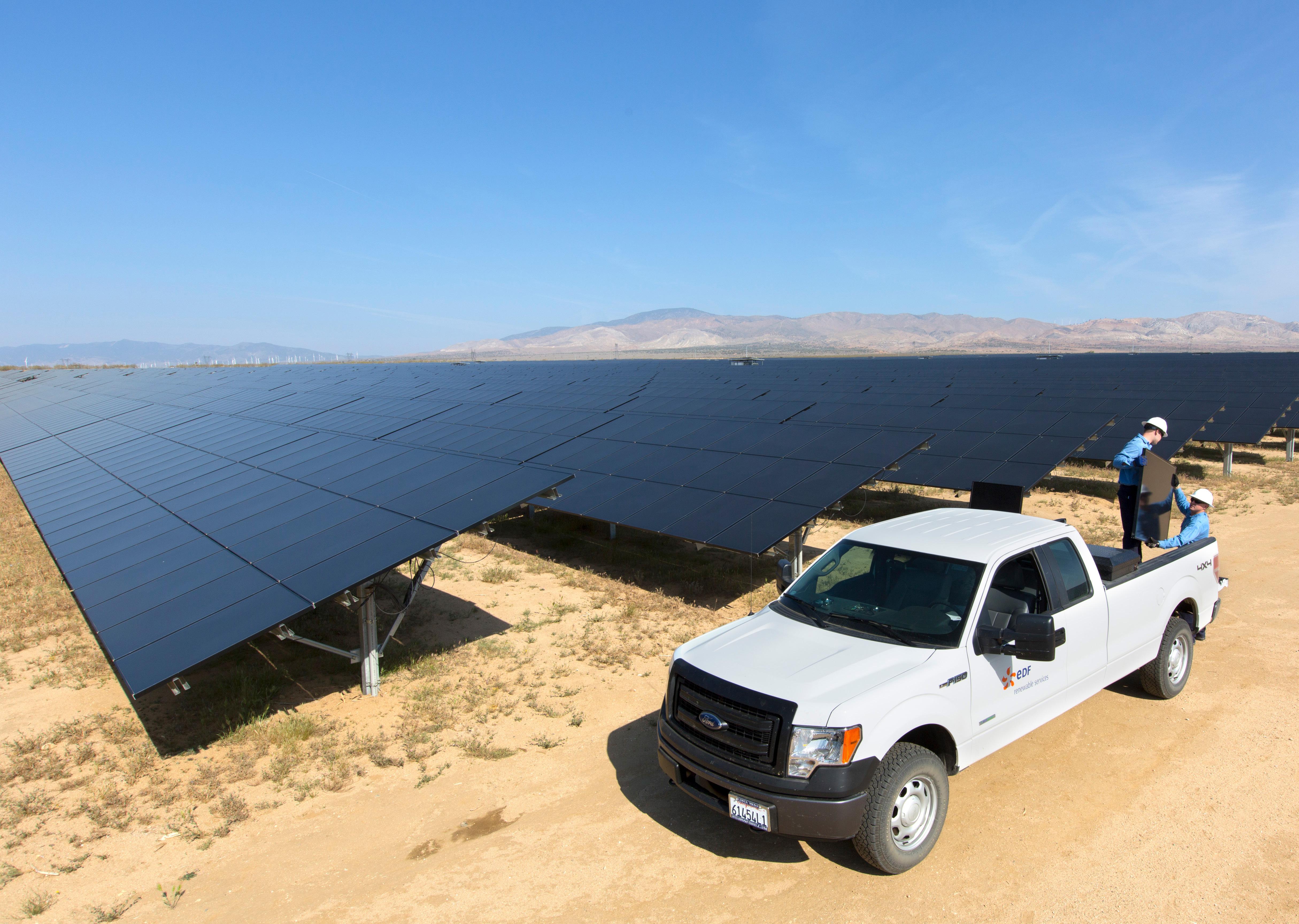
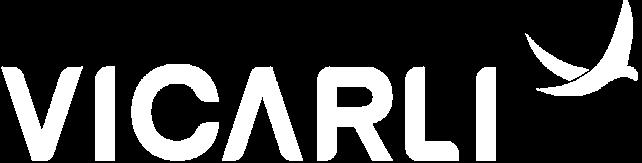
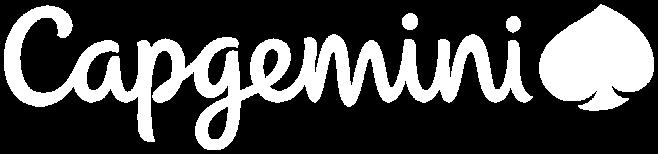
Senior Director of Supply Chain Dirk Ruitenberg shares how centralising inventory and reverse logistics are core to sustainable business
In the ever-evolving landscape of renewable energy, leaders from all corners of the sector are considering how best they can navigate challenges, all while remaining at the forefront of innovation and pioneering change for the betterment of business and the planet as a result.
