
11 minute read
MARKET REPORT
Market Report: Transformer Market and Component Developments
By Saqib Saeed and Hassan Zaheer, Power Technology Research
Clean energy is a key pillar to achieve a low-carbon future for many governments around the world. CWIEME Transformer Day, held June 22, provided updates on innovative components and transformer solutions, exclusive insights on transformer and energy market developments and expert discussions on renewable and smart grid technology. Following are excepts from a white paper commissioned for the event. Covid-19’s influence on the transformer market has been multidimensional, intricate and far-reaching, impacting the global economy and trickled down to the energy sector, particularly the power grid market. In absolute terms, the global transformer market is expected to bounce back nearly to the 2019 level by the end of 2021. Moreover, delays in lead times and supply chain constraints experienced in 2020 have mostly returned to normal, providing an optimistic outlook for 2021.
Eco-sustainability, digitalization and solid state technology, or SST, are the key trends in transformer market nowadays. Grid dynamics are changing drastically owing to aggressive penetration of renewables and EVs, forcing the utilities to opt for active power control technologies. Anticipating this, OEMs are investing heavily in developing cutting edge technologies for transformers.
Digitalization enables utilities to operate transformers for short or long-term above nameplate rating by utilizing optimal thermal conditions, monitor vital parameters using smart sensors and make informed management decisions, thus preventing overcapacity specification of transformers during tendering process. Factoring the removal of fire safety systems, reduction in civil engineering costs and longer lifespan of ester oil-based transformers, PTR anticipates aggressive penetration of
KEY TRANSFORMERS MARKET
US$148m US$187m
Distribution Transformer Power Transformer
US$1,147m US$2,620m US$1,200m US$2,790m
US$300m US$460m
Source: Power Technology Research
US$124m US$178m
US$685m US$1,390m
ester oil-based solutions in the coming decade. Despite the flexibility and potential benefits being offered for grid modernization, higher cost and reduced lifespan have limited wide scale adoption of SSTs. OEMs have been researching to justify the additional cost and complexity of SSTs by offering features and services to add value for one-to-one conventional transformer replacement.
2021 Outlook
While the global health crisis lingers in the first half of 2021 with second and even third waves of the virus in many regions, accelerating vaccine rollouts and major stimulus packages in many advanced economies have provided a beacon of hope. PTR anticipates the global transformer market will grow 10 percent in 2021, propelled by growth in the Asia-Pacific and Middle East. • China limited the virus spread at early stages and was one of the few economies to report a positive economic growth in 2020. Dynamic growth for transformers is expected to continue through 2021, driven by exports, but especially by domestic demand, including policy-sponsored infrastructure projects. The outlook significantly improved at the end of the year, driven by recovering industrial production. • Early estimates project India’s transformer market growth in 2021 to compensate for the 2020 decline, although significant uncertainties remain linked to the evolution of infections and the rollout of vaccines. • The U.S. transformer market is projected to reach pre-pandemic levels owing to the American Rescue Plan, “the Biden stimulus,” and a successful vaccine program. • Major European markets Germany, France, and Spain, are anticipated to remain below 2019 levels, failing to fully make up for the declines in 2020. On a positive note, industrial production in the Europe is back to pre-Covid levels, owing to a recovery in international trade.
Saqib Saeed is executive director research and consulting, and Hassan Zaheer is executive director client relations and advisory, of Power Technology Research. n

Breakbulk Events & Media’s biweekly BreakbulkONE newsletter keeps the industry connected between issues of Breakbulk. Here’s a selection of subscriber favorites from the past few months.
KNOWLEDGE HUB: VETERANS
TRANSIT TIME SLASHED FOR DRAGLINE REPAIR
Never Accepting ‘No’ Works for Mining Customer
BY MURRAY COOPER
Being in the right place at the right time helped to reduce the lead time of steel beams urgently required at a mining site in Queensland, Australia. In the late 1980s and early 1990s, I was working with a leading project logistics management company that had transported more than six dragline knock-down kits to several Queensland coal mines from various suppliers of mining equipment from the U.S., Germany and Japan. A typical dragline shipment was about 12,000 revenue tons of equipment, wire, rope, etc.
