
33 minute read
The Role of Virtual Tastings in a Post-Pandemic World
By: Alyssa L. Ochs
The COVID-19 pandemic affected all aspects of life in 2020, from how we received medical care to how we dined at restaurants, shopped at stores and even enjoyed our favorite craft beers and spirits. In past years, craft beverage enthusiasts planned entire road trips and even flew to other countries to experience what the best brewers and distillers of the world had to offer. But during the COVID era, producers were forced to switch gears and consider offering virtual tastings as one of the many ways to stay in business due to restrictions and shutdowns. We heard a lot about virtual beer, wine and spirit tastings during the height of the pandemic, but those conversations have dwindled as business picked back up as usual. Yet there still may be a place for virtual tasting experiences in today’s craft beverage industry, just as long as producers can evolve with the times and reestablish the relevance of this service among the mix of in-person offerings and events.
What Are Virtual Tastings?
Virtual tastings are a relatively new concept, and many people don’t consider trying them because
they don’t understand what they are. Virtual tastings are immersive, alcohol-themed experiences you can enjoy from the comfort of your home. Many of them require breweries and distilleries to ship boxes to households with sample-size portions, materials to read and opportunities for online engagement.
During the COVID-19 shutdowns, some beverage producers turned to virtual tastings as a way to keep their customer base engaged and stay afloat as profits declined. But even during times of normal business operations, virtual tastings can be used to celebrate birthdays at home and corporate events in an office. Beyond the confines of a physical tasting room, there are also opportunities for virtual tastings at team-building activities, couples’ date nights and social gatherings to help local groups get to know each other.
Types of Virtual Tastings
Some breweries and distilleries have created virtual tasting packages with beverage and food pairings to entice customers’ attention, particularly when in-person tastings were not an option. Recently, we have seen cooking kits emerge with alcoholic beverage samples and opportunities to participate in live online events.
Other virtual tastings experiences involve sending a few bottles or cans of products to consumers with exclusive online access to an hour-long video call with a brewery or distillery representative. There have also been question-and-answer sessions offered with brewers and distillers, beverage judging sheets provided so consumers can rate and pick their favorites and seasonal experiences that highlight fall and winter brews, for example. To further capitalize on virtual tasting experiences, producers can offer the option of purchasing branded merchandise, such as hoodies and beanies, as part of a shipped package for an additional, discounted cost.
Benefits of Virtual Tastings
During the pandemic times, the benefits of virtual tastings were evident because of the lack of other tasting options allowed and available. Virtual tastings enabled beverage fans to support struggling producers during difficult times while still feeling like part of the beer and spirits community. But even now, there are some significant benefits
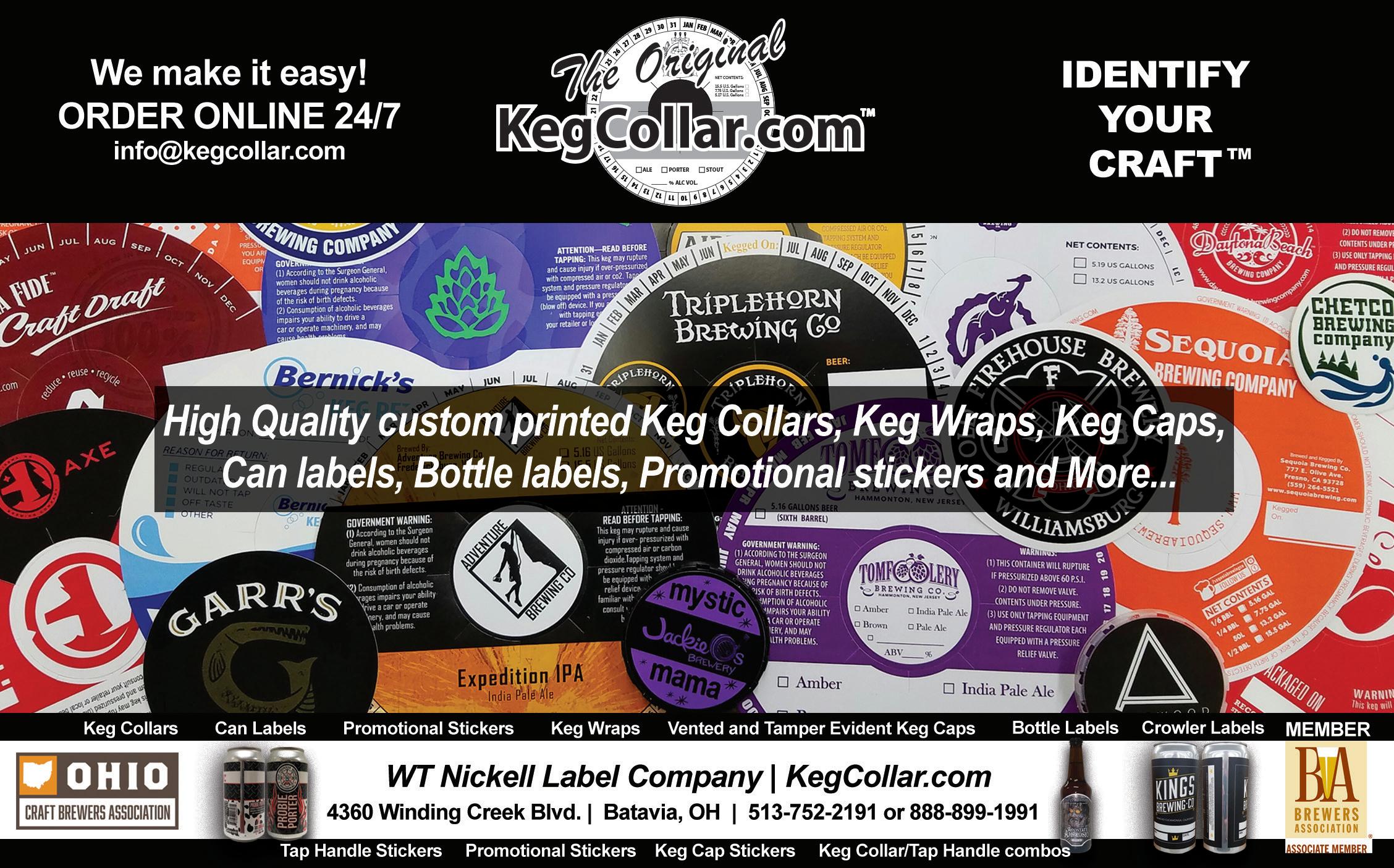
of virtual tastings that are worth considering for the months and years ahead. If marketed well, these socially distanced offerings can help breweries and distilleries reach new customers outside their home region who may not ever travel to the actual tasting room. During the winter cold and flu season, when COVID-19 cases tend to increase, virtual tastings appeal to some consumers as a safer and healthier alternative. If a tasting package includes printed materials that are informational and fun to read, there are opportunities here to help consumers better understand a beverage brand and its products. Since these packages can be designed around different interests and price points, they can offer something for everyone, from the casual drinker to the true connoisseur.
Challenges of Virtual Tastings
Yet many challenges come with putting together virtual tasting packages, first and foremost, their relevance and value. Beverage producers must make these types of delivery/online tastings worth the cost and add value consumers wouldn’t necessarily get by visiting the establishment in person. There has been declining demand for these services lately and less internal dedication to marketing them since people are willing to travel more and crave a return to normalcy in the outside world.
Meanwhile, some breweries and distilleries have been unsure of what to charge for virtual tastings. The average cost for this service is between $50 and $200, depending on how much product is shipped and other perks offered. For the virtual tasting industry to be sustainable, more effort will need to be directed to packaging and shipping beverages, which is a significant pivot from the previous experience of many beverage operations. There also need to be staff members who are tech-savvy and trained in how to plan and lead online events, as well as handle the inevitable technology glitches that so commonly occur during video calls and group chats.
Creative Ideas for Virtual Tastings
If virtual beer and spirit tastings will survive as a side gig in the craft beverage industry, now is the time to get creative with offerings, pricing and perks. If this is something that a brewery or distillery owner is interested in getting involved
with, it might be worth hiring a company or consultant specializing in virtual experiences instead of handling all aspects internally. At a minimum, it is worth researching examples of successful virtual tastings and perhaps even reaching out for a discussion or collaboration. Denver Microbrew Tour, City Brew Tours and Common Space Brewery are a few of the many groups that have excelled in this space. Other examples to learn from include Brews Less Traveled, Sierra Nevada Brewery, Fullsteam Brewery and the Sommelier Company.
One idea to consider for future virtual tastings is to make the experience customizable for certain types of products, such as whiskey, rather than taking a one-size-fits-all approach. Promotions for the service can be centered on the benefits of receiving miniature versions of spirits so that consumers can try samples before committing to full-bottle purchases. Celebrity promoters and social media influencers may be able to help revive the virtual tasting industry if breweries and distilleries make the right connections. Also, the virtual tasting experience can be enhanced by social media participation and through educational lessons about mixology and beer-brewing.
The Outlook for Future Virtual Tastings
At least for now, it seems that most craft beverage producers, including Fullsteam Brewery, have stopped offering virtual tastings since the lifting of COVID restrictions. With people feeling increasingly comfortable going out in public and preferring in-person experiences to virtual ones, there are significant challenges for the virtual tasting industry right now, but not insurmountable ones.
Winter is an ideal season to revive virtual offerings because of the predicted increases in COVID-19 and flu cases. This is also an ideal time of the year for virtual options for holiday gift ideas, because of cold weather that keeps some people indoors and potentially more difficult travel with snowy conditions.
