
33 minute read
THOUGHT LEADERS
Vaccinate Front-Line Transport Heroes
No Time for Half Measures
Rising from the ashes of 9/11, the U.S. pivoted to a new world order; an order where national security, critical infrastructure and resilience were redefined. At the forefront of what became a national policy conversation was the identification, prioritization and protection of critical infrastructure. As our nation approaches the 20th anniversary of 9/11, while at the same time combatting the Covid-19 pandemic, there remains a valuable lesson learned from 9/11, which is a relevant policy response to the Covid-19 challenges faced today by critical infrastructure front-line workers.
Critical workers such as first responders during 9/11 and the front-line workers that followed for cleanup were exposed at high levels to toxic fumes and dust. Thousands became ill with respiratory conditions and cancer linked to exposure to 9/11 environs. It took 18 years before there was an adequate national response in the form of the Victim Compensation Fund Reauthorization Act 2019. There remains a window of opportunity to use lessons learned from these front-line workers to equitably address our current front-line critical infrastructure workers.
Pertinent to current front-line critical infrastructure workers in the maritime transportation sector – including marine, trucking, rail, air, warehouse and logistics – is priority access to Covid-19 vaccines. These women and men are critical support for crucial supply chains and maintenance of critical infrastructure.
Capt. William “Bill” G. Schubert, former Administrator, U.S. Maritime Administration at the U.S. Department of Transportation, commented: “What we witnessed through the March-April 2020 timeframe was U.S. supply chains holding up under tremendous pressure and adjusting to a new normal, but if they had broken down our country would have faced the apocalypse.”
ESTABLISHING REAL PRIORITIES
While the U.S. Department of Homeland Security Cybersecurity and Infrastructure Security Agency affirms essential critical infrastructure workers have allocation to scarce resources to protect against Covid-19, the irony is they are not on the 1b priority list for vaccination in the U.S., and at the same time they are responsible for the logistics and distribution of the very vaccines that could protect them.
Lamentably, there has been no implementation of a national policy for vaccine prioritization, as individual states have the power to prioritize vaccine distribution. The very nature of the work environment in the marine transportation sector, such as working in close proximity to co-workers or members of the public, inability to perform work remotely, length of time workers are exposed to each other and/or the public, and the number of contacts they have during a typical workday, exacerbate the risk these workers face daily, as they work to maintain core societal functions.
Supply chain disruption is a national security issue. Minimizing the impact of workers in the maritime transportation sector contracting Covid-19 can be accomplished with priority access to vaccines. Implementation of this tactical risk mitigation strategy minimizes the impact of disruption and contributes to national security. Failure mode is no longer about a lack of toilet paper or bleach in the grocery store, it is about avoiding economic collapse of the system.
Securing long-term economic recovery at the global, national, regional and local scale requires the flow of goods and international trade to move efficiently and effectively. The collective voices of the overreaching maritime transportation sector must ring the bell in unison for allocation and distribution of the vaccine to these true front-line heroes. BB
Margaret A. Kidd is program director for the Supply Chain & Logistics Technology department’s bachelor’s and master’s degrees at the College of Technology, University of Houston. She is also leading the Chartered Institute of Logistics and Transport’s (UK) expansion to U.S. universities and colleges.
BY MARGARET A. KIDD, UNIVERSITY OF HOUSTON
This thought piece is part of a coordinated effort by the Exporters Competitive Maritime Council, or ECMC, to call for support of maritime essential workers during the pandemic. Marco Poisler, COO of UTC Overseas and past chairman of the ECMC, recently wrote a letter to the U.S. Centers for Disease Control. “ECMC Calls for Support of Essential Workers,” was published Jan. 25 on breakbulk.com: https://www.breakbulk.com/Articles/ ecmc-calls-for-support-of-essentialworkers
PORT PROFILE
MAKING LASTING CONNECTIONS Post-Covid Plans to Strengthen Rotterdam

BY MALCOLM RAMSAY
As the global drive towards sustainability steps up in the wake of the Covid-19 pandemic the Port of Rotterdam, one of the largest breakbulk hubs in Europe, is preparing to move full steam ahead with new development as it navigates the changing demands for breakbulk handling in 2021.
Under the ports’ Bigger. Better. Breakbulk. campaign the port plans a number of initiatives to consolidate and extend its breakbulk capabilities. Central to this is its work with partners to improve integration and handling capacity.
Twan Romeijn, business manager for breakbulk and offshore industry at the port, explained: “Bigger. Better. Breakbulk. is about maintaining a diverse portfolio and realizing a stable and future-proof market environment. We are focused on developing the connection to the existing maritime and offshore cluster and ensuring highquality service companies are present in close proximity, from floating cranes and lashing companies to heavy-lift specialists and transport companies connecting Rotterdam worldwide.”
With the port still partially restricted due to lockdown, Romeijn noted that there has been a negative impact across automotive, machinery, construction and steel shipments in 2020. But there have also been some silver linings with non-ferrous metals showing positive throughput in 2020 and forest products increasing slightly due to the demand for products related to hygiene such as protective gear/toilet paper.
“If the infection rate slows down and the vaccine programs are at full speed, we expect an economic recovery this year, with a positive impact on port throughput. There remain uncertainties, like possible longer lockdowns and slow vaccination rates, but in the second half of 2021 we should see a strong economic recovery and from 2022 onwards we expect to be back on the original growth path for the period 2020-2025.”
CHANGING DEMAND
With hopes that lockdowns will ease in the second quarter, the port is focused on more than a return to “business as usual,” however as it works with partners to develop the infrastructure to meet a changing market.
“I believe ‘circularity’ is not just a trending topic. The offshore wind business together with the coronavirus crisis have a tremendous effect and influence in the way people and politics are thinking,” said Bart-Luc Olde Hanter of Rhenus Logistics B.V., part of the port logistics division of the
Top: Rotterdam hopes to see a strong economic recovery in the second half of the year. CREDIT: PORT OF ROTTERDAM

– Peter Herkemij, Spliethoff
German worldwide operating logistics service provider Rhenus Logistics.
