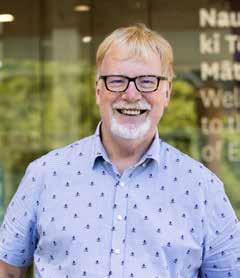
22 minute read
Charles Clifton: Earthquake, Fire, and Durability
In this extended interview with FireNZ Magazine editor Nicholas Dynon, Associate Professor Charles Clifton discusses the development of structural steel in New Zealand and the many challenges still facing the development of fire resilient buildings.
Earlier this year, University of Auckland Associate Professor Charles Clifton was made a Distinguished Fellow of Engineering New Zealand in recognition of 39 years of research making steel and composite steel/ concrete structures and buildings in New Zealand safer from fire and earthquakes.
Describing himself as “an engineer who works at a university rather than an academic”, Dr Clifton says that a significant part of his career has been about sorting fact from fiction. Along the way, his career has helped grow the use of structural steel in multi-storey buildings and made buildings of any material safer.
FNZM: Congratulations on your award – a significant achievement.
CC: It was a much bigger award than I realised when I got it. I didn’t apply for distinguished fellow; it is something you are nominated for by others. When the President of Engineering New Zealand phoned to give me the news, I was very surprised and delighted.
Essentially, the recognition was for my work in providing the technical foundation to build the market share for structural steel with an emphasis on multi story buildings. That was my job description back in 1983 when I set up the New Zealand Heavy Engineering Research Association’s (HERA) structural division.
FNZM: You mention that much of your work has been around sorting fact from fiction… CC: There was effectively no steel used in multi-storey non-industrial buildings by 1983. For non-industrial buildings by the beginning of the 1980s, the market share for steel in buildings more than two storeys high wouldn’t have even been one percent. There might have been the occasional building that used it, but it was really rare.
FNZM: What’s the market share these days?
CC: Now it’s about 65% nationwide. It varies geographically. In Auckland it’s around about 50%, in Wellington and Christchurch it’s around 85-90%, and in most of the seismic reactive areas it’s around 90%. There are some pretty cost-effective solutions for concrete in medium rise buildings that you can’t do in a high seismic zone that you can do in a lower seismic zone, which is why the market share in Auckland is lower. FNZM: You’ve said that there are three advantages to steel: in relation to earthquakes, in relation to fire, and in relation to durability…
CC: When I started out, the three barriers to the use of steel were earthquake, fire, and durability.
A lot of work had been done – led by the University of Canterbury – on developing new seismic resisting systems in concrete, and that had strong government support, which dates back to the late ‘60s and early ‘70s. Structural steel had been used in New Zealand in multi-story buildings before then, but by that stage it had become a bit more expensive, and there was also the very high-profile case of the BNZ Centre in Wellington in the early 1970s that had ran into intense problems with the unions.
The BNZ Centre involved a new form of steel construction that nowadays is reasonably commonplace but at the time was rather high tech, and it stretched the capability of the industry. They also had problems with poor quality steel, the job was badly managed, and it required a lot of onsite welding. It became embroiled in a simmering dispute between the Boilermakers’ Union led by Cornelius Devitt, which covered welders, and the National government of the day, led by Robert Muldoon. Those two were very strong and opposing personalities.
This dispute came to a head when the Government deregulated the union, which brought a whole lot of other unions out in support and pitted the unions against the government. Muldoon issued a directive, through
the government, that no more government buildings were to be built using steel, and this effectively killed the industry.
By the time we got to the end of the ‘70s the BNZ Centre was still sitting there unfinished [it wasn’t finished until 1984], and it became the symbol of this political battle. Effectively the use of steel in multi-storey construction stopped at that time.
And then the universities asked, if we’re not going to use steel for seismic resisting systems, how are we going to build these in concrete? Concrete had some known issues with earthquakes that needed to be resolved, so a lot of money was given to the universities and the Ministry of Works to develop seismic resistant reinforced concrete solutions. Seismic resistant systems for concrete were developed, and they were seen to offer better performance than anything that could be built in steel.
