

KEEP IT SAFE
OCTOBER/DECEMBER 2024
Foreword
The British Frozen Food Federation (BFFF) Health & Safety Expert Group met for its final meeting of 2024. In attendance were representatives from BFFF member companies including Asda, Sysco, Bidfood, Morrison’s, Nomad Foods, Holdsworth Foods, StoreLogs, FareShare, Heron Foods and QK Coldstores.
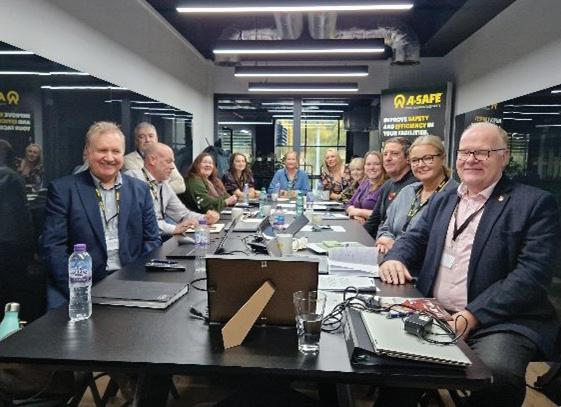
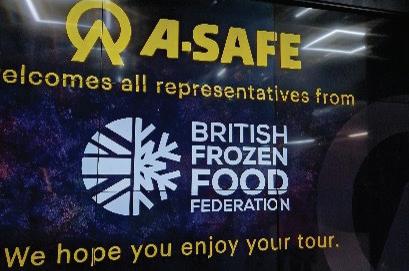
Topics to discuss were:
• Member updates,
• Review of on -18°C,
• Non-integrated forklift platforms/cages
• Food and drink manufacture forum update
• Fire water management,
• Counterline ovens
• Rest breaks for Coldstore Workers
• Managing contractors,
• Primary Authority Update
• Dock Levellers
• H&S Software
Our guest speakers was Ray Barnett from A-Safe barriers who took the group through the importance of separating pedestrians and workplace transport. In addition, we were supplied the latest version of PAS13 the recognised standard for barriers.
We all gained some continuous professional development (CPD) and witnessed at first-hand the technology A.I and robotics which is used to turn polymer beads into industrial lifesaving memory barriers.
We would like to thank A-Safe for being the perfect hosts and allowing us to use their futuristic facilities in Elland. Thanks to all our members that dedicated their valuable time to be part of this group.
To find out more about the work carried out by the BFFF Health & Safety group please contact: simonbrentnall@bfff.co.uk
BFFF INITITIVES
Bfff Supports The Food And Drink Manufacture Forum And Aligns Its Members To The Strategy Through Its Health & Safety Pledge
Bfff And Its Members Support Iosh Food & Drink Manufacture Industries Group/ Food & Drink Manufacture Forum Annual Conference
Call To Membership, We Need Your Data For Last Year 2023!
FIRE SAFETY
Essex County Fire & Rescue Services.
Impact Of Fires In The British Frozen Food Industry
Rising Incidents of Fires
Statistics from the Past Five Years
Causes and Contributing Factors
Impact on Businesses
Response and Mitigation Measures
Regulatory and Industry Standards
Midland Chilled Foods warehouse –Willenhall West Midlands
Conclusion
MEMBER FOCUS
Forklift Training- Understanding Accreditation To Ensure You’re Meeting Standards
What Is Accredited Forklift Training?
Understanding The Terminology
Added Value Is Found In Assurance And Quality
Challenging 3 Common Myths About Ppt Safety
Know Your Numbers & Keys To A Healthier Life
ENFORCEMENT
Farm Owner Fined After Fatal Fall
Company Fined After Worker Loses Finger
Routine Hse Inspection Results In £150,000 Fine For Food Manufacturer
GUIDANCE
Guidance On In-Service Examination And Testing Procedures Of Local Exhaust
Ventilation (Lev)
The House Of Commons Discusses ZeroHours Contracts, According To Cipd And Ons Research, People Are Most Likely To Work In The Accommodation And Food Sector
Legal Issues Statistics
Policy Debate And Possible Reform
Martyn’s Law Update – Second Reading 14th October
Government Launch New Workplace Health Check Programme
Bfff Has Previously Raised Awareness Of Modern Slavery With Its Members, Now Hundreds Of Rogue Employers Are Targeted In Illegal Working Crackdown
Hse Remind Employers Of Stress Legal Duty
Health And Safety At Work Etc. Act 1974 (Amendment) Bill 2024-25
BFFF INITITIVES
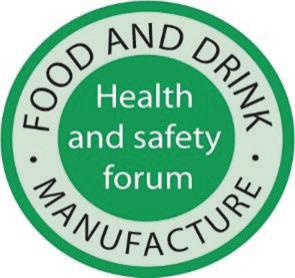
BFFF SUPPORTS THE FOOD AND DRINK MANUFACTURE FORUM AND ALIGNS ITS MEMBERS TO THE STRATEGY THROUGH ITS HEALTH & SAFETY PLEDGE
Food And Drink Manufacture Forum (Fdmf)
Recently Simon Brentnall (Head of Health & Safety) at BFFF attended the Food and Drink Manufacture Forum (FDMF), the group meets 3 times per year. In this meeting the HSE discussed their inspection plan which is multi-year and focusing on health reduction within the industry, this includes manual handling, noise, health surveillance and a duty to manage. We had a presentation from an HSE expert on noise, this outlined how research is now linking high level of workplace noise to other health conditions such dementia, heart disease and stress. Statistics show the second highest industry responsible for noise induced hearing loss is the food and drink industry. The HSE reminded everyone of HSG232 – Sound solutions for the food and drink industry, this guidance gives 60 case studies on noise together with solutions.
The Food and Drink Manufacture Forum (FDMF) is a partnership between Trade Associations, Trade Unions and the HSE. This voluntary strategy demonstrates FDMF members’ clear intent to act together, build upon previous achievements (such as the Recipe for Safety initiative) and to improve the health and safety (H&S) performance of the food and drink manufacturing industry. This forward-looking strategy demonstrates commitment from the food and drink manufacturing industry to the wider national H&S system strategy Protecting People and Places.
In order to protect people and places, central to this strategy is sensible and proportionate risk management which supports and enables business productivity and innovation. The strategy has a particular focus on tackling work-related ill-health. Actions on sharing success and supporting small employers are set out in the strategy. Delivery of the strategy will only be effective through industry leadership (from directors and all other levels within organisations, and by representative organisations) coupled with effective worker engagement.
Continued...
