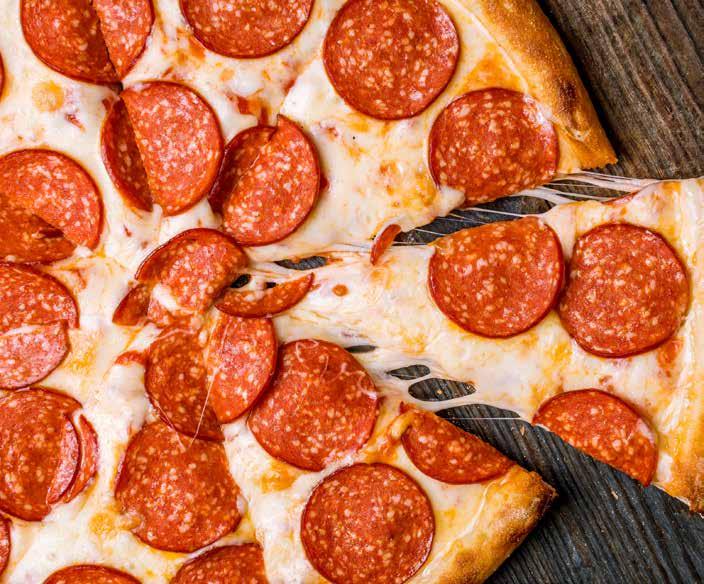
21 minute read
Industry News
from CCR Issue 9-2022
AroundtheIndustry
Restaurants
Capriotti’s
Sandwich chain Capriotti’s has been investing in tech innovation with a focus on automating more tasks at its namesake and Wing Zone restaurants. The focus on automation is designed to fuel the chains’ growth amid the ongoing labor shortage and serve customers who grew accustomed to digital ordering during the pandemic.
McDonald’s
McDonald’s will relocate its innovation center from a facility in Romeoville, Illinois to its downtown Chicago headquarters in a new hub called Speedee Labs. The labs will work on finding solutions to operational problems and improving the customer experience. About 100 employees are expected to relocate to the new hub when the first phase of the project opens in the second half of next year.
Jack in the Box’s Crave
Jack in the Box’s new Crave store format is designed to highlight the brand’s modernized design and color palette as well as to integrate new technology, including double drive-thrus and digital menu boards. Digital orders now generate upwards of 10% of the chain’s total sales and new units will be built to the Crave format starting next year.
Smokey Bones
Smokey Bones’ new drive-thru program features included digital menu boards and order confirmation screens and an express lane. Customers can order ahead or at the window and choose from a menu of dishes that are ready in five minutes or the full Smokey Bones menu, which takes longer to prepare. They also have the option of adding items from two virtual brands: The Burger Experience and The Wing Experience.
Paris Baguette
South Korea-based Paris Baguette, which is returning to growth mode in the US after a pause on franchise expansion earlier in the pandemic, plans to add 56 new locations this year. The chain has unveiled a new format that puts a greater focus on its baked goods, and several new franchise agreements are part of a plan to grow to more than 1,000 units over the next eight years.
Au Bon Pain
Ampex Brands has created a new Au Bon Pain store prototype that will debut next year in the Northeast and be the design for future corporate store remodels. The Cafe of the Future format is designed to be bright and open and focus on off-premises dining, with graband-go options displayed prominently and scan-and-pay kiosks that let customers avoid lines.
Eggs Up Grill
Eggs Up Grill plans to open around 70 new units by the end of 2022. The company has signed an agreement with Alliance Food Group to open 30 locations in the Dallas-Fort Worth market.
Hospitality
RIU Hotel
Construction is complete and occupancy has begun at the RIU Plaza Hotel, 48-story skyscraper at 145 West 47th Street in Times Square. Designed by Berg + Moss Architects and developed by Tribeach Holdings, the 519-foot-tall structure yields 353,000 square feet and 630 rooms.