While visiting major U.S. mining suppliers in March 1991, I learned that a US$50 million dragline operating in an open-cut coal mine in Queensland had been put out of action when its giant bucket struck the dragline’s boom. To give you an idea of the size, the giant bucket would scoop out enough earth in one “grab” to leave a hole the size of a family swimming pool.
The coal mine management team faced the challenge of losing 25 percent of its production for at least three months while the dragline’s boom was repaired. Engineers working on the dragline repair remedial project determined that 90 tons of special quality steel beams were required to reconstruct the damaged boom section. The coal mine procurement team worked long hours identifying a supplier of the steel beams, determining they would be sourced from a Pennsylvania steel mill, already cut in various sections and lengths to accommodate a speedy fabrication process onsite at the mine.
Murray Cooper
LV Shipping Group
LOGISTICS CHALLENGES
Logistics challenges then came into play. Normally steel beams were shipped as breakbulk cargo or on flat racks, resulting in a 30- to 35-day vessel voyage transit time.
I was able to work with the mining engineers in Queensland, via cellphone (there were no video calls in those days), as well as the Pennsylvania steel mill supplier, and quickly determined that the steel beams could be shipped via airfreight, if we could convince the 747 freighter aircraft owner to accept the freight and present the aircraft with sufficient equipment to securely lash down the load.
In 1991, not many airlines had experience in shipping steel beams, and traditionally all pallets were loaded onto the aircraft using a scissor lift, which were plentiful in the U.S. But in Australia, the nearest airport with a scissor lift capable of handling the discharge process was in Sydney, more than 1,200 miles from the coal mine delivery point. After several days of negotiations, it was agreed the steel beams could be configured on aircraft pallets and then loaded into the 747 nose-loading freighter at JFK Airport using a scissor lift.
The airfreight shipment required the steel beams be presented in a pre-specified sequence to the airfreight terminal cargo consolidator to configure the steel beams onto aircraft pallets. Also, to reduce the 18- to 24-hour transit time from Sydney Airport to the coal mine, we negotiated with the airline and local Brisbane airport personnel to discharge the steel beams using a crane in lieu of the nonexistent scissor lift.
It took a little more than 12 hours to load the steel beams onto the freighter at JFK and just three hours to discharge the cargo at Brisbane airport using a crane onto the road haulage trailers standing by on the apron.
The delivery of the steel beams from the U.S. mill to the Queensland coal mine took just five days and all the stakeholders involved were extremely happy with the outcome.
HOW WE DID IT
Behind the scenes, we conducted a risk assessment, and never accepted no for an answer. We assumed responsibility for downtime and repairs to the 747 freighter’s nose cone (if damaged during the discharge process), our company purchased insurance to cover our risks, thus turning what appeared to be an impossible task into reality.
Lessons learned here are get to the site of the action and pay attention to the details, conduct a risk assessment, and then supervise and expedite every step of the shipment process.
Murray Cooper, a 35-year veteran of logistics planning for abnormal loads, is director of corporate governance for LV Shipping Group and a Breakbulk Veteran. He has worked as a shipper and project logistics service provider in Australia, Indonesia, Malaysia and Singapore, where he now resides. He has executed supply chain logistics solutions in mining, resources, oil and gas, renewable energy, industrial projects, capital projects and sporting events. BBONE
SUBSCRIBE

to the industry’s leading source of information for cargo owners, logisticians and transport specialists.