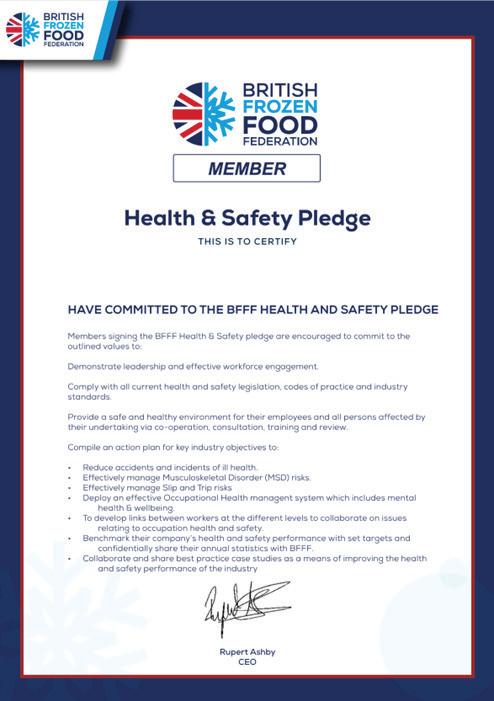
THE BFFF HEALTH & SAFETY PLEDGE
The BFFF Health & Safety Pledge aligns itself to the above strategy and our members can play their part by requesting a certificate which indicates the company are committed to these values.
To register your commitment to these values and receive a certificate to display in your premises, please contact: simonbrentnall@bfff.co.uk
BFFF INITITIVES
BFFF AND ITS MEMBERS SUPPORT IOSH FOOD & DRINK MANUFACTURE INDUSTRIES GROUP/FOOD & DRINK MANUFACTURE FORUM ANNUAL CONFERENCE
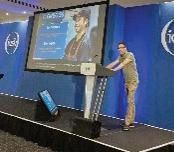
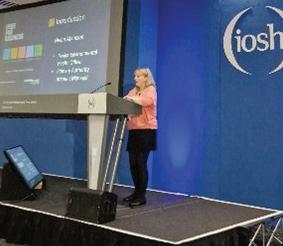
For the last 12 months BFFF continues to support both the IOSH Food and Drink Industry Group and the Food and Drink Manufacture forum. The pinnacle of this work is the annual H&S conference which took place this week. This year’s conference, entitled ‘Leading the Mix’ was held in Coventry with over 100 in attendance. The event celebrated health and safety excellence and started with an award ceremony.
We are delighted to announce that BFFF members Sysco won the runner up award for best innovation for health & safety, the award and collected by Tom Smith (Regional Health & Safety Manager). This award recognises the artificial intelligence adopted in their HGV fleet, this technology acts as the conduit in retraining their drivers and ultimately leading to better driving thus protecting the driver, third parties and the company. The benefits for Sysco have been massive including:
• Improvement of distractions such as mobile phone reduced by 40% in first 6 months,
• Reduction of on the road incidents equates to a 40% reduction in the first 3 months of inception,
• Reduction of 17% in harsh driving events,
• All insured costs down by 15%,
• Reduction in civil claims equate to since to a 10%,
• Drivers now logging performance scores of over 90%,
• Driver prosecutions in a single depot in last 6 months has reduced from an average of 6 down to 0.
We had a jam packed day with key insights from all the speakers including BFFF Members Greggs, Paul IrwinRhodes (Head of Sustainability Health & Safety) Paul talked
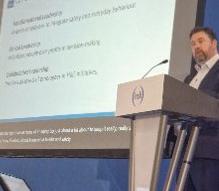
us through effective multifunctional practical leadership within their business.
BFFF’s own primary authority Helen Atkinson Senior EHO for Wakefield Council explained to the audience the benefits of being part of a scheme and having a single enforcing authority. We hope you support us in thanking all our speakers. sponsors and exhibitors. BFFF were proud to be involved in organising such a prestigious event with quality speakers who covered the following topics during the day:
• Insights into driving health and safety improvementPaul Irwin-Rhodes – Greggs,
• HSE update - David Butter,
• How well are you managing your machine safetyDominic Baraclough & Richard Bowen - Finch
• Accident reduction innovations - Allied Bakeries | part of Associated British Foods plc - Award winner
• Enhancing health and safety through culture excellence - Phoebe Smith, - Primary Authority and the benefits - Helen Atkinson & Chris Green,
• Managing a chemical incident - Kate Joy, - Root cause analysis - Peter Jenkins & James MacPherson,
• The presence of safety - Finlays award winner (Driving excellence in OSH),
• Reflecting on health and safety leadership and followership - Shaun Lundy,
• Legal update - Chris Green,
Delegates left the day with some key takeaways which will support the wider food and drink industry ensuring a safer, healthier workplace for all. To find out more about the H&S services provided by BFFF, please contact simonbrentnall@bfff.co.uk
Pictured above, left to right - Paul Rhodes, Greggs, Helen Atikinson, Wakefield Council, Dr Shaun Lundy, Tetra
BFFF INITITIVES
CALL TO MEMBERSHIP, WE NEED YOUR DATA FOR LAST YEAR 2023!
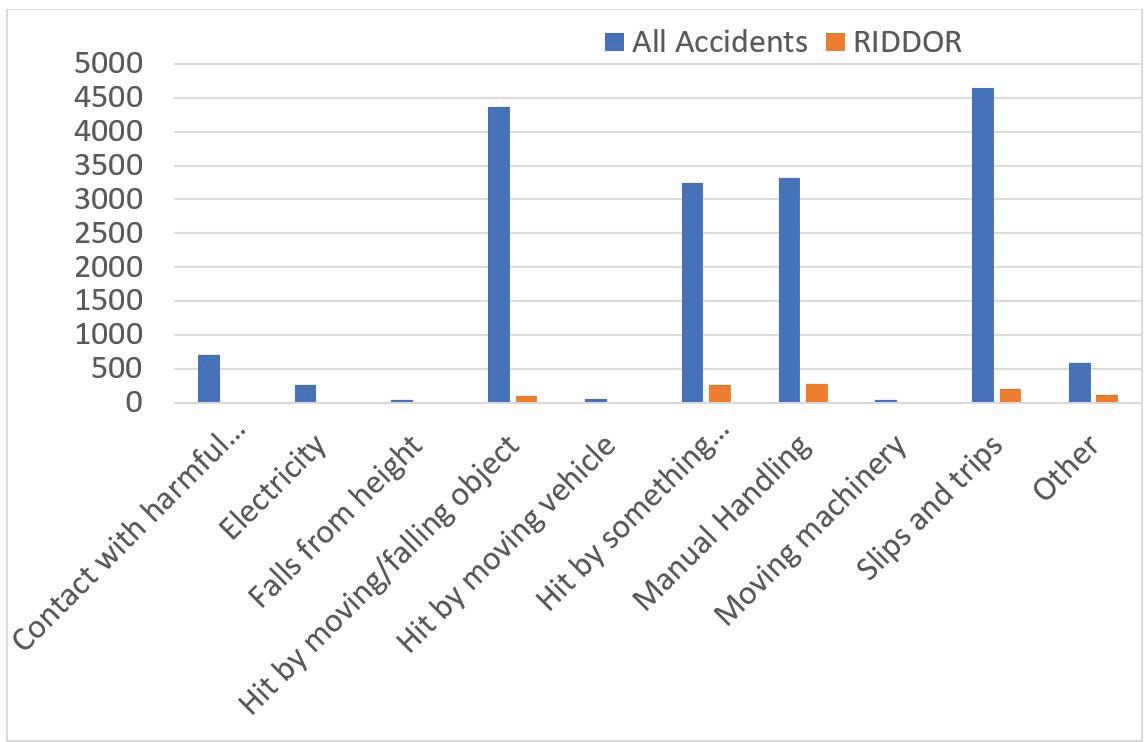
Again we encourage our members to submit their accident data from the previous year. Once collated this data provides a crucial management tool to enable member companies to benchmark their current OSH performance against that of the BFFF members in the same sector.
