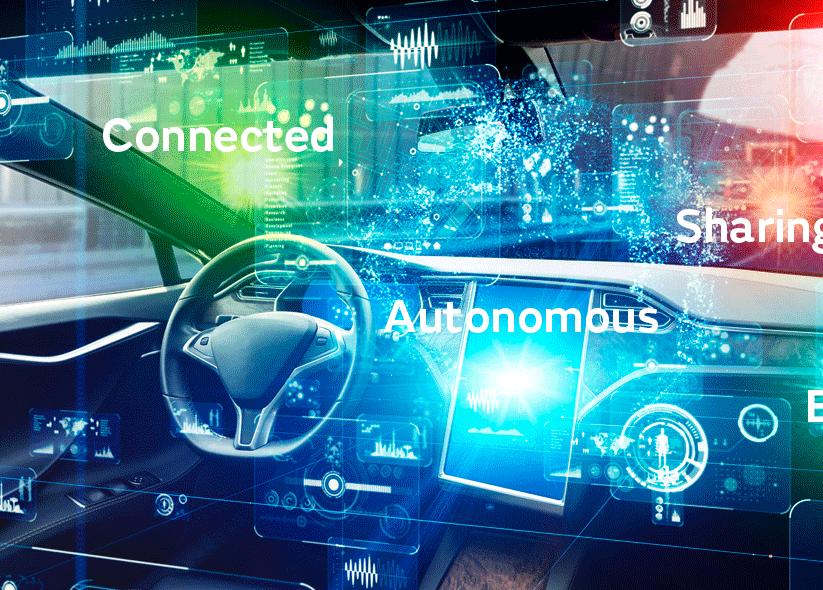
12 minute read
AUTOMOTIVE - EXCLUSIVE
Automotive MLCCs
Balancing Reliability with Miniaturization and High Capacitance in a Closely Intertwined Evolution with the CASE Trend
Advertisement
CASE trend supported by the evolution and expanding range of utilization of electrical and electronic circuits
The automobile industry is in the middle of a once-in-a-century revolution in line with the CASE trend (Figure 1). The CASE trend refers to four initiatives transforming cars and the car business; the acronym stands for “Connected,” connecting cars to the network at all times, “Autonomous,” to realize automated driving, “Shared and Services,” renewing the business models that provide means of mobility and transportation, and “Electric,” which is changing the main power source from engines to motors.

Figure 1. Once-in-a-century “CASE trend” revolution transforming the automobile industry
The four changes of the CASE trend share one aspect. As means of implementing automotive functions, they all depend on electrical and electronic technologies and IT technologies. Previous cars were an assembly of advanced machine technologies. In contrast, next-generation cars are transforming into something completely different, referred to as a “running computer,” “cluster of semiconductors,” and a “moving data center.”
Currently, there are already examples of one car equipped with more than 100 control computers (Electronic Control Unit: ECU). With the goal of increasing the convenience, comfort, safety, and environmental performance of cars, that number continues to increase. In addition, hybrid vehicles, electric cars, and other electric vehicles (xEV) are now equipped with many electronic circuits that precisely control high-voltage power reaching as much as several hundred volts. The CASE trend is accelerating the diversification and increase of such advanced electrical and electronic circuits.
MLCCs are the cornerstone of the safety and reliability that support the stable operation of on-board circuits.
The electrical and electronic circuits utilized in cars to implement various functions do not consist of just CPUs, memory, power devices, and other semiconductor chips. Countless numbers of capacitors, inductors, and other passive components are used in electrical and electronic circuits to stabilize the operation of semiconductor chips and adjust handled data signals and power supply waveforms. Without these passive components, electrical and electronic circuits cannot be operated as designed.
