
8 minute read
Vizient: Focus on resiliency
While meeting the demands of an emergency, supply chain teams will also need to anticipate future needs
The Journal of Healthcare Contracting asked Vizient for insights into how the organization and its members are responding to the COVID-19 pandemic. Responding to JHC’s questions were Steve Downey, group senior vice president, supply chain operations, Vizient, Inc.; and Julie Cerese, group senior vice president, performance management and national networks, Vizient, Inc.
The Journal of Healthcare Contracting: Can you provide us with some insights of what is going on at hospitals and health systems as it relates to their supply chain teams? What conversations are they having right now?
Steve Downey Julie Cerese
Steve Downey: Most of the conversations are centered on supplies, especially critical ones – how many days on hand do they have for masks, gowns, ventilator parts, etc. Supply chain teams are trying to get ahead of what materials they need as their hospitals ramp up to provide care and how they’ll get those in these times of short supply. They are reviewing what practices clinicians are implementing to conserve supply and vetting suppliers that seemingly come out of the woodwork. They’re working to confirm deliveries, as some locations are right on the edge of stock outs and arrival times matter. We are also seeing
members and local sites setting up emergency operations and increasing bed capacity quickly. Those emergency sites need supplies, logistics and labor and their unique requirements put pressure on the supply chain.
JHC: How are you advising hospitals and health systems to navigate any supply disruptions? Downey: We are advising supply chain teams at member hospitals to conserve where they can and to check our Disaster Preparedness page regularly for the latest updates and information. Vizient continues to explore alternative supply resources and make that information available to members as soon as possible. In addition, we are encouraging members to keep forward-looking in order to project what stock they will have and what stock they will need so that suppliers can react to their best abilities.
JHC: What are a few things that every supply chain team should being doing today as a result of COVID-19? Downey: Clear communication with key stakeholders is a major factor in successfully working through a disaster. Every supply chain team should know what supplies are critical to the care of their hospital’s COVID patients and stay on top of the days-on-hand of those materials. Working with clinical teams, they should set up conservation practices on scarce supplies. When they have challenges, they can rely on Vizient contacts and resources such as webinars and newsletters, for key information. Most importantly, they should take every step possible to keep their clinical teams safe and healthy, as these are difficult times.
JHC: How should supply chain teams be planning long-term? Downey: Supply chain teams should make their plans with a focus on resiliency because it ensures supply continuity for the long term. Vizient will soon roll out a new platform to members that will create a “two-sided” marketplace for healthcare organizations and suppliers to map supply sources, risk points and create transparency to convert those areas to needed patient care areas. Hospitals have also worked with local, state and federal health authorities to develop regional approaches to care that can support patient surges. Some Vizient members have repurposed their ambulatory practices to serve as COVID-19 testing and treatment sites, helping to preserve hospital capacity for the sickest patients.
through the supplier and provider chain. The platform will help supply chain leaders at hospitals recognize areas where supply may be constrained, at risk because of single geographic origination or with a vendor having fill-rate challenges, so they can make the necessary adjustments for supply chain resiliency within their organization.
JHC: In what ways do you think COVID-19 is transforming how healthcare is provided? Julie Cerese: To prepare for COVID-19 patients, healthcare providers quickly cancelled elective surgeries and procedures to marshal resources for the coming surge. They quickly began to assess, train and redeploy staff to support critical areas such as emergency departments and ICUs.
Organizations quickly moved to assess the facilities they own, such as closed inpatient areas, operating rooms and conference rooms and develop plans
As healthcare providers have responded to this crisis, they have made major progress in improving access to healthcare for patients. When restrictions were lifted to make telehealth more available, many providers made it the first stop of the triage process, stopping patients from arriving and overwhelming the emergency department. This has helped providers and patients to become more familiar with telehealth as a future option for their health care needs.
In addition because of critical shortages of PPE, healthcare providers have quickly stood up new and innovative processes to ensure PPE is available for front-line caregivers. This has included developing new sanitation processes, or cohorting patients in a way that enables PPE to be used longer by staff. Vizient has held weekly webinars and has been collecting practices from its members in order to improve knowledge transfer in this area.
DUKAL Strong
This year – 2020 – started out as any other year. I spent a week in Shanghai, China, in mid-January to celebrate the Chinese New Year with DUKAL’s China team when we heard there was a virus in Wuhan, China, but thought nothing of it. However, Wuhan is an economic development city and billions of dollars have been invested there by foreign countries in manufacturing, led by the U.S. With visitors from all over the world traveling in and out of Wuhan daily, coupled with a virus that is a killer, it wasn’t long before we had the beginnings of a global mess on our hands.
Healthcare suppliers in the U.S. have handled pandemics before, but never one that hit so close to home and disrupted our supply chain while immobilizing our citizens. Wuhan and its surrounding cities were all quarantined before the end of the Chinese New Year holiday, and unable to resume their normal production. With a high concentration of PPE production coming out of Wuhan, and COVID-19 spreading in Europe and the U.S., the dramatically increased demand exceeded the production capacity of the region.
