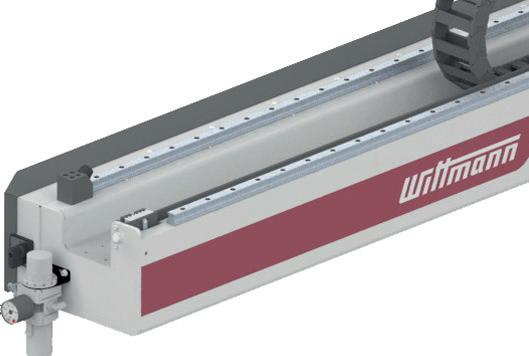
3 minute read
WITTMANN TO BRING automation launch to Interplas
from BP&R May/Jun 23
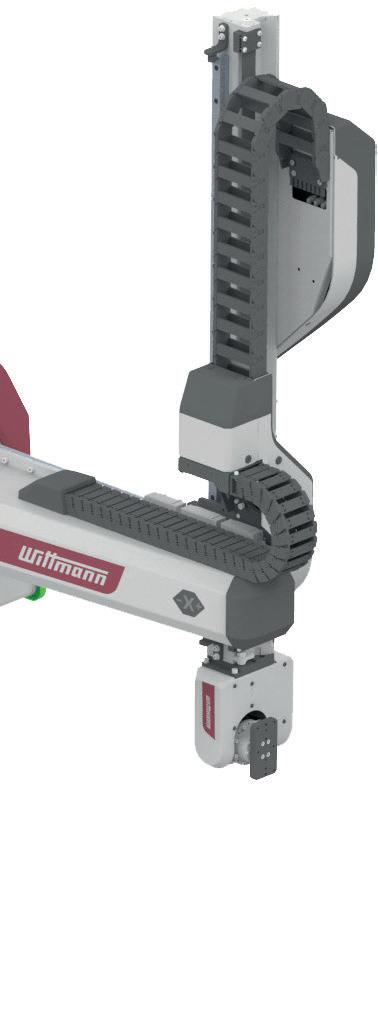
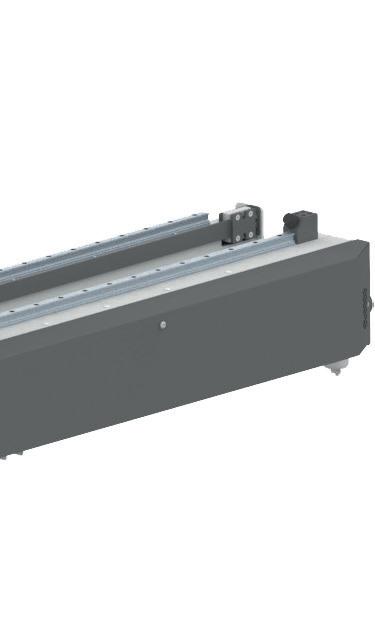
Wittmann says it owes its beginnings to a successful automation strategy – created specifically for “real life” moulder needs. At K 2022, the group presented the Sonic 143 “chess robot”, a robot palletising solution and unveiled the radical new design of the WX128 robot – a versatile and compact system that is now set to take over from the W818/W918 series.
The WX128 benefits from the technology developed for the group’s larger WX138 - already available in today’s market. The new robot features a newly developed compact control cabinet on the horizontal Z axisshortened by 30%.
This is useful for small injection moulding machines, as it makes for a compact protective housing, achieved by positioning the drive unit and connection cables on the inside.
The Wittmann WX128 relies on a belt drive concept on all linear main axes. Wittmann says the result is a high level of dynamism. The vertical axis can accelerate at roughly four times the gravitational acceleration rate. The predecessor model of the WX128 was equipped with an external rack on the demoulding X axis.
