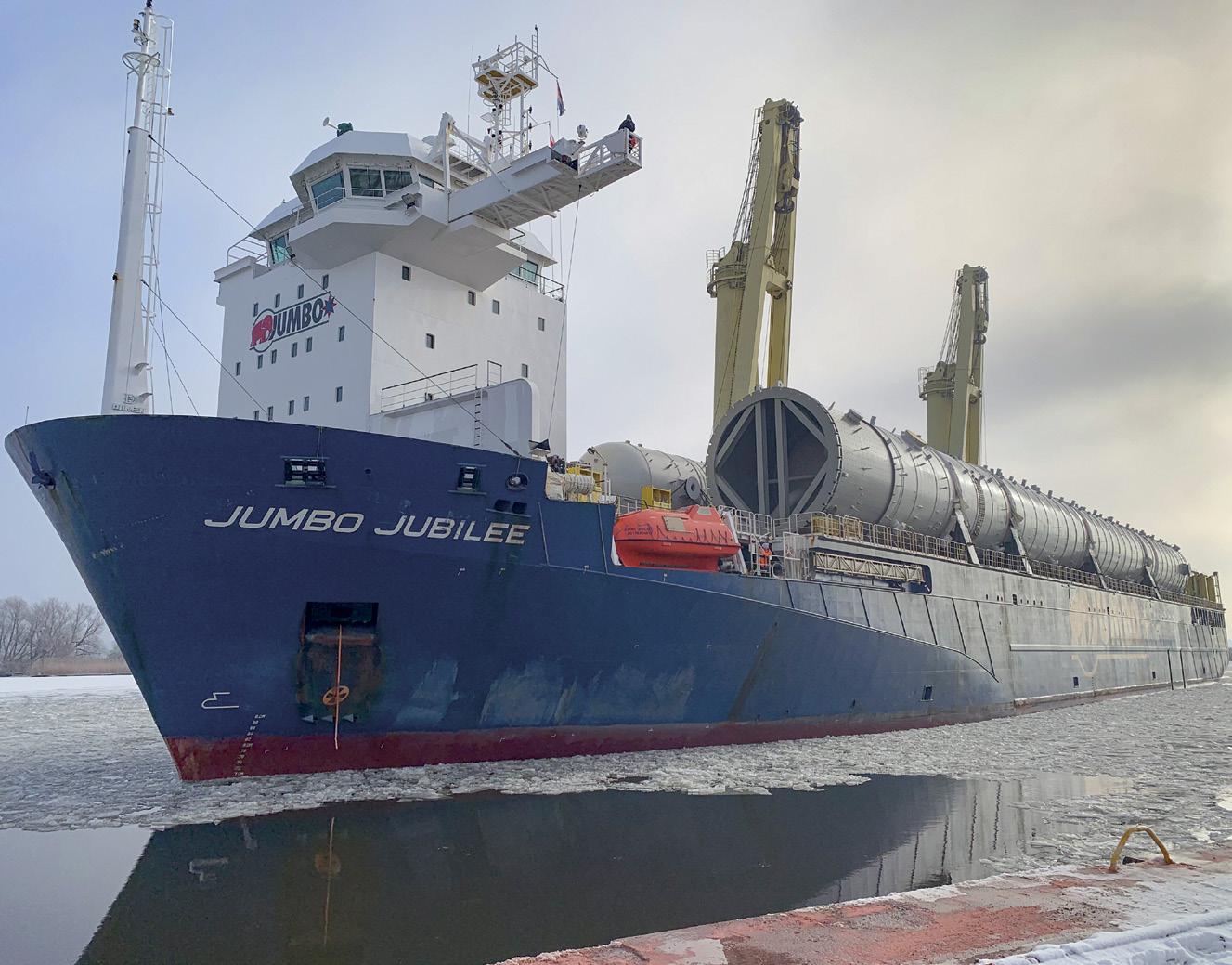
5 minute read
CASE STUDY
total the components were finally ready for transport by land. Here the team relied on Mammoet and its fleet of selfpropelled modular trailers, utilizing Goldhofer PSTs, prime movers and K25 trailers, to make the short trip to the plant construction site. The longest item – the 96-meter-long propylene-propane splitter – was moved on a KAMAG K25 modular platform trailer using two 16-axle lines with a turntable to navigate the narrow turns.