Among the many passive components, MLCCs (Multilayer Ceramic Capacitors) are one type of component that is often utilized in on-board electrical and electronic circuits in particular. Capable of realizing a miniature size and high capacitance while maintaining their characteristics in a hostile environment, the features of MLCCs are perfect for on-board use, which requires them to be utilized in electrical and electronic circuits in narrow and unforgiving spaces. Currently, as many as 3,000 to 5,000 MLCCs are utilized per vehicle. Looking at a smartphone as a representative example of an advanced electronic device, if we consider that even the latest high-end model includes 1,000 MLCCs, contemporary cars could be described as a “collection of MLCCs.” Therefore, the type and number of MLCCs utilized in cars may further increase as the CASE trend progresses.
Murata Manufacturing is the global leader supplying approximately 40% of MLCC components (Figure 2). Limited to just automotive MLCCs, Murata supplies 50% of the market, for an even higher share. This shows that the strengths of Murata’s MLCC technology stand out due to the harsh technical requirements demanded of such applications. Automotive MLCCs are components utilized in machinery that is responsible for human life. Therefore, they require a higher level of quality and reliability that is completely different from the MLCCs used in consumer devices. Only a handful of manufacturers are able to develop and supply automotive MLCCs, and Murata in particular is the industry leader in cutting-edge products.
In accordance with the progress of the CASE trend, more advanced electrical and electronic circuits will be utilized in greater numbers than before. Of course, the technical requirements with respect to MLCCs will also likely increase. Moreover, MLCC suppliers are also required to maintain production systems that can provide a stable supply of advanced components that are directly linked to the safety and reliability of cars. In terms of technology development and production system maintenance, Murata is able to supply automotive MLCCs with the quality and quantity required in the CASE era. Going forward, we will continue to support this automobile industry revolution through our technical, production, and support capabilities.
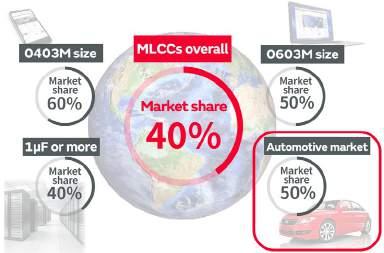
Figure 2. Murata’s market share of MLCCs
Utilizing our strengths in integrated manufacturing to create automotive MLCCs that are one step ahead.
Contemporary cars are equipped with a large number of MLCCs. MLCCs are essential components for the proper and stable operation of the various electrical and electronic circuits utilized in cars. Automotive MLCCs must also provide a miniature size and high capacitance similar to those used in smartphones. However, because they are linked directly to the safety and reliability of cars, which are responsible for human life, automotive MLCCs must prioritize the implementation
of a higher level of quality that is completely different from the MLCCs for consumer devices. Murata provides MLCC products that support the evolution of cars in the CASE era through our industry-leading technical and production capabilities. We spoke with two automotive MLCC product technology managers who are well versed in the application and technology requirement trends in the automotive industry about the type of MLCCs required in the CASE era, the frontlines of technology development to meet those requirements, and future developments.
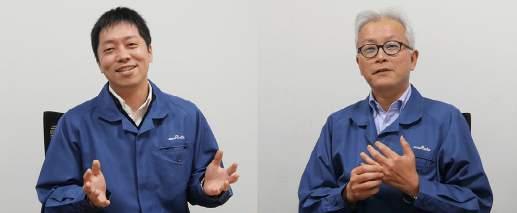
Marketing Manager Satoshi Yoshida &
Marketing Senior Manager Takahiro Yoshida
Cars are a "collection of MLCCs" and also an "MLCC museum"
--Roughly how many MLCCs are equipped in cars in the CASE era?
Contemporary cars are already equipped with electrical and electronic circuits to implement various functions, and MLCCs are used in various applications. A large number of components are used, and even the typical engine-driven vehicle that does not have an automated driving feature uses approximately 3,000 MLCCs. If the use of electrification and advanced automated driving features advances, the number of MLCCs used will surely increase further. For example, there are already luxury electric vehicles (BEVs: Battery Electric Vehicles) equipped with Level 2+*1 automated driving features that use more than 10,000 MLCC components (Figure 3).