While we don’t anticipate virtual tastings ever replacing the actual experience of drinking onsite, they could be offered as an add-on opportunity for consumers to get even more involved with their favorite beverage companies. During the holiday season, these types of tastings can take the guesswork out of planning gatherings at home with a fun activity as the party theme. As the weather warms up, forward-thinking producers may be able to expand virtual tastings to virtual festival events and online education about beer and spirits. This could lead to more formal training in the craft beverage industry and perhaps even address the staffing shortages still so prevalent in so many places around the country. Yet, in the short term, these shortages may also prevent breweries and distilleries from having the labor resources to dedicate to the tech side of beverage marketing in the first place.
If you are interested in getting more involved in the world of virtual craft beverage tastings, you should know that this market is far from saturated, and there are openings for growth. Emerging, niche companies could assist with the production and execution of virtual experiences as a service to breweries and distilleries that do not have the time, expertise or staffing to do so themselves. But for now, these types of tastings will primarily be carried out by individual breweries and distilleries that are large enough, have ample staff and enough time and resources to expand their offerings to an online audience. If successful, those offerings could be models for an expanded online industry in the future.
As a small sampling for inspiration, here are some resources to check out and virtual tasting ideas to consider:
• The Drunken Grape has a team of sommeliers and offers interactive tastings, niche event planning and execution for private parties, wine and beer dinners, and weddings/corporate/charitable events.
• Book a beer expert for your event through City
Brew Tours.
• Bourbon & Banter offers whiskey tastings for corporate events.
• Dewar’s Aberfeldy Distillery is still hosting virtual experiences upon request.
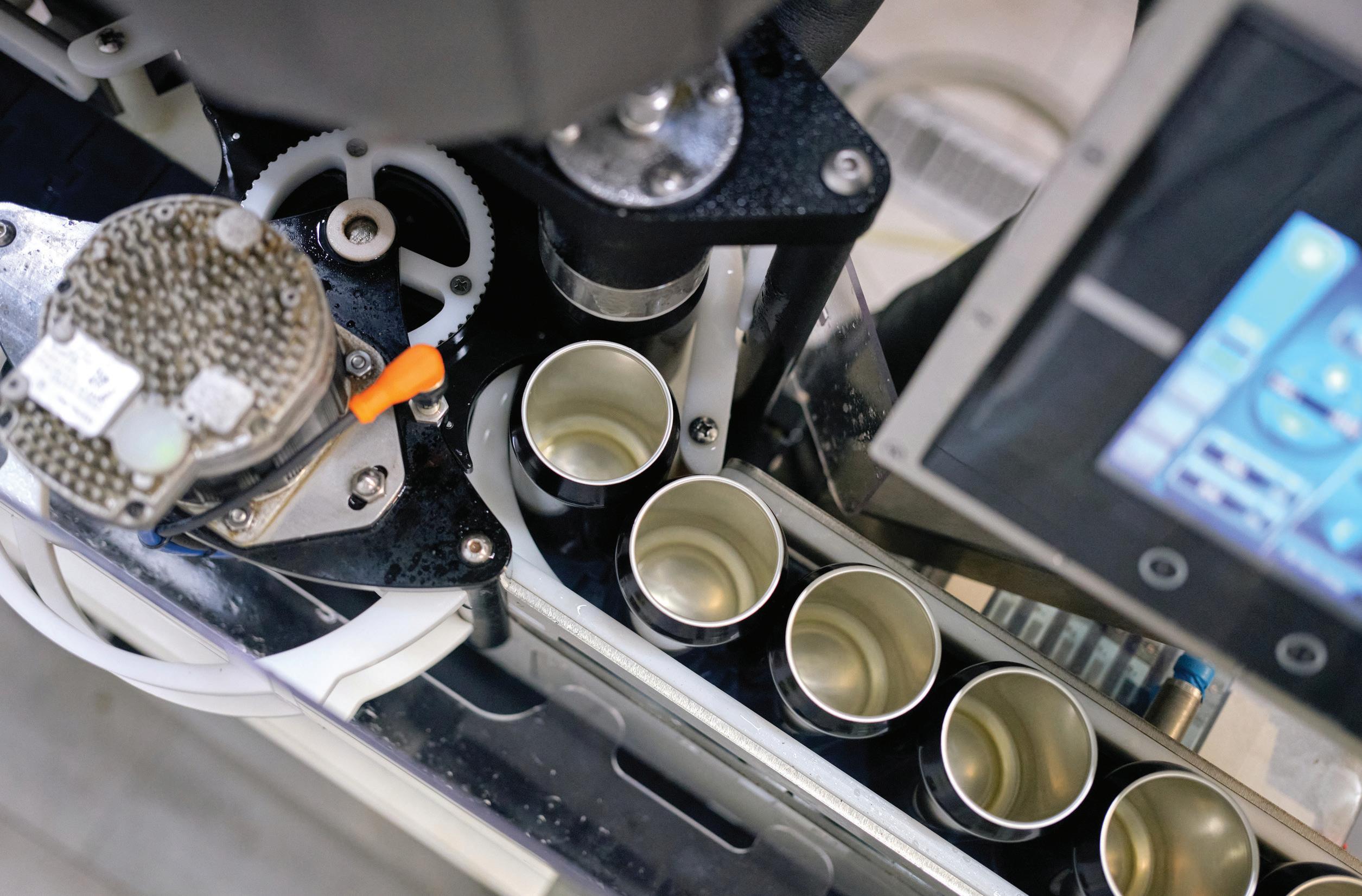
Keeping an Eye on the End Game:
By: Cheryl Gray
Savvy craft brewers want problem solvers on their team, especially when it comes to bottling and canning products. Industry experts specializing in bottling and canning needs for breweries tout the equipment and technology to handle these tasks for operations of any size.
One of those experts is XpressFill Systems, a long-established player whose clients, the company says, know to expect cost-saving innovations from its products and solid customer service, particularly after the point of sale. California-based XpressFill was founded in 2007 and began with the idea of solving a dilemma for small-scale wineries stuck with trying to bottle their wines by hand. It continues to service the wine industry, which surrounds the company’s facilities in San Luis Obispo.
Today, XpressFill manufactures bottle- and can-filling systems in its San Luis Obispo plant, using top-quality components made exclusively in the United States. Its fillers come in several models, including volumetric, level fill and carbonated technology. With affordability, compact design and ease of use among its top priorities, the company continues forging ahead with new ideas to keep pace with customer needs in real-time.
line of filling products. Its weight-sensing technology is designed to ensure accurate fill volumes that will hit their mark every time. The importance of this precision, of course, is to avoid spills and underfills, which cost valuable production time and loss of product.
Rod Silver leads the company’s Sales and Marketing Division. He describes how the XFW200C is ideal for 12-ounce to 16-ounce cans. An industrial-grade touchscreen display allows the user to enter the desired weight and the technology installed keeps track of how much product fills the can. A larger flow path gives the user access to a smooth fill along with the flexibility of filling containers with almost any product of choice, including those with some level of particulates, such as flakes or small seeds. In addition to processing beer, kombucha, juice and RTD mixtures are among some of the other options.
Twin Monkeys Beverage Systems, based in Denver, Colorado, is the brainchild of Josh Van Riper and Brian LeFevre. Their attention-grabbing moniker, along with the duo’s business model of customer-focused design, has earned Twin Monkeys a global presence in the craft brewing industry, with customers throughout North and South America, Europe, Australia, Africa and Asia.
Both Van Riper and LeFevre have engineering backgrounds. They are focused on designing the kind of automated canning systems that didn’t exist when Van Riper was brewing craft beer.
“I started a brewery and quickly found there were not good options for buying automated canning machines for craft breweries then (2013),”Van Riper said. “I got Brian to come to the brewery to discuss this opportunity and we then started Twin Monkeys to make affordable, high-quality automated canning systems for packaging beverages. We’ve grown to a 30-person company in a 14,000-square-foot facility, and we have over 500 canning machines strewn around the planet. I’m an automation engineer who does mostly controls engineering and mechanical concepts. Brian is a mechanical engineer. Between the two of us, we can design automated equipment from the ground up.”
