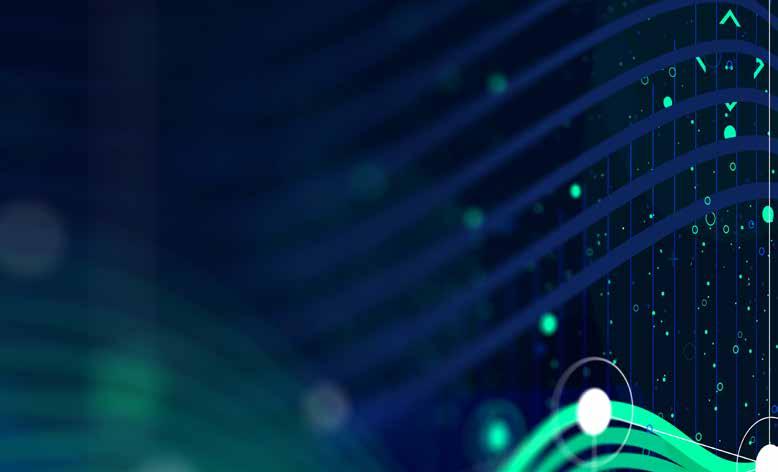
12 minute read
A Researched Essay by Mary Cameron BSc LFOH CertOH
DISCUSS THE ROLE AND RELEVANT IMPORTANCE OF MEASURED VIBRATION LEVELS AND MANUFACTURERS’ DATA IN THE ASSESSMENT OF EXPOSURE AND THE IMPLEMENTATION OF A
Advertisement
A RESEARCHED ESSAY BY MARY CAMERON BSC LFOH CERTOH REVISION DATED: APRIL 2020
Employers are required to protect their employees against the risk to their health and safety arising from exposure to vibration at work. Estimating this risk and preventing unacceptable exposure to hand arm vibration (HAV) is crucial to avoid adverse health effects.
The employer must choose the most suitable method for assessing HAV exposure based on their particular circumstances while understanding the benefits and limitations of that method. The most important action an employer can take is to focus on HAV exposure control and the principle of ALARP (reducing exposure to as low a level as is reasonably practicable as per the Control of Vibration at Work (CVW) Regulations 2005). The work process should be designed so as to avoid HAV exposure from the outset. If the process was not designed as such initially, this may result in a subsequent restructuring of the work process or carefully managing exposure which cannot be reasonably reduced any further through controls. Understanding the risk and assessing exposure may require (some or all as follows, depending on the circumstance) observing specific working practices, the use of personal dosimeters, applying Health and Safety Executive (HSE) advice, referring to relevant information on the probable vibration magnitude (e.g. tool manufacturer’s data), and, if necessary, measuring the magnitude of vibration to which the employees may be exposed (e.g. on-site monitoring of actual tool usage).
Measured vibration levels play a role in the HAV risk assessment by allowing the employer to understand the magnitude of which their employees are exposed to vibration under the actual condition of tool use. On-tool measurements can usually give more accurate data based on tool use within a particular process. As opposed to the manufacturer’s tool vibration data which is derived based on specific circumstances of application under laboratory conditions. But as with any assessment method, there are limitations. On-tool measurements rely on the operator to demonstrate
XXXX

‘typical’ use which may vary from day to day or person to person e.g. hand placement onto tool, tool age, when the tool last underwent maintenance, various tool heads, accessories or power settings, various materials being worked on, only part of the process was able to be demonstrated at the time, particular operatives’ application styles, etc. The ‘fuzzy numbers’ produced from an on-tool vibration assessment should be treated with caution, should measurement data have been gathered in a situation not reasonably representative of ‘typical’ exposure. And for this reason it must also be assured that a competent person, such as a qualified occupational hygienist, is employed to conduct the vibration monitoring as this person will be better able to gauge what the typical process conditions are and take into account any variables.