Then there was the issue of fire. It was considered that if a steel building was exposed to severe fire and the steel got heated above 550 degrees, the members would fail. Because fires typically burn at over 1,000 degrees, if steel got into a fully developed fire, it would certainly fail unless it was insulated. In the building code at the time, NZS 1900 Chapter 5 made it a requirement that if you were building in city areas you had to build in reinforced concrete and masonry – so steel wasn’t permitted to be used.
And then there was also the fact that because steel rusts when exposed to air and water it wasn’t considered suitable for use in an external environment. Because New Zealand’s environment was at the time considered to be “uniquely corrosive” – which was a perception that was fostered by the concrete roofing industry who were looking at pushing concrete tiles as a solution to New Zealand’s “uniquely corrosive” environment – it was seen that steel was not suitable for external applications.
These were the three big issues that I had to look at and figure out what was perception, what was reality, to look at how to change the perception where it was technically wrong, and to look at what to do to rectify it where the FNZM: What were the key turning points?
CC: By 1985 we were starting to make some progress. In August 1985, we held the Pacific Structural Steel Conference, where we brought in keynote speakers from around the world to contribute to the first-ever technical conference in New Zealand relating to steel. In November of that year, the structural steel seismic working group of the New Zealand Society for Earthquake Engineering, produced a set of papers on the current state of the art around the world in seismic design and steel. I was starting to get a feel of the job and assemble enough information to start publishing some useful things.
We also had the first couple of highrise buildings in Auckland in steel go up extremely quickly, and that showed people that it could be done. One of those, which was in front of what used to be the Sheraton Hotel, was project managed by an American contract manager who was used to the US methods of steel construction, which does go up very quickly. The industry was starting to pick up a bit then, so opportunities were arising.
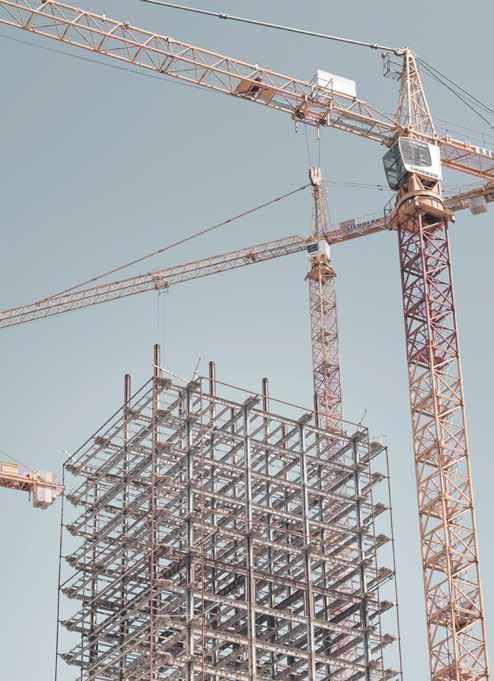
Another turning point was in 1994 with the start of what is now Steel Construction New Zealand. The competition amongst consulting engineers to bid for clients and secure design projects is fairly fierce – a lot of us in the profession would say too fierce – with fees being pushed down too low to allow consultants time to properly explore alternative materials and means of construction.
This situation had arisen in the early 1980s when developers started to come in as major clients for high rise buildings. We were starting to get technical guidance together on how to set out, develop, and implement good cost-effective steel frame with composite floor solutions for high-rise, but the problem was that the consulting engineers didn’t have time to invest in all the new learning involved to implement these solutions, and to implement them with confidence.
We looked around the world at what others in similar situations were doing, and the Canadians had this organisation called the Project Analysis Service (PAS). If a consulting engineer had a new job, they could go to the PAS and the PAS would do a really effective steel design for them to consider – often with costing information – and pass that to the consultants for their consideration. They took great care to make certain that their designs were always robust, and that was the basis on which they operated.
