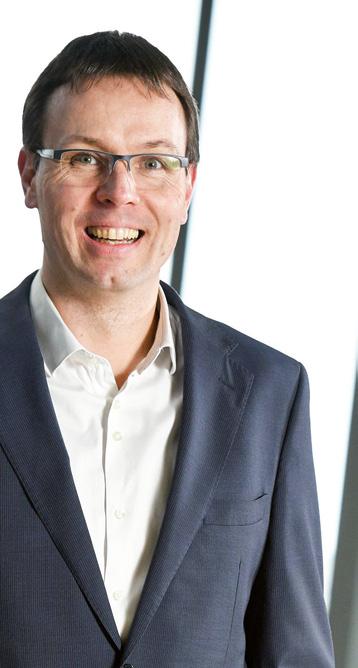
8 minute read
Demand for Dutch diagnostic SMEs curves with corona
With the increasing market demand, the corona crisis caused Micronit to ramp up production. This was challenging, because of the disrupted supply chain. However, Micronit CEO Ronny van ’t Oever also sees the opportunities this crisis offers for innovative Dutch medical SMEs like his.
Jessica Vermeer
Advertisement
One of the early goals in fighting a disease like COVID-19 is to map the virus and its family. This can be done by determining its specific DNA sequence. “If you know the DNA, or in this case, RNA sequence, you can effectively develop the necessary PCR reagents,” explains CEO Ronny van ’t Oever. Polymerase chain reaction (PCR) is a method used in molecular biology to make billions of copies of a DNA sample, which are then used to identify infectious agents.
Enschede-based Micronit is the producer of chips that allow specialists to determine the DNA or RNA sequence of viruses. Sparked by the spread of the corona pandemic, the company’s products have seen an enormous increase in demand. “Within a few weeks, our entire safety stock ran out,” depicts van ’t Oever. Seeing his team’s response, however, gave him a great sense of pride as an entrepreneur. “At times like these, my team shows an admirable passion and drive.”
The rising demand is especially difficult to meet as supply chains become threatened or disrupted. Van ’t Oever explains, “Our second supplier dropped out completely in the face of a demand that had doubled. So, that was a sizeable obstacle we had to overcome. We needed all hands on deck.” As many Asian factories closed, it was evident that simply obtaining products from the supply line was a serious challenge. “Fortunately, it’s been manageable so far. But it has really exposed our dependence on international factories.”
World player
Founded in 1999, Micronit originally focused on the miniaturization of devices
Ronny van ’t Oever sees a tremendous innovation potential in the Netherlands.
Credit: Micronit
using microtechnology. Over the years, however, the business shifted its focus to microfluidics for application in life sciences. These days, its product development department is working on new applications like lab-on-a-chip, which is designed for quick testing and can produce lab-quality results within an hour, and BioMEMS.
Although the corona crisis has driven the increase in interest of these kinds of technologies, Van ’t Oever sees most of the developments in his company proceeding in a business-as-usual fashion. “Our plans for a new building at Kennispark Twente are still on track. And despite a lot of our employees working from home, business processes are continuing surprisingly well.”
Looking to capitalize on and continue with this positive momentum, Micronit is setting some lofty goals. “We want to become a world player in DNA-related in-vitro diagnostics. By building multiple functionalities onto a chip, testing is simplified,” highlights Van ’t Oever. “To really succeed, our aim is to simplify these laboratory tests so they can be performed by personnel with lower levels of education.”
Innovation potential
The corona crisis is bringing attention to the importance and necessity of this sector in the Netherlands, notes Van ’t Oever. “There’s a tremendous innovation potential within the companies operating in our field, especially within SMEs.” One example he gives: organ-on-a-chip applications, which can be used for quicker medicine tests. “Vycap, for instance, is focusing on isolating cells, while Biosparq is working to optimize treatment of bacterial co-infections. Suddenly, the innovations of these relatively small companies have priority.”
Even though getting the right materials has priority, for now, Van ’t Oever thinks there’s huge potential for the future within the Netherlands. The sharp awareness also brings great opportunity. “Suddenly, companies and research facilities may actually get to finish certain innovative products. This could allow us to build the value chain closer to home and decrease the dependence on international suppliers.”
