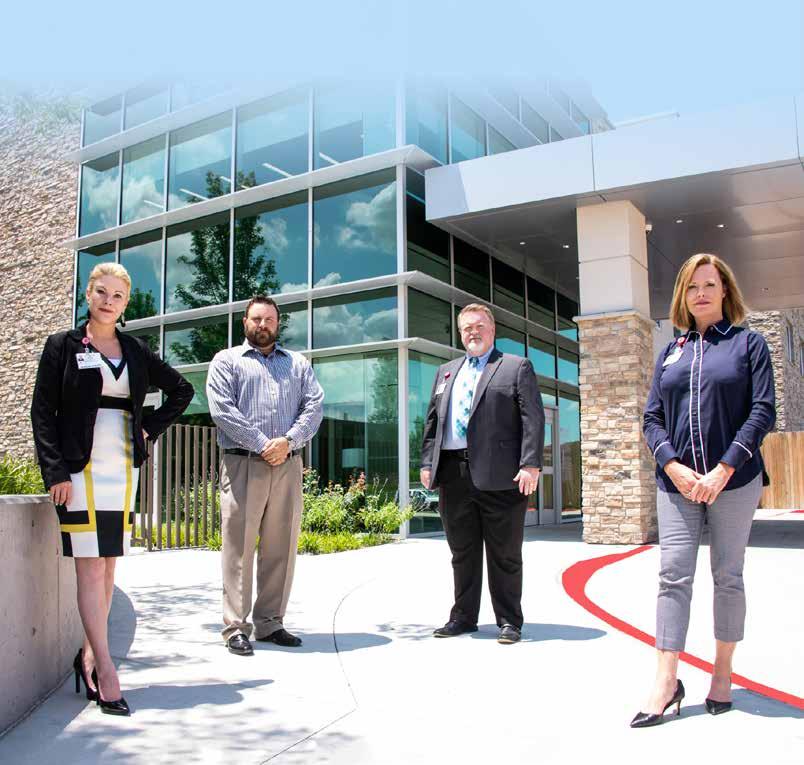
8 minute read
Texas strong
from CCR Issue 8
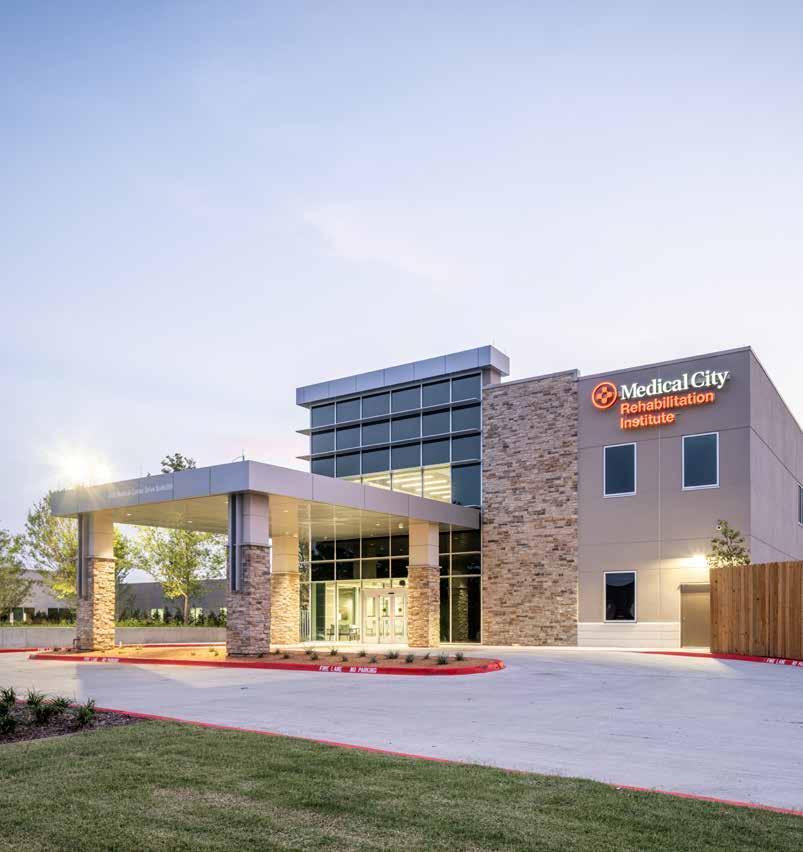
Texas strong
McKinney, Texas’ Medical City McKinney has been committed to the care and improvement of human life for more than 100 years. The 257-bed acute care hospital offers comprehensive services, including a Level III Trauma Center, cardiovascular, neurological, general surgery, orthopedics, women’s services, a neonatal intensive care unit, and is a primary stroke and stroke rehabilitation center.