Your data is processed confidentially and anonymous in the final report. For 2022, the data reported from our membership represented 37,584 employees. We now need you to submit your 2023 data, it only takes 5 minutes, please visit our website at:
Page Statistics — British Frozen Food Federation (BFFF)
Should you experience any difficulties in submitting your data please contact: simonbrentnall@bfff.co.uk
FIRE SAFETY
ESSEX COUNTY FIRE & RESCUE SERVICES.
Impact of fires in the British Frozen Food Industry
In recent years, the British frozen food industry has grappled with a concerning rise in fires, posing significant threats to both businesses and safety. The nature of materials used in cold storage means that it presents a higher risk when it comes to fire and as the demand for refrigerated products increases so the need for improved levels of fire safety. This article delves into the incidents, statistics, and consequences faced by the industry over the past five years.
Rising Incidents of Fires
The number of fires in the British frozen food sector has seen a marked increase, with several high-profile incidents capturing public attention. From small-scale outbreaks to large infernos, these fires have not only disrupted operations but also highlighted vulnerabilities within the industry.
Statistics from the Past Five Years
An analysis of data from various sources, including the Fire and Rescue Services and industry reports, reveals a worrying trend. Below are the keystatistics:
• 2019: There were 15 recorded incidents involving fires in frozen food facilities, resulting in approximately £10 million in damages.
• 2020: The number of fires rose to 20, with damages escalating to around £15 million. This year also saw an increase in insurance claims related to fire incidents.
• 2021: Fires peaked with 25 incidents, causing damages estimated at £25 million. Notably, a major fire in a prominent frozen food warehouse led to substantial product losses and operational halts.
• 2022: There was a slight decline with 18 fires reported, but the damages remained high at approximately £20 million. Enhanced fire safety measures were introduced in response to the previous year’s surge.
• 2023: Preliminary data up to September indicates 12 fires, with an estimated £12
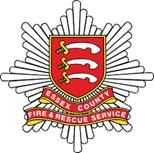
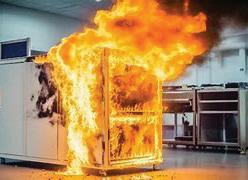
million in damages. Efforts to improve fire prevention and response have shown some effectiveness.
According to research conducted by Hochiki indicates the ‘preventable fires in the UK warehouse industry cost the UK economy upwards of £230 billion each year.
(Statistics and data sourced through Google search)
Causes and Contributing Factors
The primary causes of these fires have been traced to several factors. Equipment malfunctions, particularly in refrigeration units, have been a leading cause. The complex machinery essential to maintaining low temperatures is prone to faults that can spark fires. Additionally, electrical issues and human error, such as mishandling of equipment or flammable materials, have contributed to the frequency of these incidents.
The growing trend in electrical vehicles and other lithiumion powered technology is also increasing the likelihood of fires as it emerges with much higher-than-average damage caused with fire involving Lit-ion batteries.
Impact on Businesses
The repercussions of these fires extend beyond immediate financial losses. Businesses face significant operational disruptions, with production halts and supply chain interruptions leading to potential market shortages. The reputational damage can also be severe, as companies struggle to regain consumer trust following such incidents. Insurance premiums have seen an uptick, reflecting the increased risk associated with the industry. Damage to stock can be widespread both through direct involvement in the fire, as a result of plant shutting down causing
BFFF INITITIVES
temperatures to increase and smoke damage into areas beyond the seat of the fire itself. The risk of prosecution is another serious consideration where the prevailing circumstances causing fires, as well as the management of the emergency, are as a result of insufficient fire safety management and governance.
Response and Mitigation Measures
In response to the rising trend of fires, the frozen food industry has implemented several strategies aimed at mitigating risk and enhancing safety protocols.
These measures include:
• Enhanced Fire Safety Training: Regular training sessions for staff on fire prevention, response procedures, and the proper handling of equipment.
• Upgraded Equipment: Investment in modern, fireresistant machinery and regular maintenance to prevent equipment-related fires.
• Fire Suppression Systems: Installation of advanced fire suppression systems, including sprinklers and chemical fire suppressants, in storage and production areas.
• Comprehensive Risk Assessments: Conducting thorough risk assessments to identify potential fire hazards and developing strategies to mitigate them.
• Ensuring the competence of staff, and external contractors, tasked to manage fire safety at all levels
Regulatory and Industry Standards
Regulatory bodies have also stepped in to enforce stricter compliance with fire safety standards. The British Retail Consortium (BRC) has updated its Global Standard for Food Safety to include more rigorous fire prevention and control measures. Regular audits and inspections ensure that frozen food facilities adhere to these standards, reducing the likelihood of fire outbreaks. Regulatory partnership arrangements through Fire and Rescue Primary Authority can also provide expertise and support in the business fire safety governance and can be accessed directly or through membership with the British Frozen Food Federation (BFFF).
Case Study Example
Several incidents over the past five years have underscored the severity of fire risks in the frozen food sector: Midland Chilled Foods warehouse –Willenhall West Midlands
In January 2021, a massive fire broke out at a leading food warehouse in the Midlands. The fire, which took over 24 hours to contain, required the efforts of over 50 firefighters and 12 fire crews to bring it under control which resulted in the loss of millions of pounds worth of products. Investigations revealed that an electrical
fault in a refrigeration unit was the likely cause. The fire caused damage to over 60% of the building which included significant portions of the production plant. The company had to halt its operations and temporarily relocate to another site causing delays and disruptions in the food supply chain. Thankfully there were no reported injuries and all staff were successfully evacuated. The incident prompted the company to overhaul its fire safety measures, including installing state-of-the-art fire suppression systems.
Looking Ahead
As the frozen food industry continues to grow, addressing fire risks remains a critical priority. Ongoing investments in technology, staff training, and compliance with stringent safety regulations are essential to safeguarding the industry. By learning from past incidents and adopting proactive measures, the sector can aim to reduce the incidence of fires and their associated impacts.
Conclusion
While the past five years have seen a troubling rise in fires within the British frozen food industry, the concerted efforts of businesses, regulatory bodies, and technological advancements offer hope for a safer future. The journey towards minimizing fire risks is ongoing, but with vigilance and commitment, the industry can look forward to a more secure and resilient era.
Author: Jonathan Dixson –Essex Fire and Rescue Primary Authority manager
“
THE JOURNEY TOWARDS MINIMISING FIRE RISKS IS ONGOING
MEMBER FOCUS
FORKLIFT TRAININGUNDERSTANDING ACCREDITATION TO ENSURE YOU’RE MEETING STANDARDS
BFFF members, Mentor Training provide guidance and insight into training and PPT Safety.

Thankfully, due to the size and power of the trucks, most businesses appreciate that forklift training for novice operators is a requirement. However, the standard of training currently received across the UK is a real mixed bag, leaving some operators (and their colleagues and businesses) at risk. For training to effectively promote safety and ensure compliance, the standards to which it is delivered are critical. Taking on a training provider without an understanding of the standards and service they offer can be a false economy, and may give you inadequate protection in the case of an audit or investigation. Fortunately, the industry’s accreditation scheme is here to help. We explain its role and terminology to ensure you’re fully informed before entrusting a provider to upskill your new recruits…
What is accredited forklift training?
