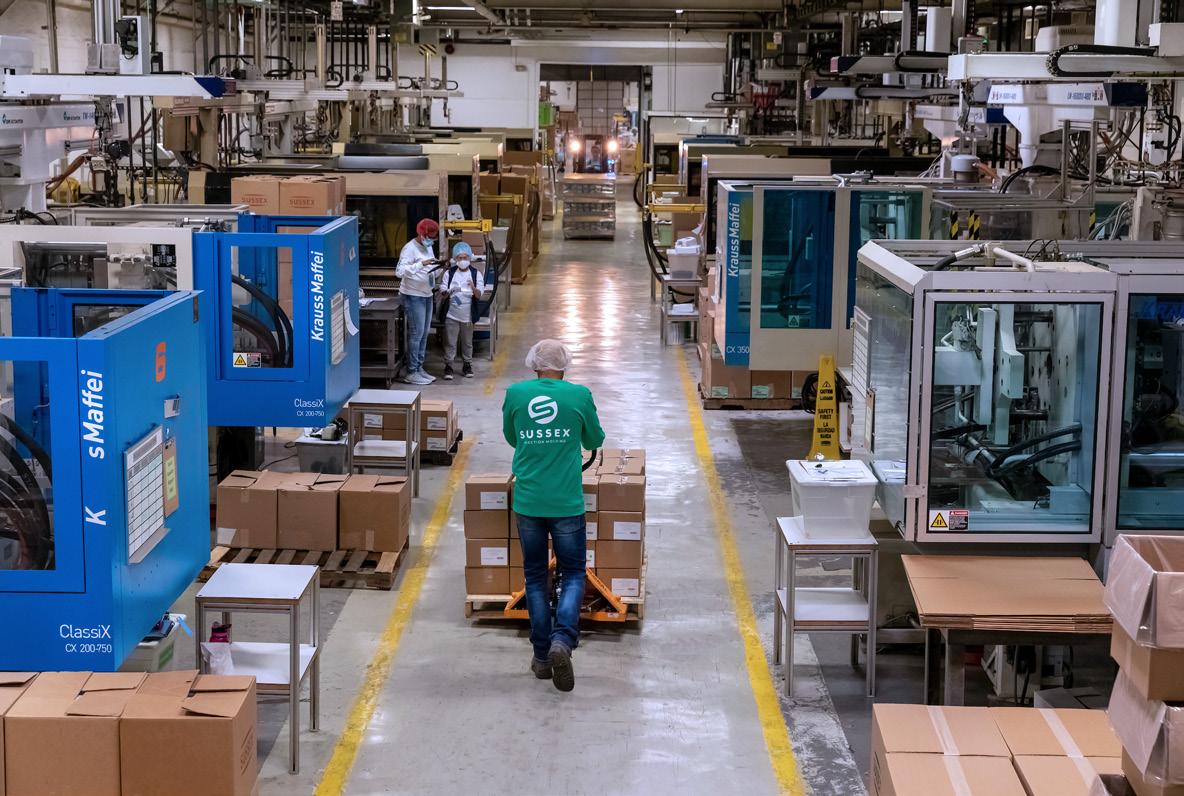
3 minute read
SHOP TALK
How can manufacturers navigate supply chain delays?
By Brandon Anderegg, staff writer
Sussex IM’s headquarters.
TOILET PAPER may have returned to grocery store shelves, but the COVID-19 pandemic and weatherrelated supply chain disruptions continue to challenge local manufacturing companies.
The February cold snap that devastated Texas, where much of U.S. resin production is located, forced commodity resin makers to close. Sussex IM was one of many manufacturers across the country to experience the ripple effect.
The Sussex-based custom injection molder relies heavily on resin to make products for industries including beauty, health care and consumer products.
“We were facing downed situations in our plant because we were not getting any of the materials we were already committed,” said Megan Tzanoukakis, vice president of supply chain for Sussex IM.
Manufacturers are approaching supply chain delays in a variety of ways with communication playing a central role in their strategy, said Molly Barndt, Waukesha County Technical College supply chain instructor.
Companies are now dual sourcing raw materials and components to mitigate supply chain delays, and in some cases connecting with suppliers in two different regions. Especially for critical components, it’s important that companies understand their relationships with suppliers, Barndt said.
Are these relationships transactional or is it a strategic partnership?
The latter means information forecasts and pipeline visibility are available on both sides. A strategic relationship could also mean that a supplier or manufacturer may be willing to house buffer or safety stock at their facility, which can build resilience in a supply chain.
Strong relationships with suppliers allowed Sussex IM to weather the Texas winter storm, Tzanoukakis said, adding that because of strategic relationships, suppliers had available inventory for the company.
“On the other side, we have a lot of visibility into our key customers’ forecast, and we were able to buy ahead and have buffer stock, continue producing and then hold inventory here,” Tzanoukakis said.
A culture of information transparency also helps companies manage customer expectations. The toilet paper hysteria at the onset of the pandemic showcased the bullwhip effect – swings in inventory from panic purchasing and sudden demand have an amplified impact moving up the supply chain.
Barndt says customers need to order earlier and update their ERP systems to reflect longer lead times experienced by manufacturers and suppliers so that delays do not affect their supply chains.
“The better the communication flow, the better that bullwhip starts to relax a bit,” Barndt said.
Manufacturers could also adjust their quotations to “expires in 30 days” instead of the typical 60 or more days. Another option may be adding a surcharge for freight, which wouldn’t permanently raise costs and can be removed when supply increases, Barndt added.
Port delays have also proven to be a challenge, making it difficult to plan for production and labor without a timeline of when materials will arrive. Translating inbound delays into production plan delays to accurately project eventual shipment dates to customers is key.
To mitigate the impact of port delays, manufacturers should consider other transportation modes or rely on logistics visibility solutions or transportation management systems, Barndt said.
Building a steady stream of inventory by planning material orders to compensate for additional delays is another strategy that companies are implementing, Barndt added.
Supply chains saw disruption prior to the pandemic with trade and tariff disputes between the U.S. and China. Pandemic-induced port delays have also increased lead times for raw materials, creating a shortage of finished goods and resulting in missed deliveries and price increases.
A record 22 weather or climate disasters causing at least $1 billion in damages affected the United States in 2020 alone, according to the National Oceanic and Atmospheric Administration.
These variables don’t even account for the unexpected mishap of a California-bound cargo ship hitting rough weather in late January and causing 750 containers to be lost at sea.
The global supply chain is no stranger to disruption, but these interferences – whether they be pandemic or climate-related – appear to be on the rise as the world becomes more volatile. n
SOLUTIONS FOR NAVIGATING SUPPLY CHAIN DELAYS
• Evaluate safety stock at distributors and intermediaries to ensure your inventory is securely held. • Identify strategic versus transactional relationships and ensure critical parts are sourced from suppliers where a strategic partnership is present. • Invest in logistics visibility solutions such as transportation management systems. • Ask customers to provide forecasts and information about their demand cycles so manufacturers can plan accordingly. • Plan material orders to compensate for the additional delays to ensure a steady stream of inventory.