
116 minute read
CONVERSATION
CONVERSATION
Join the conversation – share your thoughts, opinions and feedback with Breakbulk! Send them to gary.burrows@breakbulk.com. Items we use will be edited for appropriateness, length and clarity.
AAL SHIPPING PLANS TO BUILD 4 MPV VESSELS
MASSACHUSETTS HARBOR TO SERVE OFFSHORE WIND
AAL Shipping has added two more 33,000-deadweight-ton multipurpose vessels to its fleet and is in negotiations to build four additional IMO CO2-compliant vessels by 2024.
The MPV carrier signed a memorandum of understanding in October to add W-Class vessels to its fleet, the AAL Mars and AAL Merkur. AAL previously added four MPVs from the second-hand market: the G-Class, 28,500-dwt AAL Galveston and AAL Genoa, as well as the “mega size” W-class 33,000 AAL Paris and Grey Fox.
“We have been commercially operating all of these vessels for some time, along with several of their sister vessels,” AAL said. “Already deployed worldwide to handle project heavy-lift, breakbulk, dry bulk and general cargo, they mat our customer and trade route demands perfectly.”
The addition of the six vessels brings AAL’s owned fleet to 569,600 dwt, about 80 percent of its total operating fleet of 711,200 dwt.
AAL said it is progressing with its “third-generation” MPV ship building program and is negotiating with the CSSC Huangpu Wenchong Shipyard in China to build for four mega-size ships by 2024.
The vessels will be 32,000 dwt with 350-tonne heavy-lift cranes with combined 700-tonne maximum lift. AAL said the ships will be fully compliant with International Maritime Organization emissions regulations, and will feature technologies in line with the carrier’s digitalization and sustainability objectives.
The carrier designed the vessels with Columbia Shipmanagement, the combined team responsible for AAL’s newbuilding ship program.
“In one of the most interesting aspects of the vessels’ design, the
AAL Shipping’s latest additions to its fleet are a mixture of W-Class and G-Class (pictured) vessels. SOURCE: AAL SHIPPING
accommodation blocks have been located at the front of the vessel,” AAL said. “This fore position delivers flexibility to expand intake of over-dimensional cargo without obscuring visibility for the master. AAL said that within five years, nearly 57 percent of the heavy-lift fleet will be more than 15 years old and will no longer meet stringent requirements for premium paying cargo. About 48 percent) of the current MPV fleet has lifting gear of more than 100 tonnes, and about 20 percent has “heavy-lift” gear.
Developers behind the 804-megawatt Vineyard Wind offshore project in Massachusetts have signed an agreement with engineering group Crowley Maritime to develop Salem Harbor into the state’s second major offshore wind port.
Located about 13 nautical miles south of Martha’s Vineyard and Nantucket, Vineyard Wind is the first commercial-scale offshore wind farm in the U.S. to achieve financial close, and is expected to be the first of many following successful offshore wind lease sales by the U.S. Bureau of Ocean Energy Management.
Avangrid Renewables and investment group Copenhagen Infrastructure Partners submitted the “Commonwealth Wind” initiative in September. If approved, it will involve development of a further 1.2 gigawatts of wind power in an area 22 miles south of Martha’s Vineyard.
Under the terms of the agreement, Crowley Wind Services will purchase an area of 42 acres surrounding Salem Harbor Station from current owner Footprint Power and serve as the long-term offshore wind port operator.
David DeCamp, director of corporate communications for Crowley, told Breakbulk the deal will see the firm marshalling a wide variety of project cargo such as “foundations and other materials” as well as “wind turbine generator components, blades, towers, nacelles” to support installation construction.
Featuring 84 GE Haliade-X turbines, Vineyard will involve significant breakbulk transport during construction, but prior to this phase the partners have identified the need to create a suitable staging area to receive and prepare the various outsized cargoes.
The Vineyard Wind project has so far secured almost US$2.3 billion of senior debt and financial backers include some of the biggest names in banking, including Bank of America, J.P. Morgan, BBVA, NatWest, Santander, Crédit Agricole, Natixis, BNP Paribas and MUFG Bank.
AGING MPV FLEET FACES WATERSHED
Newbuilding activity in the multipurpose sector has fallen to an all-time low and a lack of modern heavy-lift vessels may cause a new capacity crunch within the next two years, according to the latest estimates from research consultancy Drewry Maritime.
Speaking at a recent market outlook briefing, Susan Oatway, head of multipurpose shipping research at Drewry, described a “looming age problem” for the fleet, noting “the MPV sector has been in recession for the past 10 years” and lacks much needed investment for renewal.
“There is very little spare cash, even after a bull market run that has so far lasted nine months. Added to this is the simple fact that the yards are full of orders for containership and bulk carriers, so even if owners had the spare cash and the desire to build, there are very few slots available,” Oatway said.
While coffers have been partially replenished in the last nine months, as multipurpose rates have soared over 2021, the balance sheet for most breakbulk and project cargo shipping lines still does not favor investment in new vessels and this has the potential to create a capacity shortfall for the project carrier sector at the point when project cargo could take off again.
Oatway predicts that 2023 could be “a watershed year” as a perfect storm of factors combine to shift both the supply and demand side of the equation. “At this point the average age of the fleet, for multipurpose and project carrier combined, will be over 20 years … the latest IMO rulings on GHG emissions will become much more significant for this tonnage and demolition levels are expected to rise.”
In the short term, however, Drewry expects capacity constraints to continue to support rising rates, with further increases over the fourth quarter of 2021 and a tight market for much of 2022.
Drewry predicts that newbuild orders for multipurpose and heavy-lift vessels in 2021 will struggle to reach pre-pandemic levels of slightly more than 200,000 deadweight tonnes in 2019. Compounding this problem is the rapid surge in new container capacity, which has been ordered in response to the current global supply chain congestion.
“There has been over 3 million TEU of container tonnage order this year compared to far less than half a million tonnes of MPV,” Oatway noted.
This backlog at shipyards is amplified by the fact that Chinese shipyards face energy consumption cuts, imposed by the Chinese government, which are causing a temporary slow-down of production as authorities struggle to meet CO2 output goals for 2021.
The lack of newbuilds is matched by reluctance to demolish old ships, a trend which is expected to steadily increase the average age of the fleet going forward.
Looking further ahead, Oatway predicts there will be a “significant increase” in the number of smaller older MPVs demolished from the end of 2022 onwards.
PROJECT PRICING: MEASURE TWICE, CUT ONCE
Parties involved in capital projects need to pay more attention to the carpentry adage “measure twice and cut once,” according to capital projects advisory firm Independent Project Analysis.
Research from the consultancy has revealed that major late changes add on average 12 percent to the total project cost. The knock-on effect of this is the need for supplemental funding – and ultimately a threat to achieving the planned return on capital.
“Business executives are caught off guard and none too pleased when project teams come back for supplemental funding. But very often extra funds are needed because the level of project definition—and therefore the quality of the cost estimate—was not well understood when the project was authorized,” said Ronell Auld, associate project analyst at IPA.
While project teams are responsible for planning and executing the engineering, procurement and construction of projects, business executives still hold the project risk and need to understand the quality of the estimates presented for sanction. The level of definition, or front-end loading, drives the quality of the estimate and gives the project sponsor a sense of how accurate the project estimate is likely to be. “Projects that are not well defined have more unknowns, and the more unknowns, the less accurate the estimate. However, business discipline that links the level of definition to the quality of the estimate is often missing at the start of project investments,” Auld said. “Too often, we have seen business sponsors, eager to see the project field work commence, proceed to full funds authorization with limited definition and too much confidence in the estimate. Business sponsors then become very frustrated with projects for overrunning their budgets.”
The problem, he added, is not with the estimates, it is with the lack of understanding of the basis of the estimates.
IPA described the “measure twice and cut once” approach as optimal to reducing the risk of project cost overruns.
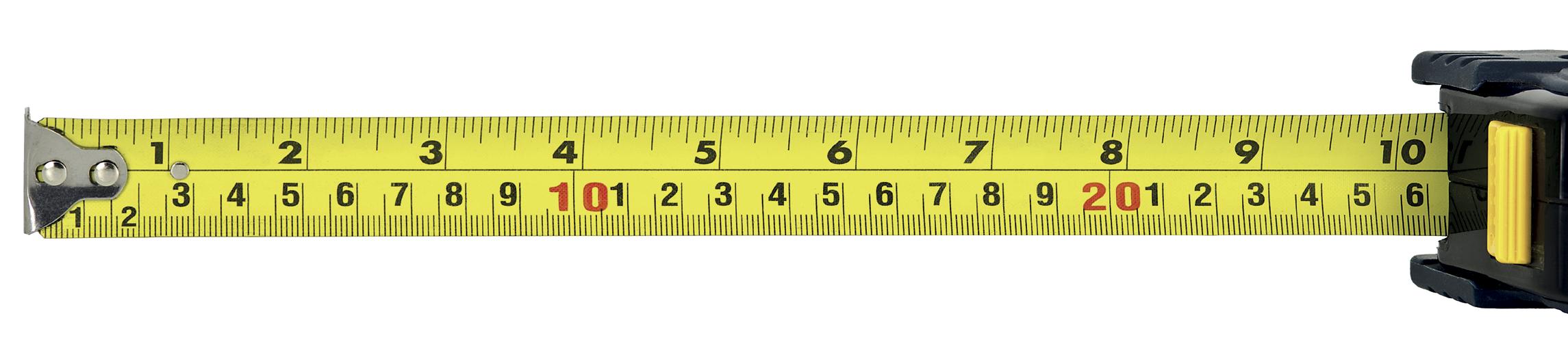
Breakbulk Swan Song
Reflection on Takeaways to Ensure Industry Success
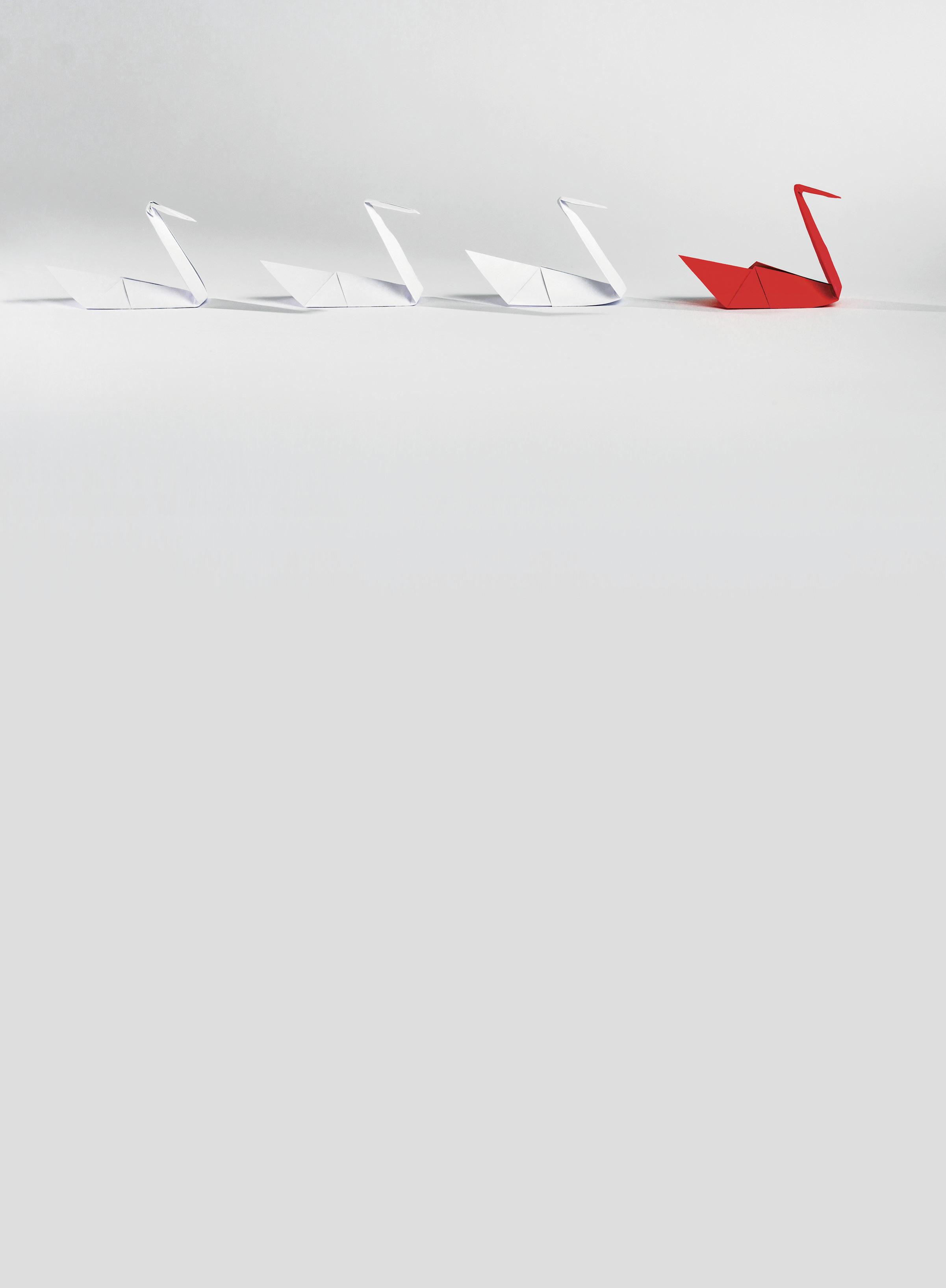
BY MARGARET VAUGHAN
This is the last article that I will pen for Breakbulk magazine. It has been an unbelievable honor and privilege to have been tapped to share my thoughts and views – such as they are – and I’m grateful for the opportunity. But my life’s being pulled farther from the breakbulk industry and it’s time to pass the proverbial pen to someone else. Let them share what they have learned and what they hold as important in our industry, just as I have. It has been an honor to have had this forum.
I leave with some of the points I’ve shared over the past three years (yes, it’s been that long) but that are worth reiterating.
Leadership: Lead from the front. Lead by example. Support and protect your staff. Respect in leadership is not a given. It must be earned.
Integrity: “Nobody can acquire honor by doing what is wrong,” said Thomas Jefferson. The breakbulk community is small, but it has many eyes and a long memory. A tarnished reputation may never be rehabilitated. Safeguard your personal and professional reputation. Always hold yourself to the highest ethical standards.
Learning: Never stop learning. Never stop keeping up with current events. Never stop thinking, evaluating, studying.
Networking: Develop your network. Attend industry events. Meet people. And when you do, look them in the eye, pay attention to them, avoid distractions. Listen more than you speak. You may need these people one day. Networking or not working, the choice is yours.
Focus: Concentrate on the task(s) at hand. Don’t play with your phone or surf your email or social media while in a conference. Attend to the details and look at people when you interact. You’ll be surprised by what you learn. Don’t commandeer the conversation; you have two ears and only one mouth for a reason.
Indispensability: If you’re indispensable, you’re unpromotable. Enough said.
Planning: “Anticipation is 90 program of any game and everything’s a game,” said James W. Vaughan. Believe in your decisions, be abundantly clear in your instructions, and be prepared for daily confusion.
Technology: Stay on top of technological advancements, keep abreast of what’s happening not just in the breakbulk industry but others that touch on it as well. But remember to always think about the downside. What mischief can be made with these new toys?
Above all, bring value to the company you serve, be kind to your associates because you can learn something from everyone with whom you interact, do good work, praise your colleagues, lift up others, and don’t put them down (you want people to work with you again in the future, right?). We spend almost half of our waking hours at work, associating with people who we’ve not chosen, but who have been chosen for us by our organizations, so it behooves us to make the best we can of it. Bring understanding, bring laughter, bring expertise, and bring ice cream. You’ll be glad in the long run.
Many thanks to Gary Burrows and Carly Fields for giving me this opportunity and to you for reading my thought pieces.
Margaret J. Vaughan has more than 30 years’ experience in all facets of supply chain management.
Thanks Margaret. We will miss you!
Supply Chain Crunches
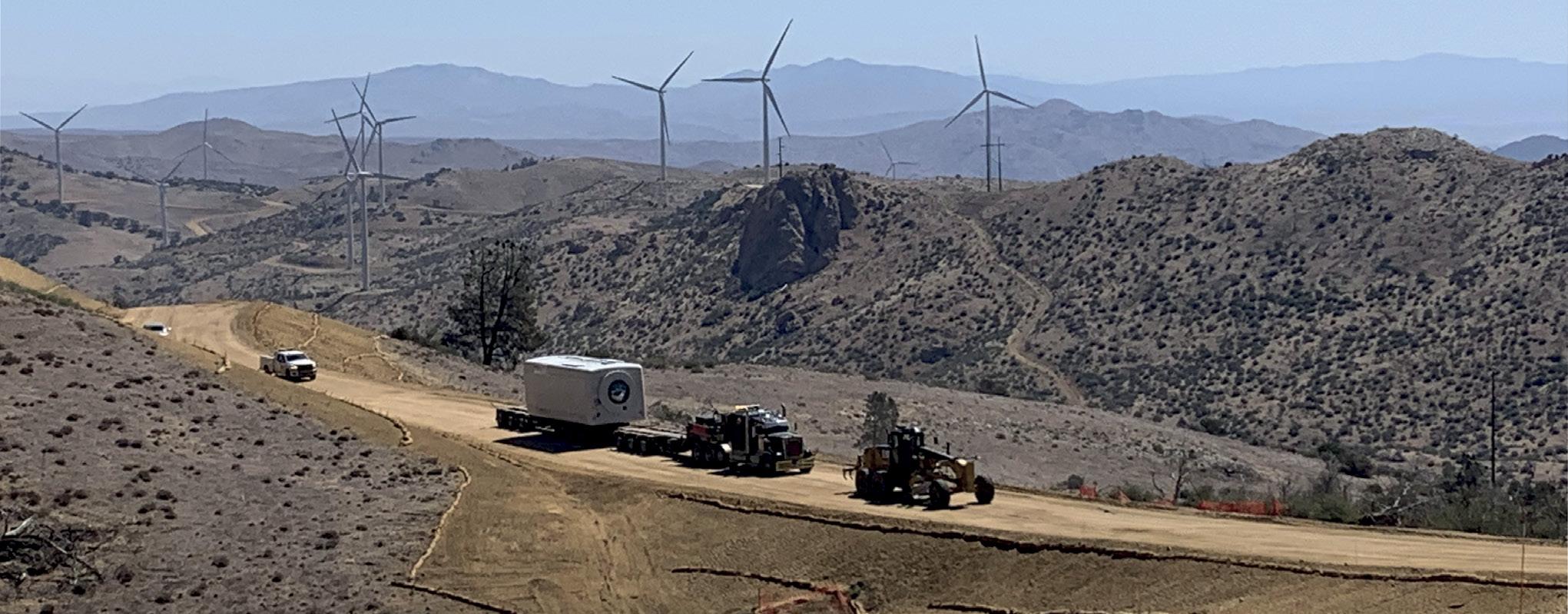
Four Logistics Barriers Disrupting Renewables Growth
Renewables are expected to grow exponentially through 2022. However, the world’s demand for clean energy is running up against some hard realities in the global supply chain. Below are four key project logistics challenges we’re seeing in the renewable energy sector and how shippers can overcome them.
Special equipment to transport goods
Today, the tallest wind turbine is 260 meters with blades as long as 107 meters. It’s no surprise that moving these oversized parts requires special equipment and expertise. Transporting just one wind turbine takes nine shipments, so lining up your equipment well in advance to protect your project timelines and budget is vital. Also, make sure you’re working with a project logistics provider who can flex with your needs when things change. If your freight comes into port 20 days later than expected and the trailers you counted on are tied up on another job, you’ll need your provider to flex, and quickly. Scale matters even more in a tight market.
Unpredictability in today’s logistics market
The scenario where you could plan weekto-week is no longer an option. In fact, when the market is this volatile, one plan isn’t enough. Your vessel may skip a scheduled port and move on to the next, leaving your freight farther away from your project site than expected. A knowledgeable renewable energy logistics provider will have accounted for that. Switching between ports, modes or trade lanes may also be part of a more active strategy to adapt to unpredictability. For example, we’re helping some of our solar customers switch to breakbulk or roll-on, roll-off as an alternative to container ships. An ocean or air charter is another option.
When capacity is this tight, you need more foresight in planning. For shipping your wind farm components, count on booking a vessel as much as 180 days in advance and use a project logistics provider with a global suite of services so you’re not stuck without enough trailers to move your turbines and blades after they arrive.
Tighter budgets for renewable energy projects
Rising material costs and historically high freight rates can eat into the profitability of your renewable energy project. That makes it even more important to avoid unexpected costs in your project logistics. The supply chain for wind and solar farms is vast and complex, and you can go over budget quickly. For example, when you’re renting a crane for US$100,000 a day, you can’t afford for the wind turbines to be three days late.
These projects have too many moving parts and variables to try to piece it together yourself, and can expose you to too much financial risk to count on the disparate processes of multiple vendors. That expertise helps you avoid the unexpected costs that can easily erase your project’s profit margin.
Lack of supply chain visibility
No one wants their supply chain to be a black hole – especially when you’re bringing in parts and equipment from across the globe, and everything needs to come together in one place in the right order at the right time.
One of the biggest favors you can do for your project is to take advantage of real-time visibility technology. It pulls data and status updates from all vendors and suppliers – plus weather, traffic, and geopolitical monitoring – to give you a real-time view of your supply chain. To keep these complex projects on track, it’s crucial to ensure that parts are where they need to be, the right transportation and specialized equipment are available, and the finished product arrives to the project site when on-the-ground teams are ready to receive and install. BB
Mike Short is president of global forwarding at C.H. Robinson.
BY MIKE SHORT
Top: A truck transports a wind turbine section.
CREDIT: CH ROBINSON
OUTLOOK 2022
TAKING A BEARING
With freight rates soaring and the promise of a project bonanza from pandemic recovery programs, Breakbulk’s Advisory Panel look towards 2022 with hope – and just a little trepidation
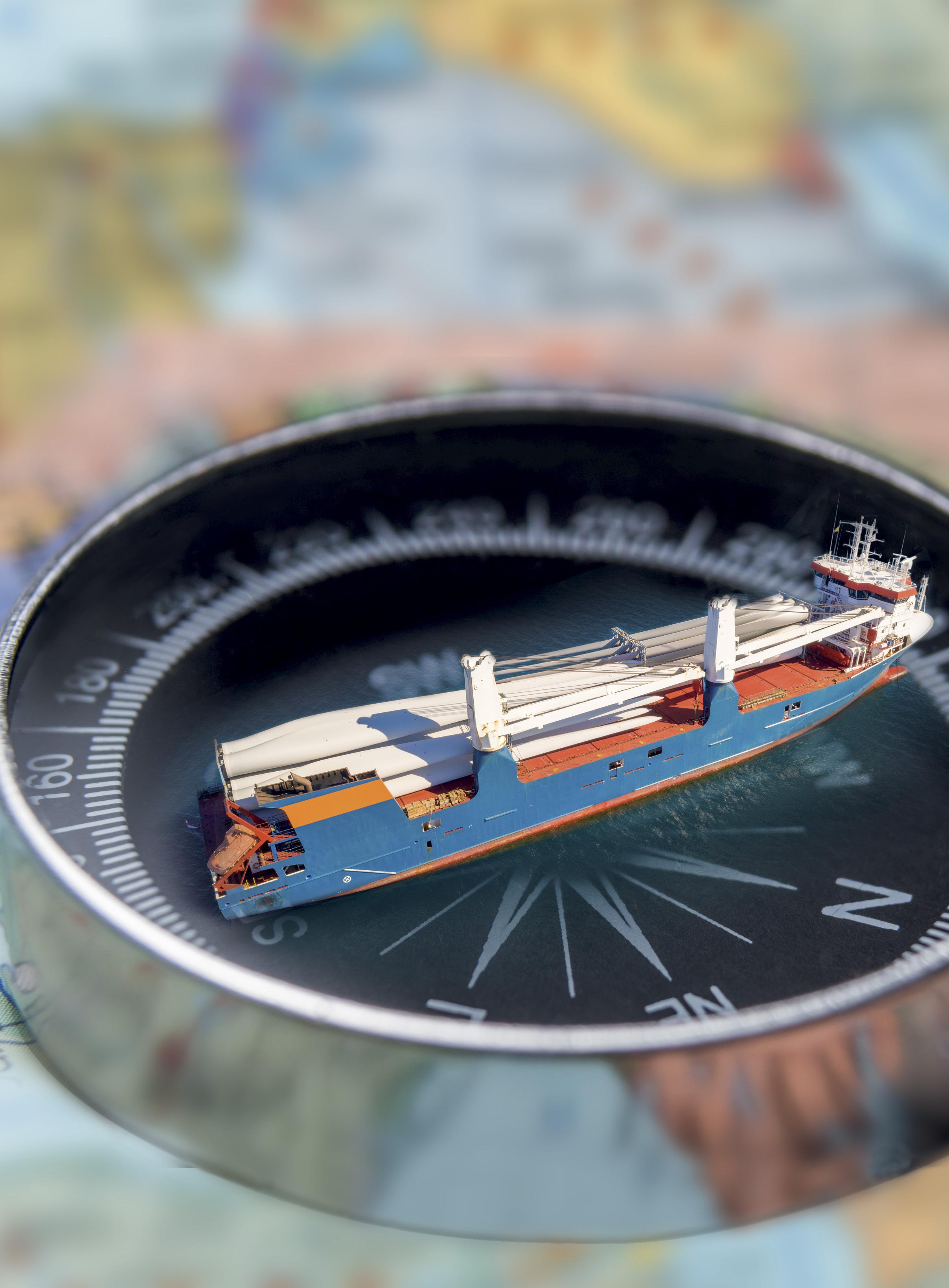
GLOBAL PROJECT DEMAND OUTLOOK
Grant
Wattman, president and founder, Jade Management Group
NO IMMEDIATE SIGNS OF STABILITY
I expect that we will be looking to late 2022 for some stability in the project market, stability that we have not seen for a couple of years. Projects are moving ahead, albeit at a slower pace due to the chaotic supply chain, in terms of pricing, capacity and performance. This is exacerbated by resourcing issues in all skill sets from project conception through to front-end engineering and design and execution. Significant numbers of individuals are leaving the industry and there is very little interest from others to jump in – being in the oil, gas and petrochemical sector is becoming a dirty word.
Nevertheless, we should look to limited growth in North America, with increased activity in the Middle East and Asia-Pacific, across the industry portfolio. I am certain there will be growth in small/micro liquefied natural gas projects, particularly LNG-to-power and small-scale nuclear.
There is lots of excitement around renewables, but remember here to follow the money. The likes of offshore wind and solar are very active and exciting things are happening. As long as governments invest in this sector it will be strong.
This brings me to infrastructure, a sector which is also fueled globally by governments looking to jump start their economy.
Another growth sector is mining, particularly in South America, Africa and Asia-Pacific as source regions for the key minerals – graphite, lithium, cobalt and platinum group minerals – required in our endeavors to reduce our global carbon footprint. Also playing in this area is our industrial and specialty gas industry, particularly hydrogen and carbon capture and sequestration. Watch for growth globally there too.
In summary, there is growth coming and activity is increasing, but we need to watch cautiously as money markets tighten, whether through inflation or governments drawing on available funds. These could lead to delays in projects because the current cost models impact the business plan, resourcing available to plan and the ability to execute projects.
I expect supply chain capacity and costing to be a challenge through 2022 and into 2023, at a minimum.
SUSTAINABILITY
Roger
Strevens, vice president global sustainability, Wallenius Wilhelmsen
There is no getting away from it: the age of regulatory disruption has arrived for the shipping industry. The operative word is “disruption,” because while there have been decades of regulation in shipping already, the scale of the change that forthcoming greenhouse gas, or GHG, regulation will bring makes it pale by comparison.
Many will be familiar with the International Maritime Organization, or IMO, as the global regulator of shipping. However, it is no longer the industry’s only major regulator. With its “Fit for 55” package of legislative proposals unveiled in July, the European Union has made clear its intention to reduce GHG emissions from shipping.
Two key proposals in the Fit for 55 package are the inclusion of shipping in the EU’s Emissions Trading Scheme, a GHG emission “cap and trade” program; and FuelEU, which would require a progressive reduction in GHG intensity of fuel. While the proposals can still change, it would be wise to anticipate some version of them to become law.
The most impactful of IMO’s agreed GHG reduction measures – so far– is the Carbon Intensity Index, which will attempt to regulate vessel operational efficiency. Moves are also afoot at IMO to create a Market Based Measure – a global carbon pricing program. However, it is unclear if the political will exists to bring such a potentially transformative measure into being.
While it can be confidently said that there will be a significant impact for shippers from these EU and IMO regulations, it is not yet known exactly what, or how much, it will be. It is therefore highly advisable for shippers to raise these issues with their carriers to keep them abreast of developments and, critically, understand their carriers’ readiness to deal with them. At Wallenius Wilhelmsen it is a discussion we always welcome.