By early March, COVID-19 had come into the New York region and broadened our focus beyond just the need to maintain our supply chain. The continued well-being of our employees and their families became an urgent concern as well. The continuity of the business hinges on our essential employees and for them to be able to complete their jobs efficiently. As an essential supplier, and one very involved in PPE, we knew DUKAL had to remain fully functional. Our Disaster Recovery Plan was enhanced to address both the pandemic and our employees’ well-being. The DUKAL main office in Ronkonkoma, New York, went fully remote on Monday, March 16 with over 50 people able to work at home. Phones rang, emails flowed, and the office become fully functional from 50 locations! That day the reality of the severity of what was happening set in. As a person who believes in “New York Strong” I had not felt so empowered since the region started to recover from the tragedy of 9/11.
As we work through the realities of meeting our customers’ increased demand, coupled with China still trying to normalize production post-virus, the industry is faced with rapidly increasing prices, especially for the PPE products. DUKAL is now competing for scarce products
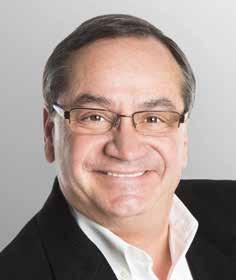
Gerard LoDuca president and founder

from buyers around the world and demand drives up pricing. Additionally, raw material shortages and hoarding also contributes to rapid and continued increases.
Look at the Raw Material Pricing Index from January to April 13 to get an idea of the magnitude of the jump:
• Polypropylene the raw material to make the SPP fabric: January RMB: 5,000 ton; April 13: 50,000 ton
• Spunbonded Polypropylene fabric (SPP): January RMB: 8,000 ton; April 13: 120,000 ton
• Labor in China has increased five times since the beginning of the year
• China factories now require a 30-40% deposit upon order and full payment on shipping
The current normal in the industry is that prices increase weekly and as of mid-April there is no timetable for stabilizing. It is very difficult to run a business during uncertain times and that is where the quality of a company’s management team is critical.
For the past 30 years, DUKAL has been able to drive redundant costs out of healthcare through smarter manufacturing practices. This past month, it has been disheartening to see 30 years of work be erased as these pandemic-related price increases wipe away a lifetime of work. However, in customary fashion we will move forward, continue to find innovative ways to bring healthcare products to market and put our customers first. Wherever that journey takes us, our team remains dedicated to being the best we can be and DUKAL STRONG!
We want to thank you, everyday warriors.
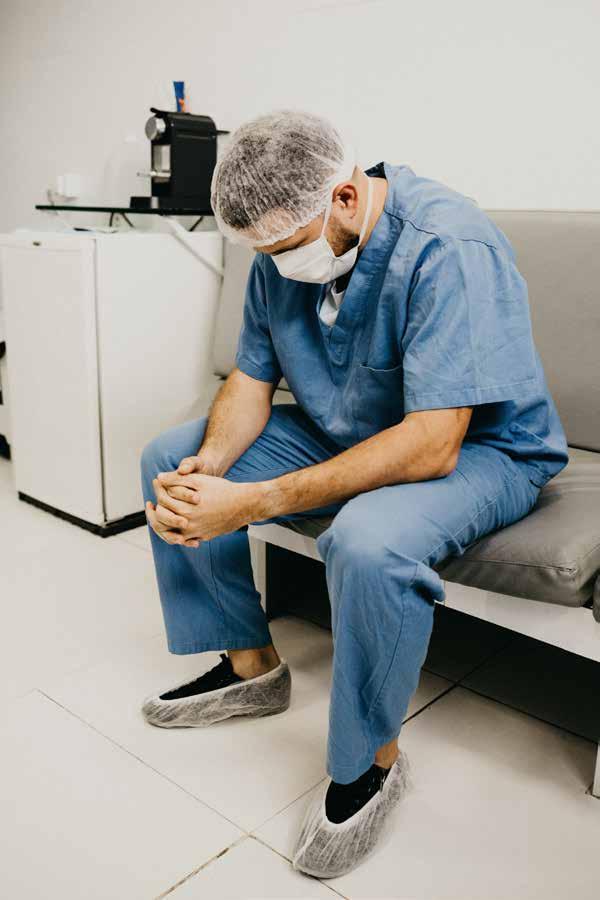
As DUKAL employees work to ensure essential medical and PPE products are reaching healthcare workers on the frontlines of COVID-19, we want to take a moment to recognize and thank the essential workers who are committing tireless hours to keep our nation going.
While it can feel like the world is standing still, everyone at DUKAL would like to acknowledge the postal workers - the grocery and restaurant workers - the farmers - the service worker - the not for profit staff - the truckers - the pharmacists - the police officers - the firefighters - the nurses, doctors, therapists and patient care aides from the medical industry, know your selflessness and dedication is so appreciated.
Follow @dukalcorp to hear DUKAL employees share their thanks.