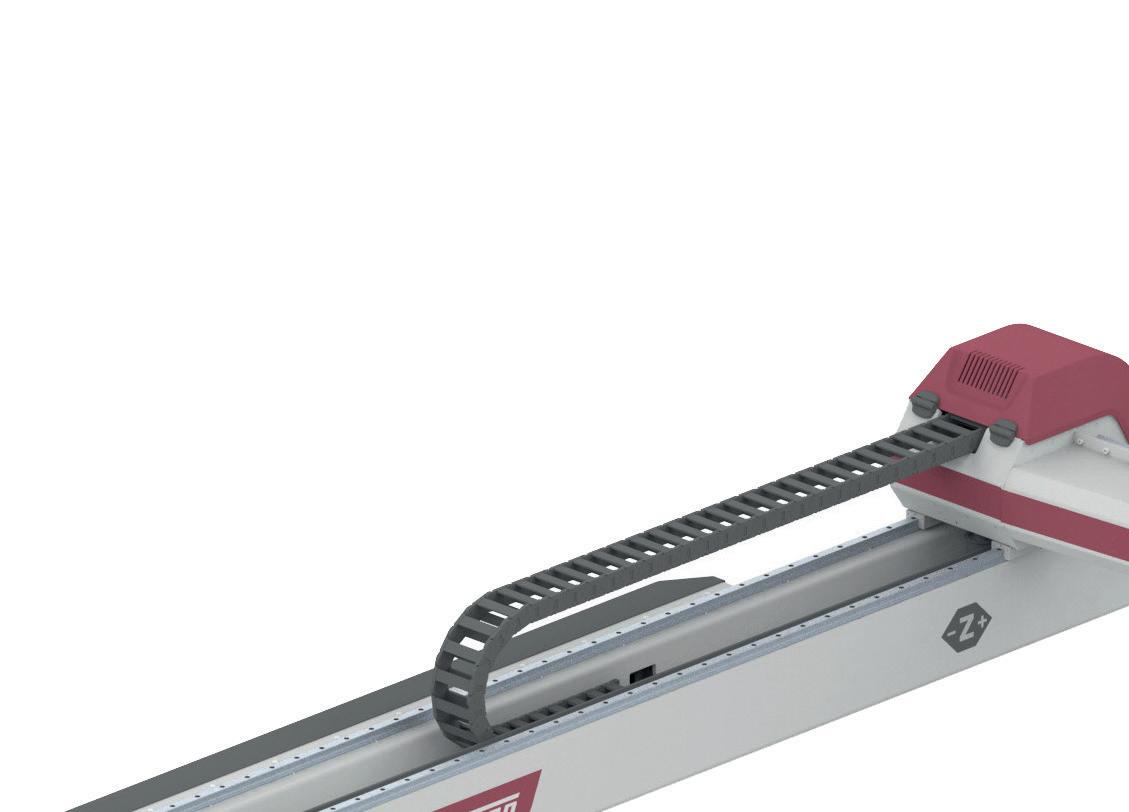
Despite the colour and livery changes, last year’s K 2022 trade exhibition proved successful for the Wittmann Group – not least in terms of its offerings in robotic solutions for injection moulders. The group will bring its latest launch to Interplas 2023.
The WX128 was designed to create an easily accessible, compact and low-maintenance design – and future proofing it with flexible upgradeability. As to equip the WX128 with up to two additional rotational servo axes. This extension can be implemented either at the time of purchase, or as a retrofit later on without having to make any alterations to the control cabinet. At K 2022, Wittmann presented the WX128 robot with an A-C servo axis equipped with an illuminated gripper.
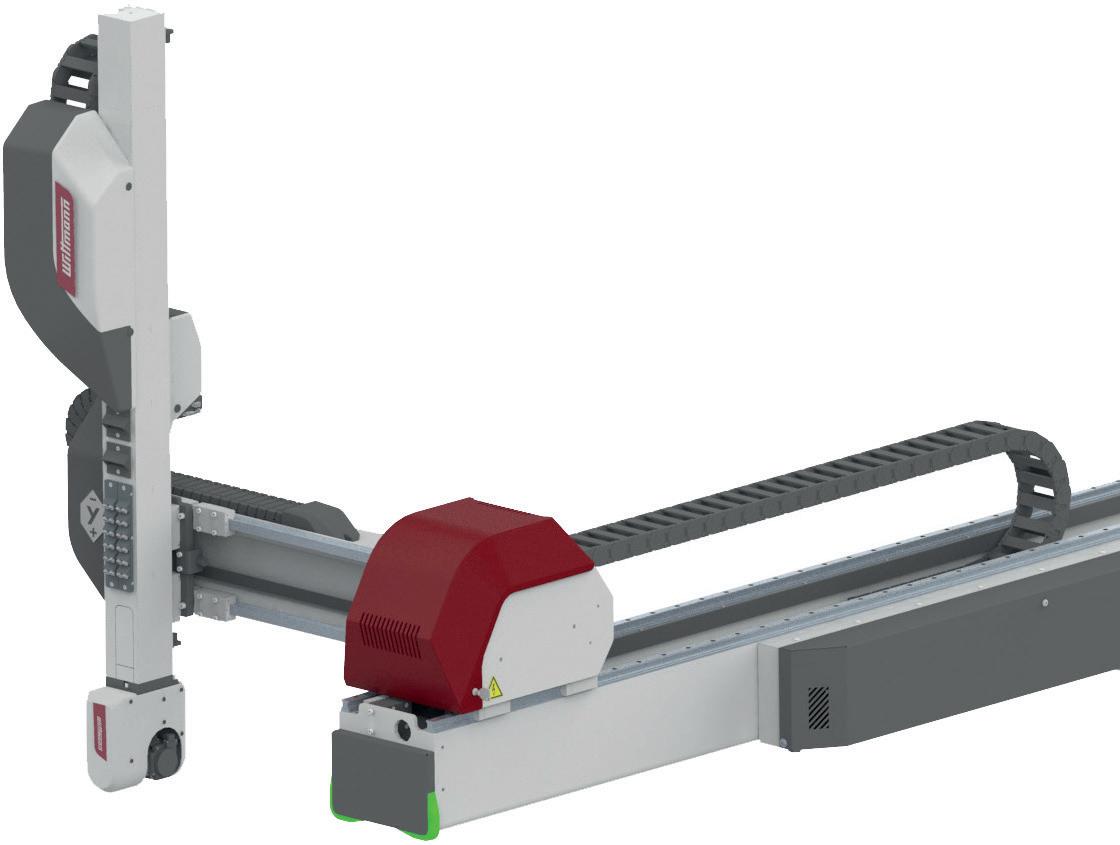
The new WX128 features a nominal load capacity of 6 kg, offered exclusively with the current Wittmann R9 control system.
At Interplas 2023, visitors to the Wittmann Battenfeld UK stand – its biggest space yet –will be able to see the WX128, as well as Wittmann’s various other automation solutions. Wittmann Battenfeld UK joint managing director, Dan Williams said: “We are happy challenging any moulder to witness how Wittmann robotics and