Medical City McKinney also has been the leading inpatient behavioral health provider in North Texas’ Collin County for more than a decade. In recent years, this region of Texas has struggled with providing fewer licensed behavioral health beds per capita than smaller counties in the state, due to numerous behavioral facility closures. This lack of local behavioral health services creates challenges for patients and staff in area hospital emergency departments, which are not typically designed, staffed or best suited to treat behavioral concerns. So, the hospital’s leadership announced their plan to build the new Medical City McKinney Behavioral Health & Inpatient Rehabilitation Institute to better address the community’s needs. To check in on their progress, we sat down with Josh Meadows, Healthcare VP at JE Dunn Construction, who provided an inside look at the unique nuances of the Medical City McKinney Behavioral Health & Inpatient Rehabilitation project. Tell us a little about your history with Medical City Healthcare.
With 16 hospitals in North Texas, Medical City Healthcare is one of the region’s largest, most comprehensive health care providers in the Dallas-Fort Worth area. JE Dunn has been fortunate to partner with several of its hospitals on numerous projects over the last five years. We also are currently managing Medical City McKinney’s latest project, which includes an emergency department expansion and renovation, a new three-story patient tower, plus an expansion to the existing central energy plant to accommodate the hospital’s continued growth.
Give us an overview of the Medical City McKinney Behavioral Health & Inpatient Rehabilitation Institute facility.
The facility is a two-story, 80,000 square foot pavilion with multiple interior courtyards. The behavioral health component, with
80 patient rooms, serves adults, including geriatric patients, with acute behavioral health needs. The inpatient rehabilitation component, with 20 patient rooms, provides treatment for strokes, amputations, brain injuries, cardiac rehabilitation, trauma, neurological and spinal cord injuries, orthopedics, multiple sclerosis and Parkinson’s. Contemporary evidence-based design for clinical spaces recommends more exposure to natural light and other natural elements through features like greenery, windows with views and access to outdoor spaces, to reduce cortisol levels and stress for patients and their caregivers. Therefore, open floor plans in common areas, natural lighting and an extensive outdoor garden enhance the facility’s healing environment. The pavilion also features views of a 300foot retention pond that utilizes the newly constructed storm drain system to capture the campus’s rainwater. The 80 rooms dedicated to behavioral health patients required a particular focus on patient safety, resulting in numerous safety and ligature-resistant features, and many other behavioral health environment best practices.
What were some of the project goals?
Because this project used a design-assist delivery method, fostering high levels of involvement and collaboration between all partners, including the design partner and key trade partners, early in the project was key. Delivering a leading-edge, high-quality specialty facility to serve the unmet needs of the community meant speed to market and schedule certainty were also critical to the project’s success. Given the significant behavioral health component of the facility, operating with a “safety first” mindset was essential throughout the project. Beyond those specific goals, our teams recognize that all healthcare job sites are hospitals, first and foremost. Therefore, we are always focused on limiting disruption to the hospital’s operations and stand ready to assist the hospital however we can, regardless of whether it falls outside the official scope of the project and our contractual obligations. This is part of how we fulfill our corporate vision to become an indispensable business partner for our clients.
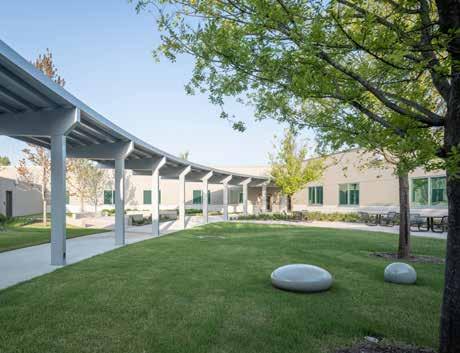
What are some of the unique nuances of building a behavioral health facility?
