
11 minute read
VLB Testing Laboratory for Packaging: “We cater to the entire beverage industry
VLB TESTING LABORATORY FOR PACKAGING
VLB Berlin’s Testing Laboratory for Packaging has been testing all types of packaging for the beverage industry since 1972. The laboratory is unique, as it is the only facility in the world that offers all the different types of testing at a single, central location. This requires an experienced team and specialist equipment – the latter of which in particular has benefited from the move to the new building, where it now enjoys “much more space” than before. We spoke to Susan Dobrick, Head of the department, to find out what else has changed since the move, what a normal working day in the special laboratories looks like, and what the new CNC milling machine can do.
1
The VLB Testing Laboratory
for Packaging was founded in 1972, and moved into the labs in the new VLB building three years ago. What has changed when you compare the new site to the old location?
Dobrick: We have much more space here. The old lab was far too small. We were running out of options for places to carry out our tests and to store our test objects. In recent years, we have experienced an enormous increase in the number of bottle crate tests we have received. A full test encompasses 25 crates, and we were having to deal with several such orders from our clients at once. Accordingly, storage capacity was limited. As such we are really glad to have moved into the new building, where we have a small wing dedicated to our laboratory area. We now have several rooms for conducting all our various packaging tests. But our growth hasn’t been limited to the space available to us – we have also been able to expand our equipment pool and renew parts of it as well. The bottle crate test requires large pieces of equipment – a drop tester or a static materials testing machine. Devices like that take up more space than a caliper gauge.
How many people work in
the Testing Laboratory for
Packaging?
Dobrick: There are six people in the Testing Laboratory for Packaging in total: three of my staff work in the laboratory, while two others deal with special analysis, research and various projects. They also sometimes help me with admin work. One of these two employees works mainly with customers who place regular orders for large volumes. We also added another member to our team at the beginning of the year. He is intensively involved in the implementation of the accreditation work, but he also handles administrative and office tasks and is involved in a research project. However, there is a strict separation between research and accredited areas. What does a normal wor-
king day look like in the Testing Laboratory for Packaging?
Dobrick: All the staff are focused on different areas, so each of us has a slightly different working day. We start every morning with a meeting. This is an opportunity for us to clarify who will be working on which orders and tests for the day. Each employee deals with the orders they’re assigned during the meeting. Every member of our team works very independently and is highly professional – the lab technicians in particular have a lot of experience, as some of them have
2
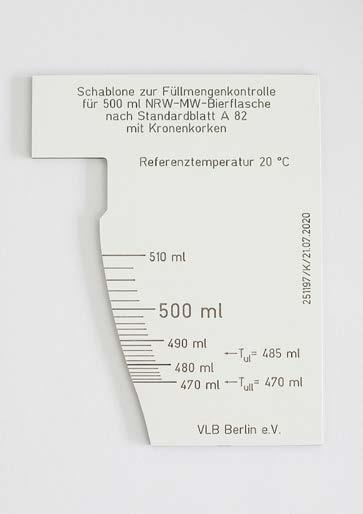
Photos: ew
been working at VLB for years. All of our past employees have passed on their wealth of experience to the new members of the team before leaving. The staff check and measure the results, and enter them into our data processing system. Once this is done, I evaluate the test results and write the report for the customer. I also conduct consultations on which test procedures are suitable for solving specific problems and questions.
Who are your clients?
What fields do they work in?
Dobrick: We have a good mixture of both domestic and overseas customers. They include packaging manufacturers, packaging developers, and users such as bottlers. We are a contract laboratory for the German Brewers' Association and the Association of the German Fruit Juice Industry (VdF).
What exactly do you test? Dobrick: We test all the types of packaging used in the beverage industry – mainly glass bottles, bottle caps, crates and labels. In addition to this, the inspection of cans, labelling adhesives, plastic bottles and various types of closures are also part of our field of activity. We also inspect special packaging such as disposable plastic kegs, special drinking bottles, mugs and glasses. We cater to the entire beverage industry – so when we say ‘bottles,’ we’re talking about beer, wine and mineral water bottles, bottles for soft drinks and juices, and even bottles for liqueurs and spirits. We are the only laboratory of our kind in the world, because we can offer a wide range of different packaging tests for the beverage industry at one central location. Some of the testing equipment we use is also used by packaging manufacturers for quality control. This enables us to provide our customers with comparable results.
What types of tests are
particularly popular right now?