Twin Monkeys Brewing Systems offers a full
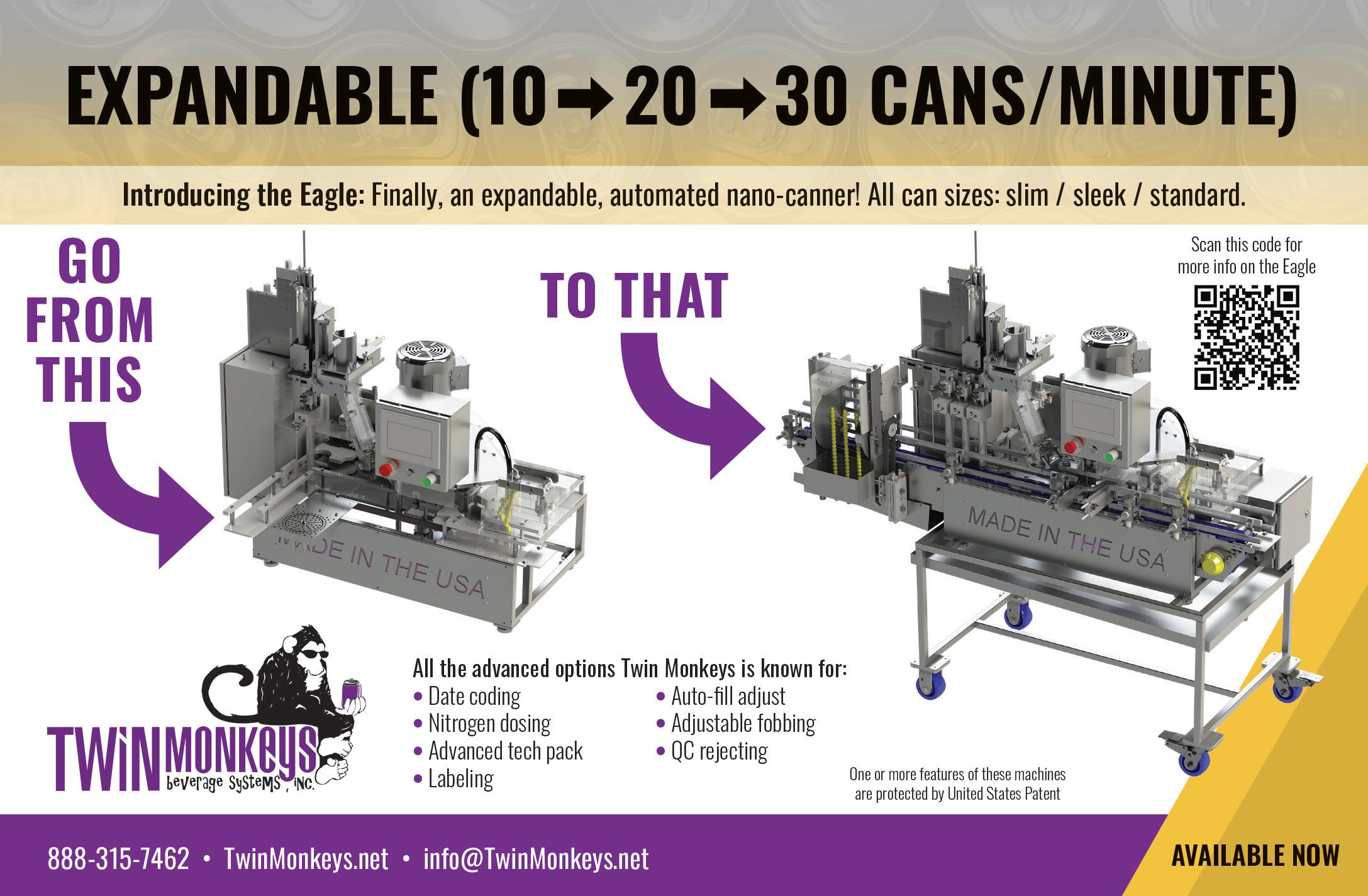

Photo Credit: Twin Monkeys Beverage Systems
range of can-fill-and-seam machines. The company offers craft brewers automation options that provide access to in-house, integrated canning lines equipped with three critical functions.
“We are singularly focused on canning machines that do three things: fill cans, put lids on cans and seal cans. We rely on other expert companies to do things like labeling, depalletization and brewing, and we want to just perfect the three things we do over and over. We’re also creating a new customer service paradigm to provide easier and more efficient access to our knowledge for our customers.”
Van Riper says that customer service extends to helping clients integrate their systems with a wide range of accessories.
“Although we only make canning machines, we consider ourselves to be systems integrators and that means we sell and support a wider range of equipment,” he said. “This provides more of a onestop-shop model for customers to lean on us for a variety of their equipment needs. We plant 50 trees for every machine we sell, and in 2021 we became carbon neutral. We do serious work, but don’t take ourselves too seriously.”
The process of canning and bottling craft beer also entails protecting the integrity of the product before it hits the market. That’s the role of Industrial Physics, which brands itself as the world’s leading test and inspection corporation. Armed with a global network of technical and support teams, the company’s 75-year history in quality control has guided the testing and inspection experience for some of the largest beverage corporations in the industry.
Industrial Physics has a presence in 75 countries, with manufacturing facilities in 13 locations. Through its vast portfolio of more than a dozen testing and inspection brands, including CMC-KUHNKE, Quality By Vision, Steinfurth, Eagle Vision and TQC Sheen, test and inspection solutions are deployed to ensure premium quality control for beverage packaging, materials and products. At the same time, the company assures clients of personalized solutions for their product needs.
Whether a small start-up or a global name in the brewing industry, Industrial Physics says its Testing and inspection solutions cater to every need and budget. Steve Davis, global product line director at industrial physics, has more than 20 years of engineering experience. He leads a team of experts who ensure that the equipment provided by Industrial Physics does its job.
“When you’re dealing with bottles, cans and metal packaging, you’ll need reliable inspection machines to ensure the quality of your drinks,” Davis said. “With Industrial Physics, you’ll improve the efficiency of your processes and improve your product, saving yourself time and money and, ultimately, you’ll keep your customers happier. Through our leading brands, including CMC KUHNKE, Quality by Vision and Eagle Vision Systems, we’ve helped thousands of beverage fillers and breweries to taste success.”

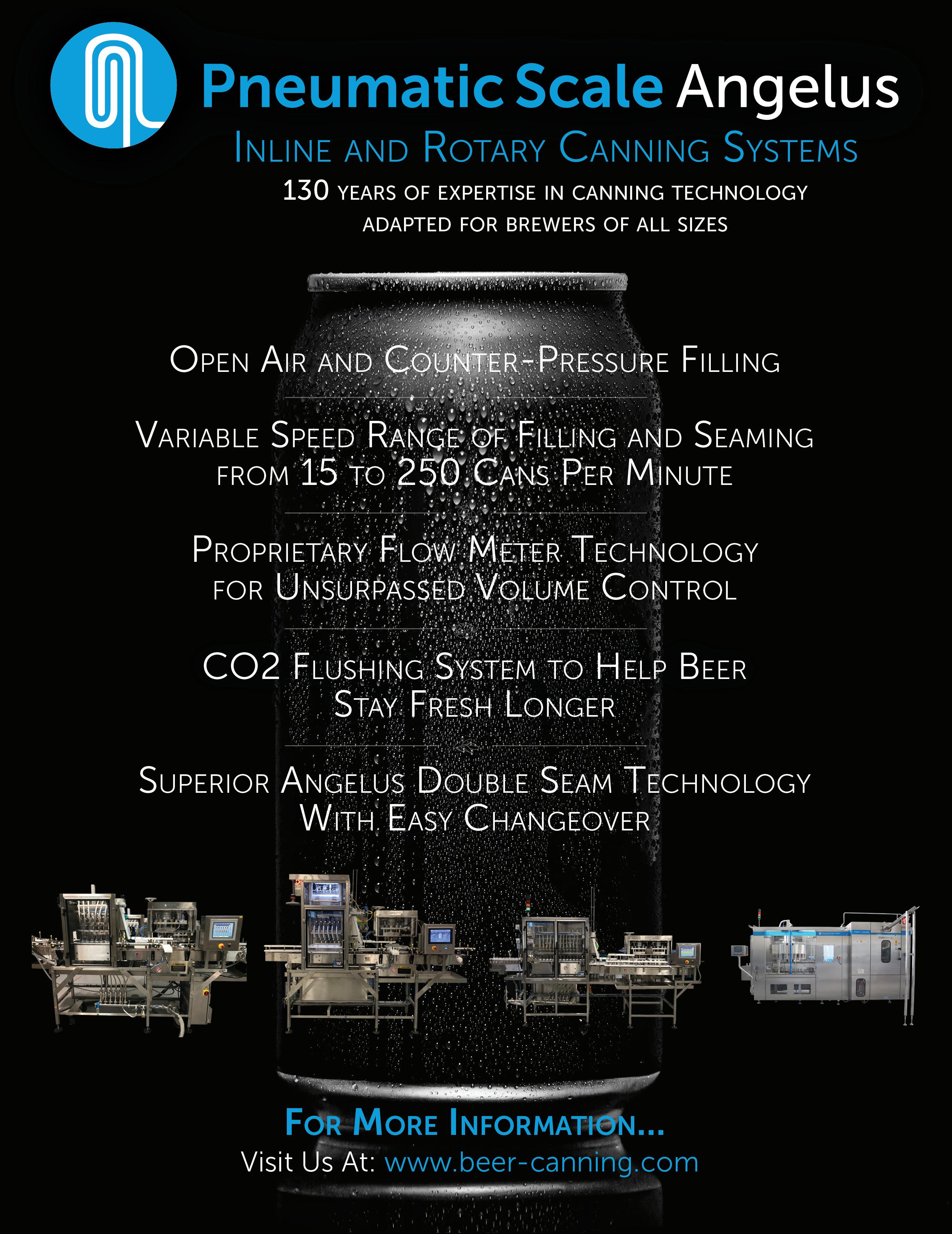
Davis went on to say, “From seam inspection and metal can testing to an inline inspection of empty and filled containers, our devices offer unmatched innovation and help you meet your quality needs. We protect the integrity of some of the biggest brands on the planet, as well as hundreds of emerging brands and everything in between. But how do we do this? By providing first-class test and inspection machines and products that check the quality of your packaging, materials and coatings.”
Davis provides an example. “Let’s take seam inspection. Our CMC-KUHNKE Auto XTS is a stateof-the-art, fully automated seam inspection solution. There’s nothing like it in the world, and it has the power to completely revolutionize seam solutions for your production line. We also have a wealth of smaller solutions to fit different needs and budgets.”
The company offers instruments designed to provide functions that include double seam inspection, non-destructive seam inspection, bottle, keg and can vision inspection, abrasion testing and headspace and dissolved oxygen testing. Customer service, Davis adds, is a priority at every point of the client experience.
“We understand that being fast, efficient and truly reliable is critical when it comes to servicing the instruments that keep your business running. And that’s why we’ve established a global network of dedicated service specialists to ensure you have an expert ready and waiting at a nearby location who can offer you support.
