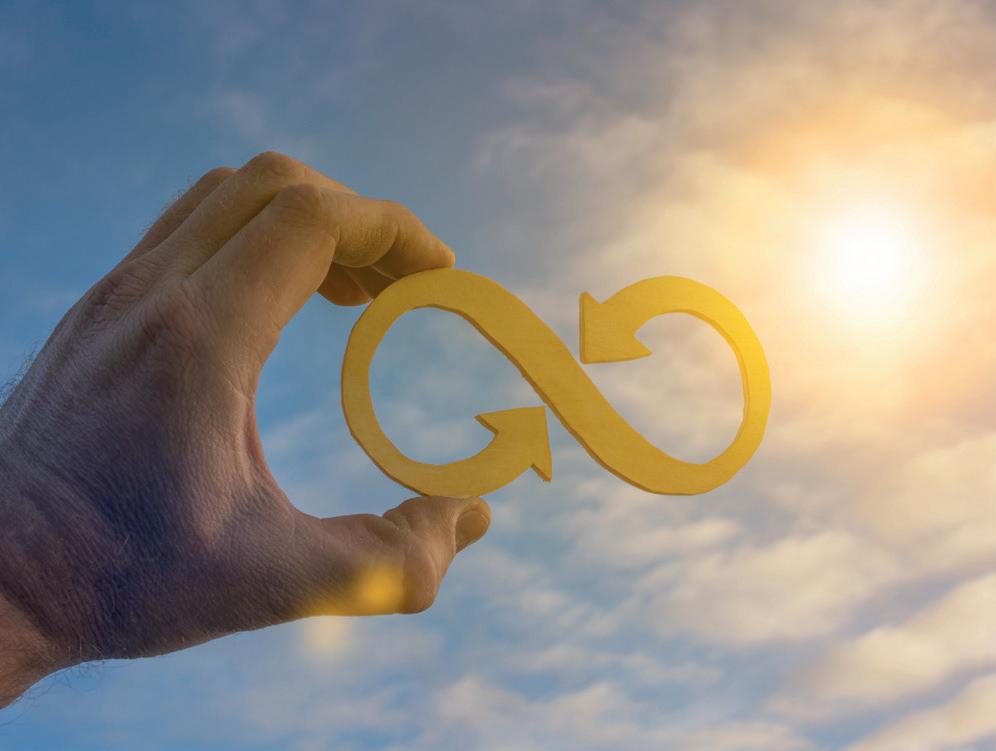
11 minute read
COMMENT
from BP&R December 2021
COMMENT The word from Hird
R
RICHARD HIRD, CHAIRMAN OF THE POLYMER MACHINERY MANUFACTURERS AND DISTRIBUTORS ASSOCIATION (PMMDA), REFLECTS ON CHAIRING THE SUSTAINABLY STAGE AT INTERPLAS 2021 AND DISCUSSES A KEY AREA IN WHICH PMMDA MEMBERS AND OTHER MOULDING MACHINERY SUPPLIERS ARE ASSISTING PROCESSORS IS ENERGY REDUCTION IN THE MOULD SHOP.
Whilst at Interplas I had the pleasure of chairing a seminar on the Sustainably Stage, focusing on the up-and-coming Packaging Tax and the value of Post Consumable Recyclate (PCR) material. What became evident is that some of the so called ‘Single Use Plastics’ are a valuable commodity if the supply chain is sustainable. This starts with the consumer not treating this versatile material as waste, but as a valuable resource that can be re-used or recycled to help alleviate the issue of Climate Change. This is a truly ‘circular economy’ material if there ever was one, especially as it is easier and cheaper to recycle than glass, with a lower carbon footprint.
All this is not news for most of us in the industry, but we may have been a little slow in making the most of this valuable resource. However, this is changing, possibly due to the imminent Packaging Tax as a catalyst, with many companies leading the way and some of those assisted by members of the PMMDA.
One such member is ancillary supplier Labotek GB, who over the last 18 months has been working on a number of Silo, Blending and Conveying installations where customers are either re-selling their recylate into other sectors/processes or switching over to PCR - in some cases up to 100%. Others are setting up their own in-house reprocessing lines. Tim Peet, Director of Labotek GB observed “We started seeing a trend just before the start of the pandemic, which has developed into our main focus as a business, with sustainability a key ethos at Labotek.”
