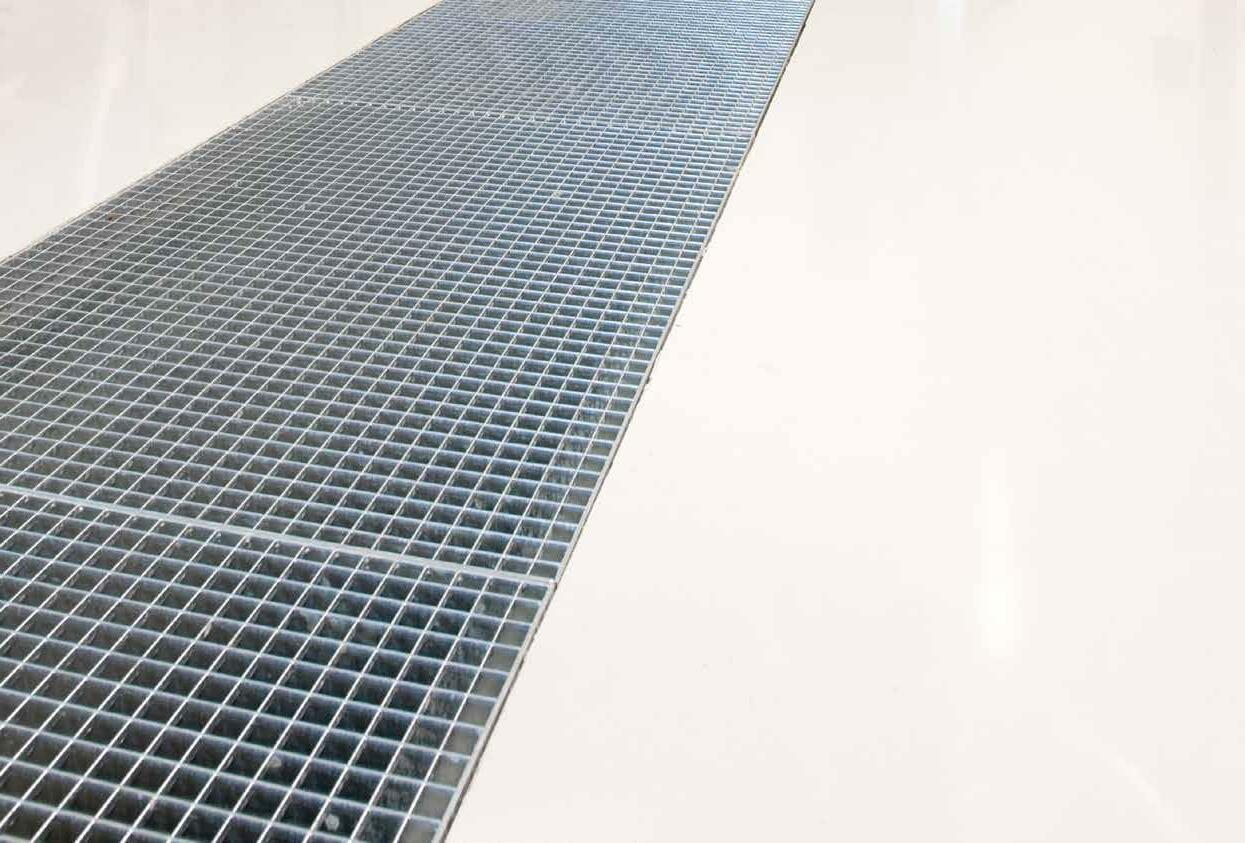
7 minute read
Custom floor for
Baby and infant food producer meets strictest food safety and hygiene standards
Custom floor for Mead Johnson
Bolidt designed and produced a new floor for Mead Johnston’s production location in Nijmegen in record time. A sleek, seamless synthetic floor system was installed over the existing, irregular substrate, producing a floor that meets the strictest standards in the field of hygiene and food safety. This producer of baby and infant food took full advantage of Bolidt’s ‘everything under one roof’ principle.