Wherever you are in the world, our experts are on hand to support your needs, whatever they may be. We know that having the right people ready to help is critical. It’s critical to delivering quality and speedy service that ensures your instruments can get up and running as quickly as possible. From installation to calibration, repair and preventative maintenance, we’ve got you covered.
We’re also passionate about being there for our customers in a more holistic way. We don’t just provide products. We’re there as a true partner. We have a wealth of solutions available across the beverage space, from metal packaging to bottles, our instruments test across an incredibly vast range of applications for many different manufacturing and laboratory needs.” Canning and bottling craft beer is a process that engages the expertise of filling, packaging and protecting products. Selecting the partner for one or more of these steps is not only based on budget but also depends upon which companies can accommodate the individualized needs of a craft brewery, no matter the size. Another important factor, experts say, is which company will stay with a brewery for the long run, ensuring that it can accommodate growth while not compromising on quality control.
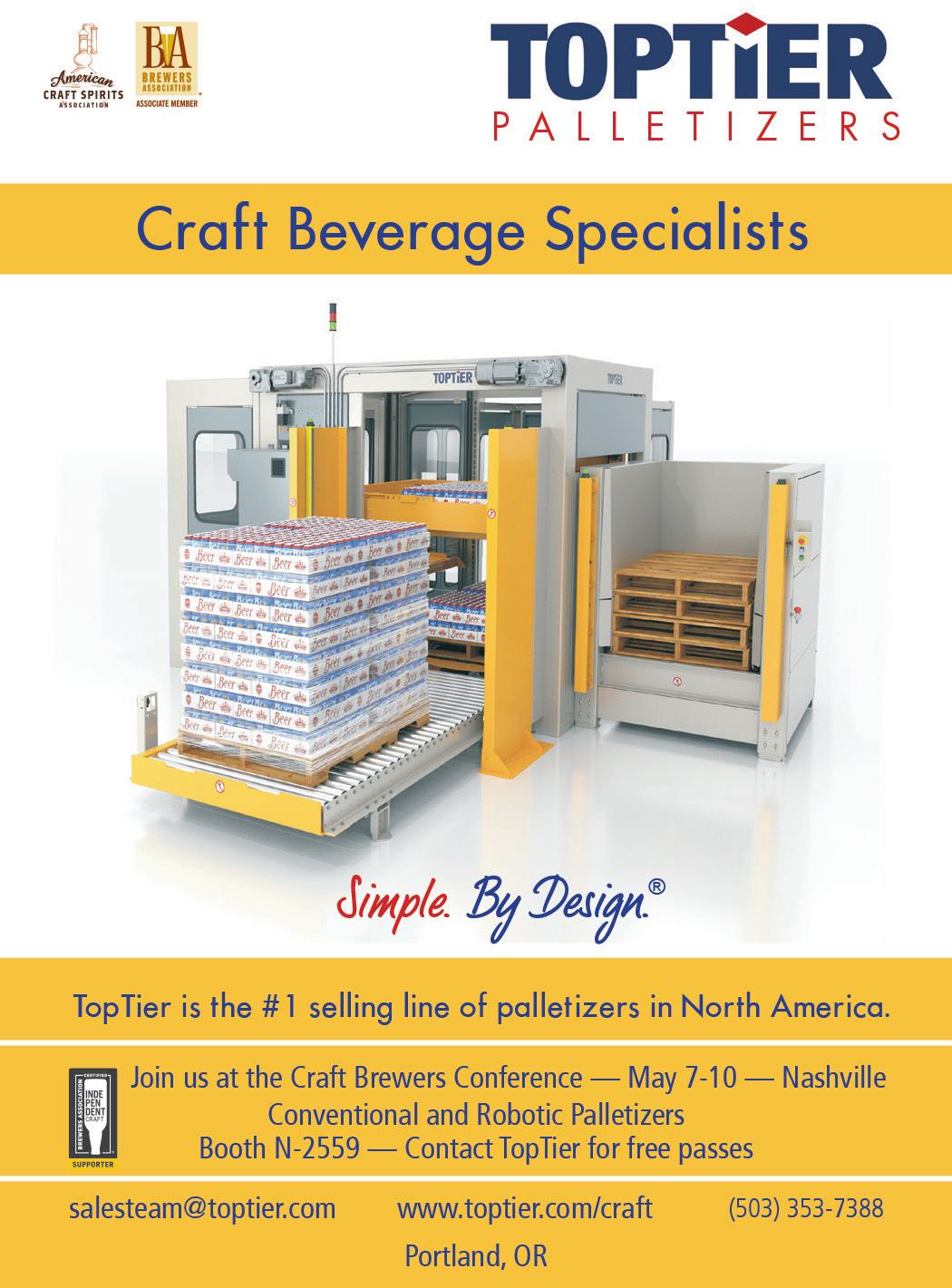
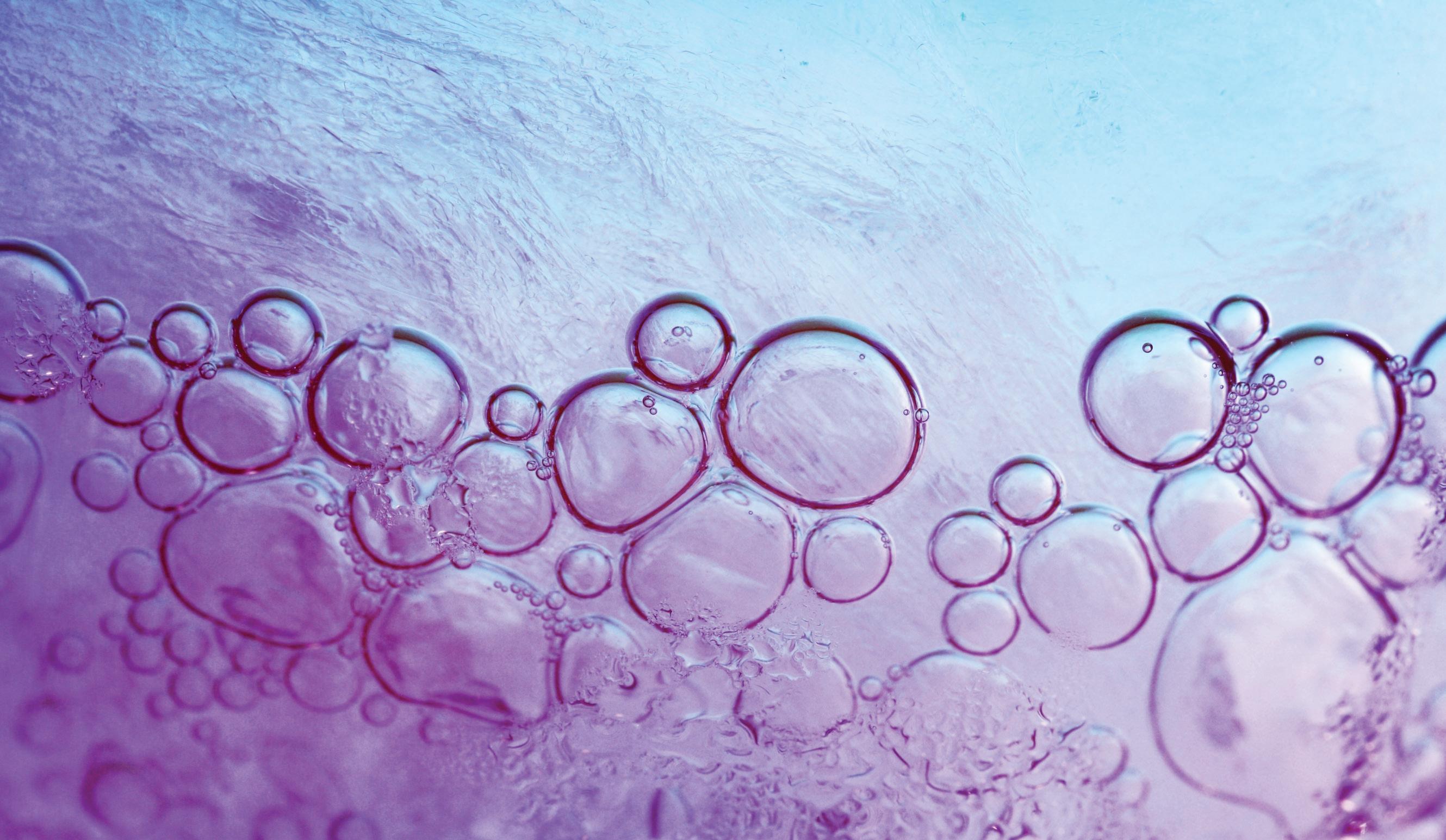
CO2 Struggles Breed Innovative Practices & Alternative Gas Use
By: Gerald Dlubala
Shortages, surcharges and sketchy availability: that’s not what any craft brewer, distiller or winemaker wants to hear about their supply stream. Yet that’s the reality that many brewers have been, and still are, living with after the pandemic played havoc with CO2 (carbon dioxide) availability.
The lack of regular, planned delivery and variable costs and surcharges of CO2 has brewers looking at ways to cut their costs or amount of usage of CO2, including replacing CO2 with nitrogen in some capacity. Nitrogen is readily available and an inert gas that does not typically react with its surroundings, so there’s no worry of adverse reactions with the brewed products.
Reducing and Replacing CO2 Use
Matt Malloy is the founder and CEO of Dorchester Brewing in Boston, Massachusetts, a contract partner brewery usually brewing for and partnering with 12 to 15 breweries at any given time. When facing a 75 percent reduction in planned CO2 deliveries from their supplier, Malloy knew it was time to look into new and alternative ways to keep his taphouse and brewery producing, especially as he is responsible for brewing beer for his partner breweries.
