Designer.Sustainable Thinker.CriticalREES.BRONWEN Solver.Problem
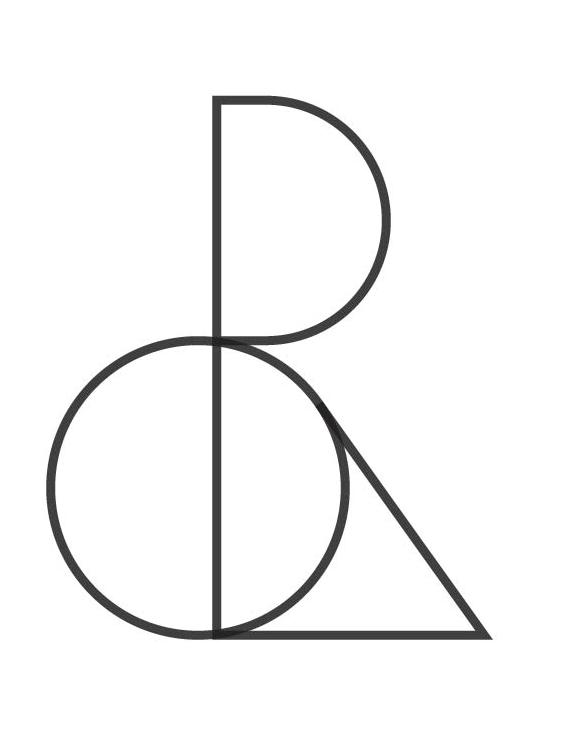
My practice revolves around sustainability, simplicity and handsmaking.on Critical thinking, psychology and investigatory research play a big part in my design process; using design thinking as a tool to ask questions, solve complex issues, and improve our surroundings. I am very keen to expand my skills, knowledge and capability within design, both in terms of creating objects, and using design as a tool for change.
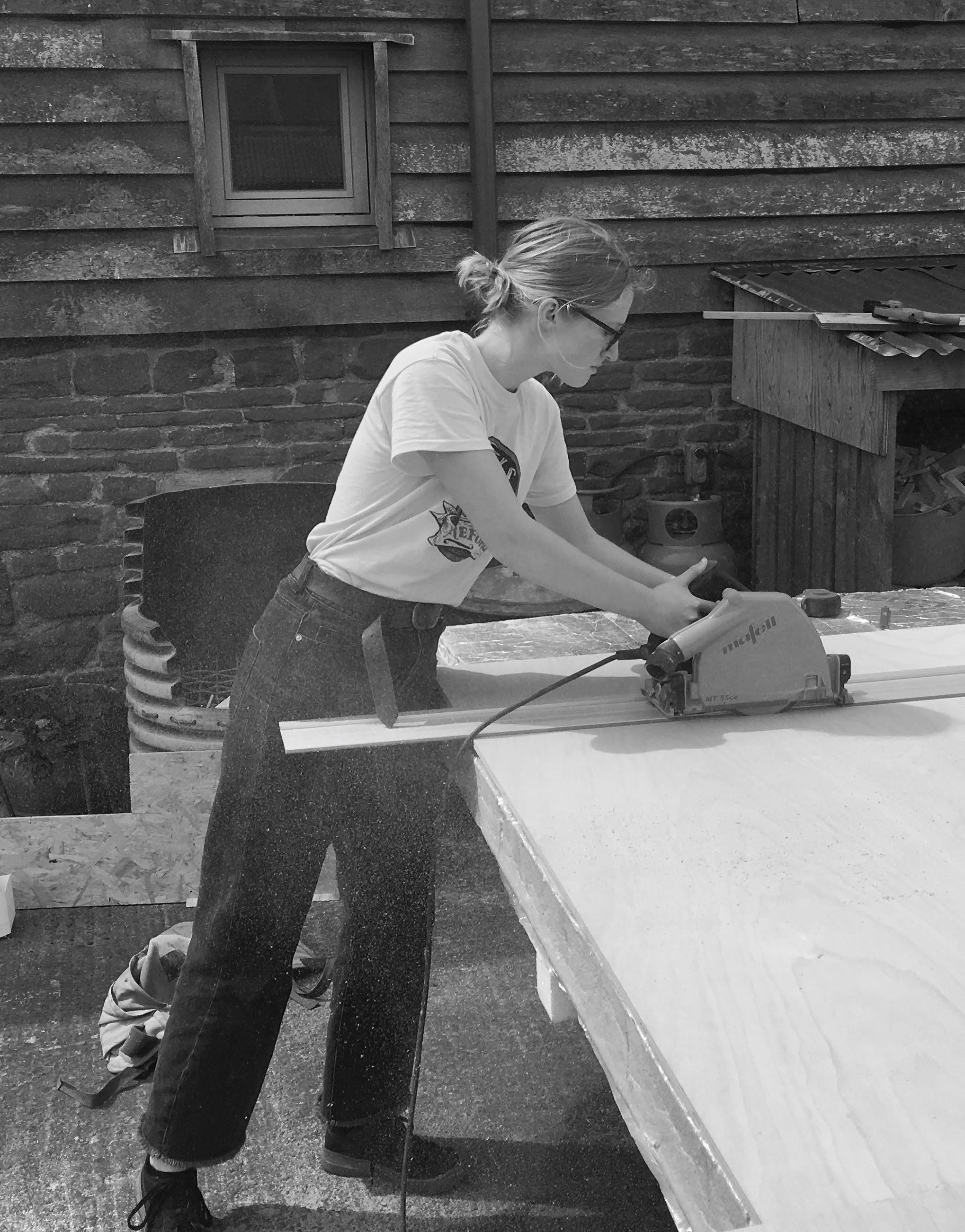
ABOUT ME
bronwen.rees@outlook.com07714651166@thebronblog
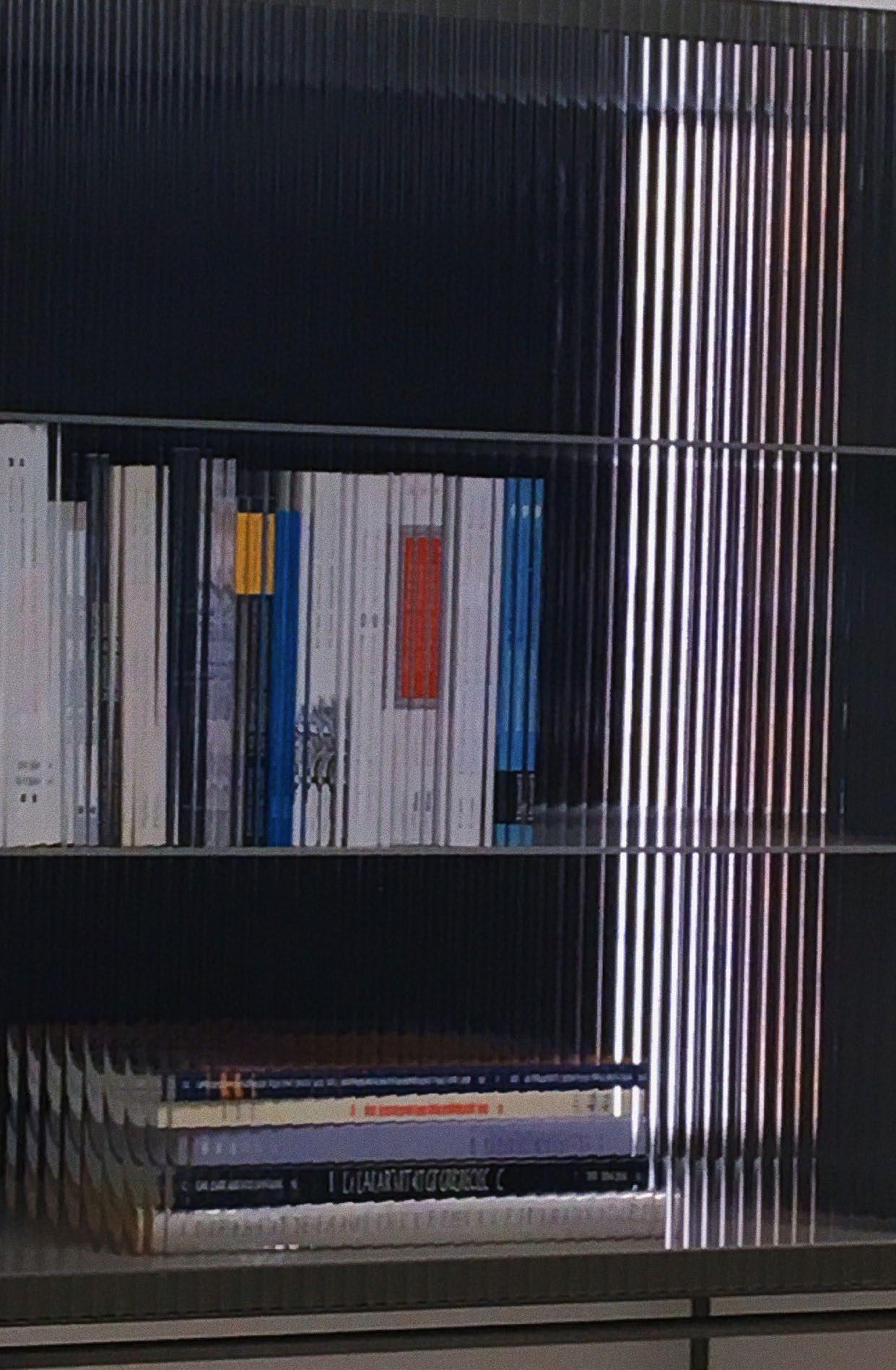
03 ZEER CABINETS
TO CUSHION
A project that challenges the unsustainable practices of the upholstery industry through re-thinking the materials and construction of a chair.
01CONTENTSLOUNGE
A free-standing cabinet to store and cool veg in, based on an ancient African design that uses no electricity.
A clothes stand to drape your clothes on when getting changed, inspired by the carpenter’s shave 05horse.CRADLE

INTO LOCKDOWN
A collection of homewares that utilise the endlessly recyclable properties of aluminium, encouraging the user to reuse their products material.
04 DRESSING HORSE
A set of ergonomic cushions that are made from second hand materials, highlighting waste and the many ways it can be re06purposed.STRAPPED
A manual designed to show the endless possibilities of a set of tension straps in lockdown living. Designed to promote creative thinking and mental wellbeing.
02 ALUMINIU.M
CHAIR
DesignersDesignersSustainableforAwardedCHAIR.LOUNGEtheMaDECertificateExcellentConsiderationofMaterials@New2022.ShortlistedfortheHabitatNew2022Award.Brief:Challengetheunsustainablepracticeswithintheupholsteryindustry,offeringaresponsiblealternativewhichaddresseswaste,materialsouring,emotionaldurabilityandmoderndayliving.Outcome:Achairmadefromnatural,renewableandrecyclablematerials;theframeissolidwoodandflatpacktoreduceemissions;thecushionsaremadefromwoolandcottonandaredetachable,providingasustainable,adaptablealternativetoourthrowawayculture.

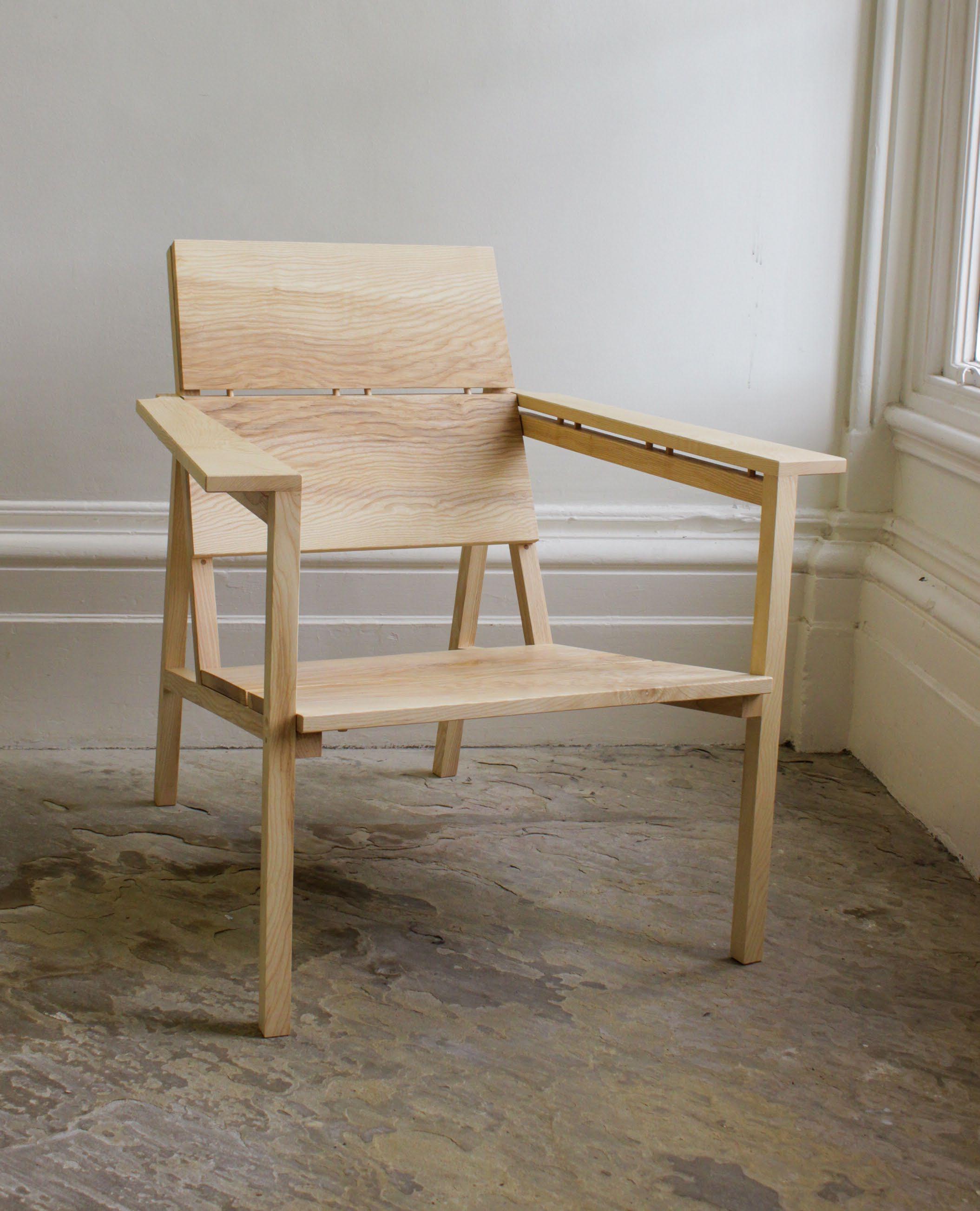
9PROBLEMmilliontonnes
of UK furniture waste ends up in landfills each year; designed to fit fleeting trends and so big and bulky that it makes moving home or carrying the piece up a flight of stairs near to impossible (OECD).
Not only this but upholstery is increasingly made from fossil-derived materials which are non-renewable and non-recyclable. They are also constructed in ways which make them impossible to separate and responsibly dispose of at the of life (RTS).
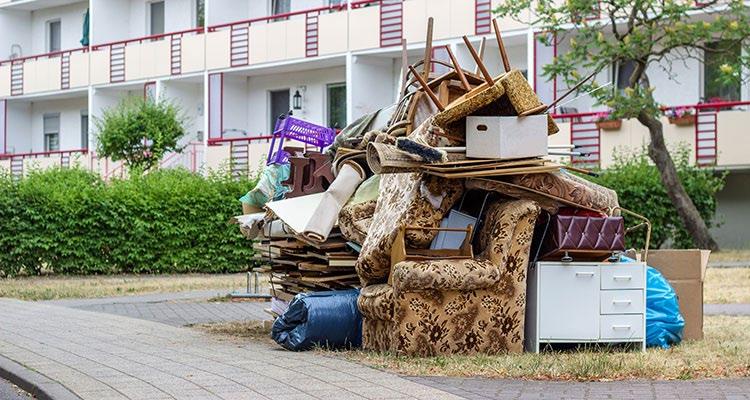
of responsible materials that were widely available in the UK led to the use of wool, a by-product of the meat industry, and English ash, a tree currently being widely felled to deal with ash die-back (SFF, Forest to Home).
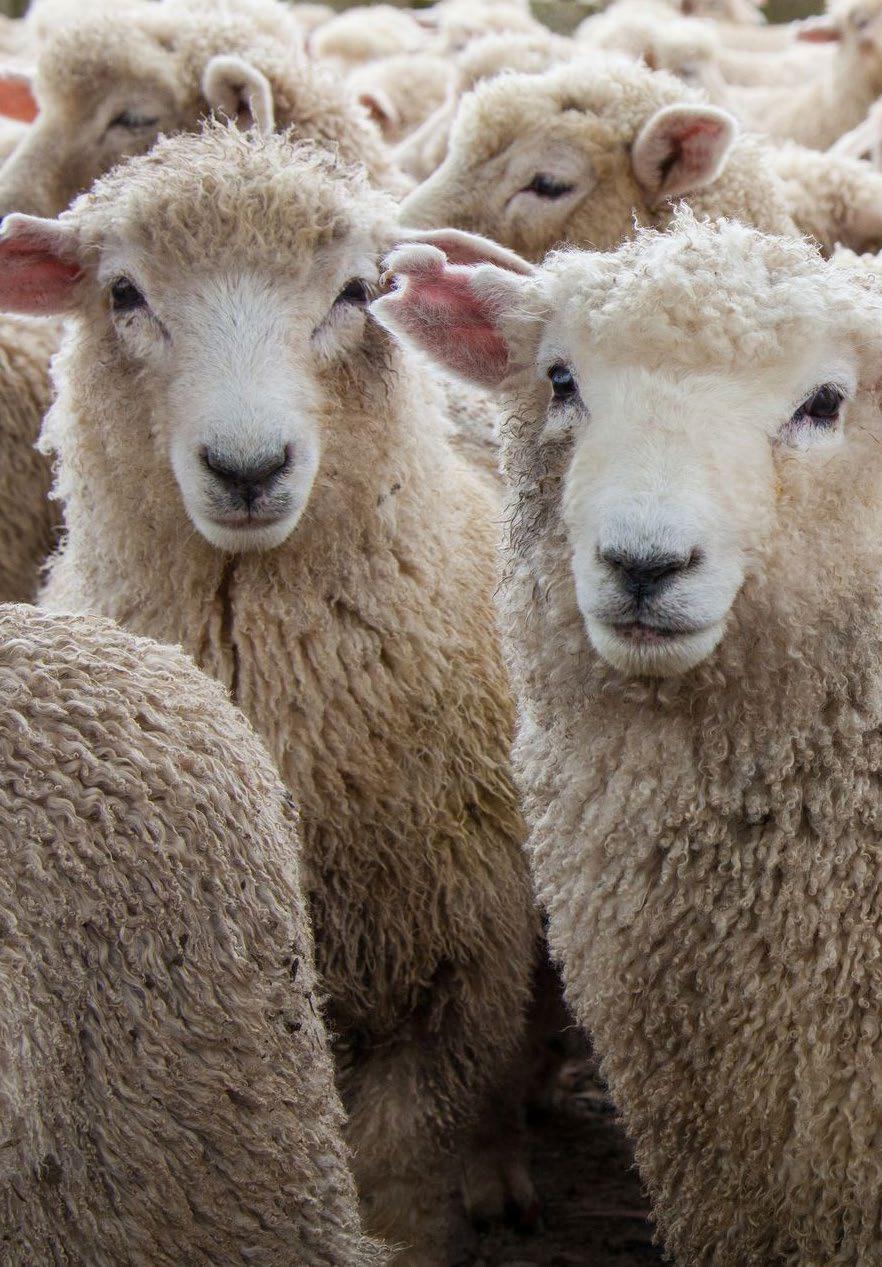
ResearchRESEARCHfor this project
revolved around designing not only a product but a system which ensured the full life cycle of the product was considered (Prof J. W. Forrester, The Design ExplorationCouncil).
All materials also fit into closed material loops, and when compared to their fossil-derived alternatives reduce the chairs carbon emissions by 75% (Cradle to Cradle, Embodied Carbon Footprint Database).
