dairy cattle or biogas.” According to Grötzinger, another indication is the calcium:magnesium ratio: “Ideally, it would be 68:12. We had 75:11. Too much calcium prevents other nutrients from being absorbed.”
Grötzinger also found that the pH level is not a decisive criteria: “There’s no point fertilizing according to a pH
Biogas Magazine | Edition 19 | 24 level.” In the past, too much calcium was often used in fertilization if the pH level was low. But he believes that if the nutrients are well-balanced, there will automatically be a good pH level of around 6.5. His farm was discovered to have a shortage of boron and sulphur. Sulphur deficiency is a widespread phenomenon, he said, but you need enough sulfur for nitrogen availability and to build up humus.
Grötzinger recommends having soil analyses made during the soil dormancy period before the soil is fertilized – ideally in November. Repeated analyses should then be made on the same date after two or three years. He recommends taking samples from a very good and a very bad area and from two or three average areas. A standard analysis costs around 100 Euros.
Digestate treatment with Leonardite and In-wa Quartz
Organic fertilization with organic manure from the biogas plant is of prime important on Grötzinger’s farm. He separates the thick part of the digestate and in that way, extracts around 500 tons of solid phase per year. Grötzinger processes the liquid phase with Leonardite and In-Wa Quartz, which are both approved in organic farming. “The high proportion of grass clover produces 7 kilograms of nitrogen per cubic meter in the manure. Despite the high protein content, the digestate no longer smells after it has been processed. That works one hundred percent,” he says. The In-Wa Quartz makes the manure black, although only 0.5 liter of it is needed for every 100 cubic meters. The digestate goes into a rotting phase and that brings
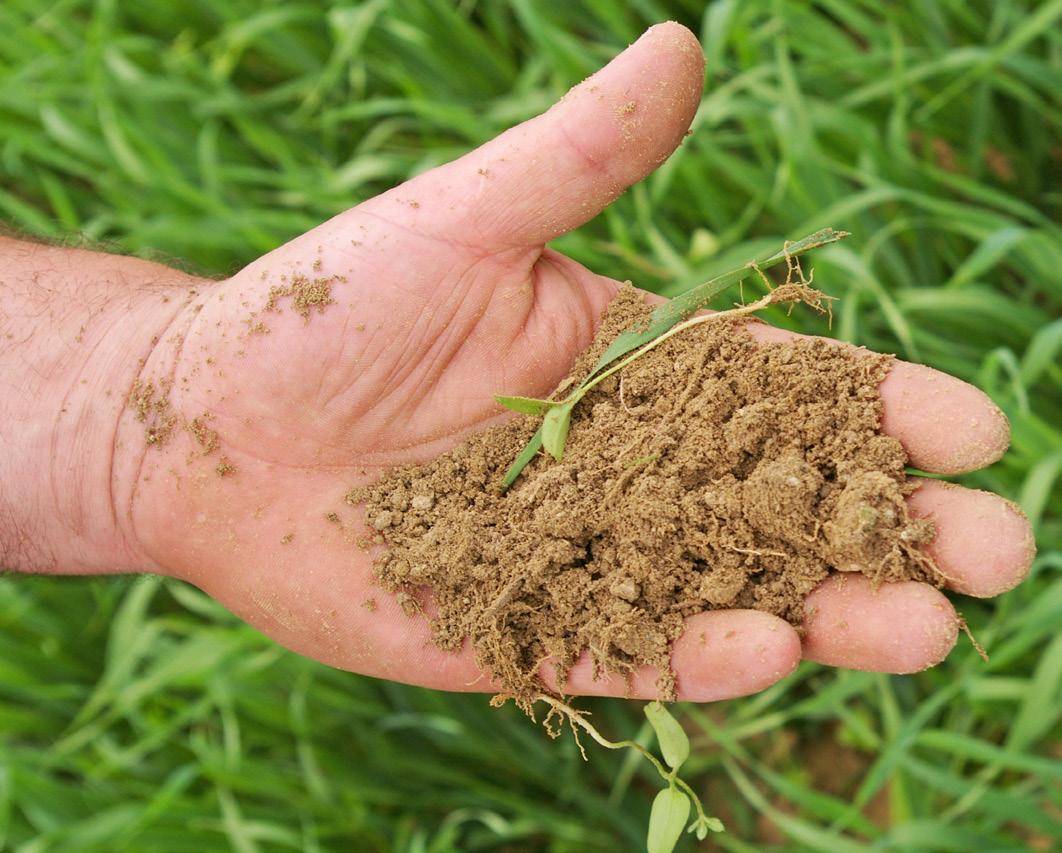
“There’s no point fertilizing according to a pH level” - Hans Grötzinger
about a stimulating effect for self-protection.
