
18 minute read
Strike Process
“why”: selflessness and humility, lift each other up; focused on team success, can do, positive attitude. There’s a rhyme and reason for things we do here at Borrow. We have these processes so we can deliver the best service / product possible. The only way we can achieve this is to work together and give a smile even when things get crazy and days get longer. Better attitude leads to better customer relationships and better work days with your team. One negative person can put a group of people in a negative state of mind. Always be positive!
A. Shift Start Meeting
Advertisement
A. Shift Start (SS) Leader lays out plan for the day including all drops, pickups, warehouse tasks and lunch
B. Review debrief notes from Delivery Checklists from drops
B. Truck + Pre-Trip
A. Check Levels of Gas / Oil / DOA
B. Truck Inspection
A. Engine
B. Lift Gate
C. Underbelly
C. Open cab door and check truck has pickup items listed on Pickup Checklist for coordinating jobs for the day + cleaning / tool kit present.
D. Look Ahead to oncoming drop. Notes present? Floor plan uploaded?
A. Be sure to check delivery notes to use notes to make pickup smoother.
E. CALL AHEAD to client and record time under Project messages–Team messages Ex) Called Ahead
F. IF AT ANY TIME RUNNING LATE OR OUTSIDE OF DELIVERY WINDOW PLEASE CONTACT ON-CALL MGR
G. While driving, the Delivery Lead will review with Team members who will do what onsite.
C. Onsite Complete
A. Lead to Record time arrived under Project messages–Team messages Ex) Arrived for strike
B. Pickup
A. SILVERWARE + FLATWARE + SMALLS all complete quantities can be review back at shop however:
A. Check all creates full / no easily recognizable missing items.
B. Double check crate counts present on pickup checklist.
B. Furniture/Table cart Load and Unload process onto truck
A. When loading onto a dock that is the same height as the truck
B. Make sure truck is tight against the dock
C. Make sure there is room on the dock to wheel the carts onto
D. Unstrap cart
E. Wheel off cart
F. This can be done by one employee on flat ground
G. If there is any kind of incline/decline two employees must do this
H. When loading onto the ground
I. Make sure parking brake is on and liftgate power is on
J. Unloading onto the ground will always require two employees
K. Both employees will unstrap cart to make sure that it does not start to roll in case we are on uneven ground
L. Both employees will walk cart onto lift gate
M. One employee will make sure cart stays still while the other operates the lift gate
N. Lower lift gate
O. Both employees then wheel cart to a safe and stable location on the ground iii) If you notice an item is damaged or stained: Follow the DAMAGE PROCESS (listed above)
1) Take Pic(s)
2) Attach to Good Shuffle order
3) SLACK it under “damaged-items” channel
4) Unless it can be fixed and/or cleaned on-site, immediately call Logistics + Product Manager. If after hours, call On Call Manager (call Owner if no answer)
5) Set aside item in Good Shuffle through the Project
6) Logistics + Product Manager will create task in Insightly and assign to any FOH personnel with subject “ DAMAGED ITEM: _____________ (item name) with description and how it happened.
7) Operations + Production Director will schedule repair
D. Spot clean all inventory before packing up
E. Find onsite contact to get sign off on job and review any items found damaged or needing repair / cleaning.
F. Record Signature + Phone Number by downloading the file onto your phone in Chrome and having them sign
D. Post Strike while in truck
A. Record your departure time under Project messages–Team messages
A. Ex) Departing from strike
B. Record and debrief notes for the job that is useful for venue sheets to be updated.
A. Ie: Union workers slowed our install by 1 hour etc.
C. Look ahead to the next drop details. IF AT ANY TIME RUNNING LATE OR OUTSIDE OF DELIVERY WINDOW PLEASE CONTACT LOGISTICS + PRODUCT MANAGER or ON-CALL Manager
D. Double check all Onsite tasks complete + notate any misses in debrief notes.
E. Do Pre-Trip for next drop or strike if applicable.
Most Common Mistakes
1) Not calling ahead. If we do not call ahead, this can put the client in an uncomfortable position / not ready for us. Also, certain venues do not have people actually working inside. Often they have to send someone out to unlock the venue. If we don’t call until we get on-site, we run the risk of sitting there for a certain period of time waiting for the person to arrive.