The Accrediting Bodies Association (ABA) was formed in 2012 to champion uniformity and standardisation within workplace transport training. The member bodies that make up the ABA together provide consistent frameworks for testing standards and categorisation of equipment. Working in consultation with the HSE, those bodies accredit training and regularly audit registered courses to ensure standards continue to be met.
It’s important to remember that not all training is created or delivered equally.
Receiving training accredited by a member body of the ABA guarantees you are getting standardised operator testing within the workplace transport category you require. You can also be assured that it complies with the requirements of Approved Code of Practice, L117, the HSE’s definitive guide to forklift safety and training.
Accredited training delivered to standards set by the ABA can help to provide employers with the assurance that requirements for safety and compliance will be met, which is added value that you may struggle to find with nonaccredited providers.
Understanding the terminology
Due to the nature of the terminology surrounding accredited training within the industry, it is important that you know exactly what to look for, or you may be under the impression that you are receiving a standard of training which you are not.
For the best assurances of quality and standardisation, check that you are receiving accredited training. It’s key to note that subtle differences in language in this area can make all the difference. For instance, understanding that an “accredited provider” may not necessarily offer training accredited to ABA standards is crucial. Also, you may notice that a business utilises “registered instructors”, but again, this doesn’t necessarily mean they are going to provide you with accredited training.
For training to be accredited to ABA standards, three key measures must all be in place:
• it must be carried out by instructors registered to an ABA member body
• testing must be done to ABA standards
• courses must be registered with an ABA member accrediting body (this can only be done by a registered provider)
If your chosen provider meets the criteria, they can offer training accredited by an ABA member body, of which you can be certain of the quality delivered.
Checking the terminology will ensure you’re as covered as you think you are – look a little deeper and make sure your provider will deliver training that complies with L117.
Added value is found in assurance and quality
Crucially, for businesses in need of forklift training, accreditation provides the assurance that requirements will be met. You will have peace of mind that your operators are receiving consistent, high-quality training, and that the courses provided cover you for any and all legal requirements.
It is important therefore, that you consider this peace
of mind when comparing quotes from multiple training providers, and properly assess the options in front of you. Which options give the necessary legal and quality assurances? Though price is obviously important, consider the future and which will be more cost-effective in the long run, should an accident or audit occur.
Essentially, businesses can fall into the trap of viewing forklift training as merely a tick box exercise. In doing so, the desire to source it as cheaply and efficiently as possible can put you at risk of selecting a provider without confirming exactly what you are getting for your money.
Always look for the relevant assurances of standards and service to ensure your operations remain safe, compliant and profitable. A provider whose standards are externally verified will ensure you and your team are in safe hands, leaving you suitably skilled and legally protected. Mentor deliver accredited training, registered with AITT, a founding member of the ABA, and all testing is conducted to ABA standards. Instructors delivering our training are all registered with AITT and undergo regular audits to ensure training is consistently delivered to their standards, wherever it takes place in the UK. We also hold training records and certificates on our customers’ behalf for a minimum of seven years, should you need them at any stage.
Challenging 3 common myths about PPT safety
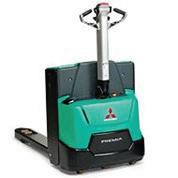
Though every bit as popular as larger counterbalance and reach trucks, powered pallet movers are often downplayed when it comes to accident risk and the training required to reduce it.
But with some powered pallet trucks (PPTs) weighing more than a small car, it’s vital that those responsible for their use understand how to do so safely.
To get to the root of the issue, we explore some of the common myths contributing to perceptions of PPT safety, and challenge them…
Myth #1: Powered pallet truck operation involves little to no risk
Many people believe there is little risk involved with the use of pallet trucks. Perhaps this is related to their stature. PPTs are smaller than other lift trucks, have no cab, and are controlled by the operator walking beside the truck using a tiller arm. Or, perhaps people are more comfortable with them because they occasionally see them, even share the same aisle space with them, when they go shopping.
But, however commonplace, the truth is that PPTs can soon cause serious accidents and costly damage in untrained hands. Though smaller in size than counterbalance and reach trucks, they too have the ability to cause life changing injuries if used incorrectly.
Unsafe PPT operation often causes injuries to lower limbs. Pedestrian varieties can inadvertently contact lower legs or be pulled over feet and toes, causing operators serious crush or entrapment injuries under the truck. Indeed, in recent years, a leading retailer was fined £1m when an operator fractured every toe on one foot after an accident in which an electric-powered pallet truck rolled backwards over it.
The assumption that pallet trucks pose little to no risk must be addressed throughout the workforce, for the good of your team and your business.
Myth #2: There is little difference between one pallet truck and the next
Another misconception stems from a lack of understanding around the variations of pallet trucks on the market (and their associated categorisation). Generally speaking, there is little awareness of the vast range available and, as a result, similar looking trucks can be pigeonholed as one and the same.
However, with each make and model having varied controls, components and functions, misidentification can mean inadvertently overlooking hazards unique to a specific variant.
There are pedestrian, rider and flip down platform variants, and all with varying purposes and a range of power sources. A good understanding of these variations will help ensure that you don’t fall foul of another common myth - that being trained on one type qualifies you to operate them all.
To help ensure the provision of relevant training for the many variants, pallet trucks are grouped into standardised categories by the Accrediting Bodies Association (ABA). Training on each category will need to include specific features which may not be relevant to another variant, so, for the safety of your operations, understanding these
BFFF INITITIVES
groupings (and therefore which trucks operators are qualified to use) is vital.
Myth #3: PPT training is not a legal requirement
As we’ve seen, with so many different variants available, one course does not fit all trucks. But there is another, more ominous, myth surrounding PPT training – that it is not required at all.
Despite the common misconception, pallet truck training is not optional – it is a firm requirement for safety and compliance.
Serious accidents occur all too often involving MHE and, tragically, most are entirely avoidable. By undergoing the proper training, operators can ensure they have the skills and knowledge to use this equipment safely, reducing the risk of accidents and incidents.
Not only does training provide a business with confidence that its operations are going to function in a safe and efficient manner, but it also helps it to ensure that they are meeting their legal requirements. PUWER 1998 specifies that employers must provide adequate training for anyone using work equipment, and this includes pallet trucks. This should cover how it’s used, the associated risks and precautions to take and, for assurances that it will meet all necessary industry standards, look for a provider delivering training to an accredited standard.
Indeed, quality is key. While sometimes perceived as sufficient and perhaps time-saving, informal training or video-based courses alone can leave PPT operators at risk of dangerous knowledge gaps and your operations open to accidents.
A good understanding of the equipment you are dealing with is ultimately required to ensure the people using it, and those around them, can remain safe and your operations remain compliant and productive. Dispel the myths surrounding PPT safety and make sure you understand the real risks affecting your operations.
For further guidance, or to discuss accredited courses for your business, visit: https://mentortraining.co.uk/ or call 01246 555222.