“We’ve long had a great relationship with our gas supplier,” said Malloy. “But this became a serious issue for us. We are a contract brewer for others, so production and quality are always our absolute priorities. We adhere to strict best practices with
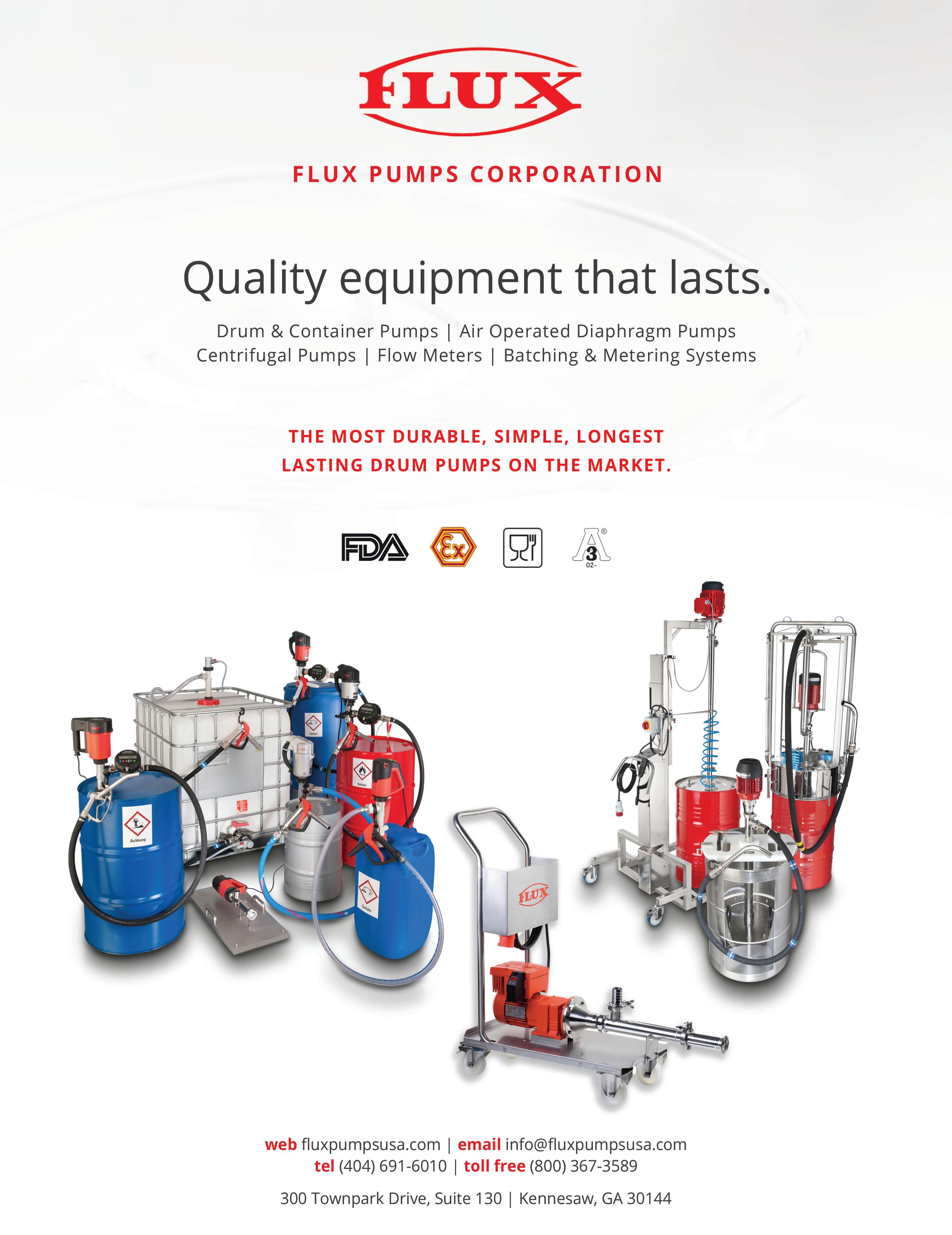
the required equipment for our industry and have to perform at a certain expected level. We have a bulk CO2 tank but couldn’t get the supplies necessary to keep us going, so we had to start looking at other options and even other suppliers than we had previously. We began by looking at where we use CO2 in our production. (Like other brewers, they found it in use virtually everywhere in their process.) We decided that the 25 percent supply we could get would go towards the most needed tasks. Then we would look for alternative solutions for other tasks that would cut the CO2 usage or, in some instances, replace the need for CO2 altogether with a better, more economical option. In our research and testing (Dorchester Brewing has a full-time quality control and testing lab), we found that we could initially replace CO2 with nitrogen in our canning, seaming and kegging operations. Additional notable savings came from using it to purge our two 60-bbl and one 120-bbl brite tanks. It was pretty much a one-for-one swap between CO2 and nitrogen. Our gas supplier helped with suggestions, and we were able to use our current piping systems by installing T-valves for switching use to liquid nitrogen supply, vaporizers and dewars when needed. We also found that cleaning under pressure used less gas than cleaning in place. All of these changes were made incrementally, using slow and steady testing to ensure that using nitrogen in place of CO2 did not compromise the quality of the beer in any one step of change.”
Malloy told Beverage Master Magazine that one very effective thing he and his brewers started doing is incorporating the German method of Spunding in their brewing process, using special valves attached to your tanks. Spunding literally means bunging, and the old German technique is making a comeback and something that Malloy says every craft brewer should at least try. It involves carefully monitoring the present gravity and sealing off the tank after the initial, aggressive fermentation stages have been completed. Once the wort ferments to near the targeted final gravity and orifices are closed off, you set the Spunding valve on the tank to your desired hold pressure setting. The valve’s attached gauge monitors PSI levels, and any levels above your set pressure tell the variable pressure relief valve to open automatically and release pressure down to the preset level when the valve will once again close. Spunding traps the naturally occurring CO2 created during fermentation so that it absorbs into the wort as it turns into beer. When done correctly, a brewer ends up with a perfectly carbonated beer ready for packaging and a decreased need for additional purchased CO2.
“Right from the start, we reduced our CO2 needs by 30 percent,” said Malloy. “Spunding saves us money, but I also believe it makes better beer. There is an increased sense of quality with better aroma components. We are making better beer, with less cost and more flexibility.”
Malloy encourages brewers to initially consider ways to save on and reduce CO2 usage before blindly transitioning everything to nitrogen.
“As brewers, we have to be super nimble and flexible in our thinking,” said Malloy. “Here at Dorchester Brewing, we’ve looked at and studied every step in our brewing and production process. As a result, we now see some of the duties that traditionally call for CO2 use, like purging and blowing down, as valid ways to use nitrogen instead and save money.”
Malloy says that Spunding, combined with an intense review of brewery practices, has gotten their facility down to a 50 percent reduction in the amount of CO2 they would typically require, but he’s not stopping there. He is currently testing nitrogen use in his can seamers and fillers. As a result, he expects to reduce his CO2 deliveries from once a week to once a month, resulting in even more savings.
Nitrogen offers a way to create your own gas supply or have a less costly bulk option. Onsite nitrogen generators provide nitrogen on demand and, depending on use, can pay for themselves in a short time, sometimes within the same year. Cryogenic bulk tanks offer an onsite nitrogen supply with fewer deliveries, and dewars are available for more minor production needs.
Innovation Leads to a Change in Philosophy and Brewery Practices
“Spunding and nitrogen use have changed how we approach brewing, but those practices have also built a new philosophy within our brewery,” said Malloy. “We are always looking to improve, and now we see a change in behavior within our team. We’ve changed cleaning protocols and team behav-
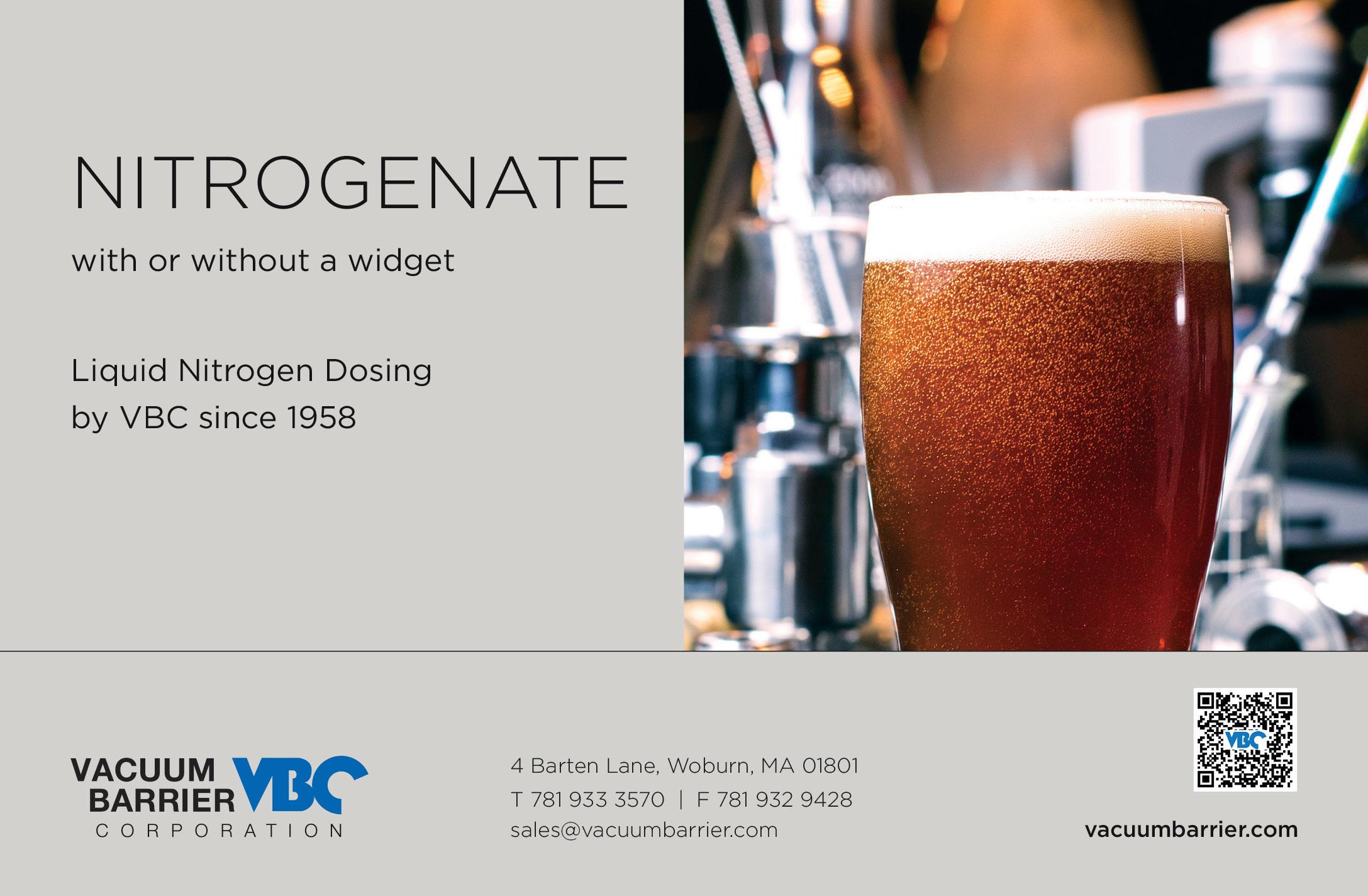
ior. Our team now sees value in every pound of gas used. Each pound used is sacred, and this type of thinking breeds innovation. We’ve used these protocols with all our brews, with no issues, differences or deficiencies noticed.”