*1 SAE International, a U.S.-based automobile industry group, has classified and defined Level 0 to Level 5 for automated driving systems according to the degree to which the system makes decisions and handles operations. Within these five levels, Level 2 is defined as the stage in which the system “controls both the steering and acceleration/deceleration under limited conditions.” While the driving is fundamentally performed by the driver, the system aims to provide driving assistance according to the situation. In contrast, Level 3 is the stage in which “the driving is fundamentally handled by the system except in emergencies.” Level 2+ indicates that although the system carries out more advanced decision making and control than Level 2, the system is fundamentally operated by the driver.
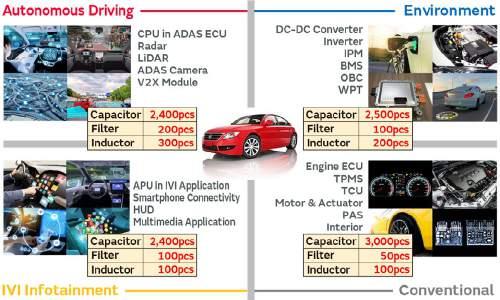
Figure 3. MLCCs used in luxury electric vehicles (BEVs) equipped with Level 2+ automated driving features
--Smartphones are an application of cutting-edge MLCCs. What differences are there between MLCCs for smartphones and those used on-board automobiles?
Automotive MLCCs require a higher level of quality and include many different types.
First, in terms of quality, it is essential that MLCCs realize a level of quality that is an order of magnitude higher than is referred to as “automotive grade.” Product development and production initiatives aiming for zero defects and a long operating life are required. Some MLCCs for smartphones are designed with a guaranteed operating life of a minimum of five years or more. In contrast, automotive grade products must guarantee an operating life of 20 years or more. More advanced technologies and a strict production system are required to improve quality even for MLCCs with the same size and capacitance, and the technological hurdle to implement automotive-grade products can be said to be considerably high. Not only is a higher level of quality required, but more diverse MLCCs are needed as well. Smartphones are also equipped with various electronic circuits, but most of the MLCCs used therein are miniature and high capacitance products. In contrast, the on-board parts associated with automated driving features and connectivity use miniature and high capacitance products with automotive level quality. The required specifications and technical requirements differ depending on whether they are for connectivity, automated driving features, or other applications. At the same time, the parts that drive and control the xEV’s main motor and battery require high-quality MLCCs that support high voltages.
--In terms of quantity, cars of the near future were described as a “collection of MLCCs,” but in terms of variety they can be called an “MLCC museum.” Will such a trend become more prominent due to the progress of the CASE trend?
That is a good question. When we conceptualize a car, which crams in all of the features implemented through electrical and electronic systems under the evolution of cars in line with the CASE trend, we get a connected BEV that is equipped with automated driving features. Realizing such a vehicle
requires the implementation of electrical and electronic circuits that are more advanced than ever, and the number of utilized components will also increase. Of course, automotive MLCCs must also evolve according to the development of applications, and the supply system must also build up to meet the increased demand at the same time.
However, the question of whether the number of components used will increase beyond the currently expected number of 10,000 components per vehicle must be carefully examined. Because the failure rate will also increase if the number of components in electrical and electronic circuits increase, a trend in technology development will likely emerge that attempts to assemble advanced and multifunctional circuits using as few MLCCs as possible. I think that solutions that combine the roles of multiple MLCCs into one will be required. This area is one issue that I feel we will have to address going forward. We have already started to propose measures to customers for reducing the number of components used. The product category mix depends on the breadth of applications that are currently visible, but we feel that it will settle down within the expected range. However, if there is some sort of new development in systems or circuit configurations, new MLCC demand may emerge. For example, at the current time BEV inverters and DC-DC converters mostly use silicon power devices. However, if SiC (silicon carbide)*2 devices or GaN (gallium nitride) devices were to be used in such applications, the specifications and configuration of electrical circuits would change, and capacitors with new specifications might be required. *2 SiC and GaN are semiconductor materials that are attracting attention as materials for creating power devices with high energy efficiency to replace silicon. Silicon carbide has already been adopted for use in on-board chargers and inverters in electric vehicles, and there are examples of practical applications. Gallium nitride has been practically applied as a material in power devices for realizing miniature AC converters, etc.