automation can instantly improve a business –including operations, energy saving, reliability and price/ performance. It’s not a cliché – Wittmann has an automation solution for every moulder. Our robots can be fitted on any machine, regardless of age, make or size.”
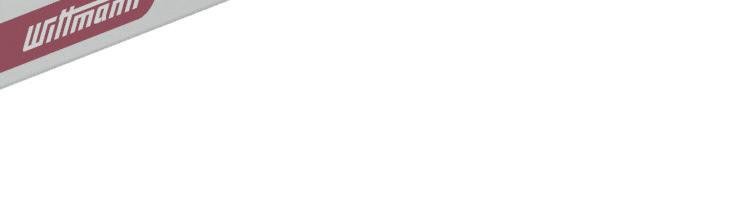
Tracy Cadman, joint MD added: “We encourage all in UK injection moulding to use the Interplas forum to make a date with us. Robotics and automation already play a key role in many mouldshops across the industry and Wittmann has been in the vanguard of this movement for decades. The exhibition always provides a convivial atmosphere and many opportunities for networking, learning and profiting.”
Williams added that connectivity and automation in injection moulding is only set to increase further as manufacturers take on more and more complex and challenging technical projects: “Relying on Wittmann repeatability and control will give any moulder complete peace of mind throughout the whole project process. I warmly encourage you to visit us at Interplas and see for yourself how we can support you from a simple pick and place solution to a fully automated multi-insert moulding application with full camera measurement and downstream automation.”