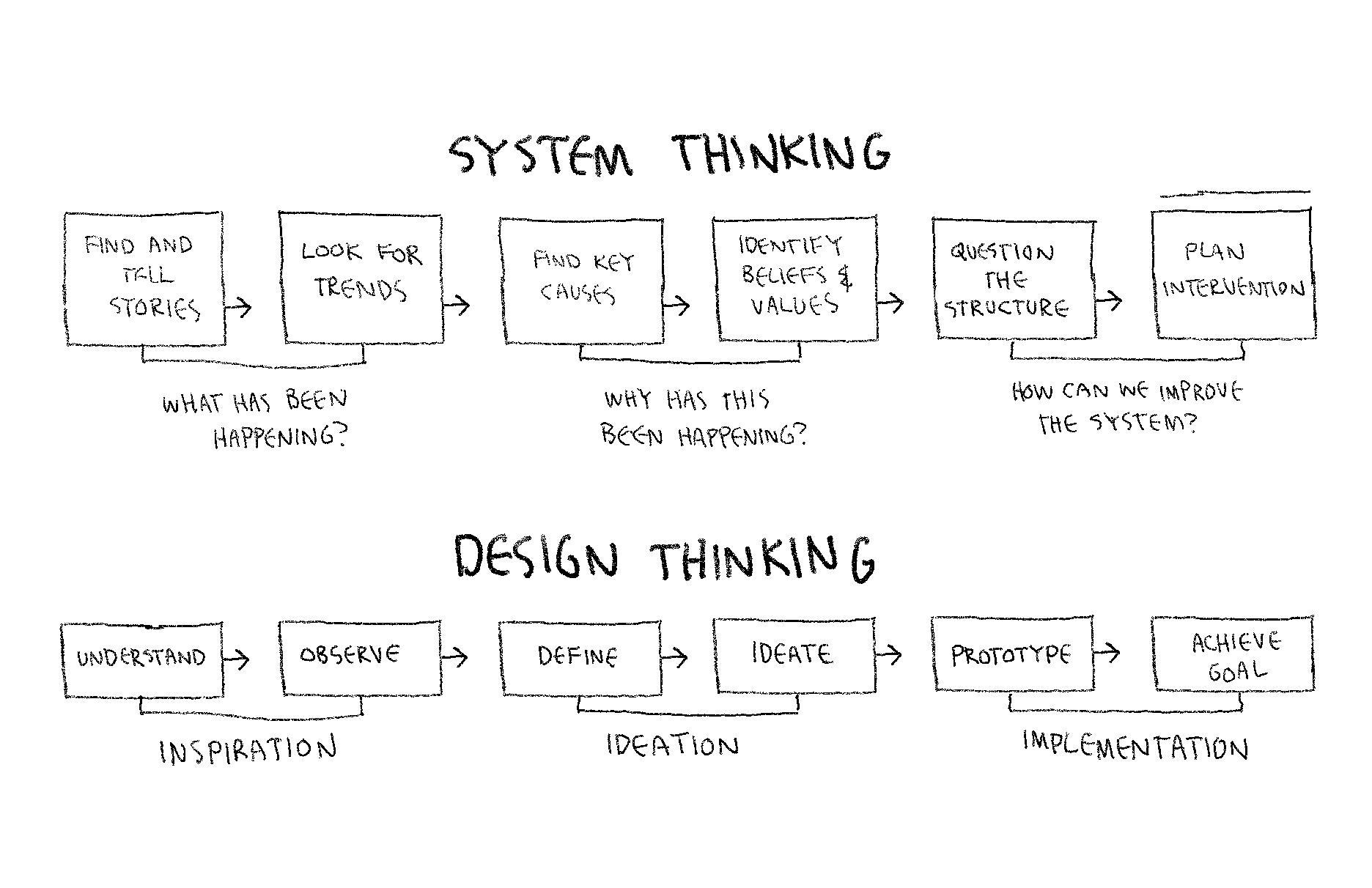
useddevelopment,MaterialDEVELOPMENTexplorationledthecushionexploringefficientandsimplewaystoutilisewool,amaterialnotcommonlyforupholstery(Seebottompicture).Extensiveprototypingandusertestingofboththeframeandthecushionsresultedinadesignwhichiscomfortable,easytoassemblyandvisuallypleasing.
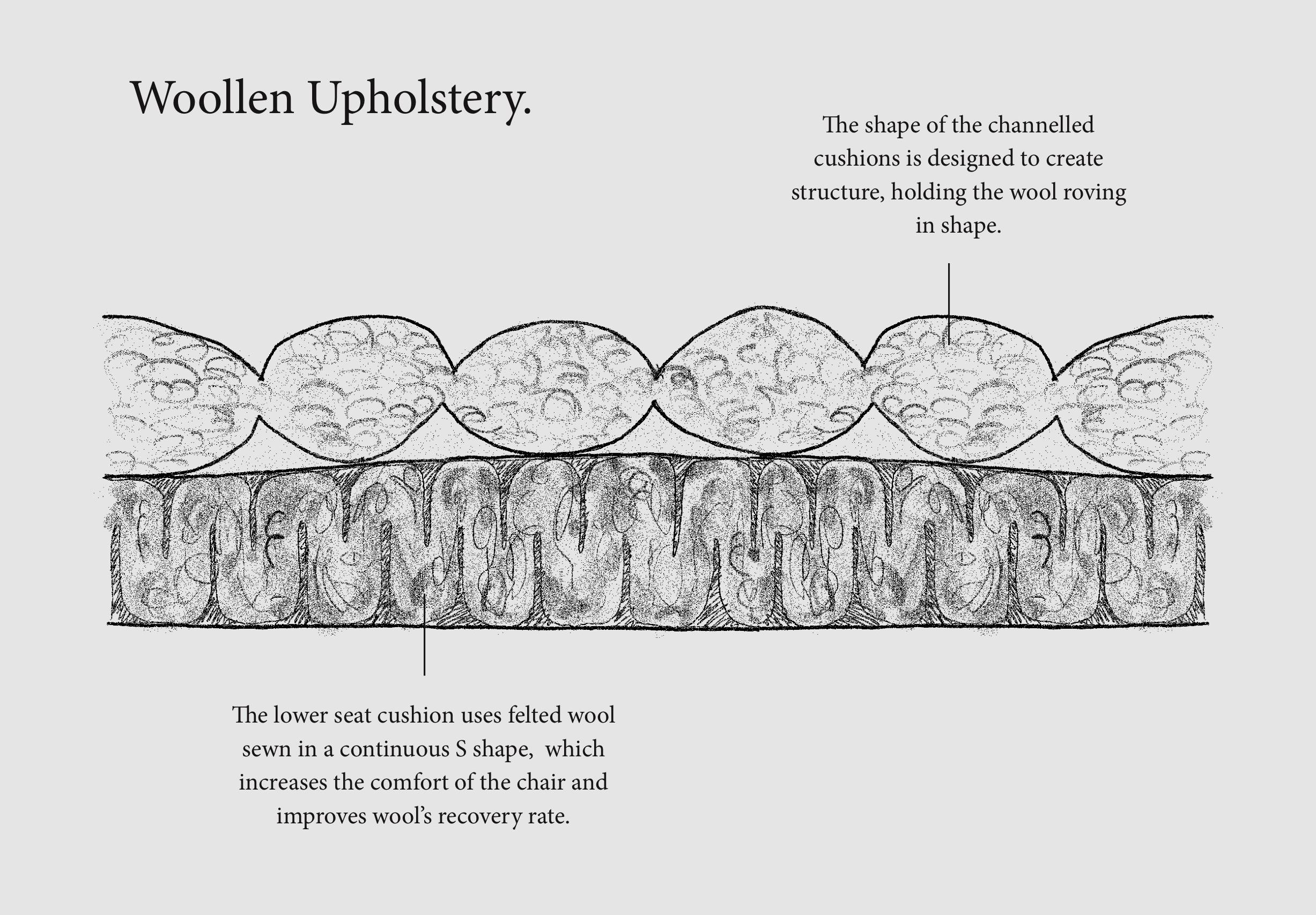
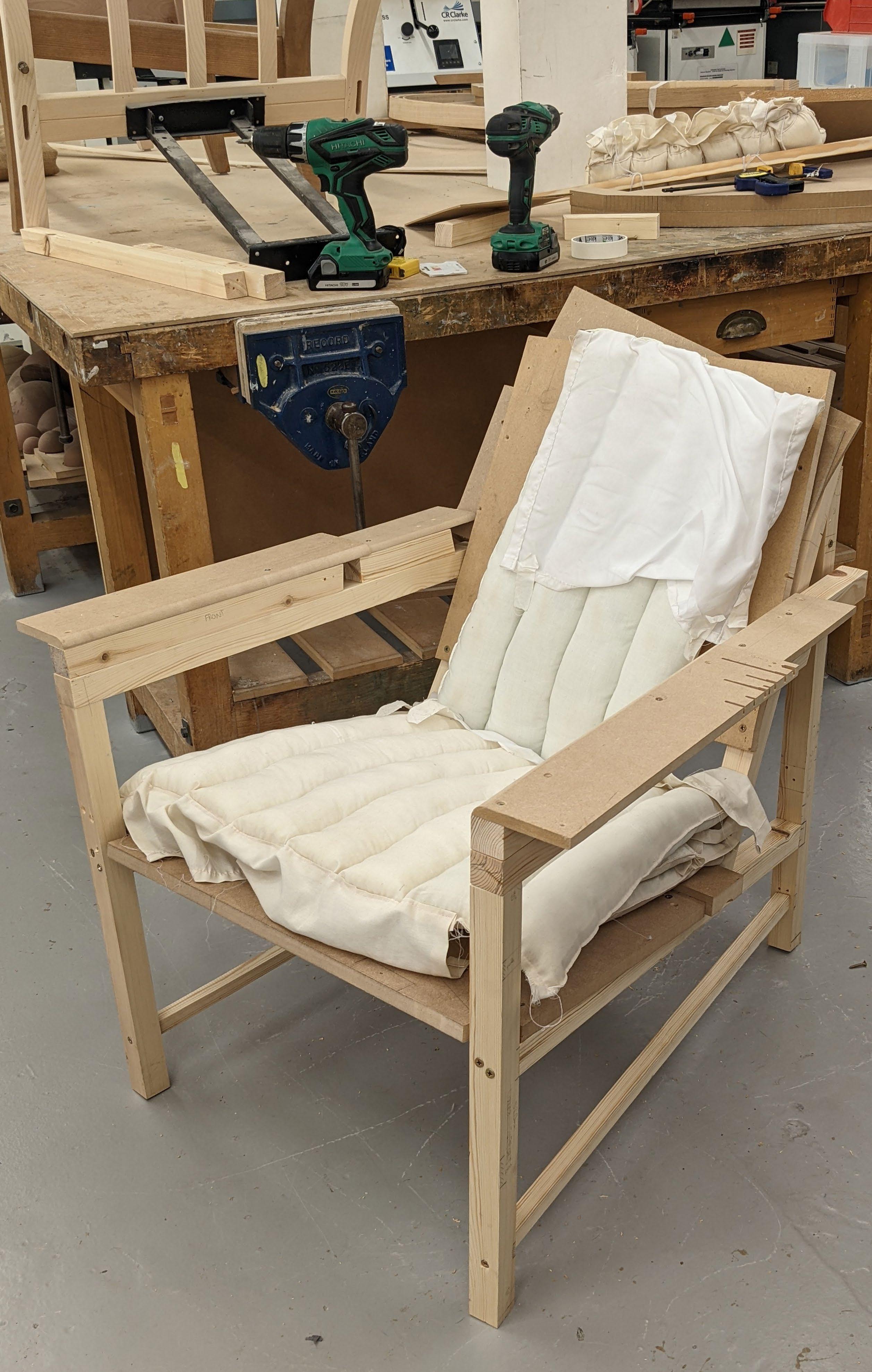
ToATTACHMENT.enableeasyattachment and detachment of the cushions, a G clip fastening is used to attach the cushions to themselves These(right). clips are fed through a dowel feature, which was designed to hold the cushions sturdily, while also adding to aesthetic appeal of the chair when “undressed” (above).
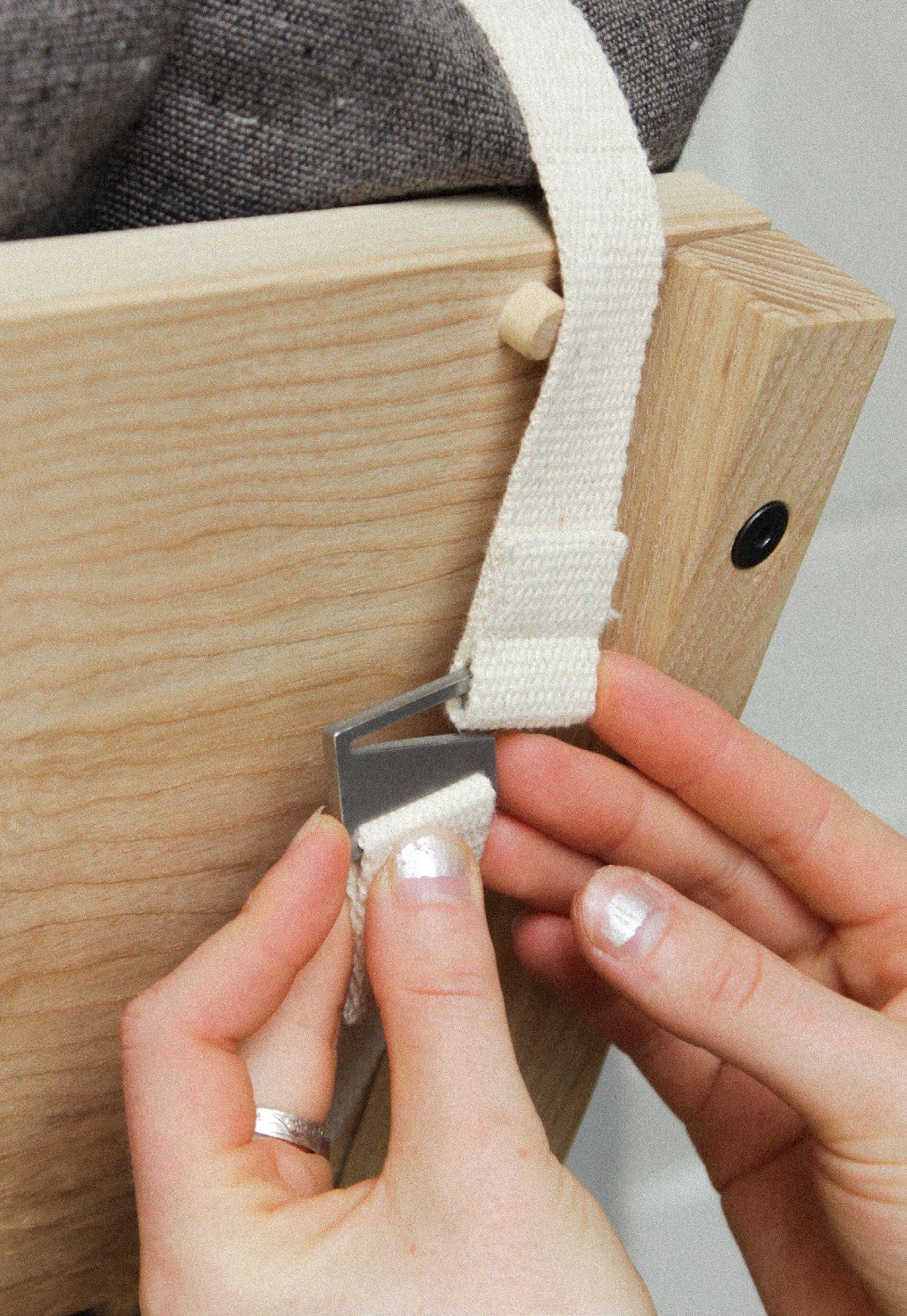

SEPARATION
The separation of the piece is crucial to the narrative of the chair and addresses several sustainabilityissues.
The detachable cushions allow the chair to be dressed in different “outfits” for different occasions, allowing the user a feeling of newness without needing a whole new product, combating “fast furniture” and consumer habits.
Finally, by making the cushions detachable, the materials are already separated and ready to be disposed of responsibly when the product reaches the end of it’s life.
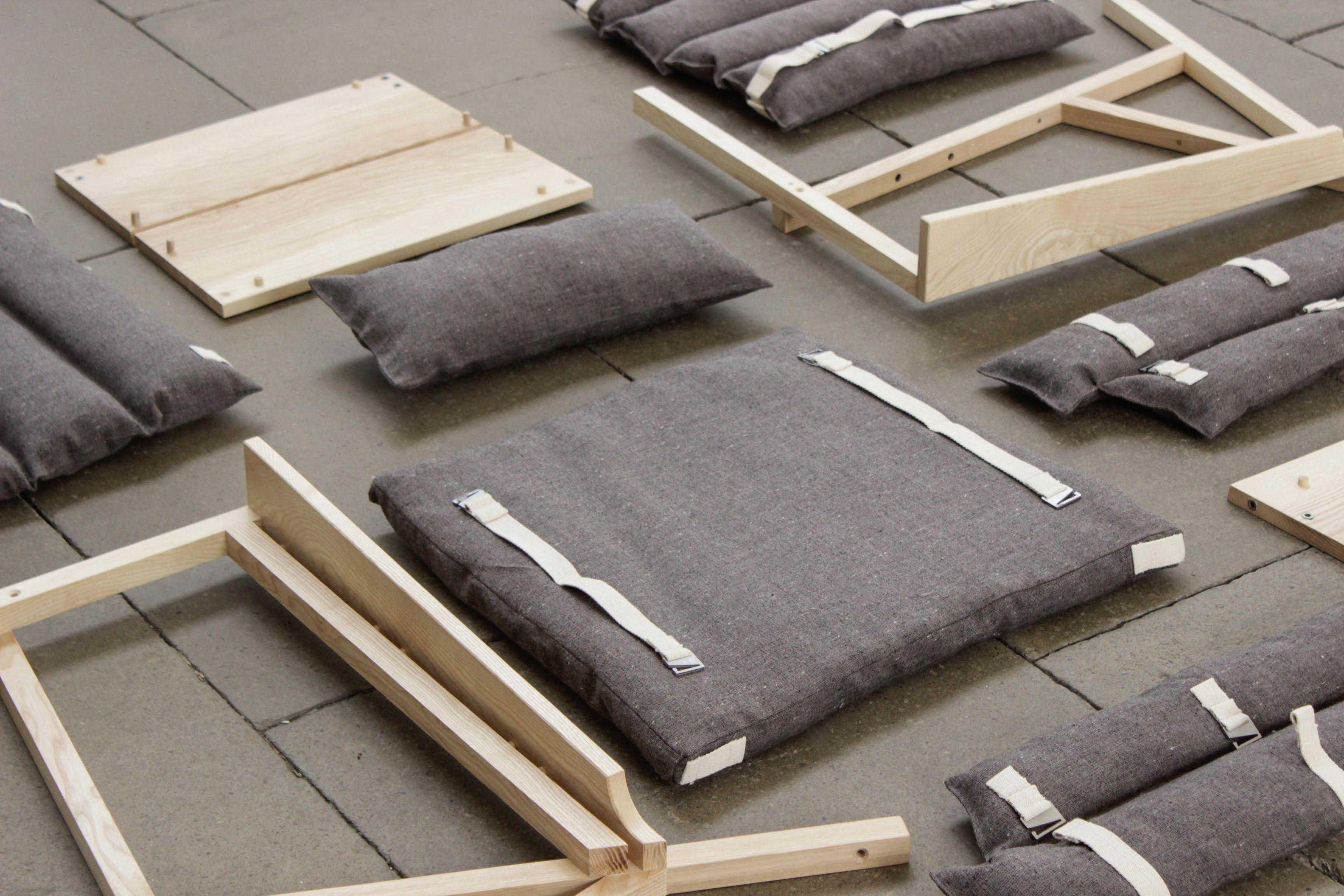
The flatpack frame reduces emissions during shipping and makes the chair far more suited for moving home and smaller modern homes such as flats.