KNOW YOUR NUMBERS & KEYS TO A HEALTHIER LIFE
Members of BFFF, Latus Health, recently delivered a webinar around knowing your numbers, such as blood pressure, BMI, Blood Sugar and cholesterol, which are essential for maintaining optimal health for you and for
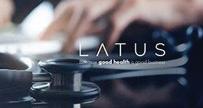
your employees. The session was delivered by Oliver Patrick a physiologist and world- leading expert in lifestyle management.
These vital statistics provide valuable insights into your overall well-being and can help identify potential health risks early on. By tracking these numbers, you can make informed decisions about your lifestyle, diet, and exercise habits to manage and prevent chronic diseases like heart disease, stroke, and diabetes.
Benefits of knowing your numbers:
• Early detection of potential health problems
• Ability to take preventative measures and manage your health proactively
• Able to trend/associate against lifestyle choices
• Increased awareness of your overall health
• Healthy habits for life are:
• Diet and nutrition
• Physical activity
• Stress management
• Sleep quality
• Quit smoking
• Reduce alcohol
Latus have a wide range of useful webinars which are free, these can be retrospectively viewed and deliver the following topics:
• Know your numbers & keys to a healthier life
• Stress management in the workplace
• Woman’s health & the menopause
• Neurodiversity in the workplace
• Nutrition from health and performance
To register for future webinars or view their back catalogue, please see below link: Webinars - LATUS Group
If you’d like to keep up to date with news and announcements about Latus Group webinars, please follow their LinkedIn newsletter ‘Latus Link’ here: Follow LinkedIn Newsletter here:
(3) LinkedIn
ENFORCEMENT
FARM OWNER FINED AFTER FATAL FALL
A Cheshire farm owner has been fined after a man fell to his death from a forklift truck while attempting to repair the roof of a packing shed at his premises in Tarporley.
Denis Thornhill and his company D.S. Thornhill (Rushton) Limited were fined a combined £16,000 after 64-year-old Mark Young was killed at Moss Hall Farm on 1 February 2021.
Earlier this year, both Thornhill and the company had been found guilty of breaching health and safety legislation following a six-week trial at Chester Crown Court. The jury cleared 78-year-old Thornhill on a charge of gross negligence manslaughter. They returned to the same court on 11 October 2024 to be sentenced.
During the trial, the court was told that on 29 January 2021, Mr Young, who worked as a roofer, had been asked to make repairs to a roof panel and fix a blocked gutter on the same building. However, as he was walking across the roof, he damaged a second roof panel so a replacement was purchased to carry out an additional repair.
He returned with his son three days later to complete the work and asked to be raised up to do it. Denis Thornhill arrived with a forklift truck that had a potato box balanced on its forks. Mr Young was lifted up inside the potato box to a height of around 16 feet, while his son, who was on the roof, attempted to reposition the panel from above. As Mr Young moved to one side of the potato box, it overbalanced, and he fell to the floor sustaining serious head injuries.
Although paramedics were called, they were unable to resuscitate him. He was pronounced deceased at the scene.
A joint investigation by Cheshire Constabulary and the HSE found that on the day of the accident there was no safe system of work implemented for working at height and unsuitable work equipment was used. The potato box did not have the required safety features for a non-integrated work platform and had not been secured in a way to prevent it overbalancing. Additionally, the forklift truck had not been subjected
to a thorough examination at the required frequency and was unsuitable for lifting people and Denis Thornhill was not formally trained in operating the forklift truck. Enforcement action was taken and a Prohibition Notice was served on the company prohibiting further work until a safe system was devised.
Denis Thornhill of Eaton Lane, Tarporley, Cheshire was cleared of manslaughter but was found guilty of breaching Section 37 of the Health and Safety at Work etc. Act 1974, by virtue of 37(1) of the Act and was fined £4,000 with costs of £4,000.
D.S. Thornhill (Rushton) Limited of Moss Hall Farm, Moss Hall Lane, Tarporley, Cheshire was found guilty of breaching Section 3(1) of the Health and Safety at Work etc. Act 1974 and was fined £12,000 with costs of £10,000.
HSE Inspector Ian Betley said after the hearing: “This was a tragic incident that could so easily have been avoided.
“The forklift truck and potato box were the wrong pieces of equipment for the job and never a suitable platform for working at height. The work should instead have been carried out using a tower scaffold, scissor lift, or a cherry picker.
“In bringing the forklift truck and potato box and using it to lift Mark at height, the company was in control of the work but had failed to implement proper planning and safe execution of it.
“All companies have a legal duty to ensure the safety of workers they employ or who carry out work for them. If that had happened in this case, then Mark’s life wouldn’t have been lost.”
COMPANY FINED AFTER WORKER LOSES FINGER
A nationwide bakery has been fined more than £360,000 after one of its employees lost a finger in machinery at a site in Northamptonshire.
Jacksons Bakery, a leading supplier of bread used in the commercial making of sandwiches, was given the fine after an engineer had a finger on his right hand caught in a flour sifting machine.
The then 31-year-old was assisting colleagues as they attempted to maintain the machine by clearing a blockage at the plant in Corby on 2 February 2023. Following removal of a guard, as the engineer assisted with the task, he checked the tension of a drive belt and his hand
got pulled around the bottom pully which resulted in the amputation of part of his right middle finger. The engineer was unaware that the machine had been switched back on.
Investigating, the HSE found that Jacksons Bakery Limited failed to ensure, so far as is reasonably practicable, the health, safety and welfare of all their employees.
In this instance there was a failure to implement a safe system of work ensuring that machinery was isolated and then locked off during maintenance work when fixed guards would be removed.
The HSE also found that engineers were unclear on when to isolate and ‘lock out tag out’ machines due to an absence of adequate training and instruction – and the fact that it was custom and practice to not robustly isolate and lock off illustrated an absence of adequate supervision and monitoring.
Jacksons Bakery Limited of The Riverside Building, Liverstone Road, Hessle, East Yorkshire, HU13 0DZ, pleaded guilty to contravening a requirement of section 2(1) of the Health and Safety at Work etc Act 1974. The company was fined £366,666 and was ordered to pay £5,386 costs.
After the hearing, HSE inspector Rebecca Gibson said “This unnecessary incident highlights the duty on employers to ensure that there are robust procedures in place relating to maintenance activities.
“If an appropriate ‘lock out tag out’ procedure had been produced and implemented and with suitable training, the serious injury would have been avoided.”
This prosecution was brought by HSE enforcement lawyer Samantha Wells and supported by HSE paralegal, Rebecca Withell.
ROUTINE HSE INSPECTION
RESULTS IN £150,000 FINE FOR FOOD MANUFACTURER
A North London food manufacturer has been fined £150,000 for failing to prevent access to dangerous parts of machinery.
A routine inspection by the HSE in October 2023 to Wembley-based Oriental Delight (UK) Limited identified multiple failings related to the guarding of machinery. Three machines were deemed unsafe due to interlocking safety
devices being defeated and guards being completely removed.
Oriental Delight (UK) Limited pleaded guilty to three breaches of Regulation 11(1) of the Provision and Use of Work Equipment Regulations 1998 and was fined £150,000 with costs of £3,020.