Extended Stay America
Extended Stay America has unveiled its Extended Stay America Select Suites brand, which will feature apartment-like accommodations for long-term guests, including equipped kitchens, onsite laundry, WiFi and pet-friendly rooms. The extended-stay brand is planning to open nearly 100 properties across 30 states.
Wyndham Hotels & Resorts
Plano, Texas is the first city to host a new extended-stay brand hotel from Wyndham Hotels & Resorts. The hotel is slated to sit along the southeast corner of Highway 121 and Rasor Boulevard. The 124room Project ECHO prototype will take up just under two acres of land and offer unique economy rooms.
Marriott International
Marriott International has opened a new global headquarters in downtown Bethesda, Maryland at a 785,000-square-foot office tower owned by BXP and The Bernstein Cos. The building includes a day-care center, test kitchen, an Innovation and Design Lab and other amenities.
Hilton Hotels
A new lifestyle hotel, Tempo by Hilton Brand, is set to open next year in New York City. The 661-room hotel at TSX Broadway will feature programming from TSX Entertainment, an area for remote workers, wellness guest rooms and a dining terrace overlooking Times Square.
IHG Hotels & Resorts
IHG Hotels & Resorts has announced its new EVEN Hotels prototype, featuring an updated restaurant that offers healthy and indulgent choices along with a market, in-room fitness experiences and a spainspired shower, as well as a complimentary tea service each night.
AroundtheIndustry
Resorts World Hudson Valley Casino
Resorts World Hudson Valley Casino, housed in a mostly vacant shopping center in the Newburgh Mall in Newburgh, New York, is scheduled to open this fall with a sports bar and 1,200 electronic table games and video lottery terminals. The 90,000-square-foot facility is projected to generate more than 250 local jobs and stimulate redevelopment at the shopping center.
Retail
Five Below
Five Below will end 2022 with 160 new locations and plans to open 200 stores in 2023. The expansions are part of the discount retailer’s plans to grow to 3,500 locations and double sales and earnings by the end of 2026.
Best Buy
Best Buy recently opened a new digital-first, small box store concept in Monroe, North Carolina. The 5,000-square-foot store features a curated selection of “best-on-category products” in audio and home theater, cameras, cellphones, computing, small appliances, smart home tech and wearables.
Mejuri
Direct-to-consumer fine jewelry brand Mejuri plans to double its store count to 22 by the end of 2022 with a format that makes it easier and more fun for consumers to spend on jewelry for themselves.
Sephora
Sephora’s new Store of the Future format will make its Asia debut in Singapore with a focus on experiences and services. The space will feature interactive areas for experimenting with products and offer hair and skin services, including an app called Skincredible that will offer customers skin analysis and personalized advice on skin care.
Reformation
Fashion retailer Reformation will open two new London stores as part of a focus on growing its presence in the UK and Europe. The sustainability-minded brand operates 35 stores in the US, UK and Canada, and its first London location opened three years ago in Notting Hill.
FatFace
UK-based lifestyle retailer FatFace will grow its North American presence next year when it opens the first of six planned stores in Canada. FatFace plans to add eight North American stores annually.
Tractor Supply
Tractor Supply is changing the name of its Petsense retail stores to Petsense by Tractor Supply and modernize the stores to make them more welcoming. Additionally, Petsense shoppers can join Tractor Supply’s Neighbor’s Club loyalty program to earn perks like free pet grooming services and gain access to digital features for ordering pet medications and getting veterinary advice.
Grocery
Meijer
Meijer unveiled its newest store concept, Meijer Grocery, which will offer a quick and convenient shopping experience in a small-footprint store format ranging from 75,000 to 90,000 square feet. The first two stores, opening in early 2023 in the Detroit area, will feature grocery staples, fresh produce, a full-service deli and a pharmacy.
Amazon Go
Amazon has opened its first Southern California Amazon Go convenience store in Whittier. The store includes “Just Walk Out” technology, a selection of locally sourced products, a madeto-order kitchen, on-tap cold brew coffee and kombucha teas, self-serve Pinkberry frozen yogurt and lockers to pick up products purchased online.