2) Not communicating if you are running late and arriving past the arrival time on calendar. It’s very important that we communicate with FOH and clients to let them know about our status. We want to give the best customer service and never want the customer wondering where we are. Communication is key.
3) NOT COMMUNICATING
Unload/Restock Process
Labeled and “Unload / Restock” in Calendar. This is one of the key steps in ensuring our product is always in “like new” condition! When done efficiently it also enables us to handle and pull product that will not need work before going out.
A. Consult “DAMAGED” slack channel to check items being unloaded with damage.
B. *****IF AN ITEM IS DAMAGED, FOLLOW DAMAGE PROCESS LISTED EARLIER****
C. As items are unloaded off of truck double check + INSPECT + COUNT product + equipment
A. If furniture or equipment is not in “New” condition or can not be made “New” in under 20 mins: move to Clean / Repair and set aside item in Good Shuffle
A. Slack DAMAGED PROCESS
B. DISH- only slack Damaged Process if dishes returned un-rinsed or have debris, broken or missing.
B. Move all tables, chairs, bars and architectural items back to proper place in warehouse.
C. For upholstery or any other item regularly kept in showroom check next usage of product in Good Shuffle
A. Good Shuffle –> Item –> Search Item Name –> Usage –> Upcoming & In-Progress Projects
B. Used in 3 weeks: Place on shelves in warehouse w/ yellow label of next job + date.
D. CHECK OFF item in Good Shuffle Checklist once Complete + COUNTED
E. Process is COMPLETE when:
A. All items are in their proper position in warehouse and are cleaned and prepped “like new.”
B. Items unable to be restocked have notes associated and have been slacked in DAMAGED PROCESS
Per Diem Rates
To be granted for shifts longer than 10 hours and will be out of town. Per diem rates for the continental U.S. are set each year by the General Services Administration (GSA). For current fiscal year (which begins October 1, 2021), the standard rate is $59 for meals and incidentals and $96 for lodging.
Vehicle Training
“why”: lift each other up, focused on team success, Good Partners The safer you drive the truck, the safer you are, the safer our product(s) are, and the most likely we’ll complete orders with happy clients. This in turn makes everyone at Borrow look good along with vendors that we frequently work with. Being a smaller company, we strive on these relationships whether they’re clients, vendors or just anybody associated with events that we are a part of.
Log Book
Accident / Incident Form i) Review instructional walkthrough video (multiple times) ii) Perform minimum of 3 pre-trips with an instructor iii) Final Pre-Trip Test
All Operation Leads must be able to pass a 3 part test before they are allowed to operate a truck without TDM or Trainer.
A. Pre-Trip Test: a verbal test where the driver must complete a thorough check of the truck to make sure everything is functioning before you get behind the wheel (this includes checking fluid levels, leaks, tires, brakes, suspenders, gauges, lights, lift-gate and other parts of the truck). Once passed, you will move to the Basic Controls Test.
• Employee will perform a pre-trip and will be tested by instructor. This will be a “pass or fail” iv) If failed, the employee can redo the test 3 days later v) If passed, employee moves to “part B”
B. Basic Controls Test: evaluates your skill at controlling the truck while backing in / pulling out through different situations given to you. We will be testing your judgement to the truck’s position relative to other objects. Once passed, you will move to the Road Test. The 4 different parts are below:
Scoring
• Crossing boundaries (encroachments)
• Pull-ups
• Vehicle exits (looks)
• Final position
The examiner will score the following:
Encroachments: You will be scored with an encroachment error each time any portion of your vehicle touches or crosses over a backing exercise boundary. Each encroachment is scored as a two point error.