Image for reference
For over 100 years, Mead Johnson has specialised in formulating and manufacturing nutrition for babies and infants. In fact, the company was one of the first manufacturers to conduct scientific research in this area. Today, Mead Johnson has some 3,000 employees worldwide and is active in more than 110 countries. This globally operating manufacturer has developed countless special products over the years, such as nutrition for infants with allergies and health problems.
In the Netherlands, Mead Johnson has had a manufacturing plant in Nijmegen since 1984, though a lot more than producing formula and such goes on here. The company also conducts research in Nijmegen and has its own R&D department where new products are developed. The main sales markets of the Nijmegen plant are Europe, Latin America and Asia, with China being the largest buyer by far. Since 2021, the company has been part of Mead Johnson China and works closely with the Chinese manufacturing plant in Guangzhou.
Mead Johnson has been experiencing strong growth in Nijmegen for years. To be able to handle the increasing demand for baby formula from China, the manufacturing plant will be expanded further in the coming years. In the meantime, renovation work is also taking place. Take the existing tile floor for example, which was recently replaced. An audit revealed that this tile floor no longer met the international requirements in the field of hygiene and food safety. The regulations of the authorities who oversee food safety are extremely strict: if the floor did not comply, and comply very soon, production would have to be brought to a standstill.
Giving bacteria zero chance
Bolidt has built an impressive track record in the food sector. So, there was no doubt on the part of Mead Johnson as to who would supply the new floor for the Nijmegen manufacturing plant. It marked the start of a complex project: the floor had to be replaced while production continued and the new synthetic floor system had to be installed over the existing tile floor. Naturally, Mead Johnson wanted the number of production stops to be kept to a minimum. An there was yet one more challenge: to meet the standards as quickly as possible, the project had to be completed in three weeks.
It was clear from the outset that Bolidt’s floors would meet the strict standards Mead Johnson was subject to. By working closely with clients and by continuously inno-
vating, Bolidt has developed floor systems that are extremely suitable for the food sector. The dirt-repellent floors are pore-tight, meaning there’s no chance for bacteria to get a foothold and start growing. The risks of bacterial growth are reduced even further because Bolidt installs the systems seamlessly, including where the floor meets the walls, skirting, point and trench drains and grates. Thanks to the wear resistance and durability of the synthetic systems, no holes, cracks or tears will appear in the floors, even when using heavy machinery and transport equipment. And given that any little crevice could allow dirt to accumulate and bacteria to grow, that is a prerequisite.
A key requirement from Mead Johnson was that the floors must be easy for the staff to clean. Thanks to the sealed surface and the seamless finish, Bolidt floor systems can be cleaned quickly with a high-pressure hose. They have been extensively tested and can withstand the daily use of cleaning agents. The floor Bolidt installed at the Mead Johnson facility also has a non-slip finish to help ensure the safety of the people working there by preventing slipping or falling while working, even in wet conditions. With these features, Bolidt floors make an optimal contribution to ensuring a safe working environment.
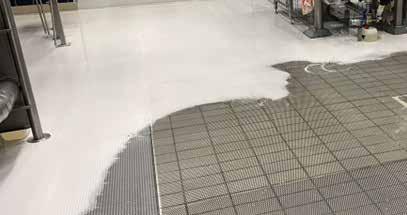
Everything under one roof
It wasn’t just the quality of its floors that convinced Mead Johnson to go with Bolidt: the fact that Bolidt has everything under one roof in Hendrik-Ido-Ambacht was also a deciding factor for the manufacturer. This distinguishes Bolidt from other suppliers, enabling the company to develop, test and produce floor systems and then install these with its own installation teams. Because Bolidt manages everything in house, Mead Johnson did not have to talk to several different parties and the floor could be completely customised, a major advantage for such a complex project that had to be delivered in record time.