H-E-B
H-E-B is continuing its growth across North Texas after purchasing 20-plus acres in Prosper, about 30 miles north of Dallas in Collin County. H-E-B has two stores under construction in Allen and McKinney that will open next summer.
ALDI
Aldi is expanding its Southern California footprint with the opening of a new market in West Hills. The opening is part of the company’s plan to add 150 additional stores throughout the US.
Lidl
Discount grocery store chain Lidl US has signed a 25,000-squarefoot lease with William Macklowe Co. and Senlac Ridge Partners to open its first location in Brooklyn, New York.
Kroger
Kroger has teamed with Kitchen United Mix to open in-store ghost kitchens, starting with a location in a Los Angeles Ralph’s store that offers food from 10 participating restaurant concepts. Four Texas locations are slated to open in the near future.
Reserving your pie
Three hotels have signed up for Uno Pizzeria & Grill's new franchising opportunity, which allows hotels to convert existing space into a Uno unit. The company also is offering a franchise model that mimics the design of the original Uno Pizzeria restaurant in Chicago. While the program still is being rolled out, the brand already has transformed three hotel venues in Illinois, Indiana and Michigan. More partnerships are expected.
What they’re saying...
— Deena McKinley, chief experience officer for parent company New England Authentic Eats, on Papa Gino’s strategy of keeping up with customers via text technology “Eliminating diesel is our goal for today, but we’re also looking to the future and our ultimate goal of operating a carbon-free fleet.”
— Matt Harris, Sustainability Manager for energy and fleet technology for Wegmans, on the grocer’s testing out Nikola’s Tre battery-electric vehicles as a possible way to increase the long-term sustainability of its fleet.
— Radisson Hotel Group CEO Federico Gonzalez on the hoteliers commitment to reducing greenhouse gas emissions to 46% by 2030 and becoming net zero by 2050
Getting all Chippy
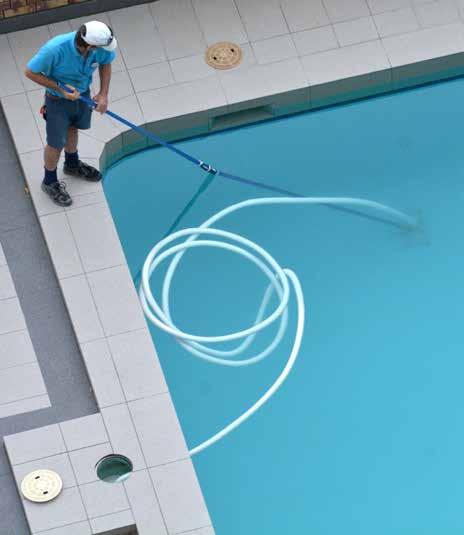
Chipotle Mexican Grill will start testing Chippy, a chip-making robot from Miso Robotics, at a single unit in California after testing the technology at its innovation hub. The chain also is experimenting with other technology innovations at select stores, including location-based tools from Flybuy to improve app efficiency and a machine learning system created by PreciTaste to reduce food waste.
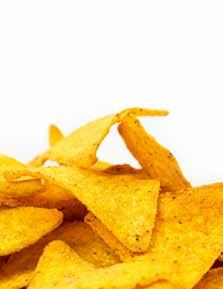
Filling the gaps
Apartnership between the American Hotel & Lodging Foundation (AHLAF) and the US Department of Labor's Job Corps will help try to fill 130,000 jobs with skilled Job Corps graduates from a number of programs, such as hospitality, facility maintenance and culinary arts. The first of its kind collaboration will provide Job Corps students access to hotel jobs and AHLAF’s apprenticeship program—an competency-based initiative that offers pathways to becoming a lodging manager or hotel cook and includes nationally recognized credential attainment. By tapping into each other’s networks and resources, developing work-based learning opportunities, and using connections to support job placement, the two organizations will join forces to grow top talent within the industry.
