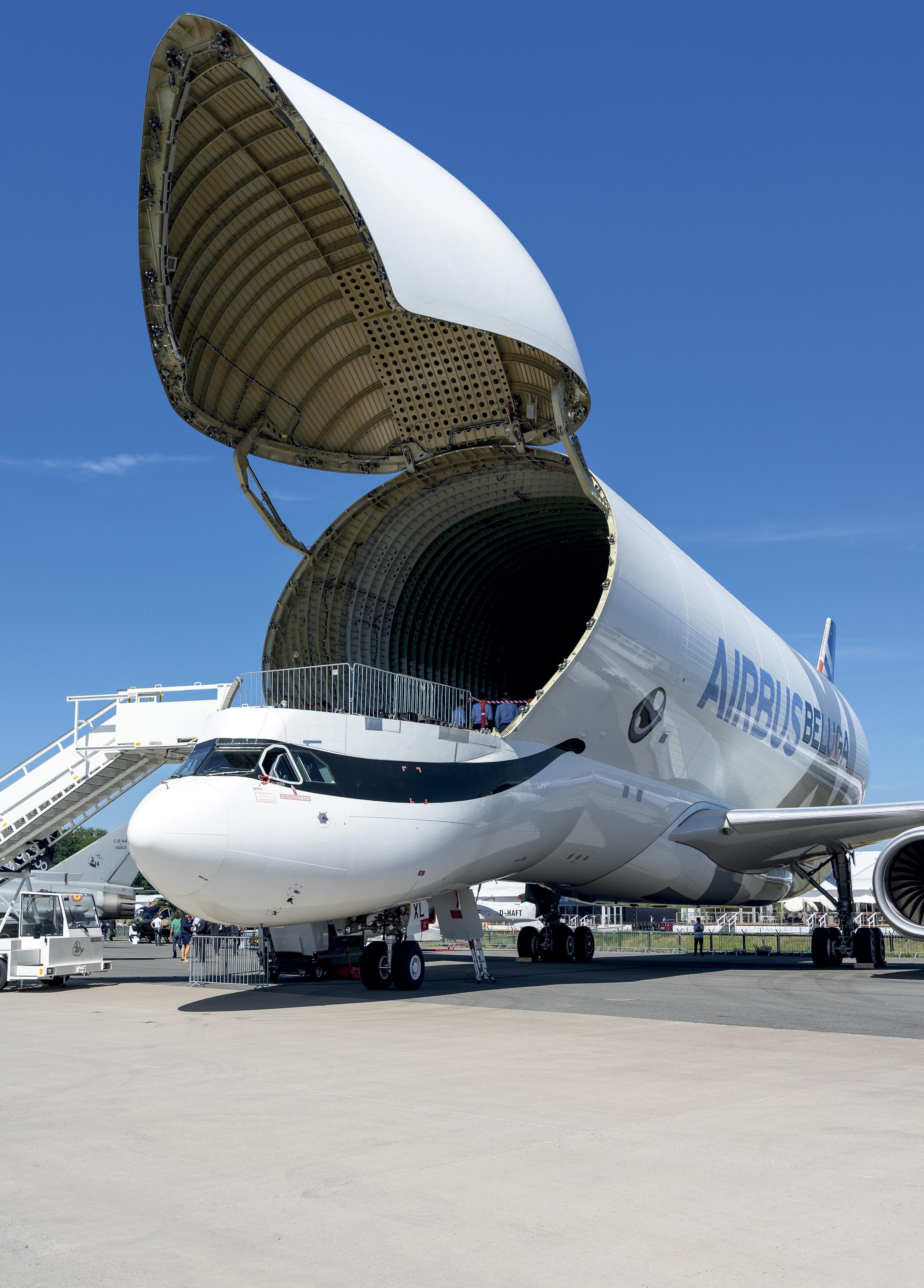
7 minute read
AIR CARGO CAPACITY CRUNCH
Aircraft Discontinuations, Geopolitical Events Add to Challenges
OUTLOOK AIR TRANSPORT
BY SIMON WEST
Boeing’s decision to discontinue its 747 freighter has triggered more concern among shippers and forwarders, as the industry faces a growing challenge when it comes to accessing aircraft and specialized equipment for moving breakbulk and project cargo.