Cue Dirk Ruitenberg, Senior Director of Supply Chain at EDF Renewables North America, a driving force behind the strategic supply chain initiatives shaping the future of renewable energy. An executive with a supply chain career spanning two decades — 17 years of which working in the renewables sphere — Ruitenberg has a rich background in logistics and utilities, spearheading the development and implementation of strategic supply chain initiatives.
It’s this rich experience that he leverages to help EDF Renewables meet its own ideas of operational excellence and environmental stewardship, solidifying its place as one of the largest utilities globally by revenue and largest carbon free electricity producer in the world. In his role in particular, Ruitenberg is responsible for developing and implementing the overall supply chain strategy for the asset optimisation business which takes care of asset management, operations and maintenance and remote
TITLE: SENIOR DIRECTOR OF SUPPLY CHAIN
LOCATION: NORTH AMERICA
Dirk Ruitenberg is leading the Supply Chain function of EDF Renewables’ Asset Optimization business unit in North America. In this position he is responsible for developing and implementing the overall supply chain management strategy, including procurement, fulfillment, logistics, warehousing and quality control of goods and services.
Prior to joining EDFR in 2019, Dirk held various global supply chain roles for Acciona Energy since 2007.
Dirk holds a Bachelor of Engineering in European Logistics Management from Niederrhein University of Applied Sciences in Germany and Fontys University of Applied Sciences in the Netherlands, as well as an MSc in International Logistics from University of Plymouth Business School in the United Kingdom.
control of renewable energy facilities in North America — covering anything from core supply chain functions, strategic sourcing, tactical sourcing, material planning and replenishment, and warehousing and logistics.
“My favourite thing about working in the renewable energy industry is that you can feel good about its purpose,” he shares. “We’re first-hand driving the energy transition and helping to fight climate change. It’s a relatively new industry, it’s dynamic, it’s exciting.
“There’s tremendous growth in renewables and many companies haven’t spent a lot of time in setting up formal processes and controls around the
supply chain because it’s always been about growing, building, and developing new projects.
“As a supply chain professional, that gives you the opportunity to apply basic principles for immediate impact.”
In the business of making said immediate impact, Ruitenberg is motivated to find ways to solve problems and overcome obstacles in a bid to make EDF Renewables and its partners more efficient, enabling it to deploy and operate more renewable energy facilities.
“I’m actively working to build a better future for my children,” he says, “and that’s a thought that motivates me every day.”
Noting that the energy industry is armed with professionals of all backgrounds which gives it the best opportunity to meet its sustainability goals, Ruitenberg can work to meet EDF Renewables’ core mission — to provide future generations with a means to power their lives in the most economic, environmental, and socially responsible way possible.
“Since I joined the business, the operation and maintenance service business has pretty much doubled in size,” he explains. “We’ve almost doubled in revenue and we’ve doubled in megawatts operated.”