The biggest benefit of having everything under one roof became apparent when addressing a serious challenge, handling an irregular surface like the existing tile floor. It was essential that the many irregularities in the original floor not show up in the new synthetic floor. With the proactive approach of Bolidt’s own R&D and production department, as well as Bolidt’s installation team, together with the client a solution was devised and the new floor was tailored exactly to Mead Johnson’s needs and wishes. The Bolidt team was able to create a solid surface by first installing expanded metal (metal mesh) onto the tile floors and applying mortar over this. They then installed a Bolidtop® 500 SAR floor over the now even surface. This system is not only heavy duty when it comes to handling chemicals and equipment, but also very wear-resistant and durable. With this new floor, Mead Johnson will meet the strictest requirements in the area of hygiene and food safety for the next 30 years as well.
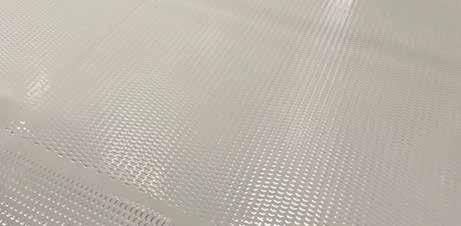
Hygienic floor for new biscuit and wafer factory Orkla in Latvia
Develop–Produce–Apply–Repeat
Multinational Orkla wanted a reliable floor for its new biscuit and wafer factory in Latvia. Because Bolidt manages everything in house, it was able to get right down to work and deliver the extremely hygienic Bolidtop® 700 system to Orkla on schedule. Exactly the floor Orkla was looking for.
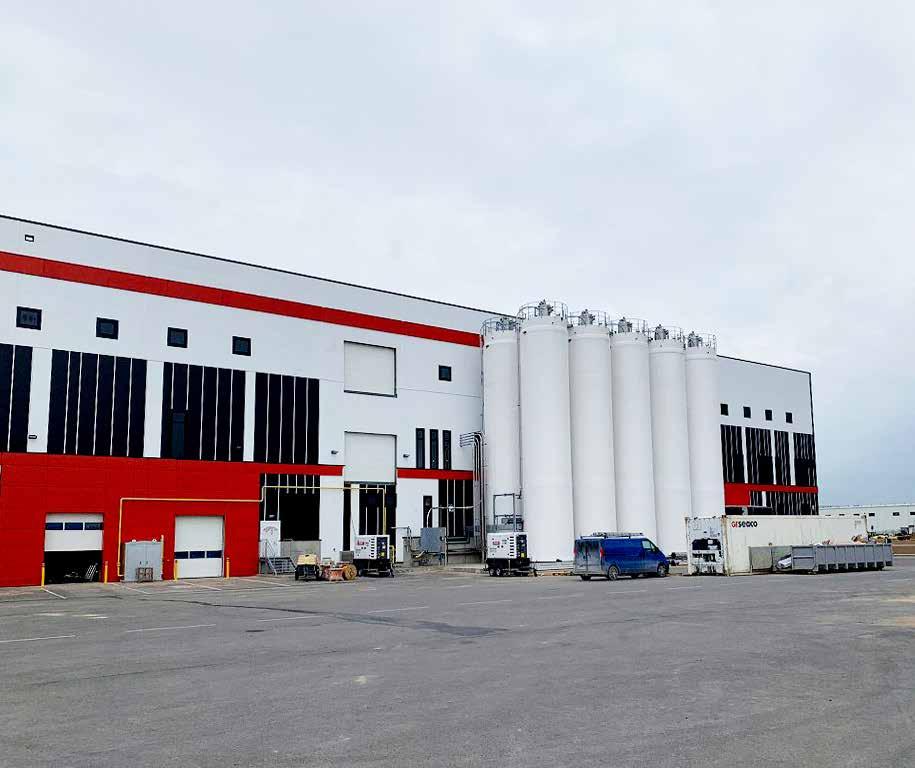
Listed on the Oslo Stock Exchange, Norwegian conglomerate Orkla has around 300 brands and more than 21,000 employees. And yet the name Orkla is barely known in the Netherlands. This is because the company is mainly active in the Nordics, as well as in the Baltics and in selected countries in Central Europe and in India. In these regions Orkla supplies a wide range of products: food, confectionery and snacks and food ingredients, care and health products, cleaning products, paint products and clothing.
