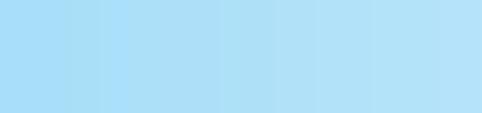
6 minute read
BOB TEAGUE


Advertisement



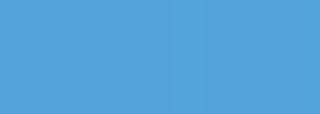













TEAGUE ON TECH BOB TEAGUE Low Oil Pressure

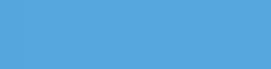
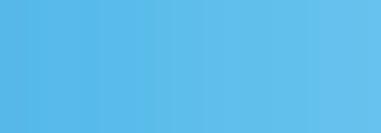
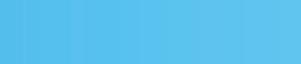
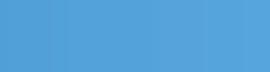
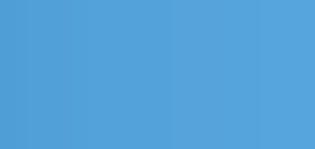


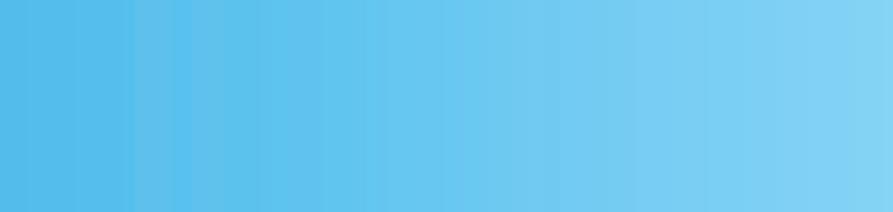

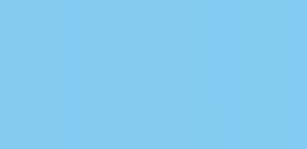
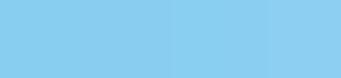
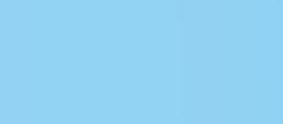
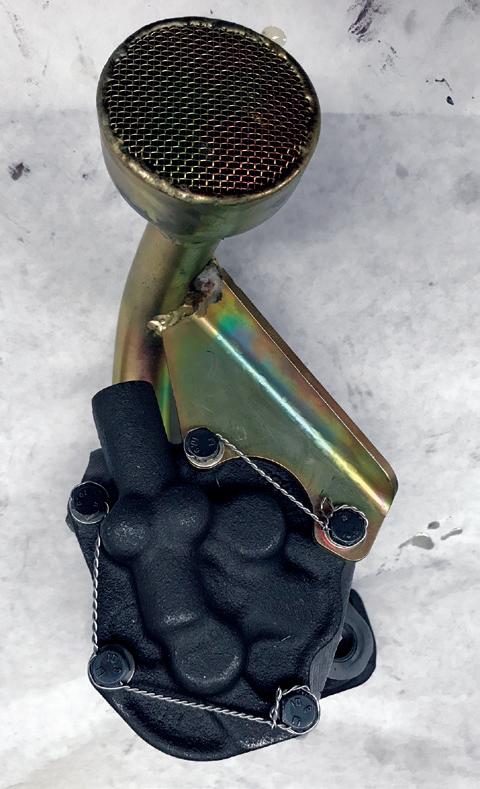