The numbers game
78 6 13 minutes seconds
The percent of consumers who said they are dining out at least once a month, with 44% saying they’re eating in restaurants once a week or more, according to TouchBistro “2022 Diner Trends Report.”
The average drive-thru service time so far in 2022, according to an annual study from Intouch Insight of more than 1,500 drive-thrus at 10 chains. The time still is about 45 seconds longer than the typical wait time in 2019. KFC took first place this year on total time, pushing Chick-fil-A to second; McDonald’s and Arby’s tied for first on order accuracy; and Chick-fil-A and Carl’s Jr. both ranked highest on overall satisfaction.
100
The amount, in millions, that True Food Kitchen has raised in its plan to add new restaurants and launch a smaller-format fastcasual brand.
The Great Indoors
RCA networking tour visit Denver REI
If you’re going to be in Denver, it’s always good to do Denver things. For example, visiting one of the hottest spots for Denver outdoor enthusiasts—which just happens to be a very cool place to hold a networking venue. Located in the restored 1901 Denver Tramway building, REI Denver was where the RCA networking crew held court. The historic building offers the latest in outdoor gear and clothing, in addition to a complete bike shop. The event was hosted by Scheiner Commercial Group Inc. and Shames Construction Company. Upcoming RCA network events are slated for New Orleans (November) and CenterBuild in Phoenix (November 30). For more information, contact info@retailcontractors.org.
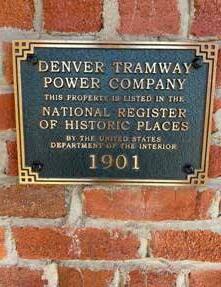

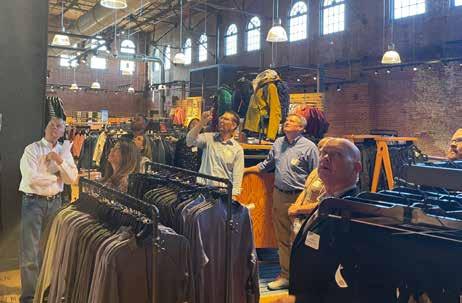
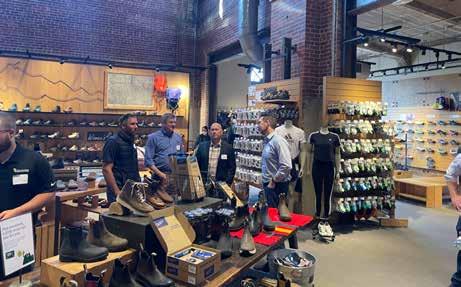

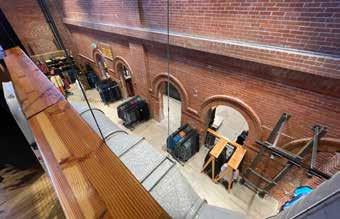

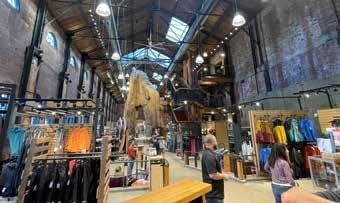

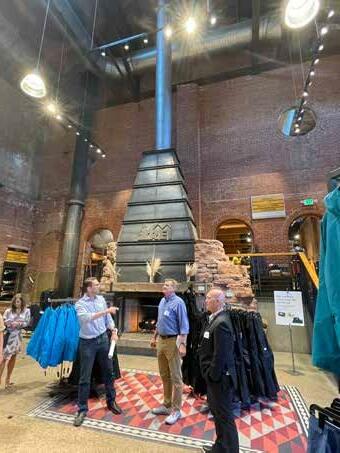
Automated construction
Improving construction affordability, productivity and sustainability via robotics
By Anna Chenuintai
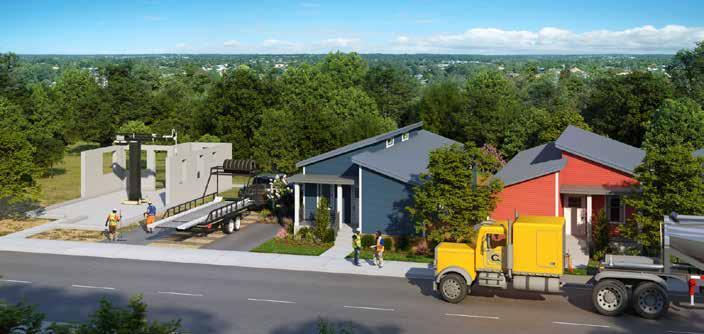
Despite record-high housing demand, the construction industry has faced a steady decline in productivity, with many citing a lack of skilled tradespeople among the leading causes. Recent findings report that over 80% of construction companies cannot find the workers they need, resulting in construction delays, higher labor prices and fewer deliveries—all of which impact profitability for builders. Facing a shortage of more than 650,000 workers, builders are investing heavily into new construction automation technology to cope with the shallow labor pool. Construction 3D printers are the latest technology bringing automation to the construction site. A wide range of advanced technologies and materials are being developed for the 3D-printed home industry. While the technology is young, 3D printing in construction is predicted to continue growing exponentially and be a $40 billion market by 2027. Economics of 3D printed homes