Malloy says that these changes help production, but just as significantly, they also add up to reduced costs for brewers. The cost savings in buying bulk is significant, with some breweries paying up to eight times as much for supply as Dorchester Brewing.
“I would recommend that craft brewers first look at all of their production tasks in detail and, where applicable, incorporate the Spunding valves in their process,” said Malloy. “The upfront cost would be that of the valves, but the savings resulting from Spunding can be significant. Getting caught short can cause irreparable harm as a craft brewer, so you should also work with your gas supplier to investigate and research the possibilities of using nitrogen for as many practices as possible. It’s a win-win situation for both of you.” and is willing to discuss his experiences and help to show other craft brewers how they can start reducing costs through Spunding, nitrogen use or both in their brewery, pub or taproom. In addition, Dorchester Brewing offers free lid seaming checks and DO (dissolved oxygen) testing for area brewers.
Reusing Produced CO2 Through Carbon Capture: Earthly Labs
Due to the nature of the brewing process, breweries produce large amounts of CO2. With CO2 supplies being in such short and erratic supply, plus variable pricing structures, it may make sense for breweries to consider recapturing some of that produced CO2 for their use. Earthly Labs, a division of Chart Industries, is at the forefront of CO2 capture technology, manufacturing plug-and-play carbon capture units that enable a brewery start capturing and using their own produced CO2 within one day of installation.
The Earthly Labs CO2 capture technology is designed to capture CO2 waste from smaller sources that ultimately make up more than half of all CO2 emissions. For breweries specifically, this
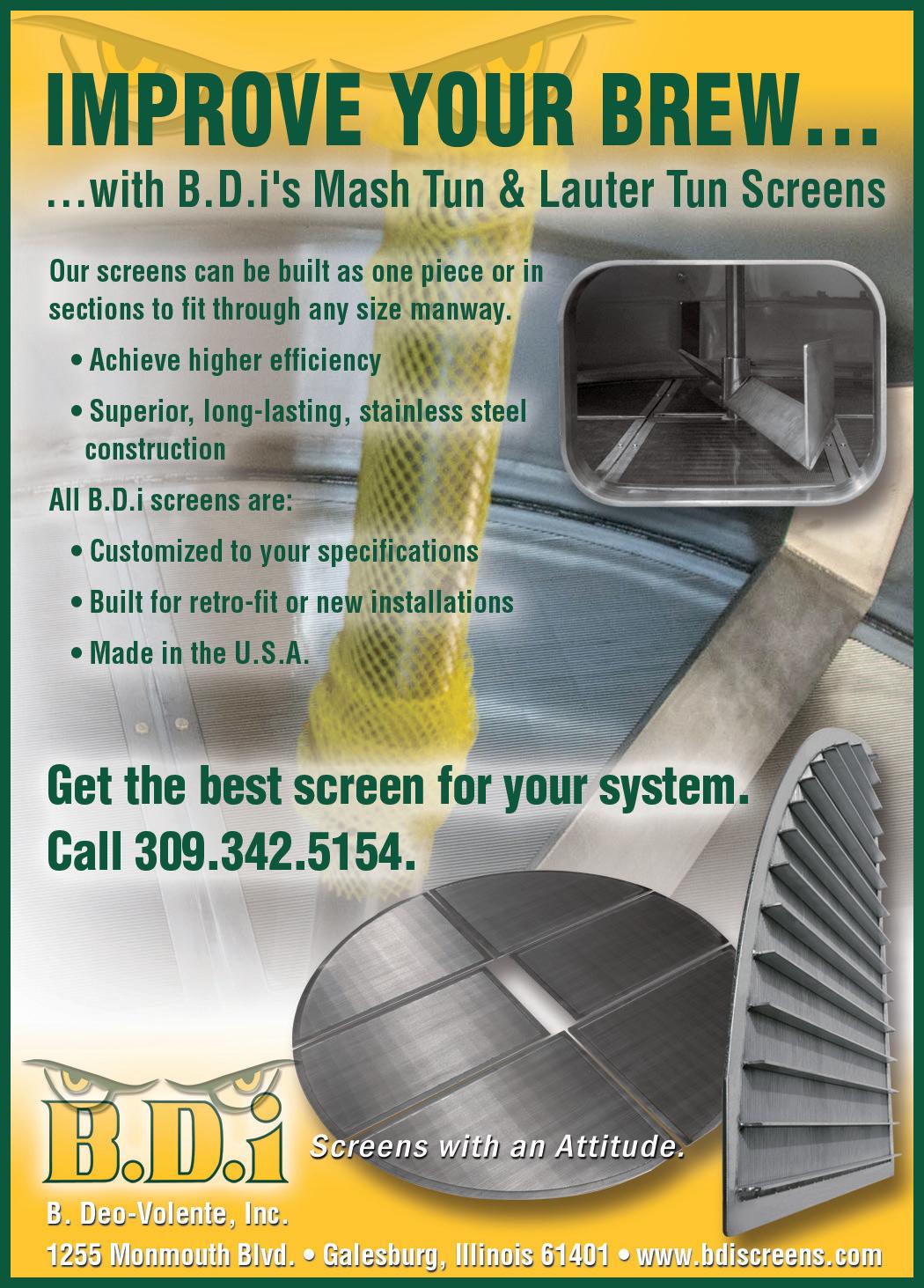
translates to allowing brewers to capture their own produced CO2 and subsequently purify it to foodgrade gas for reuse in the packaging and carbonating processes.
Using recaptured CO2 for your beer immediately allows a brewer to reduce CO2 purchases and the associated delivery fees and surcharges. Additionally, peace of mind comes with decreasing worries and making an environmentally conscious decision to increase sustainability. Earthly Labs compares the capture and reuse of CO2 to brewers or distillers disposing of spent grain because it is also a way to become more sustainable while also simultaneously benefitting your brewery’s bottom line.
Amy George, founder and CEO of Earthly Labs, says that while distilleries and wineries don’t have the amount of need that breweries have, they are also in the early stages of showing interest. Distilleries are continuously looking for ways to reduce their carbon footprint, with some having plans featuring net zero carbon futures. Wineries are also exploring ways to capture and reuse CO2 onsite to help with tank purging or carbonation needs for specific products. George says that their CO2 capture units are about the size of a double-door refrigerator and can be running and capturing gas the next day after installation if the brewery is producing gas. Training is straightforward, taking one to two days. After that, the brewery employees will be fully able to use the system under the oversight of the Earthly Labs team. Additional support is always available, including the possibility of remote monitoring. Return on investment timetables varies by producer, based on the amount of gas captured versus what a craft producer would have to pay for supply, surcharges, frequency of delivery, and more. As the price of CO2 rises, the return-on-investment timeline shortens, but on average, the client can expect the units to pay for themselves within two to three years.
Earthly Lab’s units are currently in use by breweries and craft producers of all sizes, but George says that the sweet spot for their workhorse unit, the CiCi ® (Oak), is for producers in the 5,000 to 20,000 bbl range. They can accommodate smaller producers with their CiCi ® (Teak) units, and larger producers will benefit from their CiCi ® (Elm) units.
George believes the complex, ongoing supply and delivery conditions will ultimately lead breweries to explore ways to remain viable and become more efficient in their operations. This includes capturing the CO2 waste for reuse that would typically be released into the environment and looking at replacement alternatives for CO2 within production operations.
Earthly Labs works to accommodate all producers, including offering a winery leasing program to provide flexibility during harvest seasons and to help eliminate the upfront expenditure by spreading payments into more manageable monthly programs. Additionally, the recently passed Inflation Reduction Act also allows for tax credits for these types of purchases.
