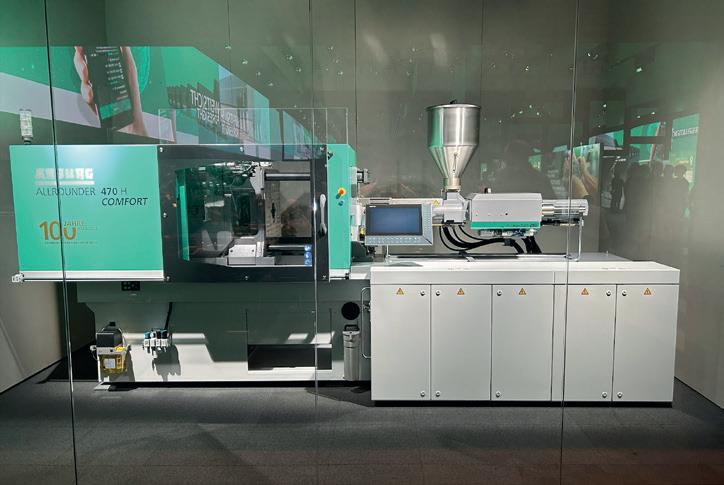
1 minute read
INJECTION MOULDING
from BP&R Mar 23
This machine is around 2.5 times larger than that of the Freeformer 300-3X –with the same external dimensions. The company also points out that this means that ‘The process is also faster and more economical. In addition, the Gestica control system has been optimised for additive manufacturing in terms of process stability, part quality and build time.’
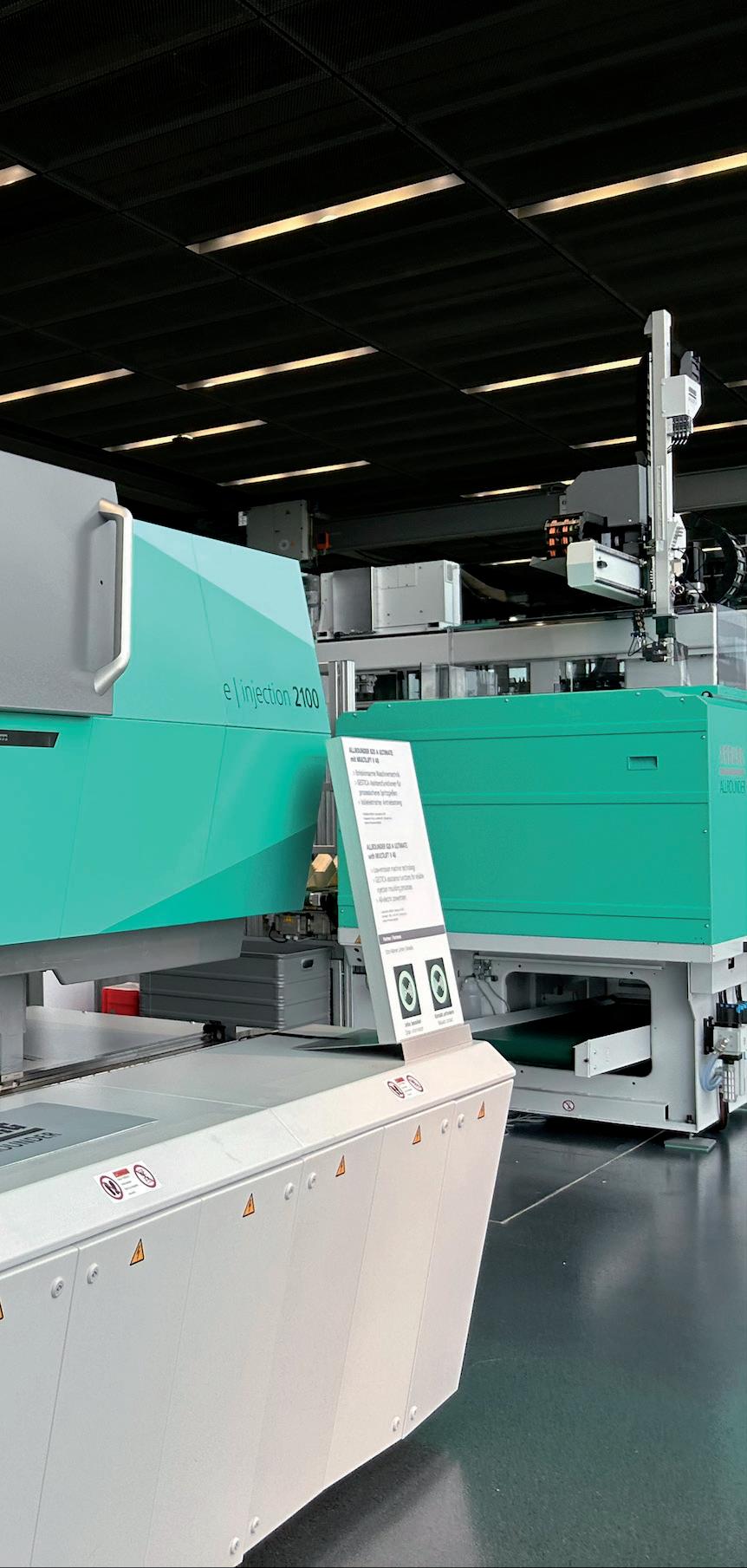
The Freeformer 300-3X in a hightemperature version was also on display along with the Freeformer 200-3X ‘soft’ which allows for 3D printing with softer materials. Arburg also displayed its TIQ and LIQ machines which allow for the processing and 3D printing of processing filaments and silicone.
Arburg also spent a considerable amount of time delving into some of the digital solutions that are underpinning the company’s strategy moving forward. This includes the manufacturing execution system (MES). This system along with the company’s centralised computer system, the ALS, allows for an interlinking network. According to the company: “The Arburg host computer system ALS is a central element with which the entire plastic parts production can be digitally planned, controlled and all relevant information can be tracked. A typical injection moulding plant running 20 machines can save approximately 1,500 hours of working time and 500 machine hours per year using the ALS.”