Originally designed to transport missiles and other military hardware, the B747-F’s nose-loading capability – which allows out-of-gauge components to be shipped in one piece without the need for disassembling – has been an integral part of the sector’s air freight arsenal for decades.
Robert Reed, director of supply chain at Nabors, a Houston-headquartered oilfield services specialist that owns and operates one of the world’s largest land-based drilling rig fleets, said the B747-F’s discontinuation had given the Robert Reed industry “food for thought.”Nabors Nabors typically uses the aircraft on an ad-hoc basis to transport drilling equipment and rig components when the most critical part of the supply chain equation becomes the compression of time, Reed told Breakbulk.
“Our most recent example was moving part of a drilling rig mast to the Middle East. It was too long to be loaded through a 777 side-door loader, so a 747 nose-loader was required,” Reed said.
Air cargo plays a pivotal role in delivering equipment and supplies for projects. Air freight is often used for emergency replacements or when shipments are on very tight deadlines.
IMPACT OF WAR
While the impact of the B747-F’s discontinuation may not be felt for some years, recent geopolitical events have had a more immediate bearing on the availability of aircraft to transport oversized cargo.
The conflict in Ukraine has seen the operations of Russia’s Volga-Dnepr Group – one of the major players in the market – severely curtailed. Although the carrier can still work on certain humanitarian operations, it has been banned from commercial flights to the U.S., Canada, Europe and other major markets.
Volga-Dnepr, alongside its subsidiaries AirBridge Cargo and the British-flagged CargoLogic Air, was one of the market’s main suppliers of combined wide-body, heavy-lift aircraft such as the B747-F, the Ilyushin IL76TD-90VD and the Antonov AN124-100.
For project cargo, the AN124-100 represents the most critical shortage.
Developed in the 1970s for strategic government purposes, the AN124-100 is commonly used to transport up to 100 tonnes of heavy and oversized cargo such as transformers, turbines, satellites, oil and gas components, industrial machinery, aircraft parts, helicopters, trains and yachts.
For shippers and forwarders, it is a unique aircraft, and one of the few models with a payload capacity to transport extraheavy components.
“It is a massive impact,” said Fayçal Boumerkhoufa, vice president of integrated project solutions at CargoLive Logistics. “Take twelve AN124-100s with an average of between 80 and 100 tonnes active payload, and that is a serious amount of cargo that suddenly needs to find an alternative solution.”
“In terms of the capabilities for project cargo, it does change the landscape and the way that air transport solutions are planned and executed.”
The hostilities have also impacted Ukraine’s Antonov Airlines, who, earlier this year, was forced to relocate to Leipzig in Germany. The carrier had been operating out of the Gostomel airbase close to capital city Kyiv.
Amnon Ehrlich, Antonov’s director of sales for North America aerospace, government and defense programs, said five of the company’s seven AN124s were still operating.
“At the time, when the war started, luckily, we had five aircraft that were outside of Ukraine,” Ehrlich said at Breakbulk Americas in Houston. “Those five aircraft are currently operating – two of them are for NATO or for SALIS (Strategic Airlift Interim Solution), the other three are operational for commercial use.
“But of course, there is the issue of maintenance. It is an aircraft that requires a significant amount of maintenance. So, there is always at least one to the side.”
Region: Global Problem: Challenge of securing air freight space for time critical project moves Solution: Manufacturers are bringing in new capacity to fill supply gaps
Fayçal Boumerkhoufa
CargoLive Logistics
ACCESSIBILITY AND COST QUANDARY
The market’s shrinking accessible fleet, which is pushing up costs for customers, is the latest development in a rapidly evolving air freight market that has seen wide-body freighters increasingly assigned on long-term contracts to commodity manufacturers and largescale forwarders.
As a result, air cargo capacity, according to Boumerkhoufa, has been “gobbled up.”