Pull-ups: When you stop and reverse direction to get a better position, it “may” be scored as a pull-up. You will not be penalized for initial pull-ups. However, each excessive pull-up will count as a one point error.
Looks: You are allowed to stop and exit the vehicle to check the position of the rear of your vehicle (look) during each exercise. You are allowed one look for the Straight Line backing exercise and no more than two looks each for the Offset to the Right and Alley Dock exercises.
When using a look, you must place the vehicle in neutral, or park if equipped with an automatic transmission and set the parking brake. When exiting and reentering a truck or tractor, you must do so safely by facing the vehicle and maintaining a three point of contact method with the vehicle at all times.
When exiting and reentering a bus, maintain a firm grasp on the entryway handrail at all times. If you do not safely secure the vehicle, or if you exit the vehicle in an unsafe manner, you may be disqualified.
Final position: It is important that you finish each exercise exactly as the examiner has instructed. If you do not fully place the rear of your vehicle into the final docking boundary or the front and back of your vehicle is not relatively straight as described by the examiner, you will be penalized 10 points and could disqualify on the backing exercises.
You must have a passing score of 12 points or less as a combined score for all three backing exercises. If more than 12 points/errors are scored, the test will be stopped and you will not pass the Basic Control Test.
i) Straight-Line Backing
You will be instructed to back your vehicle in a straight line between two rows of cones without touching or crossing over the exercise course marked by cones. If you encroach on or through any cones the examiner will stop you and you must return back into bounds.
Set your parking brake and tap the horn when you have completed the exercise.
If the back of your vehicle is not within the final docking boundary, you have not successfully completed the exercise and a position error will be scored.
ii) Offset Backing (to the right)
You will drive straight forward and then back your vehicle into the lane to the right, without touching or crossing over the exercise course marked by cones. The examiner will stop you and instruct you to return back into bounds if you encroach on or through any cones.
If a pull-up is needed, you must first back so that the entire rear of your vehicle crosses over the exercise’s center boundary line (middle cone between both lanes) before a pull-up is allowed. Set your parking brake and tap the horn when you have completed the exercise. After completing the exercise, your entire vehicle must be relatively straight.
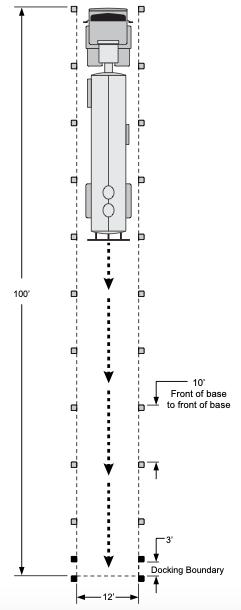
If the back of your vehicle is not within the final docking boundary or the front of your vehicle is positioned to the left or right (in front of the row of cones) of the backing lane, you have not successfully completed the exercise and a position error will be scored. See Figure 12-2 at the end of this section, for examples of the center line the vehicle must cross before making a pull-up and where the vehicle should be positioned after completing this exercise.
iii) Parallel Parking
You may be asked to park in a parallel parking space that is on your right. You are to drive past the entrance to the parallel parking space with your vehicle parallel to the parking area; and back into the space without crossing front, side or rear boundaries marked by cones. You are required to get your entire vehicle completely into the space.
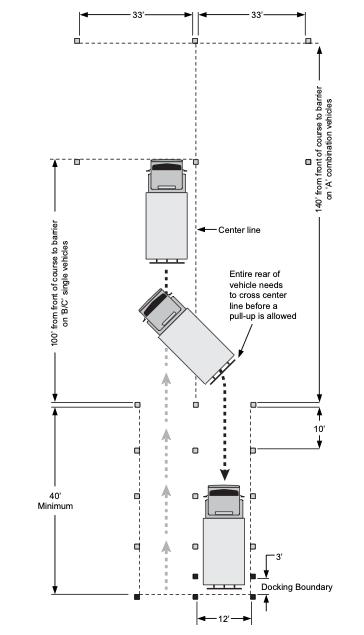
iv) Alley Dock Parking
You will be instructed to set your vehicle up at a 90 degree angle and back your vehicle (sight side) into an alley dock. You must put the back of your vehicle inside the final docking boundary. The examiner will stop you and instruct you to return back into bounds if you encroach on or through any cones.