National demand for behavioral facilities is so strong, and best practices for clinical approaches and facility designs are rapidly evolving. So, one of the greatest risks on projects with significant behavioral health components like this is the schedule. Lead times are longer for many specialized, behavioral health safety products—such as shatter-resistant light fixtures and ligature-resistant doors, bathroom fixtures, doorknobs and diffusers—which could have easily threatened the project’s schedule. These schedule risks were further exacerbated by the early months of the pandemic and some key stakeholders’ unfamiliarity with behavioral facility best practices and requirements. For example, toward the end of the project, an authority having jurisdiction determined the owner’s standard for anti-ligature doors was no longer acceptable. At the time, our team could not reach the New York-based manufacturer due to COVID-19 shutdowns. We remained committed to doing whatever it took to resolve the issue, and eventually found a solution, ordering replacement doors from the manufacturer’s parent company in Ireland, without jeopardizing the overall project schedule.
How were the risks of the novelty accompanying behavioral health projects mitigated?
Because behavioral facility project teams are often challenged with charting new territory and at least a few firsts, our team proactively allowed more time for critical decision-making, reviews, approvals and communications. This involved allocating additional time in the schedule for ensuring shared understanding about key stakeholders’ priorities, making decisions, ordering specialty products and conducting additional inspections.
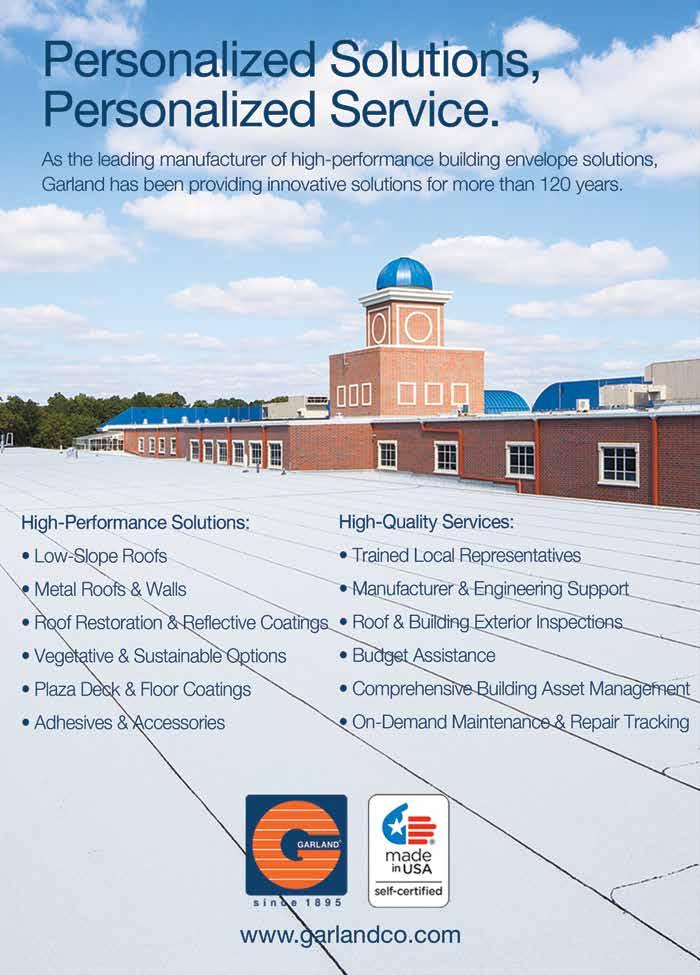
We also gave extra attention to client coordination early in the process and ample time to educate everyone about the unique aspects of the facility to prevent issues and delays. Extra time was allowed to coordinate some of the facility’s smallest details, like caulk and screws, which have special implications for behavioral patient safety. For example, snake eye screws used to be standard for these projects, but now we use pin torque screws. Screws are used throughout the facility, including under sinks for plumbing and on furniture. So, identifying the correct screw and ensuring all trade partners and manufacturers were aware of the requirement early in the project was a critical step in maintaining schedule certainty. What special efforts were made to enhance safety for the facility’s future patients and staff?