The emergence of twin-engine airplanes, whose operational costs are significantly cheaper compared with a model equipped with four engines, is a sign that aircraft manufacturers are catering towards different end-market needs, such as e-commerce and general cargo packaging.
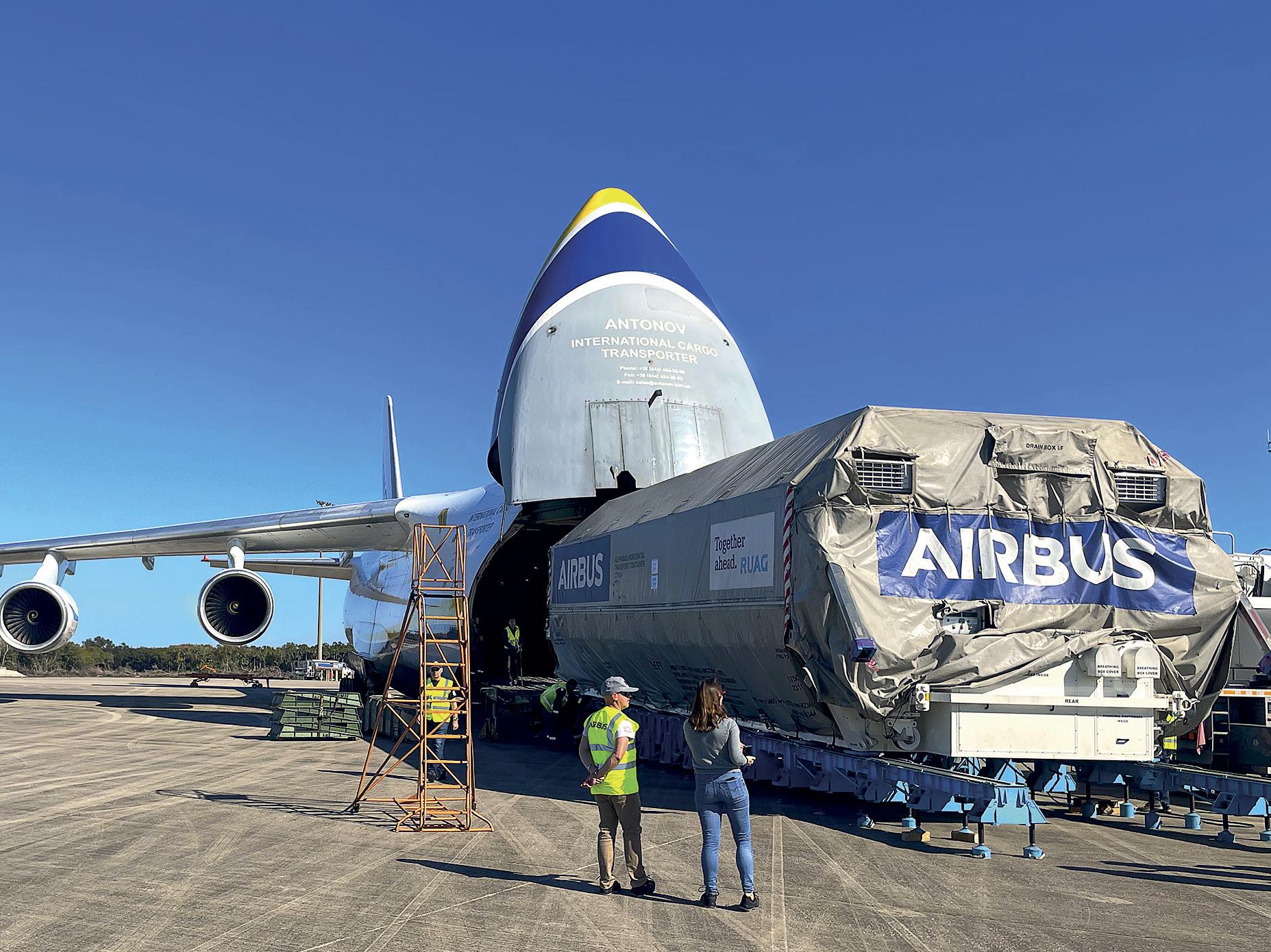
“As such we have the Boeing 777 freighter that is out on the market now as a replacement (for the 747),” Axel Kaldschmidt, vertical head for aerospace, marine and defense at Schenker Americas, said at Breakbulk Americas. “It has the same tonnage as the 747, but no nose door. And that nose door for project cargo is a huge influencer, particularly when it comes to rapid movement.”