Dobrick: The glass bottle tests will always be in demand. We perform those kinds of tests every day. Nowadays, there are a wide range of custom bottles on the market. The users of these bottles want to check their product quality based on the standard industry requirements for various characteristics, such as dimensional accuracy, stability, visual appearance and material properties. The number of tests we perform on bottle crates has also increased considerably in recent years, due to the customization options for crate design. And ever since the thickness of bottle caps was reduced, not a day goes by where you won’t find a bottle cap on our test bench.
Are there any tests that
are really only conducted by the VLB Testing Laboratory for Packages?
Dobrick: We do have one testing technique which enables us to transform new glass bottles into a defined used condition within just a few hours – the kind of condition that a bottle would normally only reach after going through the recycling system about 25 times. We remove the coating from the bottle and create scuffing rings – the signs of use and wear caused by contact with other bottles of the same type. Once they have reached this condition, the bottles are subjected to a stability test. This allows us to estimate how the quality of the bottle would change in reality. If the results are positive, the customer knows that they can use their bottles as reusable products with a clear conscience.
What do you do besides
packaging testing itself?
Dobrick: Our jobs have changed over the years. The key factor here is filling quantity templates. About ten to fifteen years ago, we would only receive requests for filling quantity templates about once or twice a year. We actually outsourced the manufacturing of this type of measur-
3
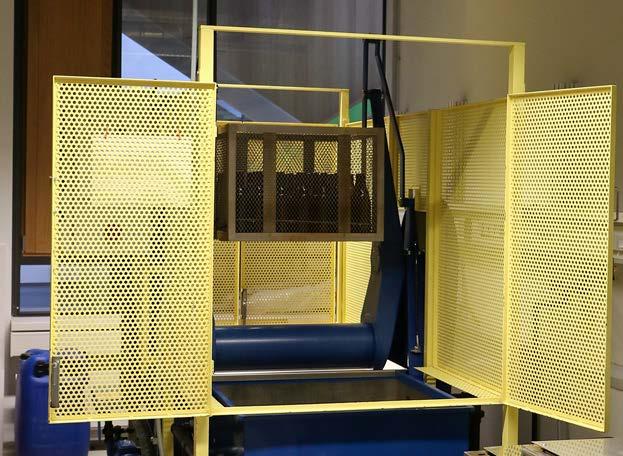
ing equipment. But now that bottles are becoming more and more individual in design, we are receiving significantly more inquiries of this nature from our customers. In order to ensure that we can serve these customers faster, we now pro-
WE BREW FOR THE BEERS OF THE WORLD
Roasted Malt Beers Malt Extracts Beer Concentrate Brewing Syrups C a r a m e l Liquid Sugar
ASPERA BRAUEREI RIESE GMBH
45478 Muelheim-Ruhr, Germany Phone +49 208 58 89 80 / aspera@aspera-riese.de www.aspera.de
4
duce filling quantity templates ourselves. With the move to the new building, we have acquired a CNC milling machine. We now supply our customers with VLB templates produced in-house. However, making the templates isn’t the most difficult step – that would be acquiring the data we need before we can start the job. In order to create the filling quantity templates, we calculate data such as different filling level heights and distances. This is manual work that requires a lot of experience, sensitivity and patience on the part of our laboratory technicians, as the template has to be manufactured with precision.
What are you particularly
proud of?
Dobrick: We can be particularly proud of the expertise of our staff – our team. Experience plays an important role in most of our tests, and of course that’s something you don’t have when you’re completely new to the job. Every year you work in the lab, you learn a little more. The more orders each member of the team completes, the better they get at identifying faulty samples
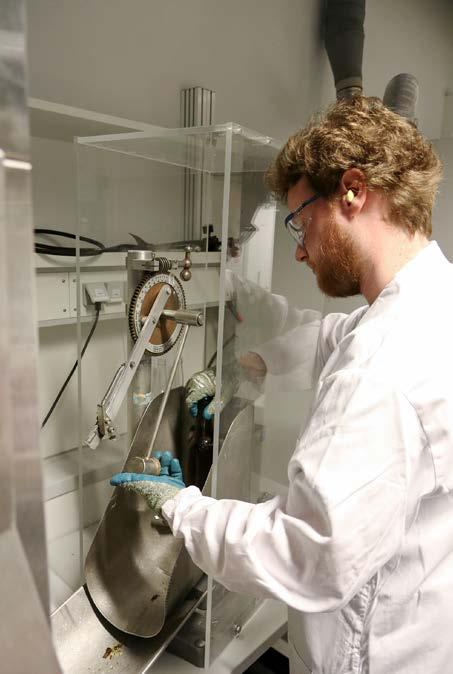
or conspicuous results before a test is even finished. Experienced employees can use the raw data to immediately recognize what direction a problem is heading in. If there’s something wrong with the stability tests, for example, we can react quickly and notify the customer. This allows them to implement quick countermeasures.