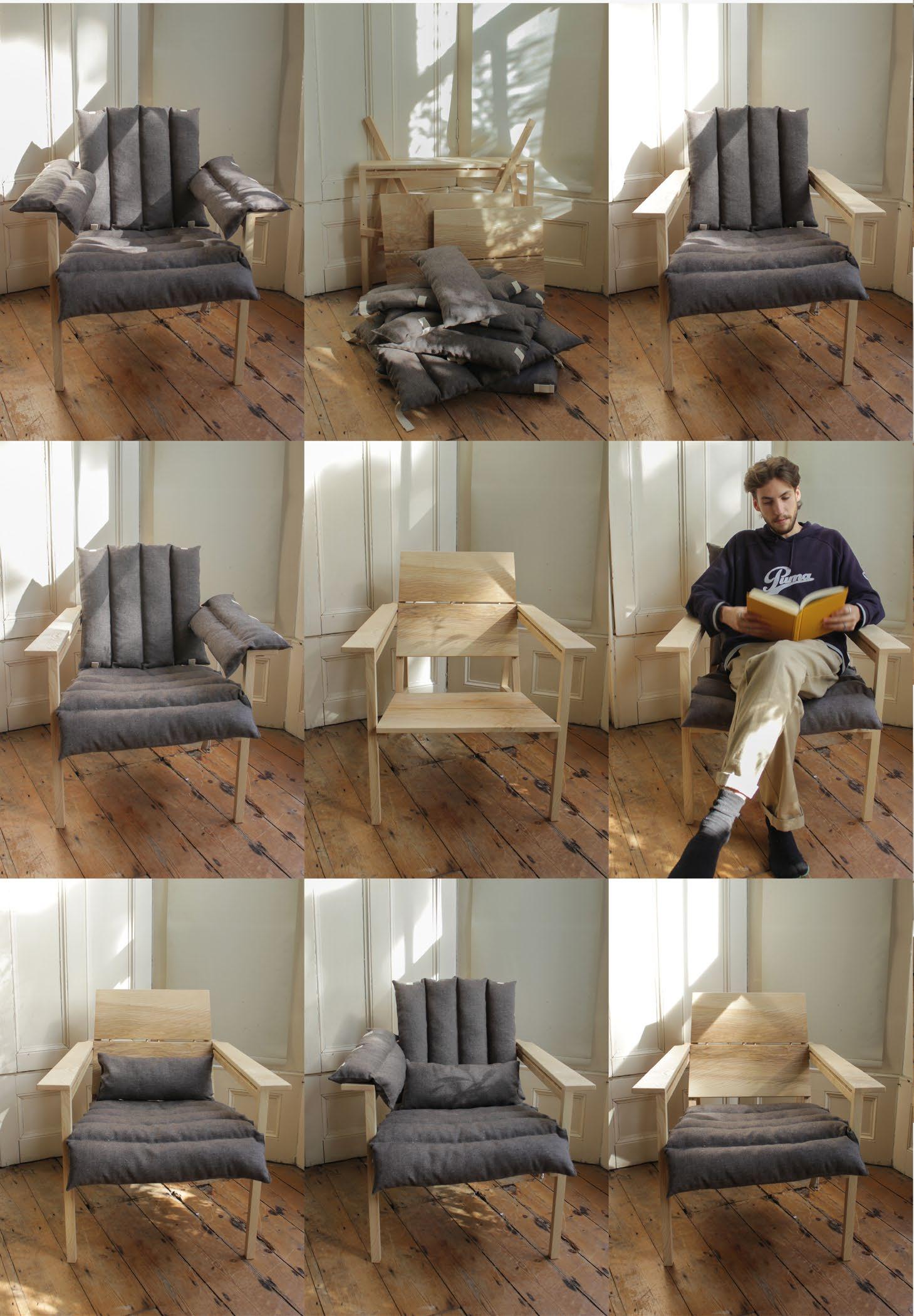
Awarded the MaDE Certificate for Excellent Consideration of Sustainable Materials@NewDesigners2022.
ALUMINIU.MForMagis.
Brief: Create an heirloom product that fits within the circular economy and reflects Magis’ nature of pushing boundaries.
Outcome: A collection of homewares, all made from 300g of aluminium that utilise the endlessly recyclable properties of aluminium for a material deposit scheme. The system encourages the user to return and reuse the material the products are made from by putting a tangible price on the material they return, introducing the customer into the circular economy as an active stakeholder rather than a passive
consumer..

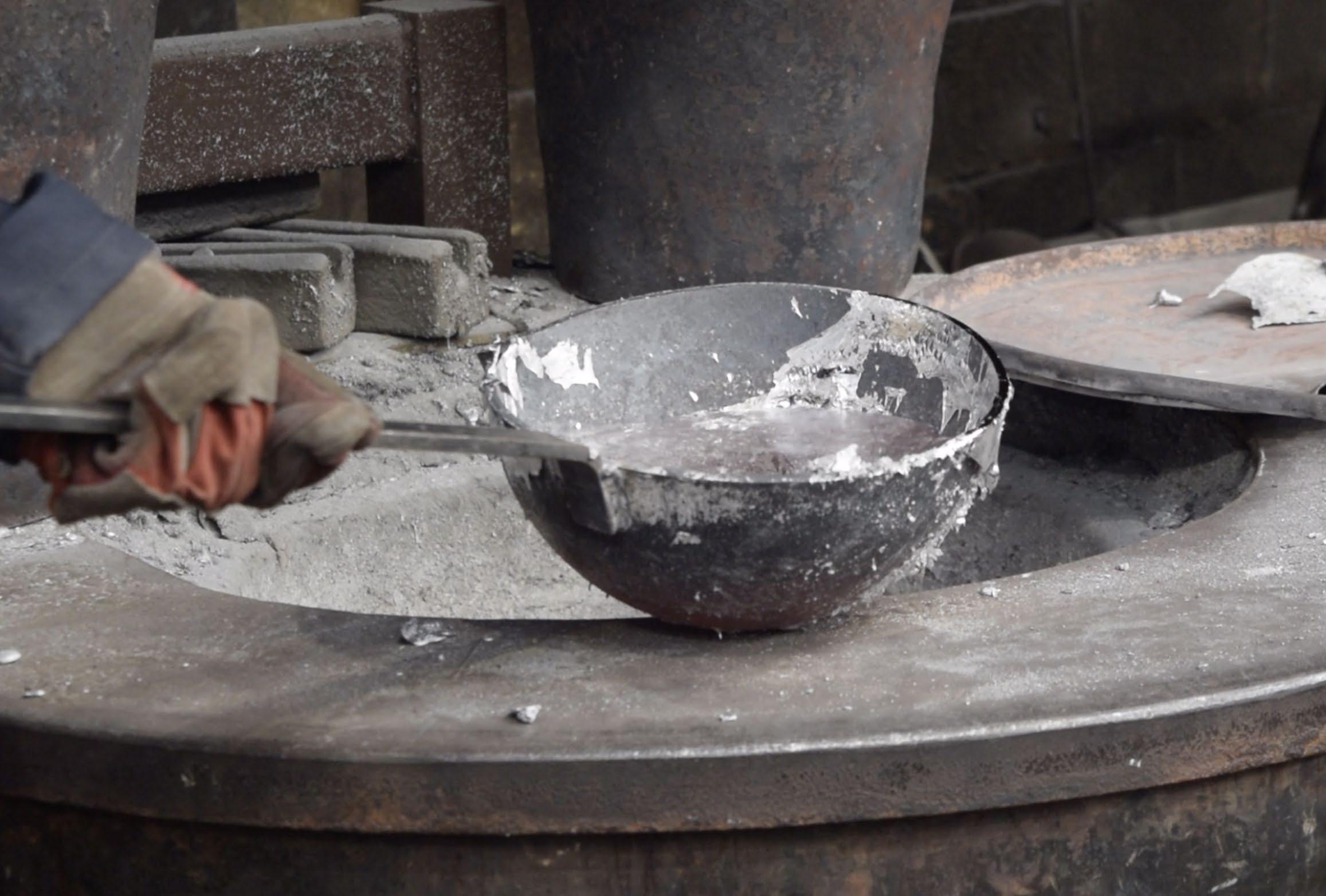
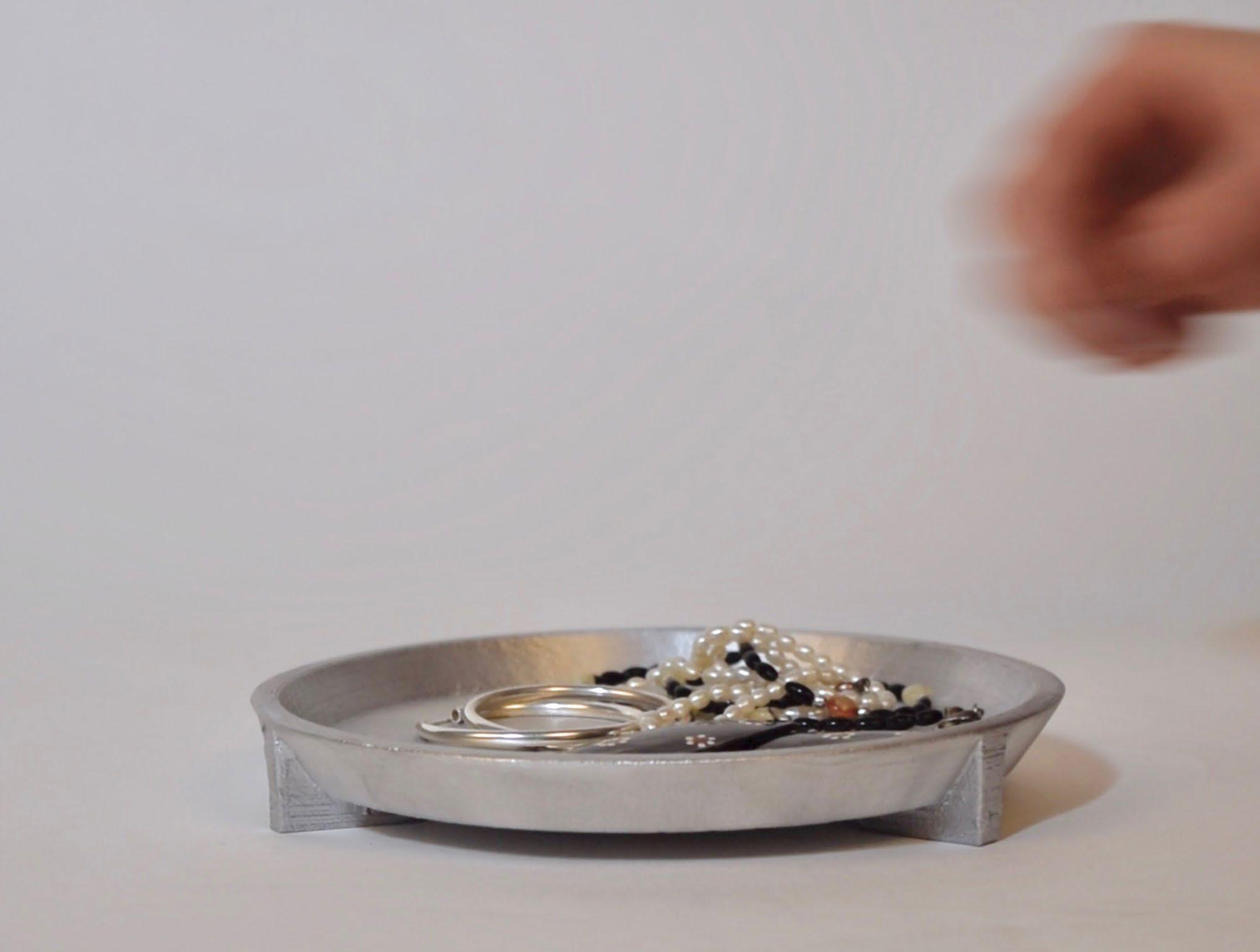
InCONTEXTaperiod where the circular economy is becoming ever more common, how can we encourage users to return their old products, and introduce them as a benefiting stakeholder into the supply chain?
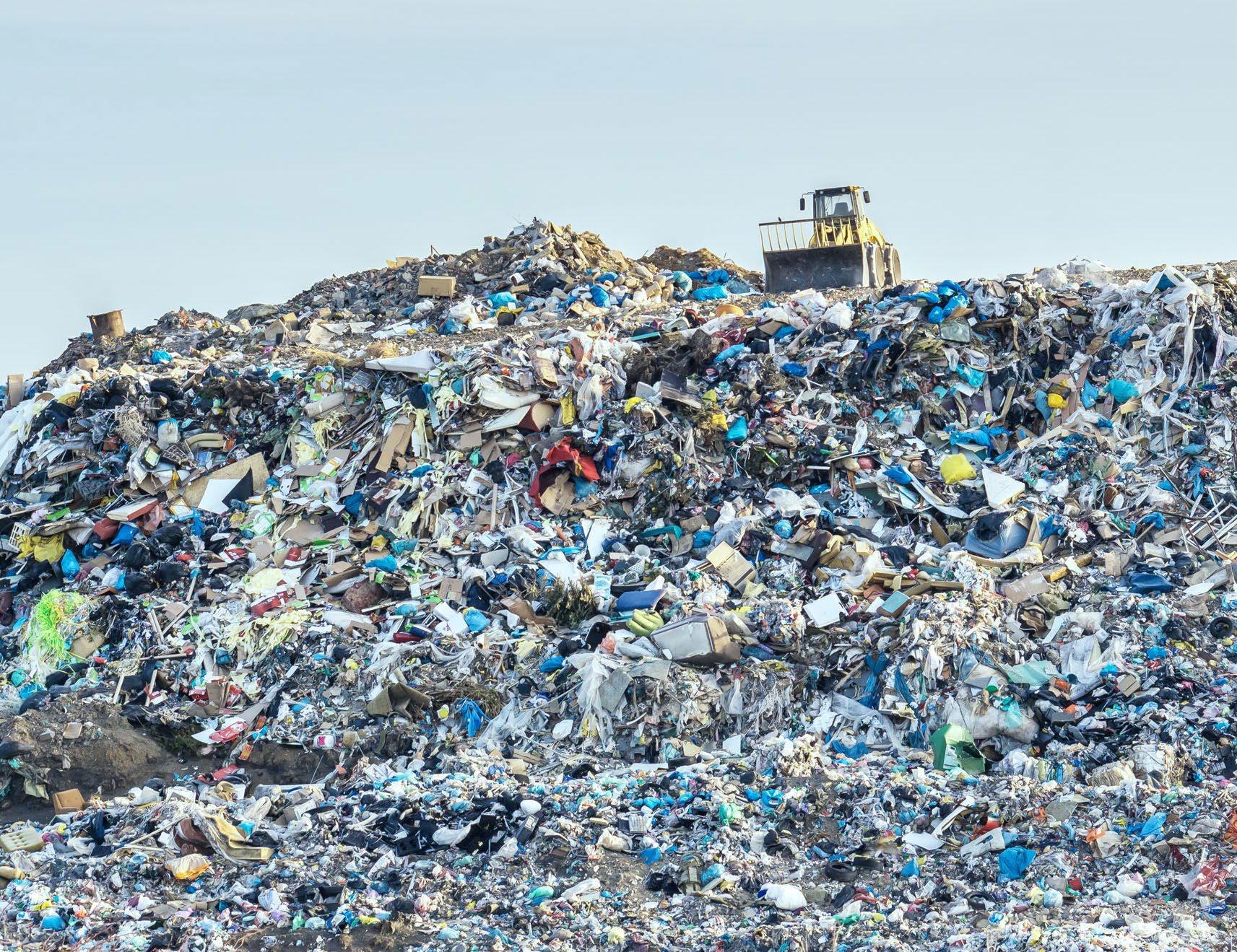
In a culture where new objects are bought before the old one is broken, how do we allow for the experience of something new without creating waste from discarded items?
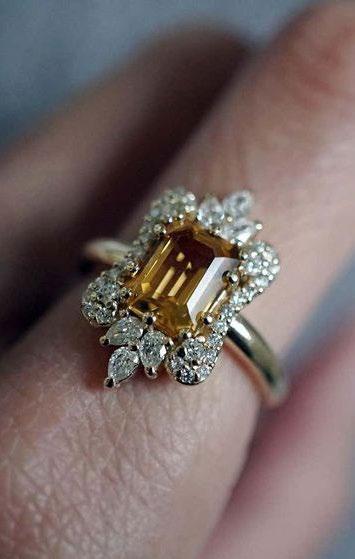
DepositCompany.MoneyReturned.
*If product has been returned, not made from original ingot. Closed Proposal.Loop
an Ingot
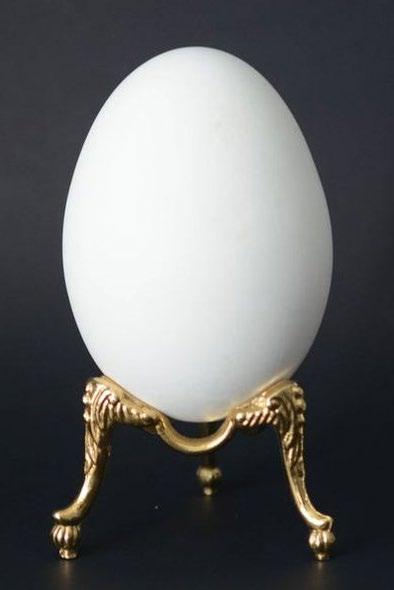
Foundry Cast Product From Old Material.
Gift or Buy Product.a IncludesPriceDeposit. Back to
New
RESEARCH Research was conducted into what increases the perceived value of an object, leading to a narrative that focused on elevating the piece using little legs, and creating objects which could be displayed with pride. Exploration into deposit schemes and repair shops led to the development of a system in which the material is the thing investing in, and then subsequently returned or re-purposed when the product reaches the end of it’s life. This creates a different relationship between the user and the material, encouraging them to view the material as valuable resource that they can cash in when finished with, instead of something worthless which they are likely to throw away.
Product Selected FromCatalogue.Website
Free Shipping of Material
ReachesUsesCustomerUpdatedProduct.ProductEndOfLife.
FoundryApplied.*Deposit&ShippingOptionsSelected.
MANUFACTURE
The manufacturing method used for this collection is sand casting. This method is done by creating two part moulds from a wooden pattern which molten aluminium is then poured into and left to cool, before being knocked out.
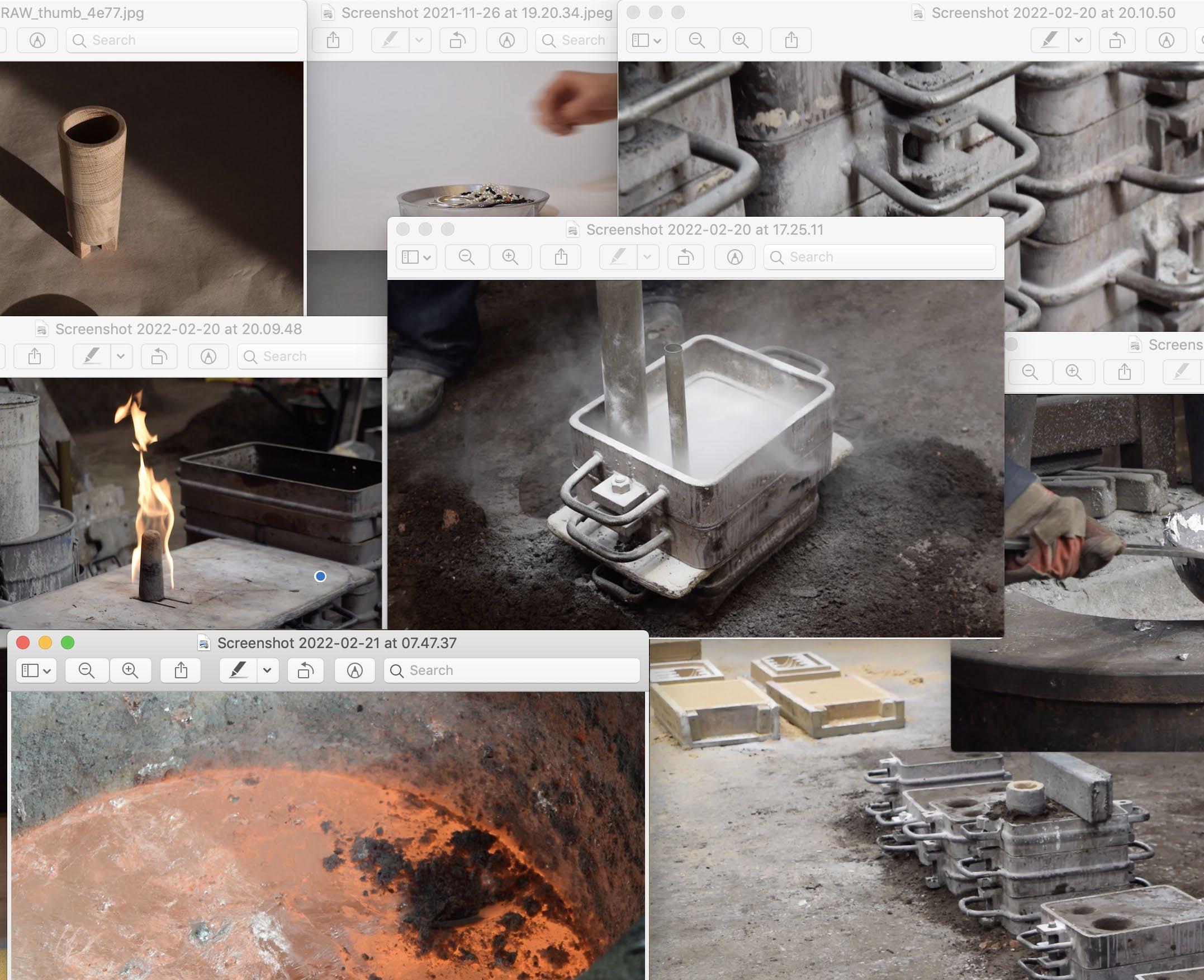
The foundry I had my pieces cast in had been using the same pile of sand for 50 years.