“In an experimental field, we treated organic rapeseed with In-Wa Quartz and lime,” said Grötzinger when talking about a particular incident.
“The rapeseed had been completely infested with the rapeseed gloss beetle. The next day, there wasn’t a single beetle to be seen.” He says that Leonardite is a lignite precursor that results from the humification of plant matter. That makes it rich in humic acids (up to 90 percent). “The Leonardite binds the nitrogen and the plant gets it little by little, whenever it needs it, which means that there is no free nitrogen present in the soil.” This conditioning prevents nitrate from being leached out. “I have two digestate storages,” he said when explaining his nutrient management methods. “The digestate from the farms that supply me with clover grass is not treated, unless this is expressly requested. The treatment costs 1 Euro per cubic meter.”
Composting digested, separated solids
Grötzinger spreads liquid digestate with the trailing shoe method and makes sure it is distributed over cultivated fields. That can be achieved by cultivating catch crops and by splitting the individual applications. “We no lon-
Biogas Magazine | Edition 19 | 25 ger have any fertilizer burn. Spreading manure over open soil would cause rotting,” he said. “You would ‚encourage‘ weeds to grow.” Grötzinger has also produced “MC compost” from the solid phase. “To do that, the material is spread on a storage clamp and compacted.
The nitrate and moisture content must be well-balanced. It takes eight weeks for compost that is rich in humic acid to form and that way there is less carbon loss than in usual compost,” he explains. According to the current fertilizer ordinance, MC compost may no longer be produced on open fields, although as it turns out, it is completely dry beneath the storage clamp and Nmin sampling has not shown considerable amounts of nitrogen. That is why Grötzinger stores the solid phase in a covered horizontal clamp and then distributes it like that. time. “Everyone is in a hurry, nobody wants to wait.”
He criticizes the lack of patience and the fact that liquid manure or digestate is then spread on the fields in as early as March. “If you see how wet the soil is, you shouldn’t be driving over it with a total weight of 25 tons.” He said that last year, he sowed maize as late as June 2nd and then managed to shred 60 tons of fresh matter; and that is all grown organically with a supply of 15 cubic meters of digestate. “I’ve never known anyone not to succeed because they did something too late, but rather because they did it too early. Just wait and keep cool,” he says. “If you take pleasure in the method and the soil, the rest will practically work by itself.”
Reprinted from
- Biogas Journal
“The system needs time to warm up,” Grötzinger summarizes. He maintains that you cannot expect any miracles overnight. But the trend in the right direction became clear quite quickly. “We managed to produce between 0.2 and 0.5 percent of humus within three years – depending on the location,” he said. But he spends a lot of time on the plant production system, criticizing that the biggest problem of some of the farms nowadays is the lack of
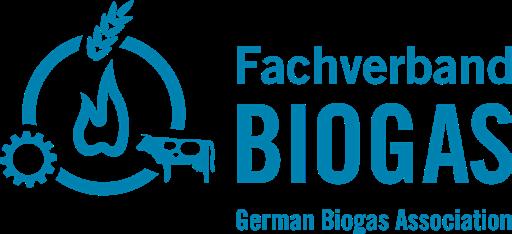
Images owned by
German Biogas Association