Anton Duisterwinkel is business developer HTSM at Innovationquarter.
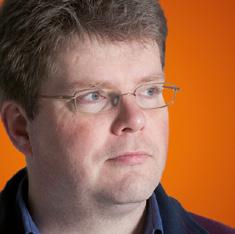
Corona crisis: chance for change
On a busy road, one driver hits the brakes. The car behind brakes harder. The third car comes to a full stop. And the fourth crashes into the third, badly damaging both cars. This is how a chain collision often starts. This happens not only on the road but also in economies. Scared consumers hit the brakes, buying much less than they used to do. End-product makers stop buying machines and instruments. Machine and instrument manufacturers come to a complete standstill. And their suppliers go bankrupt. We need to recognize that this is happening right now and move quickly to prevent the biggest industrial crash ever.
Never in history did consumers hit the brakes as hard as today. Consumer confidence plummeted in an unprecedented fashion. Even companies that at the moment see little change will be hit in a few months. The Dutch government has rapidly built a first-aid kit for businesses that were immediately hit by the corona crisis. However, the Dutch manufacturing industry will soon require intensive care, as it consists mainly of machine and instrument suppliers (OEMs) and their suppliers, first and second tier.
At the same time, we notice a sudden awareness of the importance of the manufacturing industry as a supplier of (corona)tests, face masks, breathing kits and other vital stuff. Both people and politicians are now aware of our dependency on faraway regimes that either cannot or do not want to deliver products. And they’re becoming aware of the fact that complex value chains shut down when one tiny part can’t be delivered. We were already starting to become aware of the dangers associated with growing protectionism and foreign takeovers of our innovative companies, but the corona crisis has opened our eyes all the way.
Therefore, we need to work right now on our European production chains. Making them shorter and more effective. Creating flexibility
We need production sovereignty
to manufacture whatever vital stuff is needed in any crisis. And making production chains more circular and therefore less susceptible to geopolitics on the fly. We need production sovereignty: the ability to quickly and affordably produce critical goods.
The best way to do so is to set up a digital, flexible and resilient production network, a virtual smart factory. Ideally, it will operate regionally, so that parts don’t have to cross borders. For individual companies, this may not seem attractive: typically, entrepreneurs will want to sell and source worldwide. We shouldn’t hinder them in doing so. However, I’ve already spoken to entrepreneurs who have changed their sourcing strategy, ensuring that they buy at least 20 percent of each item within Europe. That could be a good policy for governments, non-governmental agencies and even manufacturing companies.
Let’s start building our smart production network now. We can map and redraw production chains and share our intel on good regional suppliers. We can start a virtual smart factory by building and using (European!) data platforms. We can adopt and stimulate the use of flexible manufacturing technology such as 3D printing and smart robots. And we can persevere in innovating products and production technology.
Governments can contribute by stopping the import of unsafe products by enforcing EU standards. And by smart and fast licensing of flexible production sites, as well as by rapidly implementing 5G networks and acting as launching customer for breakthrough technologies. Governments can also increase access to training 21 st -century skills. And finally, they can set up well-targeted financing of innovations needed for the virtual smart factory and new, circular, value chains.
ONE-AND-A-HALF BETTER CHALLENGE
The COVID-19 virus has a big infl uence on people’s lives. Some say we should go ‘back to normal’. But this crisis could also be the start of a new, better world, beginning with the development and design of new ideas. The Discovery Factory, together with Philips, challenges children and youngsters to create inventions for the so-called “one-and-a-half-meter society.” For example, they can design solutions to improve contact with their grandparents in the new reality of social distancing.
OOne-and-a-half better
This new challenge tries to help the world with better ideas. Chris Voets of the Discovery Factory says: “We can benefi t from the fresh views from children in adapting the lessons of the coronavirus to the world as a whole. But this project also aims at involving children and parents to the new corona rules.” Philips’ Frank Visser adds: “You can’t get past technology in our society. It’s everywhere! Philips sees an important role for tech companies inspiring youngsters for a future in technology. With this new project, we want to support children to face the challenge at home, together with their parents. With the help of our experts, we encourage them to invent creative solutions that could play an important role in these particular circumstances.”