At their core, construction automation technologies seek to reduce the cost of labor and boost production volume—and with 40-50% of the total average construction cost spent on labor, there is significant room for improvement. This is particularly true for concrete masonry block construction, where on average more than 82% of total cost is spent on labor. Using a concrete 3D printer that creates walls that are identical to traditional concrete masonry block walls 3D can provide cost savings up to 33%. Yet, without the ability to scale the technology, it is nearly impossible for a construction company to deploy huge 3D printers to job sites. Some of the solutions on the market can be delivered to a job site with just two human operators, using only a small flatbed trailer. Once set up, printing can begin 30 minutes after arriving. And, with continuous printing the walls of a 2,000-square-foot home can be finished in a matter of days—nine times faster than a traditional masonry crew. Faster construction translates to increased transaction volume, and even more than per-unit cost savings. It is this ability to close more contracts that’s attracting builders to 3D printing technology. Because cost savings are often passed through to the homebuyer, doubling the annual contract volume can mean doubling annual profit for the builder. Once finished, concrete 3D printed homes are affordable to maintain and offer long-lasting durability. Compared to wood, printed concrete offers superior fire, moisture and pest resistance making it an ideal choice for regions prone to hurricanes, floods and natural disasters.
Robots and work flow optimization
Construction is an inherently risky business, and human error is a major contributor.
Workplace injuries, scheduling delays and avoidable work defects are common, and reducing the frequency of such occurrences can drive successful operations. Robotic 3D printers are never late to work, they follow the construction documents without deviating, and print times are calculated down to the second before the project ever breaks ground. This dependable performance, robotic precision, and consistent quality make 3D printers a powerful tool for reducing financial risk, optimizing workflow and accelerating project timelines.
3D printers excel at some of the most difficult, dirty and dangerous construction activities including concrete masonry, which enables skilled tradespeople to simultaneously install outlets, plumbing, insulation, reinforcement and other secondary construction activities—all while the printer still is building the walls of the home. This way, humans and robots can work together to accomplish more at the same time. Using concrete printers to copy existing concrete block construction streamlines integration of 3D technology into existing workflows—enabling tradespeople to perform finishing work without additional training. The same is true for architectural and engineering documentation, because these “printed block walls” adhere to the same building codes and design specifications as a traditional concrete masonry wall.
Simply put, concrete 3D printers enable builders to optimize construction workflow without disrupting operations because the homes being printed are virtually identical to concrete block construction, just built faster, stronger and more affordably.