The fact that Orkla does not limit its activities to the Nordics is apparent from the substantial investment the company is making in Latvia. In the city of Ādaži, Orkla is having an ultramodern factory built with 13 production lines and covering more than 30,000m2. Orkla’s new production unit specialises in the production of biscuits and wafers and should be operating at full capacity in 2023.
The construction of the modern, efficient and above all sustainable factory aligns well with Orkla’s strategy, which is strongly centred on innovation. The company sees it as its mission to make customers’ lives ‘a little better every day’ by providing quality products. From Ādaži, Orkla wants to create new products and develop strong local brands further. According to Orkla, the new production unit will enable Orkla to continue building on innovations.
Full control
When you say quality, sustainability and innovation, you say Bolidt. It’s hardly surprising then that Bolidt was commissioned to supply the flooring for Orkla’s new factory in Latvia. And that floor system was the Bolidtop® 700, an extremely wear-resistant and durable system that has already proven itself at many food companies. The reliable system is seamless, pore-tight and easy to clean, making it extremely hygienic. The non-slip top coat also makes the Bolidtop® 700 very safe. These are exactly the requirements Orkla set for the flooring in the new production unit.
Unlike the competition, Bolidt could assure Orkla that it could deliver the floor on schedule, the big advantage of handling the entire value chain in house. Not only does Bolidt develop and test floor systems, it also produces them. What’s more, Bolidt’s own staff handle the installation. This allowed Bolidt to respond agilely and quickly and offer Orkla security of supply. And there’s another advantage for Orkla in Bolidt having full control over all aspects: Bolidt can install the same floor system anywhere in the world. If the multinational decides to open new production units elsewhere, Bolidt can supply a synthetic system with exactly the same specifications as in Latvia. This also means considerable time savings and optimum security of supply.
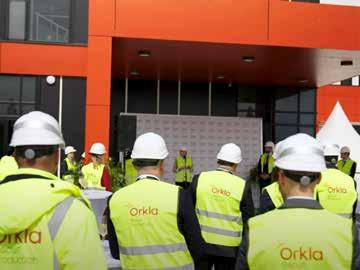
Recently, a special time capsule was laid in the foundations of Orkla Biscuit Production plant to leave a message for the generations to come.
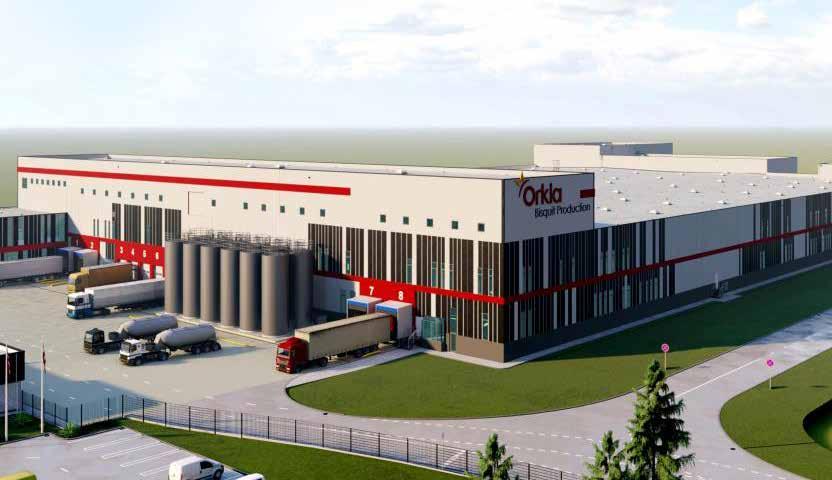