The process was chosen as it creates minimal waste due to the patterns, sand and excess aluminium can all be reused.
TheDURABILITYprojectaddresses
the complicated issue of durability, acknowledging that although a product can be designed and able to last forever, the user might (and often does) grow tired of the object before Thereforethis.the collection offers an everlasting investment of 300g of aluminium which can be re-cast into any of the other objects in the collection, allowing for the excitement of a new product without creating waste in the process.
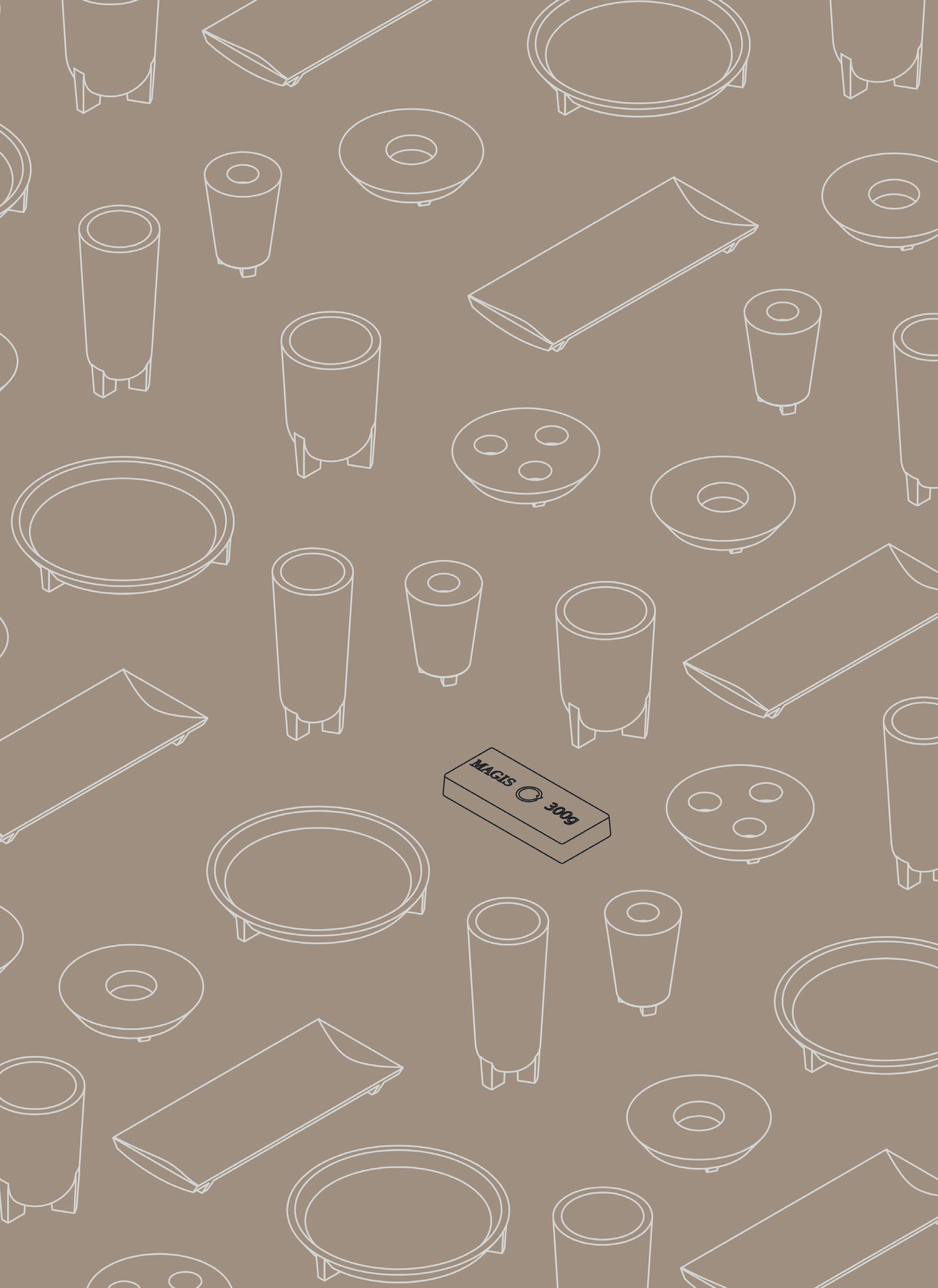
Brief: Design a system that works on the same premise as Vitsoe’s 606 Shelving System and upholds their companyethos.
THE ZEER CABINETS
ForVitsoe,withPearsonLloyd.
Outcome: A set of cabinets optimised for storing and preserving vegetables, based on an old traditional Nigerian “zeer pot” and wooden crate storage.
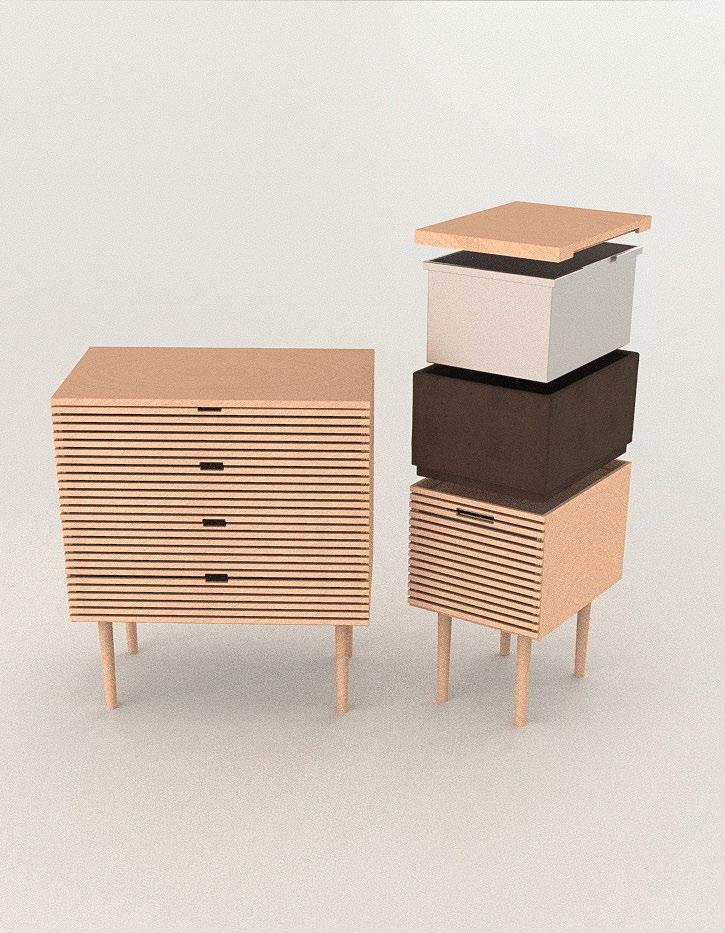

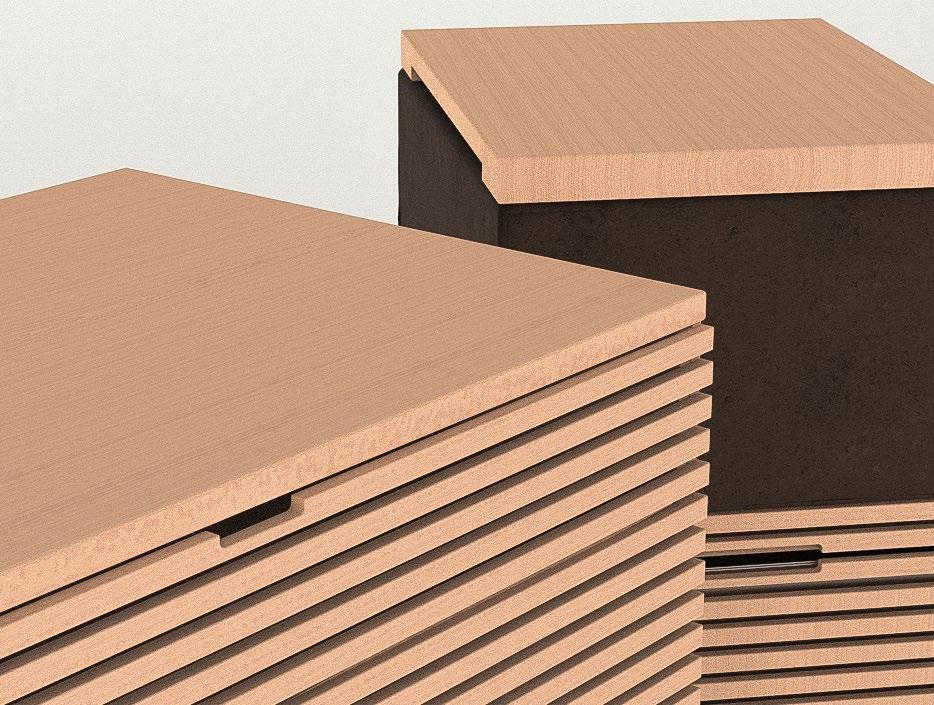
terracottaNigerianBasedINSPIRATIONontheancient“zeerpot”:apotplaced inside a larger pot. The double-wall is filled with sand which acts as a wick for water that is poured into it.

The modernised version has a metal inside, which still efficiently transfers cold into the chamber, but is also more hygienic and stops veg from getting damp.
The water then seeps through the outer pot and evaporates slowly (essentially sweating), cooling the inside pot.
The wooden frame was inspired by Scandinavian dressers, and is designed to let the veg inside breathe while keeping it out of direct sunlight: prolonging it’s life span.
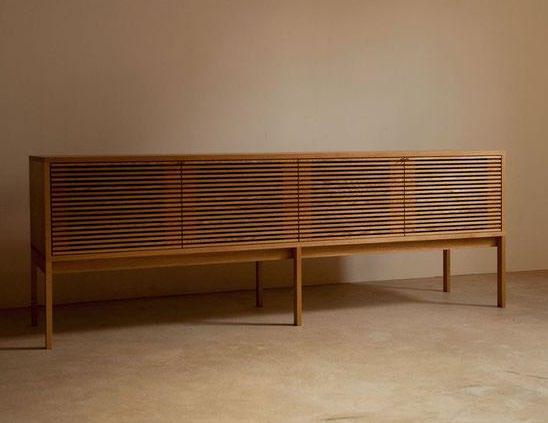
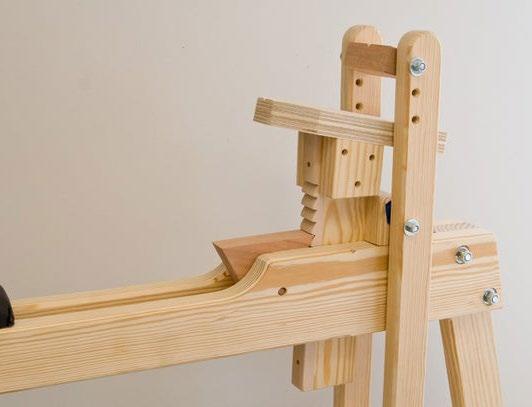
The cabinets are designed for open space living, and made to work as ambiguous stand alone pieces rather than specifically kitchen furniture, so they can be put anywhere in house.the
The legs are taller than an average kitchen counter to make the pieces feel more visuallylight.
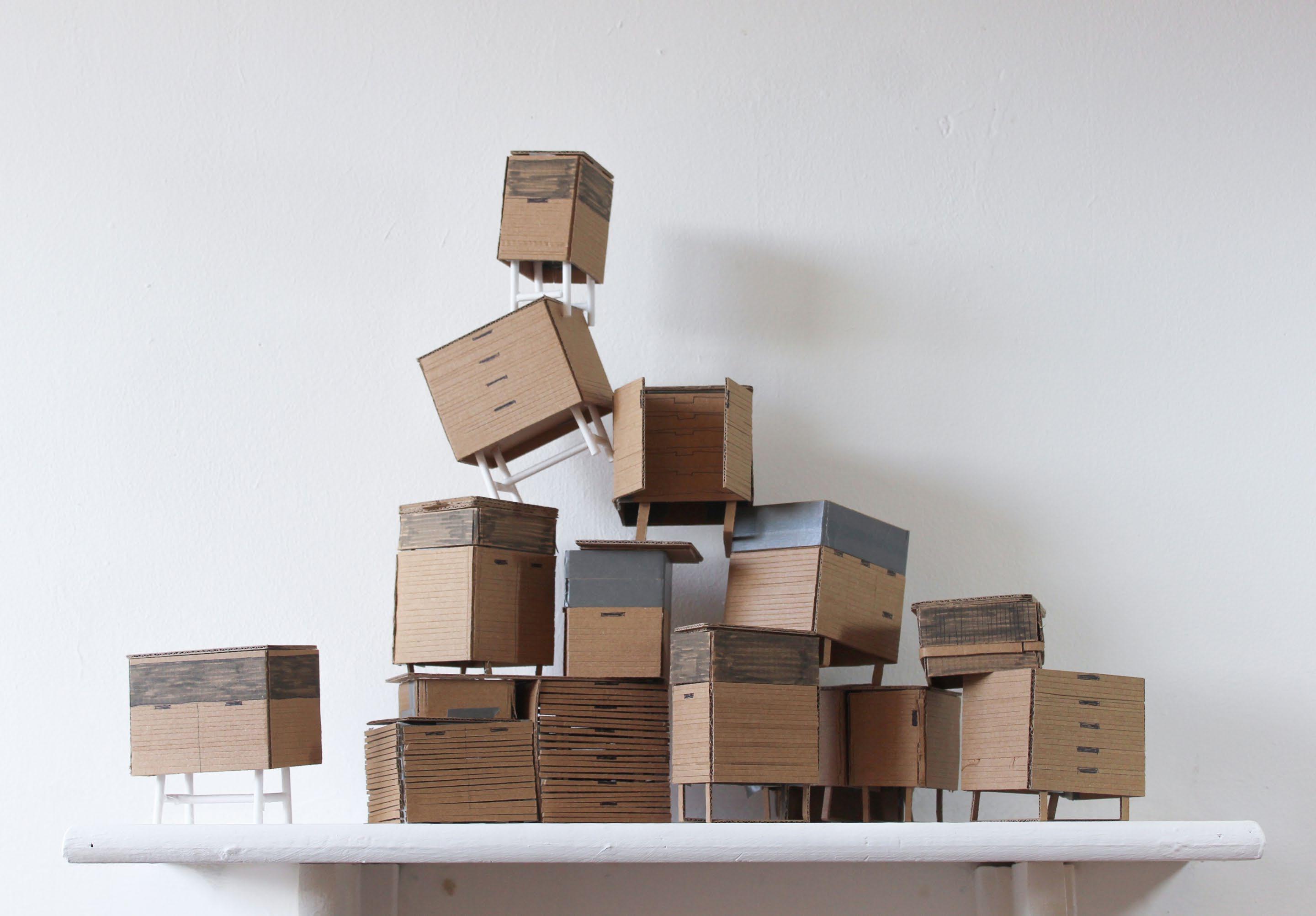
DESIGN
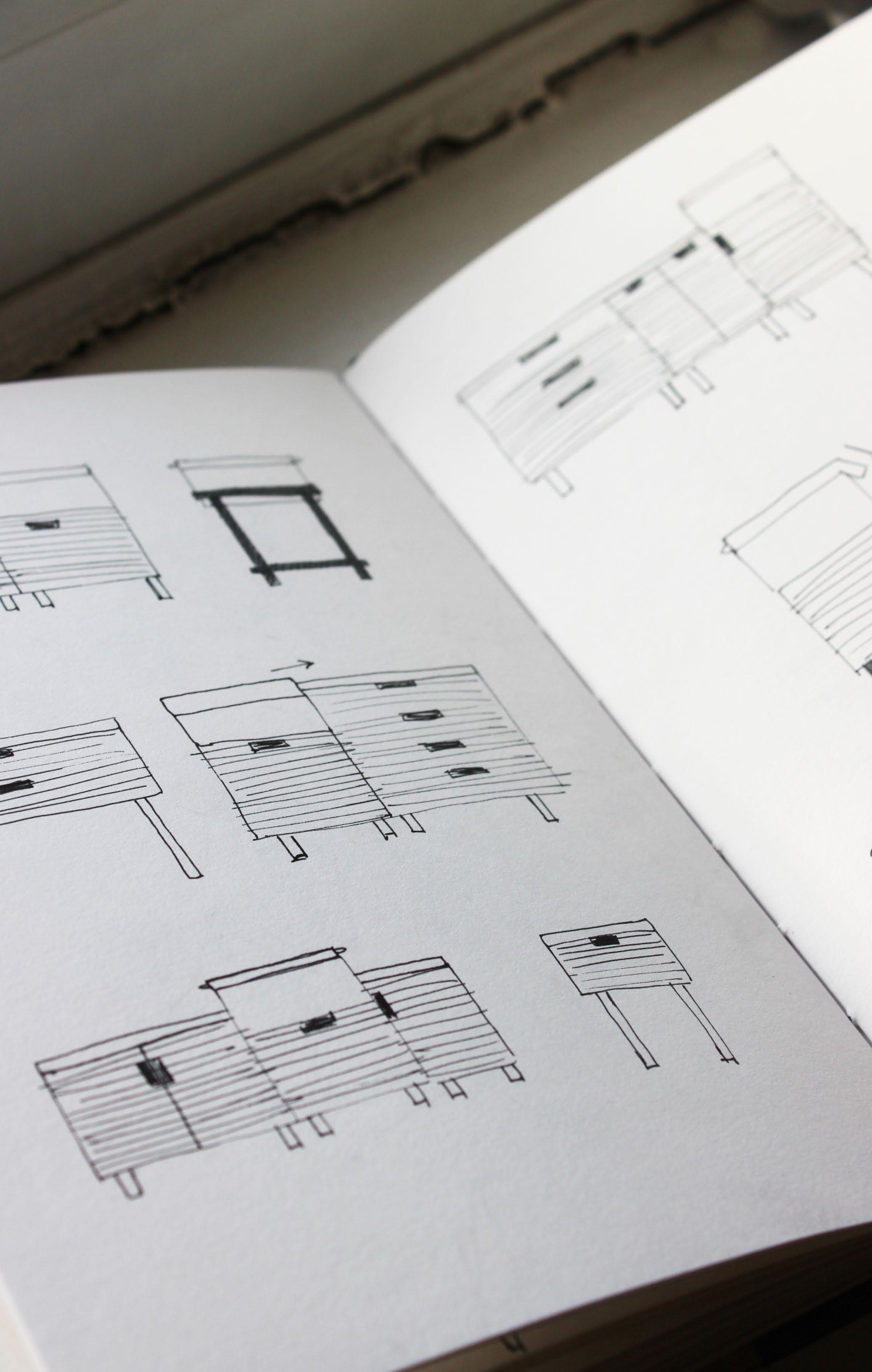
MATERIALS
Maple was used as it’s scratch resistant, and the closed grained makes it very good at blocking bacteria, moisture,stains.and Black terracotta was chosen over orange as it’s less vibrant, and therefore is more versatile in different environments, not going “out of fashion”.
