
7 minute read
Mining at a Critical Turning Point
from Future Auto NT 2024
by Boylen
The growth of zero and low emission vehicles in Australian mining is gathering pace.
As long-standing contracts expire, adoption of the new technology is starting to accelerate, with Normet forecasting its EV sales to increase from 10 per cent to 50 per cent in the next five years.
Part of the impetus is the need for mining companies to prove their environmental, social and governance (ESG) credentials. Major finance firms are increasingly refusing to invest client funds in miners with a poor environmental record.
At an individual level, the reduced emissions, heat and noise are being wholeheartedly welcomed by underground miners. However, most mines still have a heavy reliance on diesel and it takes considerable time to upgrade infrastructure to suit battery-powered equipment.
Normet
Finnish company Normet has been offering mining and tunnelling solutions, including concrete spraying, transporting and explosive charger machines, since 1962.
In 2015, it began research and development of SmartDrive, the modular battery electric vehicles it builds from scratch, using Polish battery supplier Impact Clean Power Technology.
By 2019, it had built and sold its first SmartDrive into Australia.
Eight of those vehicles, comprising about 10 per cent of Normet’s annual output, are currently operating in Australia in the Tanami Desert, the Northern Goldfields Region and in South Australia at the Carrapateena Mine and Prominent Hill.
There are another eight hybrid machines at Olympic Dam.
Hybrid units use a diesel engine to power a generator, significantly reducing CO2 emissions when under full load, operating at low rpm ranges, down from a typical diesel engine at 2700 rpm.
The balance of Normet’s sales remain dieselpowered vehicles.
Brendan Percy, National Technical Manager at Normet Asia Pacific’s Adelaide office, sees a strong future. He predicts the sales of battery electric equipment to be as high as 40 per cent within three years and hit 50 per cent within five.
Mine upgrades
There are several factors putting the brakes on the sector’s ability to dump diesel for batteries.
“People say the biggest hurdle is how fast we can develop them, build them, get them into production and get them to the mine,” Brendan said.
But that tells only part of the story.
“Most mines have not been designed to handle this amount of electrification,” he said.
“Every mine has a grid system set up for its expected power requirements for its production life.
“If the mine is 10 years old, it wasn’t set up to plug in 40 machines a day to load the grid for things like the trucks and loaders.
“You might have a 60-tonne truck that’s running on diesel. When you move to an electric model, the density of the energy storage you need on those batteries is huge because they are running such high weights.
“So an older mine that hasn’t been planning for this, if they were to plug in every charger that they needed at the same time to charge their batteries, they’d probably overload the grid and they wouldn’t be able to operate.
“The phase we see at the moment is where there are upgrades to the mines themselves for their grid structure to accommodate the extra requirement for charging these batteries.
“The appetite is there. It’s how fast mine owners and then the subcontractors can accommodate the change in technology.”
Equipment contracts
Long-standing agreements between mining companies and subcontractors also have to expire before change can be implemented.
“It very much relies on where contracts are at as well.
“If a mining company runs a five or seven-year contract with their subcontractors, they have only got that ability to make that change of request for the type of machine at the end of the contract.
“It’ll be a slow creep.
“The sector says we want to do everything now but the reality is they need to stage this because they need to make changes to the structure of the mine sites and supply chains need to ramp up to facilitate this.
“They can’t just switch diesel off straight away because they have to set up the electrical infrastructure of the mines themselves.”
Big players
The pressure to make positive change, Brendan said, is coming from the very top of the industry.
“The big mining houses are predominantly the drivers of BEV/hybrid supply.
“The majority of our sales are actually the subcontractors but the mining houses are the ones putting the big pressure on and a lot of that is driven by shareholders.
“These companies want to be at the front for the change.”
That pressure also trickles all the way to the bottom, more than a kilometre below the earth’s surface where some miners find themselves as old dogs learning new tricks.
Normet’s SmartDrive machines, including its explosive chargers and shotcrete, can be plugged into a 1000AC grid while they operate or connect to any fast chargers with CCS charging communication standard and CCS2 fast charging plugs, including Normet’s own 40, 160 or 320 kW chargers.
Their batteries can also be recharged via regenerative braking as the vehicle travels back underground.
But recharging below ground may still be necessary if the vehicle needs to return to the surface.
“The expectation is that you get a full shift out of a tank of fuel.
“BEV’s will do that with opportune charging during the shift. But if they have to then get it out of the portal and take it to the surface, they would have to stop for a bit of a charge.
“These trucks are quieter, generate less heat and the underground air is cleaner.
“Once they see the positive benefit of that, we generally get operators on board pretty quickly.”
MTA assistance
While the MTA does not offer training in the NT, some businesses have elected to send technicians to Adelaide for training. Regardless, the following points provide an insight into how some members are solving their challenges.
“In the past, where you had a mechanical fitter and an auto electrician, now you need a 1000V qualified or licensed electrician as well for isolation procedures onsite.
“So there are implications on training and skillsets.
“With every customer we’ve delivered a BEV too, the first thing we do is get them to the MTA’s training course, and then we do our own gap training after that.
“There’s a fair skillset change that the MTA is helping.”
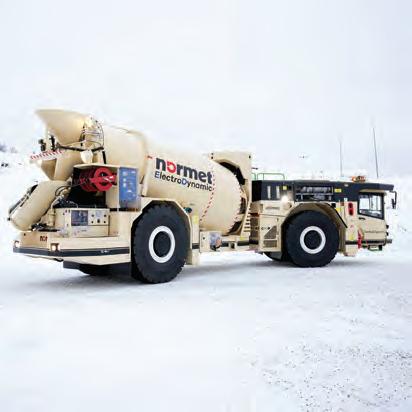
“We place a charger halfway along that journey so they can pull up, connect the fast charger, get a really quick 20 minutes and that gets them out to the surface.”
Training, noise & heat
Normet deploys one of its own to spend the first week of every machine’s life on any new site, retraining drivers.
“The lack of requirement for fuelling is great but it brings its own challenges to the operation because operators have to learn how to correctly charge the machine,” Brendan said.
“There’s some extra training involved with that, as well as how to drive and maintain it.
The MTA’s training model is geared heavily toward safety and it is an absolute priority for Normet.
“MTA is also introducing some of our training materials on Normet specific systems.”
“When assessing the introduction of BEV’s/HEV’s into a new customer’s system and site, one of the first areas we advise on is skills upgrade, including specific training avenues both external and internal to our business.
“We also explain and assess the differences in cell chemistry between those batteries and our current battery technology, which is lithium titanate oxide (LTO).
“The battery strings are closely monitored by a management system to ensure that any issue is identified in the individual cell voltage and temperature.
“There’s a fire suppression system and multiple layer control systems with complex cooling systems that automatically shut machines down.”
The benefits clearly outweigh the risks, and with miners continuing to operate under stringent licencing and investor scrutiny, it will come as no surprise to see the further electrification of mines around the globe.