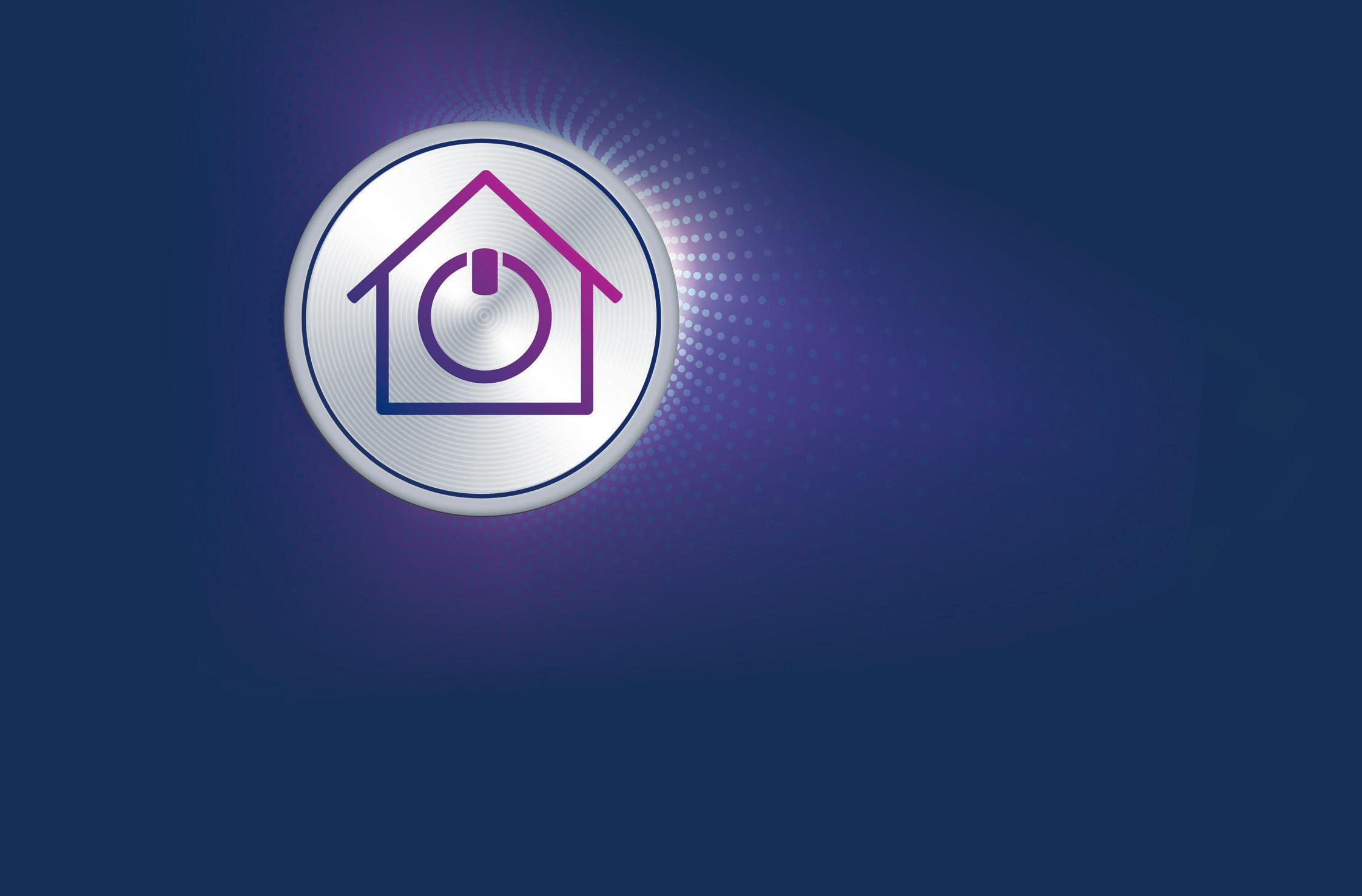
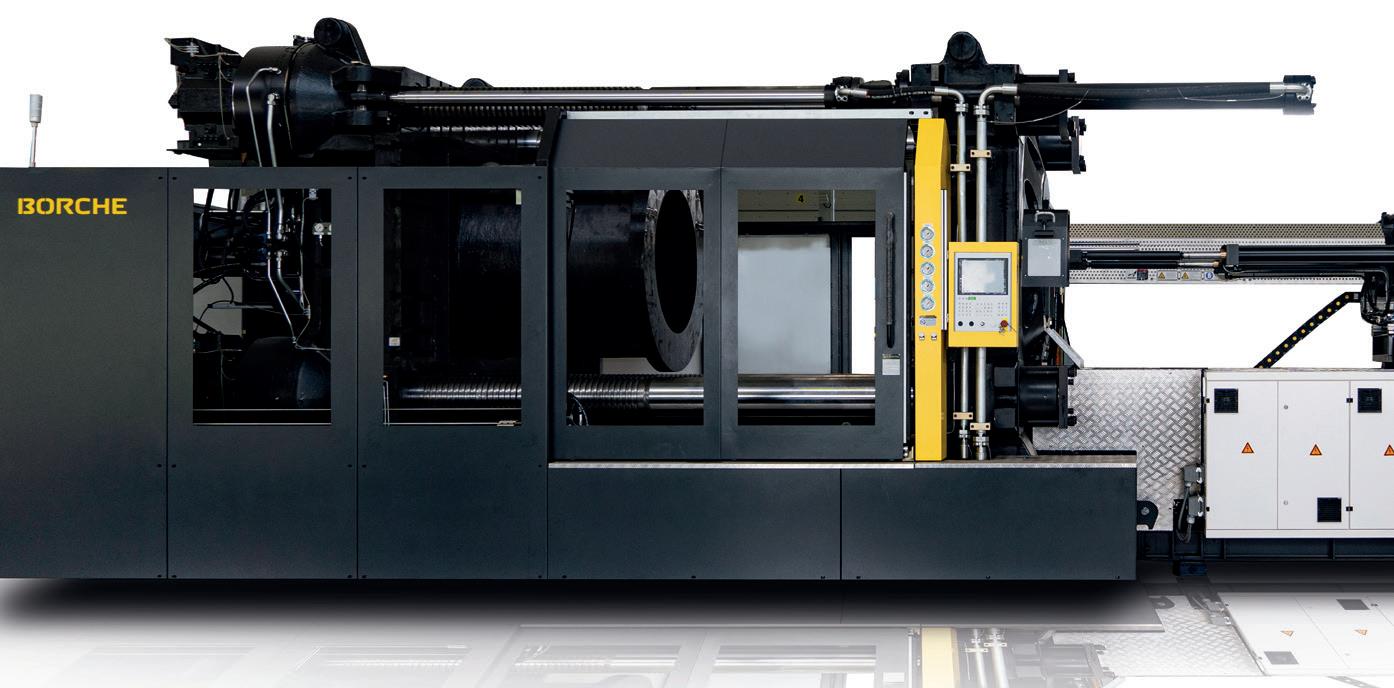
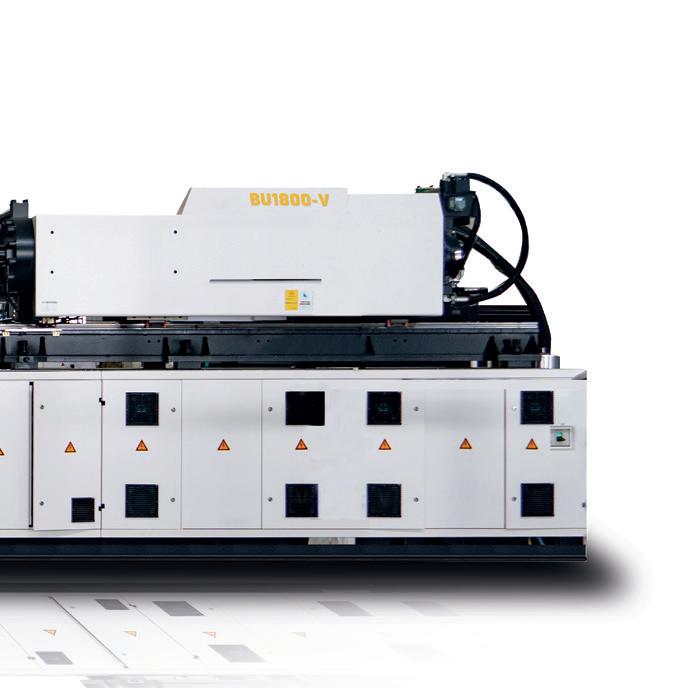

Need to invest in Injection Moulding equipment, but concerned about the impact of the electricity crisis?
BOLE Injection Moulding Machines incorporate the latest Servo Motor technology and patented designs to help reduce your exposure to an ever-changing market.