EVOLVING CUSTOMER EXPECTATIONS
Dennis Devlin, senior director – special project logistics, North America, Maersk
SAFETY AND SUSTAINABILITY GOALS
Customer expectations in global trade and logistics broadly – and in the project cargo sector specifically – are, in many ways like consumer expectations, constantly evolving. Since I joined the project logistics sector in
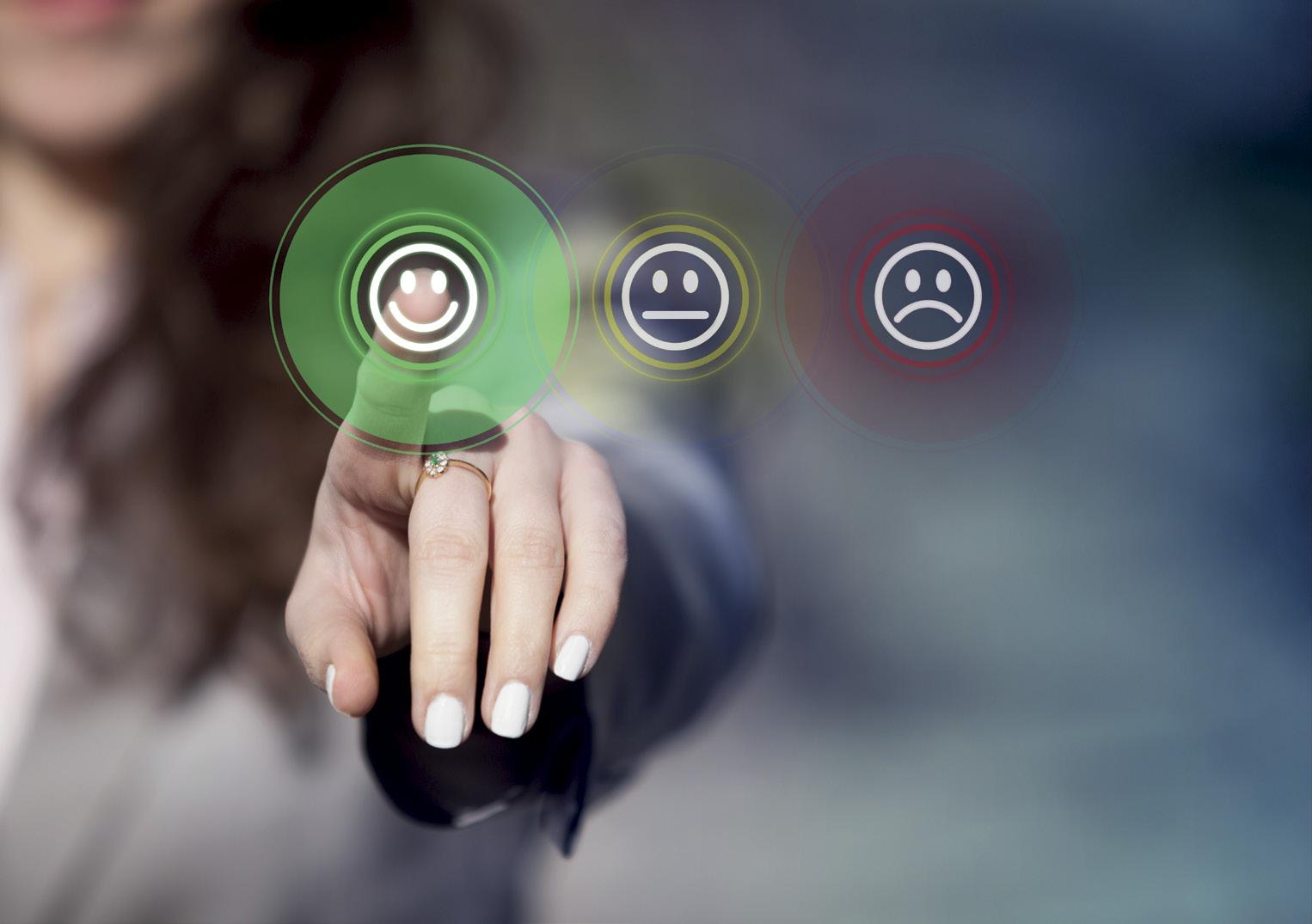
1988 safety has been a key focus of many clients, especially those in the chemicals and engineering, procurement and construction sectors. Safety will rightly continue to be a key focus. But increasingly, shippers who are qualifying freight forwarder and carrier subcontractors are focused on things that one did not see in the prequalification questionnaires decades ago, for example due diligence, policies and practices regarding regulatory compliance, anti-corruption, forced labor and human trafficking.
Given the global threat of climate change, sustainability programs and tracking are increasingly a very important key customer requirement. According to the U.S. Environmental Protection Agency, the transport and logistics sector in the U.S. is responsible for more emissions (29 percent) than the generation of electricity (25 percent).
Globally, but especially in Europe and to a lesser extent North America, logistics companies have begun to offer options to shipper clients who themselves have internal objectives around environmental sustainability, and who require action regarding sustainability from their sub-contractors, including truckers, forwarders, ocean and air carriers.
Increasingly, truck manufacturing companies are developing, and trucking companies are investing in electrically operated fleets as well as battery charging stations. Ocean carriers are investing in ships which will use alternative, less impactful fuels. Air carriers are focused on solutions for greener jet fuel. And freight forwarders are implementing detailed client programs which offer lower emission transport options, as well as track and report emissions. Barge lines and railroads will continue to highlight the significantly lower emissions generated by those two vital transport modes when compared with long-distance trucking.
Other factors such as advances in 3D printing, more domestic procurement where possible and even work-from-home policies may also have a positive impact in the future. And shippers may plan and execute procurement and logistics farther in advance, not only for reasons associated with the current supply-demand imbalance in shipping, but also for reasons associated with sustainability, such that just-in-time shipping may be a thing of the past.
Back around 2012, Unilever’s CEO Paul Polman, one of the top corporate leaders promoting sustainability at that time, wrote: “If we achieve our sustainability targets and no one else follows, we will have failed.” The good news is that others are indeed following, and many businesses are now demanding that those with whom they do business implement sustainability programs.
CAPACITY CHALLENGES
Johan-Paul
Verschuure, project director, Rebel Group
SHIPS AND INFRASTRUCTURE WANTED
Since Q2 this year, the breakbulk sector has been hindered by increasing logistics challenges and sharply rising freight rates. Where in the container sector this has led to record high new orders, shipowners in the breakbulk sector are still in a holding pattern. Also, the container sector is seeing renewed interest in greenfield infrastructure projects while the breakbulk sector remains conservative in this respect. Likely the low utilization rates of the last decade have contributed to this stance.
However, the lights are now green for new investments in breakbulk port and shipping capacity. For one, charter rates are likely to stay elevated for at least another year. While one or two years will not be enough time to build a new fleet and benefit from the current elevated rates, it will at least replenish the financial buffers making new investments possible. The challenges of realizing a global energy transition and a more circular economy will greatly depend on the breakbulk segment.
As part of the European Green Deal, the EU has raised its 2030 climate ambition, committing to cut emissions by at least 55 percent by 2030 and achieve climate neutrality by 2050. In order to reach those targets, huge investments will be required in renewable projects. With only roughly 20 percent of the EU’s energy coming from renewable sources today, the scale of the renewable project challenge is clear.
Alternative energy carriers like hydrogen and ammonia are being suggested as options for the future, however the energy density is much less than that of fossil fuels. That means that for the same amount of energy much larger volumes would
need to be transported and stored. And the requirements and redundancy factors for the stored products will be larger. On top of that, industrial facilities will need to be converted to take in the new energy feedstock and new electrolyzers will need to be built across the world.
If the European member states adopt the “Fit for 55” package and other countries follow suit, the breakbulk sector will require significant investment to facilitate its transition. As such it is vital that governments confirm their commitment to transition initiatives sooner rather than later, giving security to newbuild ordering in the breakbulk segment in the coming years.
MPV OUTLOOK
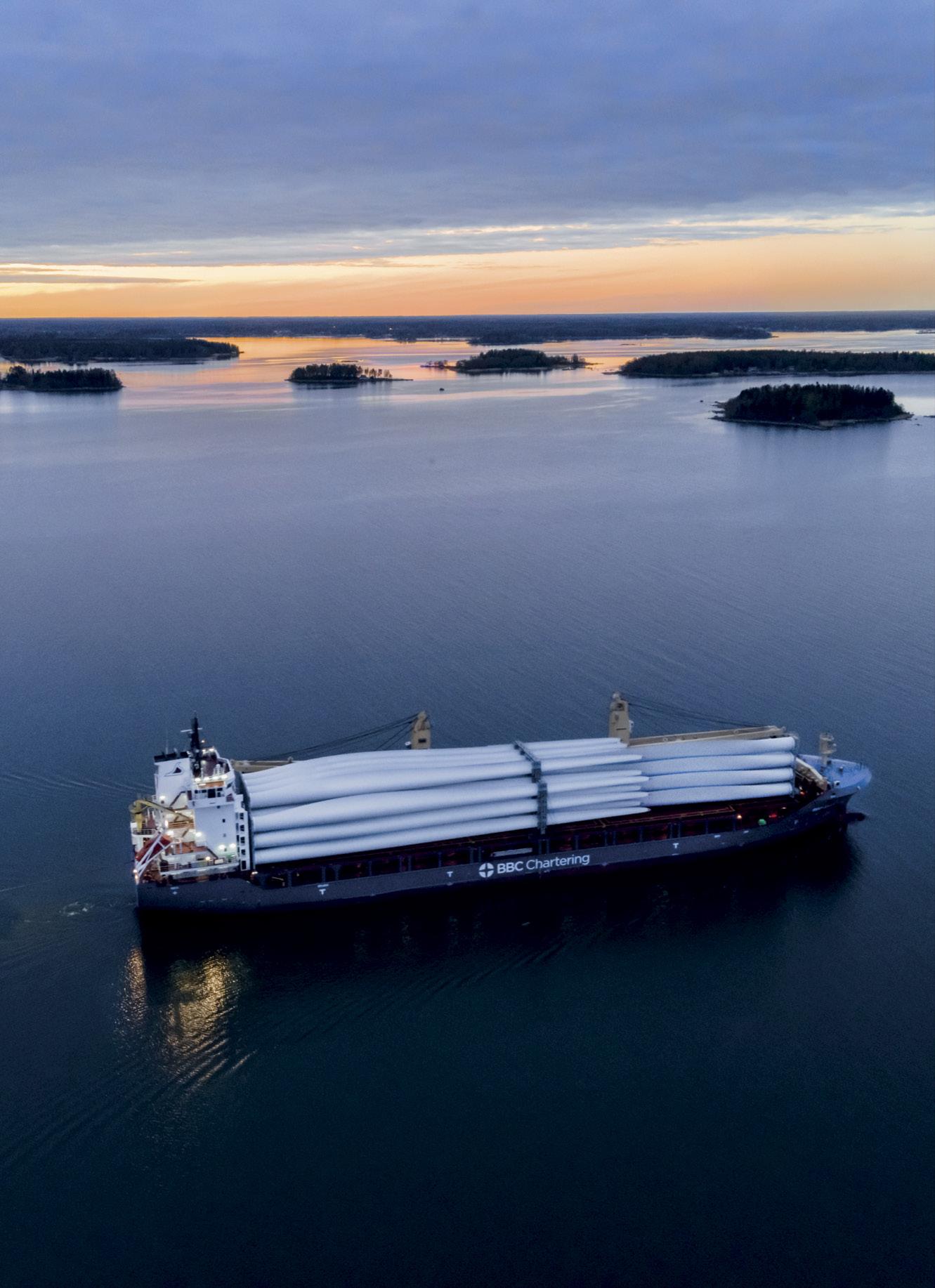
Ulrich Ulrichs, CEO, BBC Chartering
FINE-TUNE YOUR FORECASTING
We expect the heavy-lift and multipurpose market to remain very strong in 2022 with demand outnumbering supply due to a variety of factors, including surging container volumes, the pandemic, and the fleet structure.
One currently and prominently observed phenomenon is container “hype” – directly or indirectly driven by a sustained increase in consumer spending – which will continue to influence the multipurpose market throughout the course of 2022.
Needless to say, the demand for container capacity is contributing to the lack of MPV tonnage. Multipurpose vessels continue to be chartered out to container carriers and MPV carriers are carrying high-paying containerized cargoes.
The Covid pandemic has induced a lot of factors that have disrupted global supply chains. These include terminal lockdowns, quarantine of crew/vessels, slow productivity in ports and congestion, among others. Those factors are not likely to be resolved before the second half of 2022 at the earliest.
Also, there are a few underlying issues which are influencing the multipurpose sector from within. Demand for transportation requirements, especially with regards to renewable energy cargoes, remains high. The MPV fleet is in general overaged and there are hardly any newbuildings to be delivered in the coming 2-3 years. In addition to that, additional environmental regulations such as ballast water treatment systems, EEXI (Energy Efficiency Existing Ship Index), and CII (Carbon Intensity Indicator) will take capacity out of the market, either due to required dry-dockings or as a result of slow steaming. This will add cost for owners and operators, costs that must be passed on to customers.
Space will remain at a premium and freight rates will continue to stay at high levels. Lead times increased from two to three weeks in February 2021 to two to three months in September 2021. Time charter rates for MPV/heavy-lift vessels more than doubled between Q1 and Q3 2021.
Shippers are advised to fine-tune their forecasting and keep in close and regular contact with their carriers in order to secure the space and capacity they require in 2022.
CONTAINER CARRIERS IN PROJECT CARGO
Sarah Schlüter, senior director niche products, Hapag Lloyd AG
HOT COMPETITION FOR EVERY SLOT
The past one-and-a-half years have surely been a ride for us all. Initially we were fearful of whether our industry would be hit as hard as it was during the financial crisis, or wondering if we would scrape through with just a black eye. Today we simply know that the “normal” as we know it will definitely not become the “new normal” again.
Looking ahead into 2022, the liner carrier community predicts that the current situation will stay unchanged until the middle of next year. Port congestion will remain, putting a lot of strain on the liner network, and high ‘freight all kinds’ rates and increasing contract rates will put pressure on all non-standard types of cargo, leading to rate increases. Essentially, every type of cargo is competing for that one slot.
This situation will continue to make things difficult for project cargo – especially with a high number of slot displacements – particularly those destined for parts of the world with few liner service options. At Hapag-Lloyd AG we try to stay closely aligned with all stakeholders involved to find the best solution for our customers and make that space available, but this can definitely be a challenge at times.
In addition to continually improving the day-to-day handling of project cargo, our focus is also very much on digitalizing the project cargo part of our business as advancements in recent years have mainly pertained to regular cargo. It is crucial that we make the quotation and booking process simpler and faster not only for our customers but also for ourselves. Yes, project cargo is a little different from regular cargo, but that should not prevent us from pushing digital innovations that will help everyone who is part of the transport chain.
CREDIT: SHUTTERSTOCK
INSPIRING THE NEXT GENERATION
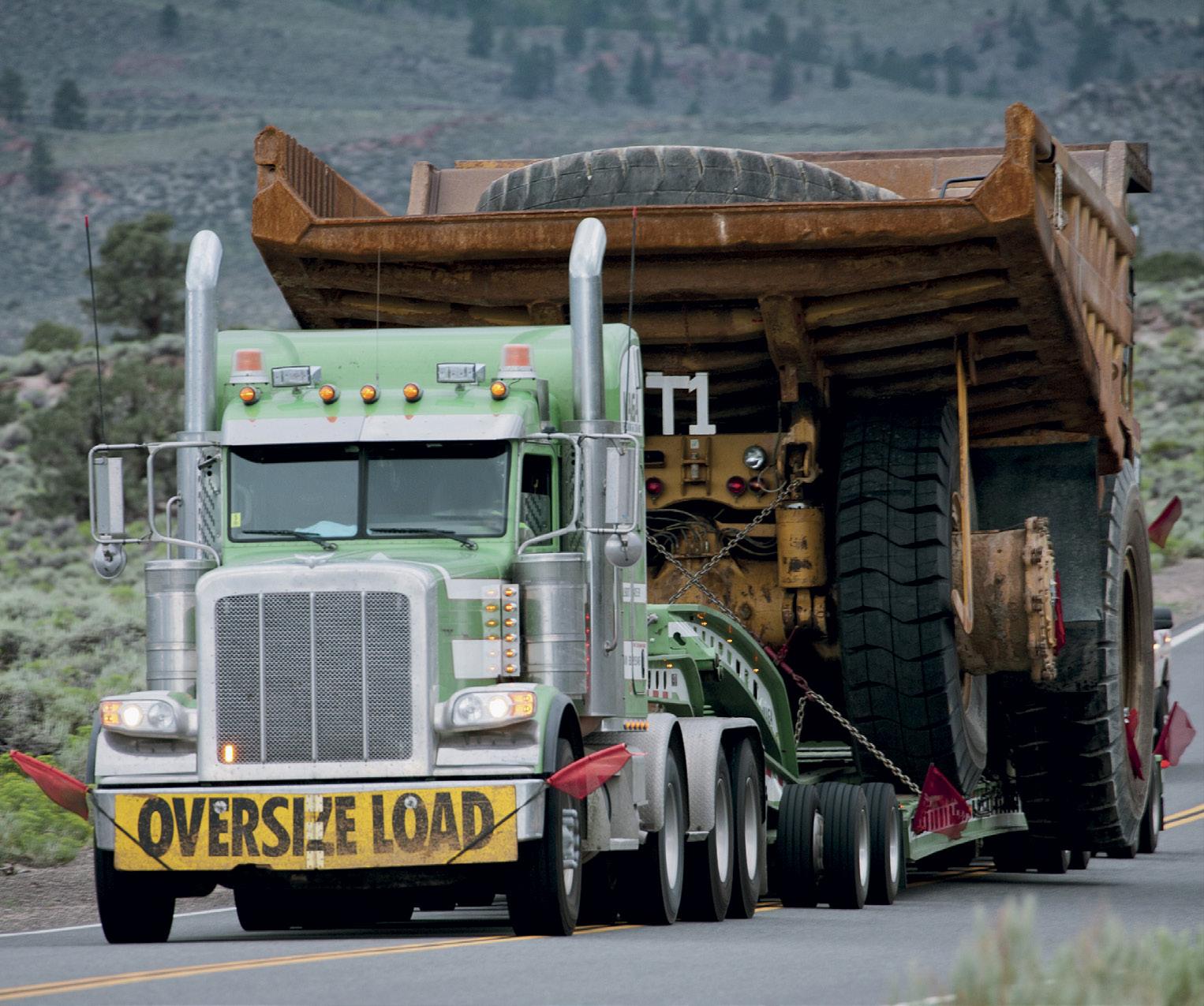
Jake Swanson, global head, sector strategy, DHL Industrial Projects
PUT PEOPLE BACK IN THE CARGO PICTURE
The biggest challenge that we face right now because of the pandemic is getting the necessary face time with the young folks trying to come into the industry. This is a challenge mainly for the next generation as they need this interaction to learn the necessary skills that will help them to grow and to understand what is going on in their respective roles.
When I was breaking into the industry, I learned a significant amount from just listening to conversations of my more senior colleagues or having the ability to walk over and ask my colleagues or mentors how to do this or that or to explain to me what this means or why are we doing things in a certain way.
The pandemic has meant that working in the office is significantly limited and this type of interaction does not occur organically as much as it used to. Remote working definitely has its advantages and I believe is here to stay, but it can create some challenges when trying to inspire the next generation.
Another challenge is that during the pandemic, organizations have been less willing to take on interns, therefore we are losing an opportunity to proactively attract talent to our industry. Internships are great ways for organizations to develop relationships with the next generation and university programs and to make evaluations prior to making decisions with regards to employment – essentially allowing for better employment decisions.
To address these challenges, breakbulk and project cargo organizations should proactively engage new hires and have regular follow-up meetings and training programs to help them as they come into the industry. I think that FaceTime meetings – either internal meetings
or with clients/subcontractors and particularly on site/at the port/on the ship – is critical for their growth. The next generation needs to see and hear things with their own respective eyes and ears to get a better feel of what they are doing. This will help them to make better decisions in the future and relate to messages that they receive during operations and critical situations.
Mentorships and shadowing programs would also be something that I recommend. Allowing the next generation to look over your shoulder and see how an industry professional or executive works and the way he/she thinks offers tremendous insight and vision for them as they look toward their own futures.
Organizations also need to take an interest in and develop an internal process for developing the next generation of leaders. Essentially, spend the time and energy and dedicate time to bring up the next leaders of your organizations. At DHL we have training programs and High Potential programs and many other engaging leadership development and management trainee programs. Senior leaders and executive management should be involved in these programs, engaging and inspiring the next generation.
Organizations should feel that if they do not inspire the next generation, someone else will.
EDUCATION
Margaret
Kidd, program director, supply chain & logistics technology, University of Houston
DEVELOPING EDUCATION FOR TOMORROW’S PROJECT PROFESSIONALS
The Covid-19 pandemic has actively disrupted global economies and trade. Within the chaos has come several bright spots, as lockdown restrictions have been lifted within some national borders. However, there remain hot spots where draconian lockdown measures are still occurring. We witnessed these lockdowns in the summer at the ports of Ningbo and Shenzhen, and, as I write, in Vietnam. Expanding vaccination rates, as well as access to vaccines in middle income and less-developed countries will assist in resolving some disruptions.
The challenges that existed during Covid-19 and that lie on the horizon for both containers and project cargo continue to be about lack of critical components, temporary closure of manufacturing, blank sailings, lack of equipment and workers, cargo visibility, port congestion, capital funding budgets, change in demand patterns and ever-growing environmental accountability. All these challenges lead to the need for a digital transformation of the engineering, procurement and construction and project cargo sectors, along with filling the educational gaps of the workforce of the future.
The voices of corporate shareholders emphasizing environmental, social and governance in the oil and gas sector, as well as in the EPC, shipping, and port sectors, are being heard, highlighting the need for energy transition. This aligns with the current Biden Administration and global climate initiatives. As a result, one bright spot in global infrastructure spending has been on renewable energy, such as offshore wind.
In response to the nascent offshore energy sector in the U.S. and in response to the need of integration of technology within our regional workforce development efforts, the Supply Chain & Logistics Technology Program at University of Houston has made two substantive thrusts.
The first is to better prepare our students for a globalized and digital future. Here, my colleague Al Henson has integrated Geographical Information Systems online introductory training into his Q3 courses. Students are using ArcGIS Online to analyze big data for decision-making related to realtime situational awareness; forecasting longitudinally and futuristically; understanding trends and patterns; setting priorities; route optimization; and distribution center locations.
The second is the launch of two specialized certifications credentialed by the Chartered Institute of Logistics and Transport, involving logistics for Capital Project and Offshore Wind Energy. In the words of Oliver Wendell Holmes Jr.: “Greatness is not in where we stand, but in what direction we are moving. We must sail sometimes with the wind and sometimes against it—but sail we must, and not drift, nor lie at anchor.” University of Houston students are that ship. BB
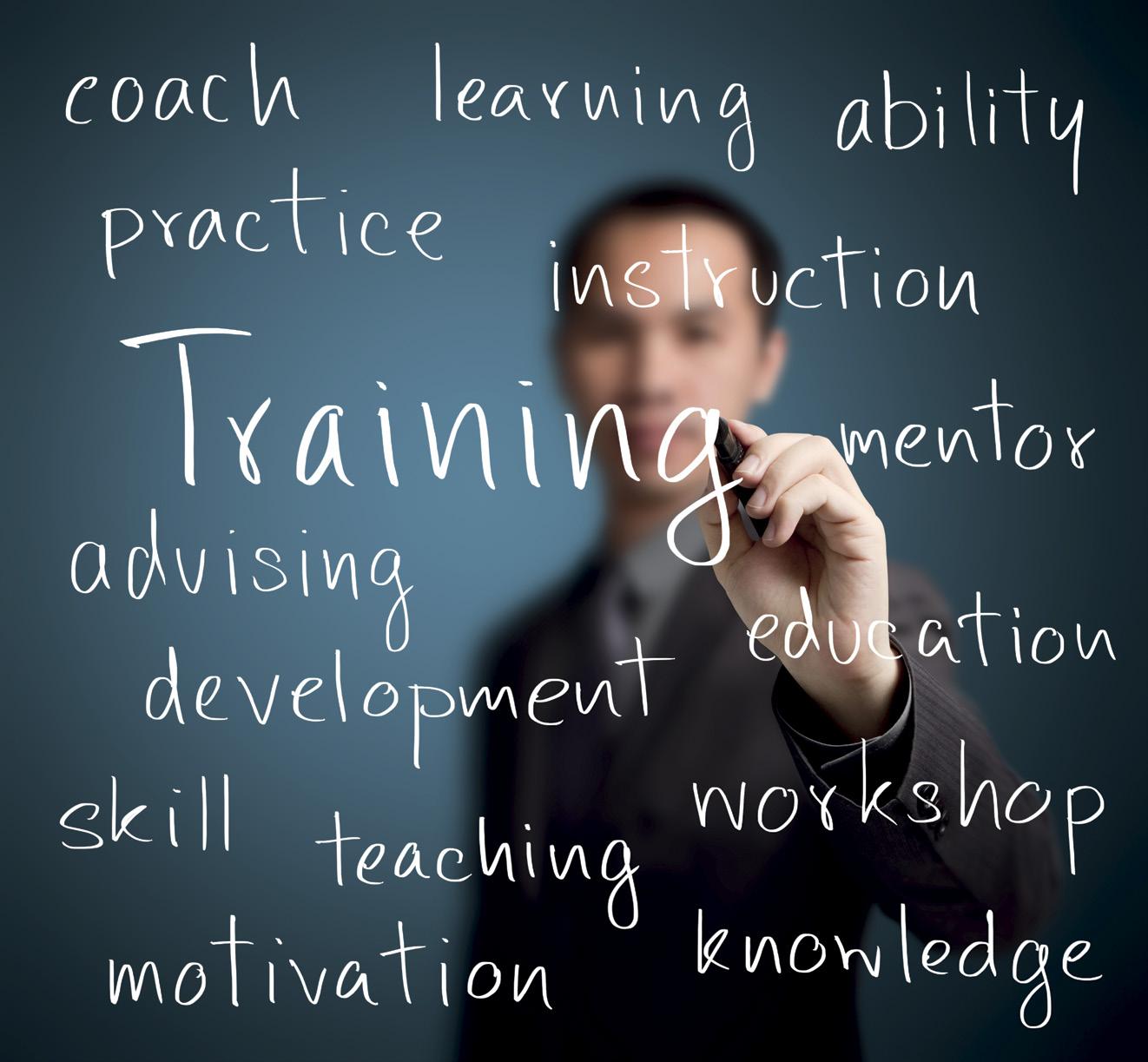
INTERMEDIARIES
ALL CHANGE FOR GO-BETWEENS
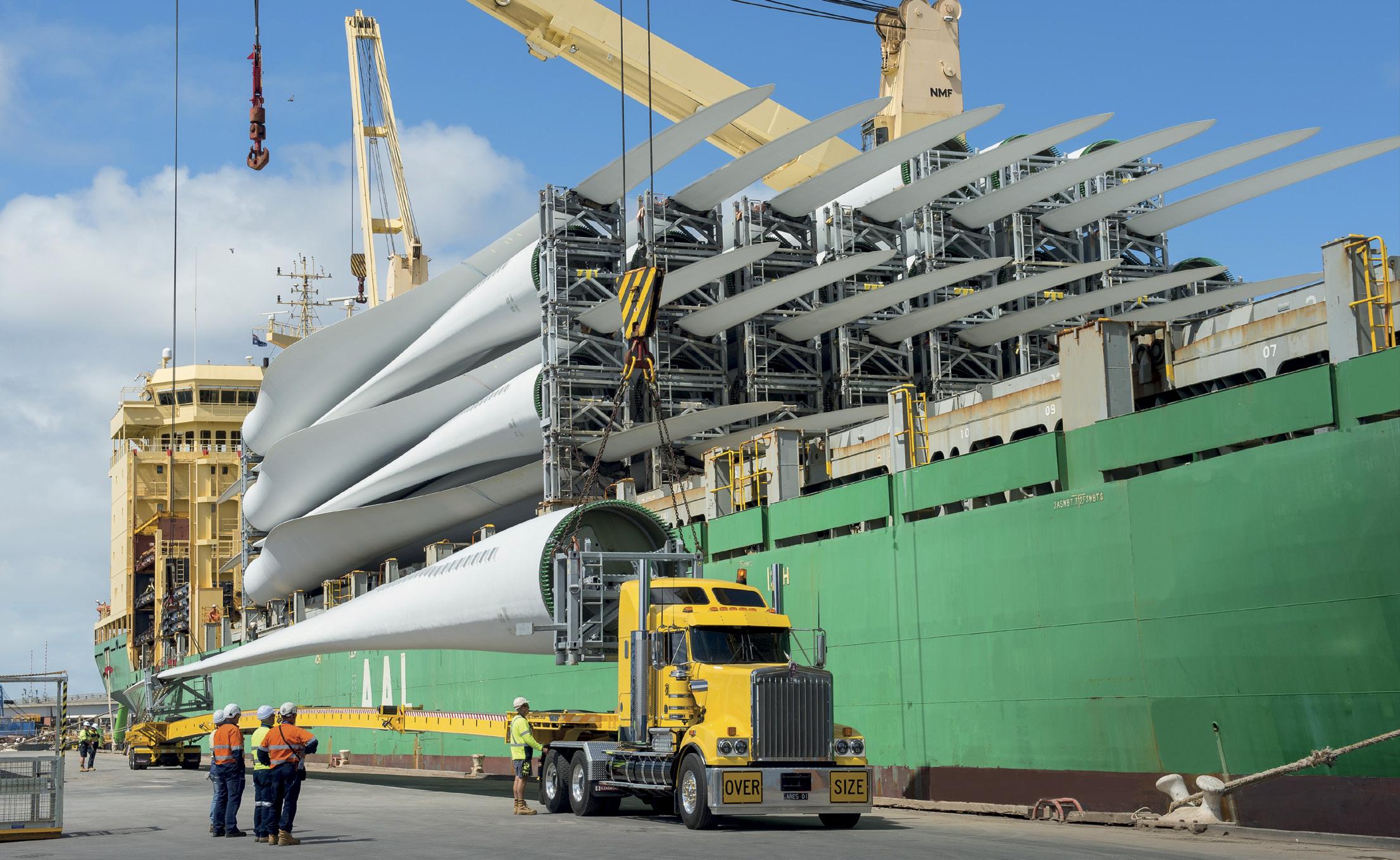
Altered Future for Intermediaries in Post-pandemic World BY CARLY FIELDS
Multipurpose ships booked out to mid-2022, hyperinflated freight rates and a new wave of container clients with different demands have all combined to put pressure on relationships throughout the project cargo supply chain. Intermediaries – carrying the weight of that burden – are sprinting to maintain some sense of normality as they strive to meet everyone’s needs.
Sharply rising shipping costs have brought volatility and unpredictability for ocean freight capacity to the market. This has impacted every aspect of the global supply chain, not only in high-value and complex projects, but also in the lower-value retail and manufacturing sectors, pointed out Tim Killen, executive vice president of deugro group. And commercial volatility has combined with a lack of available vessel space to hit operational performance. With new build capacity not expected to supplement existing supply until late 2022, Killen expected freight rates would continue to push new highs this year and will likely remain above prepandemic levels in the longer term.