After completing this exercise, set your parking brake and tap the horn. Your entire vehicle must be relatively straight.
If the back of your vehicle is not within the final docking boundary or the front of your vehicle is positioned to the left or right (in front of the row of cones) of the backing lane, you have not successfully completed the exercise and a position error will be scored.
Grounds for Automatic Disqualification
You will be automatically disqualified for any of the following:
Dangerous action:
• Anytime the examiner has to intervene and stop you from striking any fixed object.
• Applies to other dangerous situations while positioning the vehicle or completing the backing exercises.
• When you fail to put the vehicle in neutral/park and set the vehicle’s parking brake, before exiting the vehicle to perform a “look.”
• Repeated instances of exiting the vehicle in an unsafe manner while performing a “look.”
Accident:
• An accident, even if it’s minor. This includes contact with any fixed object.
- Striking exercise boundary cones is not scored as an accident.
Failure to perform:
• When you cannot comprehend or respond to instructions given during any part of the Basic Control Test.

• Applies to the inability to perform any of the backing exercises.
C. Road Test: using the first 2 tests and doing a real life scenario with a Borrow delivery / drop to a venue or personal residence. Starting off the day with a pretrip and heading to the delivery or pickup. If the tester feels that the driver safely operated the vehicle, he or she will have full reigns of the truck without supervision. Please note that this may take a few shifts to complete this portion of the test.
Qualified Drivers
For employees driving the Borrow truck, he or she must always have a spotter when backing out or in at venues or any tight places. The truck has a box that is 26 feet long and it is way longer than you think when you look through the side mirrors. The truck under NO CIRCUMSTANCES can go under a bridge that is under 13’ 2” high. An employee is to never drive down MLK here in Cleveland. Avoid driving anywhere near MLK Jr. Drive or in the city of Euclid. There are several old bridges that will not be high enough for our truck. If a driver comes to a bridge that doesn’t state the height but looks low, they must put their hazards on and have another team member jump out and be their spotter as they inch to the bridge. If in doubt, turnaround and find another route. If a driver goes under a bridge and damages the truck in doing so, he or she will be responsible along with the team member who is not driving. Each team member needs to ensure Borrow property is the safest hands as possible. Drivers must be aware of other low hanging things other than bridges. Low hanging tree branches and wires are common in residential areas so each driver needs to be aware of not only what’s on the road but what’s above it as well.
All drivers are required to turn off the breaker for the appropriate dock door they are parking in at Borrow HQ. The dock doors in our current home base are known to close at times whether or not a vehicle appears to be blocking the signal. To ensure the safety of all Borrow team members, vehicles, and other pedestrians ALL drivers must exit their vehicle immediately upon safely parking and turn the appropriate breaker off. If you are a spotter that is opening a dock door for a fellow driver you must turn off the breaker for the appropriate door as soon as the door is fully open. Any team member that fails to secure a dock door is subject to disciplinary action up to and including termination.
Failure to follow these policies can result in serious injury or death to you or to others and is a very serious matter. If you do not follow these rules and are in or cause an accident or damage to Borrow LLC property, you may be subject to disciplinary action up to and including termination of employment.
Borrow Dock Test
Most Common Mistakes
1) Underestimating the truck length when backing up. Safety is priority #1 and we must always use a spotter and be smart. If you are by yourself, you must get out at least once, and can get out multiple times to ensure the truck and more importantly yourself are not at risk.
