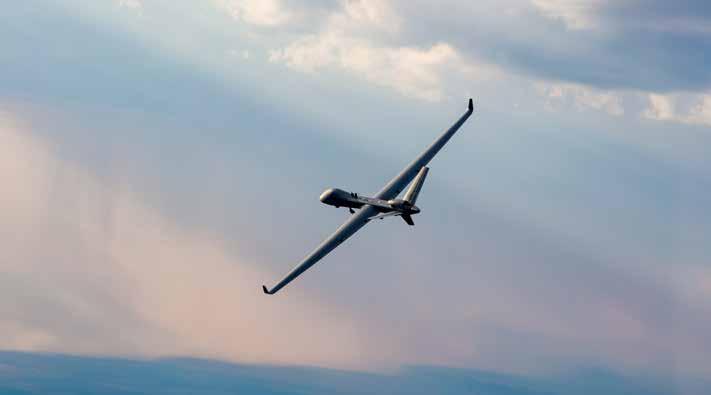
6 minute read
General Atomics Aeronautical Leverages Additive Manufacturing for Product Line of UAS
World Leader in Unmanned Systems leans Into Its Global Partnerships for Additive Manufacturing, creating high strength-to-weight ratio components and shortening the manufacturing process.
Being the world leader in Unmanned Aircraft Systems (UAS) means continuing to evolve in all areas of the business enterprise in order to continue providing customers with the best product at the best price.
At least that’s the attitude of General Atomics Aeronautical Systems, Inc. (GA-ASI), designer and developer of the MQ-9A Reaper, MQ-1C Gray Eagle, and the new MQ-9B SkyGuardian®/ SeaGuardian® UAS that have become ubiquitous in the areas of national security and defence throughout the world.
Developing global partnerships to improve products in the design phase or through-life phase is proving to be highly beneficial to GA-ASI and its customers. New Zealand’s highly capable, niche design and manufacturing industry, in particular, affords many opportunities to expand regional UAS opportunities well into the future.
As GA-ASI builds on its 30-year legacy, which includes more than 1,000 aircraft delivered and more than 8 million flight hours across its Predator® aircraft series, the company continues its long tradition to lead through innovation in technologies that differentiate its UAS platforms. One such cutting-edge technology is Additive Manufacturing(AM) for which GA-ASI has become an industry leader.
So, what is Additive Manufacturing? AM is a process by which a manufacturer takes a 3D computer-aided design (CAD) model and virtually slices it into thousands of layers. The layered data is sent to a printer where material is added one layer at a time in order to create a three-dimensional object. This process is commonly referred to as 3D printing.
AM at GA
“We began investing in our Additive Manufacturing over a decade ago,” said GA-ASI President David R. Alexander. “Using AM, we developed the ability to create components that have a very high strength-to-weight ratio, a factor that has a direct impact on fuel efficiency and aircraft performance.”
AM also accelerates the time of product launch to market by shortening the design and manufacturing process, increasing productivity, reducing assembly costs, and providing cost advantages in low-number production. Additionally, AM allows for more complex and unitised designs to be manufactured, leading to performance improvements and significant cost reductions.

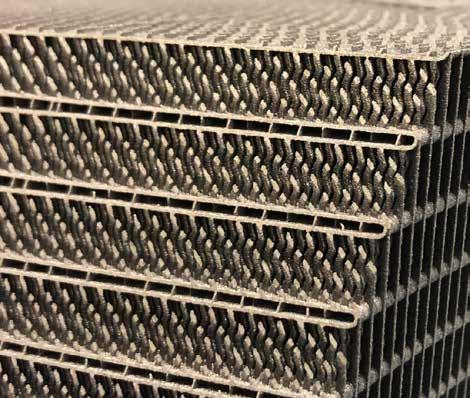
When GA-ASI initially introduced AM techniques in 2011, the focus was on rapid prototyping, tooling, and shop aids. The company has now integrated AM into its main flight-ready part production operations. In 2018, GA-ASI understood the need for growing a strong and knowledgeable AM team to lead the company into the future of the technology. Then in 2021, GA-ASI established a new Additive Design and Manufacturing (AD&M) Centre of Excellence.
The Centre is focused on rapid-reaction and recurring manufacturing of GA-ASI’s line of UAS using fully functional flightready AM applications, technology risk reductions, large-scale tooling, and next-generation flight hardware development.
AM for MQ-9B
GA-ASI has several thousand AM parts currently flying on board its UAS, with a combined total of more than 300,000 flight hours with these AM parts. That includes thermoplastics, composites, and metal components.
GA-ASI’s AM team focuses on embedding AM materials and processes as well as business-savvy applications within multiple aircraft programs and acts as the primary AM resource for all GA-ASI stakeholders. The team leverages several different AM technologies, each adapted specifically to relevant applications and requirements.
For its newest platform, the MQ-9B SkyGuardian/ SeaGuardian, GA-ASI has qualified and implemented over 240 AM parts, which ultimately optimize the manufacturing process and reduce recurring costs by as much as $300,000 per aircraft and save an estimated $2 million in tooling costs.
GA-ASI is continually looking for ways to enable, accelerate, and integrate AM technologies into its designs, operations, and products. Through the AD&M Centre of Excellence, the company adheres to a structured and stringent qualification process for AM applications that delivers a positive business case over conventional manufacturing methods.
AM for Small UAS
Militaries throughout the world are looking for new small, unmanned aircraft to take on big jobs. GAASI’s small folding-wing UAS called Sparrowhawk, for example, is designed to take off from a larger mothership such as the MQ-9B SkyGuardian, fly a scouting mission, and then return and be recovered by the SkyGuardian in mid-flight. It could then be refueled and support another operation within the mission.
Meanwhile, GA-ASI’s propellerdriven Eaglet provides “air-launched effects” for an attacking force. Suppose an MQ-1C Gray Eagle 25M released an Eaglet or two that were tasked with detecting hostile air defence radars, jamming enemy electronics systems. The aircraft might return from those missions to be used again. These are some of the most dangerous assignments in the world – which is why it makes sense to send an unmanned aircraft to undertake them. If something happens to these aircraft, no human pilot ever had to risk her or his life on the flight.
Incorporating cost-saving measures such as a greater use of AM into these and other aircraft is another way GA-ASI can provide aircraft that are both as capable as customers require but also much less costly than they would be otherwise.
Global Partnerships
Consistent with its global customer base, GA-ASI’s AM initiative has tapped expertise from around the world. One example is Conflux Technology. This Australianbased company specializes in AM for heat exchanger applications. The two companies have worked together since 2018 to develop heat exchangers compatible with GA-
ASI’s MQ-9B line of UAS. In 2022, the two companies announced their collaboration on a new Fuel Oil Heat Exchanger, which is the fourth AM project the two companies have worked on together since 2018.

“When you are leading the charge on advanced technology, you need a world-class team and agility to do it right,” said Ben Batagol, Conflux’s Head of Business Development. “Our project with GA-ASI enables drop-in replacements that remove thermal load and maintain a compact profile while also increasing performance to meet higher system demand.”
In addition to Conflux, GA-ASI has partnered with companies in Europe and India. As GA-ASI’s reach extends further into the Indo-Pacific, opportunities for an expanded network of local industry partners for rapid manufacturing and AM, including in New Zealand, will increase.