“If the economic model can change in a way that only fully sustainable products are used for clean energy the whole planet benefits. These new developments will contribute to the further hybridization and integration of offshore and breakbulk business. I don’t see anything bad in making money while making the world a better and cleaner place to live,” he added.
Rhenus has a long history in Rotterdam and operates the breakbulk and heavy-lift terminal Rhenus Deep Sea Terminal at Maasvlakte with 800 meters of deep draft quay at the entrance of the port as well as the Rhenus Waalhaven Terminal close to the city center.
ENERGY TRANSITION
Already recognized as one of the leading breakbulk clusters in Europe, the port authority plans to make additional space available for breakbulk-related services in 2021 through a range of innovative new approaches.
An example of this is the breakbulk ‘carrousel’ initiative, which involves shifting storage areas between multiple terminal operators to create economies of scale. Launched at the port’s Waalhaven site, it involves an additional 12 hectares of industrial site and 1,155 meters of quay and is designed not only to provide an additional growth incentive for the sector, but also to improve sustainability of operations.
With the drive towards sustainability to be a defining theme across industries in 2021, Rotterdam aims to
Spliethoff’s heavy-lift vessel Damgracht. CREDIT: SPLIETHOFF
be at the forefront of the energy transition as it sees demand from on- and offshore wind energy rocket.
Another longstanding breakbulk firm operating at Rotterdam is Spliethoff. Peter Herkemij, deputy director at the firm, reinforced the importance of environmental impacts across all operations and Rotterdam’s ability to offer “availability and flexibility.”
“First of all our focus is on minimizing our environmental footprint,” Herkemij explained. “Our secondary challenge is to find and keep flexible stevedores and terminals, able to overcome challenges, preferable in a healthy competitive playing field … We believe we can add value by being an efficient and reliable partner … and we highly appreciate the fast and short lines and way of working at Rotterdam – a general good feeling.”
A core part of the Bigger. Better. Breakbulk initiative, sustainability means more than the replacement of polluting fuels or a drive to energy efficiency as the port seeks to build greater resilience for the future by offering supply chain integration and flexibility.
“The normal saying ‘check before fixing’ is not applicable to Rotterdam, since one can almost assume no difficulties in draft, congestion, strikes, etc. and port calls are usually uneventful,” Herkemij added.
This outlook is echoed by Rhenus’ Hanter: “Rotterdam is a complete port. Most other ports are container ports or bulk ports. Rotterdam has it all. A huge network of services both up and downstream to enable and speed up the energy transition.”
MARKET SIZE SHIFT
With the increasing commoditization of breakbulk logistics the landscape has changed rapidly for fleet owners, with demand for bigger capacity vessels becoming prevalent and the need for infrastructure to support ever-larger loads now essential for ports.
“Where once you had two ship cranes of 100 tonnes, you were a specialized heavy-lift shipping company. Nowadays it’s normal to have a coastersized vessel with two 250-tonne cranes on board. Breakbulk has become bigger, and this means investments in bigger terminals, heavier cranes and specialized project managers have become a necessity for a breakbulk stevedore.” Hanter noted.
To meet this demand the port is planning a range of investments in new equipment, such as cranes and roll-on, roll-off facilities, as well as extensive plans to upgrade quay sides and supporting infrastructure.
“We are also making investments in sustainability, with plans to deploy new shore power connections, introduce new solar panels on warehouses, and increase the usage of greener fuels.” Romeijn added.
“The breakbulk business is ‘live and let live’ and needs flexibility. That’s why we work via the cafeteria model, where you can pick what service you want or need from us,” Hanter said. “This can result in having a handymax vessel alongside bringing thousands of tonnes of aluminum or steel and at the same time at the same quay having a specialized offshore heavy-lift vessel preparing and assisting with one lift of 5,000 tonnes. But at the end it’s all about the
right price for the right service with equipment and a multidisciplined and flexible workforce.”
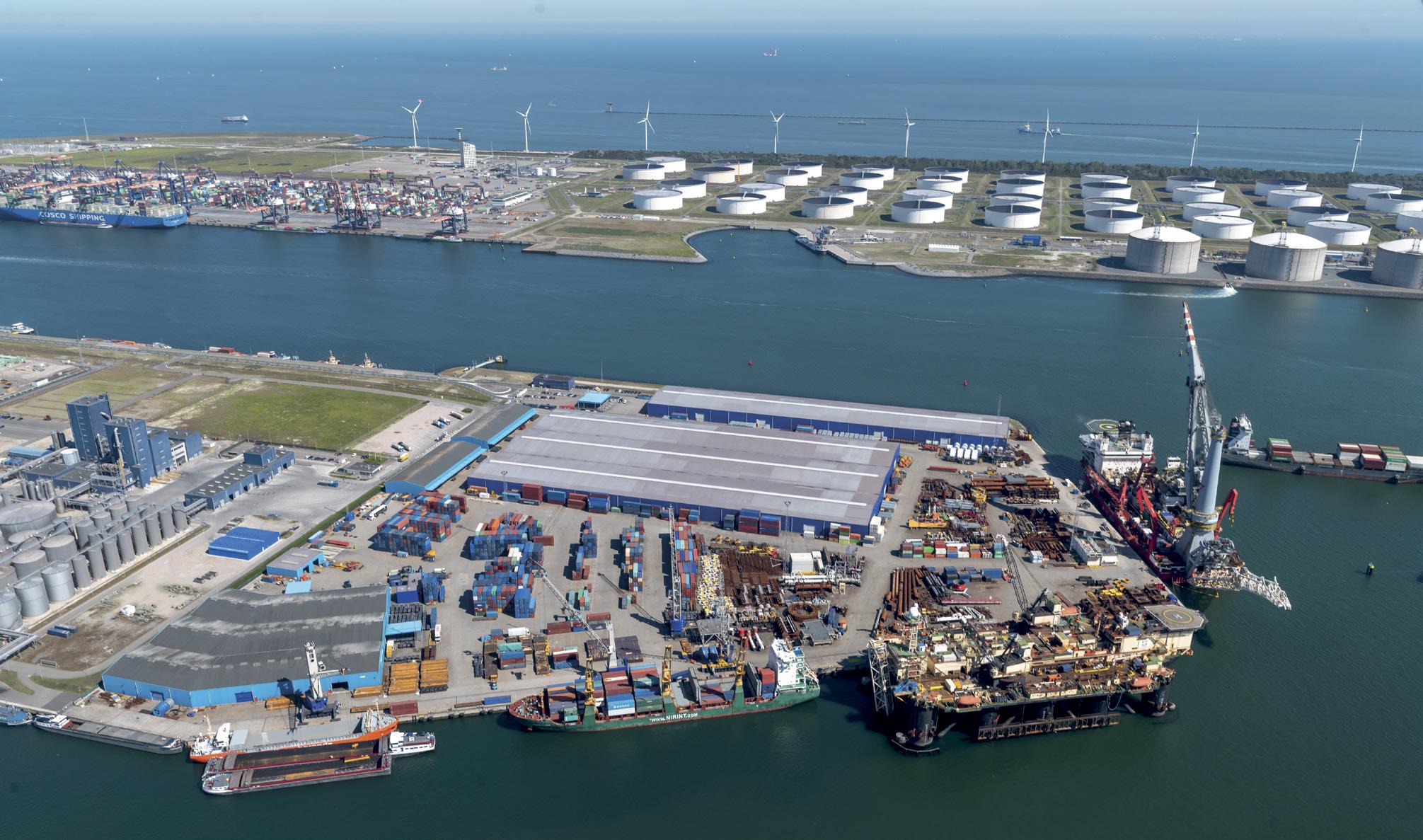