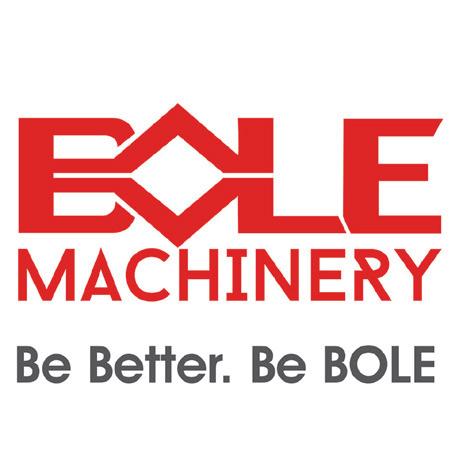
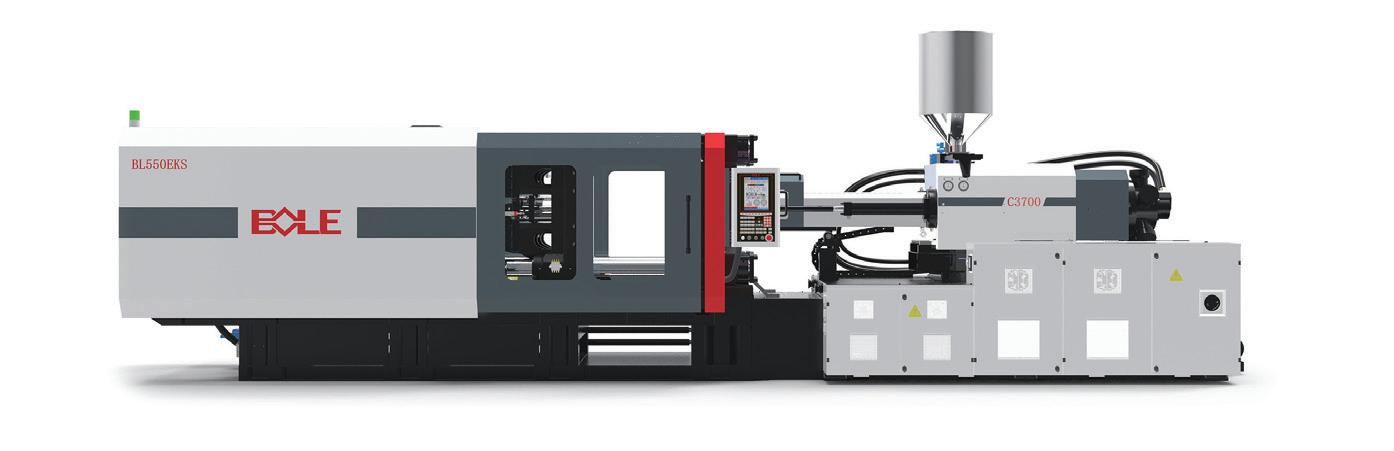
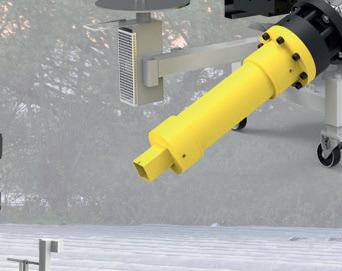
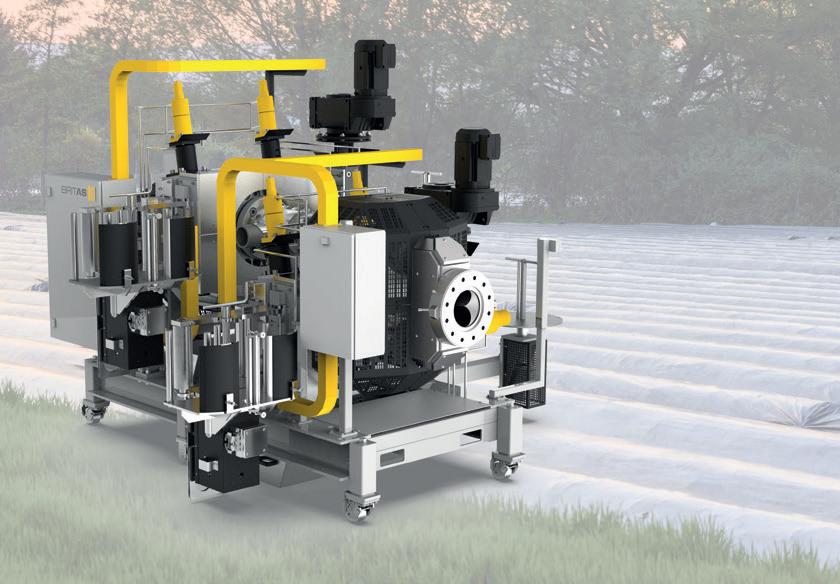
Worried about delivery times? Don’t be.