“This unprecedented change means that we will need to continue to change the way that we work within the project cargo industry. Working across the supply chain both with clients and carriers to increase lead times for planning and scheduling shipments
and building more commercial and operational predictability to be able to plan, collaborate and optimize project cargo to meet new budgets and construction schedule requirements.” Forwarders and agents not only need to appreciate the changing needs of clients and the impact on partners, they also need to adapt to these challenges and design new tangible, value-added solutions. “The last two Tim Killen years have proven that anything can happen, and as a project freight fordeugro warder we need to remain agile in our decision-making and continue to provide the industry with innovative solutions that reduce supply chain risk and costs, while ensuring the highest level of QHSES.”
WHO’S THE BOSS?
The client base itself has also transformed, with traditional multipurpose
Top: Relations with intermediaries have been thrown into sharp relief by the pandemic. CREDIT: AAL SHIPPING
intermediaries finding themselves at the sharp end of the container trade this year. Marc Willim, general manager chartering at AAL Shipping, describes the Marc Willim wave of new clients that have AAL Shipping emerged over the past 12 months as “less to do with Covid-19 and more the container capacity shortage in 2021.” He noted that the container segment is “very different from the traditional MPV markets we have served, in that the immediate shortage of space and tonnage has ‘lit a fuse’ under negotiations with container lines and container shippers – effectively shortening negotiation times and driving out spot bookings in favor of longer-term contracts of affreightment.”
Client demands have shifted too. Killen relayed how the pandemic saw project clients home in on maintaining planned and safe logistics operations in order to meet the schedules and budgets established before the pandemic started. “The focus was on ensuring security of supply, managing QHSES and providing business continuity and capacity through one of the most challenging periods in recent history.”
Thomas Skellingsted, vice president and global head of 4D, agreed that client demands have evolved to overcome reduced sailings, less availability and higher prices. Clients are now seeking “commercial assurance Thomas Skellingsted for their projects, to try and ensure that they can be 4D executed in line with the budgets created before and following the Covid-19 pandemic.”
Secondly, clients are demanding more operational and schedule visibility and assurance in order to overcome the impacts faced.
Thirdly, Skellingsted said, the focus also remains on providing safety and security for all workers during the planning execution activities of global projects, along with ensuring both the physical and mental well-being of people is maintained. “This has been, and will remain, a major challenge at a time when global mobility and availability of experienced personnel has been significantly impacted by the pandemic and current market conditions.”
IMPORTANCE OF RELATIONSHIPS
Maintaining relationships with intermediaries, albeit virtually, has been paramount over the past 24 months. Willim said that relationships have stayed “remarkably strong,” even if the mode of communication has changed. “We have got to know and work with a large cross section of forwarders and other types of intermediaries and shippers trading multipurpose, steel and dry bulk cargo between these regions. As of today, nothing has changed in the market dynamic to impact these relationships or essence of doing business – whether our counter parties are intermediaries or cargo owners.”
However, change is on the horizon. With MPV tonnage booked to the middle, and in some sizes to the end of 2022, Willim expects to see a “tightening” of relationships as the fight intensifies for the available space. This, he says, will be especially true on highdemand trades, like Asia outbound to U.S., Europe and Australia – trades that AAL serves regularly. And while a significant portion of the MPV fleet is serving the container trades, Willim said that AAL is still prioritizing breakbulk and project heavy-lift cargoes.
ENABLERS OF PROJECT LOGISTICS
Immediate visibility, predictability, transparency, integration ... these are no longer luxuries for the services provided by intermediaries; they are essential and enablers for joined up project logistics. 4D’s Vice President and Global Head Thomas Skellingsted said it is increasingly common to see IT solutions for the planning, budgeting and movement of project cargo.
“Today, project clients have a higher demand for end-to-end transparency of both their inbound and outbound supply chains in order to support data-driven decision-making for their procurement, manufacturing and consolidation activities. Therefore, the need for integrated IT solutions is paramount, providing more detailed KPI reporting to enable confident data-based decision-making to be made by our clients within project freight forwarding activities.” deugro group’s Tim Killen sees integrated digitalization tools as a “critical requirement” across the supply chain. “The benefits in operating with integrated IT systems also allow us to be able to better plan, schedule and operate with clients or partners, to work more efficiently and effectively on all aspects of logistics from procurement to inspection, consolidation and document management.”
But with this increased dependency on integrated technology comes the specter of cyberattacks. “The reality is that this threat is a critical risk to our industry and requires us to invest heavily in this complex matter to ensure we have strong protocols and systems to minimize the risk of business interruptions and loss of key global data,” Killen noted. deugro commissions internal and external security penetration tests by specialist security firms and organizes regular cyber training sessions and exercises for its staff.
Forwarders need to up their game to meet this “tightening.” deugro is banking on diversification strategies in the changing industries and geographies it covers, and also with regards to the services provided to its clients. “Thinking outside the box of traditional project freight forwarding, we have invested in new assets and facilities, a global transport engineering business, supply chain consultancy specialist as well as online continuous professional development training tools,” Killen said. Looking beyond the pandemic, these diversification activities have given deugro strength and added depth to its toolbox, he added.
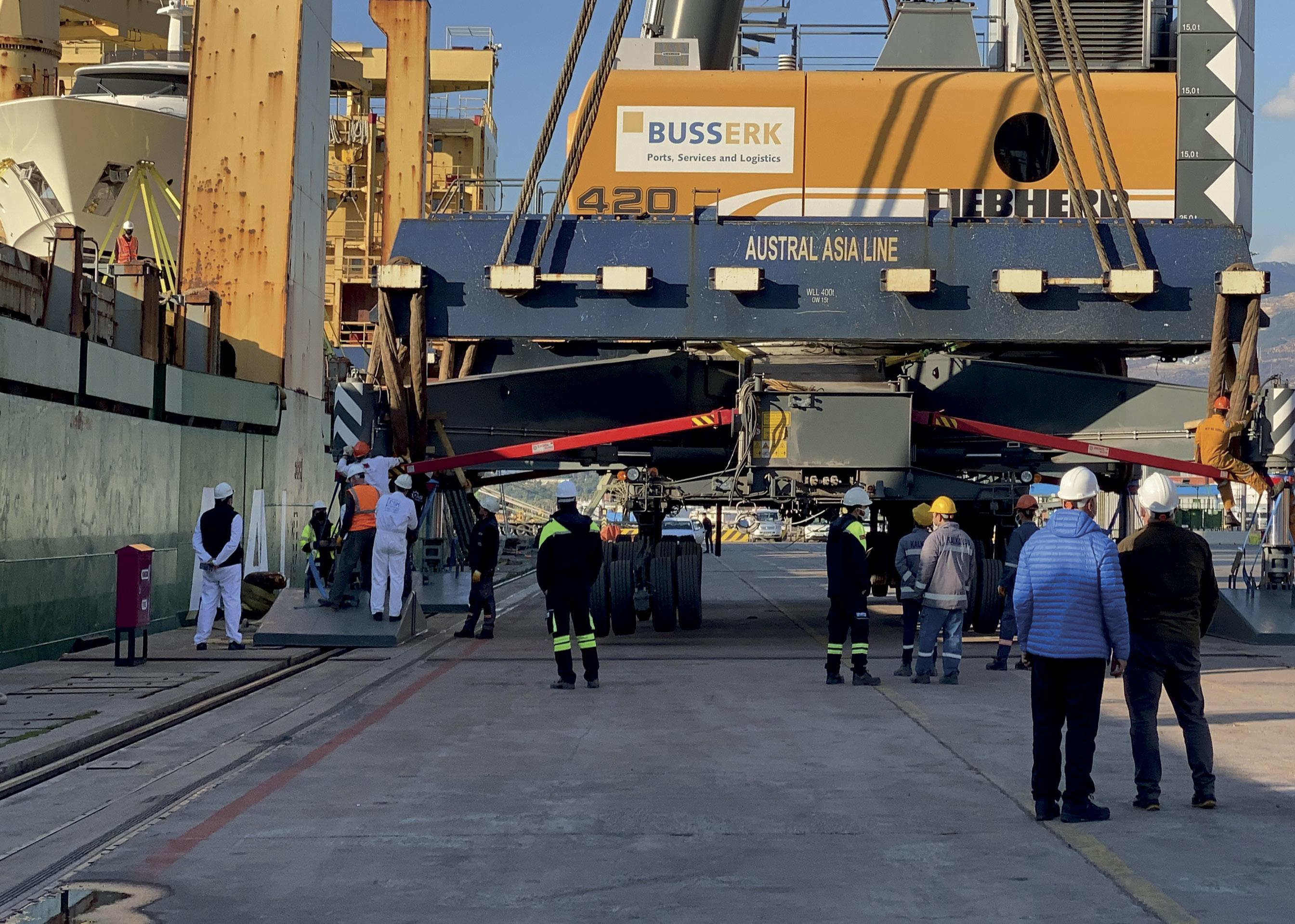
PILLARS FOR SUCCESS
Killen added that the three key pillars for project logistics success have always been people, processes and systems.
“So, we must ensure that we invest and continue to develop and improve in these three critical areas of importance.” deugro follows a six-step project risk assessment to assess the needs of a project and develop safe and secure project logistics solutions. This risk assessment process includes detailed investigations into major factors that are critical to designing and delivering economic, safe and efficient risk planning and execution for complex project cargo movements.
The six steps are: • Cargo details. • Required resources. • Infrastructure assessments. • Governmental and regulatory requirements. • Legal and regulatory (including CSR). • Environmental and sustainability.
“The challenges that the market has experienced over the last two years – including Covid-19, carbon reduction, cargo space constraints and the exciting investment in the energy transition – require us all to be able to react quickly and flexibly to dynamic challenges, and the investment and development of our teams will become even more important in the future,” Killen said.
Ulrich Ulrichs, CEO of BBC Chartering, would like to see the way forwarders select operators evolve. He called for an improvement in and/or development of due diligence on the ability of carriers to perform what they promise, and asking that forwarders “make sure they partner with reliable carriers with proven track records and HSEQ routines.”
With all the existing and mounting pressures on intermediaries, is it inevitable that the sector will see more mergers or collapses of forwarders or agents? Possibly, Killen said. “The current global unpredictability, along with financial and contracting risk pressures, will likely have an impact throughout the supply chain and will hit both manufacturing and logistics service providers. Rising commodity and logistics costs are already affecting the industry.” Couple this with the global focus to move away from traditional oil and gas projects, diversifying energy demands and low-carbon green energy technology investment, and the future of the project logistics industry is uncertain, he said. “This could place major risks on the logistics and supply chain sector, since traditional business models and services may no longer be viable to secure the necessary financial rewards seen in the last decade.”
But it’s not all doom and gloom. Killen described the freight forwarding industry as resilient and adept at re-invention. So, while there may be further mergers and acquisitions – and a concomitant change in operating models – experienced personnel will still be needed at the heart of the industry to navigate through these waters, he said. BB
Forwarders and agents have had to adapt quickly to challenges and design new tangible, value-added solutions. CREDIT: AAL SHIPPING
Carly Fields has reported on the shipping industry for the past 21 years, covering bunkers and broking and much in between.
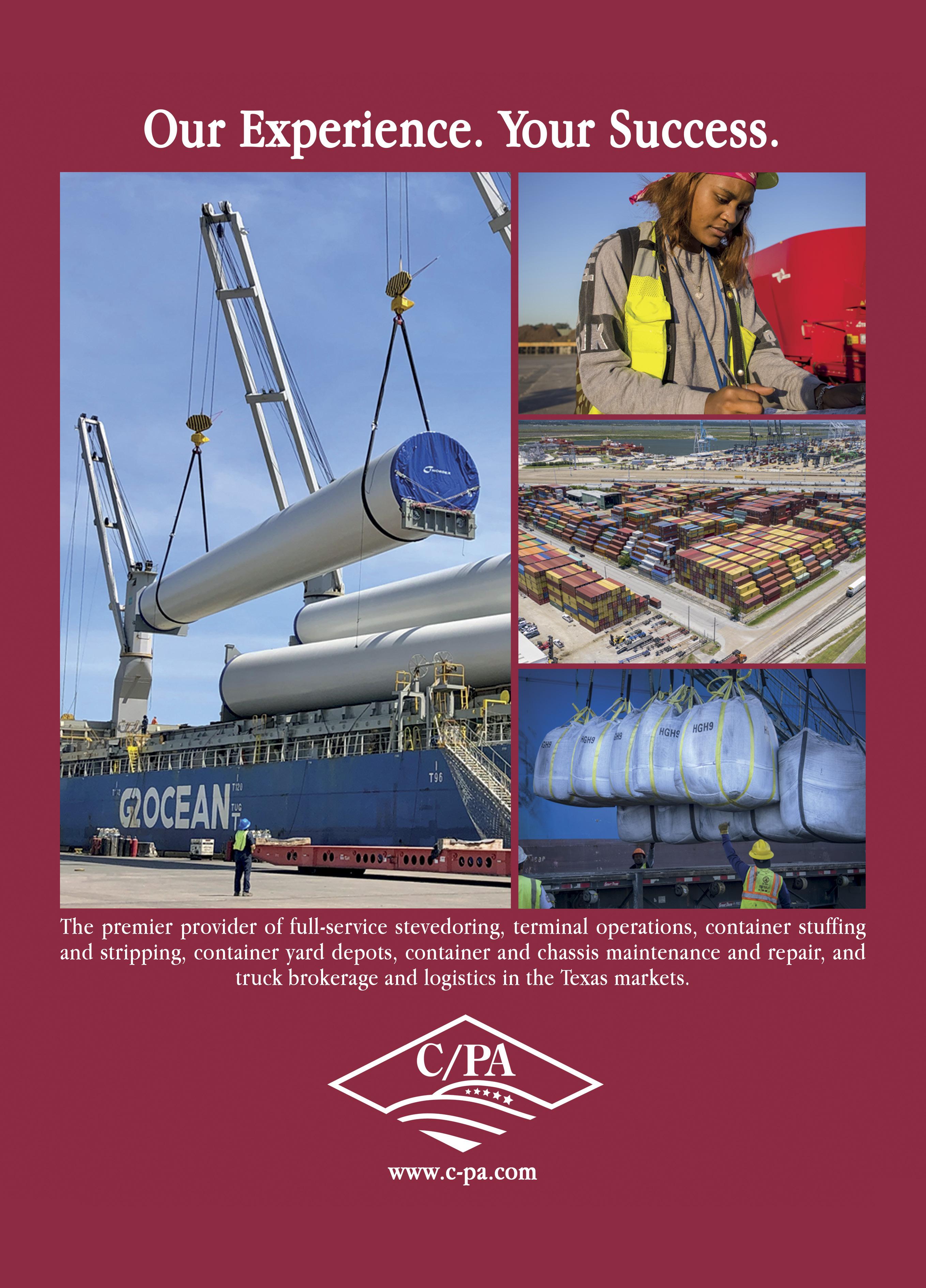
PORTS & TERMINALS
LOGISTICS RIPE FOR TRANSFORMATION
Middle East Digital Revolution Gathers Speed BY FELICITY LANDON
Earlier this year, Abu Dhabi Terminals unveiled a new AI-focused partnership with Microsoft, which promises to enhance container tracking and autonomous shuttle capabilities at Khalifa Port.
The new tech will enable the introduction of AI-based smart tracking solutions that will give 100 percent traceability of containers, and is part of a commitment to reduce carbon, costs and turnround times at the port.
Containers are seen as the natural target for the digital transformation of ports, but they are by no means the only opportunity. Efficiency in handling breakbulk and project cargoes could also be driven forward with the right digital solutions – or, to put it the other way, a lack of tracking and visibility can create a variety of risks, says Jonathan Koh, managing director at Trade Facilitation Pte Ltd.
For an extreme example, he points to the catastrophe in Lebanon last year, when 2,750 tonnes of ammonium nitrate stored unsafely at the Port of Beirut in a warehouse for almost six years exploded.
“The cargo was left in the warehouse for years. It was destined for another place, but the authorities intervened, and the cargo was offloaded in Beirut. Because there was not a proper system, it was ‘forgotten’ until the explosion,” he said. “I think that is the story behind breakbulk – if the clearance is not done, the cargo is forgotten and can end up stored with inadequate ventilation or in other poor conditions, perhaps exposed to the weather, not under cover, difficult to trace within the port parameters and also, then, susceptible to pilferage.
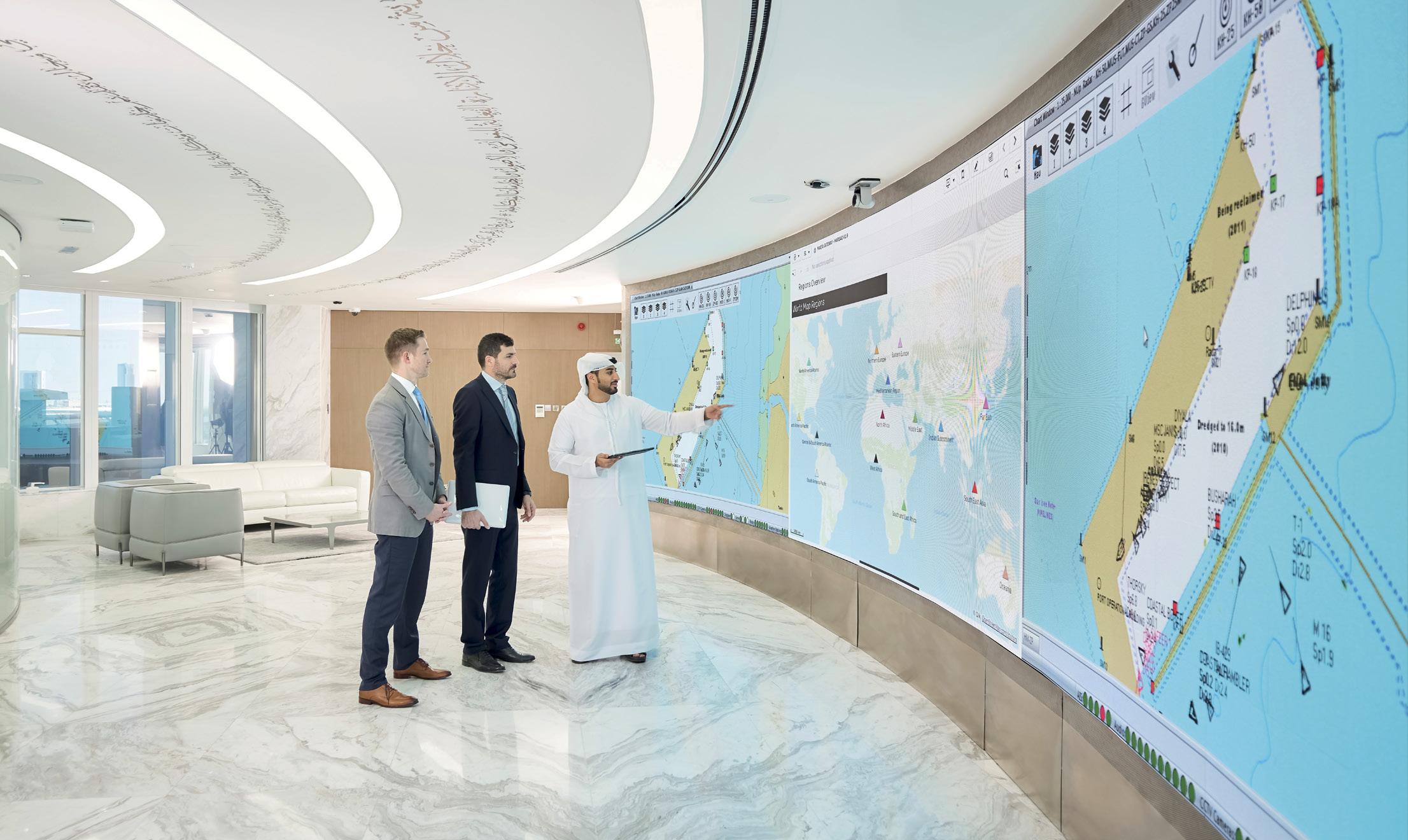
“You want to minimize the time spent for such breakbulk materials to be left or forgotten in the port.”
STORAGE HIERARCHY
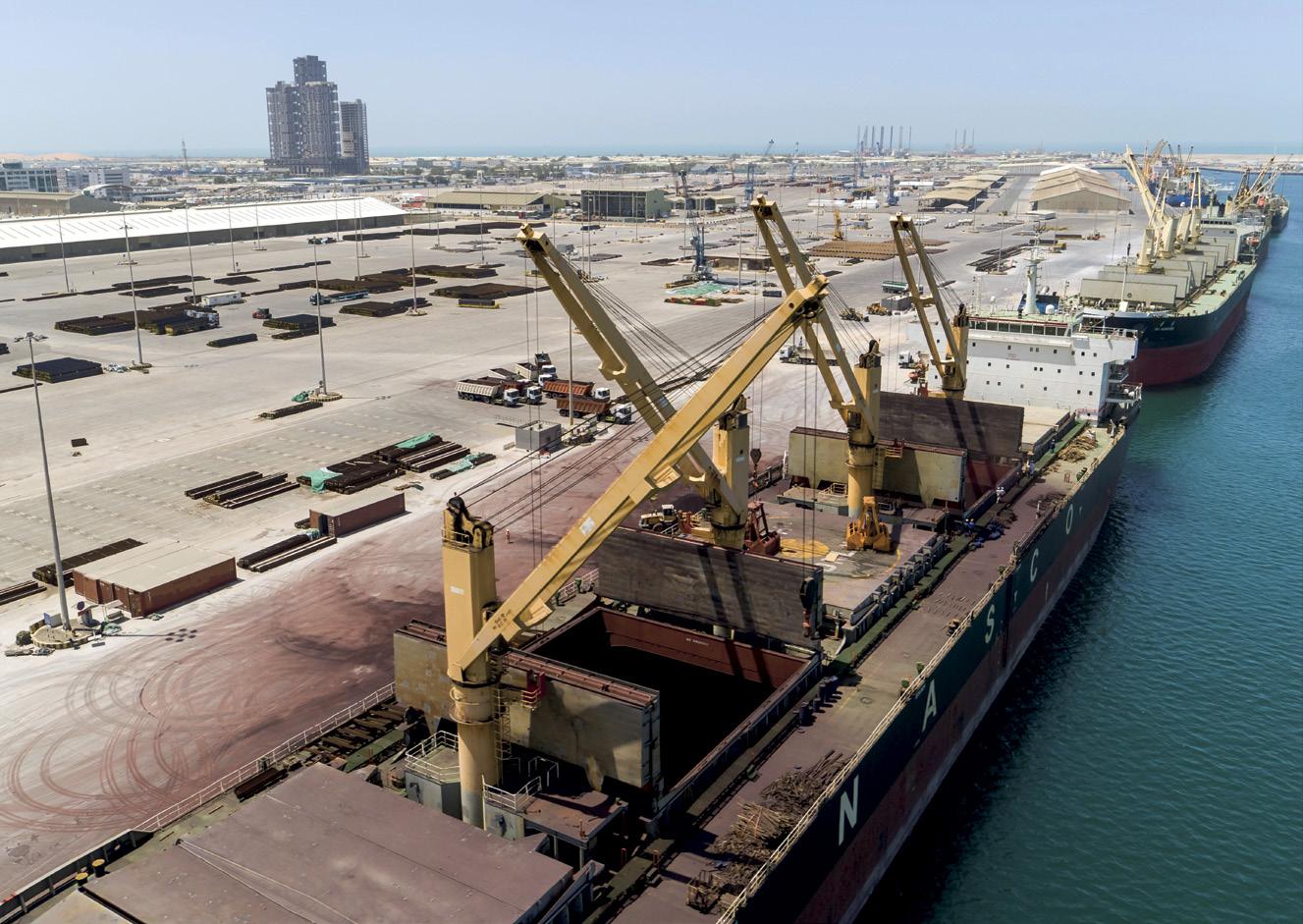
In ports facing congestion issues, containers are usually top of the storage hierarchy, Koh pointed out. “Breakbulk is likely to have a more limited area – ports will put it ‘wherever’ and it can be very difficult to track down because it doesn’t have a container number.”
The reality is that breakbulk items are often not properly stored, managed or tracked in a port; they can end up in an out-of-the-way yard which even Marie Kondo couldn’t sort out, Koh said. “It happens quite a lot – you will find rolls of steel, tires, sacks of flour.”
The introduction of a Single Window system could cover breakbulk cargoes just as effectively as containers and other cargoes, he said. “In the end it is about efficiency of the port operation. But it is also about costs – a port will only give a certain number of days when there is no charge for storage, to allow for the clearance process to happen.”
If the bureaucracy is inefficient and cargoes get delayed, storage charges start to build up. “There lies the concern, because your materials may not be under the roof. And you are paying the costs.”
Koh has recently been working on a project in Saudi Arabia to increase efficiencies around the country’s industrial exemption rules. He said this project would be applicable in many other Gulf Cooperation Council countries.
“Raw materials required for production, which are typically breakbulk, cement, steel and even large machinery for production, can come in under the industrial exemption scheme, as long as the importer, manufacturer or factory owner can justify that these materials are for manufacturing or value-added activities inside the country.
“When an application for industrial exemption is confirmed, duties and taxes can be deferred indefinitely. This is a common regulation across
“It would be resolved by a Single Window. What Customs wants is verification so when the cargo comes to the port and you produce the license number for the factory, Customs can seek verification. A Single Window would enable faster verification, reconciliation and clearance.
“At present, some people with the exemption are complaining that their cargo, although having the exemption, still has to spend a long time waiting for clearance. The reason is the break in communication and that is a typical, common occurrence.”
the GCC and applies to materials for production and construction, even production of finished goods for domestic consumption – they don’t have to be re-exported. The exemption of duty together with VAT can be substantial.”
However, the system throws up bureaucratic challenges. The factory or manufacturer, who is the consignee, must deal with the government department that grants the exemption – but once the exemption is confirmed, the actual checking is done by Customs.
“It may not be necessarily seamless – there might be breaks in communication between the industry agency and Customs, and that means delays. At present, a factory will have one license number which can be used like a multi-entry visa for the stipulated breakbulk materials. However, when the products enter the country, you are facing another authority, and there lies the problem.” Sometimes the license will indicate a quote for the factory; each time the goods come in, the authorities at the border will carry out reconciliation of the quota. There can be a lot of paperwork and delays which can mean the cargo is stuck in the port.
Koh’s work involved analyzing a way to bring business and exemption application processing into a national Single Window, and so streamline the system.
Introducing a Single Window system could cover breakbulk as effectively as containers and other cargoes.
CREDIT: ABU DHABI PORTS
WHY SUCH SLOW ADOPTION?
Among the industries that have shown a lot of interest in digital technology, logistics is “like a stepbrother,” said Meenal Madavi, business head at Oman-based Khimji Ramdas ITC, or KITC.
“It is surprising that adoption has taken so long – logistics should have been one of the first to get on the digital technology wave,” she said. “In the end, the entire world trade depends on how good your digital platforms are for the exchange of data.”
Two years ago, KITC announced a partnership with India’s Kale Logistics Solutions to accelerate trade facilitation, developing services “to spur more value for clients in the logistics industry.”
A Single Window cargo processing system would enable faster verification, reconciliation and clearance of breakbulk cargoes.
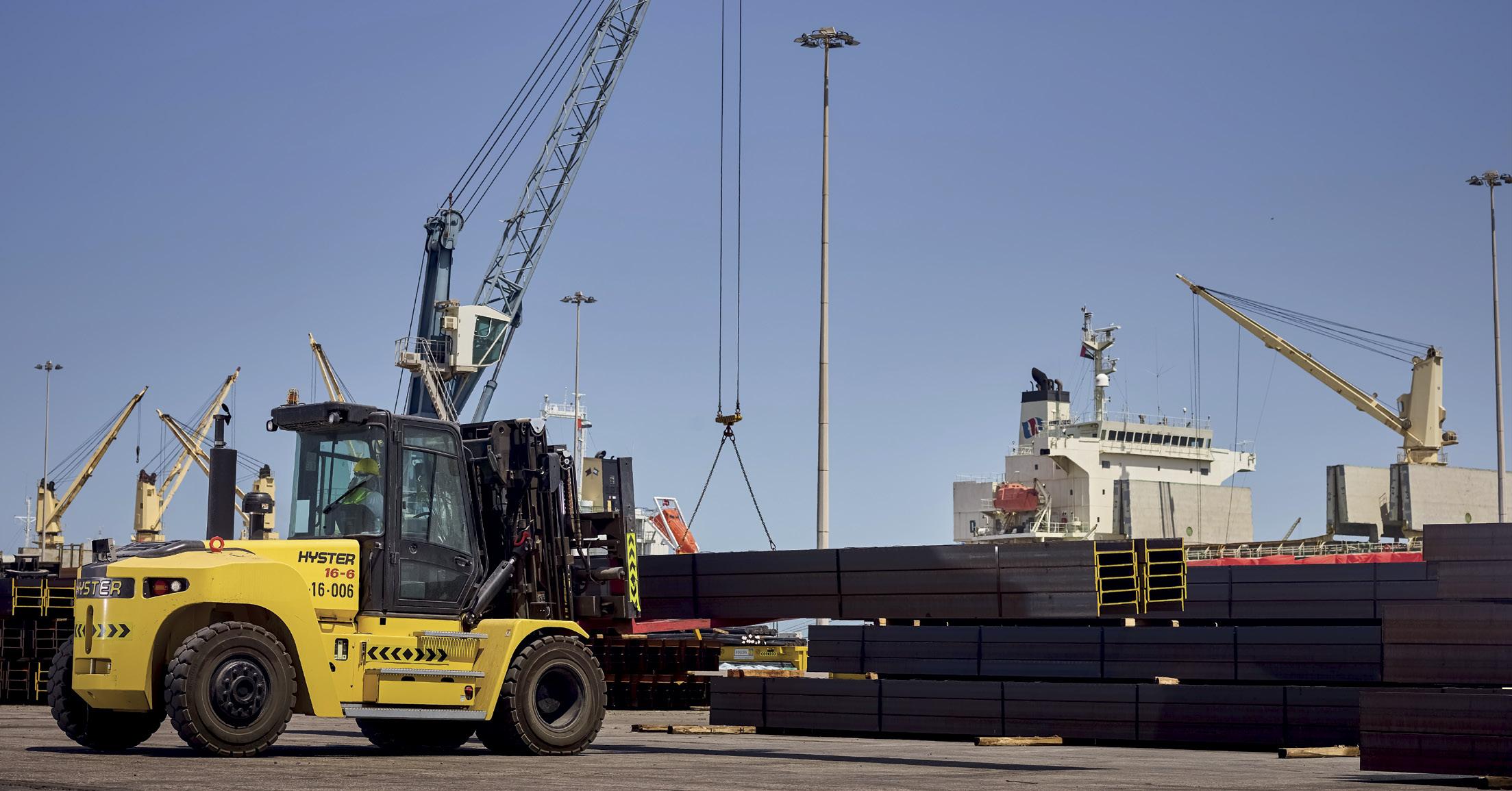
CREDIT: ABU DHABI PORTS
Oman has set out its ambitions to become a key logistics hub for the Middle East region, with logistics being one of five major industries being targeted as the country diversifies its economy away from its reliance on oil (the others being fishing, mining, tourism and manufacturing). The vision is to become a global logistics hub by 2040, increasing the sector’s contribution to GDP to RO14 billion by then.
