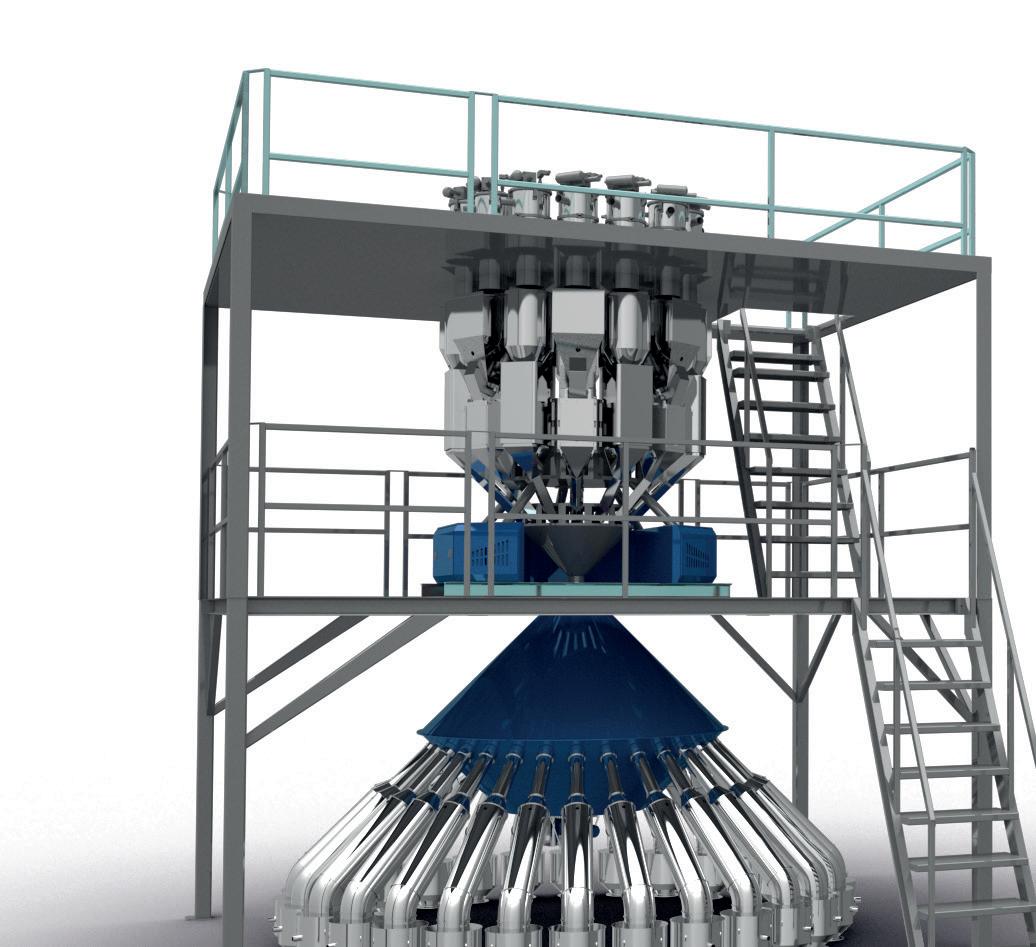
1 minute read
How central blending systems can cut the cost of using recycled plastics
from BP&R Jan/Feb 23
There’s never been more interest in incorporating recycled plastic into finished products, with taxes and incentives cropping up in countries around the world. Here, the team at ancilliaries expert Jenco argue that centralised blending could make the material easier to process.
batch blending systems, this is a significant challenge that requires adjusting the recipes for each of the systems in the factory.
Local batch blending systems limit recipe adaptation
Local batch blending systems generally are limited in terms of how many types of raw material can be used. This creates challenges when working with recycled plastics.
Some recycled plastics are of a higher grade and some are of a lower grade – and the lower grade plastics are less expensive. Therefore, sometimes it may be beneficial to create a mixture that includes several recycled materials of different grades.