“All heavy cargo was unloaded onto the trailers and had to pass a sewage treatment plant run by the project owner’s parent company. Since there were a lot of underground pipes in that area, the most important tolerance we had to secure was 8 tonnes per axle,” Lee said. “Basically, the ground bearing pressure on all public roads in Poland is 8 tonnes per axle, so all roll-off operations were planned based on that number. This number had to be seriously kept to, as the first place where the roll-off unloading was executed was the Barkowy jetty, which is also the private jetty of the project owner and its parent company.”
Extensive Civil Works
These restrictions were compounded by the fact that there was no route from the Barkowy jetty to a public road that did not cross a ‘conveyor route’, on which road modification is prohibited and traffic is unable to stop. As a result, the partners had to oversee construction of a new ramp and 650-tonne flyover bridge to ensure that the cargo could be moved without impacting adjacent railroad tracks. Wooden mats and temporary stools were also added to guarantee that roll-off was executed according to plan.
“Corner simulations and transport drawings required for creating civil works designs were made in 2D using AutoCAD. LIDAR scans were done prior to the start of the civil works, and later again prior to the first transport, to do a clash check in 3D with the transport configuration and biggest piece of cargo,” Beelen said.
Despite the site lying only a few kilometers away, deugro and its subcontractors were forced to carry out extensive civil works for this final stage, with modifications including several road widenings, the installation of foldable streetlamps, relocation of steam pipes and medium-voltage wires underground, and shutdown of local 110-kilovolt power lines.
With a clear plan in place, the team utilized the SPMTs to make the short trip to the plant construction site. During this move, temperatures hovered between –10°C and –17°C, meaning that considerable amounts of ice and snow had to be removed on a daily basis.
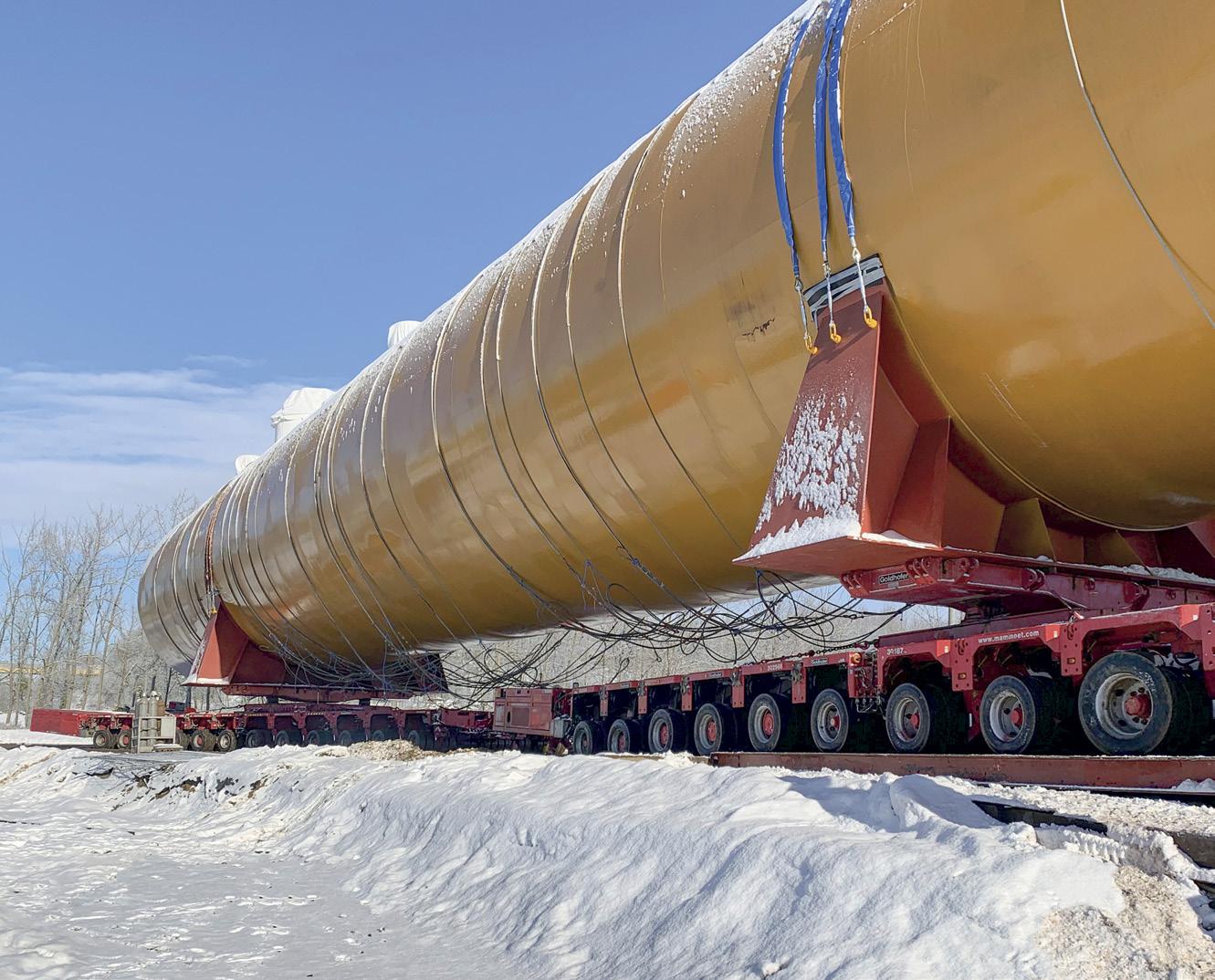