“Logistics comes very naturally to the region because of the wonderful location between East and West, with good access to Asia and even better access to the Arab world, Turkey and Europe,” Madavi said. “To optimize any industry and compete worldwide, you need investment in technology.
“With that view, KITC decided to focus on investing in each of the five sunrise industries. For logistics, Kale makes the perfect partner with its great credentials in this particular domain, especially in African and Asian countries – they understand the bureaucracy and how to work with this and still have success. Their technical and functional understanding of the industry is what really struck us. They bring the expertise from the tech/logistics standpoint and we bring our expertise from the local Oman perspective.”
Oman, with its strategic location, has plans for a semi-processing and packaging industry for insourced goods from Asia, she explained.
KITC is working with Kale on two government-related projects: creating a terminal operating system for a dryport and a digital corridor for the fishing ministry. This second project will cover the entire logistics of fishing, including equipment required for fishing ports and processing, and the processed goods coming out.
Meanwhile, the partners are working on numerous projects for private entities, around automation of warehousing and forwarding. “The need for more digitalization across all the zones of logistics is huge, whether oil and gas, fishing or manufacturing, and that includes breakbulk and project cargoes,” Madavi said. “Visibility directly translates to revenue.”
Digitalization has gained a lot of recognition now in the GCC region – both industries and consumers are waking up to it, she added. “Why should the logistics industry be left behind? Why should we get yards of paper and printouts, when it can be better managed with digital solutions?”
REGIONAL LOGISTICS FOCUS
Oman is not alone in its logistics ambitions. Saudi Arabia and the UAE are targeting the sector in their diversification strategies. Spain’s warehouse automation specialist SmartLog Group has announced it is entering these markets. Gonzalo Gomez, new markets research manager, noted that the group expects an increase in warehouse automation across the Middle East. “However, e-commerce businesses will not be the only concerned players. General retail, pharmaceutical, hospital and healthcare, and other industrial sectors will become drivers of innovation throughout the warehouse automation sector in the region,” he told local press.
Gulftainer, whose operations include Khorfakkan Container Terminal, Sharjah Container Terminal and Sharjah Inland Container Depot in the UAE as well as terminal operations in Iraq and Saudi Arabia, ran a year-long Future of Ports 2021 event, in line with its digital transformation drive. Tech startups were invited to submit disruptive ideas to transform ports and there were more than 2,000 submissions across various categories including the Internet of Things and robo-doctors, artificial intelligence and autonomous drones, big data and advanced analytics, and blockchain.
Four winners were selected to pilot their projects: • ZaiNar, providing real-time 3D location tracking. • eYard, using AI to analyze thousands of potential operational scenarios to make ports smarter, eliminating unproductive moves and optimizing delivery time and storage space. • ThroughPut, using Big Data to optimize supply chains and address operational bottlenecks. • Morpheus Networks, winner of the blockchain category, providing a SaaS platform for data sharing and visibility across the supply chain.
Felicity Landon is an award-winning freelance journalist specializing in the ports, shipping, transport and logistics sectors.
EXPANDING DIGITAL SOLUTIONS FOR BREAKBULK
There are clear opportunities for digitalization to make a difference in the breakbulk and project cargo sector, according to the Abu Dhabi Ports Group. “Digital end-to-end planning and management tools will create greater visibility across the shipping cycle and ensure more effective tracking, faster delivery times and greater efficiency,” said Noura Al Dhaheri, head of the digital cluster at AD Ports Group and CEO of Maqta Gateway. “In addition, the move from paperbased processes to digital, automated processes delivers significant benefits across the transportation chain, Al Dhaheri including greater data transparency and online coordination.” AD Ports Group A key part of the group’s strategy is expanding its capacity for general cargo and breakbulk, primarily through Khalifa Port’s South Quay and Khalifa Port Logistics, which are at the heart of an ongoing expansion project. Once complete, this work will add 6.2 kilometers of dedicated quay with depths ranging from 8 to 18.5 meters at the deepwater port.
“As a fully integrated operation, we are ensuring that all digital implementations mirror our investment in infrastructure – enabling us to manage higher volumes of general cargo and breakbulk and deliver a seamless and improved customer experience,” Al Dhaheri said. AD Ports Group has invested significantly in digital since its establishment, she said, including building the first semiautomated terminal in the region at Khalifa Port.
Maqta Gateway, the group’s digital subsidiary, developed the region’s first Port Community System, a digital platform solution that provides a single window facilitating information flow between all stakeholders, port authorities and traders, and which has already delivered millions of dollars in efficiency savings, Al Dhaheri said. The group’s Digital Cluster is built around five product lines: Single Window Solutions, marketplaces, smart devices and solutions, consultancy services and digital technology services. Among the services, a mobile app, Manara, enables real-time updates of the status of shipments as they reach their destination, as well as tracking transactions. The Masaha app enables customers to access all the information and services provided by Khalifa Industrial Zone Abu Dhabi. Silsal, a home-grown blockchain technology, is offered to freight forwarders and their customers, and will be extended to the rest of the trade community. Margo Hub is a digital logistics marketplace and aggregator which, in addition to air and sea freight solutions, offers warehousing, truck booking, express parcel, and last-mile delivery services.
INTRODUCING AUTONOMY
At Khalifa Port, CSP Abu Dhabi container terminal, COSCO Shipping Ports Ltd.’s greenfield project, will soon become the first terminal in the Middle East to introduce an autonomous port truck system. Six electric Qomolo Q-Trucks, equipped with a 360-degree sensory system with traffic monitoring and driving guidance system, will support mother vessel loading and unloading activities within the container yard.
Last year saw the launch of the Advanced Trade & Logistics Platform, developed and operated by Maqta Gateway under the supervision of the Abu Dhabi Department of Economic Development. Featuring more than 700 services and unified payment solutions, the platform serves as Abu Dhabi’s single window trade platform for all economic operators via sea, land, air, industrial and free zones. “It is greatly enhancing the customer experience across Abu Dhabi’s trade and logistics landscape,” Al Dhaheri said.
AD Ports Group sees a major opportunity to deploy digital innovations to improve sustainability throughout the value chain, she added.
“Nations are implementing aggressive net zero targets and we are deploying advanced technology to monitor and manage the emissions and waste created by global trade, including breakbulk.”
As an example, mUnity, developed by Maqta Gateway, is a custom-built system that uses blockchain technology to manage Covid-19 vaccines – tracking and tracing vaccine sourcing, storage, shipment and all related data in real-time at every step of the journey by Hope Consortium, an Abu Dhabi-led public-private partnership delivering large quantities of vaccines globally.
The system features end-to-end visibility of every vaccine, from the manufacturing facility to when they arrive at vaccination centers in the UAE and other destinations worldwide. “Based on the availability of data, the system has the capability to track individual vaccine doses up until the time of the administration of the dose,” Al Dhaheri said. “This solution can be applied to other supply chains and commodities.” BB
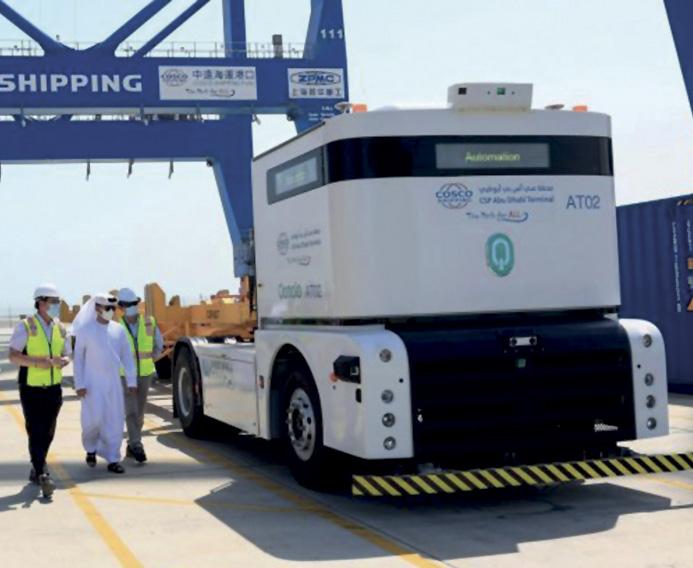
An autonomous port truck system at Khalifa Port will support mother vessel loading and unloading activities. CREDIT: ABU DHABI PORTS
RULES & REGULATIONS
PESTS IN THE HOLD
Drive to Tackle Rising Biosecurity Risks BY IAIN MACINTYRE
Industry stakeholders are calling for more measures to mitigate increasing risks of invasive species being carried in packing and bracing materials used in global project and breakbulk cargo shipping.
Amid heightened awareness of microbiological risks in the world of Covid-19 and the reality of ever-growing global trade presenting increasing opportunities for inadvertent pest incursion, greater scrutiny is being drawn on relevant practices and standards.
Faith Campbell, environmental advocate with the U.S. Center for Invasive Species Prevention, said it is “clear” that the threats presented by pests transported into native ecosystems are “global and urgent.”
“The procedure required by ISPM 15 [International Standards for Phytosanitary Measures No.15], was never adequate to curtail pest introductions,” Campbell said to Breakbulk.
Campbell cited 2010-2015 data released by U.S. Customs and Border Protection – no longer published – that “approximately 97 percent of the wood packaging shipments harboring quarantine pests bear the ISPM 15 stamp.”
“A study of imports of stone from China into Europe by Eyre et al, showed the same proportion of shipments harboring pests to be in wood bearing the ISPM 15 stamp – this indicates to me that the problem is global.”
Campbell believed there are three possible reasons why such infestation could be taking place: • The wood was never treated but the provider/exporter stamped it – “this is fraud.” • The wood was treated but the treatment did not work – “this could result either from carelessness/ negligence by the provider or from a mistake.” • Wood was treated but the treatment was inadequate.
“U.S. government inspectors tell me that dunnage is more often in violation because of a pest presence; crates and pallets because they lack the stamp. I know U.S. importers think the treatments are inadequate when it comes to large pieces of wood – as dunnage often is. This might explain why pests are present in dunnage.
“As far as I know, no country is undertaking serious studies to try to sort out the relative importance of each of the possible reasons. I consider this failure to pursue the causes of infested but stamped wood to be negligence on the part of the National Plant Protection Organizations, or NPPOs.”
Campbell said that the problem of stamped but infested wood is widespread, and the highest numbers of non-compliant wood intercepted by U.S. inspectors come from Mexico, China and Turkey.
“In past years, Italy and Costa Rica also ranked high in interceptions at U.S. borders. In the case of Italy, the pests were usually snails on crates carrying marble or tile. Of course, snails are not a violation of ISPM 15 because it applies to designated families of insects; however, snails are a significant phytosanitary threat,” she said.
RALLYING CALL FROM CIG
Recognizing the vital importance of focusing on the threat of invasive pests to natural resources across the world, the Cargo Integrity Group, or CIG, has called on actors in global supply chains to take “urgent action.”
CIG, which was formed by five global freight transport organizations, said that otherwise the International Plant Protection Convention, or IPPC, may itself take “all-encompassing, internationally-imposed steps to mitigate such risks.”
Such measures could have significant impact on global trade when it comes to both time and cost, noted the CIG.
Mike Yarwood, loss prevention managing director, TT Club – whose organization is a CIG member – said there are long-term benefits in globally embracing the issues.
“The prompt now is generated by a heightened awareness of the risk of visible pests being moved through the international supply chain and the potential damaging effects of invasive animals and plants being unwittingly introduced to other countries,” he said. “Greater awareness will lead to greater understanding of the challenge
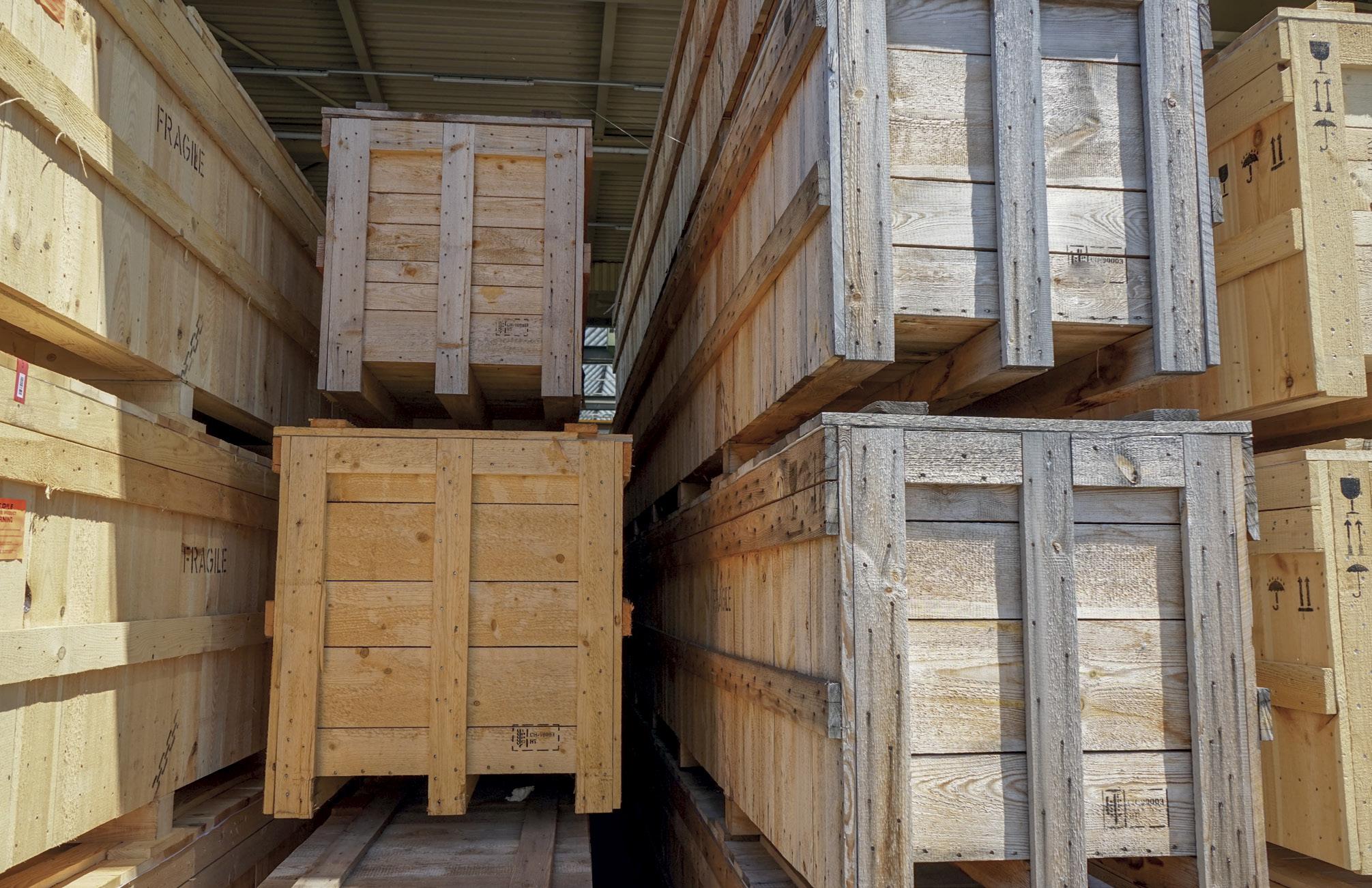
Virtually all of the wood packaging shipments harboring quarantine pests bear the ISPM 15 stamp. CREDIT: SHUTTERSTOCK
and how individual businesses and industries could have a positive impact on improving current practices.”
Yarwood drew attention to the following statement within the United Nations’ declaration of 2020 as the International Year of Plant Health: “The year is a once-in-a-lifetime opportunity to raise global awareness on how protecting plant health can help end hunger, reduce poverty, protect the environment and boost economic development.”
While acknowledging the recent CIG call to action had a particular container-shipping focus, Yarwood said the sentiment is equally applicable to all international trade – including breakbulk.
“Similar risks and principals exist. The risk continues to exist with dunnage, crates, packaging and potentially the cargo itself, depending on how and where it has been manufactured, stored, prepared and transported.”
Richard Steele, chief executive of the International Cargo Handling Coordination Association, said his organization and fellow CIG partners are aware that this is a marathon, not a sprint. “Many involved in the supply chain are still learning about the challenges associated with invasive pests and what they can do practically to prevent their spread,” he said.
A key part of the CIG Partners’ work is to raise awareness of the guidance in the Code of Practice for the Packing of Cargo Transport Units, or CTU, Code and Quick Guide. While the demands placed on shippers mean that the CIG is competing for airtime among a range of priorities, Steele stressed that this is not just about shippers, it is about working together at all stages of the cargo supply chain.
“No one actor alone can deliver what is needed. If we only spotlight one part of the chain, we limit our opportunities to succeed,” he said.
James Hookham, director of the Global Shippers Forum – another CIG partner – emphasized that appropriately-heightened biosecurity measures should not come at the cost of unduly hampering or burdening global trade. “Some of the businesses most likely to be impacted by an invasive species are often among that nation’s biggest exporters – i.e., shippers – and supporters of stricter biosecurity controls,” he said. “However, most governments that are battling this issue recognize the impact on trade if biosecurity measures are too onerous and expensive to comply with. Hence the need for risk assessment and cost effectiveness of any global measures that are introduced.”
He called for a more proactive program by governments to highlight the issue and the ways of avoiding it.
Yarwood added that certain
Biosecurity issues are increasingly on the radar of breakbulk carriers. CREDIT: SHUTTERSTOCK
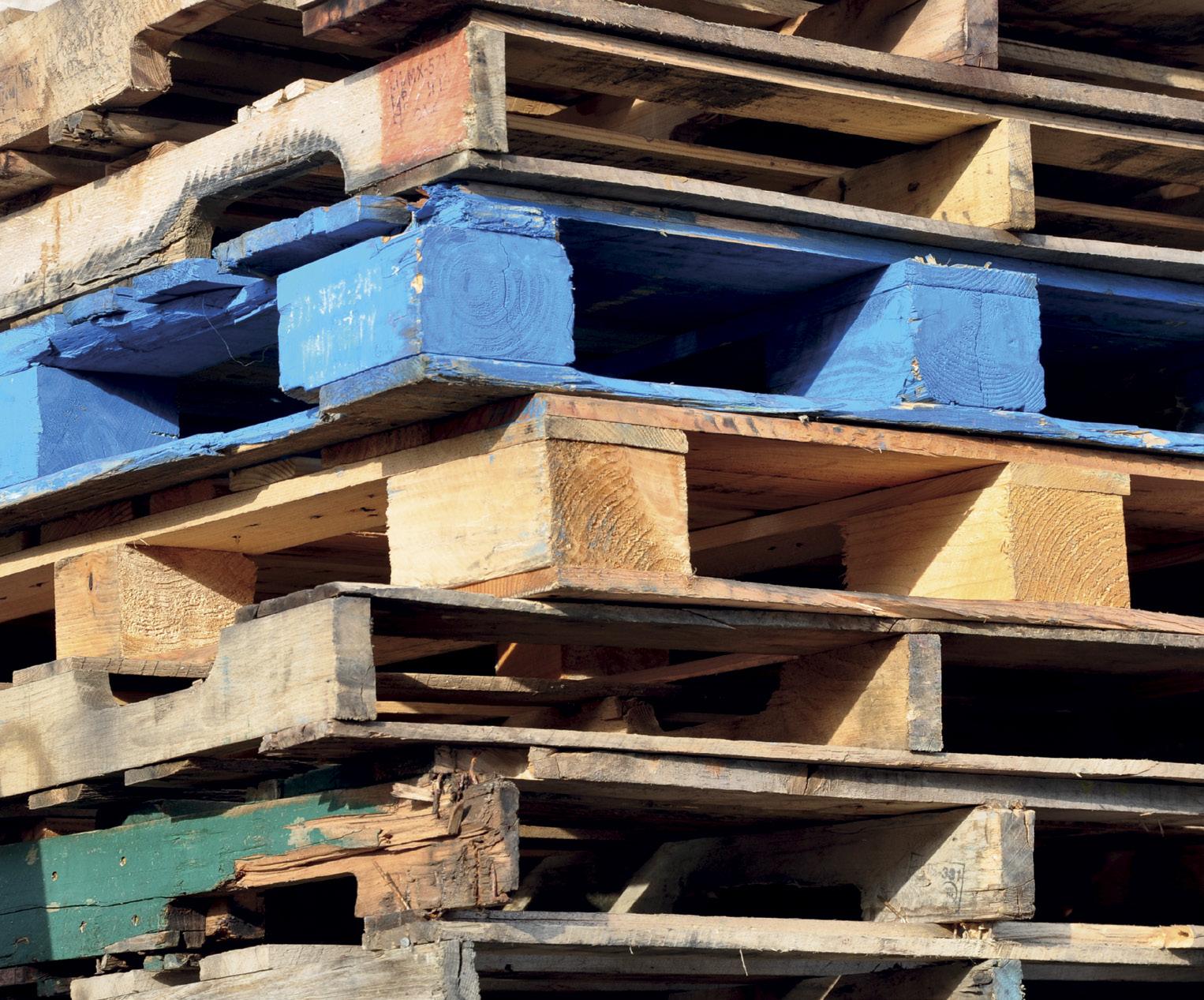
national governments are already demanding more rigorous action and proposing regulation, either nationally or internationally, to prevent the unwanted and generally inadvertent transfer of invasive plant and animal species. “Should joint government/ business activities be deemed insufficient or ineffective, mandatory requirements will almost certainly load disproportionate – and unwelcome – compliance and enforcement costs across the industry,” he said.
FIVE REMEDIES URGED
Center for Invasive Species Prevention’s Campbell puts forward five key measures to reduce the risk of pest incursion in packing and bracing materials used for project cargo and breakbulk shipping. • NPPOs of importing countries should penalize violators for each violation. “ISPM 15 was sent to IPPC member countries for their adoption 19 years ago – it is time that countries were serious about it.” • NPPOs of importing countries should complete studies to define the relative importance of fraud, misapplication of treatments and inadequacy of treatments in causing the continued
OUR CONSTRUCTION POWER FOR YOUR PROJECT SUCCESS.
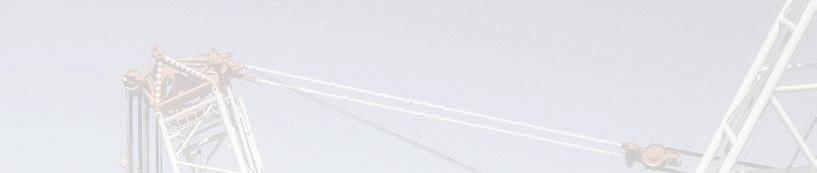
Benefi t from our innovative 360° concept for your crane, transport and logistics projects. Our performance plus: We consistently provide cutting-edge technology and expert knowledge to ensure your project’s success.
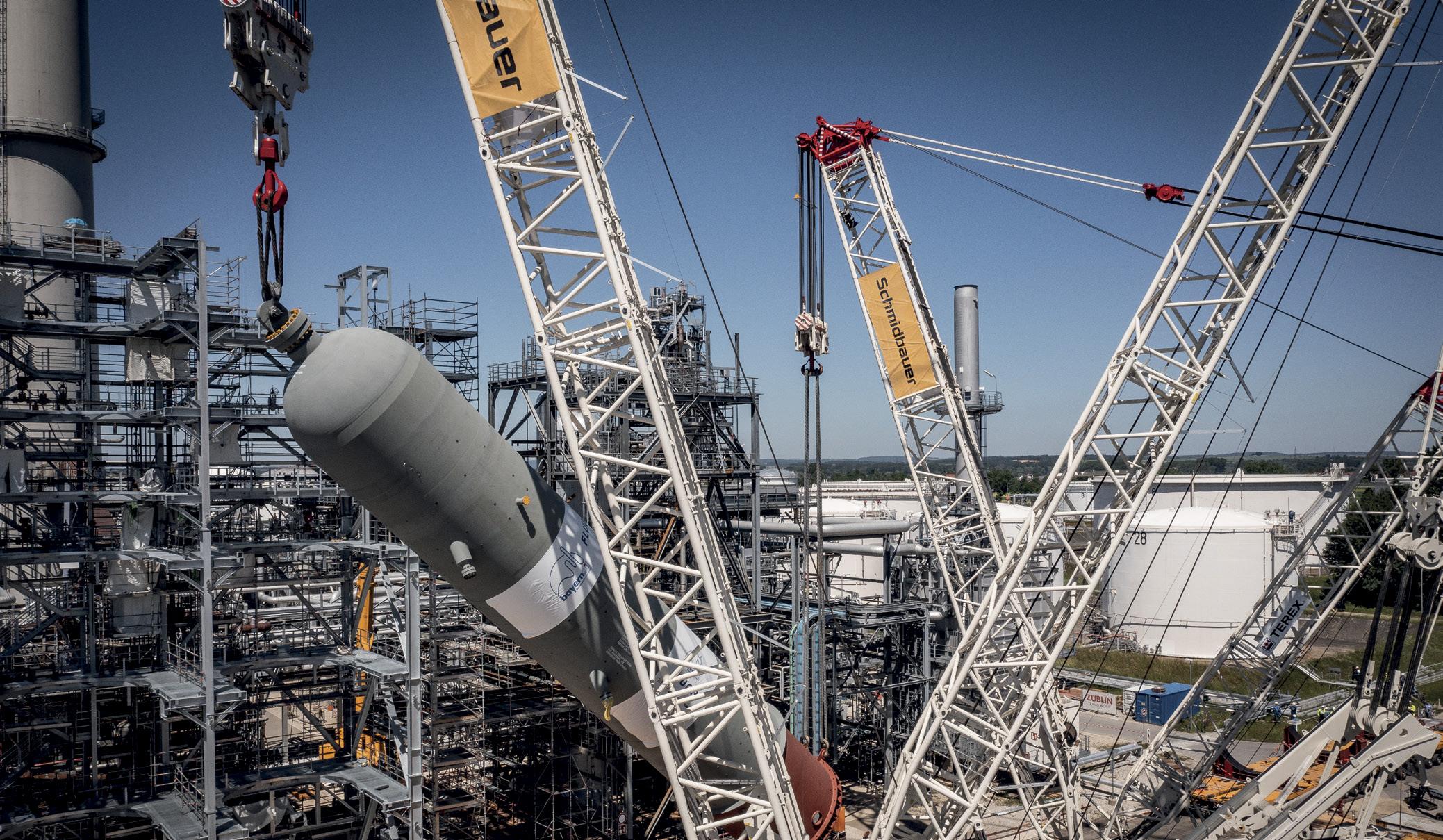
We offer empowering solutions.
We look forward to your inquiry! T +49 89 898676-0 info@schmidbauer-group.com

Schmidbauer GmbH & Co. KG · Headquarters Munich · Seeholzenstraße 1 · 82166 Gräfelfi ng · www.schmidbauer-group.com
presence of pests in wood marked as having been treated. “While the chance that any particular piece of wood harbors live pests after purported treatment is small, the huge volumes of packaging in global trade means that the cumulative risk of pest introductions continues to be too high. Once these studies have been completed, the IPPC parties should adopt measures to fix the problems identified.” • Importing NPPOs should apply their rights under Section 5.7 of the World Trade Organization Sanitary and Phytosanitary Agreement to immediately prohibit wood packaging from countries with records of exporting non-compliant wood packaging. “Those countries would be allowed to use crates and pallets made from such alternative materials as plastic, metal or oriented strand board.” • If the IPPC parties fail to act, importing NPPOs should begin the process of adopting their own, more protective, regulations on a permanent basis. “This step would require that they cite the need for setting a higher ‘level of protection’ and then prepare a risk assessment to justify adopting more restrictive regulations.” • NPPOs should find more effective means to inform shippers of which suppliers reliably provide wood packaging that complies with ISPM 15 requirements. “The current practice of NPPOs communicating with each other is not leading to the necessary improvements.”
OTHER INITIATIVES
Campbell also noted a proactive initiative by importers in Houston, Texas, aimed at improving compliance with ISPM 15. There an informal coalition of importers and the Cary Institute of Ecosystem Studies plans to hire employees of international inspection companies, which already inspect cargo for other reasons at the loading port.
“These inspectors would be trained to inspect the dunnage at the source of shipments to identify – and reject – suspect dunnage before the shipment is loaded,” he said.
And amid all this, it appears biosecurity issues are increasingly on the radar of breakbulk carriers. Last year, Mitsui O.S.K. Lines, or MOL, became the first Japanese line to be certified under the Australia Department of Agriculture’s Vessel Seasonal Pest Scheme. In a statement, MOL said as a sustainably-growing company contributing to Australia’s social and economic growth, it has an ongoing commitment to initiatives that reduce pest risks to the nation’s agricultural industry. Following in MOL’s footsteps, breakbulk cargo movers across the modes could lead from the front when it comes to eradicating unwanted passengers on cargo packing. BB
Iain MacIntyre is a New Zealandbased, award-winning journalist, with lengthy experience writing in the global shipping scene.