From my own practical experience when using a BOSCH Sander and Drill, I found that on-tool vibration measurements during conditions of use relatable to those conditions stated under the manufacturer’s information sheet were, for the most part, comparable to the manufacturer’s vibration data. Although variations were seen (the manufacturer’s data over-estimating in some cases) the differences were likely due to differing push forces, test subject’s size or posture, angles of tool application or the exact types of materials in use. This demonstrates that it is difficult to come across real-life situations of tool use which precisely reflect laboratory conditions of testing. This notion is backed by several HSE research reports which revealed in many cases a low-rate of verification for the testing standard (EN 60745). The reasons included a lack of precise specification of the dimensions and design of the test bit, drilling into new concrete blocks vs weathered/aged
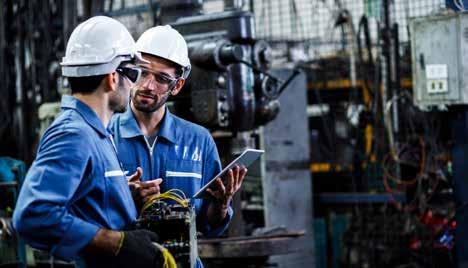
concrete blocks, pendulum settings, the manufacturers’ data were based on earlier test codes, poor clarity about how the machine/tool should be used, push forces in the test codes being unnecessarily high, etc. (HSL, RR868 p.6, RR879 p.4, RR754 p.6, RR717 p.8, 20092011). The employer should thus be wary of the variability of the laboratory test data for these reasons
Research which involves HAV emissions testing largely promotes the application of site-specific on-tool measurement data and cautions against the use of manufacturer’s data. Stating that the test data obtained from different laboratories may vary greatly, as measured vibrations have been shown to vary with the subject’s physical size and with the magnitude of applied hand forces. Difficulties in fabricating a durable mechanism that provides consistent tool loading may also contribute to interlaboratory variances (McDowell et al., An Evaluation of Impact Wrench Vibration Emissions and Test Methods, 2007, p.126). Vibration emissions measured in the laboratory are unlikely to be fully representative of those in the workplace. Therefore, for final tool selections and for reliably assessing workplace vibration exposures, vibration measurements should be collected under actual working conditions (McDowell et al., Comparing Three Methods for Evaluating Impact Wrench Vibration Emissions, 2009, p.617).
The HSE is also aware that some standardised test methods may not be representative of the tool’s vibration risk. HSE guidance cautions that vibration test codes tend to under-estimate the vibration of tools when used in the workplace (by a factor of 1.5 to 2 for pneumatic and electric tools). This being said, the manufacturer’s data must still be considered, as stated under the CVW Regulations. The HAV risk assessment should include consideration of any relevant information provided by the manufacturers of work equipment. The Machinery Directive requires machine manufacturers to provide information on vibration emissions at the hand (which values are obtained from harmonised European vibration test codes) thereby highlighting any ‘residual risk’ associated with the machinery due to shortcomings of the protective measures adopted by the manufacturer. Declared emission values allow purchasers to compare machines tested to the same standardised test code.
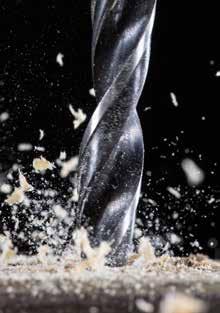
The emission values can show when there are large differences between machines, so that high-vibration tools can be avoided (EU, Good Practice Guide HAV, 2006, p.15). Although the manufacturer’s data is largely cautioned against, the need for the manufacturer to provide details on residual risk is statutory and so stands. It does though serve a purpose in providing a ball-park figure of the tool’s vibration level in order to direct the employer in purchasing low-vibration tools from the outset. The employer may therefore use this information for tool comparison purposes especially at purchasing stage. Measured vibration levels conducted on-site are important for obtaining more accurate data of site-specific exposure. This may be needed when it cannot be reasoned that the manufacturer’s data (or other reliable data resources e.g. the HSE hand-arm vibration exposure calculator tool, Operc or Havtec databases) is representative of exposure from actual tool use in a particular process. Since the declared vibration emission level normally only represents the main applications of the tool, any tool use outside of its ‘main applications’ may significantly increase the exposure level over the total working period. The HSE’s standpoint is that should it be reasonable to expect that the manufacturer’s data is representative of the range of exposure which may be experienced on-site (i.e. the process and testing conditions are similar) then this data may be applied for the purposes of a preliminary assessment of exposure, in lieu of on-tool vibration measurements (where a specialist may not be readily available to attend site).