“Supervising such a complex and highly demanding transport during day and night with temperatures down to –17°C is a challenging task for everyone involved,” Sebastian Rostek, transport engineer for dteq, said. “Safety is our first priority in everything we do – especially under extreme conditions like during this project.” BB
To view a film of the project visit here: https://www.youtube.com/ watch?v=mADxMISW00Q
Based in the UK, Malcolm Ramsay has a background in business analysis and technology writing, with an emphasis on transportation and ports.
BY LORI MUSSER
Bomb cyclones, cyclone clusters and the “blizzard of the century” – North America faced the full wrath of Mother Nature in 2022.
The bomb cyclone that hit the U.S. West Coast in January 2023 floored power lines, brought flash floods and rock slides and toppled large trees. The North America winter storm in December 2022 left millions without power with warnings of temperatures as low as -70º Fahrenheit.
Upending normal life, even the best project contingency planning cannot overcome some extreme weather events.
Risk mitigation and supply chain resiliency are complex endeavors. They can be especially challenging for breakbulk or specialized dimensional cargoes that might be open to the elements when transported, have temperature-sensitive components, or be easily damaged by load shifts or rough handling caused by heavy weather. Being prepared and proactive, having actionable assets and teams at the ready, and responding rapidly are best practices. So is having a long-term climate-change approach to supply chain management in hand.
The United Nations is convinced global warming is upon us and exacerbates the weather emergencies that impact all industries. It predicts that climate change will cause US$2 trillion in losses by 2030 and that supply chains will suffer seriously.
WHAT’S COMING AND WHERE
To address weather challenges, supply chains must dust off their crystal balls. For cargo owners that need a transformer or some steel on a project site at a set time, it makes sense to mitigate for potential weather-related issues. Early delivery, last-minute rerouting or pulling inventory from an alternate yard or even supplier are possibilities, but simply choosing the optimal supply chain routing in the first place is always a good idea.