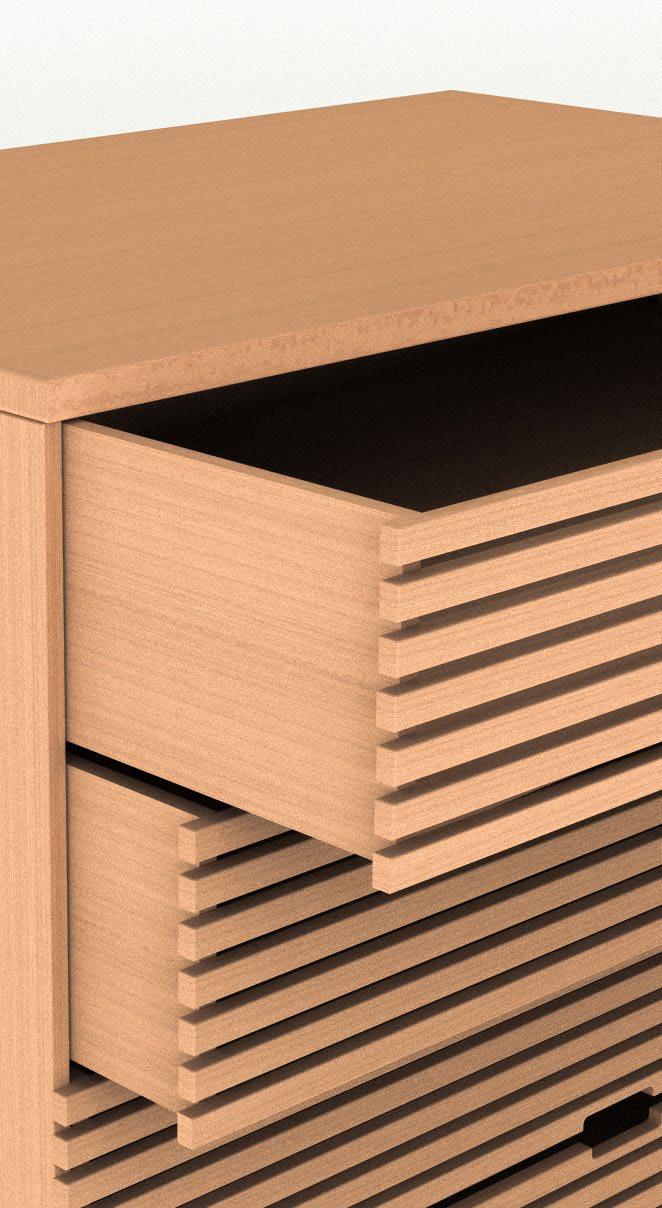
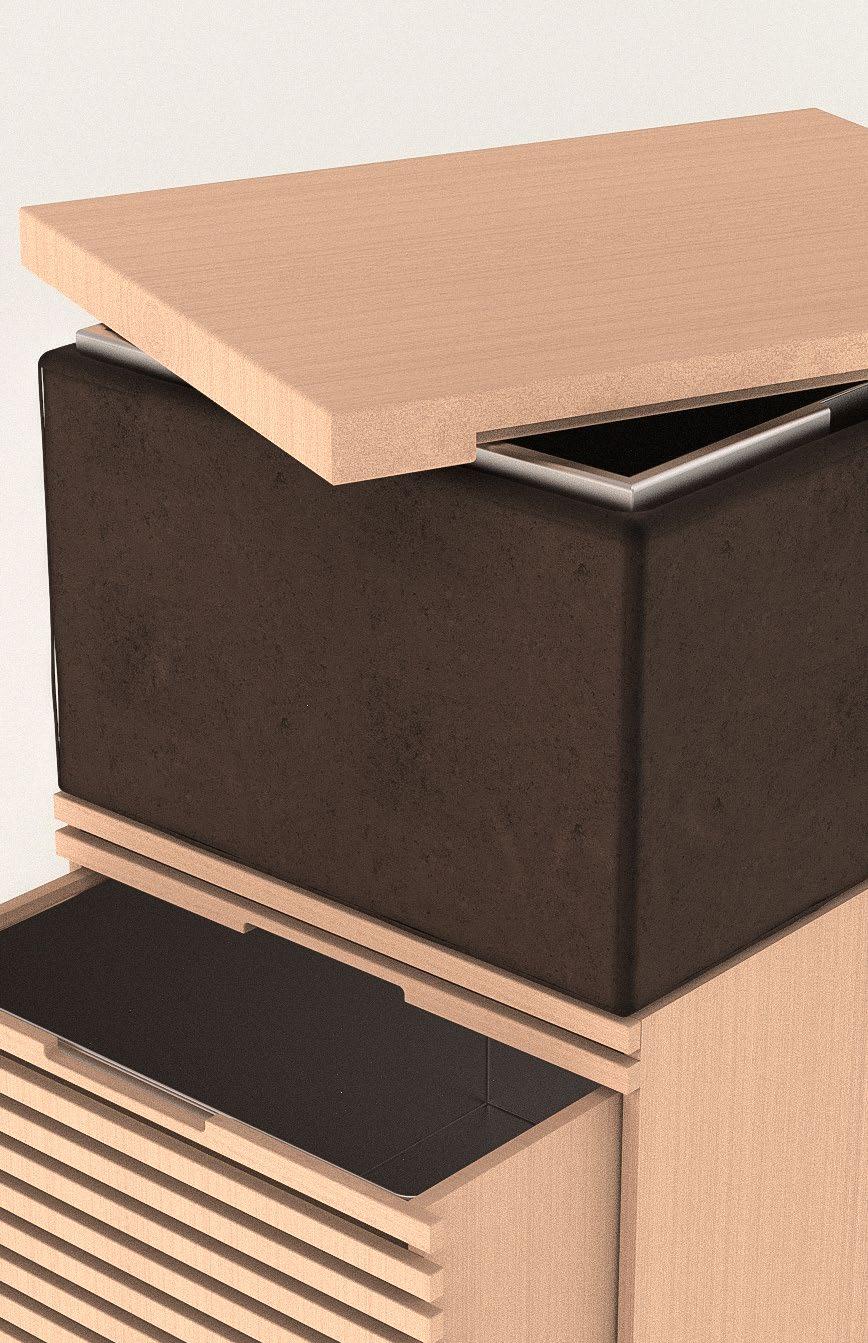
TheDIMENSIONSheightisstandard counter-top height (900mm) for easy food prep, and the lid doubles as a chopping board, with a food waste bin underneath the board that offcuts can be scraped straight into from the chopping board.
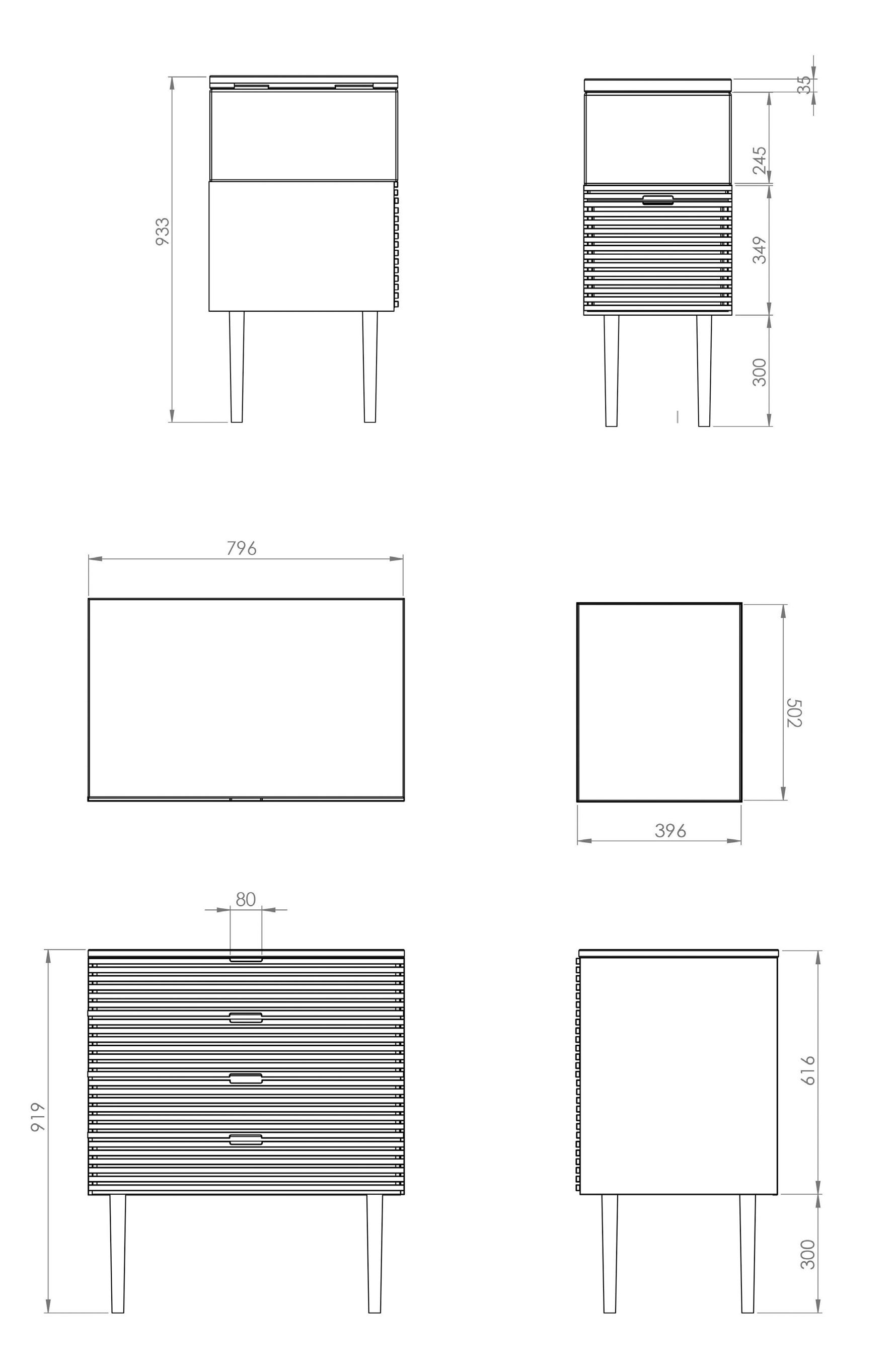
Brief: Create a wooden piece for SCP’s Boxed Collection, that can be carried home under someone’s arm as an impulse buy.
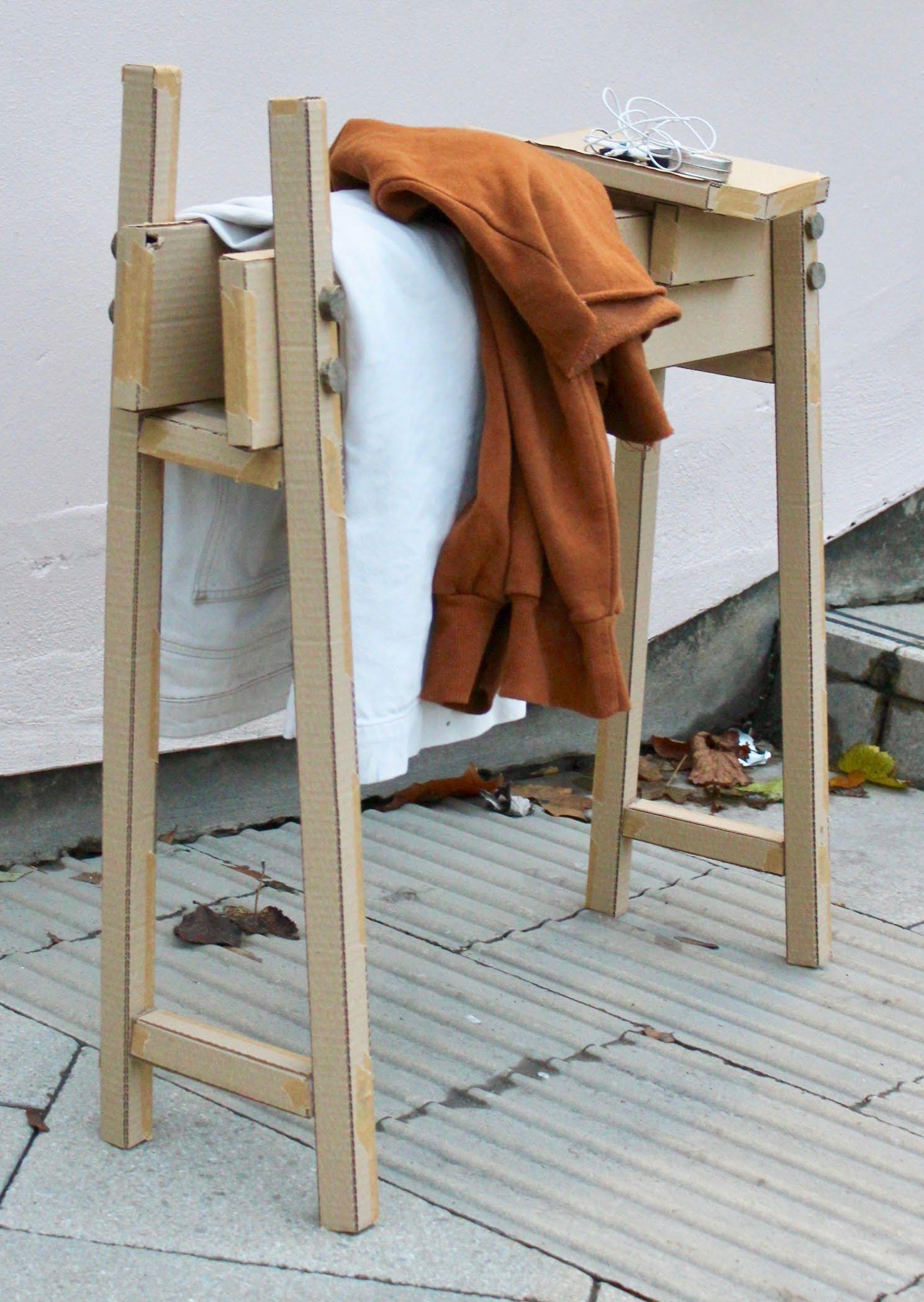
Outcome: A ‘dressing horse’ to drape your clothes over when getting changed; with bag holding ‘ears’, and a pocket contents ‘saddle’.
THE DRESSING HORSEForSCP.
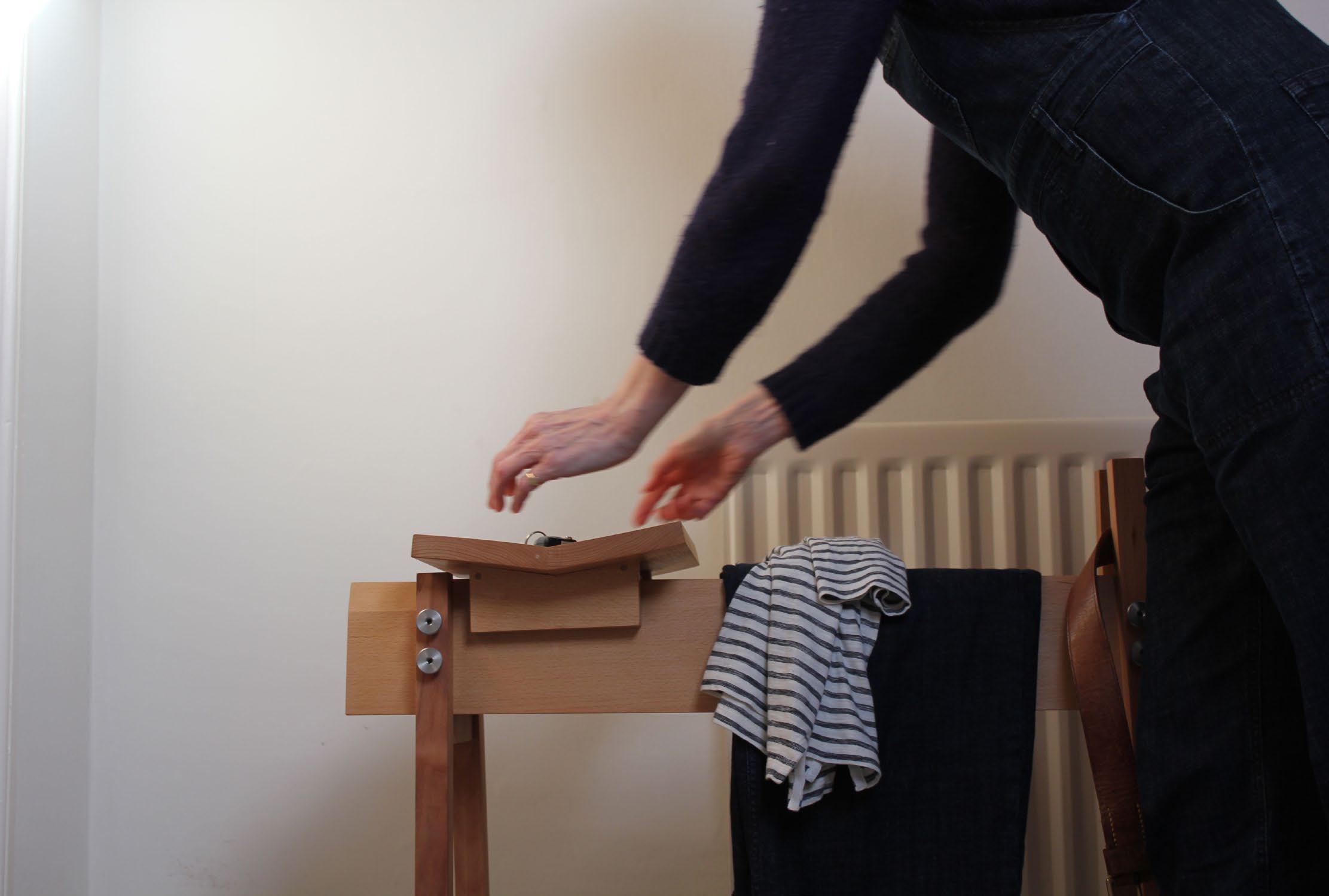
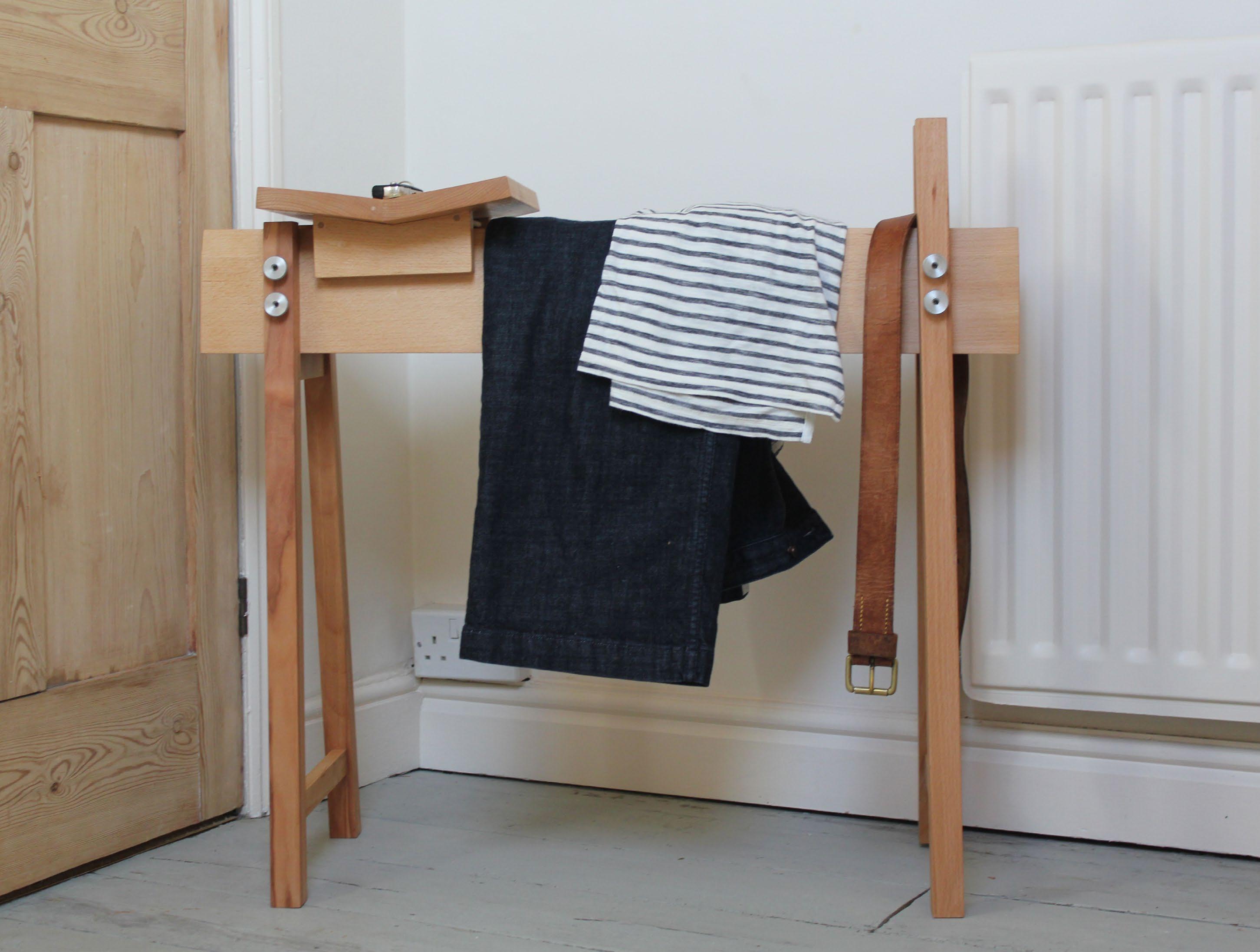
TheINSPIRATIONpiecewas inspired by the carpenter’s shave horse, with a few key features carried through to the final design: The splayed legs, the two piece main body and the asymmetric design.