Another key area in which PMMDA members and other moulding machinery suppliers are assisting processors is energy reduction in the mould shop - in particular with the advent of servo hydraulic machines. A typical example is White Horse Plastics (WHP) based in Oxfordshire, who recently ordered a SmartPower 60 from Wittmann Battenfeld UK (WIBA UK). WHP Managing Director Paul Bobby commented “after labour and raw material costs, energy and utilities present us with the next
most significant overhead. I always expect to see some significant improvement when comparing old to new, but these outcomes were far more impressive than could ever have been hoped for. In fact, the greatly reduced running costs from the SmartPower machine were so incredible that it led to us repeating the exercise in order to check our methodology. But when repeated these results were exactly the same.”
WIBA UK’s Tracy Cadman added that “the bonus for everyone is that green energy is profitable energy - and by some way when we have customers of all kinds telling us that our newly supplied equipment is now reducing their energy consumption by a factor of between five and ten.”
In addition, Steve Lacey of STV Machinery, suppliers of refurbished machines and Yizumi machines asks the question - does replacing an otherwise good variable displacement pump machine give real energy saving, when compared to the latest servo hydraulic machine? In his opinion it does - citing an example where one of his customers conducted a real-world direct comparison between his existing 10 year old machine and a new Servo Hydraulic Yizumi, resulting in a net energy cost saving of £252 over a 3 shift 168 hour production/week. Lacey’s advice is to always conduct a true comparative test rather than take the published savings at face value, as every moulding process will have its’ own particular parameter and running conditions.
In closing, our industry has a lot to shout about and educate the wider audience of the true value of a truly sustainable material and equipment that is already contributing to improving Climate Change.
Q: How do the various vacuum generators differ?
IN
THE LATEST INSTALMENT OF OUR ONGOING SERIES ANSWERING THE MOST FREQUENTLY ASKED MATERIALS HANDLING QUESTIONS, THE EXPERTS AT MOTAN COLORTRONIC BRIEFLY PRESENT THE MOST COMMONLY USED VACUUM GENERATORS IN THE PLASTICS INDUSTRY.
Part of the heavy workers of pneumatic suction conveying – the precise term for the most important conveying method in plastic processing – are without a doubt the vacuum generators. They must run interference free around the clock if required, should be as maintenance free as possible, and ideally should operate economically and as needed. Simply put, vacuum pumps generate a vacuum in the material hopper on the processing machine. The air that then flows in after transports the granules of powder through the pipe and hose lines into the hopper. A safety filter installed between the pipe lines and the vacuum pump prevents contaminated air or dust and granule particles damaging the pump. Some of the most important vacuum pumps are: • Side channel vacuum pumps • Claw vacuum pumps • Disc vacuum pumps • Root or rotary blowers
Side channel blowers are the most common and are mainly used for length and diameter of the material lines, and the line system must be considered.
With this data the required pressure difference and volume flow can be determined – and the most suitable vacuum pumps can be selected. Maximum requirements of the units to be supplied with material are crucial for the necessary power of the vacuum generator. In the simplest case this means that the material loader furthest away with the highest throughput determines the power performance. Standard vacuum generators run with constant performance, regardless of the actual requirements of each material loader. This is why a vacuum generator with power regulation may be beneficial. In combination with the correct controls, power regulation can adjust the power to the actual requirements. As a result, material protecting conveying speeds can be set individually for every material loader, every conveying distance, and every pipe diameter. Energy consumption then also corresponds to the actual requirements.
simple conveying tasks with short distances and large volumes. They operate contactless without oil and therefore require almost no maintenance.
Rotary blowers also operate contactless and without oil. They are suitable for large throughputs at low pressure differences, but this restricts the conveying distance.
Disc or claw pumps are suitable for larger distances. The disc principle for suction conveying operates with circulatory oil lubricant, which requires regular maintenance. As a result, these robust all-rounders are suitable for a large range of applications.
The claw vacuum pumps operate dry and contactless and are considered to be very energy efficient and safe.
