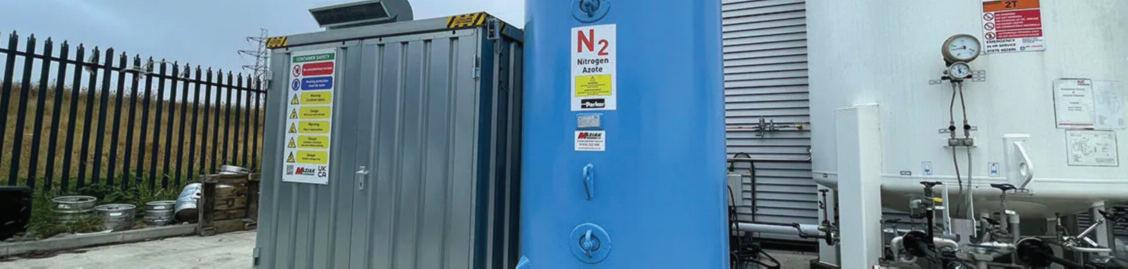
2 minute read
Nitrogen generation for craft brewer Wells & Co
Replacing CO₂ with nitrogen reduces reliance on CO₂ and can save 73% in costs per cubic metre, and Wells & Co has chosen Parker ’s NITROSource, a standalone system, to generate nitrogen on demand and replace CO₂ in production processes.
“As a business, we’ve seen the impact of the huge increases in energy costs on the price of CO₂ as well as regular supply shortages,” says James Hunter, Head Brewer at Wells & Co “While we can’t replace CO₂ completely, we can swap nitrogen in to a number of our processes By installing NITROSource, we’ve reduced our costs and our carbon emissions ”
Advertisement
Breweries face ongoing challenges with CO₂ cost and supply CO₂ shortages have hit breweries hard in recent years. It’s used throughout production so interrupted supplies can often cause output issues and may push prices up The energy crisis has made the situation worse The rising cost of gas recently prompted CF Industries to halt ammonia production at its Billingham plant, meaning that the production of CO₂ at the plant will also cease Where CO₂ is available, brewers are seeing huge price increases
Wells & Co, a leading craft brewer, produces 25,000 hectolitres of beer at its Bedfordshire plant, using 500 kg of CO₂ each day While their CO₂ costs were contracted, the contractual price is linked to supply and if CO₂ becomes hard to get hold of, the cost rises Wells & Co didn’t experience production downtime because of CO₂ shortages, but this was only because it was able to buy gas in bulk
James Hunte adds: “We have a bulk tank on site that is sized for regular 4-6 weekly refills of CO₂, but that’s something smaller breweries simply can’t do Supply shortages are a real problem for many brewers ” Lowering costs and reducing reliance on CO₂ were key business objectives
Nitrogen can replace CO₂ in some processes and with Parker ’s NITROSource, it can be generated on demand at a fraction of the cost of buying in gas While the level of dissolved oxygen (DO) produced must be considered, any potential degradation of product quality is assessed in the initial scoping exercise
“NITROSource generates food-grade nitrogen and it’s the only system on the market that offers full BRC compliance as installed,” explains Hunter “It was straightforward ” The scoping and sizing exercise calculated existing gas usage, taking into account the link between peak demands, purity and buffer capacity
“If you get your calculations right, the installation should be straightforward,” says James “It’s literally plug and play for the unit, then you just have the electrical supply and peripherals like the pipework to manage ”
The brewery’s use of CO₂ has reduced by 50 tonnes per year
NITROSource generates 22 m3 of nitrogen per hour, and the equivalent of around 500 kg of CO₂ in 12 hours. Converting to NITROSource has reduced costs by over 70% and Wells & Co now uses nitrogen to transfer the conditioned beer after fermentation and control the top pressure in the buffer tanks and the finished tanks The first two purging processes are driven by nitrogen, while CO₂ is still used in the third round www.parker.com