Newcomers to these types of projects are often challenged by the diversity of risk tolerances and safety approaches from one facility to the next. This can be impacted by factors such as the patients’ acuity level and the facility’s staffing model. Therefore, one key to an effective “safety first” mentality is to try viewing and experiencing the environment through the eyes of rehabilitation patients with limited mobility, or behavioral patients who might try to harm themselves or others. Starting during design, we conducted mock patient walk-throughs with the facility’s staff to help the entire project team see and experience the facility more like a
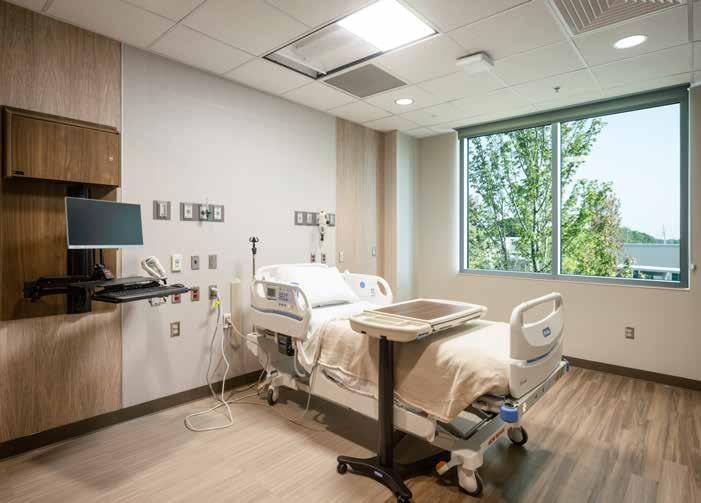
patient. The increased awareness, understanding and empathy helped us be more proactive about safety throughout design and construction. We also contracted with a third-party ligature consultant to review the drawings and walk the jobsite at various points throughout the project. This provided more peace of mind for everyone and helped prevent costly rework and delays.
With the additional time required to communicate and educate the team, and coordinate and deliver a safe facility, how did you accomplish the speed to market goal?
Through early design involvement, we were able to work with the design team and local planning and zoning to develop exterior wall panels for the building’s envelope that could be prefabricated off-site. The panel design included the glazing, which also underwent initial quality control testing to prevent water issues prior to installation. This reduced the schedule by 15% and helped us achieve dry-in of the facility two months sooner than possible with conventional construction. The prefabricated skin helped not only with the schedule, but also with quality. With assembly in a conditioned warehouse at ground level, workers were able to attain better quality, and inspections occurred more frequently to ensure a high-quality exterior. We also leveraged prefabrication for patient room headwalls to further accelerate the schedule and reduce construction congestion on the hospital’s campus.
What general construction challenges were encountered?
While most of our challenges were related to the specialized nature of the facility, we also faced other obstacles. For example, the project was originally designed as a slab-on-grade facility. However, due to the location, the geotechnical engineer recommended elevating the slab and creating a crawl space. The facility’s interior courtyard feature, and countless underground utilities that had to be relocated, made the late addition of a crawl space particularly challenging.
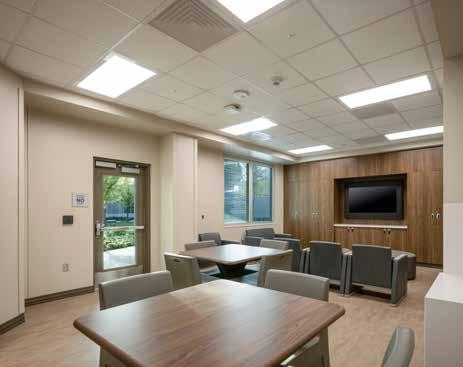
How did the team overcome that challenge?
We leveraged our familiarity with the campus to identify risks early and used field teams to precisely identify and survey all existing utilities. The team found that numerous utilities were not documented on the facility’s as-built documents, but rather were discovered in the field during our proactive evaluation of the site. Our in-house virtual design team then used the field data collected to create a 3D BIM (Building Information Modelling) model of all existing underground services. The model helped us coordinate those utilities, identify tie-ins, and aided our decision-making and pricing efforts related to rerouting the utilities to accommodate the crawl space. This was critical for mitigating risk and managing costs.
What advice can you offer to firms embarking on their first behavioral health project?
First, commit to comprehensive, proactive communication with all stakeholders from start to finish. This will prevent issues later in the project and will give everyone more peace of mind and buy-in with plans and decisions. Second, do not underestimate the value of involving partners with behavioral health experience. This will help the team make the right decisions and have the right resources necessary to develop the best plans and promptly address issues throughout the project. Finally, be prepared to do things a little differently. Building a facility with many behavioral health safety components may require you to subcontract and coordinate the project differently. But adjusting your approach to best serve the project will pay off in the end.