INVESTMENT IN THE FUTURE
To ensure this flexibility going forward, Rhenus plans investment in a range of new equipment that will meet not only the demand for larger capacity, but also sustainability goals of clients. This includes plans for electric terminal vehicles to reduce emissions, and the introduction of roll-stop systems of recycled plastics replacing wood for storing steel coils at its terminals at Rotterdam.
“At the terminal we follow the principle of reduce, re-use, recycle, meaning to lower our footprint wherever we can. It’s all about minimizing the amount of waste we produce, dunnage we receive and remembering to recycle any materials that can be used for a new purpose,” Hanter said.
In 2020, the firm invested in the first Dutch full electric Kone Gottwald mobile harbor crane, and this year plans to expand the operational range of the crane on the terminal, investing in a new power grid for electricity supply.
“Also part of the further electrification of our terminal is the solar panel project to have our warehouse roofs full of solar panels. In total 36,000 panels will be installed generating more than 10 megawatts. We are also further developing our offshore services, as the terminal is ideally located to the entrance of the port at the North Sea and thus perfect for supply runs and campaigning.”
New lifting capacity is also on the horizon for another operator at the port, RHB, which sees benefits from greater flexibility.
“We recently invested in another Liebherr heavy-lift crane, making our daily operations even more flexible and efficient. Furthermore the use of these two Liebherr giants gives us the ability to lift even bigger and heavier units then before. Besides these cranes we make use of eight high-speed multipurpose cranes ensuring a smooth and quick operation,” said Mike van der Pluijm, director of RHB.
CONNECTIVITY AND DIGITALITY
Alongside the port’s internal development, another key factor for future growth is the links it maintains with other breakbulk hubs around the world.
“The port of Rotterdam has great connections to the rest of Europe and the world. Due to our unique geographical location, the port is easily reachable, no locks or any other obstacles, very well organized and is able to provide with all services which may be needed,” van der Pluijm said.
Romeijn explained that a key task going forward is to “keep in contact with other breakbulk clusters, whether terminals, cargo owners, shipping lines, forwarders or agencies, to know what is happening in the market and how Port of Rotterdam can be of help.”
To achieve this, a key element of the port’s roadmap for development includes the rollout of new digital solutions that ensure the port remains at the center of global breakbulk trade flows.
“With the changing of the guard in the U.S., there is hope that the Biden government might have a different view on trade restrictions, which could be good news for steel trade. Also, as global container freight rates have spiked for various reasons this could additionally benefit breakbulk cargoes.” Romeijn noted. BB
The Port of Rotterdam operates via the cafeteria model, where customers can pick the service they need.
CREDIT: PORT OF ROTTERDAM
Based in the UK, Malcolm Ramsay has a background in business analysis and technology writing, with an emphasis on transportation and ports.
BY MALCOLM RAMSAY

CUTTING EDGE OF INNOVATION
Rotterdam Hub Pioneers Breakbulk Evolution
Located at the heart of Rotterdam, the Innovation Dock building is exploring some of the latest trends in breakbulk, driven by the concept of cross-sectoral collaboration.
The Innovation Dock at RDM Rotterdam has been developed by the Port of Rotterdam, and the unique building features more than 7,500 square meters of space, dedicated to supporting start-ups and research and development departments of established multinationals. RDM Rotterdam operates alongside its sister initiative M4H, and together they are part of the Rotterdam Makers District, the best spot in the region for the innovative manufacturing industry.
“RDM and especially the Innovation Dock is about innovation and using new technologies. Our focus is on manufacturing companies that facilitate the energy transition, for example hydrogen and offshore wind,” Jouke Goslinga, program director at RDM Rotterdam, told Breakbulk.
Previously the site of a shipyard, the building has seen extensive renovation in recent years with Dutch architecture practice Groosman Partners adding a suspended office environment with an additional 1,000 square meters of office space to support a new generation of innovation.