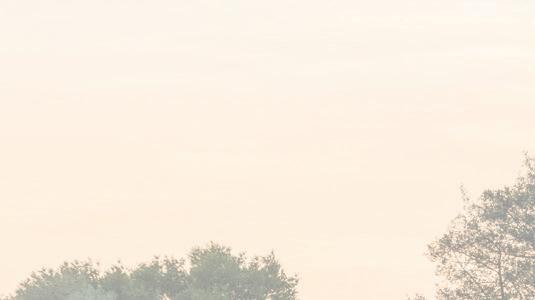
We have stock of machines between 50t – 1000t from our EKS, FE and DK ranges which are backed up by our team of in house engineers and a 3 YEAR WARRANTY on non-consumable mechanical parts that can be delivered within 5 days from order.
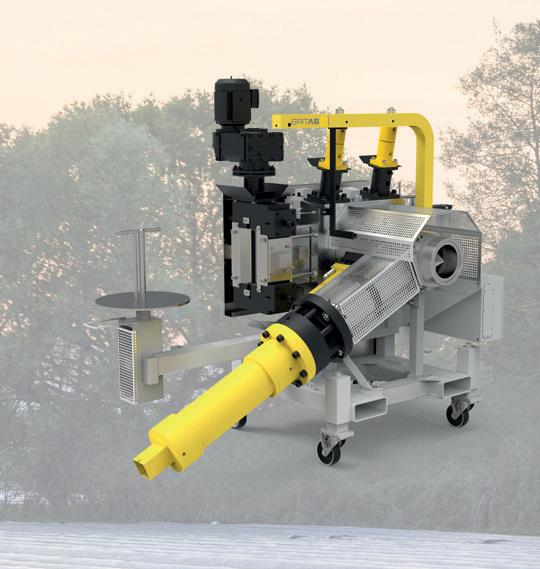
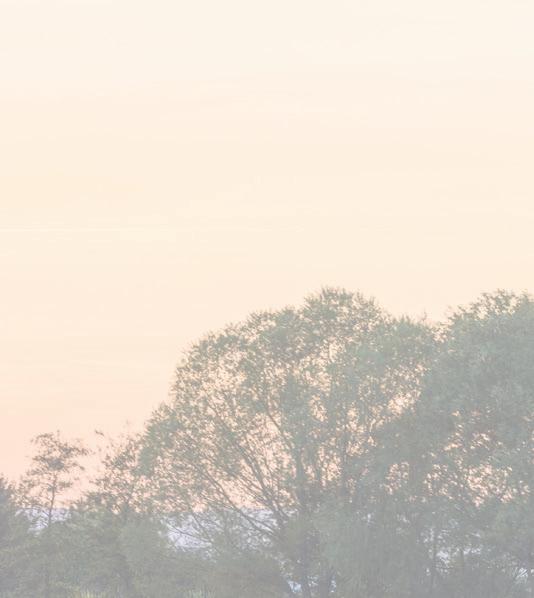
Contact us to find out about our Part Exchange scheme.
Back in 2003, we spotted an opportunity to offer clients something unique. An innovative and comprehensive manufacturing solution that combined the benefits of British standards and values with Chinese manufacturing efficiency and precision. That’s why we created Sino.
Where East meets West
Fast forward 20 years and our experienced British designers, engineers, and management work alongside the team in our fully equipped 54,000-squarefoot factory in Shenzhen to offer clients high quality with keen cost efficiency, swift turnaround times, and stressfree project management.
Our unique infrastructure and experience set us apart from traditional Chinese toolmakers. We are a British and Chinese company with a 50% shareholding held by Rob Harris and 50% by Li Xie.
As a truly hybrid solution, our Western/Chinese structure is the DNA of our business and the secret to our manufacturing excellence. It enables us to design, manufacture, and deliver a huge range of high-performance mould tooling and components for leading companies across the globe. Plus, our British creative and technical knowhow ensures professional project management and communication throughout the turnkey process.
Our manufacturing ecosystem means clients can rely on us for everything from concept to delivery. To help customers with complex product design solutions, we’ve worked with a UK design agency that specialise in solving mould design problems for over a decade. They work closely with our in-house mould designers in Shenzhen to finalise the work