Releasing globally pioneering products one after another to the market
--Currently, what kinds of MLCCs is Murata releasing to the market for any type of application?
We are releasing a variety of product types for a fairly broad range of applications (Figure 4). We are releasing automotive grade products that are miniature, high capacitance, and low inductance (low ESL*3) as products that support the connectivity (“C”) and automation (“A”) aspects of the CASE trend. As examples of cutting-edge miniature and high-capacitance products, we have released the 1608M (1.6 x 0.8 mm) size with a capacitance of 10 μF and a withstanding voltage of 6.3 V, the 3216M (3.2 x 1.6 mm) size with a capacitance of 47 μF and a withstanding voltage of 4 V, and the 3225M (3.2 x 2.5 mm) size with a capacitance of 100 μF and a withstanding voltage of 2.5 V. Murata was the first company in the world*4 to commercially release these products, which lead the industry in terms of miniaturization and high capacitance for on-board use. *3 ESL stands for equivalent series inductance and is an indicator that represents the impedance of an AC signal that exists in series, resulting from the capacitance of an MLCC or other device. *4 As of December 2020
In the area of low ESL products used around the periphery of power supply control ICs in automated driving systems, which make it possible to reduce the number of components, we have released distinctive products such as the 1005M (1.0 x 0.5 mm) size at 1 μF and 4V and the 1608M size at 10 μF and 4V three-terminal capacitor (model number: NFM). In this case as well, Murata was the first company in the world to release such products to the market. In addition, CPU processing power is increasing with the growing sophistication of automated driving, and we are receiving requests to mount capacitors within packages. In order to meet such needs, we released the 0510M (0.5 x 1.0 mm) size, which is a 1 μF, 4 V LW reverse capacitor with a low ESL and a thin form factor (maximum thickness of 0.22 mm) that can be embedded within a package. Meanwhile, to support the “E” of “Electric,” we released 10 nF and 630 V products with C0G (stable temperature characteristics) in the 3216M (3.2 x 1.6 mm) size, 33 nF and 630 V products with C0G in the 3225M (3.2 x 2.5 mm) size, and 54 nF and 1 kV capacitors with metal terminals and C0G in the 5750M (5.7 x 5.0 mm) size as MLCCs for use in on-board chargers*5 (OBC), which charge secondary lithium-ion batteries. *5 An On-Board Charger (OBC) is a piece of equipment that converts household AC power supplies to direct current to charge the battery utilized in an electric vehicle, etc.
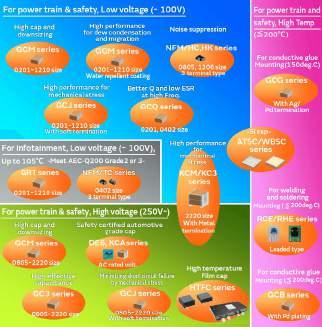
Figure 4. Murata’s lineup of on-board capacitors
--Murata has many world’s-first products and seems to be truly leading the industry.
It can certainly be said that Murata is leading the industry when it comes to products for connectivity and automated driving. However, regarding products for electrification, there are still some areas, including other types of non-MLCC capacitors, where competitors lead. Naturally, we will catch up in these areas soon, but because we believe that Murata’s strength lies more than anything in its high level of quality, we plan to release unbeatable products featuring a high level of quality, which is most important for on-board use.
About This Article:
This article is provided by Murata Manufacturing Co., Ltd.