“We want to attract entrepreneurs who make the real difference in supporting these trends with technologies like electrification, robotics, AI/ digitalization, IoT etc.,” Patricia van Bergeijk, communications advisor for RDM Rotterdam, noted, highlighting hydrogen, offshore wind, smart logistics and waste-to-value as major trends under investigation by participants that are directly impacting breakbulk operations.
High-profile companies such as Ampelmann, Studio RAP and Concr3de are existing members and as lockdowns ease this year, RDM is eyeing renewed growth, with new members bringing a range of skills and expertise.
The buildings original roof trusses give clearance of 20 meters height, allowing companies to explore not only the latest digital solutions and software development, but also providing adequate space for high tech prototyping and test facilities.
DISTRO PLATFORM
A clear example of the benefits the hub can bring was demonstrated with the successful rollout of the Distro new energy platform. Bringing together 32 companies at the RDM site this platform works with solar panels and battery storage to allow users to trade energy between themselves in a local market.
“Next month we will launch Distro permanently,” van Bergeijk noted, indicating the speed of development possible at the site due to the collective approach of members and the rapid turnaround from idea to reality.
Developed by S&P Global Platts and Blocklab, a subsidiary of the Port of Rotterdam Authority, the new platform not only demonstrates a new model of collaboration, but also highlights the important role that sustainability plays for the sector.
“This is the first time in the world that blockchain technology, artificial intelligence and high-frequency commodity trading have been combined in a single platform,” the company said.
The collaborative spirit extends beyond the energy that users of the site share, with RDM organizing regular events, and while these have been understandably limited due to the Covid-19 pandemic, the schedule is already looking busier for 2021.
“Every year we organize the Future Flux Festival. We invite all entrepreneurs and education institutions in the Innovation Dock, RDM and M4H to showcase their innovations during this festival,” van Bergeijk explained, adding that the aim is for the festival to be held in the first week of July, pandemic restrictions permitting. BB
The hydrodynamic laboratory Aqua Lab is used for technical training and can be utilized for research purposes.
CREDIT: ROYBORGHOUTS FOTOGRAFIE
Based in the UK, Malcolm Ramsay has a background in business analysis and technology writing, with an emphasis on transportation and ports.
REGIONAL REVIEW
STEP CHANGE IN SAUDI

‘Project HQ’ Confirms Saudi Arabia’s Ambitions
BY SIMON WEST
Although it is too early to understand the impact of Saudi Arabia’s “Project HQ” on markets and companies, the new policy will not have gone unnoticed by international project logistics providers.
The Saudi government said in midFebruary that from 2024, it would no longer work with foreign companies whose Middle East headquarters were located in any other country in the region.
State news bureau SPA said the measure applied to government-owned agencies, institutions and funds, and was designed to encourage contractors to set up base in the Kingdom to create jobs for nationals and boost the local economy. Foreign firms opting not to relocate could still do business with the private sector, SPA said, adding that detailed regulations would be issued later this year.
“The decision … will reflect positively in terms of creating thousands of jobs for citizens, transferring expertise and localizing knowledge, as well as contributing to the development of local content and attracting further investment to the Kingdom,” Saudi Minister of Investment Khalid al-Falih said on Twitter.
Middle East-based project industry executives contacted by Breakbulk were reluctant to comment on the policy so soon after it had been announced. The measure though is likely to be seen as a ploy to gain a whip hand over its neighbor and ally the United Arab Emirates, the main logistics hub in the Gulf Cooperation Council, or GCC, and preferred regional base for dozens of international freight forwarders.
FALSE DAWN?
Amid a pandemic-induced recession, Saudi Arabia’s ambition is to lure the foreign talent and money it needs to achieve the aims of Vision 2030, a sweeping nationwide project unveiled by Crown Prince Mohammed bin Salman in 2016 to pivot the economy away from oil towards more sustainable, private sector-driven industries.
However, Ryan Bohl, Stratfor analyst for risk intelligence company RANE, said Saudi’s latest tactic could fall short of its intended goal. “It is not likely that we will see a rush of contractors or companies going over to Saudi Arabia, though we will likely see companies setting up new ‘regional HQs’ in the future in the Kingdom if that makes them more competitive for Saudi contracts, even if the bulk of their operations remain in the UAE.
Top: Kumar Ganesan of GAC said Saudi Arabia’s ambition of leapfrogging Dubai as the Middle East’s main logsitics hub was “quite realistic.”
CREDIT: GAC
“We will also probably see carve outs for this policy, with some companies able to get exemptions as the policy evolves and it becomes clear that Saudi Arabia will not be able to strong arm companies into relocation. Overall, this policy by itself is not likely to substantially make Saudi Arabia more attractive to companies than the UAE and Qatar, but it could signal a willingness by the country to get more aggressive in its economic competition with these other Gulf states.”
The new policy comes at a time when Saudi industrial activity is on the rise, enticing project logistics with a steady stream of new cargo-carrying opportunities. The government’s Vision 2030 industrial development and logistics program, charged with boosting the GDP contribution of mining, logistics, industry and energy, aims to attract investments worth 1.6 trillion riyals (US$427 billion) by 2030, creating an additional 1.6 million jobs along the way.
Renewable energy is one sector poised for growth, with the government targeting 27.3 gigawatts, or GW, of clean capacity by 2024 and 58.7 GW by 2030, of which 40 GW is expected to come from photovoltaic and solar plants, 2.6 GW from concentrated solar power, 16 GW from wind turbines and the remainder from other renewable sources.
By that time, half of the country’s power generation will come from renewables, with the other half derived from natural gas, according to government projections.
So-called smart cities such as Neom on the Red Sea coast are also sources of new work for service providers. A half-trillion dollars will be spent to build towns, ports, enterprise zones, sports stadiums and tourist destinations from scratch. Completion of the clean energy-powered metropolis is slated for 2025.