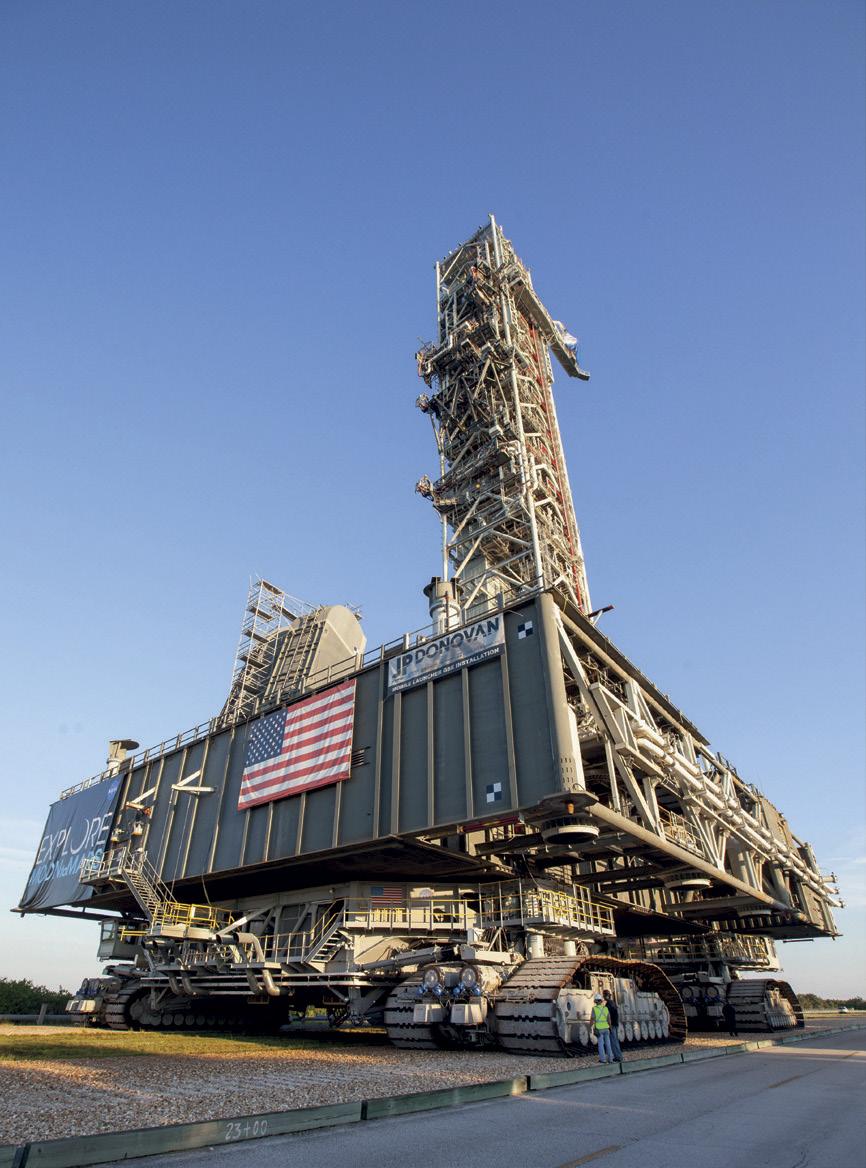
PROJECT CARGO CASE STUDIES REGIONAL REPORTS MARKET ANALYSIS AND COMMENTARY PORTS & TERMINALS ENERGY INFRASTRUCTURE OCEAN CARRIERS ROAD/RAIL/BARGE/AIR TECHNOLOGY & EQUIPMENT BREAKBULK EVENTS
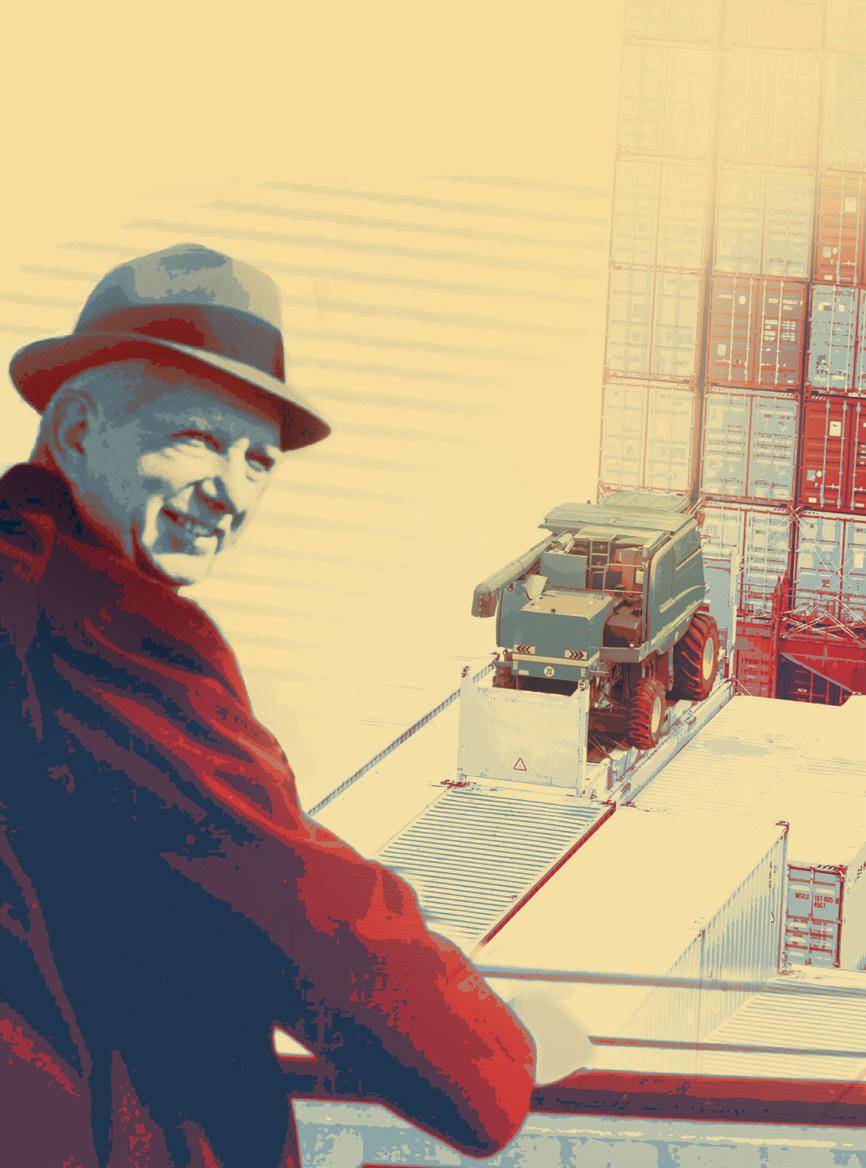
To start your subscription, visit www.breakbulk.com/subscribe/
For advertising information, go to
Breakbulk Movers Support Carbon-free Switch
Future Fuel Conundrum | Hydrogen Sweetspot | Post-Brexit Learning Curve
The Publication for the Industrial Project Supply Chain Industry
PART FAMILY NOW OF THE
Project Cargo Takes Malcom McLean’s Vision Out of the Box
Issue 2 / 2021
MPVs Back in the Black | Biden Turns Tide for US Wind | Tunneling Digs Deeper
This Breakbulk Issue is Sponsored by AAL Shipping
The Publication for the Industrial Project Supply Chain Industry Project Supply Chain Industry
Issue 1 / 2021 The Publication for the Industrial Project Supply Chain Industry
Opportunities ahead for GCC • A Novel Supply Chain • Egypt’s Strength in Adversity • Life After Expo 2020


KNOWLEDGE HUB: BUSINESS OUTLOOK
‘SMART PORT’ PLAN FOR PORT OF AÇU
HPC, UTC Overseas, Radix, UH Partner
HPC Hamburg Port Consulting, UTC Overseas, Radix Engineering and Software, and the University of Houston’s Supply Chain & Logistics Technology Program are collaborating to develop a “Smart Port Digital Growth Masterplan” for the Brazilian Port of Açu, or PdA, Latin America’s largest private port.
The partnership’s goal is to develop a five to 10-year vision for the technological platform for PdA and its ecosystem. The plan will focus on optimization of operations, attracting new technologically aligned businesses, and establishing a technological governance plan and systems architecture, according to a statement from UTC Overseas.
“Brazil is one of the strongest U.S. trading partners,” said Marco Poisler, UTC Overseas’ chief operating officer of global energy and capital projects. “The Port of Açu has a strong relationship with the Port of Houston ... Fostering and improving this connection through increased trade and advanced technology is very exciting.”
INNOVATION AND DIGITALIZATION
The masterplan development is based upon benchmarking of key worldwide ports, including Port of Antwerp, PdA’s strategic partner through the Port of Antwerp International, which is one of the pioneers in the smart port concept, focusing on innovation and digitalization.