Complex Cargo Made Easy
Breakbulk cargo isn't typical cargo. Good thing the Port of San Diego isn't your typical port.
• OPEN SPACE • FLEXIBILITY • EXPERTISE

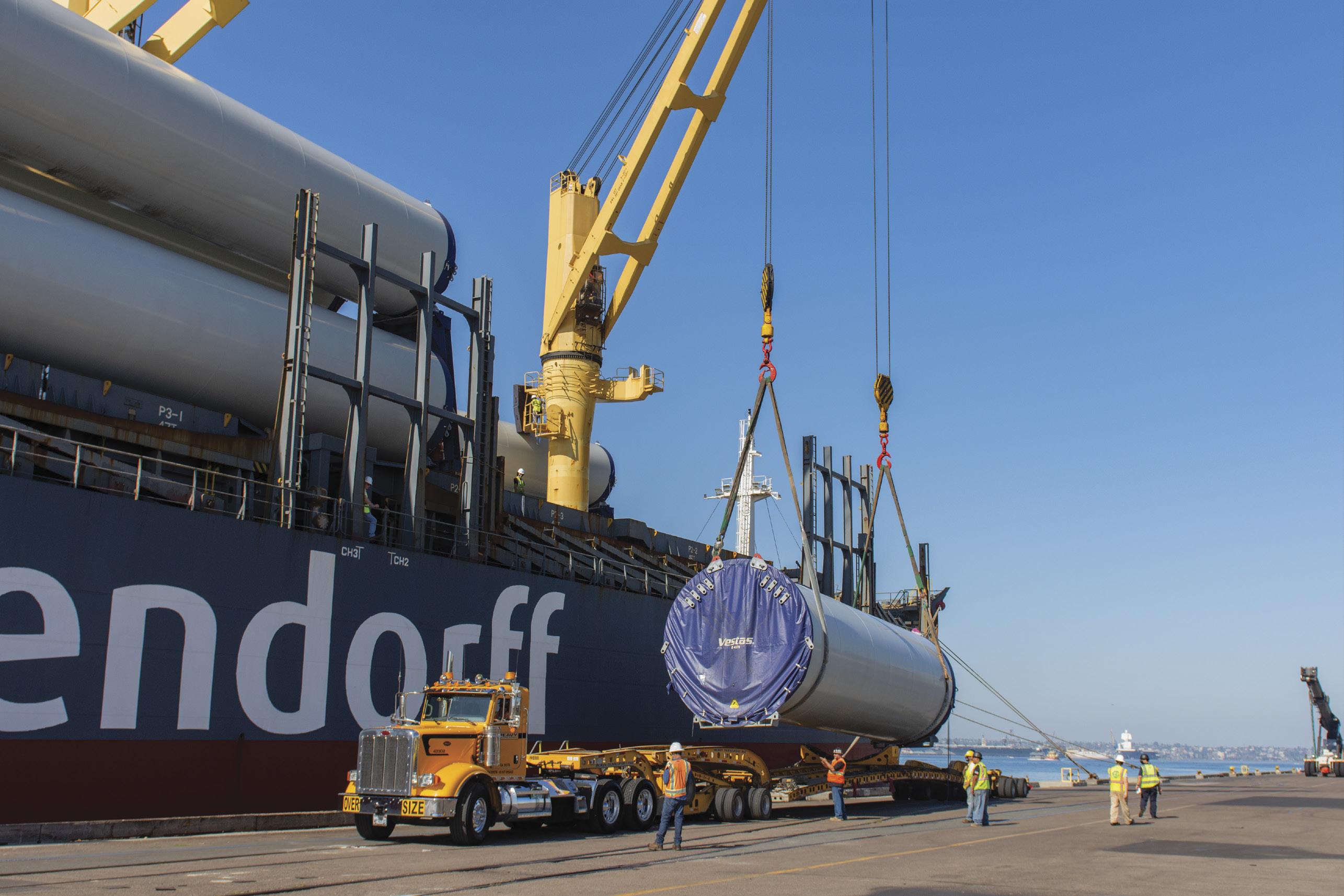
Learn more at: portofsandiego.org/cargo
CASE STUDY
BY MALCOLM RAMSAY
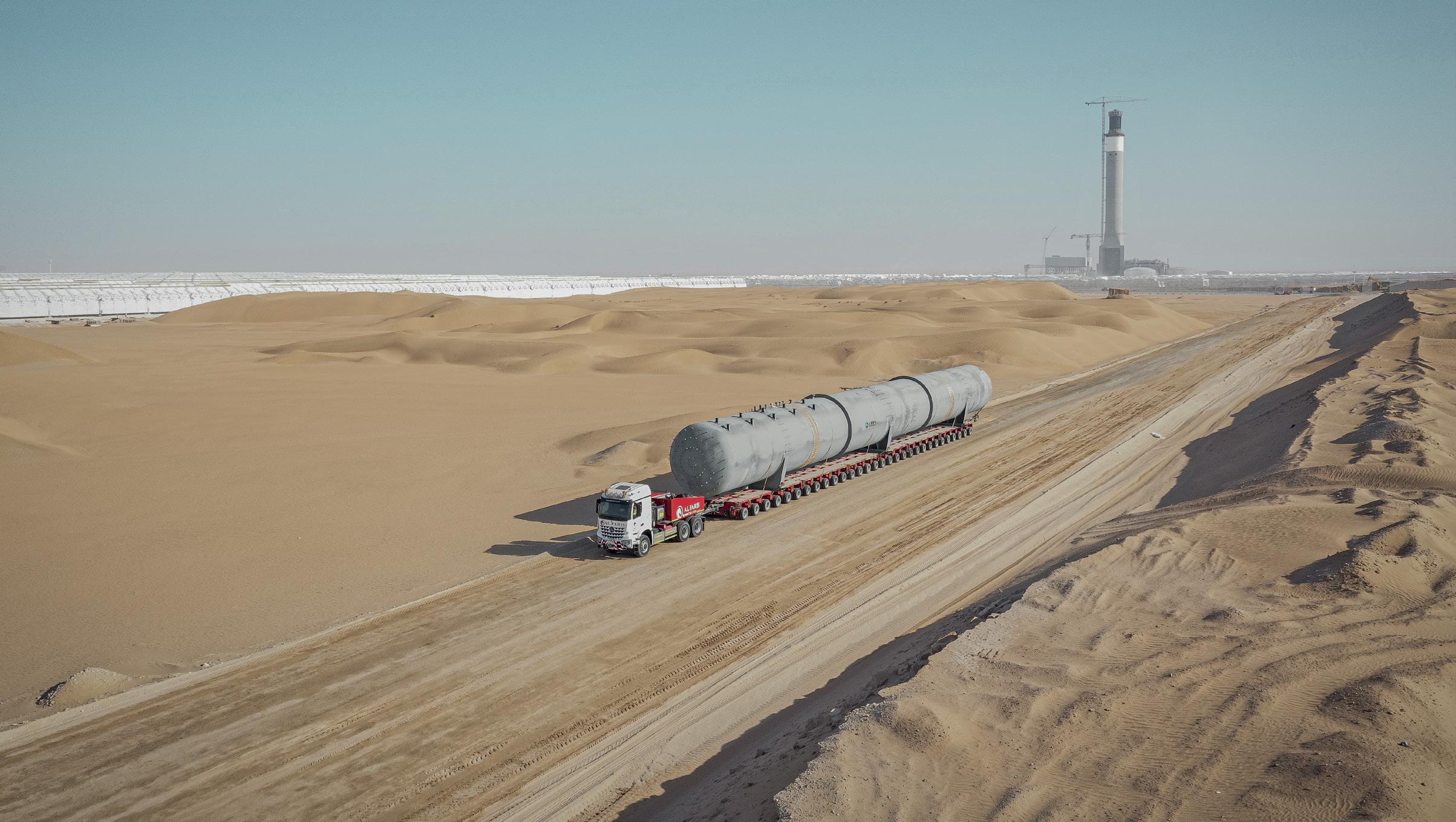
TAMING DUBAI’S DESERT
Overcoming Route Challenges for Solar Move
With soaring daytime temperatures and a lack of access to water, the arid, desert region of Saih Al-Dahal to the south of Dubai is largely uninhabited. But over the last decade this landscape has emerged as the perfect setting for the world’s largest single-site solar facility, the Mohammed Bin Rashid Al Maktoum Solar Park.
Heavy transport specialist Al Faris Group negotiated this difficult terrain to deliver a shipment of 30 outsized tanks for the solar park, supporting the next phase of this ongoing development.
“This delivery was part of a major extension project at the park,” Kieve Pinto, executive director at Al Faris, told Breakbulk. “We were selected for our extensive experience handling this sort of complex, heavy-lift project and, despite challenges with the route, our dedicated team ensured this important cargo was all delivered safely and on time.”
Originally established by DEWA in 2012, the Mohammed Bin Rashid Al Maktoum Solar Park has grown steadily with three phases already complete and a further two phases ongoing. The fourth phase of this project, Noor Energy 1, is the world’s largest singlesite concentrated solar power park and has been developed in collaboration between DEWA and Saudi investor and operator ACWA Power.
The cargo carried by Al Faris for this latest development included 30 overflow tanks, each weighing 235 tonnes. To make handling more complex each giant unit also measured 52 meters in length, necessitating detailed planning prior to delivery.
“A systematic approach to identify affected stakeholders was used,” said ACWA spokesperson Mohamed Yousef. “This approach not only considered the project, but also put into consideration associated facilities, transport routes and areas potentially affected by cumulative impacts.”
DISCHARGE AT JEBEL ALI
The overflow tanks were supplied by Chinese power generation and electrical equipment manufacturer Shanghai Electric and arrived at Jebel Ali Port, in the south of Dubai, aboard a COSCO multipurpose vessel.
“To prevent face-to-face contact, the project team worked with co-operators through phone and video conferencing to carefully design a transportation route, identify obstacles along the route, and develop corresponding solutions,” a spokesperson for Shanghai Electric said.
“After in-depth research and repeated verification, the project team designed a detailed plan to hoist the super-large and heavy overflow tank.”
Upon docking at the port, the cargo was discharged from the vessel to trailers using on-deck cranes. For this project Al Faris selected Goldhofer THP/SL conventional hydraulic trailers arranged in two files with 30-axle configuration.
“When it comes to transporting ultra-heavy and voluminous cargoes on- and off-road, the THP/SL modules are often the most economical solution,” said Dean Exner, Goldhofer’s regional director of sales for the Middle East. “They are the key to extremely high payloads in combination with long continuous operations.”
With the tanks discharged in pairs to travel, the convoy of trailers were pulled using Mercedes Arocs trucks from Al Faris’ fleet.
“Considering the cargo dimension, weight and route condition from JAFZA to the Solar Park, this equipment was chosen for safest convoy,” Ganesh Prabhu of Al Faris explained.
ROUTE PLANNING
While the surrounding Jebel Ali Free Zone is well equipped to deal with oversized cargoes, the onward route to the solar park proved more challenging as the roads beyond the city limits were small and frequently unsuitable for extra-long loads.
Top: The move of the 235-tonne tanks proved more challenging on the roads beyond the city limits. CREDIT: AL FARIS GROUP

“A project of this nature requires exceptionally detailed planning to orchestrate the complex activities necessary for ensuring uninterrupted safe services; from route analysis to on-road safety permissions,” Al Faris’ Pinto said.
Alongside technical analysis of turning space and height clearance along the route, the in-house team also had to prepare support documentation and HSE protocols to share with the client and partners involved in the project.
The first step in this process was to carry out a route survey physically, Prabhu explained, noting that “all the sharp turns, bridges and gantries present in the route were physically measured.” Following this, the technical team then turned to AutoCAD trailer software and Google Earth images to confirm the swept path analysis.
Confident that a successful route had been established, the in-house team then liaised with Dubai’s Roads and Transport Authority, or RTA, to secure the necessary approvals and consent for the required road modifications to begin.
“After the survey, we submitted the report to the RTA for approval and obtained the required ‘No Objection Certificate’ for road modification,” Prabhu said. “Then, as per RTA standard guidelines, an approved thirdparty contractor was hired for the road modification work.”
This work involved a variety of “significant road modifications,” including construction of new bypass roads to avoid overhead height restrictions and temporary traffic management systems to handle diversions.
“Our team of engineers and technicians carried out the operation smoothly with the utmost safety and efficiency with all approvals and safety measures in place and with the help of police escort vehicles,” Pinto said.
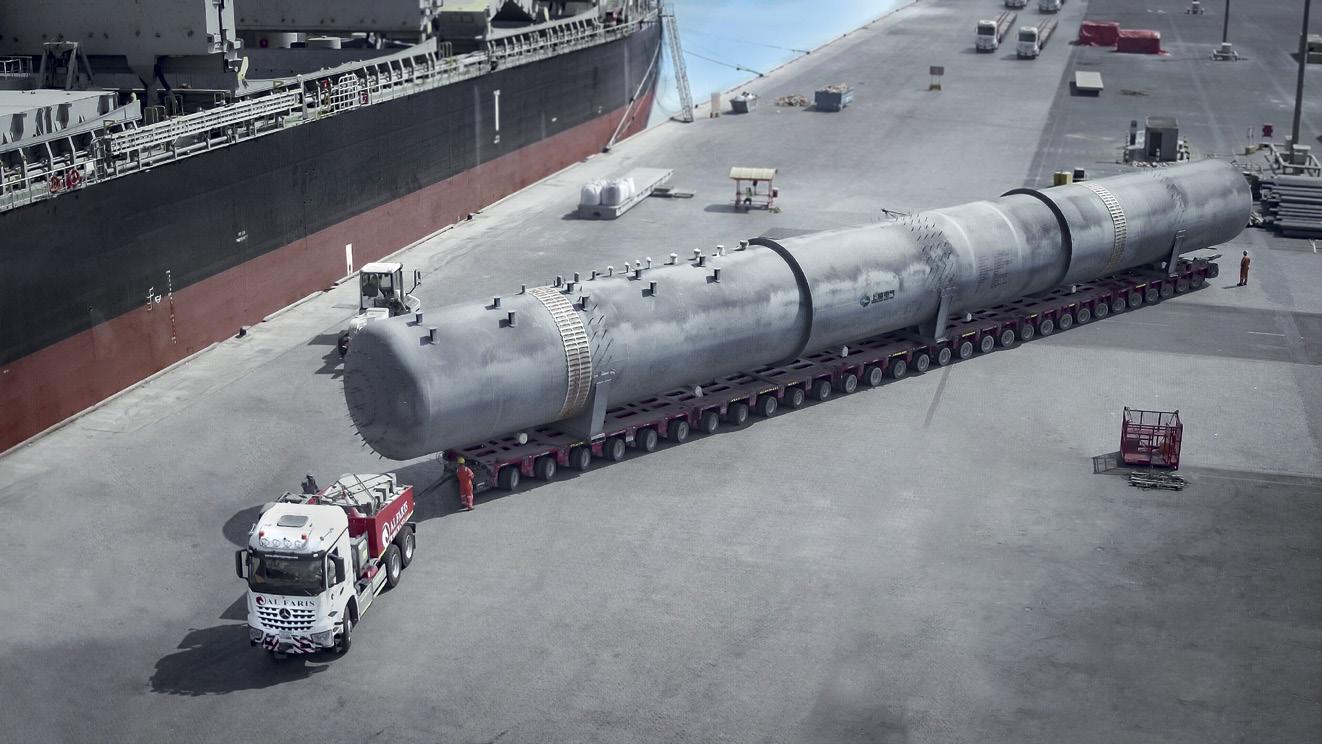
INSTALLATION PHASE
The final stage of the project involved Al Faris installing the components at the project site, using a Liebherr crawler crane from the firm’s the client. According to the load exerted by the crane, ground compaction was done. Also, the access area for the trailer with the cargo was designated and prepared accordingly.”
With the tanks now successfully in place, the final stages of development are taking place, paving the way for the near 1 gigawatt of additional capacity from the Noor Energy 1 project when it is fully commissioned in 2022, and helping to deliver DEWA’s targeted capacity of 5 gigawatts at the park by 2030. BB
Al Faris moved the load with Goldhofer THP/SL conventional hydraulic trailers arranged in two files with 30-axle configuration. CREDIT: AL FARIS GROUP
The Liebherr crawler crane had a lift capacity of 400 tonnes.
CREDIT: AL FARIS GROUP
existing fleet. With a lift capacity of 400 tonnes, the crane was used in parallel with smaller supporting mobile cranes.
“The foundation design was such that the crane must lift the cargo and then it had to travel approximately 80 meters to the foundation area for installation, for which the crawler crane was chosen,” said Pradeep Puthran, Al Faris project manager.
Again, pre-planning was a vital element in successful completion of this stage and Prabhu noted that the team completed the lifts according to a meticulous plan.
“Prior to the move, the crane placing area and foundation area were inspected,” Prabhu explained. “Then the crane load calculation was given to Based in the UK, Malcolm Ramsay has a background in business analysis and technology writing, with an emphasis on transportation and ports.
REGIONAL REVIEW
TURKEY’S ‘CRAZY PROJECT’
Canal Istanbul Faces Barrage of Criticism BY SIMON WEST
Since taking power in 2003, first as prime minister then as president, Tayyip Erdogan and his ruling Justice and Development Party, or AKP, have given a green light to dozens of large-scale construction projects in Turkey, a strategy that has been a boon for breakbulk movers.
Flagship projects during the twodecade infrastructure drive have included the New Istanbul Airport, one of the world’s busiest according to developers, the Galataport cruise ship terminal, also in Istanbul, and the 1,850-kilometer Trans-Anatolian Natural Gas Pipeline, or TANAP, a key section of the Southern Gas Corridor venture to transport natural gas from the Caspian Sea to Europe.
One project in particular though, has been garnering the headlines: Canal Istanbul.
If built, the US$15 billion development, first announced a decade ago, would carve out a 45-kilometer shipping channel between the Black Sea and the inland Sea of Marmara, and would run parallel with the Bosphorus, one of the world’s busiest trade corridors.
The canal was formally launched in June with the laying of foundations for the first of six bridges that will traverse the planned route. But work on the waterway, which Erdogan himself has jokily dubbed a “crazy project,” has yet to begin.
“Turkey will become the world’s most important logistics center with the Canal Istanbul. The Black Sea will turn into a trade lake for Turkey,” said Transport Minister Adil Karaismailoglu prior to June’s launch.
PLANS MAKE ‘LITTLE SENSE’
Serious questions though remain over its viability, with many claiming the plans make little logistical, environmental or economic sense. Erdogan said in June the canal would take six years to complete.
“This is a very controversial project and no one knows whether it will happen,” said an Istanbul-based logistics executive, who asked not to be named.
The government has insisted that a new passage is needed to ease congestion on the Bosphorus, reduce waiting times for entry that on clear days average 13 to 14 hours, and provide safer transit conditions for vessels. Some 41,000 ships sail through the Bosphorus every year, a number expected to rise to 68,000 by 2039, according to the transport ministry.
But Yoruk Isik, an Istanbul-based maritime analyst, scholar at the Middle East Institute and staunch critic of the new canal, told Breakbulk that over the last two decades, traffic on the Bosphorus has declined, mainly due to fewer tankers transporting oil and gas and larger ships that can carry more cargo,
Canal Istanbul
Bosphorus
Black Sea
Sea of Marmara
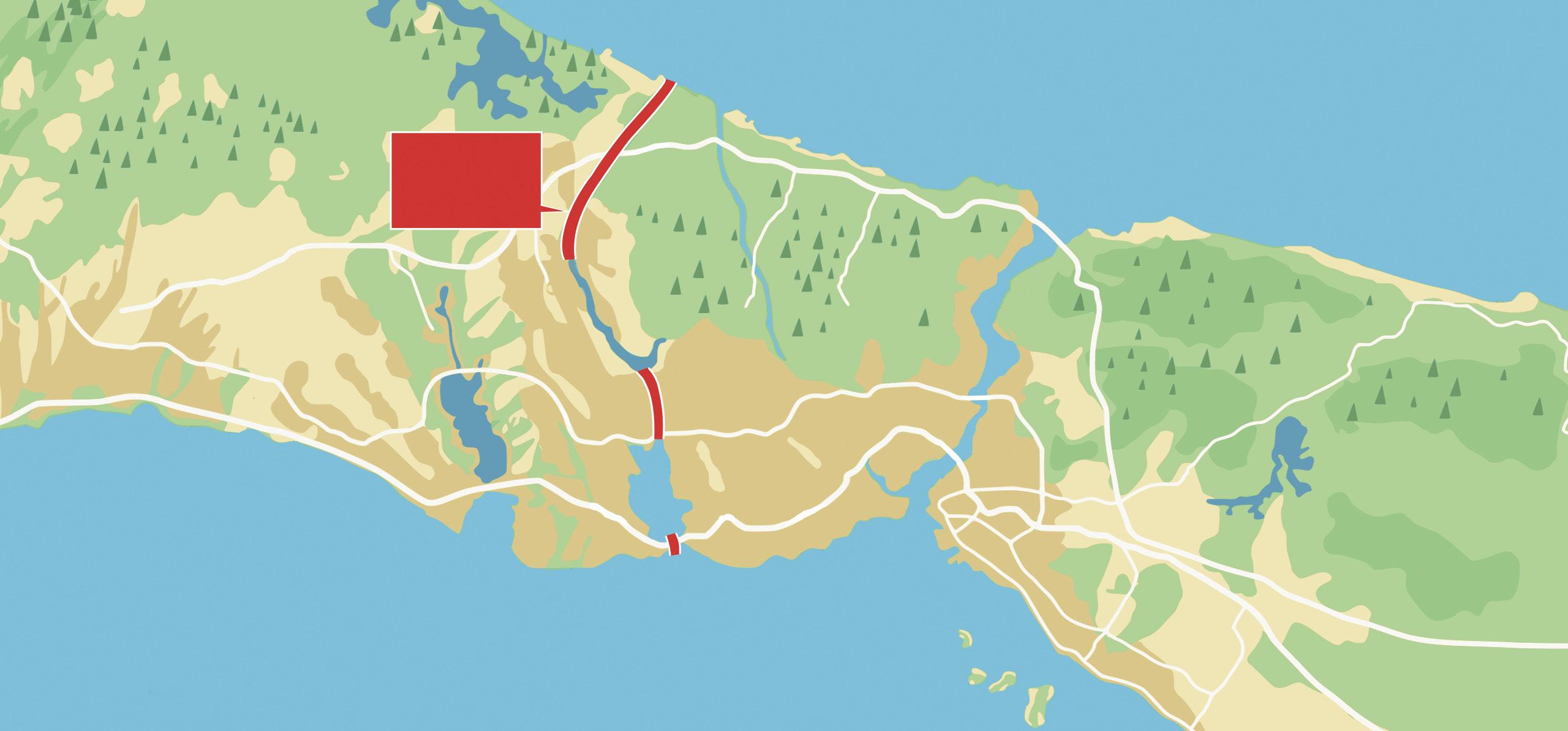
while safety has improved thanks to more advanced vessels and better traffic management.
“Transit is getting slightly smaller, and that is because Turkey builds so many pipelines,” Isik said. “And the Bosphorus is actually safer through technology – the last major accident happened more than 40 years ago. Improving safety does not require new construction.”
According to the plans, the new waterway will be 20.75 meters deep with a minimum width of 275 meters, dimensions that could prove hazardous for larger vessels, Isik said. “Passing through a natural strait like the Bosporus, however challenging it might be, is significantly safer than going through a narrow canal.”
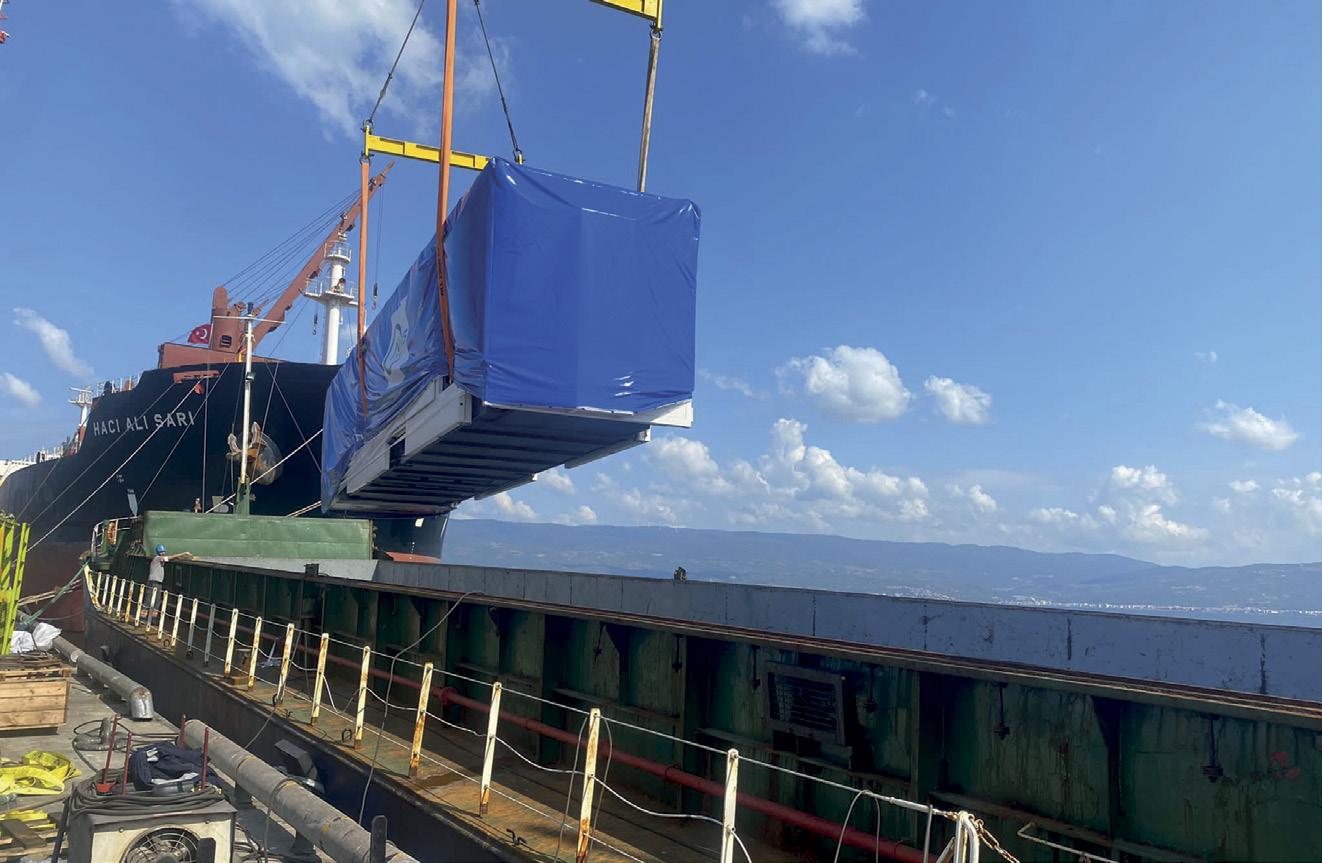
ENVIRONMENTAL IMPACT
Detractors also claim the project would cause irreparable damage to the environment.
According to the ministry, Canal Istanbul would run on a fairly straight route from Karaburun on the Black Sea coast down to the Kucukcekmece Lagoon on the Sea of Marmara’s northern coast. Construction though would entail slicing through marshlands and forest and threatening local ecosystems and water supplies.
“It will fully destroy one of Istanbul’s freshwater reservoirs and expose another one to salination,” Isik said. “Istanbul and Turkey already suffer from drought, while the Black Sea is already very polluted. How this will affect the Marmara Sea if connected by a canal is unknown.”
Istanbul Mayor Ekrem Imamoglu has also joined the chorus of disapproval, claiming the project poses a grave danger to the city’s surface and ground water resources.
“No sensible politician can support a project of this sort, at a time when climate change is causing unprecedented damage to our planet’s water resources,” tweeted Imamoglu, who last year began legal proceedings against the development.
Imamoglu, from the center-left Republican People’s Party, or CHP, also slammed June’s inauguration after a consortium led by state-run COSCO Pacific bought a 65 percent stake in Kumport, Turkey’s thirdlargest container terminal, located on Istanbul’s Ambarli coast.
However, given the enormous financial and environmental challenges, and the substantial public opposition, Ozkan said it was “unlikely” that the canal would be built. “It is difficult to see how such a project could and whether it should go ahead.”
Isik was even more damning in his appraisal. “On a scale of one to 10, the possibility of this canal getting built is minus one. There is absolutely no financial logic to build such a canal. There is no natural need, no customers, no demand.”
Forwarders in Turkey have plenty of project options springing from the government’s construction push.
CREDIT: KITA LOGISTICS
ceremony as a sham, claiming the start of the bridge construction is part of a separate highway construction project, approved years ago.
The project’s environmental impact could see the government struggle to secure financing.
A Reuters report in April citing unnamed senior bankers said some of Turkey’s largest banks would be unwilling to invest in Canal Istanbul because of the risks. European backers of Turkish banks would unlikely accept Turkey’s environmental approval, they were quoted as saying.
FUNDING CHALLENGES
Gulcin Ozkan, a professor of finance at King’s College London, agreed that funding for the project remained a major challenge.
“Turkish banks, having signed the UN’s Principles for Responsible Banking framework, which requires signatories to ‘avoid harming people and the planet,’ would not be able to provide the financial backing for the project. Other signatories of the principles would be similarly constrained,” Ozkan said.
Chinese, Dutch and Belgian banks have been cited as potential investors, although concrete plans have yet to take shape, Ozkan added.
China secured a foothold in Turkey’s shipping industry six years ago
ALTERNATIVE PROJECT OPTIONS
Should Erdogan’s “crazy project” come unstuck, as so many experts predict, forwarders in Turkey have plenty of alternative options springing from the government’s construction push.
“Investments continue non-stop in some key areas,” said Emre Eldener, managing director at Istanbul-based Kita Logistics, and president of the Turkish Forwarders Association. “There are underwater LNG storage projects, upcoming Black Sea oil exploration projects and of course, the Akkuyu nuclear power plant (NPP).”