According to project tracking platform MEED, project awards in Saudi Arabia over the next five to 15 years are forecast to reach US$1.2 trillion, versus US$700 billion in the UAE and US$100 billion to US$200 billion each in Kuwait, Qatar and Oman.
Kumar Ganesan

GAC
Peter K. Mathew
Fleet Line Shipping
REALISTIC AMBITIONS
Kumar Ganesan, managing director of GAC Saudi Arabia, said Saudi Arabia’s ambition of leapfrogging Dubai as the main logistics hub in the Middle East was “quite realistic.”
“Saudi Arabia is the largest logistics market in the GCC with a consistent growth rate of 5 percent every year. Its proximity to three continents and access to various trade routes give it a huge advantage. Like many countries, Saudi Arabia has experienced a slowdown due to Covid. But the country is in good stead to achieve its objectives and is headed in the right direction.”
Despite its size and dominance in regional hydrocarbon production – crude oil remains the bedrock of its economy, contributing about two-thirds of government revenue – the country still lags behind many of its neighbors when it comes to cargo sourcing.
Peter K. Mathew, founder and managing director of Fleet Line Shipping, a Dubai-based project cargo handler that regularly ships to Saudi Arabia, said the Kingdom’s oil and gas industry still relies heavily on imported machinery and components, much of which is routed or controlled in Dubai.
“Saudi Arabia is yet to have heavy engineering and industrial fabrication companies like we have in the UAE,” Mathew said. “As part of the Kingdom’s 2030 vision, we could expect such industries in the near future, but it will take some time for them to catch up to the UAE in terms of manufacturing and infrastructure capabilities.”
Once that happens, the supply chain’s center of gravity could start
Bertling Logistics and Bahri have a venture to provide end-to-end logistics services throughout the Middle East. CREDIT: BERTLING
The Saudi government is driving private-sector growth by cutting red tape. CREDIT: GAC

edging towards Saudi. “We could see many logistics companies, especially asset owners such as transport and crane companies, increasing their presence in Saudi,” Mathew said.
Operators are already sensing opportunity: the Ministry of Investment claims the number of foreign transport and logistics companies setting up business in the Kingdom rose by 47 percent in 2019.
CHANGE OF MODEL
As heavy-duty manufacturing gains more momentum, it will rely less on imports from other states in the GCC, driving companies in the region to adapt their business models. “We have definitely witnessed a shift, with an increasing number of firms opting to migrate their fabrication to Saudi,” said Colin Hindley, CEO of Agility Iraq.
“This has been prompted by developments in infrastructure and manufacturing capabilities in the Kingdom, enabling companies to reduce their costs by manufacturing in Saudi Arabia, and at the same time utilize strong logistics infrastructure and trade agreements with the GCC and other countries, North Africa for example, to export the material fabricated and make it cost effective.”
While some global operators choose to build up offices and representatives in Saudi Arabia, others, such as Bertling Logistics, see joint ventures as a valuable way to keep in with the growing market.
The Hamburg-based project cargo specialist announced in January it had teamed up with Saudi transport and trucking company Al Khaldi to provide logistics services to customers in the Kingdom. Al Khaldi-Bertling Logistics, headquartered in the eastern city of Al-Khobar, began operations on Feb. 1.
The joint venture’s Operations Director Adel El Said told Breakbulk the venture would focus on newly awarded and prospect projects in the oil and gas sector, including refinery and drilling rig moves inbound and outbound, desalination plants and non-oil and gas related energy industries such as solar and wind power.
“Bertling has been active in Saudi since the early 1990s, and has always handled transport to and from the Kingdom. Due to the manifold new business opportunities arising in Saudi following the Vision 2030 program, we decided to enter the market again with our own local office, but together with a strong local partner at our side,” he said.
SETTING A TREND
Al Khaldi-Bertling Logistics follows other recent joint venture agreements, including Bollore Logistics’ Riyadh-based venture with Saudi transport firm Bahri to provide endto-end logistics services throughout the Middle East, and Panalpina’s partnership with Al Rushaid.
According to Agility Iraq’s Hindley, the Saudi government is taking “positive steps” in improving the ease of doing business in the country, making it increasingly attractive for logistics companies to set up operations.
Ganesan at GAC also pointed to a more business-friendly environment, claiming the government was driving private-sector growth by cutting red tape through its digitalization plans and simplifying administrative processes.
A Ministry of Investment brochure that tied in with the Project HQ announcement, quoted by news agency Reuters, laid out additional perks for companies that move their headquarters to Saudi Arabia, including zero corporate tax for 50 years, potential favoring for government contracts and a 10-year waiver on mandatory quotas to employ nationals. As it stands, the country’s Nitaqat system gauges the number of Saudi employees in a firm’s workforce against the number of non-nationals, leading to strict hiring policies that can create headaches for service providers.
“The winds of change are blowing rapidly in Saudi Arabia,” Ganesan said. BB
Colombia-based Simon West is a freelance journalist specializing in energy and biofuels news and market movements in the Americas.