Dear Bob: I have a 2000 Mercury carbureted HP500 with an M3 ProCharger in my boat. Last winter, after 470 hours of operation, I had the engine rebuilt. I had asked the builder to install a high flow oil pump; however, I believe he installed a standard Melling M77 oil pump. Prior to the rebuild, my engine had oil pressure of 70 to 75 PSI at WOT (5,000 rpm). Now, the highest oil pressure is 45 psi.
I am running Valvoline VR1 50 racing oil and the idle cold oil pressure is about 40 psi, which drops to about 24 psi when the engine is hot. The oil pressure comes up to 45 psi pretty quickly off idle when hot but will not go any higher. I have confirmed and duplicated the dash gauge pressures with a mechanical gauge.
I have received opinions at both ends of the spectrum. The builder felt that the 45 psi was sufficient and offered to provide a different pump at no charge. Of course, that’s the easy part compared to pulling the motor again. I ran the boat last season with no apparent issues, but the oil pressure makes me nervous as I know the rule of thumb of 10 psi / 1,000 rpm. I am well short of that standard. I would appreciate your input.
I also wonder if you would offer your opinion on what fuel pressure I should be running at WOT and 8 psi of boost.
Michael Cosgrove Louisville, KY
I share your anxiety regarding the substandard oil pressure in your motor. If the engine were a stock 260 hp small block, or a stock 300 hp big block Chevy, I would not be so concerned. Being that your engine is unnaturally aspirated, and capable of turning in excess of 5,000 rpm, 45 psi of oil pressure with straight grade 50 weight oil makes me nervous too.
It is important to realize what establishes the oil pressure in the engine. When your engine was stock from Mercury, it did not have a high-volume oil pump. But with the standard pump, it had decent oil pressure. The point is that the oil pump is only part of the equation. The oil pump does have a pressure relief valve built into the cap. The fact that your oil pressure immediately comes up to 45 psi (and no further) could indicate that the oil pump that the builder used has a relief valve spring that is too weak for the application or the relief valve plunger is stuck in an open position. If a Melling 77HV is used, sometimes it is necessary to shim the spring to raise the relief setting. I recommend that you use a Melling part number 10778 pump which has chrome-moly shafts. It also has the drive and idler shafts that have been extended into the cover for additional support, which eliminates possible deflection inherent during higher RPM operation.
In order to verify if your oil pump is the problem, I would perform a comparative test. Obtain a pre-oiling device. You can make one by modifying an old distributor. Remove the distributor, install your mechanical oil pressure gauge, and “pre-oil” the engine using a substantial 1/2 inch electric drill motor. Then, remove the oil pan, install the new Melling 10778 oil pump, replace the pan (without sealing it for the test), and repeat the test with the new pump. If that resolves the pressure problem, put the pan on for real and you are good to go. If it does not, the following are other things to consider.
Engine bearing clearances are one of the most significant components of the oil pressure equation. If the rod and main bearing clearances are too great, the increased flow results in lower pressure, with all other things being equal. Proper rebuilding of a high performance engine requires that the crankshaft be precisely measured, and compared to the measurement of the bearings installed into the torqued main caps and connecting rods. This operation requires special inside micrometers that are designed to measure engine bearings. This is because the bearings are not perfectly round when installed. The measurement is less from top to bottom, compared to side to side. The crankshaft is measured with a standard micrometer. It is also important that all the measuring instruments are calibrated to each other. The block, crank, rods, and measuring micrometers must all be the same temperature to achieve accuracy. Once the clearances are measured, using a combination of “standard,” .001” under, or .002” under or .001” over (HX) bearings are used to establish the correct bearing clearances. For high performance big block Chevys, the main bearing clearance should be about .003” on the number 1 through 4 mains, and about .0034” on the rear main. Connecting rod bearing clearance should be between .0027” and .003”. It is possible that your builder simply used “standard” bearings because the crankshaft was “standard.” If that is the case, it is also possible that the clearances are excessive which would result in lower oil pressure.
Left: Melling 10778 Oil Pump and Pickup. Center: Measuring crankshaft for rod bearing clearance. Right: Measuring main bearing installed in block.