However, this frequently is not an option supported by the machinery due to the limited number of raw material options supported by local batch blending systems.
In addition, local batch blending systems require the same recipe used for all production machines serviced by each of the blending systems. It’s not possible to define different recipes for the different products.
Centralised blending systems offer greater flexibility and efficiency that eliminate many of the problems that come up, when integrated recycled plastics in production.
Using centralised batch blending, manufacturers can make better use of recycled plastics – thereby cutting down on production costs, and improving the bottom line.
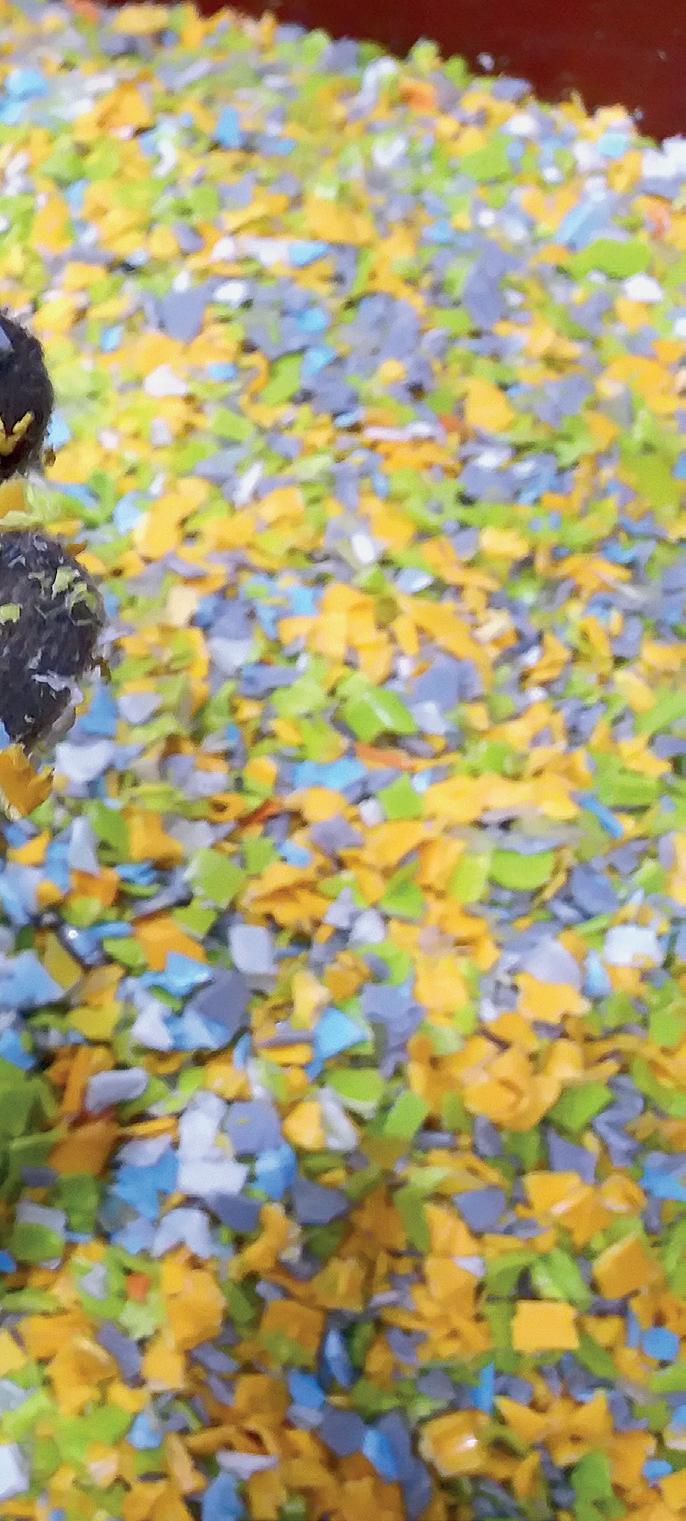