Chart Industries CO2 storage solutions and partner networks offer opportunities to turn waste streams into value for businesses while reducing environmental impact. Chart also partners with buyers and distributors to help sell excess CO2 to other partners in the exchange ecosystem. The ultimate goal is to reduce as many emissions as possible to help achieve overall climate goals.
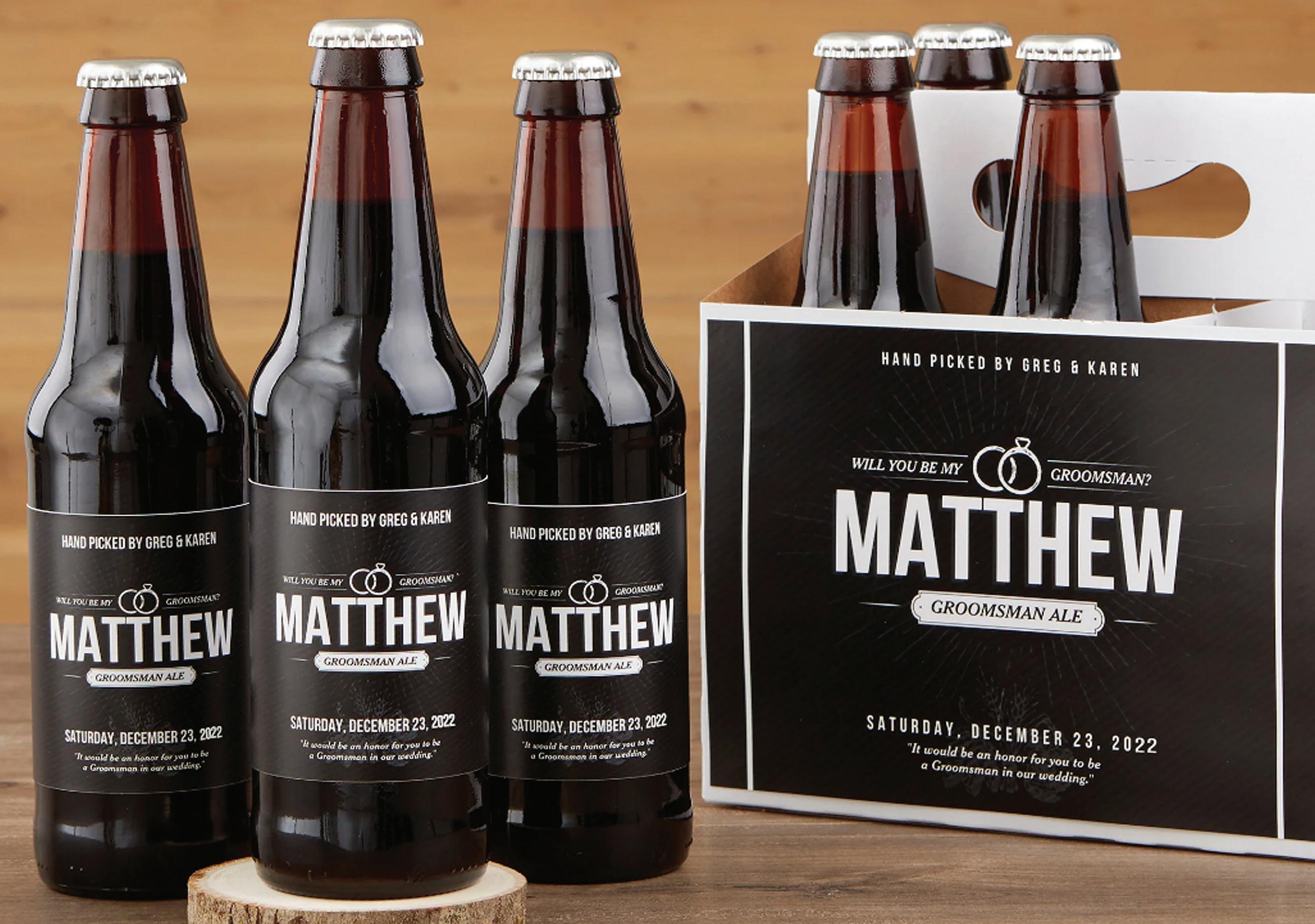
Customizing Beverages
the Easy Way By: Angelo Coletta, CEO - Zakeke
Enabling customers to customize their purchases is a quick and easy way to expand into new markets and boost profits. Some distilleries and craft brewers are beginning to take advantage of this innovative approach to scale their businesses. For example, Silent Pool Distillers increased their orders fivefold in 2020 in part with the help of product customization.
Possibilities abound for other distillers and craft brewers to do the same. Moreover, it’s easier to enable customization than most business owners think. Today’s product customizers offer automated processes that reduce the required amount of attention and manual labor to little or nothing.
What is Product Customization?
Product customization allows customers to change the visual appearance of products according to their own individual needs and desires. Sellers empower consumers to build their own unique products, perhaps by adding their names or those of others. Depending on the specific product and
customization service, customers may also be able to add photographs or longer messages of their own writing. In a sense, the product becomes a canvas for them to create upon.
Some of the beer, wine, and spirits industry’s biggest names allow their bottles to be customized, offering proof of concept. Tito’s Vodka and Hennessy VS Cognac bottles can be etched, and a large selection of bottles can be engraved, including Don Julio tequila, Woodford Reserve bourbon, and Dom Perignon champagne. Other makers, such as Maker’s Mark, Jameson, and Jack Daniel’s, offer bespoke labels. Silent Pool Distillers does this for four of their distinctive gins.
A wide range of items can be customized, including purses, jewelry, keychains, apparel, towels, and bedding. There are even services that customize things you wouldn’t expect, like USB drives, coffee sleeves, drinking straws, bobbleheads, and — believe it or not — cookies or cakes.
Why Enable Product Customization
The answer is simple: product customization improves the bottom line. According to a 2019 Tech Clarity survey of 285 companies that offer customization, 71 percent listed increased sales as one of its benefits. More than 50 percent pointed to differentiation and higher margins. Thirty-five percent nodded toward customization’s “cool factor,” and 34 percent said they experienced higher close rates. Forty-two percent indicated that offering customization had become a necessity in their industry to stay competitive.
Product customization elevates profitability for a number of reasons. First, customers are willing to pay more for customized products. According to Bain & Company, they will reach into their wallets to the tune of 20 percent more than the uncustomized version. This means manufacturers who customize can set higher prices. Meanwhile, they don’t incur new costs, since automated processes minimize the work required. While customers may only purchase a single customized item or a small lot, these sales are a painless way for the business to expand, and they do add up.
Secondly, product customization encourages customer loyalty. The same Bain & Company report also found that, “customers who had customized a product online engaged more with the company. They visited its website more frequently, stayed on the page longer and were more loyal to the brand.”
Happy customers can result in repeat business and referrals to their friends and family. The ability to customize sets a business apart, distinguishing it from competitors in the eyes of consumers.
If that wasn’t already enough, Bain reported lower rates of return for customized products than for their mass-produced counterparts. When customers take ownership of the look and feel of their purchase, they tend to be more satisfied with the outcome and less likely to change their minds.
All of this adds up to increased sales and a better business.
Why Customers Love Customization
Customization appeals to customers for many reasons. Part of the draw is that it makes customers feel special. They are willing to invest their time and effort into creating a unique product that is tailored to their own tastes and exacting requirements. Since they are the ones who determine what the final product looks like, it is sure to please them.
Another reason is that customization provides customers with a sense of control, that all-too-scarce commodity in today’s hectic, stressful, and sometimes overwhelming world. They are in the driver’s

seat throughout the process. This is one element of their lives that they can impose their will upon and be confident of receiving gratification.
It can also be just plain fun. For instance, Silent Pool Distillery’s user-friendly website steps prospective customers through the creation process. After clicking on the option to personalize their gin, they are taken to a new web page with four varieties that may be customized: Original Juniper, English Garden, Fresh Grapefruit, and Spiced Pepper. When customers click on the name of the flavor they want to purchase, a new page comes up with the product’s specifications.
Beneath the “Add to Cart” button, a “Customize” option takes customers to an interactive interface where they design their bottle’s label. A large button with an upward-pointing arrow invites them to upload photographs of themselves, their loved ones, pets, or places special to them. Alternatively, they may choose from a library of 140 million stock photos arranged by helpful categories like “Business & Finance,” “Sport & Extreme,” or “Travel and Vacations.”
Next to the upload arrow is a button that allows clients to add text to the label, giving it a special name or writing warm messages to recipients. Customers can change the font size, make the text bold, position it anywhere from top to bottom, center the words, or align them to the left or right. They can even bend the letters along a curve of their own making. Magnifying glass icons allow them to zoom in to view fine details or zoom out to gauge the overall look.
If a given component starts to mess up the label, then the customer can delete it. If the whole design ends up being a disaster, they can reset the label with the click of a button and start over.
The result is a unique, bespoke bottle of high-quality, sustainable gin that’s perfect for gift-giving on birthdays, anniversaries, and holidays, as well as for celebrations, bachelor and bachelorette parties, showers, and weddings.