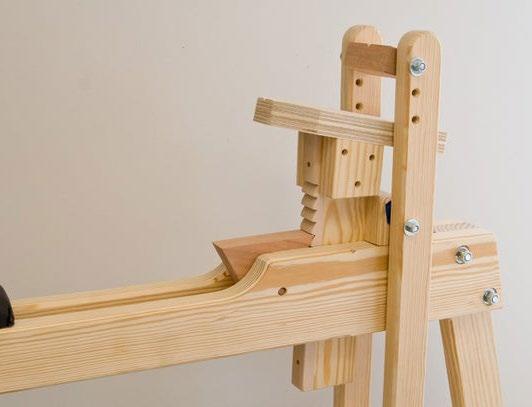
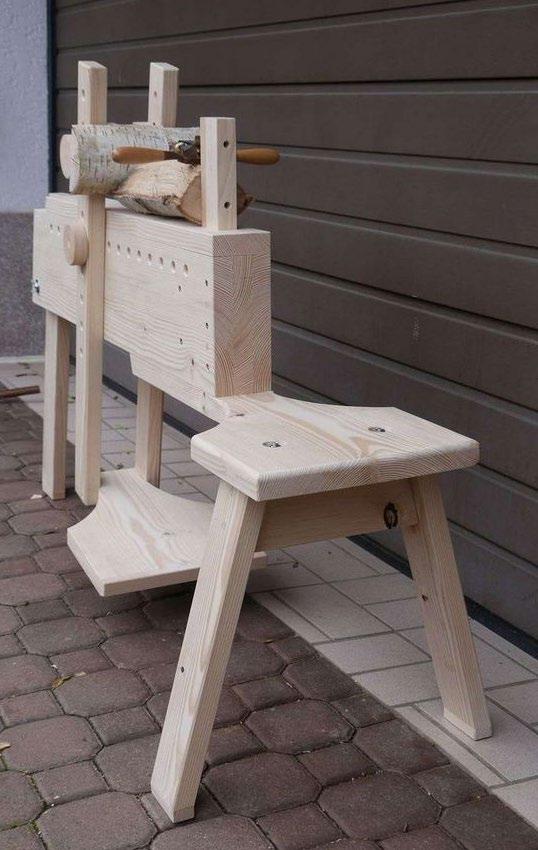
werelooking1:5throughDEVELOPMENTThefinaldesignwasdevelopedextensivemodelmaking,atscaleandproportions.Theheightandproportionsfinalisedthroughmakingseveralfullscalemodels(seetitlepage),lookingathowclothesandbagsfittedontothepiece.
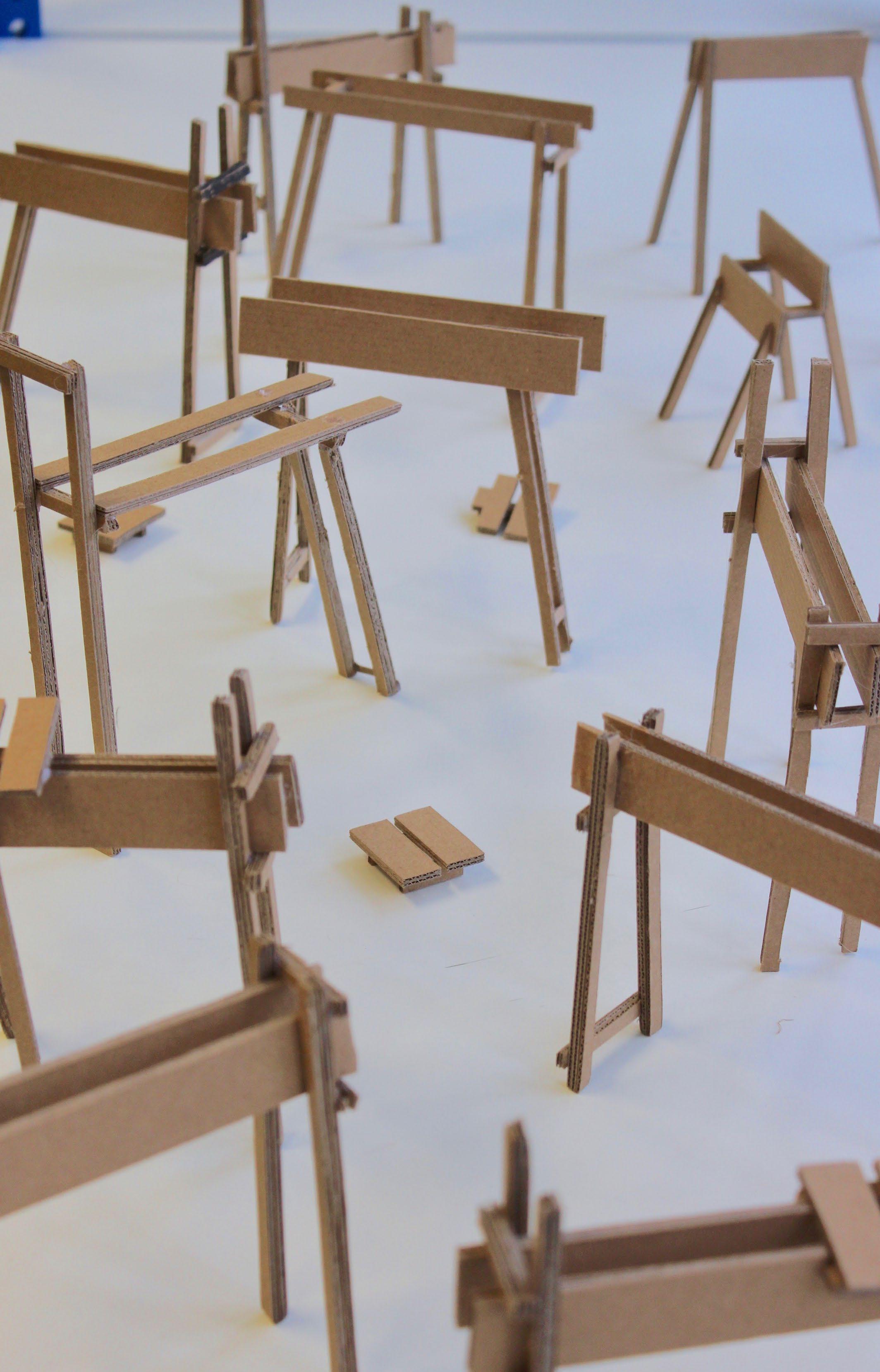

MANUFACTURE
The main frame is joined together using dominoes. This hides the joints, so the focus is not detracted from the thumb nuts, which are the main feature. The saddle was made using wood glue and clamps, and dominoed for strength.extra
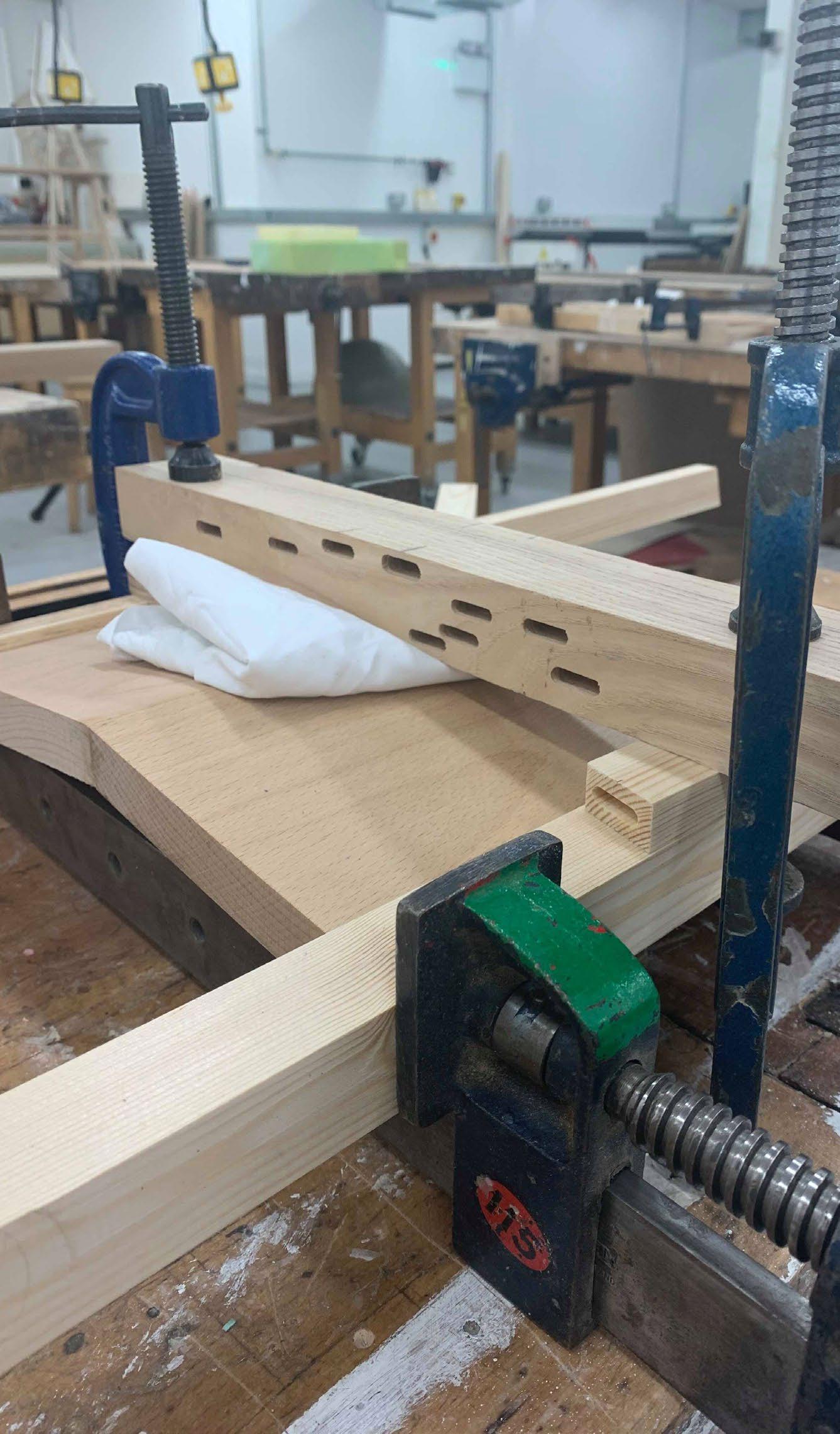
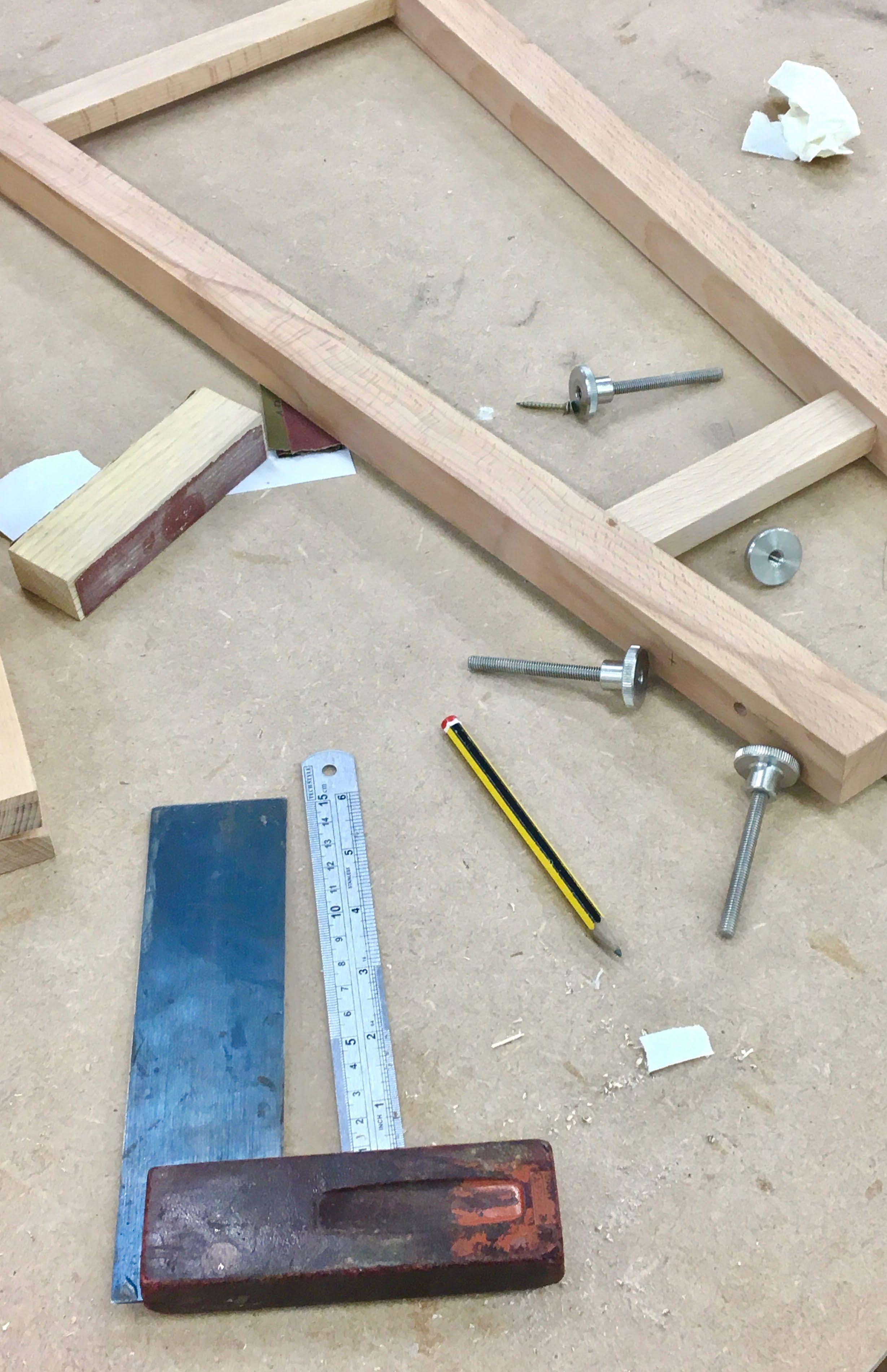
TheASSEMBLYpieceis assembled using thumb nut screws that are easy and pleasant to use, while also hinting at the industrial screws used in many shave horse designs. The top of the horizontal planks are chamfered using a router to encourage clothes to be draped over them.

Brief: Explore and experiment with a material of your choice, discovering innovative ways of creating an everyday object.
CRADLE TO CUSHIONMaterialExploration.
Outcome: A set of pillows made entirely from second hand materials. The visual aesthetic was inspired by the contrasting materials and neutral colours found on many old buildings, and the pull string was incorporated to make the piece more tactile and ergonomic.

INITIAL RESEARCH
85% of all textiles go to the dump each year (EPA). Every hour, enough unwanted clothes are collected in the US to fill three Olympic swimming(WRAP).pools Due to these facts, all the materials used for this project are second-hand clothes charity shops can’t sell due to damage that are otherwise headedlandfill.for
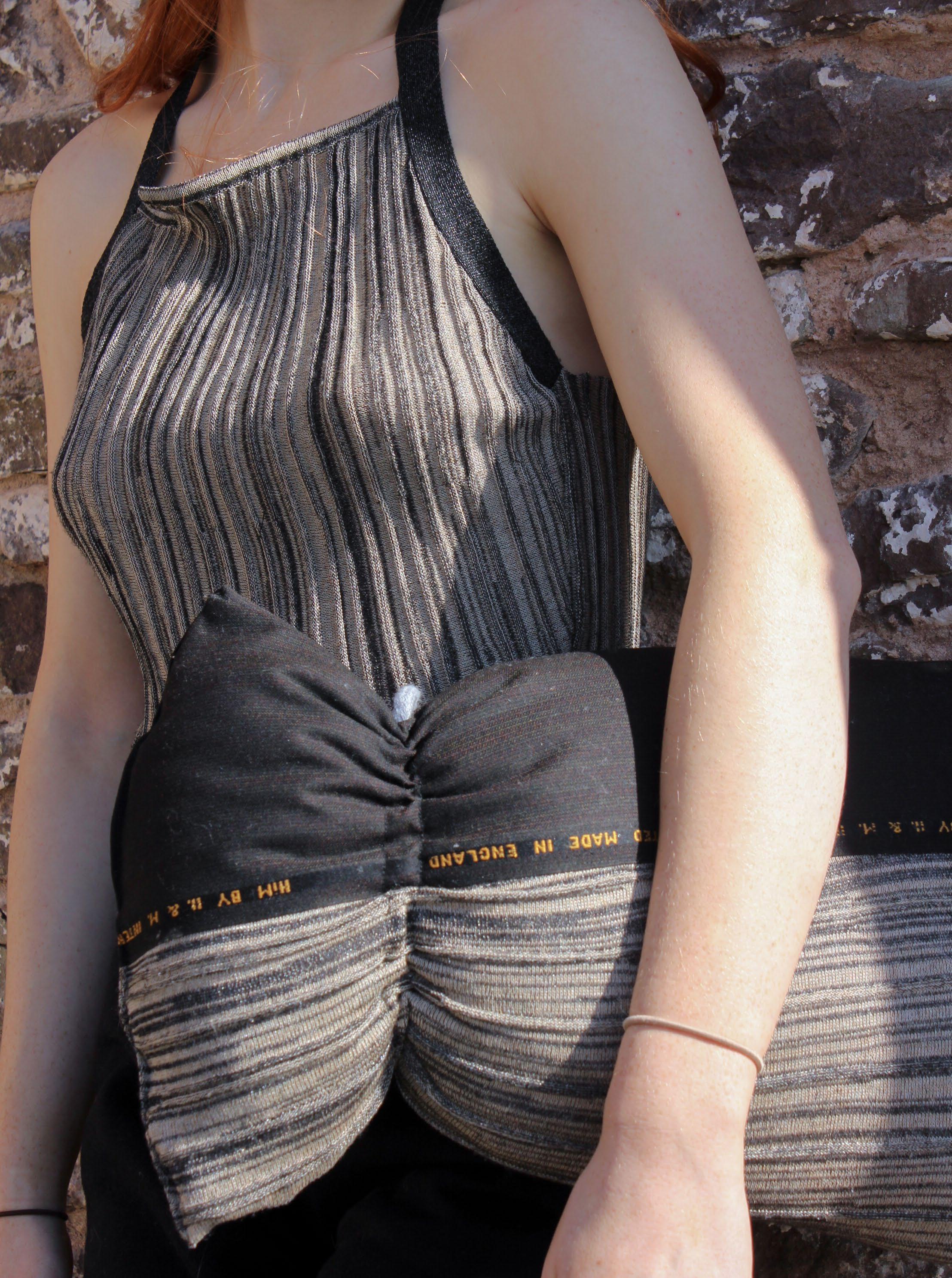
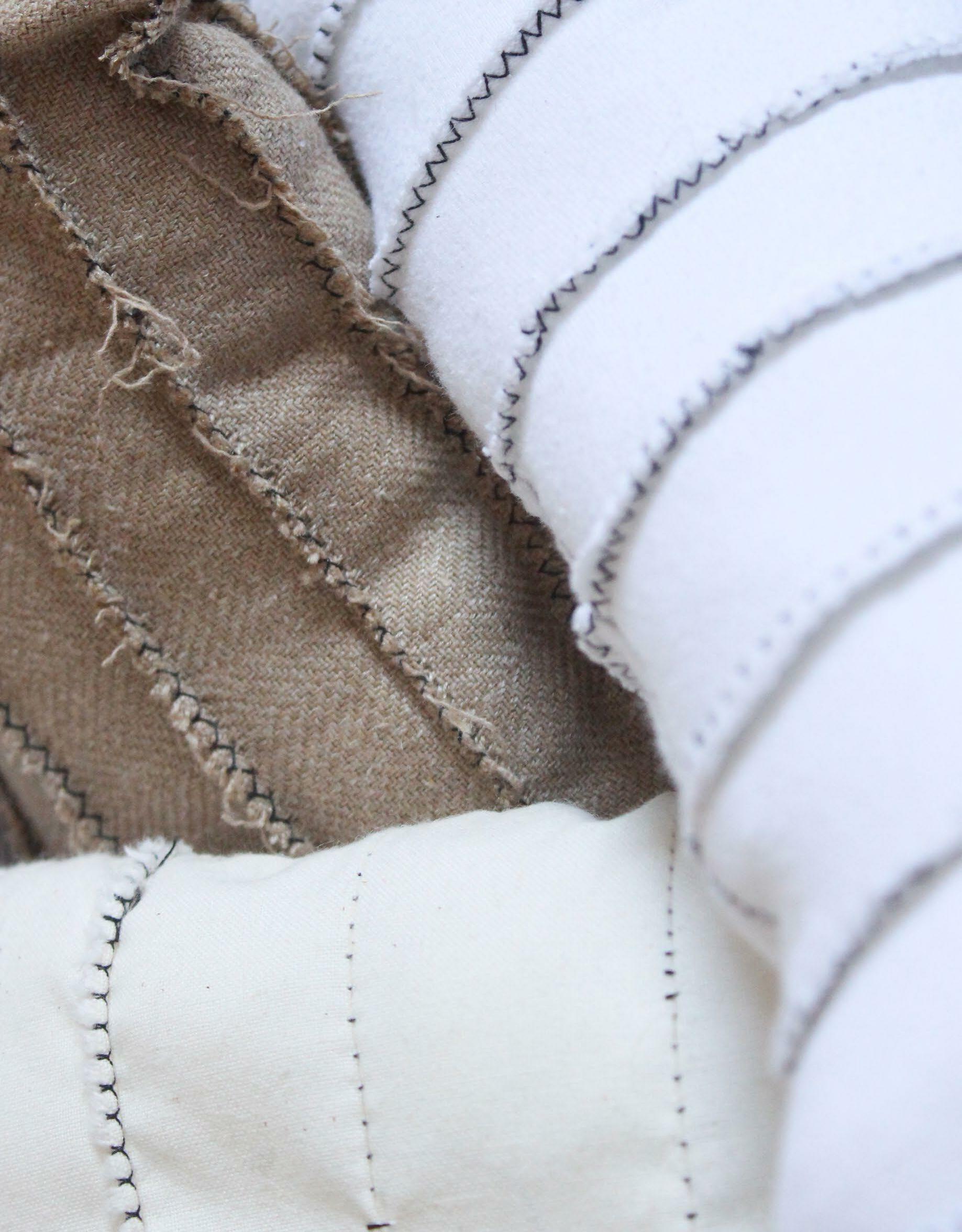
TheINSPIRATIONinitialinspiration for this piece came from looking at buildings nearby where I live and looking at what aspects appealed to me: Vertical lines, contrasting textures, neutral colours, structure with defects and Ivariation.wantedmy main influence to me something unrelated to fabric so it would push me to use the material in ways that wouldn’t normally occur to me.