Following the hearing, HSE Inspector Marcus Pope said: “This case sends out a clear message to the food manufacturing industry that HSE will not hesitate to prosecute when inspectors find serious health and safety failings, particularly when previous enforcement and advice has been provided.”
“Once again we see how critical it is that all employers make sure they properly assess and apply effective control measures to minimise the risk from dangerous parts of machinery.”
This prosecution was brought by HSE enforcement lawyer Arfaq Nabi and supported by HSE paralegal officer Imogen Isaac.
GUIDANCE
GUIDANCE ON IN-SERVICE EXAMINATION AND TESTING PROCEDURES OF LOCAL EXHAUST VENTILATION (LEV)
With LEV’s being a big part of the food industry we urge our members to make sure that commissioning documentation is supplied anyone completing the 14 month thorough examination. Failure to supply this documentation will mean the inspector will not have performance information relating to the expected draw/ extraction at different points of the system. This will result in them stating an average reading. The average reading will not satisfy the requirements of the Control of Substances Hazardous to Health Regulations (CoSHH). In addition, we hear of new guidance for LEV inspectors being published by SAFed as below:
Published by the Safety Assessment Federation (SAFed), this document highlights that those undertaking thorough examinations and tests of Local Exhaust Ventilation (LEV) require clear and definitive guidance with respect to the procedures that should be adopted.
The purpose is to ensure that such control measures are maintained in an efficient state, in efficient working order, in good repair and in a clean condition so that the control measure is effective in adequately controlling the hazardous substance in accordance with Regulation 7 of COSHH. Unlike other thorough examinations to ensure the continued safe use of equipment, the purpose of a thorough examination of LEV equipment is to ensure that it provides the effective and adequate protection from airborne hazardous substances to protect workers. In some cases, this may require air sampling to confirm the workplace exposure assessment. This can be provided by the inspection body, if they have the necessary equipment and competence to do so, or it can be provided by an external organisation as a supplementary test.
The aim of this guidance is to provide member companies with the appropriate information to ensure that the requirements of the Control of Substances Hazardous to Health Regulations 2002 (as amended) (COSHH) Regulation 9, the Control of Lead at Work Regulations 2002 (CLAW) Regulation 8, and the Control of Asbestos Regulations 2006 (CAR) Regulation 13 are taken fully into account when undertaking LEV thorough examinations and tests.
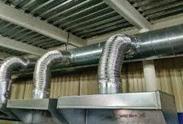
In addition, the guidance will help to achieve a consistent approach by member companies when undertaking this activity, covering a variety of processes by ‘typical extraction type’. It is noted that the guidance is for the use of Engineer Surveyors (ES) and it assumes a level of competence in the examination and testing of LEV to cover the legal requirements to examine such equipment. https://www. safed.co.uk/publications/tc8-local-exhaust-ventilation
Should you want to learn more about this topic please contact: simonbrentnall@bfff.co.uk
THE HOUSE OF COMMONS
DISCUSSES ZERO-HOURS CONTRACTS,
ACCORDING TO CIPD AND ONS RESEARCH, PEOPLE ARE MOST LIKELY TO WORK IN THE ACCOMMODATION
AND FOOD SECTOR
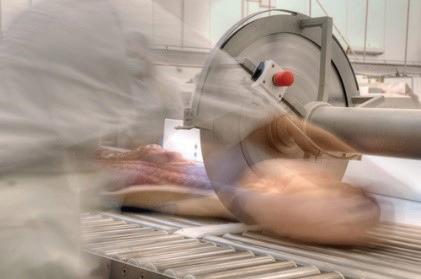
This House of Commons report discusses the use of zerohours contracts, including statistics on their use, legal implications, and surrounding policy debate.
Zero-hours contracts are a type of contract used by employers where workers have no guaranteed hours and agree to be potentially available for work. They are used by
BFFF INITITIVES
companies seeking labour flexibility and by workers seeking flexibility around their other commitments.
Opinion on zero-hours contracts has been mixed. Employee organisations tend to argue that the contracts result in financial insecurity for workers who lack key employment rights. Meanwhile, employer organisations stress their utility when seeking to meet fluctuating demand and argue that they play a vital role in keeping people in employment.
LEGAL ISSUES
The fact that someone is working under a zero-hours contract does not itself determine what employment rights they do or do not enjoy. Rather, that depends on their employment status, for which a range of legal tests exists.
However, zero-hours contracts can make it challenging to establish someone’s employment status and their qualification for certain employment rights. “Mutuality of obligation,” the mutual obligation to offer and accept work, is a key legal test for being an “employee.” With some zerohours contracts it can be hard to establish whether such mutuality of obligation exists or not.
Similarly, there is a difficulty for some zero-hours contract employees in building up enough uninterrupted continuity of service to qualify for certain employment rights, such as unfair dismissal. This is because a week’s gap without work can be enough to reset the timer on their continuity of service.
Since 2015 employers have been banned by section 27A of the Employment Rights Act 1996 from inserting “exclusivity clauses” into zero-hours contracts, which try to stop employees with such contracts from also working elsewhere.
STATISTICS
The Office for National Statistics (ONS) collects statistics on zero-hours contracts as part of the Labour Force Survey. According to ONS, over a million people were employed on a zero-hours contract in April to June 2024. There was a marked increase in the reported use of zero-hours contracts from 2012-2016, though it is likely this was due to increased awareness of such contracts at the time. Since then, the rate of zero-hours contracts has increased by a smaller amount, from around 2.5% to 3.5%.
Based on a small survey of businesses by the Chartered Institute of Personnel and Development (CIPD), businesses report that they are most likely to use zero-hours contracts to manage fluctuations in demand.
According to a combination of the ONS and CIPD research, People on zero-hours contracts are more likely to be:
• Aged 16-24.
• Female.
• Working part time.
• From London and the South East.
• Employed in the accommodation and food sector.
• On average, paid slightly less than those not on zerohours contracts (around 6% less in hourly pay).
• Reporting lower opportunities for career progression.
POLICY DEBATE AND POSSIBLE REFORM
The perceived increase in zero-hours contracts in recent years has prompted expressions of concern both inside and outside of Parliament, although many support their use. A series of Private Members’ Bills aiming to ban or regulate zero-hours contracts have been introduced in recent years, though only one, the Workers (Predictable Terms and Conditions) Bill 2023, received Royal Assent and no commencement order to bring this act into force has been made.
Instead, following the 2024 general election, the newly elected Labour government has pledged to ban “exploitative zero-hours contracts,” as part of a promised Employment Rights Bill, as noted by the King’s Speech 2024: background briefing notes which committed to: “Banning exploitative zero-hour contracts, ensuring workers have a right to a contract that reflects the number of hours they regularly work, and that all workers get reasonable notice of any changes in shift with proportionate compensation for any shifts cancelled or curtailed. This will end ‘one sided’ flexibility, ensuring all jobs provide a baseline level of security and predictability.”
MARTYN’S LAW UPDATE – SECOND READING 14TH OCTOBER
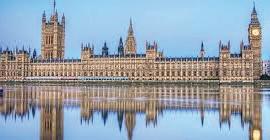
BFFF INITITIVES
The Terrorism (Protection of Premises) Bill was introduced to Parliament on 12 September 2024. It will have its second reading on 14 October 2024. At this point, ministers will debate the general principles of the Bill.