The emphasis should be placed on ensuring that the vibration magnitude data in use (however sourced) is reasonably true to the situation on-site. However, a strong argument for the use of on-tool measurement data is the expectation that it should be the tool in use to do the job under assessment. This is what the HSE expect to see when measurements have been undertaken. But as long as the employer has sourced the general range of the tool’s expected vibration magnitude in that process then either method (manufacturer’s data or on-tool measurement) can provide the information needed to sufficiently assess the risk and base controls around. Occupational ill-health court cases are typically concerned with the employer’s lack of appropriate actions to control exposure, not whether or not on-tool vibration measurements have
been taken. So the employer should focus their resources on risk reduction actions rather than unnecessarily hiring in a specialist to undertake the on-tool vibration measurements and subsequent reporting. It comes down to a cost/ benefit analysis: would the money and resources spent on monitoring (which is not required by the HSE) be better spent on improving processes and equipment? (Wilson, P., 2019).
This being said, I have found in my experience that it often cannot be reasoned that the manufacturer’s data is representative of exposure from actual tool use on-site. As an example, I recently attended a train maintenance depot to perform on-site testing of vibrating tools (with various blades and power settings) which were used to cut into a polyurethane sealant for removal of damaged train windows. Prior to my visit, the employer had set a 30 minute limit of total tool usage per person per shift based on the manufacturer’s data for these tools (stating a magnitude of 10 ms-2) to achieve a HAV exposure at the Exposure Action Value (EAV) of 2.5 ms-2 A(8). My findings when assessing these tools under various conditions of use found that the average vibration magnitudes were two to three folds higher than stated by the manufacturer. This indicated that daily exposure is likely to exceed the Exposure Limit Value (ELV) of 5.0 ms-2 A(8) if the tools are used for 30 minutes total per day. In this case, the employer had become reliant on the validity of the manufacturer’s vibration data (by incorrectly assuming that conditions of tool use on site were similar enough to the laboratory test conditions) and this resulted in overexposure even from restricted usage time.
My client’s approach was not correct from the get-go in that one should not ‘work up to the limit’ but must apply an ALARP approach in all cases of HAV exposure. Based on my on-tool measurements, even with just 10 minutes of tool use per day, the EAV would be approached or exceeded. Therefore time limitation on these tools was not a practicable solution to
Occupational illhealth court cases are typically concerned with the employer’s lack of appropriate actions to control exposure, not whether or not on-tool vibration measurements have been taken. So the employer should focus their resources on risk reduction actions rather than unnecessarily hiring in a specialist...
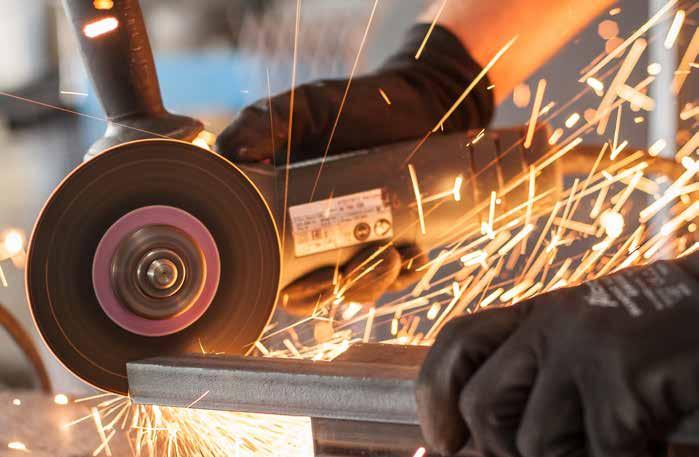
reducing exposure to an acceptable level and alternative means of exposure reduction needed to be considered. For example, alternative means of window removal such as grasping tools to pull the sealant out, seek low-vibration tool alternatives or adaptions, use of non-vibrating tools to cut out the sealant, breaking a portion of the glass to relieve pressure along the edges prior to cutting with vibrating tools, or seek advice from specialist window removal companies. So, as I have seen, the manufacturer’s data can be misunderstood and misused by the employer. On a contrary note, there is no legal requirement to undertake on-tool measurements or monitoring of vibration. The CVW regulations direct the employer to assess daily exposure to vibration and if necessary measure the magnitude of vibration to which employees are likely to be exposed. But from my experience with an array of site managers where I have discovered situations similar to this example, I would recommend that it is necessary to undertake on-tool vibration measurements in most cases.
