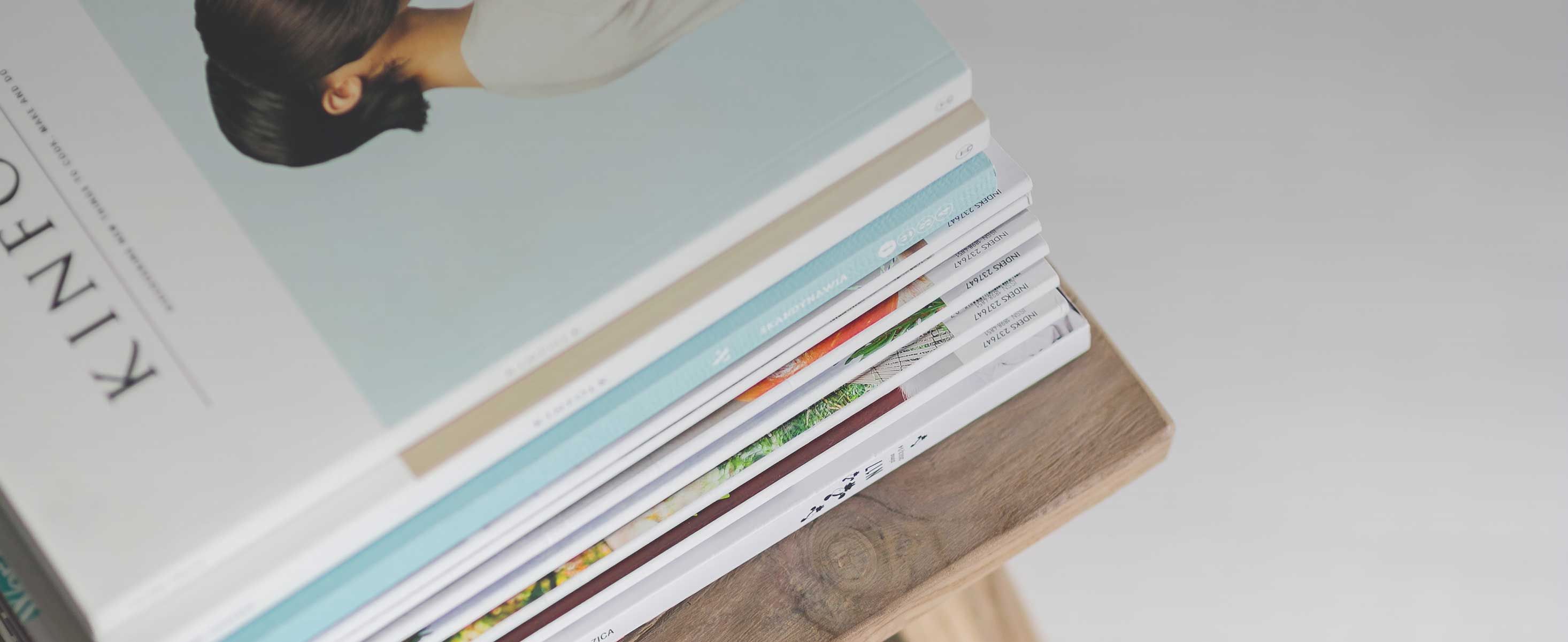
4 minute read
KILOTONS OF CARGO MOVED IN THE BIG FREEZE
deugro’s Early Involvement with EPC Key to Success
Constructing any major petrochemical plant entails numerous obstacles, with kilotons of components to be transported to site and complex lifting procedures necessary for installation. This process is made all the more difficult, however, when passage to the site involves navigating temperatures as low as -17°C and piloting semi-frozen waterways.
This was the challenge faced by project logistics firm deugro when it successfully delivered 120,000 freight tonnes of cargo for Hyundai Engineering as part of Polish chemical firm Grupa Azoty’s new Polimery Police plant. Located in Police in northwestern Poland, construction of this vast plant began in January 2020 but was delayed by Covid-19 and complicated by the scale of the out-ofgauge, or OOG, units needed.
The first petrochemical complex producing polypropylene in Poland, construction required OOG units
BY MALCOLM RAMSAY
weighing 7,156 tonnes, (67,800 freight tonnes) to be shipped from Asia to Poland. The largest of these units included an 889-tonne propylenepropane splitter, five 613.98-tonne propylene storage bullets and a 596tonne reactor.
Problem: jetty. Given the difficult conditions expected in Poland, preparations were planned around the unloading sequences and the final discharge method at the Barkowy jetty in Police.