The first heavy component of a steam turbine set – the rotor of the high and intermediate pressure cylinder (HP and IP cylinder), more than 12 meters long and topping 107 tons – is delivered to the Akkuyu NPP construction site. CREDIT: AKKUYU NUCLEAR JSC
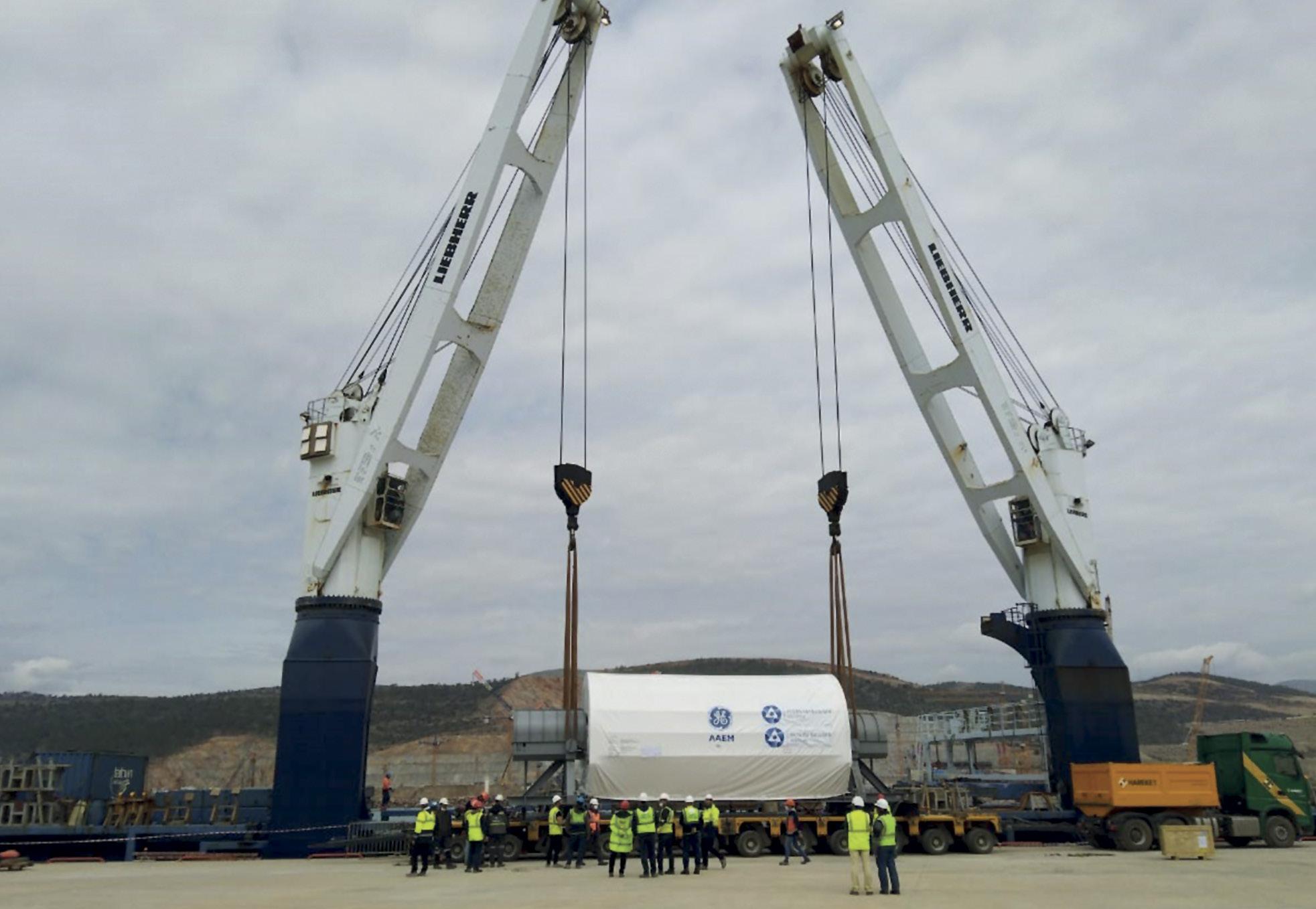
Turkey’s 1915 Canakkale Bridge and Motorway Project, incorporating the longest mid-span suspension bridge in the world, is taking shape.
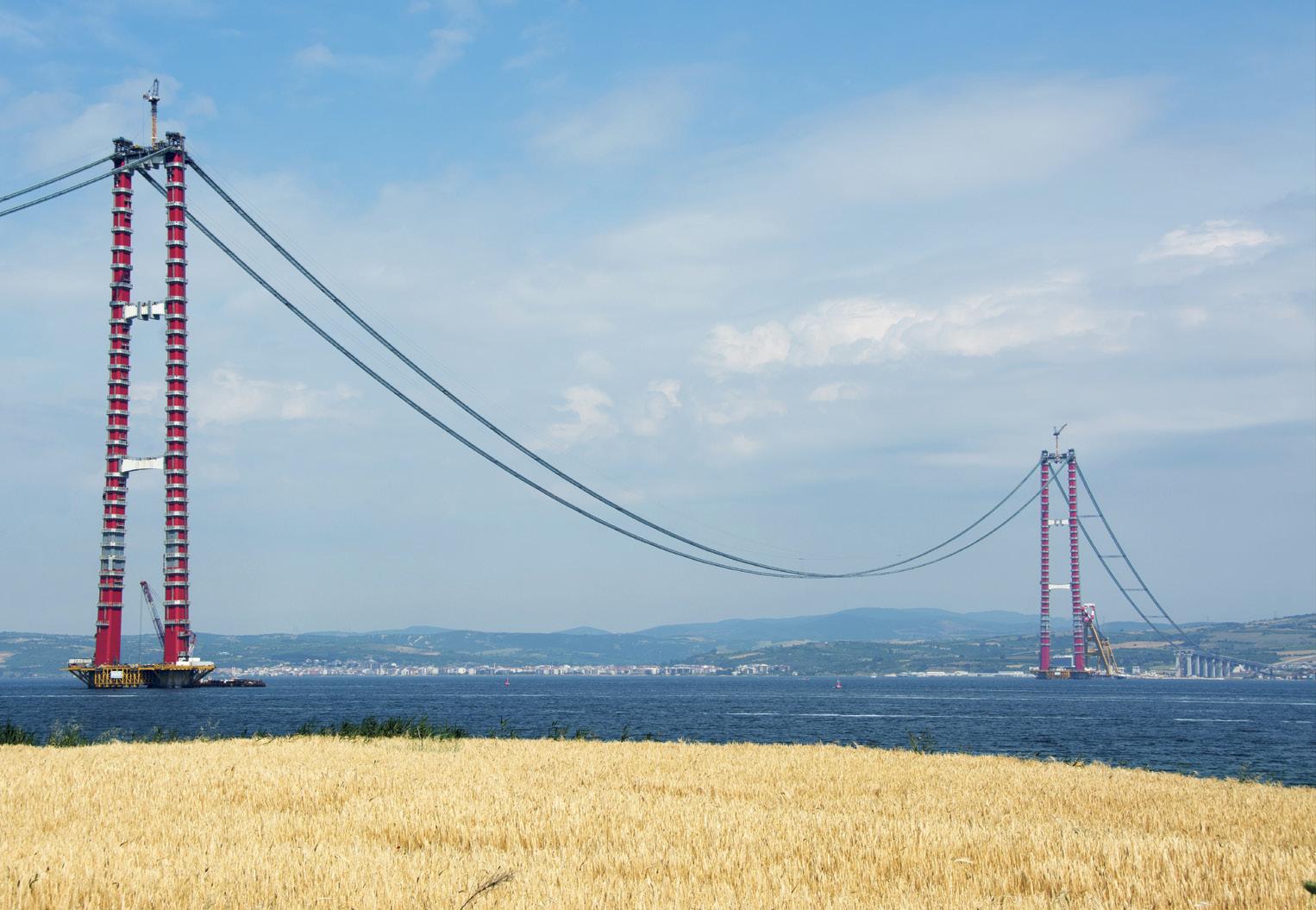
CREDIT: SHUTTERSTOCK
Akkuyu, Turkey’s first NPP, is being built in southern Mersin province by Russian nuclear conglomerate Rosatom, with work on the first of four 1.2 gigawatt reactors beginning in late 2017.
Once up and running, the US$20 billion plant is expected to provide about 10 percent of Turkey’s electricity demand, with completion of all four reactors slated for 2026. Russia-based transport group FESCO is providing heavy-lift logistics services for the project.
Last year, the group shipped four steam generators weighing 358 tonnes each from manufacturing facilities at Volgodonsk in southeast Russia to the Black Sea port of Rostov-on-Don, and on to a terminal near the port of Mersin.
Another site that has been offering forwarders significant cargo-carrying work since it broke ground in early 2017 is the 1915 Canakkale Bridge and Motorway Project, a €3 billion venture that developers claim will incorporate the longest mid-span suspension bridge in the world.
The bridge and approaching viaducts will stretch 4.6 kilometers across the Dardanelles in northwest Canakkale province, south of the Marmara Sea, and is slated for completion in March 2022, some 18 months ahead of schedule. The venture has called for the transport of dozens of heavy-lift components, including bridge foundations, tie beams and 700-tonne mega-block decks.
“The bridge is almost complete, so I believe the transport will be finished when the last two pieces of the main bridge are delivered by barge,” Eldener said. “There are still opportunities until the end of this year.”
ELECTION WRINKLES
Turkey’s infrastructure boom meanwhile is unlikely to be hampered by the outcome of presidential elections in 2023.
Erdogan’s two victories in 2014 and 2018 preclude him – on paper at least – from running for a third term. But with the AKP’s power over the courts, the president would likely prevail in any constitutional scrap with opposition lawmakers.
“No judicial authority, I think, would dare to reject Erdogan’s demand to run for the third time,” said Toygar Baykan, assistant professor of politics at Turkey’s Kirklareli University.
Furthermore, the AKP’s widespread use of patronage – the use of state resources to reward loyal supporters – could mean Erdogan, sitting atop this tightly interwoven network, has no option but to run for another term. “Even if he wants to retire, his responsibilities to his broad network of supporters would stop him from doing so,” Baykan said.
“In the case of a change in the government, the new ruling party or coalition would hesitate to introduce dramatic measures to transform the Turkish economy. The construction business would continue to occupy a central position.”
That is, with one major exception. “Canal Istanbul is an extremely contentious and entirely different issue. If the opposition coalition wins elections and forms the government, I think they would cancel it.” BB
Colombia-based Simon West is a freelance journalist specializing in energy and biofuels news and market movements in the Americas.
EXCEEDING YOUR BIGGEST EXPECTATIONS
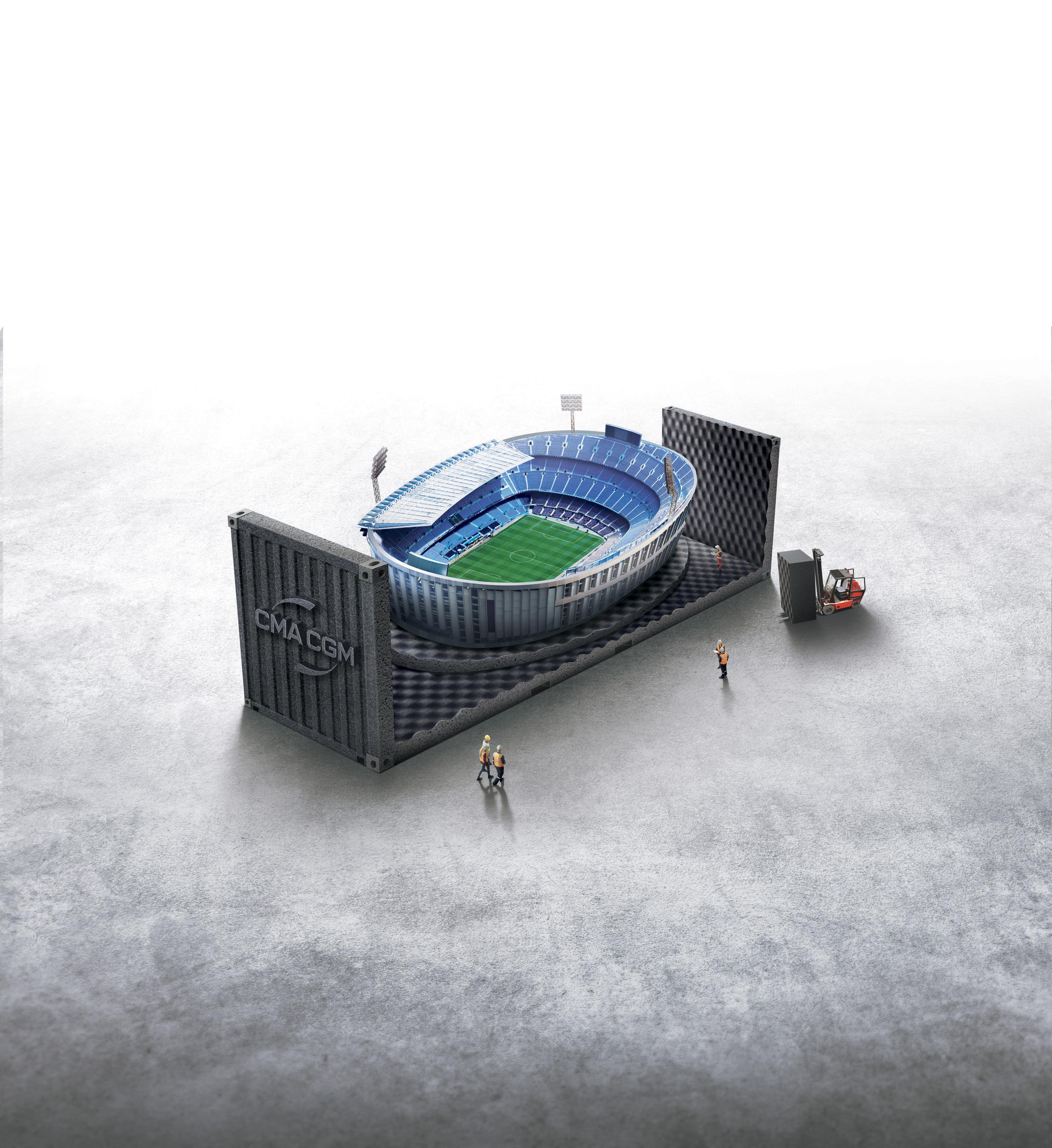
CASE STUDY
The blade lifter reduced the swept path area of the 55-meter blades.
CREDIT: COLLETT
SIMPLIFYING BLADE LIFTS

New Gadget Breezes Through Wind Moves BY MALCOLM RAMSAY
Navigating the twisting roads of Dumfries & Galloway in Southwest Scotland can be difficult at the best of times, but the task is made all the more complex when it involves a cargo measuring more than 50 meters long.
Heavy haulage firm Collett recently rose to this challenge when it became the first firm in the UK to utilize a blade lifter vehicle to deliver a set of turbines for the remote Windy Rig wind farm, 10 kilometers south of New Cumnock.
Partnering with Belgium heavylift specialist P. Adams Transport, Collett was responsible for delivery of 12 turbine blades from the Port of Ayr to the wind farm as well as transport of ancillary components from the King George V Dock in Glasgow.
Neil Mackinnon, project manager at Collett & Sons, told Breakbulk that the project was commissioned by Norwegian state-owned renewable energy group Statkraft. As well as having the expertise and project experience, P. Adams also had a blade lifter suitable for the project.
The blade lifter was developed by heavy-lift manufacturer Goldhofer and offered numerous unique advantages for the project, including allowing the project team to tilt the blade to an angle of up to 60 degrees, and also mount the blade horizontally on to the module.
“This tool can be integrated both into a self-propelled modular trailer and a ‘classic’ modular trailer with a pulling truck,” a spokesperson for P. Adams said. “It can lift the blades up to an angle of 60 degrees to swing over obstacles such as houses or trees. The system has a lifting capacity of 500 tonne-meters, which allows transportation of even the biggest on-shore blades on the market today.”
The Goldhofer blade lifter also allows for rotation of up to 340 degrees and features lifting torque of 55 tonnes, allowing the team to consider routes that would otherwise have been impossible or highly disruptive.
“This is the first time a specialist blade transporter has been used in the UK,” a spokesperson for Statkraft explained, highlighting the importance of local liaison for this project – the firm met with the local community council and held regular community liaison meetings to discuss how best to minimize disruption and keep residents informed.
The unique design of the blade lifter allowed the team to reduce the swept path area of the giant blades, which each measured 55 meters in length.
“By utilizing the blade lifter, the client could avoid civils costs and modifications along the delivery route – thus reducing the impact on locals and avoiding third-party land deals,’ Mackinnon said.
The blades are the key components in 12 Vestas V112 turbines that power the wind farm, each of which stands with a 69-meter hub height.
CAREFUL PLANNING

While the introduction of the blade lifter trailer provided distinct advantages for the team, it did not do away with the need for extensive pre-planning and route surveys. With most of the components arriving in King George V, or KGV, Dock – about 60 kilometers north of Port of Ayr – the project team also had to coordinate two different routes and loading operations.
“The route was surveyed, and the data used to produce Swept Path Analysis models and drawings using AutoCAD and SPA software. This was all carried out in-house,” Mackinnon explained. “Only the blades were delivered to Ayr. All other components were delivered to Glasgow KGV Dock. The blades were loaded by cranes at Ayr onto super wing carriers and transported out of the docks under police escort to a transition point 12 kilometers from the site.”
This first section of the journey was completed at night to take advantage of lower traffic levels. However, from the transition point onward, the route became more difficult for traditional transport using the super wing carriers, so the team coordinated the transfer of the blades to P. Adams’ blade lifter.
“At this point they were loaded onto the blade lifter and taken one at a time to site and offloaded by crane at the turbine hard standing. Once the crew gained familiarity of the route, the blade lifter could travel to site in three hours,” Mackinnon noted.
In parallel, transport of the remaining turbine tower components was arranged from Port of Glasgow. These outsized items included tower to assess the road to ensure it still met the requirements of the axle loadings for the loaded vehicles used on the project.”
“Preparatory road works were required on both sides of the C35 to allow access,” Statkraft added. Deliveries of turbine components commenced shortly after the crane removal.
With these obstacles overcome, the project teams successfully completed delivery of the components in July, with turbine installation completed in August. As of September, all the components had been delivered and the turbines erected, with electrical connection underway – a success for the inaugural use of the blade lifter in the UK. BB
sections measuring up to 30 meters long and weighing 55 tonnes. These were transported using specialized tower clamp trailers, which Collett explained were utilized to “to allow self-offloading on site and reduce the need for cranes.”
Heavier components such as the nacelle, which weighed 64 tonnes, and the V112 drive trains, which weighed 61 tonnes each, were loaded onto multi-axle, low-bed trailers for the 93-kilometer journey to the wind farm.
REPAIR AND MONITORING
With the routes approved, transport was all set to go ahead, but weather conditions proved challenging as heavy rains in the region presented difficulties. “Localized flash flooding damaged the route to site, which caused some delay as the road required repair and monitoring for the length of the project,” Jacob Collett of Collett explained. “Collett employed an engineering consultant
The blade lifter can lift blades up to an angle of 60 degrees and has a lifting capacity of 500 tonne-meters.
CREDIT: P. ADAMS Based in the UK, Malcolm Ramsay has a background in business analysis and technology writing, with an emphasis on transportation and ports.
CARGO LENS
CARRY ON SAILING
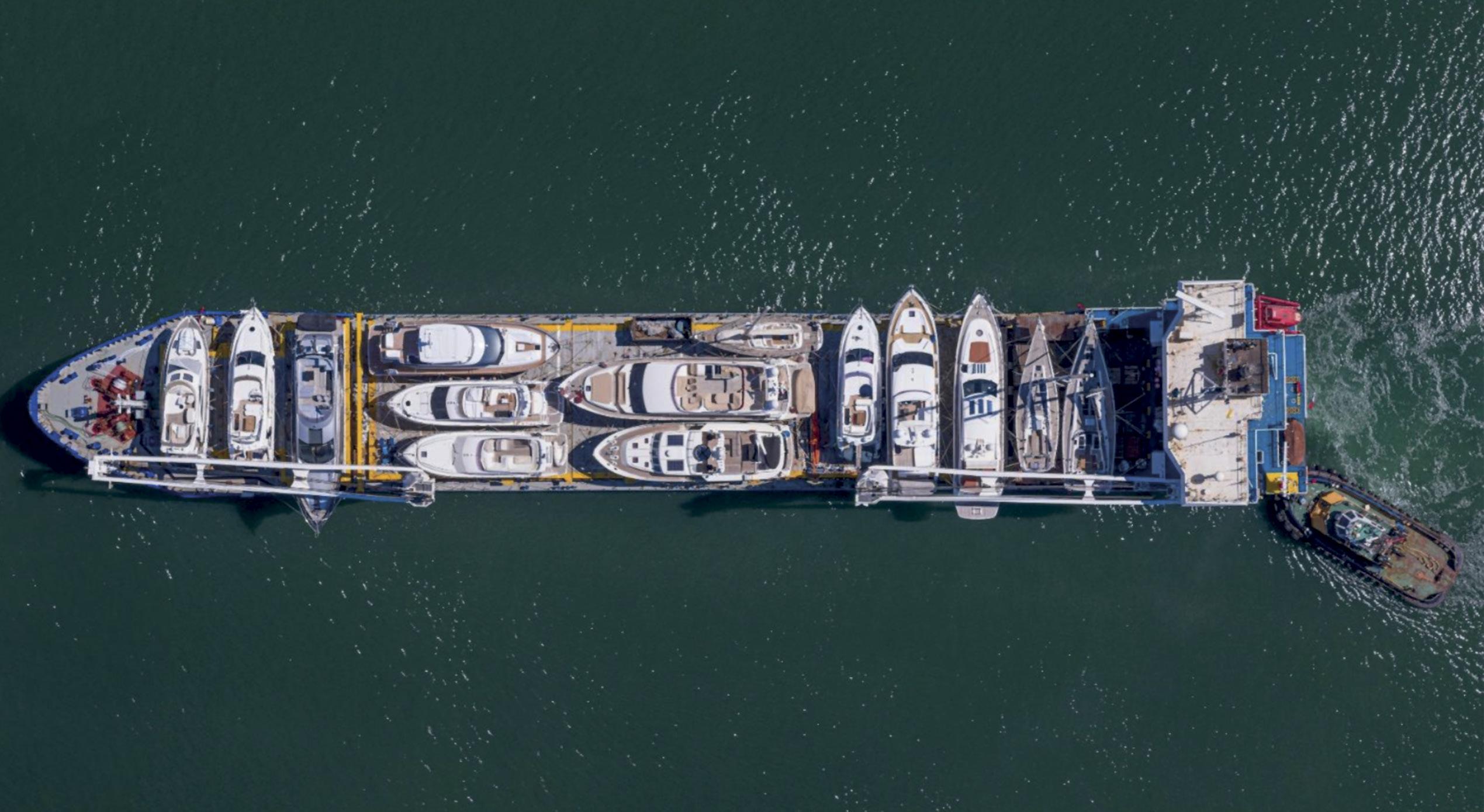
No Tail Off in Demand for Yacht Moves BY SIMON WEST
Timing is everything.
When Simon Judson took over as CEO of Peters & May in November 2020, his appointment “heralded a new era of ambition, expansion and consolidation.” His arrival was also, of course, in the midst of the global pandemic and its considerable fallout.
“It goes without saying that stepping into this role in the middle of a pandemic presented its own unique set of challenges,” he told Breakbulk. “Contrary to what some might assume, the market demand for yacht transportation remained strong and, in fact, increased over the course of the year; however, it was noted that uncertainties related to travel restrictions led to many boat owners holding off before committing to booking transport.”
One reason for the increase in demand was a growing number of clients seeking to bring their yachts “back home” from the Mediterranean to Northern Europe so that they could use them locally without incurring the risks involved with travel, Judson said. “Allied to this, another factor which fed into the increased demand for P&M’s services was that yacht owners were unable to travel to their yachts to relocate them themselves. Additionally, they would have been unable to find a suitable captain and crew, as Covid restrictions meant that everybody was homebound.”
Traditionally, P&M has often arranged skipper and marina services as an integral part of its transport arrangements, and there has been a definite upsurge over the past 18 months in customers opting for the company’s “allinclusive” service package, including skipper, transport insurance, marina, boat cleaning and Customs clearance formalities.
Covid-19 has not been the only new challenge to day-to-day activities. “The new sets of regulations and requirements introduced because of Brexit have also kept us extremely busy. Our freight forwarding section has had to expand quickly to support all Brexit-related queries concerning VAT,” Judson said.
Meanwhile, in addition to its sizable client base of long-term and returning customers, P&M has seen an increase in demand from people who are completely new to boating and yachting.
“A typical phone call might be received from someone interested in buying a second-hand yacht for the first time ‘but the yacht is in Spain, and I need it in the UK – can you help?’ ”
Jan Maarten Boissevain, commercial director at Amsterdam-based Sevenstar Yacht Transport, said that in terms of overall volumes, the past 18 months have been “business as usual,” albeit with a different mix and far higher shipping rates.
“For us, this year has been the same as the year before and the year before that – not much more or less busy,” he said. “The big changes have been that some trades are no longer being used, mainly because of the pandemic, and racing and other fun events vanished from our scope of work – and we still think there is only a small number of boats going to places to have fun. They are either going to a new owner or somewhere else or being repatriated.”
Racing and other events have been picking up again this year, he said. “People are keen to move again – that’s for sure. But they also need to understand that what was happening two years ago with shipping rates is no longer the case. People need to get in line with double the price almost, otherwise they can’t go anywhere.
Pricewise, he added, everything has gone through the roof and there is an issue in sourcing proper vessels to perform yacht transportation. The high rates are good for the carriers, he noted – “otherwise there would be no money for new investment.” However, “it is devastating for a lot of cargoes and one of them is yachts, which are seen as a low-paying, highdemanding cargo. We can only sell
Top: The pandemic saw an increase in demand from clients looking to bring their yachts back home. CREDIT: PETERS & MAY
certain routes for a certain amount of money. Shipping is not going to bail us out if they can make more money elsewhere.”
Part of the Spliethoff Group, Sevenstar’s established network of people based in key locations around the world has paid off during Covid-19 travel restrictions.
“We have people to do operational work in the ports everywhere, working for us exclusively, so we can continue to do business,” Boissevain said. “That is very important to our clients and ourselves. It is how we have always worked, both before and after the pandemic, and now we can benefit from that.”
‘UNFAIR’ COMPETITION
Copenhagen-based Thorco Projects reported an increase in demand for yacht transport, as well as a growing demand for luxury vessels. Its regular services from Europe (Baltic/ North Europe/Iberian Peninsula/ Med) are divided into trade lanes, so from Europe to the Middle East Gulf, Bay of Bengal, Asia, Australia, Africa West and East, U.S. Gulf and East Coast South America.
Since March 2020, Thorco Projects has transported all sorts of yachts from Europe, mainly the UK and France, and also from Asia to the U.S., Thorco’s Business Development Manager Wallace de Barros noted.
“What we can say is that yacht transport increased, at least in our regular services. Inside Europe, we saw movements – orders from brokers and forwarders – from the UK to France, Spain and Gibraltar, for repositioning purposes mainly. We also handled many new yachts and boats out of Italy to many destinations.”
However, he said, although Thorco saw the orders, he viewed the competition with small coasters, containerships and roll-on, roll-off vessels as unfair, “as they have a different way to calculate the ocean rates.”
As for changing demands, Thorco noted it had seen more luxury yachts and boats, “maybe because the condition to work from home (or ocean or anywhere) opened up new possibilities for new work environments.”
Thorco describes the transport of yachts and boats around the globe as “an important niche market” for the company, with its regular trade lanes ensuring a speedy and cost-efficient solution for everything from heavy tugs to high-tech racing boats.
“For Thorco Projects, which has projects in its name and blood, the transport of yachts is a central part of our business, and we acquired this know-how over past years,” de Barros said. “We have got closer to companies specialized in moving boats and yachts – they really add value to the business and see that they are able to consolidate a good number of boats and dilute the transport cost among all their clients.”
Thorco can construct tailor-made cradles for boats as required, he added. “Our port captains can design lifting beams or lifting devices to make lifting possible without damage, and we contract divers’ assistance case by case.”
CLIENTS TAKE AN INTEREST

P&M has in recent years seen a growing interest from boat owners in the actual transport itself, even if the shipment has been arranged by the broker from whom they bought the yacht. Judson sees this as a positive and as an opportunity to explain what is involved and help clients to understand the process, especially on the technical side.
“We have the most experienced and skilled technical team and loadmasters in this market, all of whom are happy to set time aside to talk clients through each step of a shipment,” he said. “It is important for us that owners tell us all they know about their yacht, so we know what to look out for when planning and lifting their yacht. Equally, the owner – being involved in the plan and attending the lift – may learn more about their yacht which they can refer to in case the yacht is lifted again somewhere else.”
One of the company’s most traditional sailing routes between the Mediterranean and Northern Europe
Boat owners are showing a growing interest in the transportation process. CREDIT: PETERS & MAY
A thirst for new sailing areas is being matched by rising demand for new yachts.
CREDIT: PETERS & MAY
is still running on a monthly basis and has been expanded to call into more ports in the Eastern Med and the Baltic.
“Croatia and Turkey are becoming ever more popular, as are Baltic countries. The clear inference is that clients are foregoing crowded marinas and nightlife hustle and bustle for the lure of exciting new cruising grounds,” Judson said. “Encouragingly, P&M is regularly informed by industry customers and manufacturers that this thirst for new sailing areas is matched with a rising demand for new yachts. The broad perception of yachting/ boating as a “safe haven” is great news for the marine industry, especially following a time when Covid forced many factories to close temporarily.”
P&M has seen an upswing in requests to ship both power and sail catamarans, as well as hybrid- and solar-powered boats – the latter being partly manufactured in Asia then shipped to Europe for completion before being delivered to the end customer. “We expect this niche to grow in the coming years as well.”