2) Taking sharp turns. The truck is very long so you must always take wide turns (especially at intersections). If you cut a turn, you run the risk of hitting the curb and damaging tires along with shaking inventory in the truck.
3) Not ensuring the dock door power supply is turned off when parked in a “Home” dock. All dock doors must have the breaker switch turned to “off” position immediately when parking in a dock at Borrow HQ.
Workshop
Borrow Builds / Upholstery Process
“why”: creativity + can do, positive attitude. Borrow is a place where ideas are encouraged no matter what position you hold here. When it comes to Borrow Builds, there are so many projects that can be used for an event and in turn, benefit Borrow. Each project can hold a certain amount of speed bumps so it’s always important to communicate with the team and always look for solutions / efficiencies.
A. Creative Submission or Damaged Item submitted via slack. Creative Director either approves for work order or shelves for future or denies.
A. Unless Damaged by Borrow than Proceed to B.
B. If approved for Work Order CD slacks too FOH to start process. FOH creates a “Project" for the item with appropriate pipeline.
A. Project to be created by Ops Director if “Borrow Project”
C. Operations + Production Director Creates a Work Order and attaches to the Project with a task for Creative Director to check.
A. If this is a “repair” or “maintenance item” or Pre-Approved project no approval needed and skip to step E.
D. Submission is approved by Creative Director or Operations + Production Director in which case said person communicates via slack and updates the Insightly Pipeline.
A. If not approved Creative Director to delete pipeline.
E. Product Development Lead, Build Team Lead, Lead Upholsterer or Operations + Production Director i) Print 2 copies of work order (1 just by itself and the other with time sheet + QC attached) ii) Put both copies Operations + Production Director’s office iii) Add to Google Doc
F. Operations + Production Director i) Orders all necessary materials and marks off ordered on WO.. ii) Once materials are received WO notated on WO. i) All labor is scheduled on Apple calendar and Microsoft To Do two weeks ahead. iii) Hangs copy with time sheet and quality check of Work Order on Workshop and/or Upholstery whiteboard iv) Moves single sheet work order to “In Progress” on cork board.
G. Build Team Lead / Product Development Lead / Lead Upholsterer i) Follows sketch / plans to the exact dimensions and details desired
• All days / times worked on project along with details of task(s) gets recorded ii) If there’s any idea about a change in the sketch whatsoever:
• Stop what you’re doing + submit an updated sketch on Creative Submissions Slack channel — be as detailed as possible
• Wait to hear back on approval or not
- If time sensitive, giveCreative Director and/or Operations + Production Director a call iii) IF STAINING or a certain look in the wood is desired, Approval must be gotten by Creative Director Before moving on — submit pictures via Slack on “Creative Submissions” channel under specific Creative Submission post.
- Move to work needs reassessed on cork board if there is a delay.
• Once we poly, it is extremely difficult to undo staining. Too much labor, time, and materials will be wasted if we need to make changes
• Once approved, keep the project moving
- Again, if time sensitive, give Owner and/or Operations + Production Director a call iv) There should be constant updates communicated with Creative Director + Ops Director between stages of projects (i.e., construction, sanding, staining, painting)
• This helps FOH be aware of progress + it will give more eyes on the project just in case something is not completed the right way or if the final look won’t be exactly what we had in mind. It is easier to fix this between stages rather than undoing after we complete it. v) Once the build is complete + timing is all recorded: a. Ops Director puts work order on Borrow Builds Board “Quality Check” b. Move project to a corral for inspection / quality check a. Borrow builds items to go in Builds Overflow b. Borrow Upholstery to go in Upholstery Overflow
H. Operations + Production Director i) Schedule a task + SLACK message to Creative Director for quality check.
I. Creative Director i) Will quality check the piece + decide if it’s approved or if more work needs to be done on it ii) If additional work needs to be done, it’s hung back up on workshop whiteboard with all necessary work that needs to be complete (go to step “G”) iii) If approved, Creative Director will:
1) Update timing, work order (attaching in Insightly), and Good Shuffle
2) Put work order in Operations + Production Director office
• SKIP STEP “J”
J. Build Team Lead / Product Development Lead / Lead Upholsterer i) Move upstairs to photo / new inventory area on 4th floor
Work Order Completing
A. The Pieces of Parts of a Work Order i) Quality Check Date: 2 weeks prior to delivery date for rentals or retail or equipment needed for such. ii) Quality Check Date: Inside Creative Projects - to be determined based on event and client schedule.