An End to Escort Anomalies
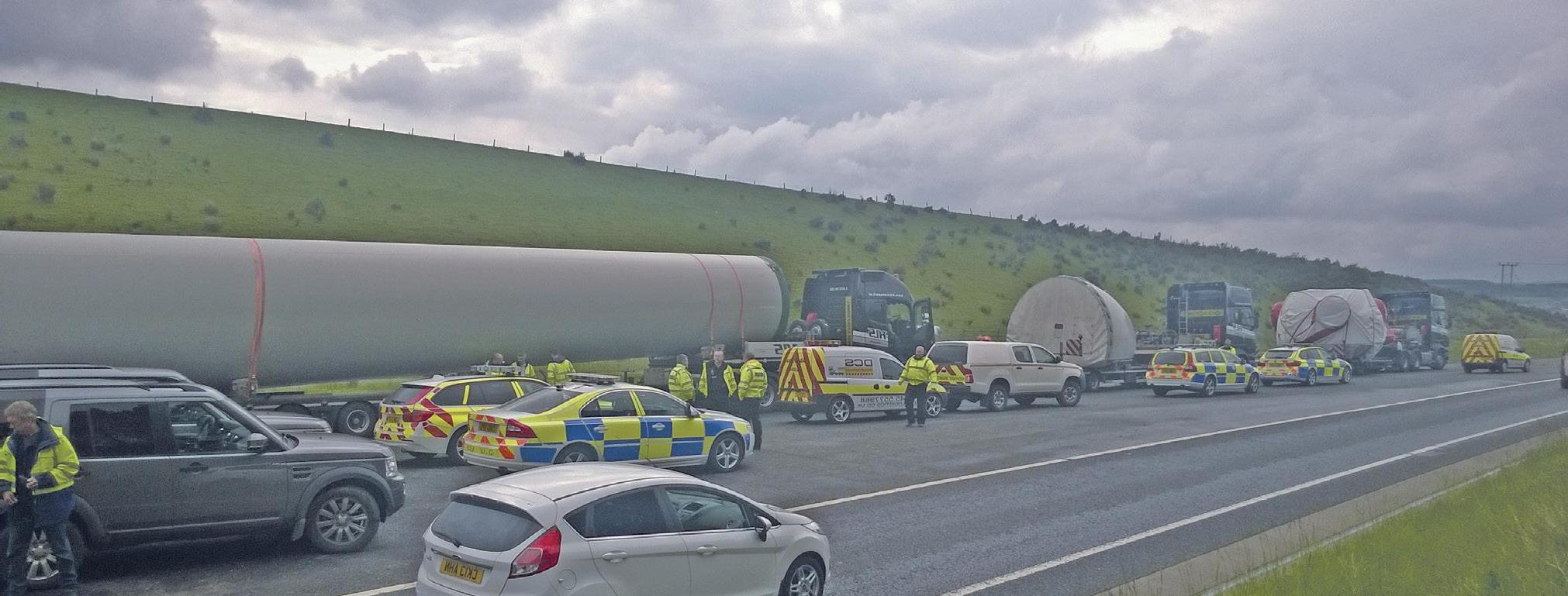
UK Works to Formalize Requirements
Many hundreds, indeed, possibly even thousands of abnormal loads move through the UK road network daily. Some you might notice – lots of flashing amber lights, some with accompanying escort vehicles to aid the protection of other motorists. But others you may not notice. They either do not “fulfill” the requirement to be escorted, or they move in the early hours when traffic levels are generally lower.
Whether noticed or not, they are here to stay and play a vital part in the UK economy supporting investment projects – from new roads to wind farms to nuclear power stations – and will play a major part in the UK government’s recent announcements to “build, build, build.”
For the most part the requirement of abnormal loads to be escorted has little legislative foundation in the UK. Pre-2004 this role was provided by the police in the interest of public safety and was very ad hoc, dependent on which police area you were operating in. Many times as an abnormal load driver I recall “waiting at” to be “taken over” by a neighboring force when crossing the county line.
Since 2004, abnormal loads escorting is no longer considered to be a core police duty. From that point on, it became standard practice for the majority of moves to be undertaken solely by private operators, and for police assistance only to be utilized where loads were exceptionally abnormal and would require the need for direct police control for stop and direct assistance, for example. For this service, police forces levy a specific charge; however they can only do so for loads moved under a permissive system if the escort is requested.
Interestingly, there is no requirement for a private escorting operator to undergo any training in the UK. There is a code of practice, but this is a voluntary scheme. Of course, there are many safe and “fully trained” operators out there, most (if not all) members of the UK’s Heavy Transport Association, or HTA. However, under current legislation it would be permitted for anyone to put a flashing amber beacon on top of their vehicle and escort an abnormal load weighing more than 100 tonnes.
NO COMPROMISE ON SAFETY
We at the HTA believe that no compromise should be made in relation to safety, and that this area of operational importance should be, at the very least, pulled into a formal set of parameters that operators must sign up to. This would include formally recognized training to ensure that a minimum safety standard is obtained and maintained.
The HTA’s project SAbLE – “Safer Abnormal Load Escorting” – is a step towards safer national standards. The aim is to analyze good practice from the UK and elsewhere in the world to ensure that movement of these loads is performed as safely and efficiently as possible. The project, led by international road safety consultancy The Transafe Network, will examine current practices in risk assessment and escorting of abnormal loads, and identify future practices, which have the potential to enhance the safety and efficiency of these moves. This will include practices to improve safety for all road users, and the most efficient use of the road network.
The project aims to bring together a full range of stakeholders including abnormal load haulers, route surveyors, permit agents, consultants, abnormal load escorts, infrastructure owners and managers, equipment manufacturers and the police. It will examine practices in risk assessment and escorting of abnormal loads and identify future practices which have the potential to enhance the safety and efficiency of these movements.
By supporting this project, the industry can be confident in its support of the infrastructure in our growing economy, and is especially poignant given the current situation that the country, and indeed the world, finds itself within the Covid-19 pandemic. BB
Marcus Gough is chair of the UK’s Heavy Transport Association and head of transport for Ainscough Crane Hire Ltd.