The pumps differ particularly in how they operate and thus also their effectiveness. They can only be compared when restricted to the characteristic curve of volume flow based on intake pressure. When designing a suction conveying system, various criteria need to be taken into consideration when choosing a suitable vacuum generator. As well as the general environmental conditions (for individual cases the height above sea level), the material and its properties, ABOVE: Central vacuum generation station with side channel blowers and safety filters in the background (photo: Motan-Colortronic)
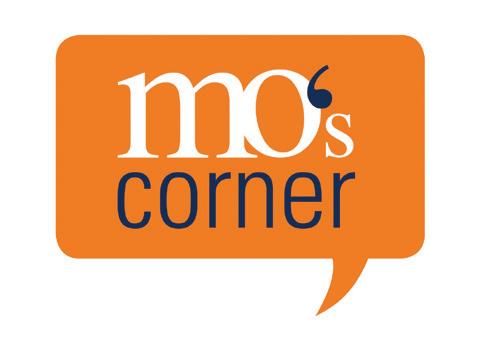
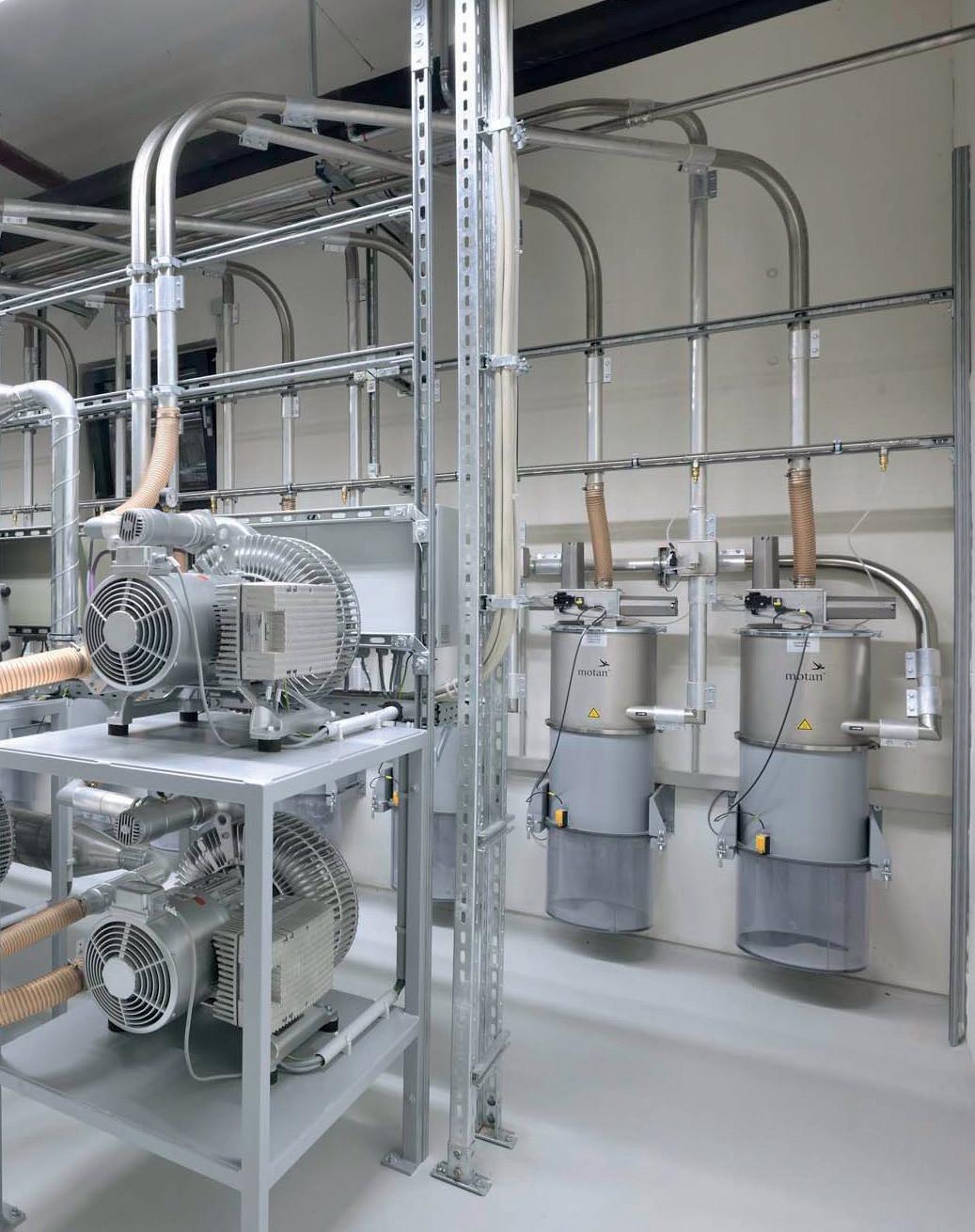
26 - 28 SEPTEMBER 2023
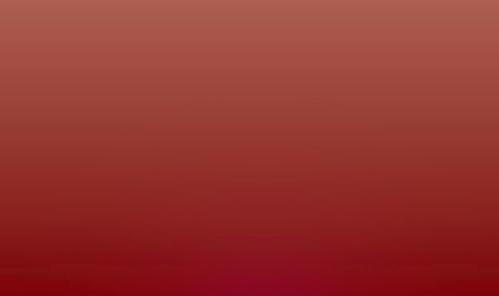
88%
of exhibitors said they made a sale directly related to Interplas. 92%
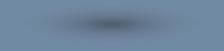
of visitors found a new supplier or technology they has not known of before.