The new legislation, also known as ‘Martyn’s Law’ in tribute of Martyn Hett who was killed alongside 21 others in the 2017 Manchester Arena attack, aims to ensure venues across the UK must consider the security of the public, and take steps to protect them from harm.
Under the changes, a new duty will be placed on those responsible for premises and public events, requiring them to take appropriate action to strengthen public safety, with requirements reflecting the size of the venue and the activity taking place.
As set out in the Bill, those responsible for premises will be required to fulfil necessary but proportionate steps, according to their capacity, to help keep the public safe. This includes a tiered approach, linked to the size of the venue, how many people will be there and the activity taking place, making sure undue burdens are not placed on small businesses.
A standard tier premises will apply to locations with a capacity of more than 200 people but under 800. These businesses will be asked to undertake simple yet effective activities to put in place procedures to reduce harm to the public in the event of an attack. These could be as simple as training staff to lock doors, close shutters and identify a safe route to cover. The standard tier premises will most likely to be applicable to larger retailers in the food industry.
The enhanced tier will apply to premises and events with a capacity of more than 800 individuals, given the devastating impact an attack could have in these spaces. These locations will need to put in place measures such as CCTV or hiring security staff.
Head of Counter Terrorism Policing, Matt Jukes, said:
“Through Martyn’s Law we can ensure that the public have additional protection from terrorist attacks while at events and public venues. Counter Terrorism Policing welcomes [this] bill and we look forward to seeing it progress through Parliament.
“We’re all inspired by and motivated by the experience of victims and survivors. Figen Murray has campaigned tirelessly for Martyn’s Law and it’s thanks to her unwavering determination that we are one step closer to ensuring the public has additional protection in the form of this legislation.
“We will continue to work with the public, with businesses, and with the government to ensure that when a terrorist
attack takes place we have the right mitigations in place that will prevent other families from experiencing those tragedies.”
Following Royal Assent, the government says businesses will be given time and support to understand and implement their new obligations and allow for the new regulator to be established. This will include dedicated guidance so that those affected will have the required information on what to do and how best to do it.
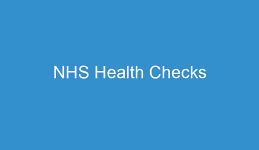
GOVERNMENT LAUNCH NEW WORKPLACE HEALTH CHECK PROGRAMME
The government has said that more than 130,000 people across the country will be better protected from diseases such as heart disease, kidney disease and diabetes, as it rolls out a life-saving health check programme to workplaces across the country for the first time.
The checks, which can be completed quickly and easily for employees at work, record a range of information about each patient, which is then used to determine their cardiovascular risk.
Employers from a range of professions will take part in the programme including those from the building, hospitality and transport sectors, and social care.
The announcement is part of the Health and Social Care Secretary’s commitment to supporting the government’s mission to boost economic growth by improving the health of the nation.
With every check providing the equivalent of an NHS appointment, these checks will save thousands of hours of valuable NHS time, helping to cut waiting lists and rebuild the NHS.
Andrew Gwynne, Minister for Public Health and Prevention, said: “We know so many deadly diseases can be avoided
BFFF INITITIVES
if we seek help in enough time. That’s why we’re working to improve access to treatment while also taking steps to address the preventable causes of cardiovascular disease.
“This innovative new programme is an important step towards community-focused healthcare and supporting economic and productivity through improving health, shifting the focus from treatment to prevention, easing the strain on the NHS and helping people to live well for longer.”
Over 16 million people are eligible for an NHS Health Check, but current data shows that only around 40% of those invited went on to complete one. This is especially true for men, who are less likely to get early help but who are more likely to develop cardiovascular disease at an earlier age than women. This new programme aims to reach more people through their place of work and make it more convenient for people to understand and improve their cardiovascular health.
NHS National Clinical Director for Stroke, David Hargroves, said: “Convenient and efficient NHS checks in the workplace could spot thousands of people at risk of a range of cardiovascular diseases, and with high blood pressure the biggest risk factor for stroke, early detection will undoubtedly save lives.
“This new programme shows the NHS is committed to preventing ill health and I would urge anyone invited for a check to come forward and get support to improve their cardiovascular health.
Councillor Louise Gittins, Chair of the Local Government Association, said: “Health checks can save lives. They can prevent people from developing largely preventable diseases, such as heart disease, cancer, type 2 diabetes and liver disease.
“Councils are exploring new ways to boost uptake, targeting individuals or communities at increased risk, and using proactive outreach programmes to get into those communities who are less likely to attend their general practice.
However, there is more that can be done, and by partnering council and employers, we can make sure more people get a health check and hopefully prevent illness later on.”
In addition, the government has also announced the development of a new digital version of the NHS Health Check which will be ready for testing early in 2025.
The service will be available through the NHS App, meaning users can undertake their health check at home and have the results automatically written back into their GP electronic health record, within a few clicks.
Local authorities in Norfolk (East of England), Medway (South East) and Lambeth (London) have been selected to pilot the new digital health checks in early 2025.
The digital programme will deliver around one million checks in its first four years. Plans are being put in place to make digital NHS Health Checks available nationally, alongside the face-to-face programme to give patients more choice.
BFFF HAS PREVIOUSLY RAISED AWARENESS OF MODERN
SLAVERY
WITH ITS MEMBERS, NOW HUNDREDS OF ROGUE EMPLOYERS ARE TARGETED IN ILLEGAL
WORKING CRACKDOWN
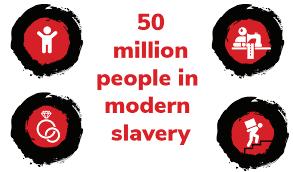
In July, the Home Secretary announced that the government would crack down on unscrupulous employers who are hiring migrants illegally and exploiting vulnerable people, alongside extensive work to disrupt the criminal networks who bring the workers to the UK.
During an intensive week of action from 18 to 24 August, Immigration Enforcement teams carried out targeted visits to rogue businesses suspected of employing illegal workers.
Over the course of the operation, more than 275 premises were targeted, with 135 receiving notices for employing illegal workers. In addition, 85 illegal workers have been detained.
In many cases, illegal workers live in squalid conditions onsite, earn far below the UK national minimum wage, work longer hours than legally allowed and may have entered the UK illegally, overstayed their visas or arrived under visitor conditions.
BFFF INITITIVES
The fact they are paid so little also allows their employers to undercut honest competitors who follow the law, and these businesses often do not pay their fair share in taxes to contribute to the economy.
This operation is part of a larger, ongoing effort to tackle illegal employment and exploitation of vulnerable people in the UK. More operations of this kind will be conducted in the near future.
Unscrupulous employers are potentially liable to substantial financial penalties. The maximum civil penalty for employing illegal workers is £45,000 per worker for a first offence and £60,000 per worker for repeat violations.
Immigration Enforcement teams also play a critical safeguarding role, working closely with the Gangmasters and Labour Abuse Authority and other organisations to allow employees to report labour exploitation.