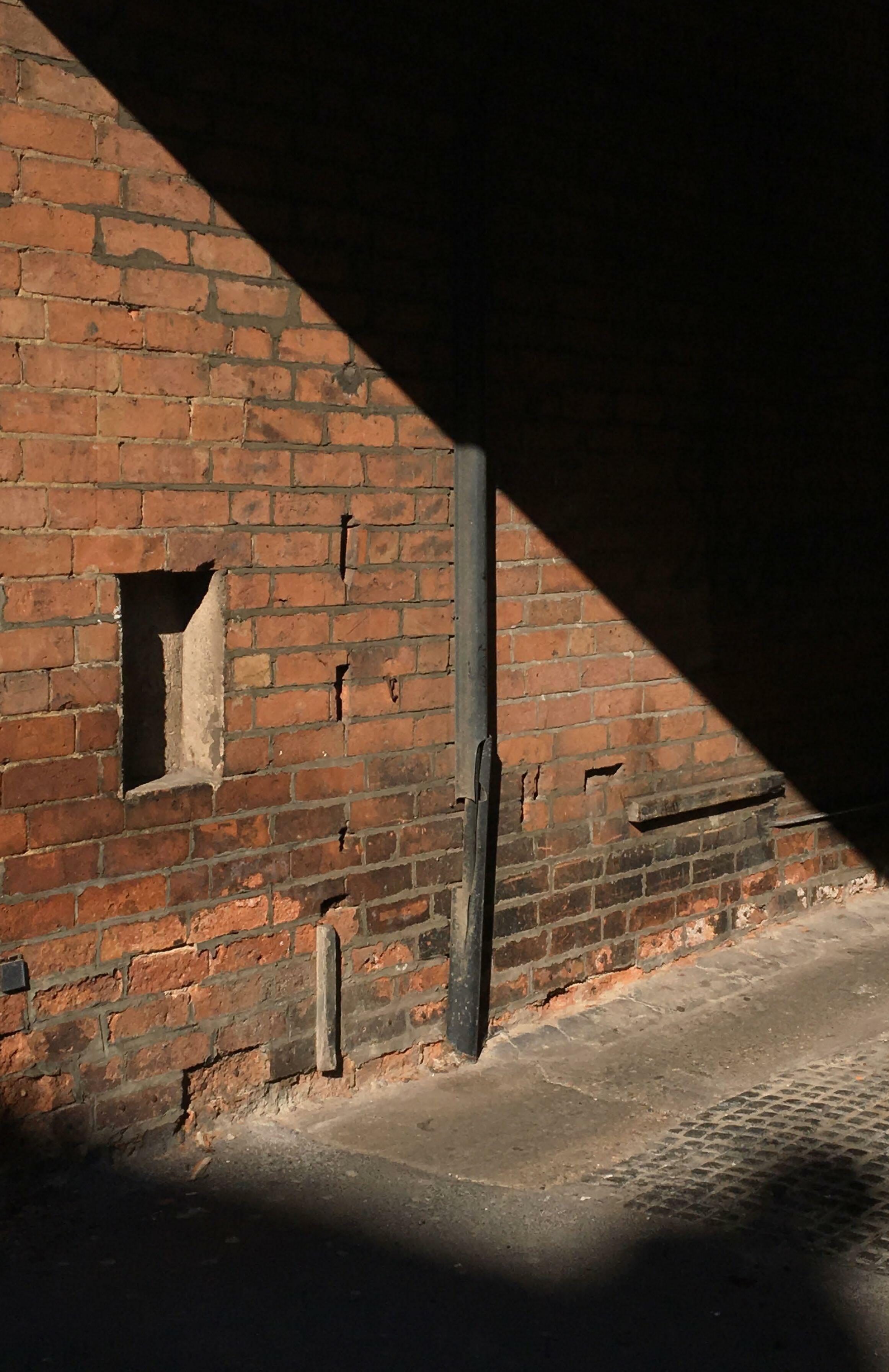
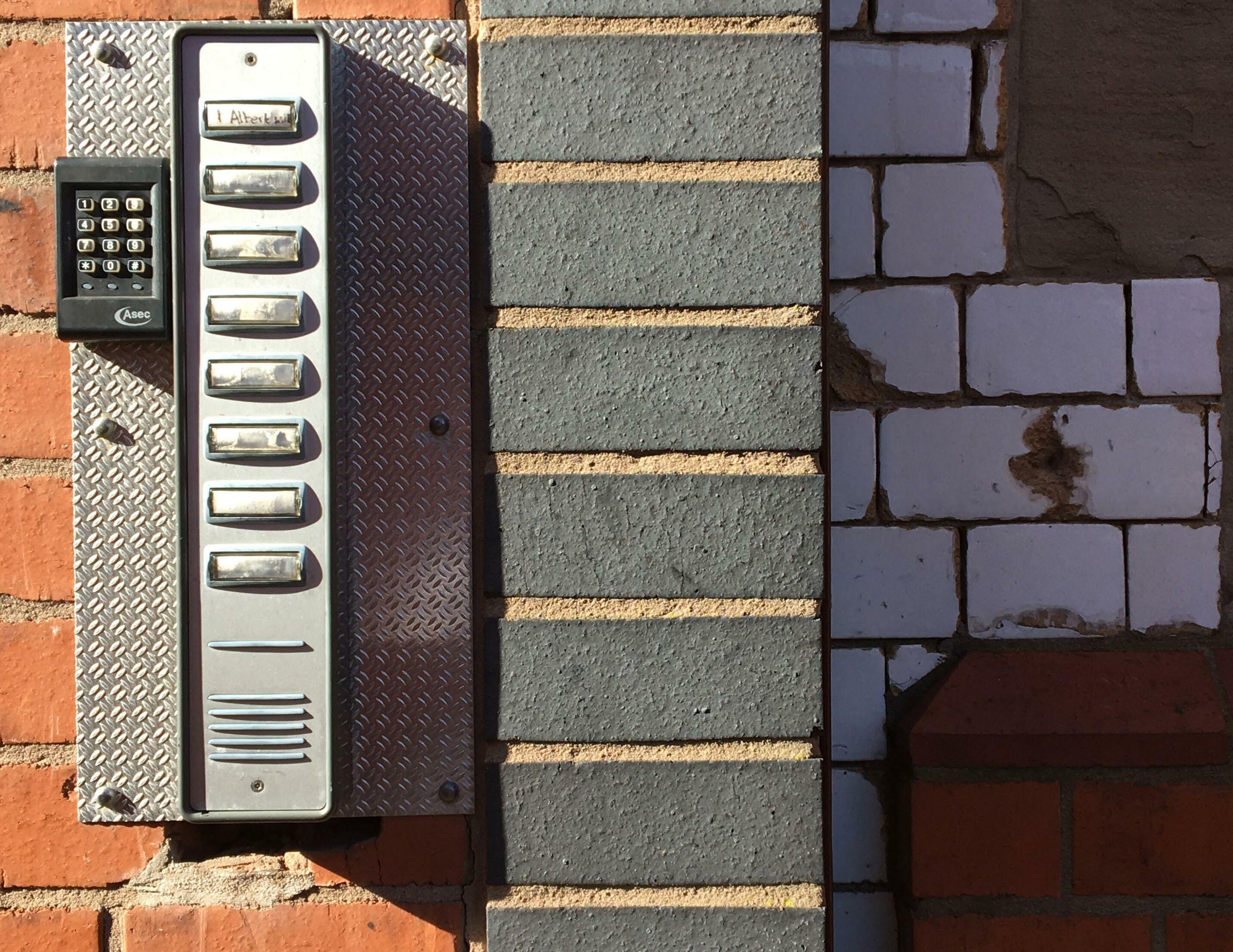
RESEARCH I researched innovative ways of using fabric, especially looking at runway fashion and patchworking techniques (right - Balenciaga). These helped inspire the way I sewed together the fabric. I also did some primary research into what makes a pillow “good”. I identified that each of my pillows had a different USP that I liked about them: The sequin one is interactive and tactile, the velvet one is soft and subtly eye catching, and my bunny is surprisingly ergonomic due to it’s shape.


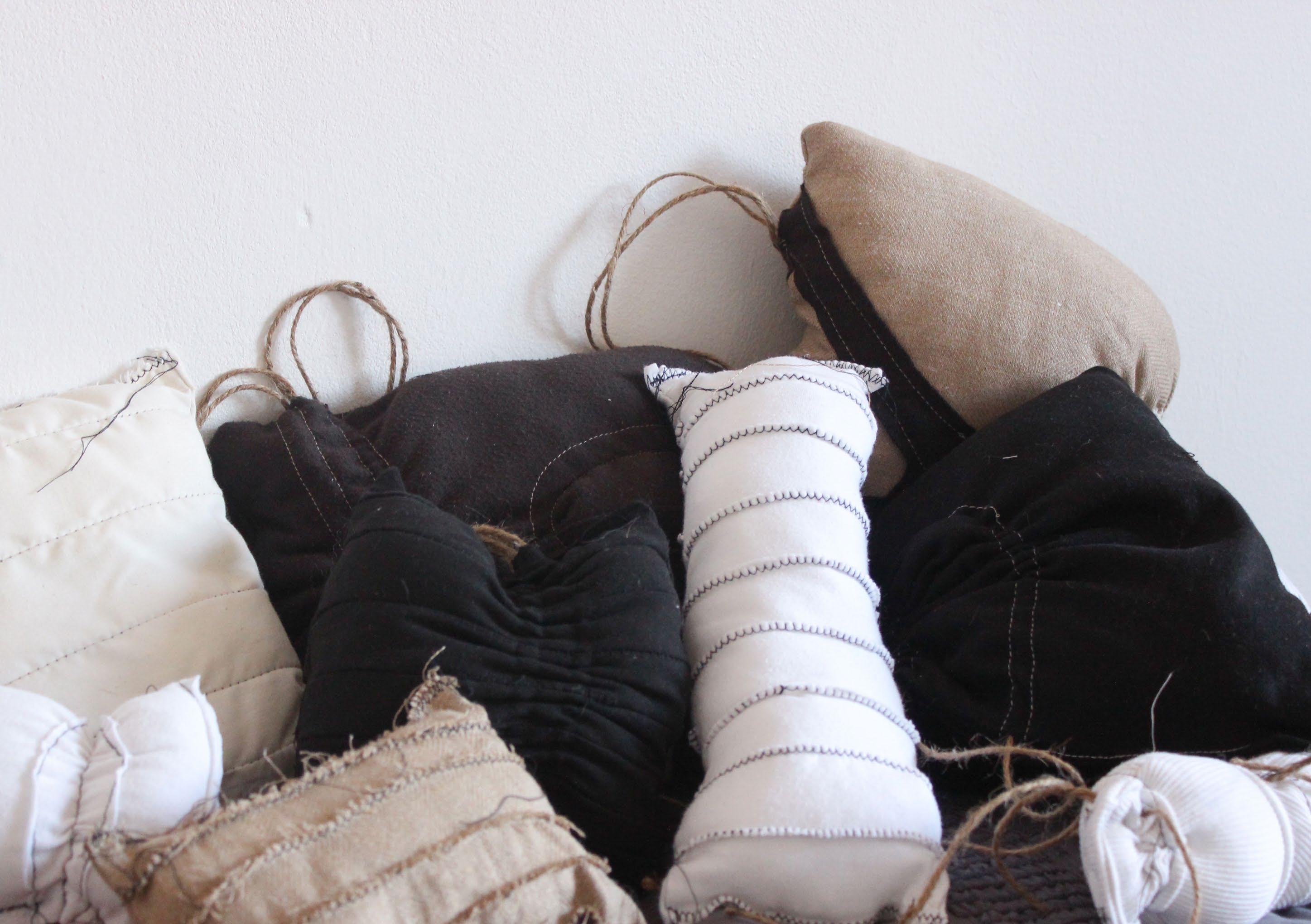
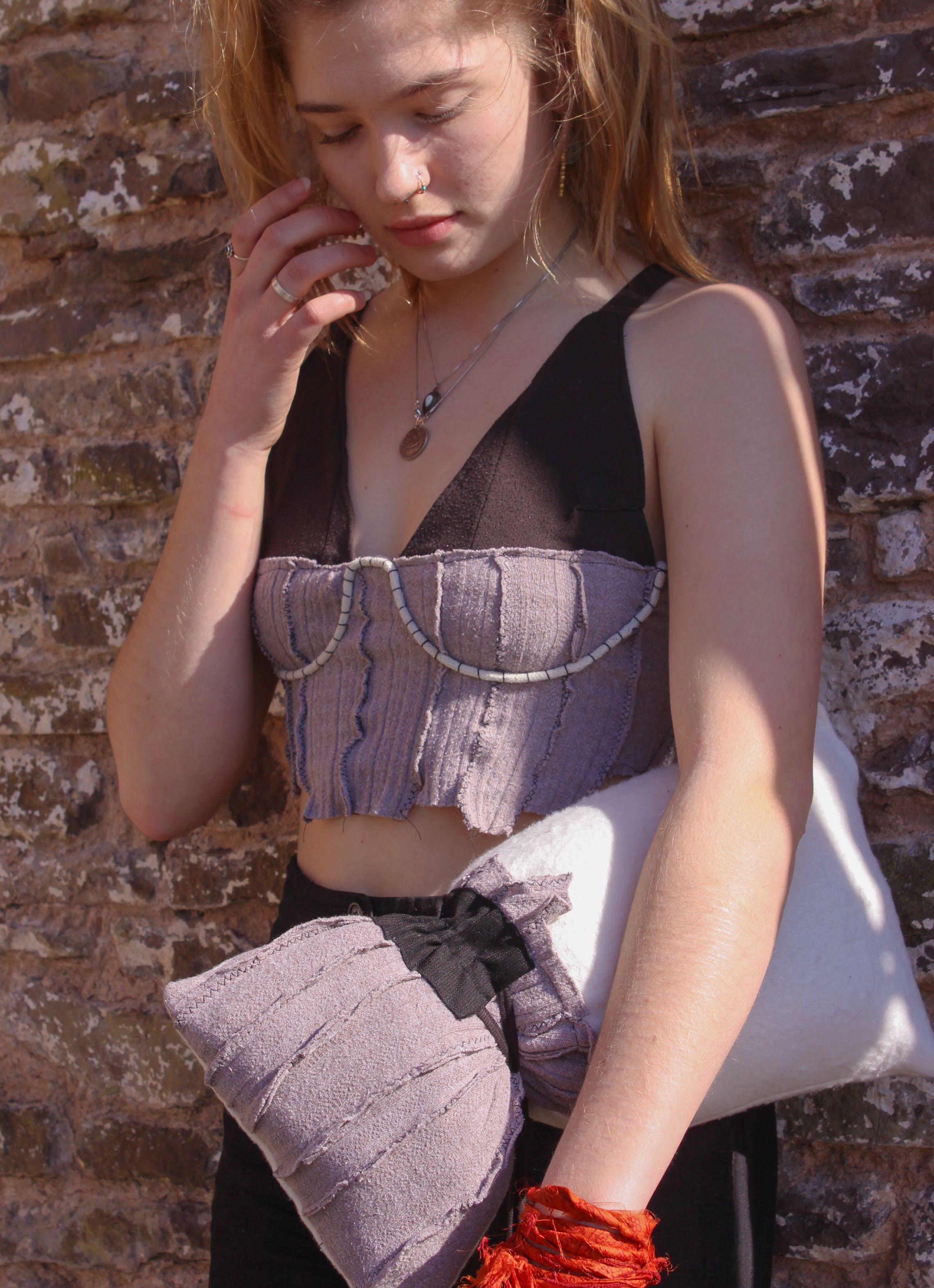
This was to further my own understanding of the material, but also look at it with fresh eyes, especially in terms of how to reuse material we often simply throw away.

outcomeThisEXPERIMENTATIONprojectwastheofseveralweeks
of experimentation (see top left a few examples of prototypes).
STRAPPED INTO LOCKDOWN promotesmanualisolationBrief:Cateringforemotionalwellbeingduringthecovid-19lockdown.Exploretheemotionalneedsofdifferentpeopleduringtheperiodofapandemic.Createaproductthatassistsandimprovestheirmentalwellbeing.Outcome:Apairoftensionstrapswithanaccompanyingthatoffers28differentalternativewaystousethem,helpingpeoplewithareastheymaybestrugglingwithduringlockdown.Ithealthymentalwellbeingthroughcreativethinking,learningnewskillsanddoingexercise(withtheassistanceofthestraps).