On-tool measured vibration data can give ‘fuzzy numbers’ and the manufacturer’s data may be unreliable. Should it be determined that it is not suitable in that particular process to apply the manufacturer’s data then on-tool measurements of vibration may be required to ensure that the residual risk of vibration exposure is being appropriately managed. And visa versa, should it be determined that on-tool measurements are not necessarily required and the manufacturer’s data is suitable. Although on-tool measurements may be more accurate, arguably if both data sources were to produce the same general range of vibration magnitudes then the subsequent controls would be the same. With both data sources having their limitations though, employers should recognize these limitations, choose the most appropriate method, and focus on understanding the level of risk through a ‘soundly based estimate’ of daily exposure. The employer must determine (through observation over a representative period) which tasks expose workers to vibration, who is
exposed, what tool they use and what for, and the total time they are in contact with the tool in operation i.e. a daily ‘trigger time’ estimate. At the same time, questioning if the principle of ALARP has been applied to the work process, if the EAV or ELV is likely to be exceeded, if the hierarchy of control has been adequately reflected in the current controls, or if modifications to the process are required. On completion of the risk assessment the employer must implement an appropriate HAV exposure reduction programme and monitor the effectiveness of the controls through the regular review of that risk assessment.
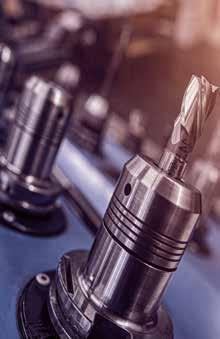
REFERENCES:
1. ISVR, HSL, BGIA, INRS, and HSE under the supervision of The Working Party
“Vibration” mandated by the Advisory Committee on Safety and Health at Work in cooperation with the European Commission (2006). Guide to good practice on HandArm Vibration, Non-binding guide to good practice with a view to implementation of Directive 2002/44/EC on the minimum health and safety requirements regarding the exposure of workers to the risks arising from physical agents (vibrations). Edition V7.7. [PDF]. European Union, page 15. Available at: http://resource.isvr.soton. ac.uk/HRV/VIBGUIDE/HAV%20Good%20 practice%20Guide%20V7.7%20English%20 260506.pdf [Accessed March 2019]. McDowell, T., Dong, R., Xu, X., Welcome, D., Warren, C., (2007). An Evaluation of Impact Wrench Vibration Emissions and Test Methods. The Annals of Occupational Hygiene, Volume 52, Issue 2, March 2008. [PDF] Morgantown, USA: National Institute for Occupational Safety and Health (NIOSH), NIOSH Health Effects Lab, page 126. Available at: https://academic.oup. com/annweh/article/52/2/125/278857 [Accessed February 2020].
2. McDowell, T., Marcotte, P., Warren, C., Welcome, D., Dong, R., (2009). Comparing
Three Methods for Evaluating Impact Wrench Vibration Emissions. The Annals of Occupational Hygiene, Volume 53, Issue 6, August 2009,. [PDF] Morgantown, USA: National Institute for Occupational Safety and Health, Health Effects Laboratory Division; Montre´al, Que´bec: Institut de
Recherche Robert-Sauve´ en Sante´ et en Se´curite´ du Travail, page 617. Available at: https://academic.oup.com/annweh/ search-results?page=1&q=Comparing%20
Three%20Methods%20for%20 Evaluating%20Impact%20Wrench%20
Vibration%20
3. Wilson, P., 2019. ASA Ruling: Wrist Mounted HAV Monitors Do Not Measure To The Standard … Not Suitable For Regulatory Risk Assessment... [online] Invc.com. Available at: http://www.invc. com/fact-wrist-mounted-hav-monitorsdo-not-comply-with-the-standard/ [Accessed March 2020].