“Large ports in the world, such as Antwerp, Rotterdam and Hamburg, use different and excellent port and maritime traffic management tools,” said Port of Açu Chairman José Firmo, “but few operate in the way that Port of Açu operates, integrating these tools in the same environment. There is a worldwide demand for greater integration of port and navigation systems.”
Luis Alfredo de Almeida Cruz, business development manager of Radix, said the company has developed digitalization projects for other ports, notably the CSN Port at the city of Itaguaí, Brazil, and some VALE ports. “We’ve found that the digitization of the various stages of the production process will allow the analysis of medium and long-term trends, with the aim of increasing the availability and efficiency of the port. This will lead to better decision-making – based on data – reacting more quickly to the market and with a leaner, more reliable and economical cargo movement.”
PdA expects the digital masterplan to generate greater efficiency, reduce time of shipments/landing, and link all clusters and production steps, such as movement statistics, availability, maritime safety data, customer specifics, and engagement with all stakeholders in the ecosystem.
Pablo Bowen, associate partner of HPC Hamburg Port Consulting, said digital plans are the first step to becoming a world-class port. “End-toend visibility of the extended supply chain, including the last mile, is one of the challenges. Availability of common software platforms for port communities’ stakeholders sharing information and with efficient processes is another challenge and makes the difference between port communities.”