Statue for the best inventors
The challenge itself also is corona proof; together with their parents, children can work out their ideas and submit them on the project website anderhalfb eter.nl. The best inventions will be rewarded with a 3D-printed statue of the inventors themselves. It’s important that young inventors get this appreciation and it certainly helps the image of the tech industry so that youngsters will apply for tech studies, also in this new future world.
The Discovery Factory is there to inspire youngsters for a future in design and technology. Projects are supported by tech companies such as ASML, Brainport Industries, Daf Trucks, Frencken Europe, Hager, NTS Group, Philips, Stam en De Koning and VDL Group, and by Bits&Chips as the media partner.
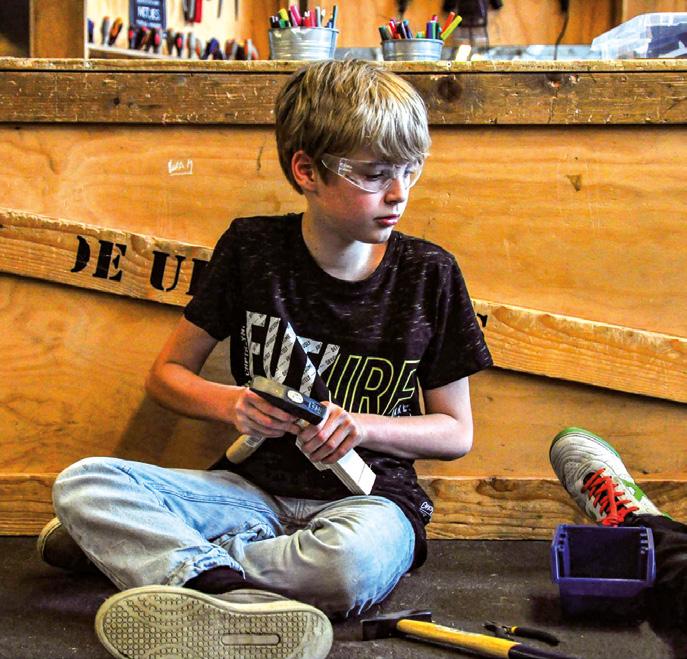