EDF Renewables is now operating more than 50 renewable energy projects under full scope in North America.
Ruitenberg continues: “To enable this growth, it was necessary to transform the way the supply chain works in procurement. We transitioned from a very transactional approach to a more strategic orientation. So we reorganised the team and brought in talent with strategic sourcing experience, and we started analysing spend as a foundation to establish mid and longterm agreements.”
To do this, Ruitenberg and his team has put a wealth of focus on establishing framework agreements and building partnerships with its supply base, implementing metrics and supply chain
tools to better control processes. This allows for procurement activity to become a centralised function.
As well as this, Ruitenberg’s team also initiated a project to centralise inventory ownership in its operating company and established a central warehouse. Working with SAP to develop a solution to support automated replenishment of inventory items based on aggregation of spent data and consumption data, EDF Renewables gained the capacity for growth to be supported without excessively scaling up the department in lieu.
“It was necessary to create a more efficient process and then drastically reduce the number of transactional POs for our fulfilment buyers,” he explains. “Shifting from
“Every temperature sensor, accelerometer and wind vane in these turbines is generating data”
DIRK RUITENBERG SENIOR DIRECTOR OF SUPPLY CHAIN, EDF RENEWABLES
one-off replenishment of individual project sites to consolidating ordering into our central warehouse went a long way in that process.”
Ruitenberg is firm in his belief that he and the rest of EDF Renewables are carrying out strategies that are far from rocket science or reinventing the wheel, but applying basic supply chain concepts to an industry which historically hasn’t been operating in this way.
One way in which they are streamlining operations is by having centralised inventory, which he says boosts project profitability and the success of energy project operations across EDF Renewables.
Where EDF Renewables previously had siloed warehouses for previous projects — resulting in inventory that is not being used
“We’re first-hand driving the energy transition and helping to fight climate change”DIRK RUITENBERG
SENIOR DIRECTOR OF SUPPLY CHAIN, EDF RENEWABLES
and, consequently, wasted — the company has since moved to keeping its inventory in a central location so supplies can be distributed when needed. This also allows for back-up in times of downtime or supply issues; extra inventory, rather than sitting idly, can be distributed where best needed and more efficiently. Keeping all elements of this process in-house, improves overall supplier visibility and mitigates supply- and demand-related risks.
“A traditional approach to spare parts inventory management — where each project independently owns and maintains siloed inventories on site — is an approach that logically, if you are starting to have a large portfolio of projects, tends to be economically inefficient.
“Wind turbines often have tens of thousands of parts, and not all parts fail in the same frequency. But you need to have a lot of them on hand in order to avoid long downtimes when they happen to fail. If you are able to spread out slow moving inventory across the entire fleet, you’re much more efficient. That’s the basis for the project.”
As a result of this, Ruitenberg has seen a great improvement when it comes to control of processes, creating efficiencies and boosting project profitability as a result. EDF Renewables aren’t the only large renewable energy project owners taking this
approach, but what sets them apart from the rest is that EDF Renewables extends the same benefits to third party owned projects.
Partners ensure EDF Renewables delivers secure and responsible energy generation EDF Renewables is also implementing reverse logistics to its operations, something Ruitenberg admits is ‘finicky’ when it comes to use in the renewable energy industry. As parts fail or become ineffective from continued use, said parts are sent back to the supplier to be replaced.
“Historically, this process has been heavily relying on inputs and decisions of the corresponding operating sites with manual tracking and often decentralised sourcing of repair solutions,” Ruitenberg admits. “It’s a remote setup rather than being on a factory floor. But there are wind farms and solar projects across North America in remote areas, and without having systemic tracking solutions in SAP for failed components, you are relying on the technicians to actually let you know that they have a bunch of failed components sitting on the shop floor that need to be dealt with.”
To overcome this nuisance, EDF Renewables has partnered with business and technology consulting company Capgemini, which implements a robust and efficient reverse logistics process within SAP supporting EDF Renewables’ business needs around tracking failed components. A longstanding partner to EDF, Capgemini has a deep understanding of the energy industry — specifically renewables — and shares common values.