Solution:
Understanding the unique challenges involved in this move was a central aspect of the project and close communication with the client was essential, not only in winning the contract but throughout every stage of delivery.
“deugro supported Hyundai Engineering since the beginning of the engineering, procurement and construction bidding stage, both commercially and technically,” Jin-Ho Lee, deugro Korea, told Breakbulk. “We also participated in package bidding for the project as a registered logistics partner of Hyundai Engineering. Despite strong competition, deugro was awarded the heavy-lift portion of the project, as the logistics service provider, including offshore, onshore and civil works for the project—exactly the part of the project we bid for.”
Early Start For Visits And Surveys
Before any operations began, deugro and its sister company dteq Transport Engineering Solutions conducted detailed site visits and route surveys to identify potential obstacles and challenges, and used the data from these visits to plan appropriate transport and engineering solutions, with project preparations spanning approximately one year.
With components fabricated at sites hundreds of kilometers apart, deugro was contracted on a freight on board basis to deliver cargo from the ports of Gunsan and Masan, South Korea and at the Port of Zhangjiagang, China. The cargo would then be shipped to the Port of Morski on the Baltic Sea coast, before onward transport by barge to Barkowy
For deugro the first operational stage involved prepping heavy-lift vessels as many of the cargo units were not stackable. This meant the firm had to develop a customized stowage concept to match the vessels’ stowage capacities.
“The reactor and propylene-propane splitter are not very different. However, regarding the propylene storage bullets, at the beginning no saddle was installed so we had to support the installation of the saddle on board at the port of loading,” Lee explains. “Both suppliers’ facilities are close to Gunsan and Masan, so as per the request from Hyundai Engineering, we put a vessel on each port.”
Firstly, 249 cargo units, weighing a total of over 16,000 freight tons, and including the 44-meter-long reactor, were loaded on board Spliethoff’s Ice Class E3 multipurpose vessel Pietersgracht using its on board cranes in South Korea.
A second operation then saw 40 cargo units, totaling 15,962 freight tons, and including the propylene-propane splitter, loaded aboard Jumbo’s heavylift vessel Jumbo Jubilee at the Port of Zhangjiagang. With the cargo safely loaded the components then began their 8,000-kilometer journey to the Port of Morski.
Icy Reception
Upon arrival in Poland the temperature was -17°C, and as a result ice breakers and special tugs had to be arranged to break the ice prior to berthing. For the onward journey in Poland, deugro partnered with engineering and heavy-lift firm Mammoet and forwarder Best Logistics to ensure the path from the port to the project site was seamless.
“In Port Morski Police, the biggest issue was to fit in with the schedule of other ships handled by Grupa Azoty,” Piotr Bossy of Best Logistics explained.
Once berthing slots were secured, the main equipment was discharged directly from the vessels onto three barges, with special care taken to monitor the vessel’s mooring orientation and wave swells while simultaneous ballasting operations were completed to precisely transfer the cargo. Loadspreading was also carried out with a 400-millimeter timber load-spreading layout on the barge deck and in accordance with the strong point of the vessel and saddle distances of the cargo.
From here the barges sailed south, down the West Oder, to the Barkowy jetty, six kilometers away, where they were discharged to trailers. Local port authority restrictions, however, meant that discharge from the multipurpose vessels to barge and from barge to land could only take place during daylight, while traffic regulations meant that road transport could only be conducted after 2300 hrs. This combined with the fact that the three barges were utilized on consecutive return trips, meant that the window for loading was tight, and as a result transport took six weeks in total.
What’s more, the barges faced ice thickness of over 5 centimeters, outside of the normal operating conditions for inland barges, so the team had to arrange ice breaking services from Port Morski.
Bossy of Best Logistics commented: “Luckily for us, in Port Barkowy Police, Grupa Azoty dumps warm water, so it never freezes,” but added that the entry canal to Port Barkowy Police caused problems as “we had as little as 2-meter clearance when passing through with 20-meter-wide pontoons.”
VIGILANT ROLL-OFF
During barge unloading at Barkowy, the mooring configuration was also a critical factor, with the team relying on four on-deck winches and an additional temporary bollard on the pier to ensure stability.
“Space-wise, for driving off we had sufficient tolerance, as the civil works and roll-on/roll-off ramp were specifically designed for the pieces of cargo we had to receive,” Rutger Beelen of Mammoet noted. “The biggest challenge was for deugro to find barges or ships which were suitable for the cargo available and had sufficient ballast capacity to keep level with the quay.”
With more than 30 barge trips in