Save the date

Interplas is back in 2023, bringing with it the opportunity for you to experience the UK’s largest plastics industry exhibition showcasing the full spectrum of plastics processing machinery, materials, software, services and ancillaries in one place.
It’s also the only plastics event in the UK where visitors can see working machinery LIVE on the show fl oor and where they’ll come to compare, contrast and buy.
With an expected 14,000+ attendees across the three-day event, as well as new features and an expanded fl oorplan, now is the time to position yourself as a company that can offer solutions, showcase innovation and offer expertise to an audience known for its quality and purchasing power.
MATERIALS HANDLING | NEWS
Coperion Partners in Development of Manufacturing Technologies for Graphite-Polymer Based Bipolar Plates
Within the framework of a joint project with the University of Stuttgart’s Institute for Plastics Technology (IKT), Robert Bosch, and Matthews International / Saueressig, Coperion is working on the continued development of proton exchange membrane (PEM) fuel cells for efficient delivery of energy for everyday mobile use.
Bipolar plates as a core element of fuel cell stacks, and in particular their thermoplastic graphite compoundbased implementations, are the focus of this work. The extremely high fill levels pose challenges upon the process technology, the likes of which have not been seen before. As a partner in this project, Coperion is leveraging its comprehensive expertise in developing the required machineside solutions for manufacturing compounds.
In this project, addition of fillers to the polymer in the Coperion ZSK twin screw extruder is being improved to avoid creating agglomerates and degrading the polymer during compounding.
Bipolar plates, made from graphite-polymer compounds, lend themselves to mobile applications due to their low weight. They combine properties such as electrical and thermal conductivity and gas non-permeability with markedly higher mechanical capacity than pure graphite plates can achieve. Moreover, they withstand the effects of moisture and acid media at typical operating temperatures over longer periods of time than do metal alloys.
Coperion has set this task for itself: To transfer all the experience gained in its years of feed limited plastics compound manufacturing to the preparation of mixtures consisting of high amounts of graphite and low amounts of polymer, to lay the foundation for future upscaling.
With the aid of patented Feed Enhancement Technology (FET) from Coperion, intake of difficult material within the process can be optimized.
For the base technology to improve intake behaviour, Coperion uses patented Feed Enhancement Technology (FET), which is ideally suited when finer, non-compacted fillers are used. The intake section of the side feeder is equipped with a porous, gas-permeable wall. A vacuum is fitted on the outside, and part of the air contained in the mixture is sucked out. The bulk density thus increases and with it the material’s absorption capacity in the side feeder.
Coperion has also developed a processoptimized machine concept to homogenize the mixture. Parallel to this, the company is using numeric 3D flow simulations (CFD) for virtual and real optimization of the polymer and filler mixing process. Along with the project, Coperion is also developing an inline quality tool to detect process and product fluctuations, whereby the regulation of compound quality should be realized in real time.
