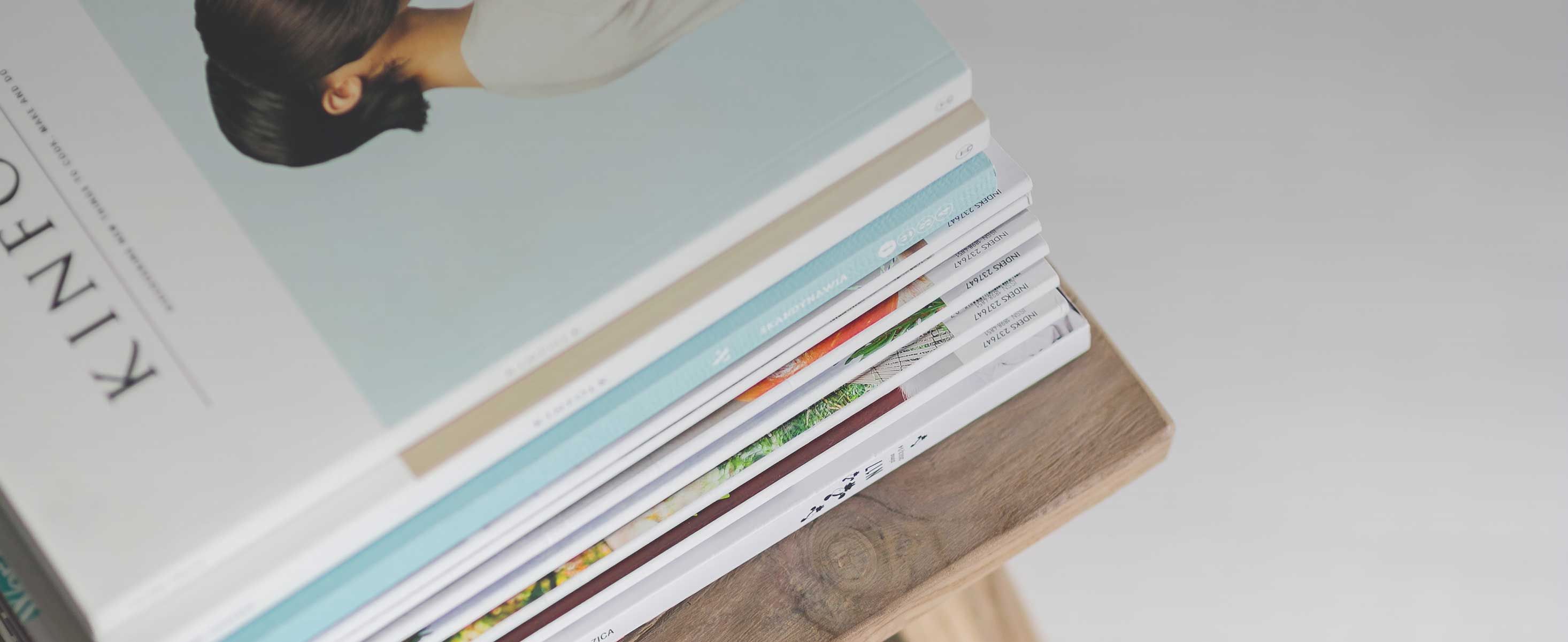
3 minute read
Machinery energy consumption
BOBST has always been working on reducing its packaging machines’ energy consumption and extending their lifetime. As a manufacturer, Bobst Group is committed to reducing greenhouse gas emissions in its value chain (scope 3) while continually optimizing its customers’ equipment to meet their needs for profitability and sustainability. However, the recent energy supply and cost issues that converters have faced require rapid solutions to support the packaging industry to control and save energy more effectively than ever before. As a result, BOBST is accelerating the development of appropriate technologies to deploy them as quickly as possible in the marketplace.
Given the size, functionality, and technical performance of packaging machines producing at high speed and equipment designed to operate 24 hours a day, seven days a week, the environmental load of machinery energy consumption remains a significant challenge in the packaging industry. Therefore, in addition to ink, waste, and substrate reduction, BOBST is focusing on keeping the energy needs of its packaging solutions to a minimum, to lower its customers’ production costs and decrease their carbon footprint.
Optimizing energy requirements
BOBST’s 2021 Sustainable Report outlined that a packaging machine consumes the most energy during its use phase at the converter’s premises (around 90% of its life-cycle carbon impact alone). To improve the energy requirements on both new equipment and the base of installed machines, BOBST not only launched new features and training in 2022 but allocated two people to this subject, acknowledging the importance of measuring and reducing the climate impact of its packaging equipment.
The carbon and energy-saving calculator commissioned by the Business Unit Services & Performance (BUSP) has made it possible to compare obsolete direct current motors (DC) with new generation alternating current motors (AC). On average, the latter saves 13% electricity (equivalent to 18 MWh per year), as shown by the value BUSP has measured on retrofitted customer equipment. As a result, a yearly saving of 7 tons of CO2 emissions is equivalent to what a fossil fueled car emits during a 50 000 km trip. With the present energy crisis, this retrofitting has a payback in 4-7 years.
In die-cutting, the new BOBST Hybridblanker delivers a versatile tool frame that replaces several dedicated structures, saving raw material and weight during shipping.
> Operations reporting
>Equipment reporting
> Packaging use & end-of-life reporting
> TCFD
> GRI index
EXPERTFOLD 165 e-commerce version, a folder-gluer line, offers two features that proactively contribute towards sustainability in converting, while providing key operational benefits at the same time. The first is a split driving system, which has a key role to play in the reduction of waste and lower energy use by eliminating disruptive stop-start production runs. When the system detects an error in the process, such as incorrect glue application, the folder-gluer halts production of the defective boxes while continuing production of compliant boxes. In essence, the first half of the machine can be stopped to correct the issue, while the second half continues to run. The key advantage here lies not just in continued productivity, but in fluid correction of issues without stopping the entire production line. The second key sustainability edge in the EXPERTFOLD 165 e-commerce version is an update to the POLYVACUUM module. The technology has recently been updated to optimize energy resources; a redesigned lower vacuum conveyor system has resulted in better air flow management, alongside a reduction in air consumption of up to 20%.
In 2022, BOBST set up the first climate impact and awareness training within the Group (90 people from managerial positions including BOBST Board of directors and top management executives) and developed an online eco-design course for R&D engineers, managers, and supply chain actors. BOBST also approved a proper sustainability machine evaluation sheet and implemented it on 13 essential BOBST products by the end of that year. It has provided an overview of their environmental impacts (with a strong focus on energy consumption) and insights into needed improvements. In the past, electricity was the only energy to be tackled. With its new indicators, BOBST can also now account for compressed air and the occasional gas consumption.
Goals, targets, and indicators for 2023
BOBST will announce the SBTi (Science-Based Targets Initiative) reduction targets in its sustainabiity report 2023, including targets concerning the energy consumption of BOBST machines.
Designing more sustainable products – All product lines’ R&D and managing staff are targeted by workshops on energy savings, being developed at a wide scale in 2023.
Eco-design course – Forty-six people completed this training in 2022. The 2023 target is to enroll at least 200 participants among R&D engineers, Supply Chain & Management.
Sustainability machine evaluation sheet – The 2023 target is to have the whole catalog of BOBST machines evaluated using the same method. On this basis, BOBST will head to its next goal: the online monitoring of the machine’s impact during the use phase at the customer’s plant through BOBST Connect.
Sustainability report 2022
> Strategy
> Operations reporting
>Equipment reporting
> Packaging use & end-of-life reporting
> TCFD
> GRI index