We decided we’d adopt the same thing. The Steel Structures Analysis Service (SSAS) was set up by the then market development manager for NZ Steel and myself through HERA and supported administratively out of HERA House. We seconded a very experienced steel designer, at that time a senior consulting engineer with one of the big consulting firms, to run the new service, and it started to work very well. He and I wrote the HERA Report R4-76 – Seismic Design Procedures for Steel Structures, which was published in 1995 and is still widely used. That was the first generation of new structural steel seismic solutions and built on excellent research into seismic resisting steel frame system solutions being developed from the mid 1980’s at the Universities of Canterbury and Auckland. Things took off from there.
In 1995 we had the Northridge Earthquake in the USA in which a building with hollow core concrete floors and thin toppings partially collapsed. This was the typical floor system that had been incorporated into the modern, multi-storey reinforced concrete buildings since around 1980. In this case, the floor system was built on a steel frame, but it was the floor system that collapsed, not the frame. Several academics at the engineering schools had started to really worry about how resilient these hollow core floor systems would be in earthquakes, and when this happened, they got concerned about the vulnerability of the many buildings in New Zealand being built using these systems.
At the time, the concrete industry claimed that the collapse only occurred because the floor system was built on a steel frame, and the academics said; well, we don’t think so, if you look at the pictures it wasn’t the steel frame that failed, it was that the floor fell out of the frame, and we think the same thing would happen in concrete, and probably the way concrete behaves in earthquakes might well make the situation worse!
So, in 2000, they set up a landmark large scale test of a full-scale part of a storey of a modern steel building with long span precast floors. It was an impressive test, and sure enough at about a quarter of the deflection that would be expected in a severe earthquake, the floor started to crack up, and shortly after it actually fell out of the frame and landed on the floor of the lab. That really got people worried as to how resilient these floor systems were going to be.
The solutions that the precast sector developed in response increased the cost of building these floor systems by 10-15%, removing the cost difference between precast floors with toppings and concrete slab on steel deck on steel secondary beams. Consequently, more people started to use composite systems and as that happened then the consultants got familiar with designing them, the contractors got familiar with building them, and so the steel market share went up.
We also kept publishing design guidance for fire. We published the slab panel method, which was a way of designing these floor composite floor systems to be able to leave at least half of the total supporting beams without any insulation by using two-way action in the slab instead of one-way action – which actually increases the resilience while decreasing the cost.
We then published the work I’m singularly most proud of because it was a completely new design procedure, rather than adapting a procedure or concept developed from overseas: the guidance on durability. As far as I am aware it is also the first fully New Zealand developed engineering design procedure which has been adopted by another country and adapted for use there (Australia).
I had spent quite a bit of time around the country over the previous 20 years looking at how fast steel rusted and what caused it to rust. BRANZ had done a study in 1981 monitoring the rates of corrosion of test samples at 183 sites throughout New Zealand. Working with the then manager of Steel Construction New Zealand (SCNZ), we linked these rates of corrosion to various climatic effects, enabling us to develop corrosion maps for structural steel in New Zealand and then publish a detailed design guide on how to determine the surface-specific corrosivity category for any piece of steel in New Zealand.
This provided the demand side of things, so you could go through a process and work out a demand and you could then determine what the corrosion conditions would be on a particular steel surface being designed. With that information you could go back into the painting standard and determine the appropriate coating system for each steel surface.
Through this, we were able to show that in some cases people were seriously underestimating how corrosive the environment was, but also that in many cases people were seriously overestimating. So, there were solutions where far too much coating material was being put on, and other solutions where far too little was being put on.
That meant that the New Zealand Transport Agency (Waka Kotahi), for example, were able to feel much more confident using steel in bridges, which meant that steel use in bridges started to slowly increase. The original procedure was peer reviewed by a senior consulting engineer with an international reputation in corrosion protection and further development of the guidance on durability is continuing under his protégé.
By 2010 the market share for steel and concrete multi-storey buildings nationwide was pretty much 50/50.
Then we had the Christchurch earthquakes. In the Canterbury earthquake series, the steel framed building systems all performed better than expected, and the concrete systems performed worse than expected, especially the pre-cast floors with thin toppings. Once again, the precast industry came up with solutions to solve the problems, but they were more expensive and pushed the cost up another 10 to 15%, and now the composite systems that had performed excellently in Christchurch were generally cheaper. This change in cost coupled with the excellent overall performance of the structural steel framed buildings with composite floors, further increased their use and brought the market share up to its current level.