“Capgemini was selected in 2023 as implementation partner to design and build the reverse logistics processes. They have mapped our requirements and now they’re building the solution in SAP,” he shares.
It’s vital for companies that partner with EDF Renewables to not only ensure a safe and secure, responsible generation and deliver better value, but to also have a comprehensive understanding that EDF Renewables’ responsibilities extend beyond its own direct activities.
“We expect our suppliers to operate in a manner that demonstrates the same commitment to sustainable, responsible and ethical business practises that we require for our own employees,” Ruitenberg says.
One of those said partners is logistics operator Vicarli, which runs its central warehouse operations, taking on St. Louis in 2021 followed by a second location in Las Vegas in 2023.
Renewable energies fuel sustainable supply chains. We have the expertise to accelerate your transformation.
Increase energy generation, reduce expenses, elevate efficiency, and increase ROI.
“Vicarli provides value added services, including the enrichment of material master data”DIRK RUITENBERG SENIOR DIRECTOR OF SUPPLY CHAIN, EDF RENEWABLES
Ruitenberg elaborates: “Vicarli has proven to be a great business partner to EDF Renewables. They not only operate our warehouses, but constantly strive to find ways to provide value added services, including the enrichment of material master data. They capture physical attributes, like weights and dimensions, read off manufacturer and model names, and
create harmonised tariff schedule codes that allow us then to export to other countries. All of that’s made available to our fulfilment buyers and allows them to facilitate better sourcing decisions.”
This eliminates issues that arise from buying products from manufacturers, overriding often vague descriptions, and allows EDF Renewables to gather as much information as possible to streamline part sourcing.
AI advances having major impact in EDF Renewables’ supply chain Technology is another way EDF is streamlining its operations and ensuring it is acting as consciously and sustainably as possible.
As well as rolling out its own internal AI tools, EDF is working on several key digital initiatives across the company, with one large global initiative being its renewable
“We expect our suppliers to operate in a manner that demonstrates the same commitment to sustainable, responsible and ethical business practises that we require for our own employees”DIRK RUITENBERG SENIOR DIRECTOR OF SUPPLY CHAIN, EDF RENEWABLES
data lake. It aggregates all operating and performance data from EDF’s global portfolio of resources, totalling more than 21GWs across 22 countries.
“Every temperature sensor, accelerometer and wind vane in these turbines is generating data,” Ruitenberg shares. “There’s a lot of data across these assets that needs to be dealt with in a big data approach. It’s being analysed using AI data science techniques and then a bunch of expertise in different business lines.”
The approach allows EDF Renewables’ field technicians to maintain the company’s assets using a handheld device. The tool, which also gathers best practices on maintenance actions and work constructions based on common fault codes and operating parameters, along with the data lake, allows for further optimisation.
“So in the supply chain, we’re expecting to get more accurate forecasts of failure rates and material requirements as a result of that,” Ruitenberg hopes. “And as generative AI advances, it’ll likely enable the industry to further automate tasks, predict and prevent failures, and ensure more stimulus operation.”
Keeping with Ruitenberg’s future-centric outlook, he and the wider team at EDF Renewables will continue consolidating its material fulfilment and planning processes while focusing on optimising its fleet by inventory.
“Our current inventory levels are a bit high, partially driven by the acquisition of slow-moving inventory and supply chain disruption during the pandemic,” he explains.
“We’re also planning to improve the user experience for our field technicians when it comes to site inventory management by rolling out a handheld device version of Vicarli’s warehouse management system.”
Another key area is last mile delivery. With renewable assets typically in remote locations — something further exasperated with the increasing development of offshore wind — EDF Renewables is focusing on getting the necessary parts into the hands of the technician via the likes of drone delivery.
“There’s a multitude of projects under way,” he concludes. “And a lot of this will certainly become a reality.”