BY MARCUS GOUGH, HTA & AINSCOUGH CRANE HIRE
RULES & REGULATIONS
BY PAUL SCOTT ABBOTT
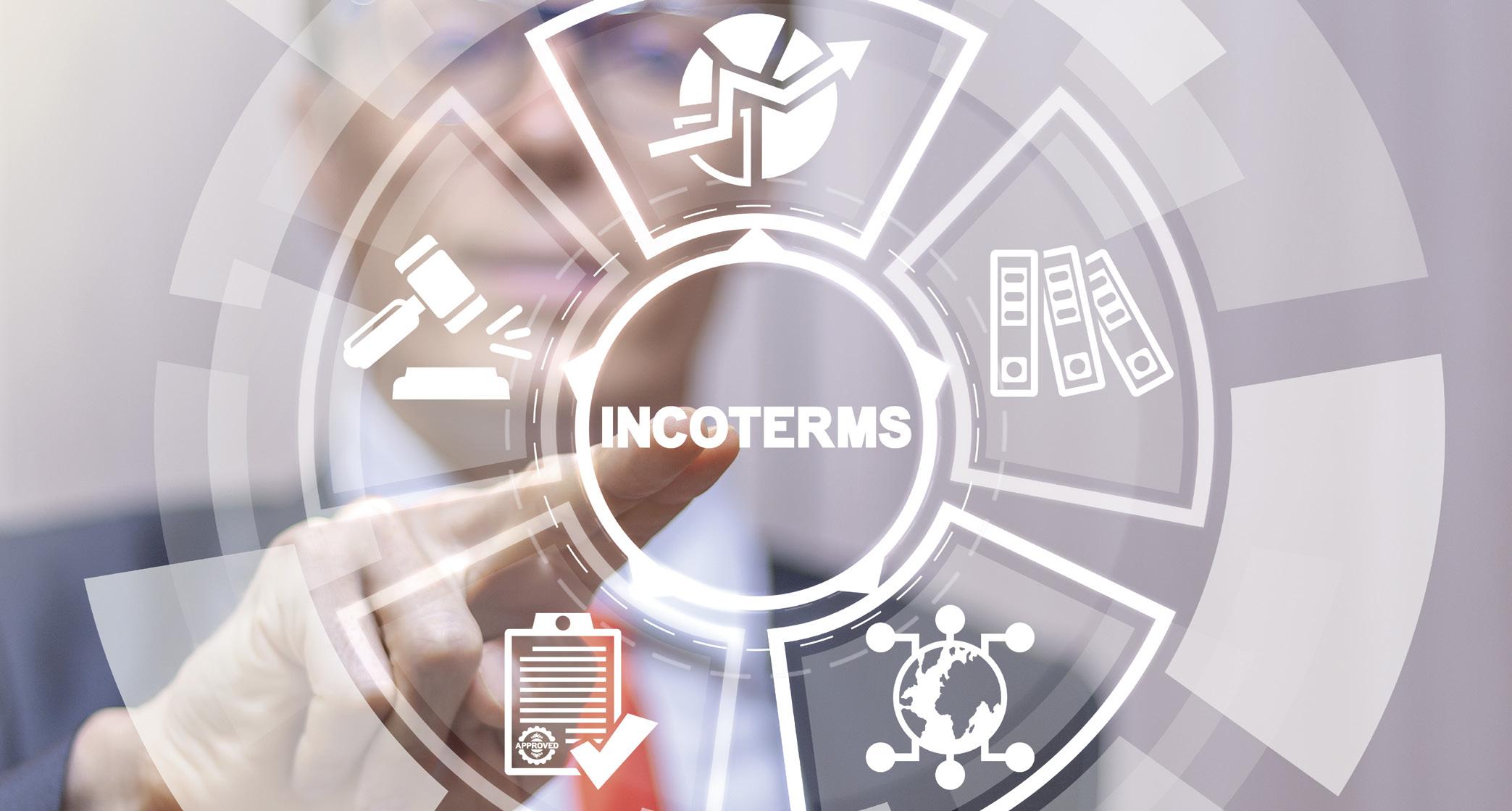
PLAYING BY NEW RULES
Incoterms 2020 Seeks to Clarify ABCs of Transport Contracts
FOB. FAS. CFR. CIF. EXW. FCA. CPT. CIP. DAP. DPU. DDP.
These 11 three-letter acronyms can spell commercial success – or misfortune – for those engaged in transport of breakbulk, project and other cargoes.
And the latest iteration of the rules they set out – Incoterms 2020 – aims to make them easier to understand and properly applied in contracts that define responsibilities, costs and risks for sellers and buyers in international and domestic trading agreements.
Through better application of these acronyms, the likelihood of costly disputes can be significantly reduced, according to four global experts on Incoterms sharing thoughts with Breakbulk.
“The legacy of Incoterms 2020 will be getting people to read and use the rules correctly,” said Emily O’Connor, director of trade and investment for the International Chamber of Commerce, or ICC, the 102-year-old, Paris-based world business organization that develops, reviews every 10 years, provides certified training on, and holds the registered trademark for Incoterms (short for International Commercial Terms).
CLEARER IS BETTER
David Lowe, partner and head of international commerce at Londonbased multinational law firm Gowling WLG, who co-chaired the expert drafting committee for Incoterms 2020 after being a member of the Incoterms 2010 committee, said he believes the expanded yet simplified explanation of the terms in the new 194-page Incoterms 2020 book is definitely a positive step.
“The good news,” Lowe said, “is that the changes do not change the fundamentals – all Incoterms have been kept and just one has had its name changed. The real change is in the detailed drafting of the Incoterms to make them clearer.”
Murray Cooper, director of corporate governance in the Singapore office of Netherlands-headquartered LV Shipping & Transport Group, who has been applying Incoterms for four decades, said he is impressed with the revised edition.
“It is clearer and easier to understand,” Cooper said of Incoterms 2020 in comparison with its 2010 predecessor. “It more clearly articulates what each term is.”
Vilasini Krishnan, senior consultant with UK-based 4D Supply Chain Consulting, a project logistics consultancy that features Incoterms training in its portfolio, emphasized the importance of intelligibility while adding a cautionary note.
“Overall,” Krishnan said, “the latest revision does provide more clarity, which is easier to understand and use, hence reducing the risk of misusing Incoterms. This is important because misuse of Incoterms could expose companies to huge commercial and operational liabilities.