Environmental regulations coming into play in the next few years will see older generations of the 747 taken out of the market, tightening availability further, the executive said.
AIRBUS COMES TO THE RESCUE
Repurposed aircraft entering the market could offer customers some respite.
European aircraft maker Airbus, for example, is getting ready to launch more of its A300-platform Beluga ST widebodies for ad-hoc charters. Five STs are being refurbished for heavy cargo operations after Airbus announced the aircraft would be replaced by six brand-new A330 Beluga XLs, used to ship Airbus aircraft sections to different Airbus sites in Europe. “Knowing the Beluga ST fleet can still fly for another 20 years or more, we thought, OK, and to North America, Europe, Middle East, Asia, Asia-Pacific and the Indian Subcontinent. We also see some needs for the military market in some African regions.”
A second lifting function expected to begin operations next year is an onboard cargo loader, designed to fly inside the Beluga. The loader, which boasts a payload capacity of 20 tonnes, will be deployed for more urgent missions, allowing the carrier to be even more autonomous and reactive, the executive said.
Reza Fazlollahi
Airbus Beluga
let us give them a second life,” said Reza Fazlollahi, business development and commercial director at Airbus Beluga.
“We spoke with freight forwarding companies and brokers all over the world to understand the needs and the challenges the oversized air cargo market was facing. And we quickly understood that there was a need for capacity.”
The ST has a customer payload capacity of 40 tonnes, and while less than that of a 747 or an AN124-100, its unique dimensions – including an inside height of 6.7 meters – means the aircraft is ideal for carrying oversized cargo for industries such as oil and gas, aerospace and construction.
A first Beluga ST is already in operation, with a second slated to start flying early next year. “The third will join at the end of next year, and a fourth one in 2024. And the fifth one either at the end of 2024 or beginning of 2025,” Fazlollahi said.
The development, meanwhile, of two loading techniques for over-dimensional freight will allow the Beluga ST to handle different types of cargo.
The first technique is an outboard platform, a 5-metre-high lifting device that will be positioned in advance of an aircraft’s arrival and deployed alongside a crane to offload cargo. The platform can be assembled and disassembled in one day and easily transported in standard 20-foot containers.
Up to 20 platforms positioned at strategic airport locations will be available by the end of 2023. “The precise locations are not known yet,” Fazlollahi said. “But we see high demand from
Nose-loading capability allows out-of-gauge components to be shipped in one piece without the need for disassembling.
CREDIT: ANTONOV AIRLINES
FUTURE BUILDOUT CHALLENGES
For manufacturers, the cost of building new aircraft, or reshaping existing ones, is crucial.
“Anything is possible with the right money and time and investment,” Kaldschmidt said. “If you look at the 747 passenger aircraft, you can convert it into a freighter, but only with the side door. In order to do a nose door, it is a structural change, then your costs start getting very prohibitive.”
Project cargo owners themselves may be forced to adapt.
The diminishing pool of available cargo aircraft could result, for example, in more modularization, whereby projects are disassembled prior to shipping, then reassembled once delivered to the job site.
“Modularization will provide more opportunity to compress the delivery time for critical material by using air freight in a world without a 747 noseloader,” Reed said. “Even if a project is planned for ocean shipping, supply chain disruptions occur, and air freight needs to be utilized.”
For Boumerkhoufa, there is no quick solution: “Building aircraft, or refurbishing aircraft – these are gargantuan tasks,” he said.
“I am not saying it cannot be done under the right circumstances. If the right funding and attention is there, things do happen. But for now, the way everything is laid out, how the market and the world are moving – we face a big challenge.” BB
Colombia-based Simon West is senior reporter for Breakbulk.