HERA had been funded principally by a levy on steel via an act of parliament in 1979. About six or seven years ago that levy was finally renegotiated, and before that Steel Construction New Zealand (which had started off as the SSAS in 1994, funded initially by New Zealand Steel) needed to find a long-term funding solution. The industry recognised the value SSAS was providing and the need to support it financially long term. After several years of negotiation, a voluntary levy based on per tonne of steel used was agreed and implemented, giving SCNZ significant, secure long term funding.
These organisations and the industry haven’t looked back. We now have a very strong technical support base for steel, very strong industry organisations in HERA, SCNZ, and the National Association of Steel Framed Housing (NASH) working together to support the industry, and with support from the universities’ engineering schools, which was historically Canterbury and Auckland, and now also AUT and Waikato. The fabrication industry is now a world leading industry, and all major contractors are experienced in structural steel multi-storey construction.
The original model that we set up at HERA to increase the use of structural steel was based on a framework established by British Steel for promoting structural steel in England, and we followed this. In this model there was one technical organisation looking after turning research into design guidance and another technical organisation looking after the fabrication industry commercially. Whereas in England, there are four separate organisations, in New Zealand HERA does technical development and industry development, and SCNZ does fabrication, erection, and design guidance, and produces technical guidance (supporting documents for the use of codes and standards).
FNZM: You mentioned that there is a lot on the wish list in the fire and steel area…
CC: Yes, there is a lot on the wish list. The two extreme events that really test a building are severe earthquake and severe fire. If you look at the severe earthquake, going back to the 1970s we started to look seriously at how do buildings perform in earthquakes? Why do they perform the way they do? What are bad performance characteristics that you have to overcome? And what are good performance characteristics enabling the building to ride out the earthquake without collapsing and killing everybody?
A lot of work has been done since the mid ‘70s to understand whole building performance in earthquake and turning that into design and detailing guidance so that, when implemented properly, one can build a building that performs in the way that it’s intended to, preserving life safety and increasingly with emphasis on post-earthquake return to service.
The same thing has not occurred in fire. In fire it’s quite the opposite, because in fire traditionally everything is tied back to the fire resistance rating of individual building elements in the standard fire test.
Typically, the way that fire resistance is built into a building is that somebody comes up with a fire resistance rating either by a Deemed to Comply document (acceptable solution) or by taking C/VM2 (verification method) and doing a design. They come up with a fire resistance rating (FRR), then either the architect or structural engineer looks at each element of construction and determines what they need to do to make certain that this element – whether it be a beam, a column, or a wall or a floor – can meet the FRR prescribed (which was determined from that element’s performance in the standard fire test).
Then you assemble everything together, and the inherent assumption is that the performance of the structural system will be at least as good as the performance of the worst performing element in the standard fire test.
So, firstly there’s an assumption that your fire resistance rating does actually represent the fire severity from the burnout of a real fire, and the second assumption is that if you apply the fire rating to every element independently and join them all together the overall system will perform better than the worse performing of the individual elements. In many ways both assumptions are incorrect, which is reflected in the poor performance of multi-storey buildings in severe fires, which we will return to later.
For example, in an apartment building we design for a fire rating typically of 30-60 minutes, which is based on a fire load energy density of 400 Megajoules per square metre. This is actually pretty accurate if you take all the fire load in an apartment, and you average it over the total floor area. But in practice, you get things like walkways, bathrooms, and toilets that have no fire load in them, and then kitchens and bedrooms that have double the design fire load.
Given this, you’re going to get a fire of varying severity across an apartment as the high fire load areas will experience a much more severe fire than the low fire load areas. That means that your building has to be able to contain a fire of severity that might be double what you designed for, and it’s got to be tough enough and deformable enough to remain standing and prevent fire spread – and to not collapse.
If you look, for example, at a steel frame system, the floor system has much higher inherent fire resistance than the individual floor slab or beams have in a standard fire and has the ability to undergo controlled deformation without loss of integrity or load carrying capacity. The columns potentially have less fire resistance in a real structure than they do in a standard fire test, because the loading conditions on the column are quite different.