Anna Cheniuntai
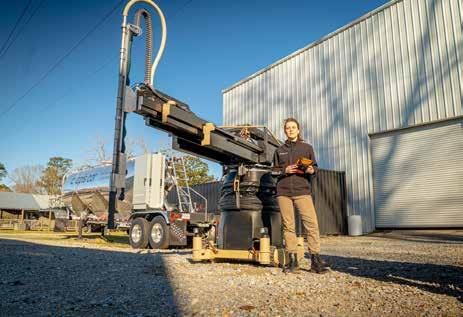
Better materials for better buildings
Despite the rising popularity of disposable consumer products, homeowners continue to view their primary residence as a longterm asset and the preferred investment to safeguard household wealth. For this reason, concrete is widely viewed as a superior alternative to woodframed construction because it is more affordable to maintain, retains value longer, and saves money in the long run. With that said, money isn’t the only green at stake—and many homebuyers are concerned about their home’s impact on the environment. Traditional construction methods generate a massive amount of waste which ends up in landfills and negatively impacts our environment. In fact, construction and demolition waste more than doubles the amount of all other municipal solid waste combined. Unlike stick-built homes, which are difficult to recycle, concrete and steel are some of the most widely recycled materials on earth. Moreover, 3D printers produce zero waste during construction, and most printers run on electricity, not gasoline or diesel. Currently, 3D print materials are composed mostly of sand and cement, but many companies have demonstrated successful testing of geopolymers and other carbon neutral materials which can improve building performance and the environment in which we live. 3D printing alone is not a remedy for everything wrong with how we build structures today. But as manufacturers struggle to keep pace with demand, 3D printing technology is a catalyst to rethinking and improving the overall construction process. CCR
Anna Cheniuntai is co-founder and CEO of Apis Cor, the pioneer of advanced, robotic 3D printing technology for the fabrication of full-scale buildings on Earth and on the Moon and Mars. Apis Cor holds the Guinness World Record for constructing the largest 3D printed building on Earth. The company also received top awards from NASA's 3D Printed Habitat Challenge for deep space exploration.
The road ahead
Easing organizational growth pains in construction through technology
With a boom of more than 1,400 new firms created in the past two years, the construction industry has left pandemic-focused uncertainties in the past. Rapid industry growth and the looming expiration of the COVID-19 (Temporary) Measures Act (“COTMA”) relief presents firms with a unique crossroads to meet demand. Expected project volumes will require CIOs to guide their companies on how to manage business tools alongside actually completing work on deadline. How can they best leverage technology to continue growing rapidly and sustainably? We sat down with John Meibers, VP/GM at Deltek, to get his thoughts on where things are heading. What factors led to the current boom in construction demand?
There are a number of areas that are seeing increased construction demand as a result of the pandemic—industrial construction and data center construction are two of these. During the pandemic there was a significant change in consumer behavior when it came to ecommerce; companies had to make changes in how they structured their supply chains which created growth in industrial demand. The pandemic also brought about a larger number of people working remotely and a higher demand for virtual meeting tools. These changes created a higher demand for more data centers to be built. In addition to these factors, residential construction demands continue to be on the rise and the Bipartisan Infrastructure Law (Infrastructure Investment and Jobs Act) will drive construction demand increases in late 2022 and 2023.
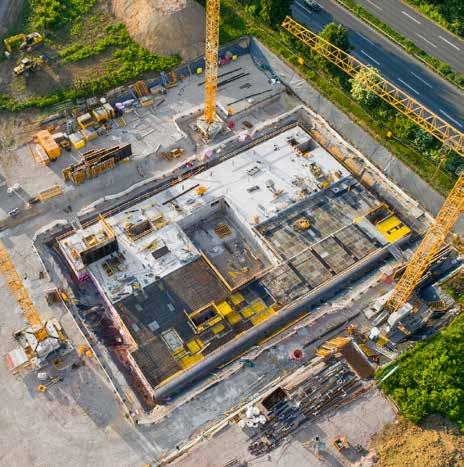
What are some successful strategies to implement for managing high project volumes?