Home Secretary, Yvette Cooper said: “It is completely wrong that dodgy employers can work hand-in-glove with the smuggling gangs who risk people’s lives to bring them here illegally and push them into off-the-books employment.
“These workers are sold complete lies by the gangs before being made to live and work in appalling conditions for a pittance. We are determined to put a stop to this, which is exactly why we have launched crackdowns such as this.
“While this operation marks an important step forward, our commitment to tackling this issue is ongoing. We will ensure those who break the rules face the full force of the law.”
HSE REMIND EMPLOYERS OF STRESS LEGAL DUTY
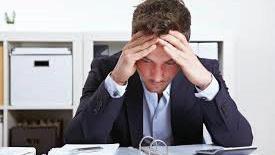
To coincide with last week’s Stress Awareness Week 2024, the HSE reminded employers to carry out their legal duty to prevent work-related stress and support good mental health at work.
According to HSE figures, the average employee suffering
from work-related stress, depression or anxiety took an average of 19.6 days off work, almost the equivalent of a month’s working days, with an estimated 875,000 cases in 2022/23.
The HSE’s Working Minds campaign provides employers with simple steps to prevent days lost due to work-related stress.
Kayleigh Roberts, Work-Related Stress and Mental Health Policy Lead at HSE, said: “Our statistics clearly outline that there is a work-related stress issue in Britain and we want this to change. A total of 17.1 million working days were lost in 2022/23, and this figure has a serious cost to the individual and to the business. Employers can make a difference by understanding and fulfilling their legal duty to prevent work-related stress and support good mental health at work.
“That is why we are reminding employers during Stress Awareness Week that it is critical they recognise the signs of work-related stress and get to the root causes behind this issue. Prevention is better than cure and understanding the risks is the first step to preventing them.”
The legal duties for employers are:
• Carry out risk assessments for stress and act on them.
• Take steps to prevent work-related stress.
• Organisations with fewer than five employees don’t have to write anything down (but it is useful to do this, for future review).
• Organisations with five or more employees, are required by law to write the risk assessment down.
There are six main areas that can lead to work-related stress if they are not managed properly. These are: demands, control, support, relationships, role and change. Factors like skills and experience, age, or disability may all affect someone’s ability to cope.
Kayleigh added: “Although tackling stress may appear daunting for some employers, failing to recognise the signs of work-related stress and acting on them can result in reduced productivity, sickness absence or even losing a valued member of staff. I would urge all employers who are looking for guidance to seek help through our Working Minds campaign, which helps companies follow five simple steps.”
Working Minds calls on employers to follow the five Rs. They are to: Reach out and have conversations, Recognise the signs and causes of stress, Respond to any risks you’ve identified, Reflect on actions you’ve agreed and taken, and make it Routine.
Andrew Berrie, Head of Corporate Partnerships at Mind, said: “We’re delighted to continue to support HSE’s Working Minds campaign. Mind has long been working with employers of different sizes and sectors to help them create mentally healthy workplaces, but as these insights show, this has never been more important.
“While many of us will face pressure in our working lives, unchecked and unmanageable pressures can lead to strain and can have a debilitating effect, resulting in stress. Stress can cause mental health problems, and make existing problems worse. For example, if you often struggle to manage feelings of stress, you might develop a mental health problem like anxiety or depression.
“It is vital that employers take steps to mitigate against work-related stress and create an environment in which employees can have open and honest conversations about triggers of stress and poor mental health. This can start with just a simple, person-centred conversation between managers and their teams.”
Jenny Scott, Head of Communications at NEBOSH, said: “The statistics show a worrying picture of the mental ill health that people experience because of their work. But it doesn’t have to be this way. We are delighted to continue our support for the Working Minds campaign, which provides great resources for employers who want to foster good mental health and prevent work-related stress. We will also welcome the HSE’s Phoebe Smith to the NEBOSH Online Conference this November where she will guide delegates through the essential steps of creating a workrelated stress risk assessment.”
There are three main reasons employers should prevent work-related stress and support good mental health; it’s the law, it’s good for business and it’s the right thing to do.
HEALTH AND SAFETY AT WORK
ETC. ACT 1974 (AMENDMENT)
BILL 2024-25
A private members’ bill has been introduced in the House of Commons to amend the Health and Safety at Work etc. Act 1974.
The change would place a requirement on employers to:
• Take proactive measures to prevent violence and harassment in the workplace.
• Make provision for protections for women and girls in the workplace.
• Require the HSE to publish a Health and Safety
Framework on violence and harassment in the workplace, including violence against women and girls in the workplace.
The first reading in the House of Commons took place on 21 October, and the second reading is scheduled for 29 November 2024.
Currently, there are no publications for this Bill, which is common in an early stage of a Bill, when it has not been fully drafted.
” Employers must prevent workrelated stress by recognsing its signs, addressing root causes, and supporting mental health to reduce the 17.1 million working days lost annually due to stress, anxiety, or depression.”
TRANSPORT HUB
CHANGES TO SAT NAV INSTRUCTIONS FOLLOWING FATAL CRASH
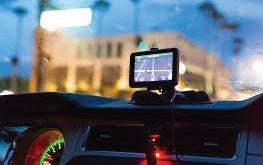
Google and Apple have agreed to amend their audio prompts after a double fatal crash appeared to have been caused by incorrect directions from a sat-nav.
A coroner warned tech companies, including TomTom, to a risk of future deaths after a woman drove the wrong way onto the A5 near Milton Keynes.
Sean Cummings, assistant coroner, said Tracey Haybittle, 58, and Amal Mohamed Ahmed, 38, both died in a headon collision after Ms Ahmed appeared to have followed “audio directions from her sat-nav application”.
TomTom said recent changes had been made to its verbal instructions. Apple and Google hoped changes to their audio prompts would provide clearer guidance.
In November 2023, Ms Ahmed was “following audio directions” when she drove down the slip road near the Little Brickhill junction.
In a Prevention of Future Deaths report for Ms Ahmed, the coroner noted police attending the crash saw three other vehicles “perform exactly the same manoeuvre as Ms Ahmed and attempt to travel down the slip road in the wrong direction”.
National Highways has since erected signs to prevent motorists from accessing the slip road.
Responding to the report, a spokesperson from Apple said the company would add special voice guidance for drivers heading past the A5 offramp toward the A5 onramp.
They said: “We trust that the steps we are taking will be helpful to try to avoid any future such tragic events.”
Motorists will be instructed to “continue straight at the overpass” as they travel west. While on the overpass, drivers will be instructed to “turn right onto A5 toward Milton Keynes, Bletchley”.
Google said while it was not clear whether Google Maps was involved in the incident, it had also made improvements so similar incidents did not occur in future.
It said its teams were working on improvements to the timing of audio to provide enhanced guidance in situations such as those in this case.
A spokesperson said: “This will involve an amended audio prompt as a driver approaches a junction where they would cross an overpass - ‘after the overpass, turn right’.
“We hope that this will provide clearer guidance for drivers and help reduce the risk that they make an incorrect turn.” TomTom recommended users updated their systems after it recently implemented additional safeguards to “limit drivers’ confusion where possible”.
It said this had been done by timing the verbal commands closer to the actual exit, and after passing the off-slip road.