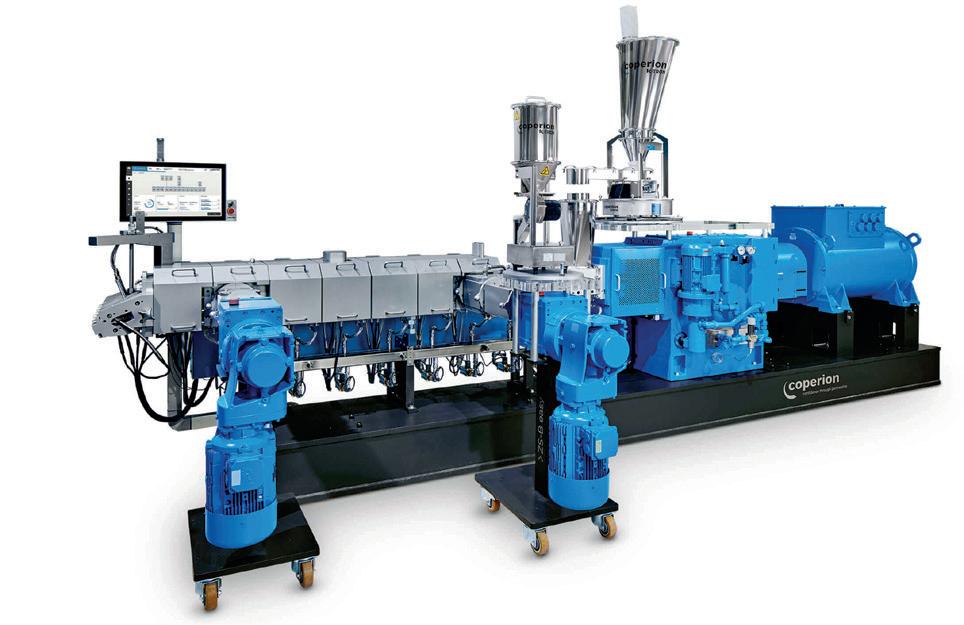
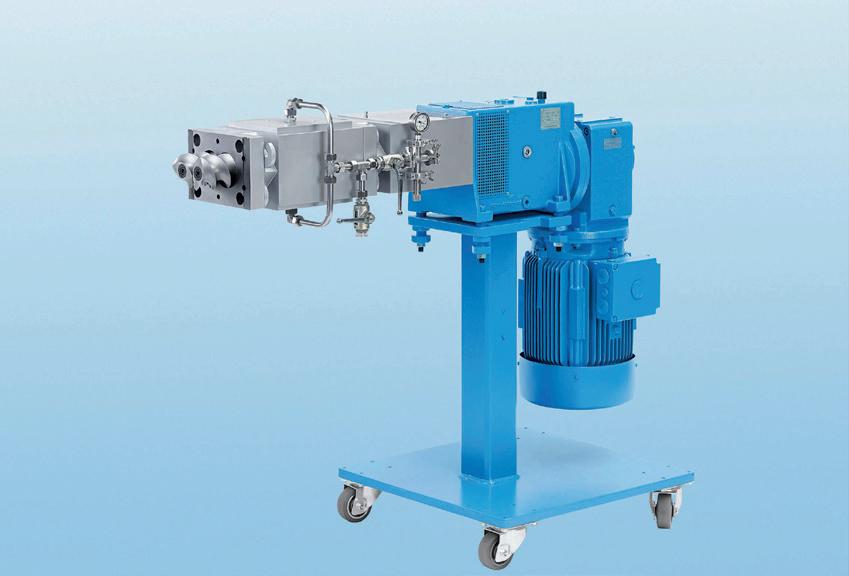
Maguire introduces New Bridge Breaker for HighCapacity Blenders
A pneumatically operated device that is deployed inside one of the hoppers in a gravimetric blender makes possible accurate dosing of regrind, recycled plastics, and other ingredients that tend to agglomerate or “bridge,” obstructing flow through the dispense valve of the hopper.
Maguire Products, Inc. has introduced the new “bridge breaker” for its three largest blender series, those with maximum throughput capacities of 5,000 kg/ hr, (11,000 lb/hr) and capability of blending up to twelve ingredients.
The Bridge Breaker Consists of: 1. A hopper insert that directs material straight down onto the dispensing valve. 2. A rotary device that operates automatically while the dispense valve is open. The device rapidly pulses between clockwise and counterclockwise movement, enhancing material flow through the dispense valve.
The hopper insert, which provides a vertical alternative to the sloping wall of the hopper, can be retrofitted in any blender currently in operation. To make up for the space occupied by the insert, the complete hopper assembly includes an extension to accommodate the desired quantity of material.
“The new bridge breaker addresses the growing demand for recycled content in plastic products and the increasing use of regrind as a means of reducing production costs,” said Frank Kavanagh, vice president of sales and marketing. “More and more processors have been finding it a challenge to keep such materials flowing consistently. In fact, we developed the bridge breaker to help one of our customers solve a problem with trim scrap.”
The three largecapacity Maguire® blender families, the 1200, 2400, and 3000 Series, blend up to twelve ingredients, using a wide range of removable hopper and feeder configurations and numerous dispensing devices. The blenders handle raw materials in a variety of forms, including regular pellets and regrind, bulk powders, flake, and ingredients that are especially bridge-prone, such as wood flour. As with other Maguire weigh scale blenders, once all ingredients are dosed into the weigh chamber, the batch falls into a mixing chamber. A microprocessor makes corrections from batch to batch, including adjustments to compensate for variations in extrusion rate or bulk density, maintaining overall batch accuracy to within + / - 0.1 per cent.