The company said it adapted rapidly and comprehensively to accommodate the increasing demand and the working methods necessitated by the pandemic. There has also been the challenge of ensuring that equipment such as shipping cradles and lifting gear is in the right place at the right time, even with bookings often being made at the last minute, due to client uncertainty related to Covid restrictions.
“At the beginning of the pandemic, there were even cases where all yachts had not been booked for a certain shipment, but the company had a loadmaster flown out to the port of loading anyway to ensure he was there and had gone through quarantine in time for the day of loading,” Judson said. “Thankfully, the process has become easier again, but it nevertheless taught us a great deal about the way we wish to work in future, bringing the team together and inspiring trust in colleagues and clients alike.” BB
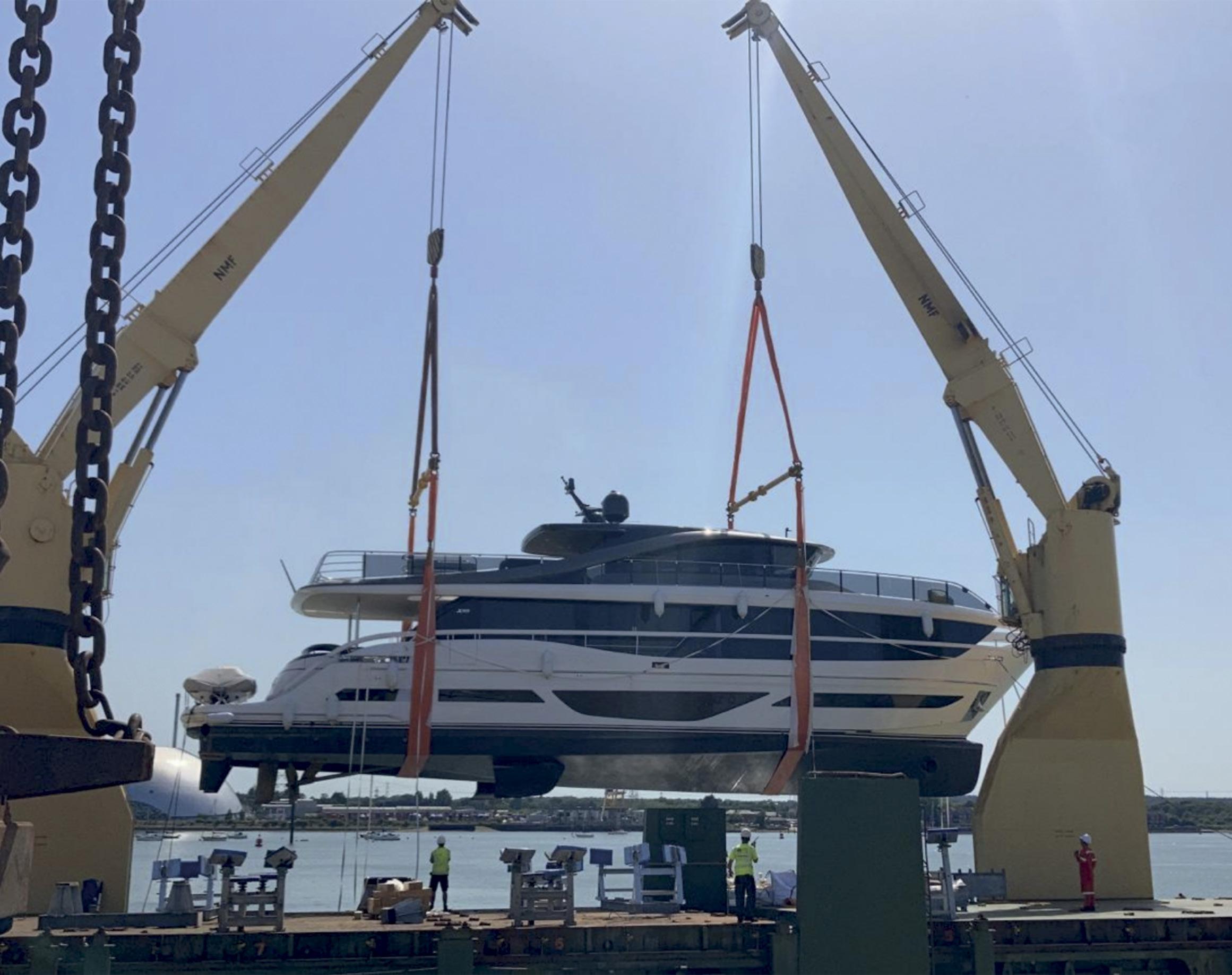
Felicity Landon is an award-winning freelance journalist specializing in the ports, shipping, transport and logistics sectors.
01 - 02 February 2022 Dubai World Trade Centre, Dubai, UAE middleeast.breakbulk.com
17 - 19 May 2022 Rotterdam Ahoy, Rotterdam, Netherlands europe.breakbulk.com
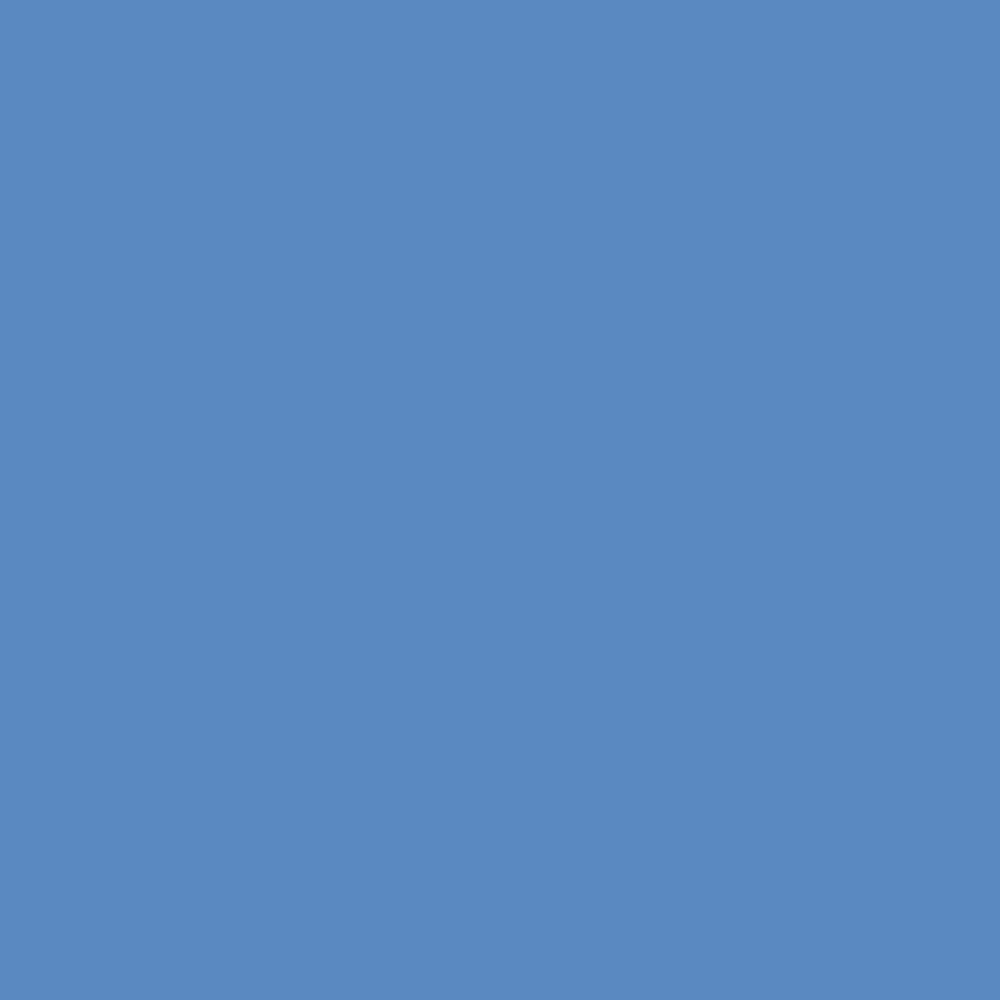
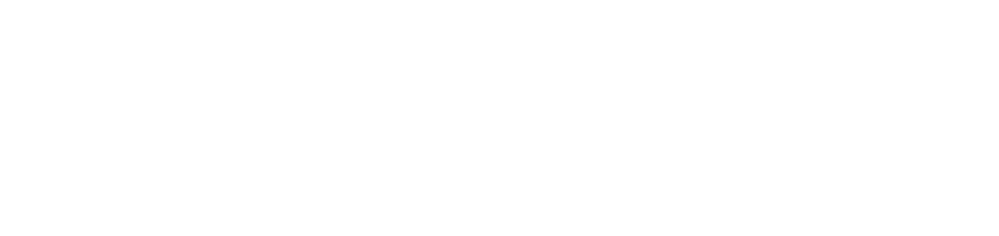
September 27 - 29, 2022 George R. Brown Convention Center, Houston, USA americas.breakbulk.com
INLAND TRANSPORTATION
INFRASTRUCTURAL HOPES US$1.2 Trillion Bill Proffers to Deliver Project Opportunities BY PAUL SCOTT ABBOTT
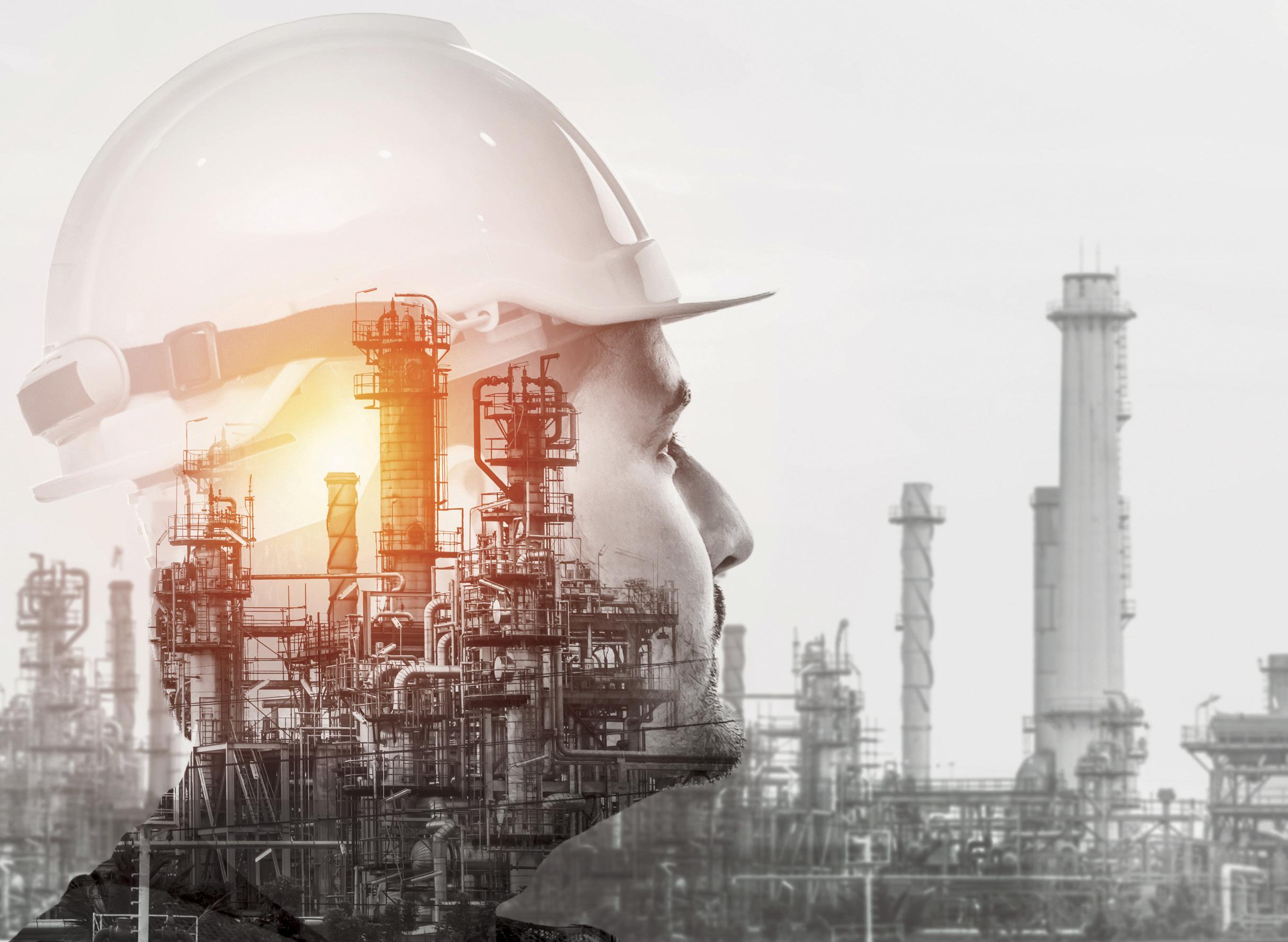
As chances of timely passage of a US$1.2 trillion infrastructure bill began falling faster than autumn leaves, hopes remained that the measure will yet deliver abundant opportunities for construction endeavors and related project and breakbulk cargo moves, as well as long-overdue improvements across transportation modes.
While politicking was continuing to stall U.S. House of Representatives passage of the Infrastructure Investment and Jobs Act following the Senate’s Aug. 10 approval of a revised version of the bill, a cross-section of interested observers shared with Breakbulk perspectives on the far-reaching benefits – and challenges – the measure could bring.
These experts, like so many Americans, were continuing to be optimistic the bipartisan infrastructure bill would clear its final legislative hurdle despite efforts in Congress to tie it to the Democrats’ even bigger US$3.5 trillion social spending and climate proposal that is a cornerstone of President Joe Biden’s agenda.
Andrew J. Gardner
Kiewit Supply Network
Christopher J. Connor
American Association of Port Authorities
“The infrastructure package currently before the House will definitely provide opportunities for the project and breakbulk cargo sectors,” said Andrew J. Gardner, president of Kiewit Supply Network, Lenexa, Kansas-based provider of comprehensive procurement services for construction and engineering industries.
While noting the number of materials for projects funded via the bill that can be sourced internationally will depend on Buy America Act requirements, Gardner commented: “Investments in bridge repair, replacement and rehabilitation, as well as investments in public transit, electric vehicle infrastructure and power infrastructure will increase project cargo demands across the United States.”
In addition, he said, the recent proliferation of cargo vessels off the California coast highlights the need for investment in port infrastructure to increase the number of vessels that can be unloaded and reduce the time required to unload each vessel.
PORT FUNDING EYED
Indeed, funding for port projects is among the key benefits the infrastructure program is seen as furnishing.
“The proposed infrastructure bill currently considered by Congress would provide sustained and substantial funding for ports,” said Christopher J. Connor, chief executive officer of the American Association of Port Authorities. “This would be a generational
CREDIT: SHUTTERSTOCK
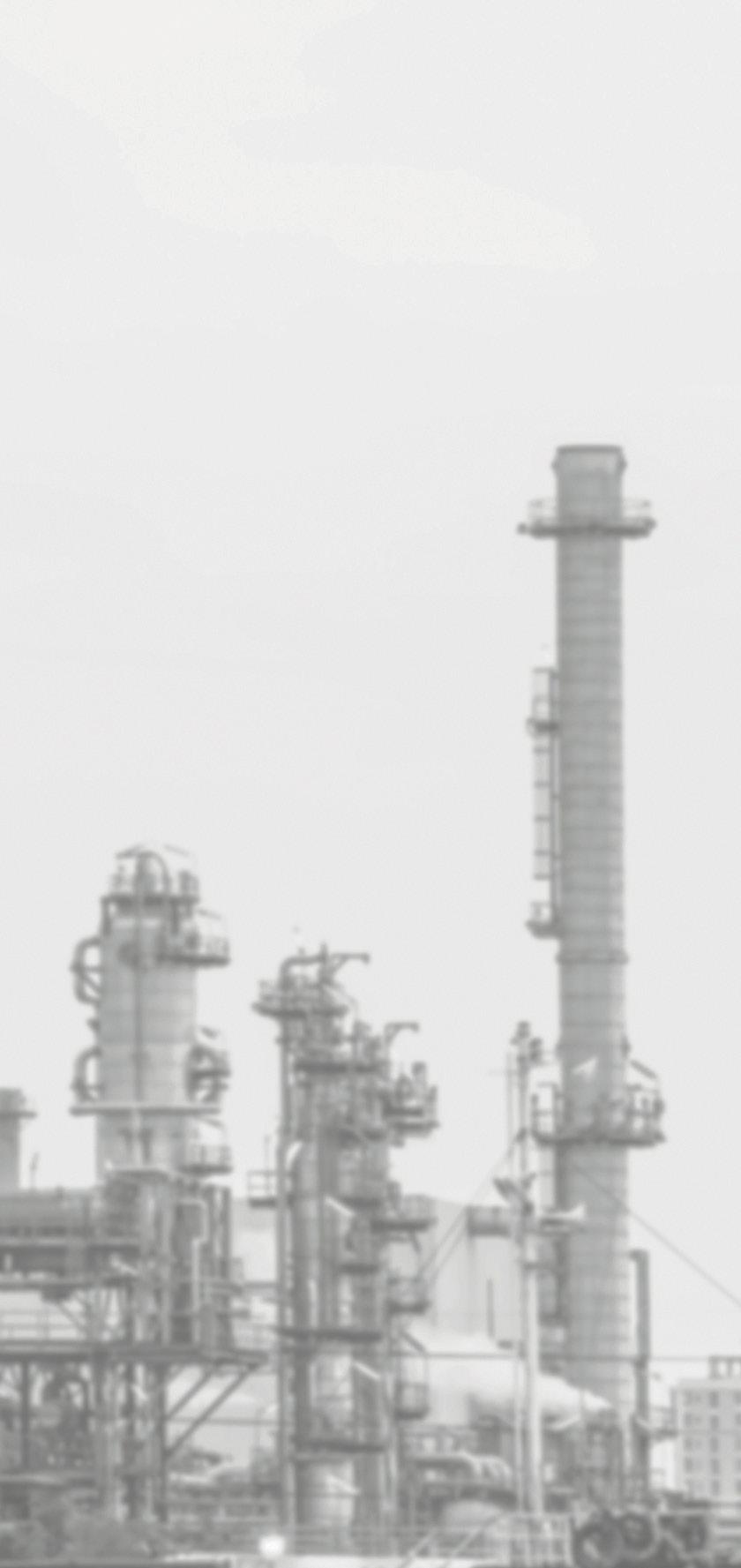
investment that would equip the port industry with the resources to move freight with even greater efficiency for years to come.”
In the 2,702-page iteration passed by the Senate in August, the bill calls for nearly US$17 billion over five years to go toward port-related undertakings, including port infrastructure development grants and U.S. Army Corps of Engineers construction, operations and maintenance projects along navigation channels.
Such investments are well-directed, according to Connor, who said: “Port funding yields a strong return on investment. Spending one dollar on maritime infrastructure returns two to three dollars to the national economy in jobs and productivity.”
Sharing in the view these investments will be enormously beneficial is Martin T. Whitmer Jr., partner in Whitmer & Worrall LLC, a Washington-based bipartisan government relations and strategic consulting firm, who cited the link between US$25 billion in combined port and airport spending to US$303 billion targeted for highway and bridge improvements, plus a streamlined federal agency decision system for project delivery. “This massive investment – coupled with Martin T. Whitmer Jr. environmental streamlining – means that infraWhitmer & Worrall structure will be upgraded across all modes of transportation,” Whitmer said. “It does no good to efficiently unload a boat if the boxes sit and wait for trains and trucks because of congested rail and highway infrastructure. These investments will more than pay for themselves by reducing time, cost and emissions of moving freight.”
The Infrastructure Investment and Jobs Act, Whitmer noted, also creates an Office of Multimodal Freight Infrastructure and Policy in the U.S.

Construction of plants such as the Lackawanna Energy Center in Jessup, Pennsylvania, requires extensive shipment of project cargoes – activity expected to be on the upswing with a broad-reaching infrastructure program in place.
CREDIT: KIEWIT SUPPLY NETWORK. Department of Transportation, while setting aside US$5 billion for freight movement megaprojects; US$8 billion for the Infrastructure for Rebuilding America, or INFRA, grant program; and US$20 billion for major multimodal freight discretionary grants.
“All of these investments are geared toward economic growth, moving goods quickly and safely while also maintaining the highest standard for the traveling public,” Whitmer said.
ECONOMY TO GAIN
According to a Sept. 17 report from S&P Global Ratings, the Infrastructure Investment and Jobs Act would more than pay for itself, adding US$1.4 trillion to the U.S. economy while providing nearly 900,000 new jobs over an eight-year period, while stimulating renewable energy programs.
The S&P Global analysis shows a rise in U.S. per capita income of 10.5 percent more than in a scenario without the infrastructure initiative.
Private-sector productivity would
Project cargo moves, such as this one for an oil refinery, are anticipated to increase following passage of a massive infrastructure measure. CREDIT: TUCKER COMPANY WORLDWIDE

also get a boost, averaging about 10 basis points per year, likely lifting average GDP growth on an annual basis to 2.1 percent compared with an even 2 percent gain without the infrastructure program.
The downside is there may be difficulties filling all the new positions with qualified skilled trade workers. A recent U.S. Chamber of Commerce report indicates 88 percent of commercial construction contractors already are having moderate to high levels of difficulty finding the skilled workers they need – and that’s before US$1.2 trillion in new infrastructure projects is added. This is leading to a call for expansion of workforce development programs.
Member firms of the Specialized Carriers & Rigging Association are likely to be among those with a demand for additional skilled labor, according to Chris Smith, the trade group’s vice president of transportation, who said public construction projects such as those to improve roads and bridges are apt to generate some of the most substantial hiring needs.
“It’s going to be a boost for our members for sure,” Smith said. “There’s going to be a ton of business opportunity for our folks.”
Smith also pointed to another facet of the bill buried within its more than 2,700 pages: establishment of federal programs to facilitate use by states of funding to secure automated permit systems for transport of oversize and overweight loads. That would remove cost as an issue for the 14 U.S. states that currently are still without such systems.
Chris Smith
Specialized Carriers & Rigging Association
Jeff Tucker
Tucker Company Worldwide
‘DESPERATE’ NEED
Jeff Tucker, CEO of Tucker Company Worldwide, a Haddonfield, New Jersey-based third-party logistics firm focused on specialized freight, said he sees investment in infrastructure – especially at and around ports subject to rising water levels – being as critical to national security as to breakbulk cargo operations.
“One of the greatest American natural resources of the 20th and 21st centuries is our infrastructure and our ability to move freight efficiently and inexpensively,” Tucker said. “However, our highways and bridges are in desperate need of expansion and reduction of bottlenecks to scale our economic growth.
“Many interstates and regional highways were built for the 1950s and 1980s and need significant investment,” he added. “This is especially true where ports are located – usually in congested urban areas without a lot of land to make expansions and improvements.
“The opportunity that infrastructure spending affords to breakbulk shippers and carriers is extraordinary, too,” Smith said. “Nearly every significant infrastructure project this nation undertakes will require countless breakbulk shipments to be made and moved. Infrastructure spending is as good for the nation as it is for breakbulk shippers, carriers and brokers.”
Kiewit Supply Network’s Gardner said the dual-pronged benefits of more project and breakbulk cargo moves and better multimodal infrastructure for accommodating such transports will be accompanied by a significant delivery-related challenge.
“The proposed investments will benefit project and breakbulk cargo,” Gardner said. “In addition to the project cargo needed to support improvements and expansion of roads, bridges, rail, water and power infrastructure in the U.S., this investment in infrastructure will ensure that future cargo transport will be faster, more efficient and more reliable.
“The challenge,” he said, “will be how we support these projects to ensure timely, reliable delivery of materials at a cost and schedule that doesn’t put any infrastructure project at risk.” BB
A professional journalist for more than 50 years, U.S.-based Paul Scott Abbott has focused on transportation topics since the late 1980s.
ACCELERATING GROWTH AT PORT HOUSTON
For more than 100 years, Port Houston has owned and operated the public wharves and terminals along the Houston Ship Channel, including the area’s largest breakbulk facility. Port Houston’s Turning Basin terminal and multipurpose facilities specialize in breakbulk, heavy-lift, steel, ro-ro, liquid and dry bulk. Centrally located on the Gulf Coast, Port Houston facilitates the movement of cargo coming or going to the U.S. West and Midwest, with reach to 156 million consumers within 1,000 miles.
It is no secret that Houston is the energy capital of the world; that said, the Houston Ship Channel plays a special role. With more than 200 public and private terminals along the waterway, the ship channel is home to the largest petrochemical complex in the U.S. and secondlargest in the world. With more than 200,000 barge transits and more than 8,000 vessel calls annually, the channel represents more than US$800 billion in economic value to the U.S.
Over the course of the pandemic, many challenges have affected the industry and supply chain, causing global disruptions that are still felt to this day. Port Houston is not immune to these challenges, and thus continues investing in infrastructure, the expansion of the channel and fostering relationships with stakeholders to help prepare for the future.
Port Houston is the advocate and a strategic leader for the Houston Ship Channel and is currently undergoing the process of deepening and widening the waterway, a billiondollar project known as Project 11. This October, at a special Port Commission meeting, the first contract for Project 11 was awarded to initiate dredging. The expansion will help ensure safer and more efficient movements for vessels on the channel. At Port Houston, cargo is flowing at unprecedented levels and any supply chain challenges translate into opportunity. One result is the Turning Basin Terminal began to see a surge in containers to accommodate customer needs. Just recently, the Star Lygra, a G2 Ocean breakbulk ship, arrived at the breakbulk docks with 53 Amazon containers from Asia. Steel imports are also steadily rising as the oil and gas industry recovers. There has been a 28 percent increase in steel as-of September year-to-date compared with the same time last year.
In addition to this, land to accommodate cargo is in high demand and Houston continues to be a hotspot for warehousing and laydown for general cargo. Port Houston is a key player in meeting those property needs, with land available adjacent to the waterfront, FTZ designation and flexible spaces suitable for wide, heavy cargo and vehicles.
“At Port Houston we embrace our position as a centrally located port serving a large region of consumers. Providing efficient and predictable cargo movement through our port during an unprecedented surge in global imports continues to be a top priority for us,” said Roger Guenther, executive director at Port Houston. “We expect elevated levels in the supply chain to continue well into 2022 and will continue to explore opportunities including accelerating an already aggressive capital investment strategy for our terminals to stay in front of the demand.” n
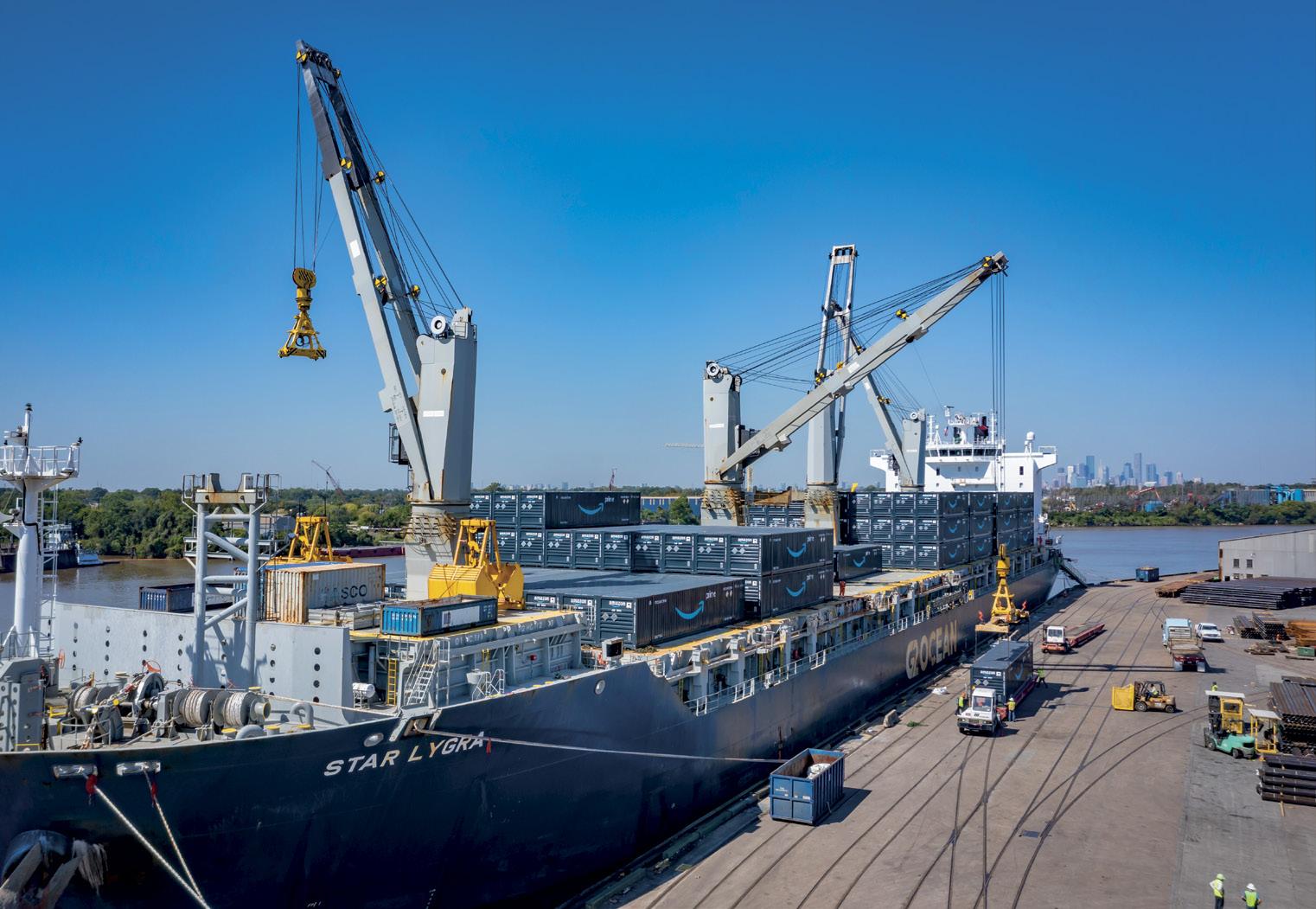
PROFILE
IT’S ALL IN THE
STRATEGY Crowley CEO Responsible for Industry Success Story
BY LORI MUSSER
Following in the footsteps of his father and grandfather before him, Thomas B. Crowley Jr. is a champion of progress for the maritime industry and kindred sectors.