To compliment this feature Arburg has introduced the ‘Gestica control system’s intelligent assistance’ to its machines a piece of technology which the company believes will allow for those with less training to operate machinery. According to Arburg: “In times of junior staff shortage, this is particularty interesting. The starting point for the use of the recyclate package is the “aXw Control ScrewPilot”, which compensates for malfunctions in the filling process and keeps the mould filling stable. The new “aXw Control RecyclatePilot” ensures a stable shot weight by means of adaptive process control, while the “aXw Control PressurePilot” ensures bionically optimised pressure control.”
Streamrunner ® Multicolour
Multi-component injection moulding reaches a new level
The Streamrunner is an additively manufactured hot runner with maximum design freedom. Through the free three-dimensional design of the runners, completely new possibilities are created in multi-component injection moulding.

New possibilities for product designers Distribution of different plastic components or colours over a very small area Channels can be intertwined with each other

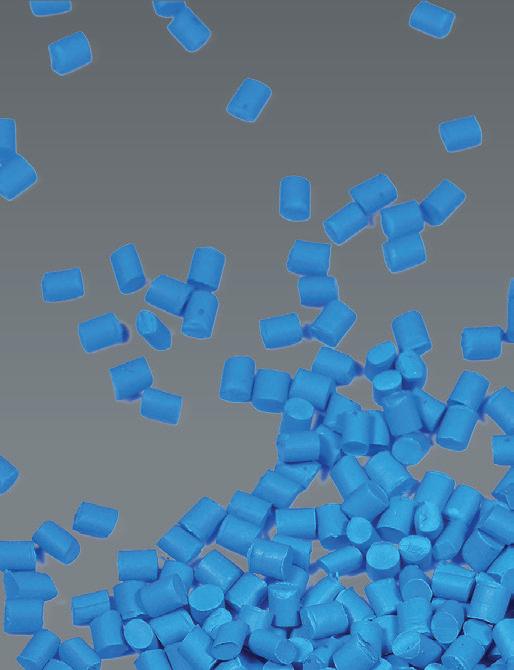