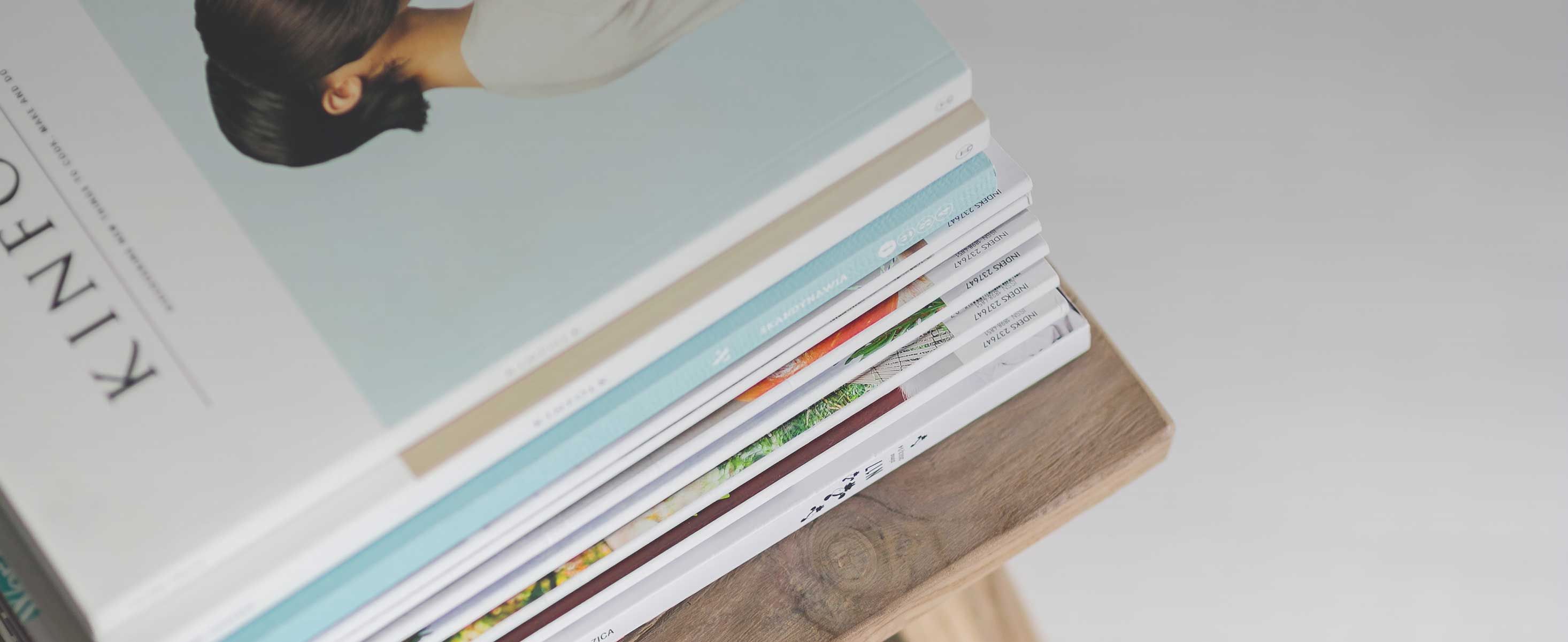
4 minute read
A new century, a new approach
Making objects layer by layer is more revolutionary than you might think
From the student’s study to the professional designer’s office, from the dental laboratory to the jewelry retailer, from the aerospace factory to the hospital basement, 3D printers have become invaluable business tools. Applications and reasons are as diverse as the users and industries. But what is it about 3D printing that enables these new innovations and opportunities?
Advertisement
What links all these applications and users is one underlying ability: to transition 3D information digitally and seamlessly from the virtual world to the real world with nothing but a computer and a 3D printer to go from bytes to bits.
This may seem innocuous at first; many modern production technologies are driven by digital data and controlled by computers. But let’s consider this in the context of how we have historically manufactured products. The modern manufacturing world is a plethora of different technologies, processes and tools, but they can be largely categorized into three families.
For as long as humans have wielded tools, we have had three methods at our disposal to manipulate our environment and “make things.” We have either removed material, joined materials, or reformed them to achieve a desired shape. Whilst the discrete methods of how we do this are many, from backward impact extrusion to reaction injection molding, they all fit into one of these three categories.
Making objects additively, layer by layer, is an entirely new manufacturing methodology distinct from subtractive, fabricative, or formative processes. This presents a number of unique opportunities for how parts can be produced, and in turn, how supply chains operate, businesses sell, and manufacturers invest.
Because 3D printing uses a layer-by-layer, particle-by-particle approach to manufacturing, it is able to make complicated shapes that are unimaginable using traditional process such as molding, machining, or casting. Unlike these traditional processes, complexity with 3D printing is also dislocated from cost, making it a highly efficient way of making intricate shapes.
Couple this capability with the fact that 3D printing is entirely digital, and this dissolves the traditional relationship between part cost and production volume. We now have a process that is highly suited to low volume production applications where traditional tooling investment can be difficult to justify.
A new manufacturing methodology for the 21st century
Subtractive
Material is successively removed or subtracted from a solid block until the desired shape is achieved. Common subtractive methods include drilling, milling, and turning and are capable of producing parts with superior tolerances and excellent surface finish quality, but can be limited in the geometries they can produce.
Est 2.5 million BC / Hominids Fabricative
Elements or physical materials are combined and joined to create an object. This approach includes mechanical and chemical joining methods such as weaving, riveting, and glueing and is often used to create larger, more materially or mechanically complex parts such as performance composites or complex structures.
Est 6,000 BC / Western Asians Formative
A combination of mechanical forces and heat are applied to material to form it into the desired shape. Formative methods include casting and molding. These methods are suitable for high-volume production of individual parts or manipulation of high-performance materials, but can be costly when used for low volumes of parts.
Est 3,000 BC / Egyptians Additive
Material is manipulated and deposited in a controlled way layer by layer to form an object. Unlike other production methodologies, the layer-wise approach allows for the creation of new geometries, mechanical properties, and part functionality that is only achievable via an additive process.
Est 1984 / Californians
Many of the manufacturing paradigms that govern our modern industrial economy stem from how we manipulate material to produce objects, parts, and products. Even as more advanced machining, assembly, and molding processes develop, these “rules” still remain. An additive approach comes with its own set of rules, many of which go counter to convention; complexity is free, economies of scale don’t exist, parts can be produced without the need for factories.
Claims that 3D printing was to usher in a 4th industrial revolution were over-hyped. But it does offer a 4th mode of manufacturing. The applications and benefits of this new, 4th approach have been A/B tested for over two decades, with many companies already integrating additive as a production solution to solve problems or capture opportunities that can’t be addressed by conventional methods. As we move into the next decade, this 4th way of making will be seen less as a technological novelty and more as another manufacturing solution, with its own set of benefits and limitations, applications, and technology variations. It is a new approach for a new century, and those organizations that build a base of knowledge as to what, how, where, and when to use it will be the leaders that set the pace of competition in the years to come.