Since 1994 – 102 years after the company was founded by his grandfather with a lone rowboat – Crowley has served as CEO and chairman of Crowley Maritime Corp. He hasn’t been idle. The scope and scale of the company today are a far cry from a single Whitehall rowboat on San Francisco Bay, but the same level of energy and vision that jumpstarted the company all those years ago appears to be alive and well today.
In the last 27 years, Crowley has overseen an evolution which is one of the great success stories in maritime transportation and logistics. Diversification appears to have largely spared the company from the incredible vagaries of the marine sectors in the last decade or two. Today, the company’s four global business units include Crowley Logistics, Crowley (Government) Solutions, Crowley Shipping and Crowley Fuels. Headquartered in Jacksonville, Florida, the company is one of Florida’s largest employers and earns revenue in the range of US$2.5 billion each year.
Tom Crowley projects a friendly, open, focused presence. After only a few minutes of conversation, his vast knowledge of all things maritime and his interest in symbiotic initiatives comes shining through. Perhaps that is to be expected of a CEO who was raised in the business. He recalled with pleasure visits to shipyards and tugboats as a child, followed by his first part-time job in the company as a high schooler.
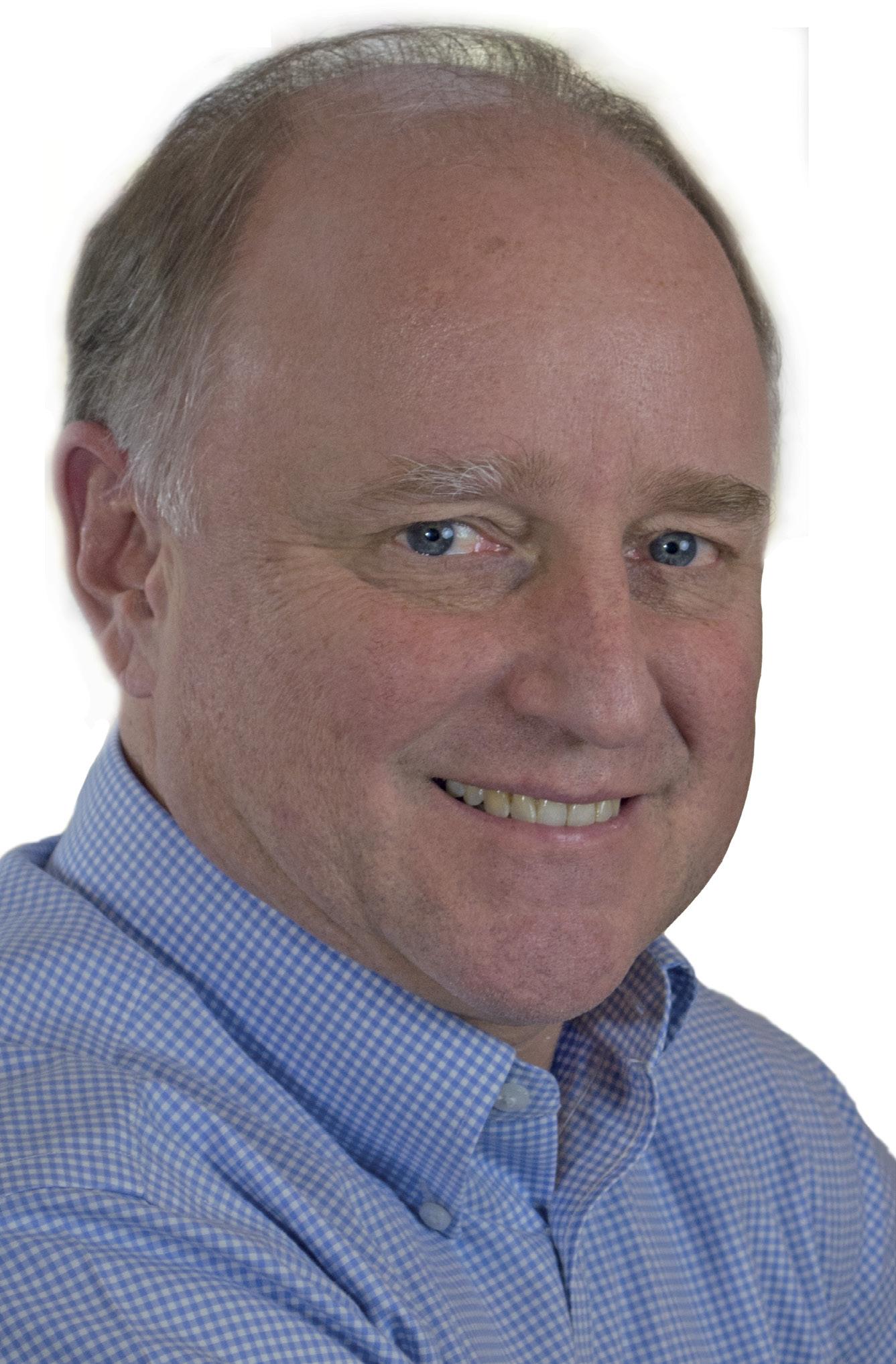
Thomas B. Crowley. CREDIT: CROWLEY
Crowley serves as a chief executive of the four business units in different geographical areas and in different business segments. He said he focuses on “building a good strong team, good communications, and leveraging technology.” Agility is critical in his scope of business, and so he takes time to cultivate an agile attitude – “We have to be receptive to customers’ needs” – and a positive culture that permeates all activities.
MAKING CONNECTIONS
Tom Crowley said his favorite part of the job is connecting with people within his organization – mechanics, truck drivers, mariners, office staff. “It gives me better perspective,” he said.
He described his management style as adaptable, which has likely served the company well during the Covid-19 era. “The amount of change that has occurred is significant. Some people say we lost a year. I say that we gained five to 10 in deploying technology and changing the way in which we work, in many aspects for the better.” He then cautioned there would be some catchup needed to keep culture intact and talent engaged in this new era, “but I think the effectiveness of our team and people has leapfrogged.”
Crowley described his team as having a “get it done” approach. “Employees have a lot of pride in the company. They go after challenges,” he said. Family and employee ownership are a hallmark of Crowley Maritime, and quite possibly one of the main secrets to its success. Crowley is quick to credit his team for achievements large and small, for dedication and commitment, and even for their altruistic endeavors.
The company has numerous programs that channel its good corporate citizenship. Its Crowley Cares initiative has done everything from painting an orphanage in Central America to donating and distributing food to veterans-in-need to raising awareness for health and wellness through American Heart Association events. Crowley Cares programs are
For many CEOs a work-life balance is hard to strike. “My job is not a transactional job,” Crowley said. He must always think big-picture and long-term. Results of decisions made each and every day are not usually seen for a while. “In my personal life, I like a nice beginning and an end.” That extends to time spent with family in a range of outdoor activities – skiing, boating, hiking – as well as simple endeavors like cooking and even cleaning out the garage.
Crowley shared another career highlight, which he called possibly one of his craziest decisions, which was taking on the Costa Concordia salvage job. The grounding of the cruise ship in the Tyrrhenian Sea in 2012 was an international news event. Crowley’s former TITAN Salvage subsidiary, in partnership with an Italian marine contractor, was able to remove the wreck, since deemed the most technically demanding marine salvage in history. The wreck required anchoring and stabilizing, preparing supports on the underside, parbuckling, affixing sponsons (buoyancy chambers) and then refloating with 36 hydraulic strand jacks, and delivering to Genoa scrappers. TITAN received numerous awards for the herculean effort including one from the North American Marine Environmental Protection Association.

Crowley focuses on building strong teams, good communications and leveraging technology.
CREDIT: CROWLEY
employee-driven, fostering change in the communities the corporation serves, Crowley said.
The company sees great value in diversity. “For us, it is starting from the inside out. We’ve had a diversity and inclusion council for a number of years, creating employee resource groups to better connect,” he said.
When asked about career highlights, Crowley was modest: “Probably the most satisfying was our response to Hurricane Maria – getting relief down to islands.” In addition to an enormous effort to first protect and then fix and then redeploy or reopen terminals, warehouses, vessels and other assets, the company made heroic efforts to facilitate the collection, transport, release and distribution of food and aid cargo.
STRIKING A BALANCE
During his tenure as CEO Crowley has seen much change: “We have been involved in many geographies and types of service – generally focusing on hard-to-reach sites … or those with logistical challenges. I would say the biggest change [lately] has been the rapid drop-off of offshore oilfield development.” That change has triggered a change in corporate strategy that emphasizes flexibility and adding value using the equipment or expertise or other assets it can bring to table.
Crowley’s diversified fleet services a range of maritime industries.

CREDIT: CROWLEY MARITIME SERVICES
SUSTAINABILITY STRATEGY
Crowley Maritime is a recognized leader and aims to be “the most sustainable and innovative maritime and logistics solutions company in the Americas by 2025.”
“Clearly our industry has an opportunity to clean up emissions and do things better. Previously we were focused on [not] spilling oil but it goes beyond that now … there is a long way to go to lessen the industry’s footprint,” Crowley said.
Electric equipment and assets are integral to Crowley Maritime’s plans. “We have a team internally that developed a concept for a fully electric tugboat, working on battery power. We’re excited about getting that launched in a couple of years,” Crowley said, expressing pride in employees who approach challenges proactively.
In developing its sustainability plan, Crowley Maritime created a materiality matrix, prioritizing what matters most to ensure that strategic actions have the highest potential for positive impact.
New energy is a high priority. Crowley launched the world’s first liquefied natural gas-powered ConRo ships in 2018 and 2019 on the Puerto Rican trade. A US$550 million investment built two American ships and associated port upgrades. The vessels accommodate international and domestic containers as well as roll-on, roll-off.
In the LNG arena, Crowley has designed and developed customizable LNG bunker barge concepts, will charter (with Shell) an LNG bunker barge that will be U.S.-built and have a record 3.17-million-gallon capacity, and is deploying 10,700-gallon ISO tanks to enhance mobility of LNG to customers in Puerto Rico, the Caribbean and Central America.
WINDS OF CHANGE AT WORK
In January 2021, Crowley created a New Energy division. The company’s media release described a goal of providing broad, coordinated services supporting emerging energy sectors, particularly in LNG and offshore wind.
JONES ACT AND WORKFORCE ADVOCATE
A staunch supporter of the U.S. Jones Act, maritime academies, and their role in national security preparedness, Thomas B. Crowley, Jr. said the offshore wind industry will require U.S.-built vessels and U.S. mariners.
“This is a very great opportunity for this country to create more jobs locally,” he said. “American jobs are incredibly important, and these aren’t just service jobs. These are highly trained,” he said, adding that the quality of talent at maritime academies is incredibly impressive – “some of the best and brightest” – and that Crowley Maritime is probably the largest employer of cadets in the nation. Ever a proponent of proficiencies, in August, Crowley Maritime and Massachusetts Maritime Academy announced they will create a first-of-its-kind training and workforce development program dedicated specifically to the New England region’s offshore wind energy industry.
In June, Crowley Maritime and the University of North Florida announced plans for a Crowley Center for Transportation and Logistics, predicated on a US$2.5 million gift. The university’s transportation and logistics program is elevated by a high-tech Logistics IT Solutions Lab that spotlights advanced supply chain tools and solutions, according to Crowley.
Rendering of Salem Harbor, a 42-acre port for offshore wind, which Crowley is involved in.

CREDIT: CROWLEY MARITIME CORP.
Crowley said he sees sustainability as integral to future success, and that the industry needs to work hard on the transition. He said he sees a great many opportunities related to new and clean energy, including opportunities for corporate investments and for creating new well-paying jobs: “Offshore wind is upon us now. Strategies are aligned. We have studied the market and understand where developments will be.”
On Sept. 30, 2021, Crowley announced a major wind energy deal. The company is to enter into a public-private partnership with the City of Salem, Massachusetts, to create and operate at Salem Harbor a 42-acre port for offshore wind, under an agreement with Vineyard Wind, the future anchor tenant. The site will be purpose-built for the assembly and staging of turbines – blades, nacelles and tower sections destined for offshore installation.
This venture seems fitting for a corporation whose strategies routinely position it as a provider of service offerings through the full lifespan of a transaction, as in complete supply chain services for cargo, or in this case, complete project development, port operation and maintenance, and undoubtedly future Jones Act-compliant feedering to and from offshore wind sites.
Crowley said: “We’re looking at ongoing needs from shoreside terminaling to supporting wind farms,” and he described skill sets that will serve the company well in the jump to offshore wind including expertise in moving large construction project components, experience in offshore oil and gas services, engineering and naval architecture strengths, and management and operational proficiency in deploying U.S.-flag assets.
Since 2018, Crowley has also extended its defense and government logistics reach. Building on long-time experience in government ship management, the company was awarded the US$2.3 billion Defense Freight Transportation Services contract, one of the U.S. Department of Defense’s largest transportation services contracts.
FUTURE ESSENTIALS – VISIBILITY, PREDICTIVE ANALYTICS
Crowley predicted that powerful drivers of future success would include visibility and analytics. “Cargo visibility is paramount ... Customers want to know when it is getting there or when it will be delayed. Tracking, data analytics, predictives,” in concert with learning the business of customers to put in place better solutions, is becoming critical.
With new capabilities, Crowley said, it is easier to follow the movement of cargo from “where it is worth nothing to a place where it adds value and is of service. It takes heavy assets and equipment to get the job done, and more and more it takes technology and that will change us.” Predictive analytics will transform all parts of transportation, creating efficiency and sustainability, he said, so Crowley Maritime is “looking for opportunities where we can combine technology and good old-fashioned knowhow to do things better for the customer.”
At a time when many logistics CEOs swoop in from a parallel industry and leave just a few years later, Crowley stands out as a longtimer with a master hand, a strategist who somehow combines a stalwart ambassadorship for maritime, with an eagle eye for leveraging existing corporate strengths into new and apparently successful businesses. BB
Based in the U.S., Lori Musser is a veteran shipping industry writer.
CASE STUDY
BLACK HAWK UP
BY THOMAS TIMLEN
Helicopters Make Unusual Air Journey to the Philippines
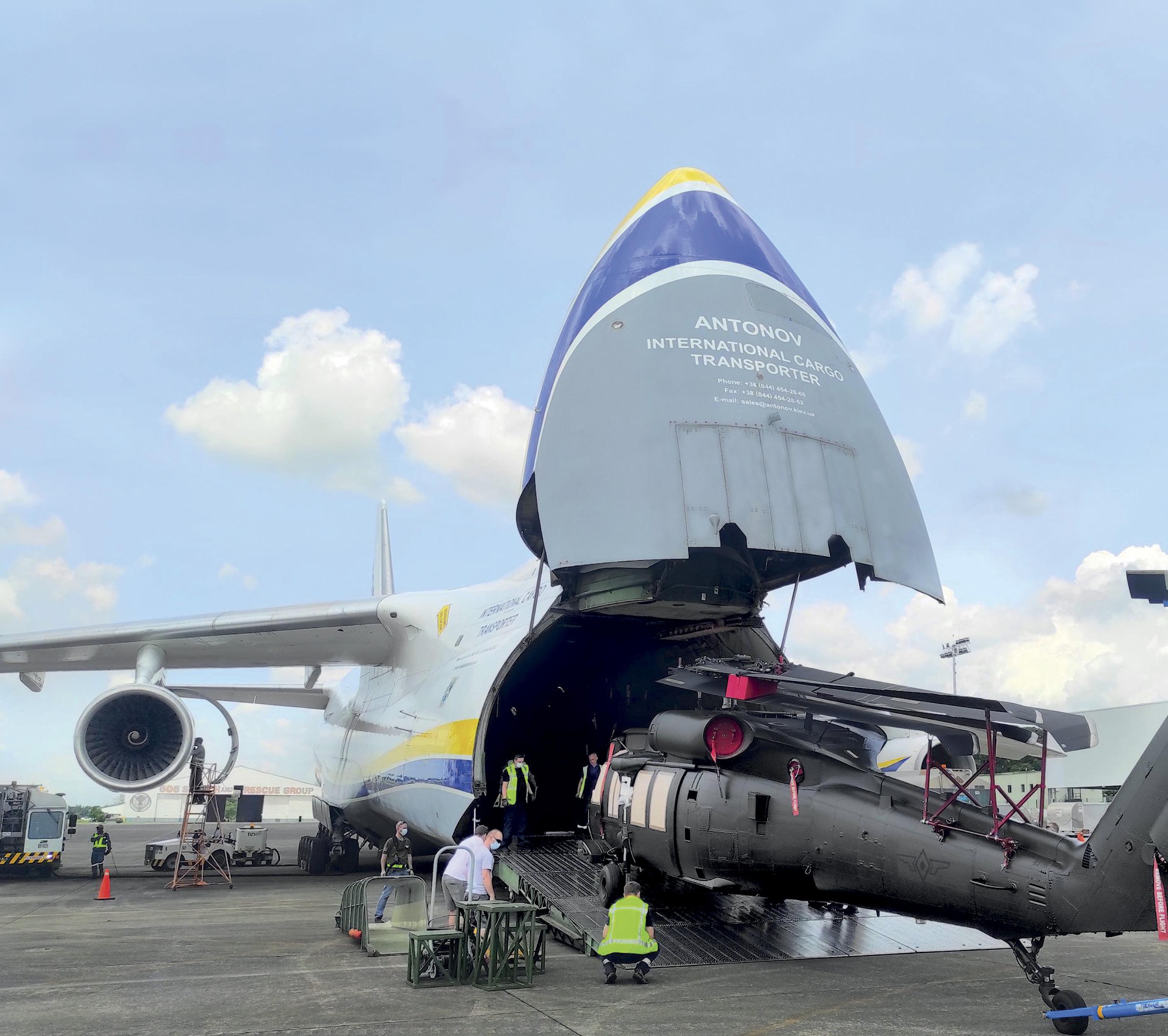
As the Philippines Army vintage Bell UH-1 Huey helicopters that hark back to the 1960s have aged, an increasing frequency of mishaps placed mounting pressure on the government to initiate a program to decommission and replace them with a modern and efficient replacement fleet. Pressing for the purchase of replacement aircraft, President Rodrigo Duterte described the Hueys as having “metal fatigue.”
Heeding the calls of the president and others, the Philippine government awarded the Polish company Polskie Zaklady Lotnicze Sp.z.o.o., (PZL Mielec) the contract for 16 S-70i Black Hawk helicopters in April 2019 as part of the Armed Forces of the Philippines Modernization Act.
In addition to the traditional military defense roles played by the Philippines’ helicopters, they have been deployed to support operations to suppress insurgency groups in the southern parts of the country, while also playing a critical role in disaster relief operations by distributing aid across thousands of islands in the aftermath of storms and typhoons and transporting injured and sick victims from remote areas to medical facilities. The new challenge involving the distribution of Covid-19 vaccines throughout the country has escalated the urgency to modernize.
At a cost of US$241 million, the 16 helicopters are being manufactured by PZL Mielec under license from Sikorsky USA. The first batch of six Black Hawk helicopters was delivered in December 2020. The second batch of five helicopters arrived on June 7, at the Philippines’ Clark Air Base in Pampanga.
Speaking at Clark Air Base in June, Philippine Air Force spokesperson Lt. Col. Maynard Mariano said: “With the latest delivery, the PAF now has 11 Black Hawk utility helicopters. Meanwhile, the third batch of five helicopters
The Polish-built Sikorsky S-70i Black Hawk helicopters were loaded using the AN-124-100’s winch system.
CREDIT: ANTONOV AIRLINES
is scheduled to be delivered before the end of 2021.”
“We are grateful for the trust that the Republic of the Philippines has placed in PZL Mielec and the Sikorsky S-70i Black Hawk aircraft for its Combat Utility Helicopter fleet,” said Janusz Zakręcki, PZL Mielec president and general director. “We were able to complete delivery on time according to the schedule as a result of the strong partnership between PZL, Sikorsky, the Philippine Department of National Defense and the Philippine Air Force.”
MODE OF MOVEMENT
The deliveries in November and June were orchestrated in a way that might come as a surprise, as the Black
In fact, the transport went so well that shipper Sikorsky said it would have no hesitation in choosing air freight for delivery of the helicopters in the future.
Several factors led to the decision to transport the Black Hawks by air. “We achieve economies of scale when transporting five aircraft on the same flight, that is, by filling the plane versus shipping the same quantity by sea,” a Sikorsky spokesperson explained. “Each aircraft can be transported without needing to be completely wrapped, unlike in the case of a sea shipment. There is lower risk of damage compared to transporting by road and sea haulage. The speed of delivery is one to three days compared to weeks by road and sea.” Also, the spokesperson pointed out that the delivery of one helicopter by sea in the first batch was delayed and arrived two weeks after the Antonov air shipment.
Hawks were not transported by land and sea, but rather by air.
With almost 10,000 kilometers between the PZL Mielec facilities in Poland and the Clark Air Base in Pampanga, it would not be unreasonable to assume that the helicopters would be transported by road or rail from the manufacturing site to the closest seaport in Poland for an onward ocean transport. However, except for one Black Hawk that was transported by sea, air freight provided several advantages for the rest.
Each S-70i helicopter measures 17.52 meters long, 3.2 meters wide, 3.9 meters in height, and weighs 5.6 tonnes. Each consignment of five Black Hawks weighs in at 35 tonnes when including the loading equipment. The only aircraft fit for the job was Antonov Airlines’ world-recordholding Ruslan AN-124-100, capable of transporting a payload of up to 150 tonnes and the world’s largest production transport airplane.
Amnon Ehrlich, Antonov Airlines’ aerospace, government and defense programs director for North America, described to Breakbulk how collaboration facilitated the successful air transport. “Although the total payload in terms of weight was considerably light for our aircraft, loading five Helicopters safely and transporting them without damage takes considerable collaboration. We have been working closely with both Sikorsky as well as their logistics supplier Helicopter International Shipping Services (HISS) for the past several months to ensure that all current and future program requirements are met.”
Representatives for Sikorsky, a Lockheed Martin company, told Breakbulk that the company is highly satisfied with the service provided by Antonov Airlines and the freight forwarder HISS. Transport by air of the S-70i Black Hawk aircraft was planned from the beginning for both air shipments to the Philippines. Close collaboration with Antonov and HISS ensured that the 10 Black Hawks arrived at their destination in the Philippines without damage and on schedule.
HANDLE WITH CARE
While Black Hawks are built for battle and therefore strengthened to protect their crew and structural integrity, appropriate handling must still be observed.
“While Black Hawk helicopters are designed to rigorous military standards, we treat any helicopter with care,” Sikorsky’s spokesperson said. “To ensure easy roll-on, roll-off onto the Antonov, we merely fold the main rotor blades while they are still attached to the rotor head. Given the size of the Antonov plane, there is no need to fold the tail pylons. Once loaded, each helicopter is securely strapped to the cabin floor.”
While freight rates are comparatively lower on ocean routes compared with air freight, cost advantages can still be gained when engaging an air carrier, the spokesperson said. “Sikorsky delivers commercial and military helicopters by airfreight when there is a business case to do so and/or when a delivery schedule requires it. On a per aircraft basis, filling the Antonov plane with five Black Hawk helicopters is less expensive than shipping the same five helicopters by sea.”
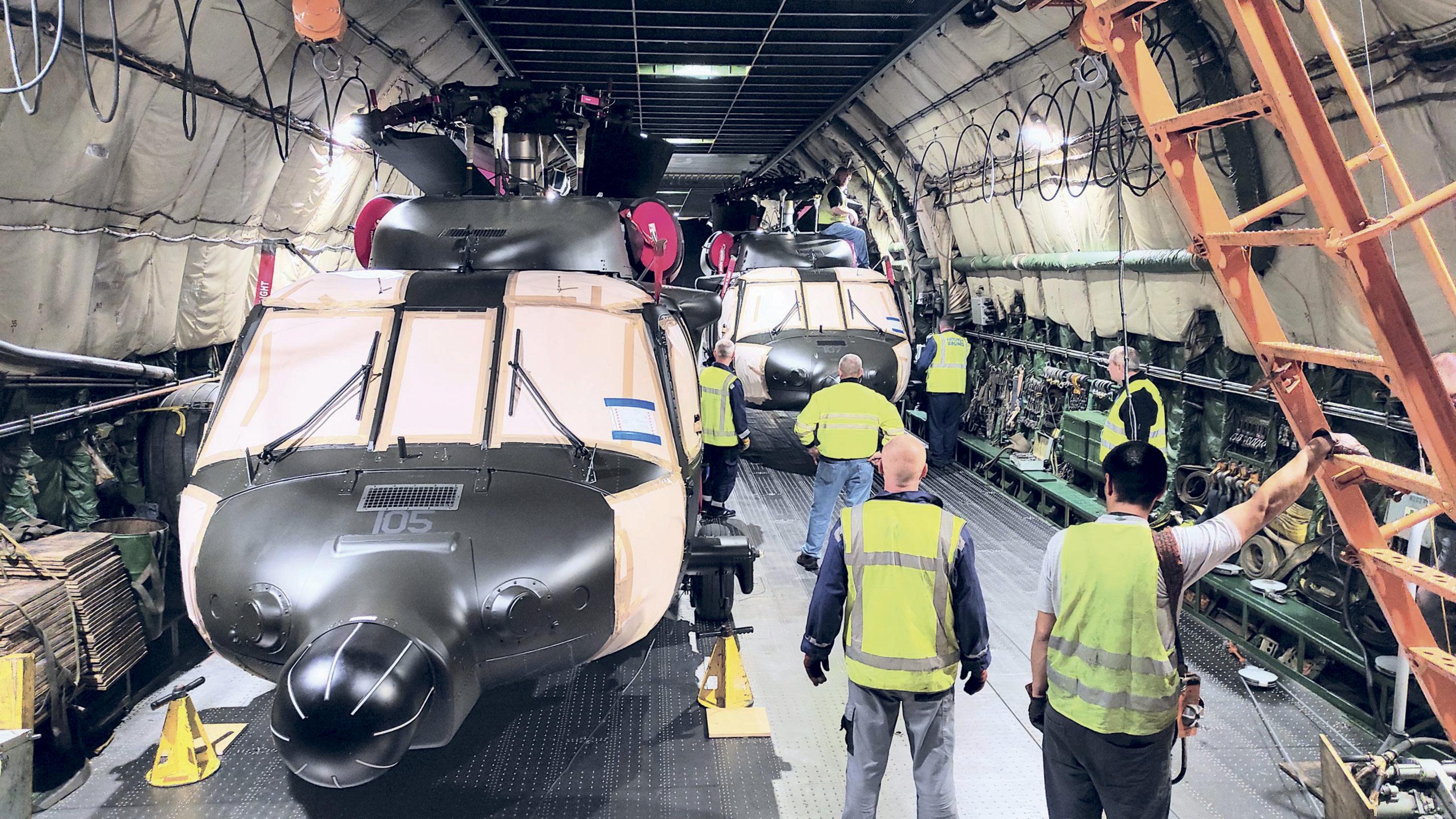
Detailed loading and unloading plans were developed by Antonov Airlines’ in-house engineers to ensure the safe stowage and transport of the military cargo within the AN-124-100’s cargo cabin specifications. CREDIT: ANTONOV AIRLINES
Certainly time-related advantages of moving cargo by air are attractive – and in this case they exceeded expectations: “We planned from the beginning to ship the five Black Hawk aircraft by air to the Philippines. Doing so allowed us to deliver to a more aggressive schedule. Shipping by sea would have added two months to their arrival in country, versus two days to transport by air.”
There were other factors to consider as well in the selection of mode. “Surface transport is less expensive on a per aircraft basis. We will often transport a single helicopter by sea.” For a single helicopter, air freight will amount to about three times the cost of ocean freight. In contrast, for five helicopters, ocean freight is about 50 percent more expensive.
Similarly, the distance between the place of manufacture and the place of delivery impacts the choice of transport mode. “Not all helicopters are transported by sea or air freight. The option to ‘ferry’ one or more helicopters also exists, meaning Sikorsky and/or the customer’s pilots fly the helicopters to their destinations. S-70i Black Hawk helicopters produced at the Lockheed Martin PZL Mielec facility in Poland, and destined for another European country, would be ferried in this way,” Sikorsky explained.
Other factors that make air transport more attractive include the lower risk of damage to the Black Hawks, lower risk of tampering or sabotage during transport, and a reduced risk of damage as there is less handling of each unit in comparison with on-loading and off-loading between road, rail and sea links.
PLANNING THE LOAD
Prior to loading, detailed loading and unloading plans were developed by Antonov Airlines’ in-house engineers to ensure the safe stowage and transport of the Black Hawks. Sikorsky’s spokesperson said that process needs to be started early in the project.
“Collaboration of an air shipment from Poland by Sikorsky’s Aircraft Delivery Operations team in the United States can begin 12 weeks before departure typically with one administrative point of contact at Antonov Airlines. Detailed planning with HISS of the load/unload, export paperwork and other associated logistics occurs four to six weeks ahead of departure via two to three administrative points of contacts. Personnel at PZL Mielec are also involved. Planning discussions take place via email, Skype, and phone calls.”
With the safe arrival of the second batch of helicopters, the Philippines wasted no time with their deployment. “The recent arrival of the five Black Hawks will further boost the heli-lift capability of the Armed Forces of the Philippines and will help the government deliver more services in more areas in less time,” said Mariano, of the Philippine Air Force. “In the past few months, the Black Hawks transported vaccines and PPE (personal protective equipment) sets to the remotest areas of Batanes, Bicol, and other parts of the country.”
The collective efforts of project cargo specialists allowed the helicopters to be put to work on schedule – in view of Mariano’s remarks, all expectations of this project were clearly met. BB
Thomas Timlen is a Singapore-based analyst, researcher, writer and spokesperson with 31 years of experience addressing the regulatory and operational issues that impact all sectors of the maritime industry.