The plan will propose digitalization of logistics processes and draw new businesses as a productive port.
“Beyond digitization, the ‘port of the future’ plans for new industry cluster needs, looks to collaborative partnerships to drive innovation and growth, applies the value proposition of the ‘triple bottom line,’ [and] understands the importance of filling the skills gap to not only prepare the ‘workforce of the future’, but more saliently to attract knowledge intensive industries, such as high-tech,” said Margaret Kidd, program director, Supply Chain and Logistics Technology, University of Houston. BBONE
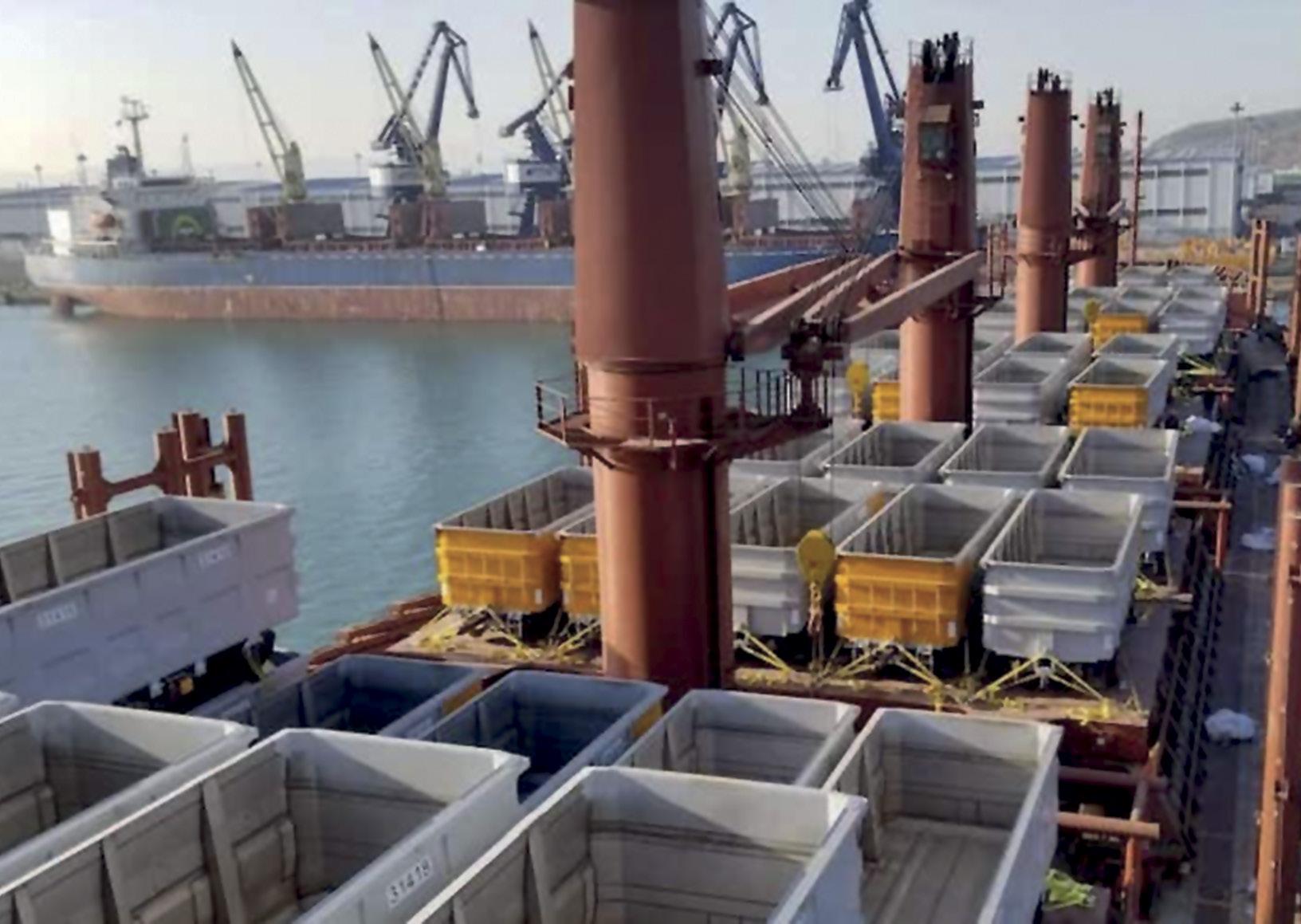
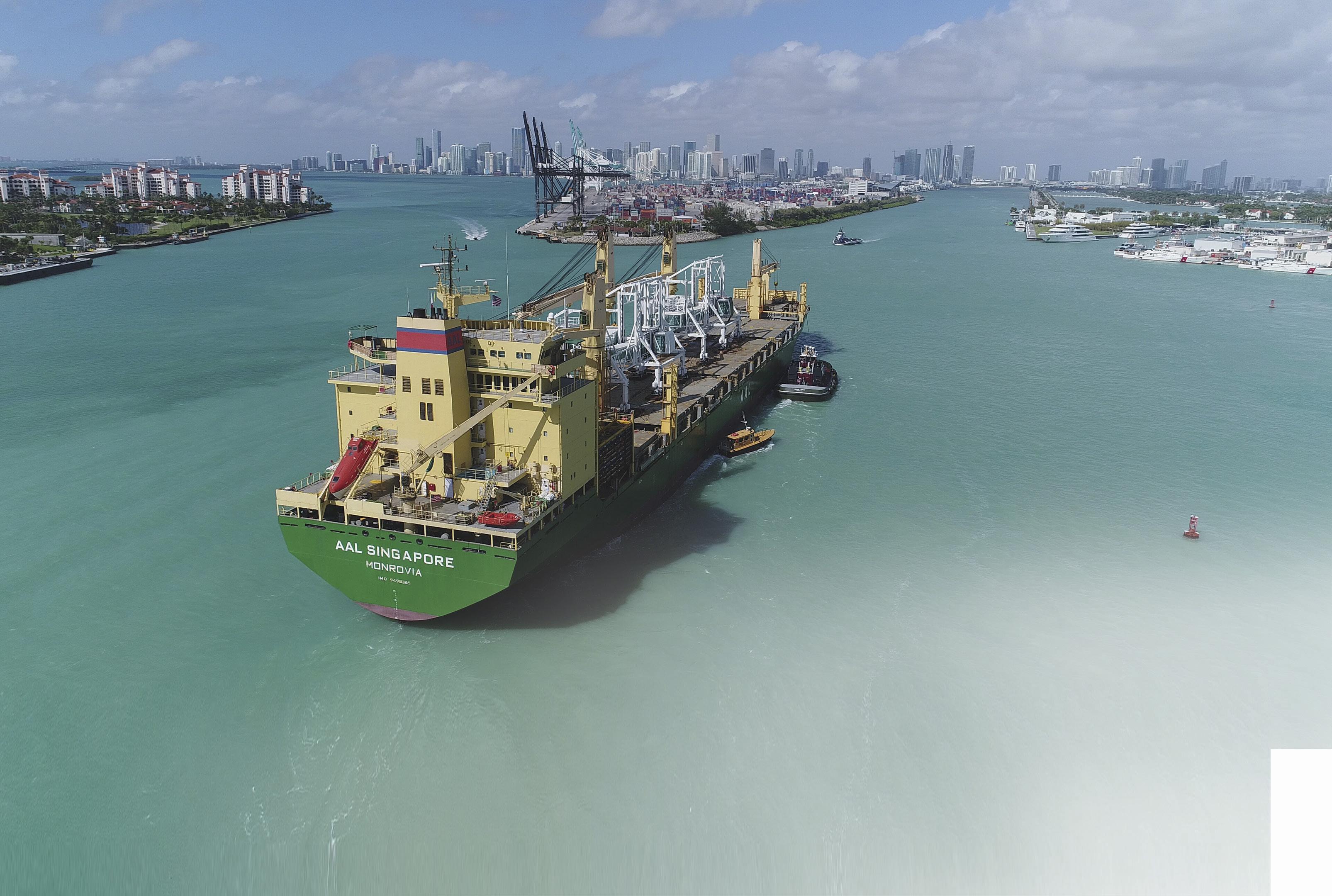
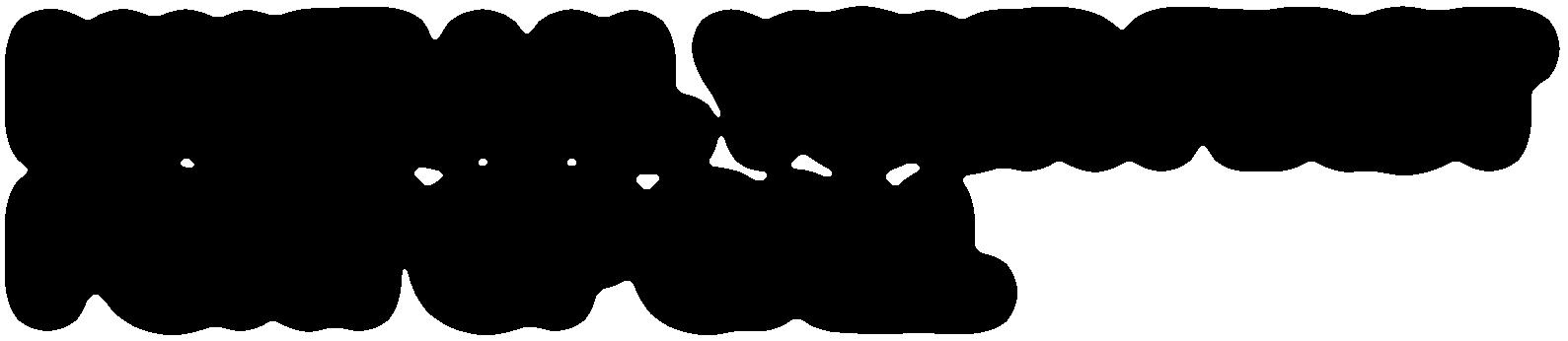
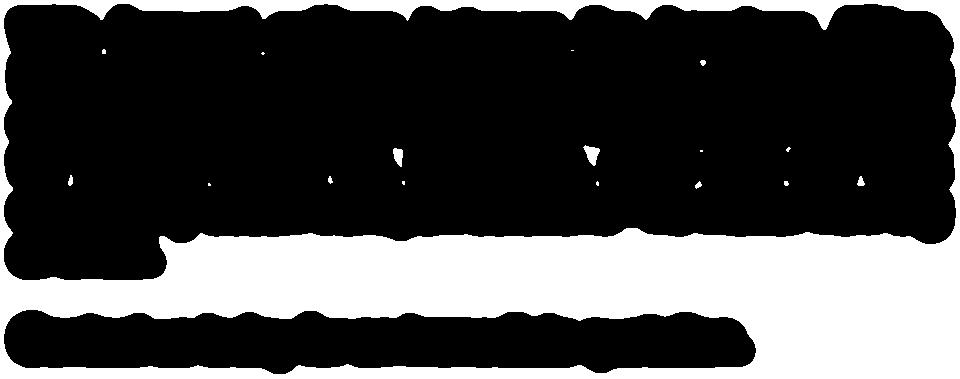