5
What equipment
does the laboratory have? What have you got that makes it really special?
Dobrick: Oh, we’ve got lots of unusual equipment. For example, we bought a digital microscope when we moved into the new building. This gives us a high degree of flexibility and enables us to achieve magnifications of up to 2000 times normal size. This makes it easier to view certain faults in bottles or cans, for example, and identify them more accurately. It generally gives us a better picture of all the surfaces we test. That’s something we’ve never had before. Another piece of equipment that’s really special is our static materials testing machine. It’s a universal testing machine, which means it can compress, measure and stretch. We mainly use it as a tool for measuring the length and testing the compression pressure of bottle crates. Another one is our ramp pressure tester, which has been in continuous use for many years. We use this to test the internal compression strength of glass bottles. I never cease to be amazed at the reliability of the values it delivers, even after all these years – especially as this is one of the most important measurements taken during a bottle test.
What guidelines and regulati-
ons do you base your tests on?
Dobrick: Special Technical Delivery and Purchase Requirements (STDPR) are closely related to the collection of brewing analysis methods used by the Central European Commission for Brewing Analysis (MEBAK®) – it’s important to use both

for comparison, although the MEBAK Collection of Brewing Analysis Methods is more comprehensive. Aside from that, of course, we use the German DIN standards, which are incorporated accordingly into the respective collections. Last but not least, there’s also our in-house methods, which we have developed and verified over the course of many years. Some of our clients, such as those based outside of Germany, work with different standards or test methods. This often presents us with very special challenges, but we use all the facilities available to us to overcome these.
Who comes up with these
kinds of methods?
Dobrick: Methods like these are developed by working groups. These working groups bring together users and manufacturers of packaging, such as representatives of breweries, staff from glassworks, and crate and label manufacturers. These meetings are used to discuss tests and agree on test parameters, using DIN standards where necessary. The participants set threshold values and tolerances, and agree on the exact processes to be used. The results are written up as recommendations. The methods need to be based on the latest available technology, so they have to be revised every few years. One example of something that has come
out of these group processes is the Special Technical Delivery and Purchase Requirements (STDPR), such as those we use for glass bottles and cans.
Do you participate in such
working groups or committees?
Dobrick: Yes, I take part in STDPR working group meetings, I’m a member of the Competence Forum for Beverage Containers, and I sit on the DIN Standards Committee for Packaging. I am involved in the revision of the MEBAK Collection and act as an expert on packagingrelated investigations on the Technical Scientific Committee (TSC) for Filling, Packaging and Business Technology. I also give lectures and supervise internships as part of our VLB courses. For the past three years, I have been a lecturer for prospective packaging technicians at the Beuth University of Applied Sciences in Berlin.
What are the latest packaging
trends in the brewing and beverage industry?
Dobrick: Many new trends are initially subject to secrecy, and need to be investigated thoroughly. Every now and then we see new packaging, some of which is gaining
6
ground in the market, while other types disappear from the scene. There is a lot of fluctuation in terms of design elements on bottles or crates, in particular. Lightweighting has been an ongoing issue for quite some time now, and we often notice this in the values from our tests. For example, the issue of mass is inextricably linked to the question of whether the lighter product is still stable enough. As a trend, lightweighting plays a role in all areas, and it affects bottles just as much as bottle caps and crates. Sustainability is also an issue. More and more companies are now using recycled materials. Eva Wiesgrill
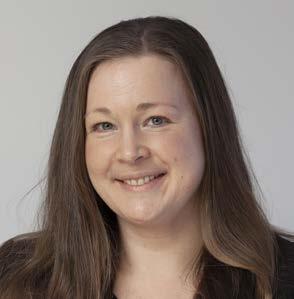
Contact:
Susan Dobrick, Head of the VLB Berlin Testing Laboratory for Packages dobrick@vlb-berlin.org
CHECK OUT OUR NEW VARIETIES
WWW.HOPSTEINER.COM

Fig. 1: An employee works on the static materials testing machine Fig. 2: An example of a filling quantity template Fig. 3: The thermal shocker tests the thermal shock resistance of bottles Fig. 4: By the means of a pendulum impact test the impact strength of bottles is tested Fig. 5: The pop and push gauge Fig. 6: The microscope allows 2000x magnifications of all packaging surfaces