Regions:
We know that California is the wildfire capital of the U.S., with about 9,000 wildfires that burned more than 2 million acres in 2021 alone (25 percent of all acreage burned annually in the U.S.), according to the National Interagency Fire Center. Lightning is a big culprit, and NOAA reports that earlier, shorter, drier springs set the stage for intense fire seasons in the future. California fires can close roadways and rail routes.
And we know the Caribbean and Gulf of Mexico are hurricane hotbeds. According to Universal Property & Casualty Insurance company, Florida has been hit by more hurricanes than any other state (41 percent of the 292 hurricanes recorded since 1851). The second most hurricane-prone state is Texas. Hurricanes may come with high winds, torrential rain, flooding and modal closures.
In northern climates, extreme cold can also be particularly challenging. Last year, the China State Railway Group unveiled a bullet train that can operate at up to 350 kilometers per hour (217 mph) in temperatures as low as -40°C. Its innovative features reportedly include bolts made with a chromium-molybdenum alloy, temperature-resistant brake control devices, and stainless-steel pipes equipped with heating devices.
According to Canada’s CN Railway, a number of train components grow temperamental in extreme cold. The company’s new ‘2022-2023 Winter Plan: Meeting the Challenge’, outlines a comprehensive plan of attack on cold, and its video, The Tipping Point, shows that at temperatures of 25°C and below, the physical properties of steel are stressed, increasing the chance of defects and surface fractures, and train braking systems are subject to freezing which can lead to lost air brake pressure and result in longer air brake system charging/ recharging times. These are just a few of the significant safety issues that force train length reductions and reduced speeds.
Tech Tools For The Job
There are a plethora of technologies to help carriers and cargo owners re-route, wait it out, protect their shipments, and get back up and running quickly.
For the past three years, Wallenius Wilhelmsen has made significant investments in its IT and cloud infrastructure and has been working on installing sensors onboard vessels to obtain the data relevant for cutting back fuel consumption. These sensors monitor vital vessels’ operational parameters such as fuel consumption, shaft power, speed, electricity consumption and more.
“We can now harvest this data using cloud technology, then run it through a complex mathematic model which, with the help of AI technology like that from DeepSea, ultimately provides the vessel captain with detailed instructions regarding optimal route and vessel speed. These tools give instructions foreseeing sailing conditions with great precision when correlated with weather forecast prognosis updates. No human being, no matter how many years of experience they have, can compete with these automated sailing instructions. It reduces emissions, it reduces fuel consumption, and it increases safety during operation,” Geir Fagerheim, senior vice president of marine operations at Wallenius Wilhelmsen, said to Breakbulk.
Bill Kerrigan is chief commercial officer for industrial freight logistics specialist, RPM Freight Systems. He said RPM handles complex loads in every type of extreme weather.
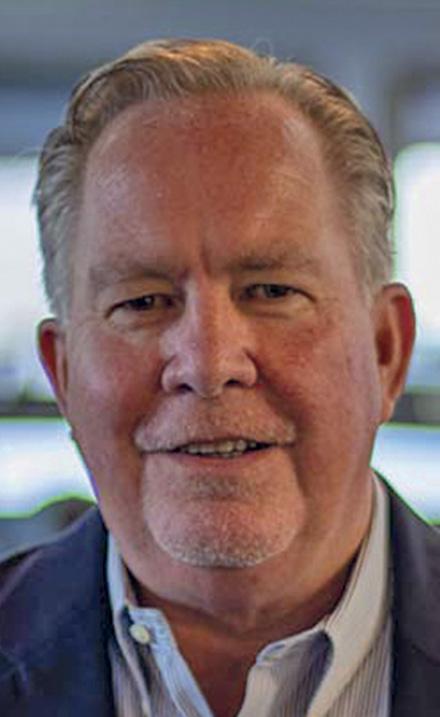