• Reference Google Doc iii) Blank Space for Inspire Pic iv) Hour estimates.
• Use prior work orders, ask and google time estimates with a wide range.
- Best Case: Be Aggressive v) Labor
- Worst Case: Novice timing.
• Break Down per step / department.
• Fill in estimate of hours based on prior work orders or google research.
• Standard Labor Rate: $16 vi) Materials
• The name of products and where we purchase from. Make sure to include as much info on the material as possible. - Pricing through Amazon or Hardware Store
B. Terms of Service: brief description of what we’re doing.
C. Description of Project: use dimensions when applicable.
D. Blank Space at Bottom
E. Include all dimensions / measurements / sketch / All Build / Upholstery Cuts Listed.
• If need additional space attach a separate sheet.
Most Common Mistakes
1) Staining process is rushed. This is very common because you would like to stain a piece and then apply finish to it. Remember we need to always go through the steps for approval and make sure it is the exact look we want. Once we apply the finish, we cannot undo and this will add more work than what we originally planned.
2) Incorporating new idea / diverting from original sketch. Improvements and ideas are encouraged but we must follow the protocol rather than “assuming” we will go with the idea. Money and the “look” are factors when we do the sketch so we must keep this in mind and never rush. Always “SLOW DOWN” and communicate ideas to ensure the team succeeds.
3) Moving new project upstairs to photo area before Quality Check.
“Inspection” is part of the Borrow Square and it’s important that we follow the process we have in play. There must be a final Quality Check before we move complete Build upstairs. It’s exciting to finish a project but if we move it upstairs and there’s a flaw, we’ll need to bring it back downstairs to correct it.
Equipment
*Review videos linked for all below (click on the name of the tool for video)
B. Drill
C. Impact Drill
D. Pocket Holes
Saws
E. Orbital Saw
F. Miter Saw
G. Jig Saw
H. Table Saw
Power Tools
I. Dremel
J. Grinder
Air Compressor
A. Air nossel
B. Pneumatic nail gun
Sanding
A. Orbital sander
B. Hand sanding
Planing
C. Hand Planing
D. Stationary Planer
Finishes
A. Staining (3 different pieces)
B. Poly (3 different pieces)–water based, oil based
C. Danish/Tung Oil Application
D. Tack Cloth
Painting
A. Latex (painting walls)
B. Oil-based paint (on inventory)
C. Paintbrush Maintenance
Fire/Safety for paint + oil rags
A. Never leave flammable materials out. Keep them in the fire safe cabinet when not in use. This includes paints and used rags
B. Borrow burnt down in 2019 due to a rag being left out.
Wood Glue Ups (planks)
Judith Sofa Construction (1st test project)
Safety
A.
TRAINER
Job Role Expectations BOH
What makes a great……..
Warehouse Lead
• Understands the importance of setting up delivery crews for success.
• Positive + Energetic
• Ready to take on the job responsibilities of Warehouse Lead
• Is a checklist maniac and obsessed with the details.
• Has a “figure it out mentality.”
• Never leaves prep half way done.
Delivery Lead
• The safety of his team is his #1 priority
• Never forgets to call ahead
• Is polite and friendly with all clients
• Is a documentation stickler and never forgets notes
• Strategizes better equipment and takes the initiative to talk to Mgmt
Borrow Builds
• Safety + Systems stickler
• Not afraid to keep MGMT accountable on timelines
• Thinks and plans ahead
Team Member