And the other thing that the standard fire misses out on completely is connections. There’s no standard fire testing of connections because you can’t actually do it. The issue of connection performance in severe fires is a significant unknown in all multistorey structural systems.
The standard fire test also doesn’t treat materials the same. It is based on a standard fire prescribed timetemperature curve in a purpose built fire testing furnace, so if you do a standard fire on a concrete or steel element, which absorbs heat and doesn’t burn, to generate the prescribed time-temperature curve you’ve got to pump quite a bit of fuel into the furnace in to keep the gas temperature up while the heat’s going into the structural system that you’re testing as well as into the walls of the furnace.
Timber, on the other hand, burns, so you basically have to turn the fuel load down so that you don’t overheat the furnace, and you end up with quite a different severity of fire for timber compared with for steel and concrete. This affects the charring rate of timber in a furnace test. Modern engineered timbers also burn more readily than solid timber on which much of the furnace tests have been conducted.
The other thing is that well designed concrete floors on steel decks on steel beams are very deformable in fire without failure, so if you get a very severe fire locally the system will deform and shed load into the areas that are less effected. The same thing doesn’t happen with other floor systems.
In earthquake there’s a recognition that while you design a building for a specified level of earthquake, in practice the demand could be quite a bit higher than what you designed for. You want the building to be tough enough so that the behaviour is essentially the same if the earthquake’s more severe than you expected. We’ve done a pretty good job of achieving that.
In fire we haven’t. There’s been no attempt at all to build toughness into buildings in fire so that they will sustain a fire that’s more severe than what has been designed for.
One of the things that we’re looking at now is developing solutions that will give a similar reserve of toughness to a more severe fire than you expected to what we currently have in earthquake. We’re getting well down the track of being able to provide guidance on that for composite floor systems supported on steel frames, thanks to our understanding of their whole structural system behaviour in severe fire, which is better than that for any other structural system.
Some of the solutions that have been developed, especially around concrete floor systems, for improving their performance in earthquake may well decrease their performance in fire. BRANZ has recently done a test on a hollow core concrete with thin topping solution in the furnace, which was rated for 2+ hours in the standard fire, and it started to fail after 29 minutes.
The Americans – I’m on the expert advisory group for NIST’s fire research lab in Washington (the largest fire testing laboratory in the world) – can do full-scale tests of two stories with complete control over the additional loading and complete control over the fire, which nobody else can do. They built this facility because of the urgent need to understand whole building response in fire, which necessitates the need to be able to test full scale with control over the structural fire severity and the imposed loading on the test building.
They’ve been doing a series of tests on composite floor systems – composite floors on steel beams on steel frames – and in the first test they used the very lightly reinforced composite slabs which are typical East Coast USA construction. The system was designed to achieve two hours of standard fire exposure, however it failed integrity at about 75 minutes due to severe slab cracking.
I recommended to them that they follow some of the design and detail requirements that we use in New Zealand slabs, and so in the next test they changed the slab detailing to what we do, with increased slab reinforcement, and that achieved twoand-a-half hours. They then turned the fire off and kept the applied load on while it cooled down, so we were able to show that just a change in the amount and positioning of the reinforcement in the slabs actually hugely improves the performance of the overall system.
In New Zealand, we’re significantly hamstrung by a lack of funding for fire engineering research. We haven’t had a severe fire in a multi-storey building that has led to the sort of damage that we’ve seen in some of these fires overseas. Since 2000, over 30% of the buildings overseas that have had severe fires have collapsed either partially or totally. If the same thing had happened here, then I’m sure there’d be no shortage of questions being asked and research money thrown in. Of course, it is much more preferable to develop a good understanding of building response to severe fires and appropriate design solutions before such a scenario happens
So, we do what we can with the funding that we’ve got. That’s where being part of this group at NIST is really helpful because it gives access to facilities and the ability to have some influence on what’s being tested in those facilities that we would never have been able to achieve in New Zealand.

Charles Clifton, University of Auckland Associate Professor