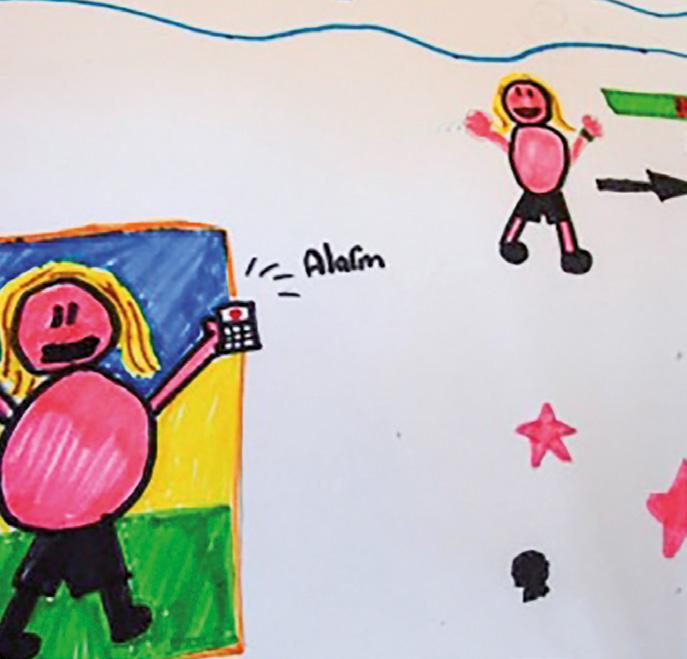
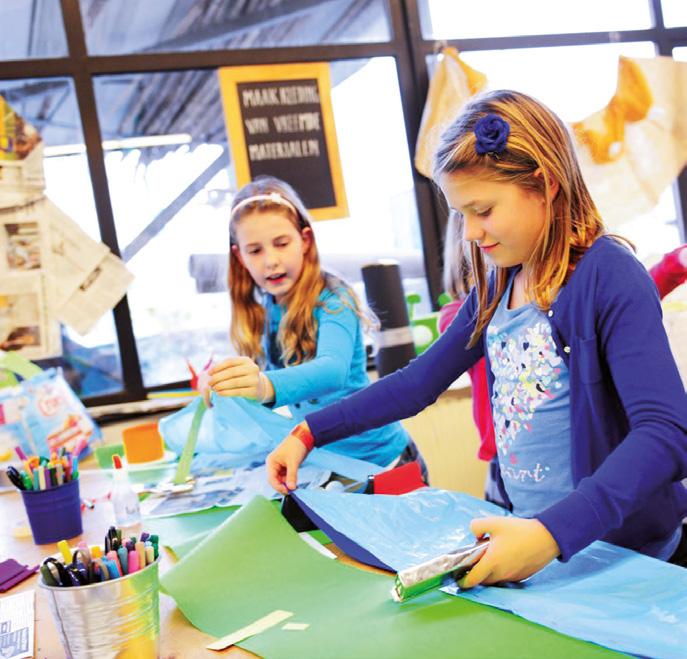
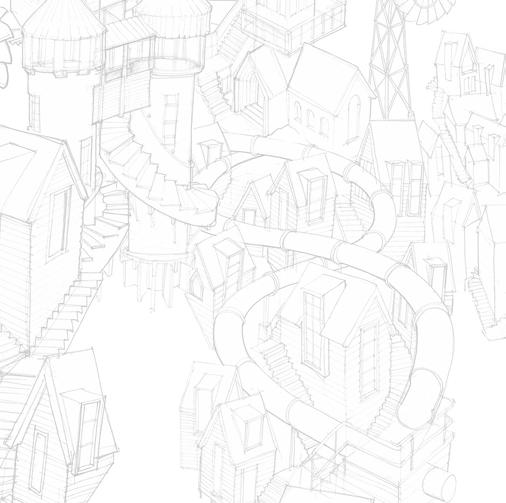
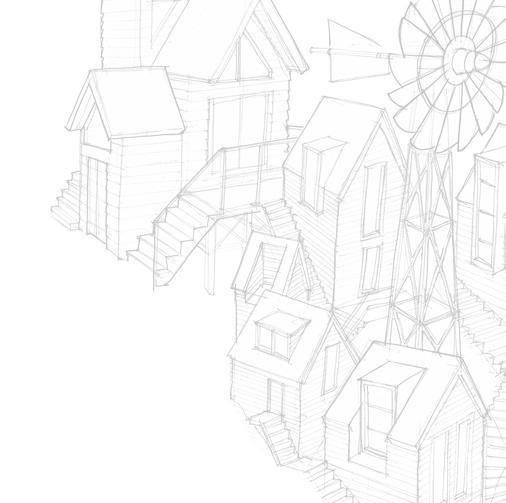
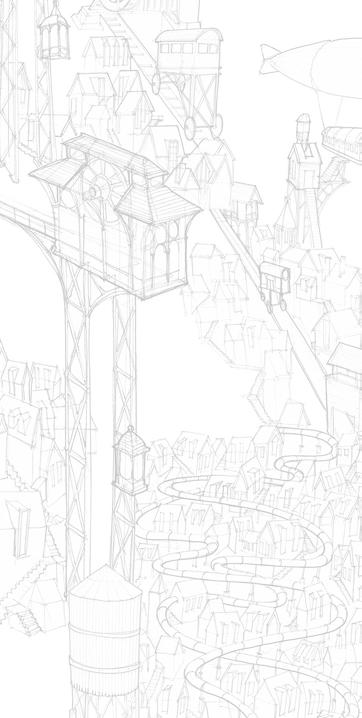
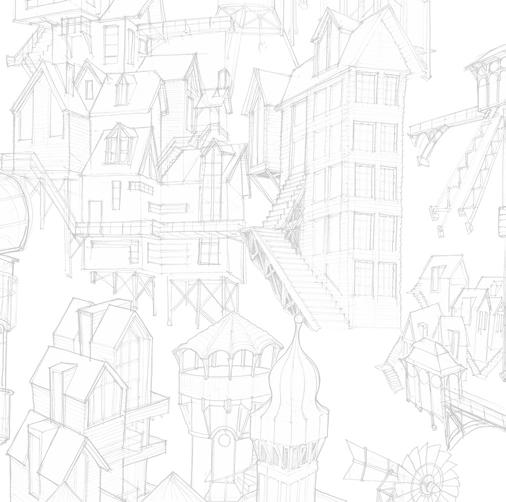
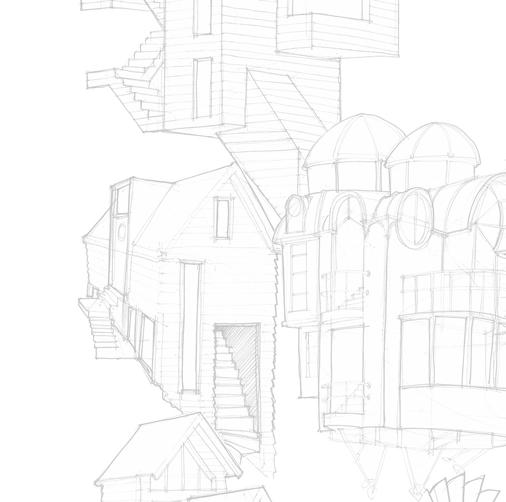
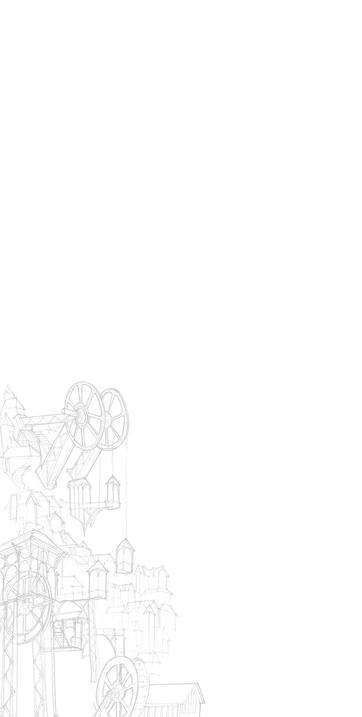
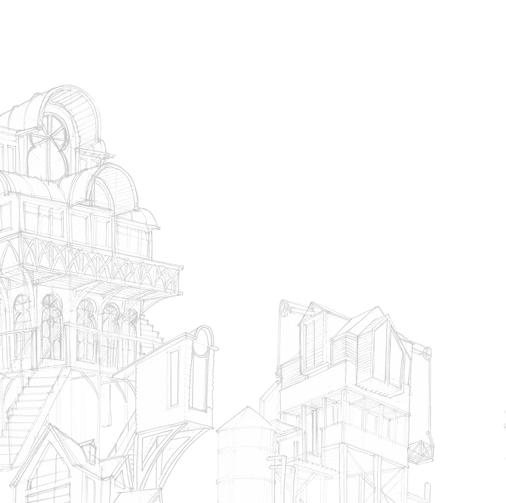
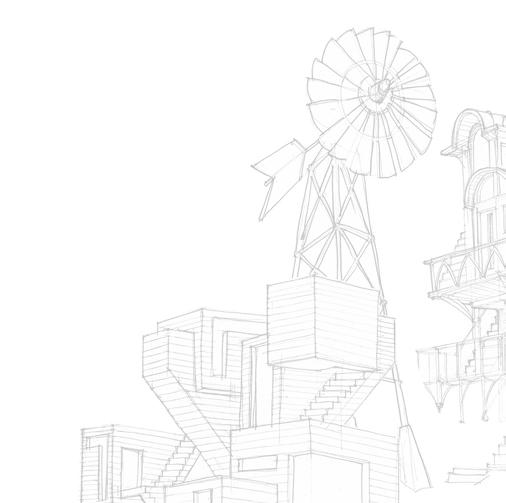