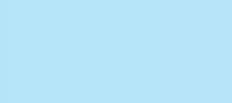
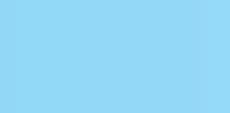

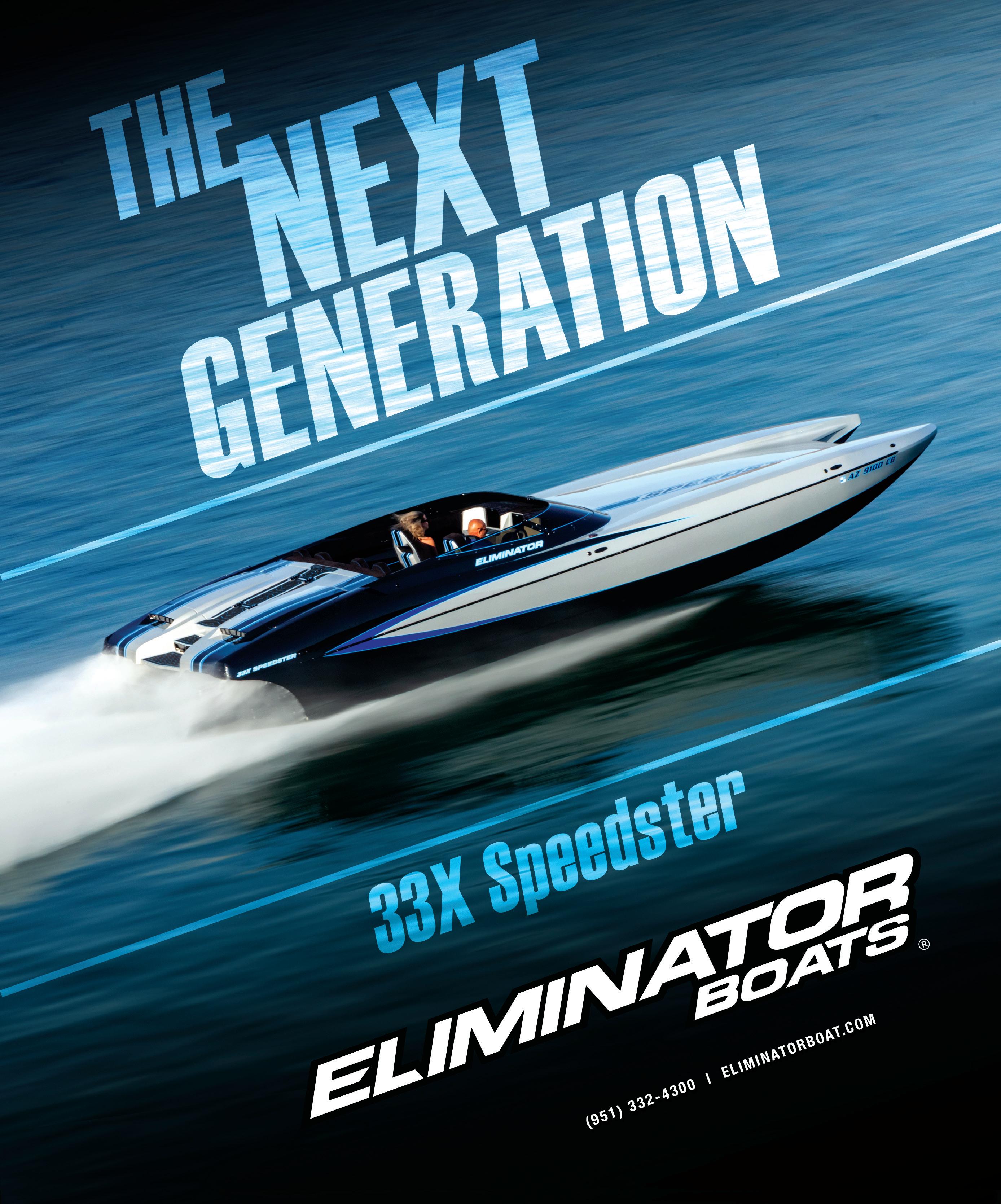