Throughout the process, customers delight in the knowledge that they are putting together a one-ofa-kind present. Surprise is guaranteed: No matter how hard the recipient might try to guess what’s coming, they will never be able to guess what this
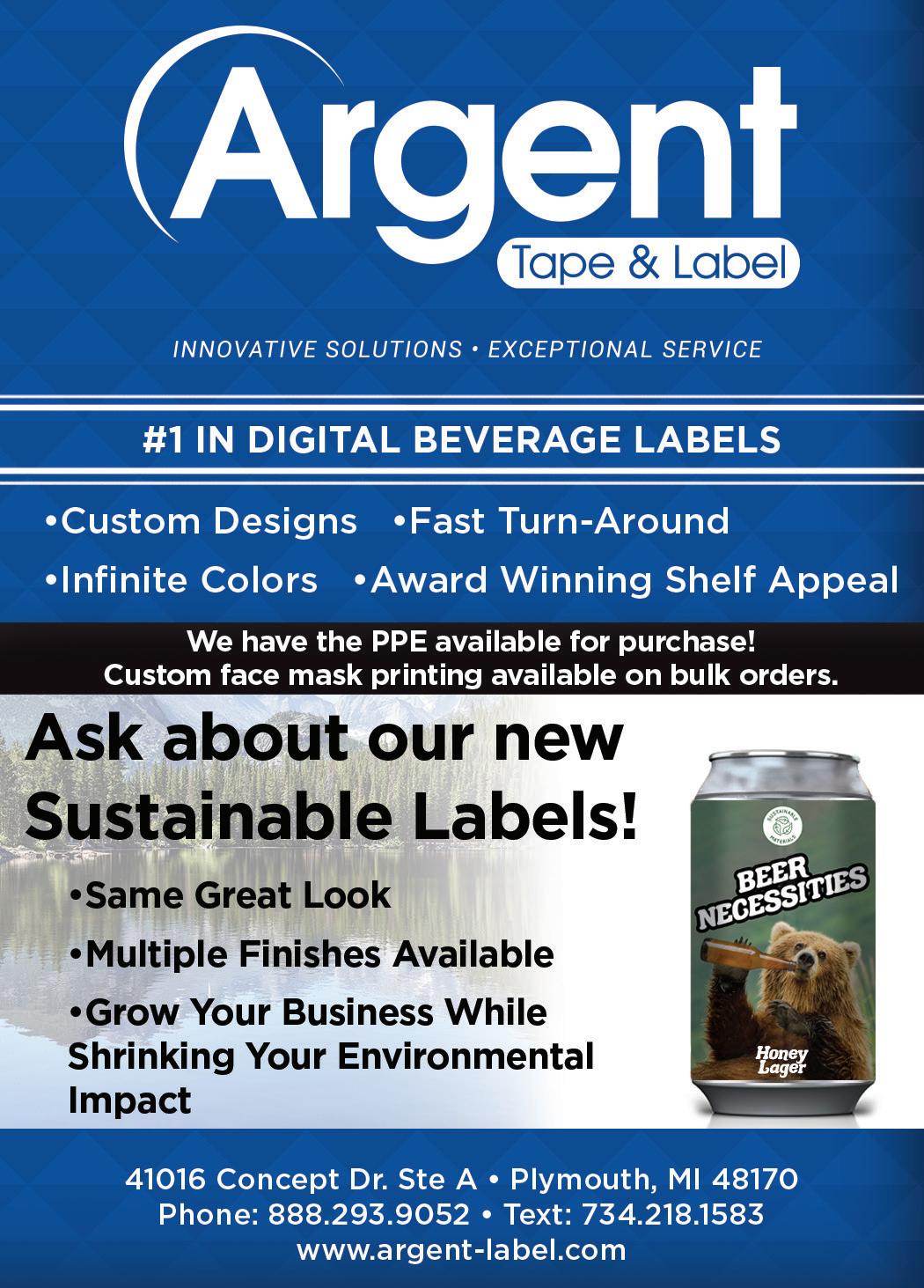
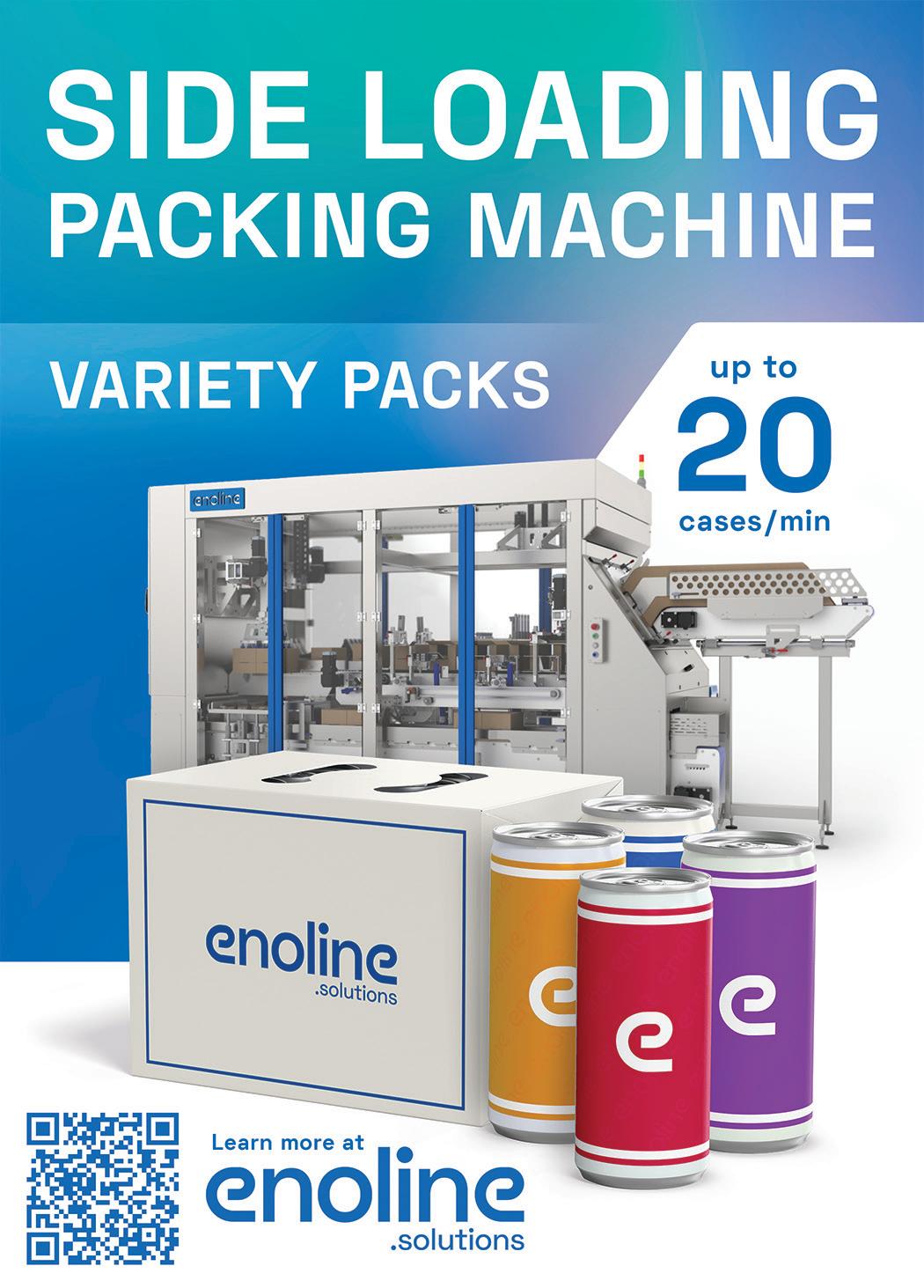
gift is going to look like. Connection also seems assured — people tend to react positively to seeing their own name on an item, which often translates to feeling good about the person who gave it to them.
No Hassle Customization for Sellers
Savvy distillers and craft brewers are understandably wary about adding a new feature to their already complex businesses. The last thing sellers want is to labor over a single item. Luckily, those days are over. Today’s customization services integrate with business’s existing websites and simplify the customization process itself.
Take the case of Silent Pool Distillers. The distillery got their start offline, producing artisanal spirits with local ingredients in the Surrey Hills Area of Outstanding Natural Beauty, a nationally protected landscape in the United Kingdom. To take advantage of online sales, they built an online storefront on the e-commerce platform BigCommerce. Thus, the distillery was well positioned when the COVID19 pandemic hit, closing pubs and restaurants in droves. The spurt in online shopping boosted their sales to new levels.
When the business sought a way to start customizing their products, they wanted a service that would integrate with BigCommerce and not force them to reinvent their online shop. They chose Zakeke, a visual commerce platform that works seamlessly with not only BigCommerce, but also many other ecommerce platforms, including Shopify, Etsy, Wix and WooCommerce. It can also employ an application programming interface (API) for integration if needed.
Silent Pool Distillers installed Zakeke’s software and configured its easy-to-use “plug and play” system. In the context of information technology, “plug and play” means software that does not require users to understand programming or make any adjustments. Instead, it is designed to work well immediately from the moment it is brought to life.
After this initial setup, the distillery’s preexisting online shop gave customers access to Zakeke’s cloud-based platform for designing their own labels for certain products. Since the process is automated, this personalization happens without requiring attention from the seller. Once an order is placed, all employees at Silent Pool Distillers need to do is download the customer’s file, print it out, and attach it to an appropriate bottle.
By equipping the Silent Pool Distillery to offer bespoke labels on their bottles, Zakeke boosted their sales while allowing the distillers to remain focused on what they do best: making high-quality spirits.

The Power of Personalization
Today’s customers increasingly expect the ability to personalize their products. A 2020 report by Dassault Systèmes and CITE Research found that 83 percent of consumers “expect products or services to adapt [to their individual specifications] in a matter of moments or hours.”
The future belongs to businesses who can meet this challenge. Local distilleries and craft breweries stand to gain by incorporating customization, just like the big names in the industry. Branching out in this direction enabled Silent Pool Distillers to capture a valuable new market segment and increase sales even during the dark days of the pandemic.
The power of personalization helps retailers please long-standing customers and attract new ones. That’s why distilleries and craft brewers of all kinds should consider adding product customization.