“An unsuitable Incoterm could mean seller/buyer obligations, risks and costs are not clearly defined, leaving them open to significant cost impacts, potential delays and damages and associated risks – not to mention the damage to the trust and relationship between seller, buyer and other parties in the supply chain,” she said. “Resulting lawsuits and legal interference are often time-consuming and impose financial burden.”
MISUSE ‘FRIGHTENING’
Although Incoterms have been around since 1936, their misapplication, particularly by non-lawyers, including sellers and buyers with relatively small companies, remains a significant concern.
“Incoterms are often used without people really knowing what they
mean,” said the ICC’s O’Connor, whose work has focused on Incoterms for the past decade and a half. “The mismatch between the frequency with which they are used and the lack of understanding is frightening. People feel real pain when they don’t really understand the rule they chose.”
O’Connor’s advice is thus quite straightforward: “Users, make sure you understand what the rule says. Pick the right rule. It is really important. You are signing a contract that could have painful monetary consequences if you don’t understand what your Incoterms rule means.”
According to 4D’s Krishnan, the process should include treating every new sales contract as a singular case and revisiting (and revising if appropriate) existing contracts to ensure they take into consideration the latest Incoterms changes.
“We often see that businesses tend to use the same Incoterms for all sales contracts without considering the country of origin and destination, customs clearance requirements at both ends, risks associated with different modes of transport, seller/buyer capacity and capabilities, and so on,” she said. “This ‘if it’s not broken, don’t fix it’ mentality is a concerning complacency, as what worked for a particular country of origin and destination might not necessarily work for a different country pairing for the same buyer and seller.”
DOUBLE-CHECKING URGED
Attorney Lowe, the Incoterms 2020 committee co-chair, said such a “this is how we’ve always done it” mindset invites problems.
“Do not use an Incoterm without checking and reading it to make sure it’s appropriate,” Lowe warned. “Too many people use a particular Incoterm because they always have and have not checked that it’s right.
“This is crucial: Most Incoterms issues arise from people using the wrong Incoterm or not reading and understanding the Incoterm,” he added. “Increasing the chance that a user actually reads the Incoterm will improve usage.” at Terminal) rule to now be called DPU (Delivered at Place Unloaded), thereby allowing for deliveries at construction sites and in other instances where no true terminal is involved as risk passes from seller to buyer. • Adjustments to levels of insurance coverage required under CIF (Cost, Insurance and Freight) and CIP (Carriage and Insurance Paid to), the two rules that impose insurance requirements. • Updates to the FCA (Free Carrier) rule regarding onboard bills of lading, potentially resolving misuse of FOB (Free on Board), which should not normally be used for container shipments. • Detailing of security requirements for each Incoterm, further enhancing such guidance introduced in the 2010 edition. • Clearer allocation of costs between sellers and buyers, with each Incoterm accordingly redrafted.
Even with these changes and overall clarifications, ambiguities will inevitably remain, according to LV Shipping’s Cooper.
“Incoterms 2020 is a lot better and clearer,” he said, “but it is terribly difficult to cover every possible circumstance.”
The process to develop the next update, presumably Incoterms 2030, will soon be under way, once again gathering insights from those who use the rules in their day-to-day conduct of business, as was the case with the ICC’s five-year undertaking to produce Incoterms 2020.
Cooper said he is hopeful the next effort will deploy a digital approach in reaching out to industry leaders via LinkedIn and other online platforms, engaging an even broader range of professionals from various disciplines, “now that the technology is here to do so.”
The ICC’s O’Connor said the objective for Incoterms going forward should, in fact, be quite simple: “Next time,” she said, “we look to make them even clearer and easy to use.” BB
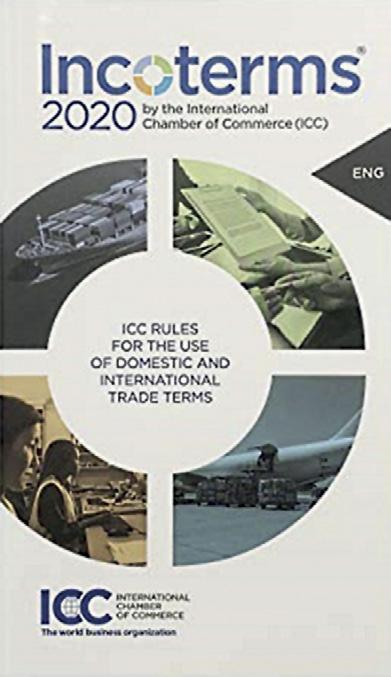
For a breakdown of Breakbulk 2020 terms, go to: https://www.breakbulk.com/Articles/ incoterms-trade-guidance-offered-in-11-rules
Encouraging readability and comprehension was behind the 2020 rewrite, which, for example, includes a matrix tool for comparing rules, greater use of pictures and explanatory notes, and an expanded yet easier-to-grasp introduction. Throughout, Lowe said, the new book is written in “plainer English.”
This, according to LV Shipping’s Cooper, is especially important for those who are not lawyers and, particularly in small and midsize enterprises, or SMEs, those who count contracts among myriad duties.
“The companies I worry about are the SMEs, which may well be without contract specialization,” Cooper said. “They may not even have an Incoterms book.”
Another continuing concern expressed by Cooper relates to conflation, mostly on the part of those in the U.S., of Incoterms and acronyms of the U.S. Uniform Commercial Code, or UCC. His recommendation is that Incoterms, not UCC terms, be used in all international contracts.
CHANGES ‘MORE SUBTLE’
As for the latest changes themselves, the ICC’s O’Connor described them as “slightly more subtle” than those made in Incoterms 2010, which, among other things, reduced the actual number of acronymous terms to 11 from the 13 used in Incoterms 2000.
The most notable alterations made in Incoterms 2020, the experts agree, include: • Renaming of the DAT (Delivered A professional journalist for nearly 50 years, U.S.-based Paul Scott Abbott has focused on transportation topics since the late 1980s.