The more projects you have in construction the more important it is to have the right tools to manage them. A contractor needs to be proactive and have these tools in place before their volume increases, because once it does, it will be very difficult to implement new systems and processes. The contractor should start by evaluating their job cost process. This includes everything from how their jobs are structured and reported on, to their Work in Progress (WIP) process and how the time is reported on a daily basis from the field. The WIP process is a key element of not only job costing, but also of financial reporting to a contractor. A contractor needs to look at how often they create their WIP report and how timely they are with getting updated cost projections on each project. As the volume of projects increases, it becomes even more critical that a contractor has a good cost projection method in place to allow them to proactively manage this increased number of projects. Other processes that should be evaluated include the purchasing and committed cost, equipment costs, customer billing, field-to-office communication, and payroll processes. These processes can help to determine if firms can easily handle a rapid increase in volume, and if not, they should consider potential changes to their ERP system to allow for future growth before it is too late.
What are some signs that signal a construction firm is growing too rapidly?
Some of the signs that a construction firm is growing too rapidly are obvious, while
others are not. One of the obvious signs is the inability to get real-time information on projects that need to be managed. For example, the accounting team may struggle with keeping up with the volume of work associated with rapid growth. Other critical things such as timely WIP reporting, accurate financial statements accounting for the over-under billing from the WIP, and lack of visibility into committed costs associated with each project may be issues to take into account. Another obvious sign could be working in certain geographic regions or doing types of work that haven’t been done before, which puts a strain on the payroll process. Some examples of this would be handling a prevailing wage job for the first time or working in a state or locality that has payroll tax requirements that they haven’t previously dealt with. A not-so-obvious sign may be that a company is using more spreadsheets and other manual methods to try and keep up with the extra volume of work. While this may work for a while, it is only a matter of time before these manual systems will fail and need to be replaced with a more robust system that can handle the workload.
For a contractor, tech implementation is key to sustainable growth for a number of reasons. Manual processes and other workarounds, while in the short run appear to solve the problems, are in fact, just hiding or masking them. This can lead to additional problems getting worse, potentially setting contractors up for future failure. If they take on a significant amount of additional work, their manual processes and workarounds may temporarily keep them afloat with their reporting and business needs. But at some point, these manual systems will fail and can lead to a contractor’s undoing—once these manual systems begin to fail it may be too late. The only way to prevent this is to put the right technology systems and tools in place to be built for sustainable growth. Tech implementation also allows for the creation of a team of top construction industry professionals who desire to work for contractors that understand the importance of tech implementation.
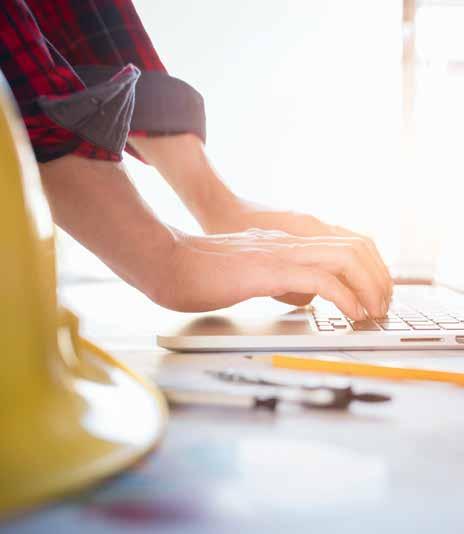
Some of the signs that a construction firm is growing too rapidly are obvious, while others are not. One of the obvious signs is the inability to get real-time information on projects that need to be managed.
How can firms best leverage technology to meet increased demand?
Technology can help a contractor meet their increased demand in a number of ways. With the right technology tools in place, a contractor can handle the increased demand with the current staff that they have today. These tools will assist the existing staff in increasing the amount of work they do when it comes to estimating and bidding jobs, purchasing material, managing submittals and RFIs, and managing day-to-day accounting and payroll needs. Technology also will help the contractor attract and retain the best talent in the construction industry, which is more important now as we continue to experience an increased labor shortage in construction. CCR