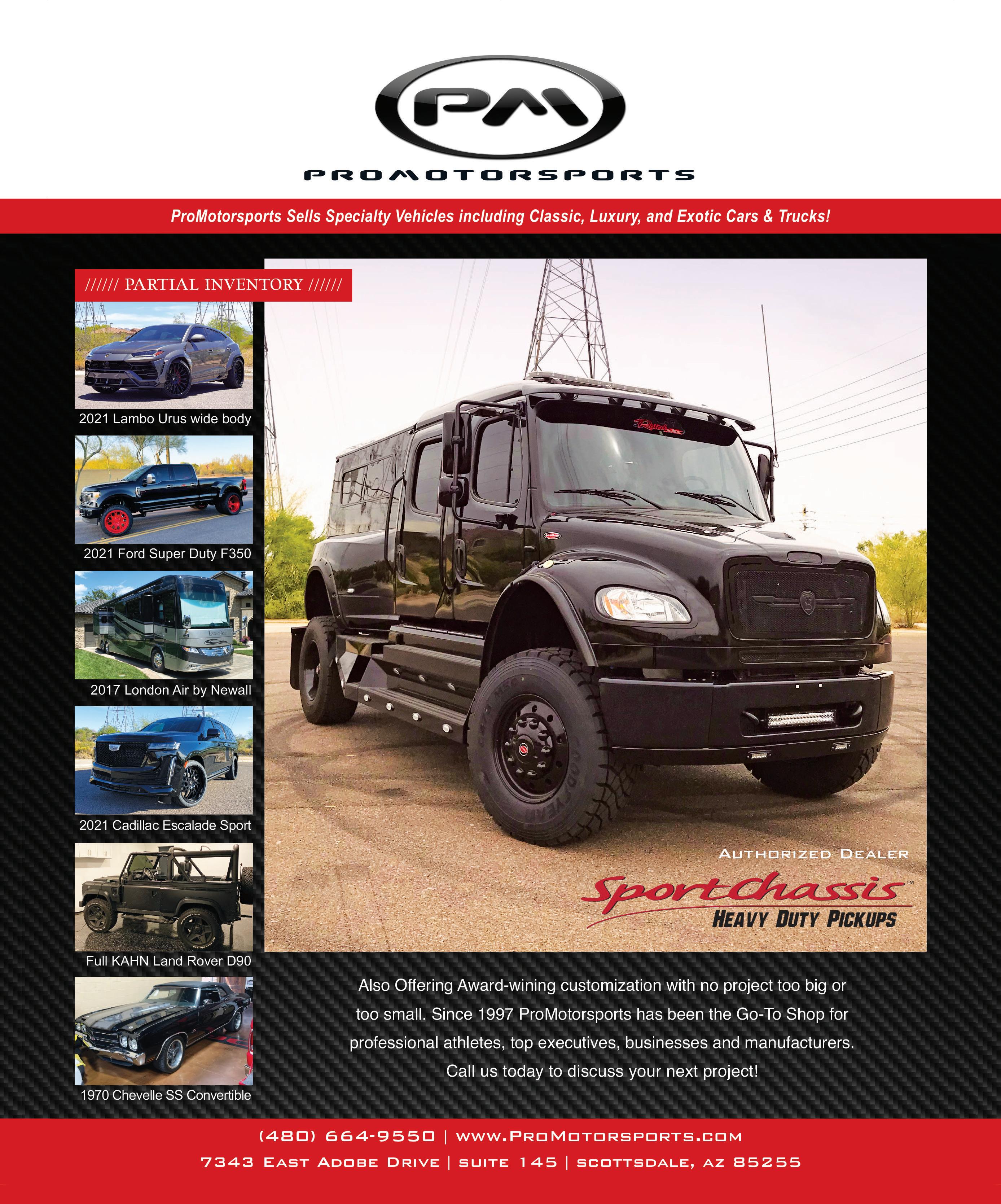
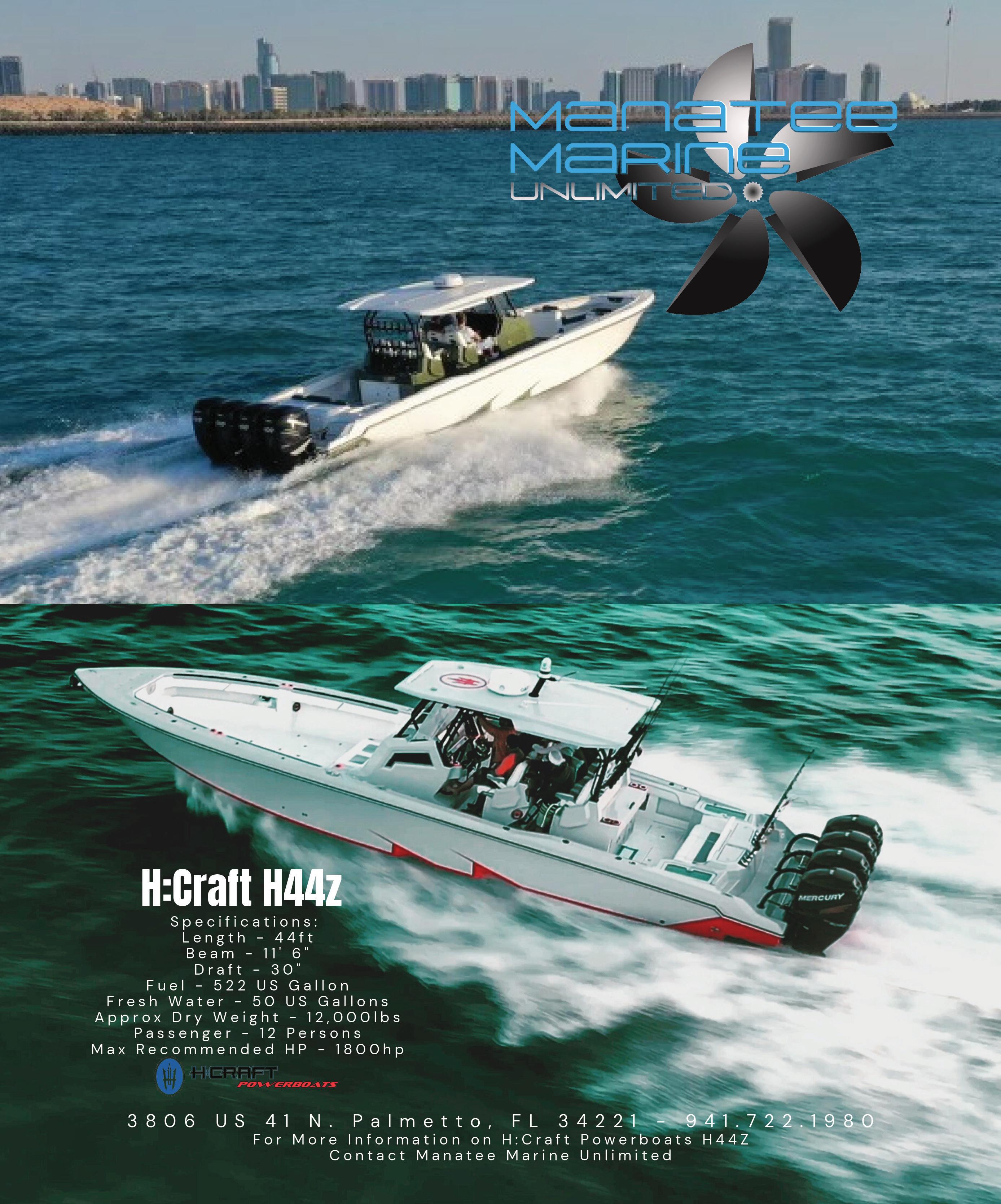