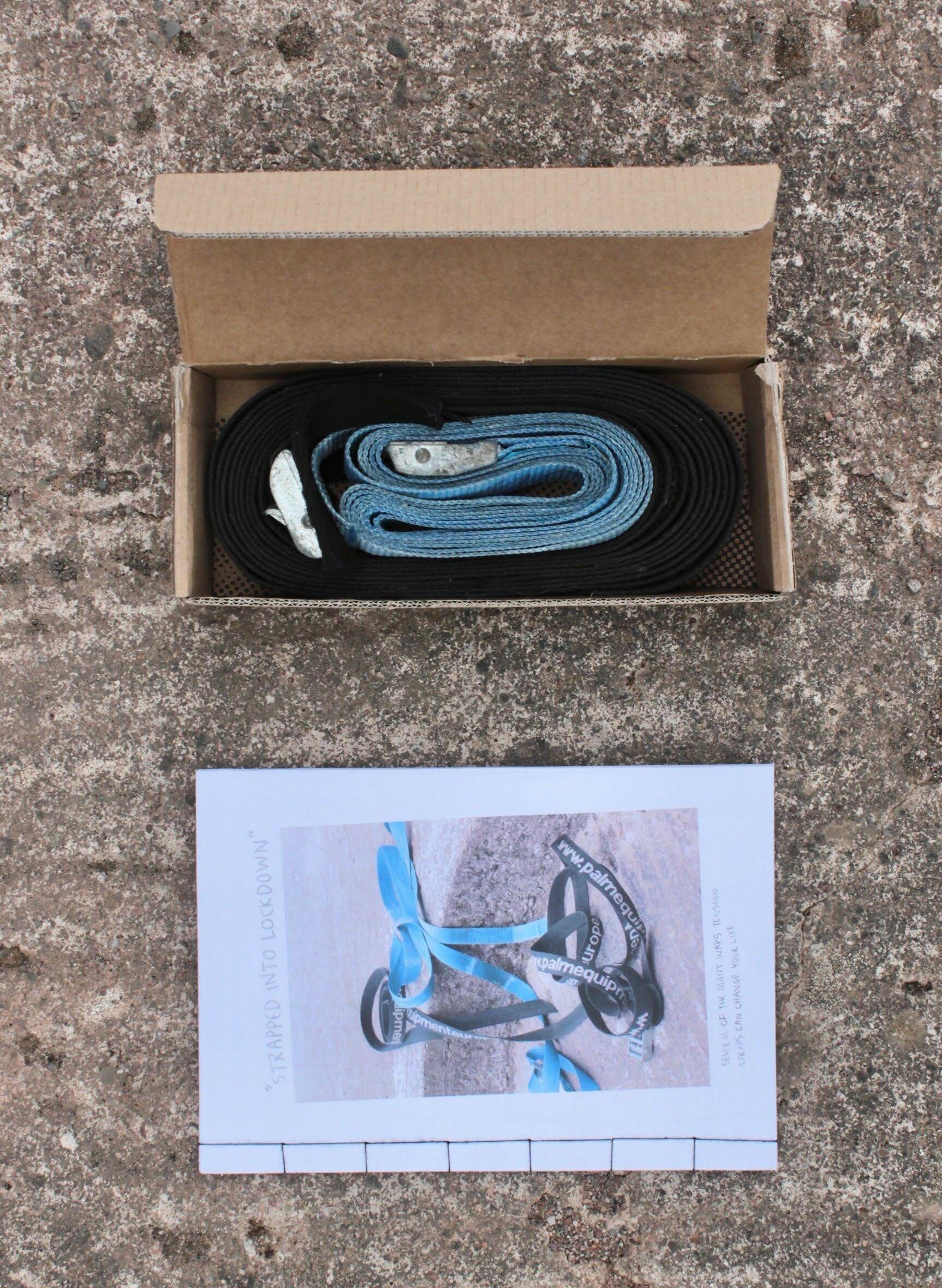
The instructions are a mixture of photos and illustrations to help make them clear. They are arranged in a continuous flow that merge the ideas together, encouraging readers to combine and think up their own ideas. The whole manual is handwritten with pencil, to make it feel less digital and more tangible; something that is becoming ever less common in this exclusively online lockdown world.
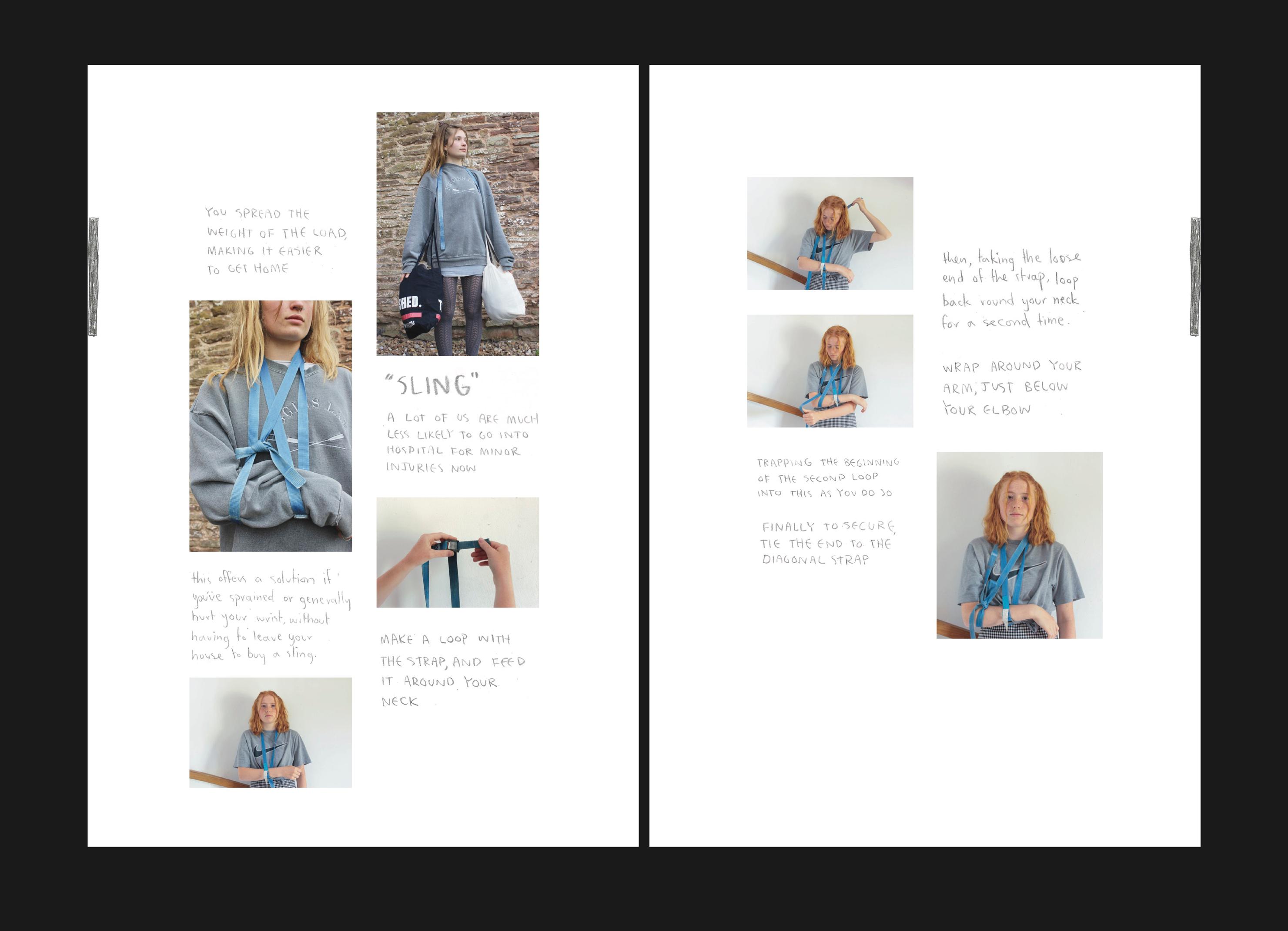
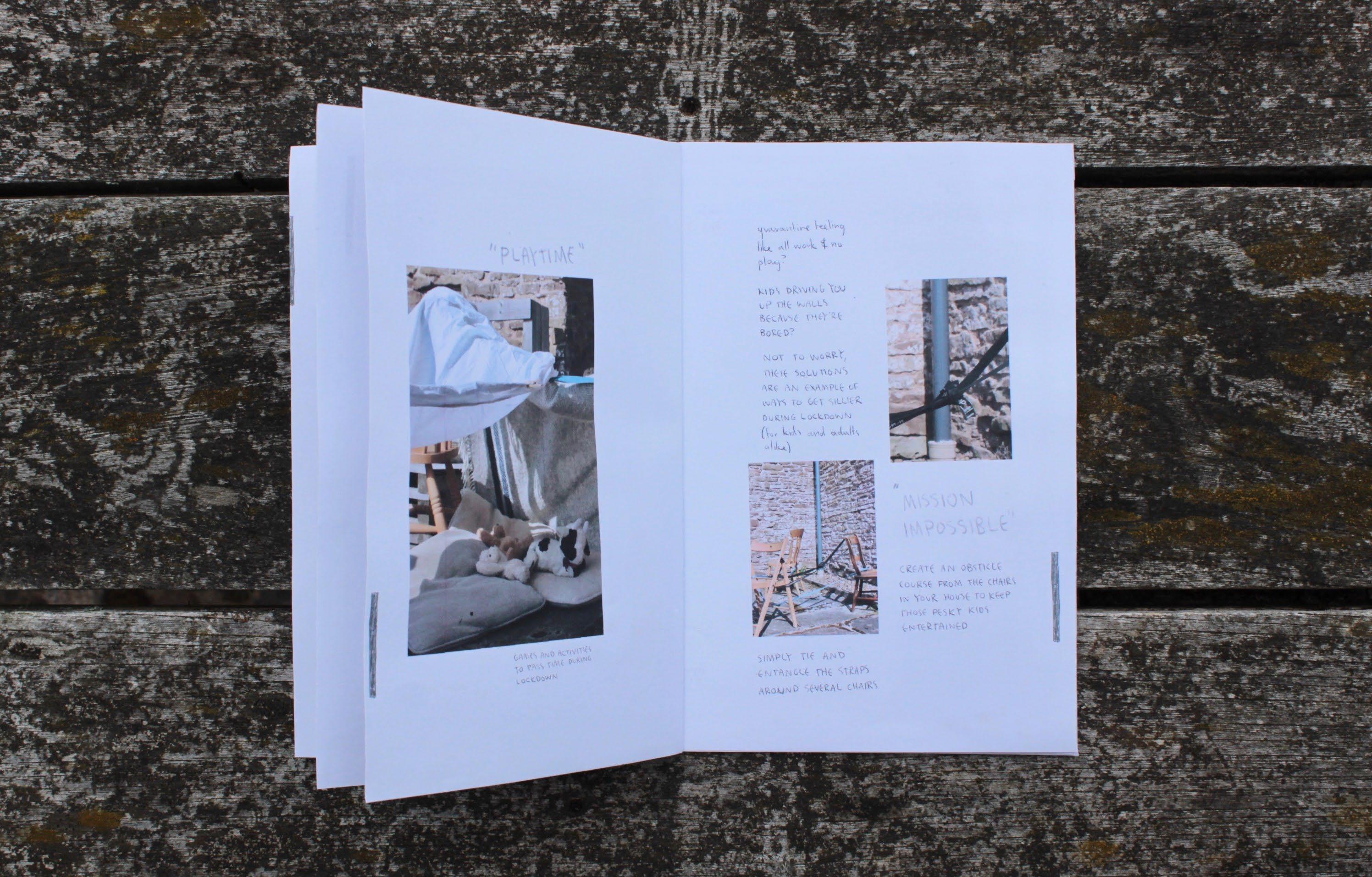
MANUAL
DESIGN
TheRESEARCHproject was based on the multiple emotional needs and wants of people, inspired by Viktor Papnek’s ‘needs vs wants’ diagram It(above).wasalso heavily influenced by ad hoc home design, in particular the comical inventions of Heath Robinson (left).
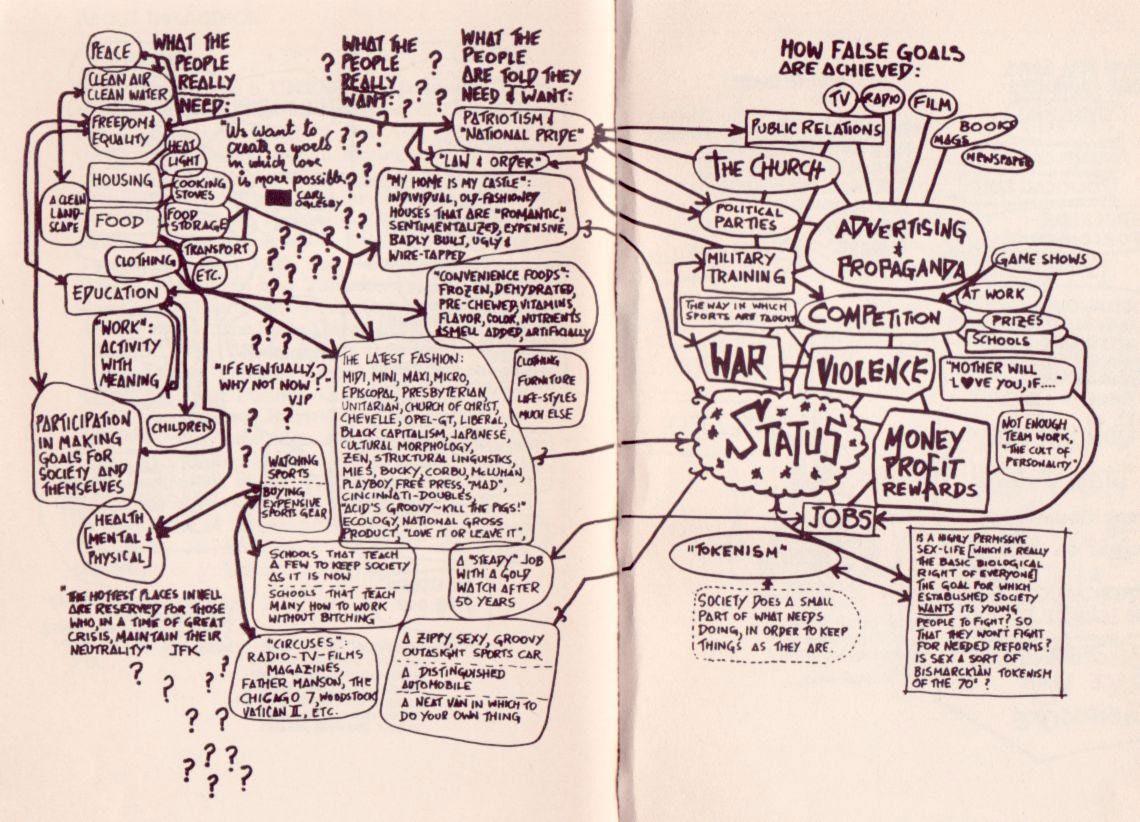
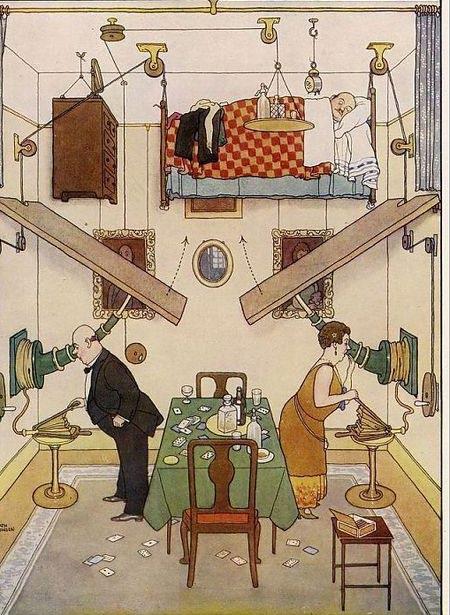
My inspiration for the style of the manual came from multiple sources, but overall the theme was reminiscent of blue prints with an minimal, illustratory twist (rightCecilia Serafini). The idea for the box came the growing letterbox packaging trend (below - LetterHamper).Box
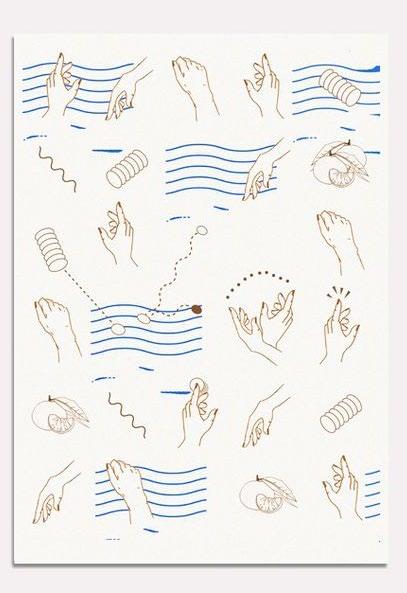
INSPIRATION
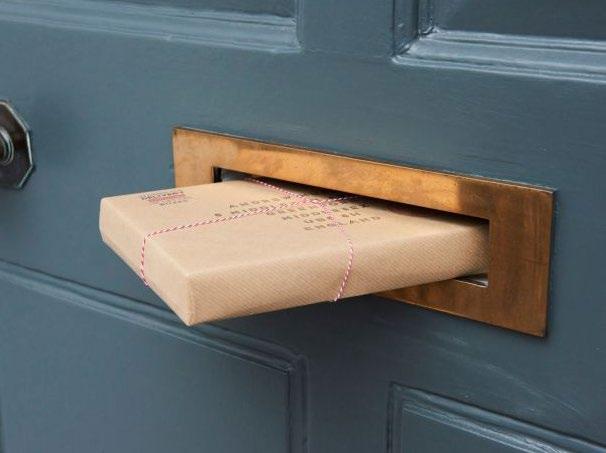
TheMARKETINGwrapround the packaging is designed so lots of different versions of ‘this is a...’ can be printed onto it, to highlight the endless uses of the product.
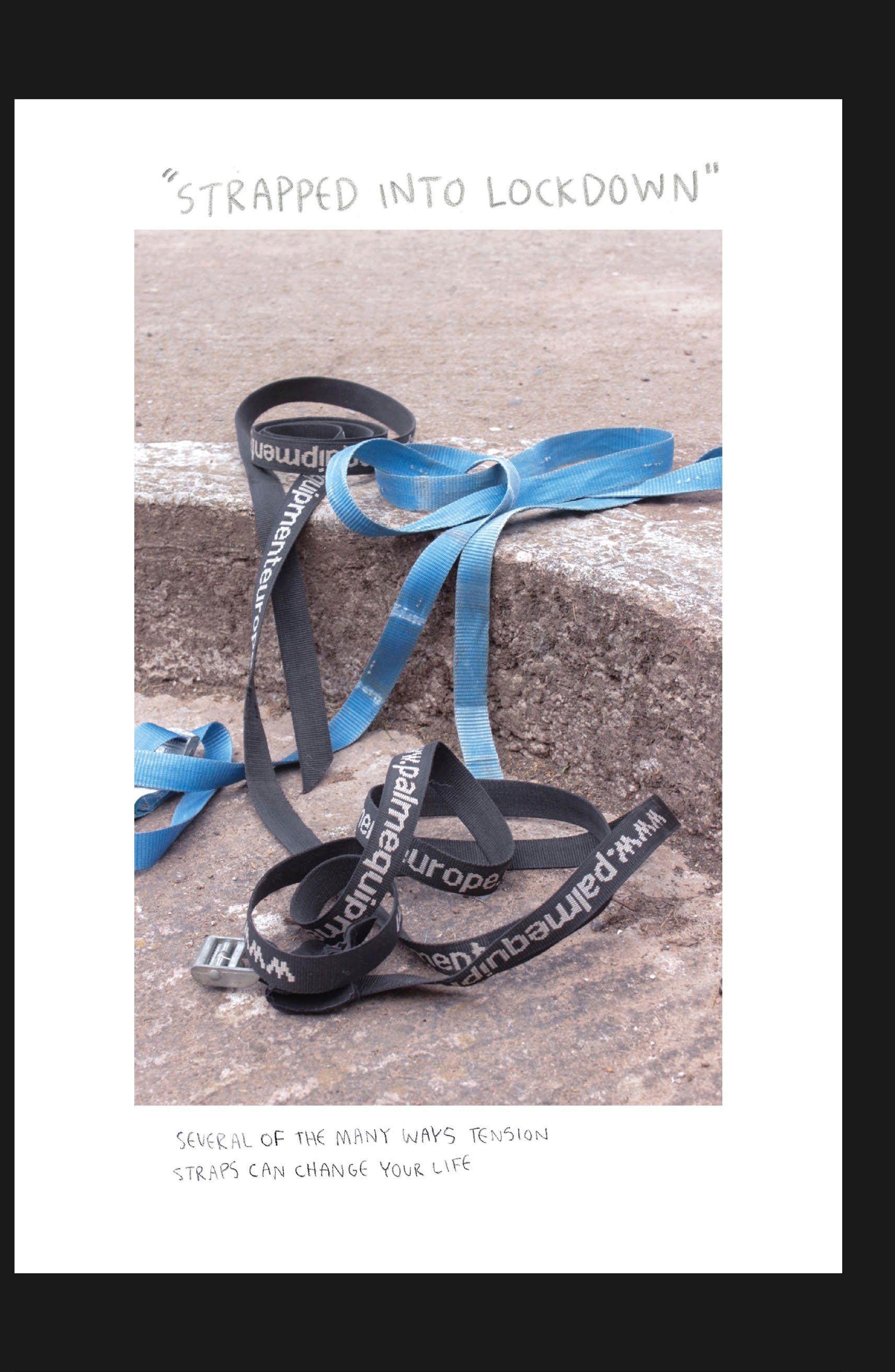
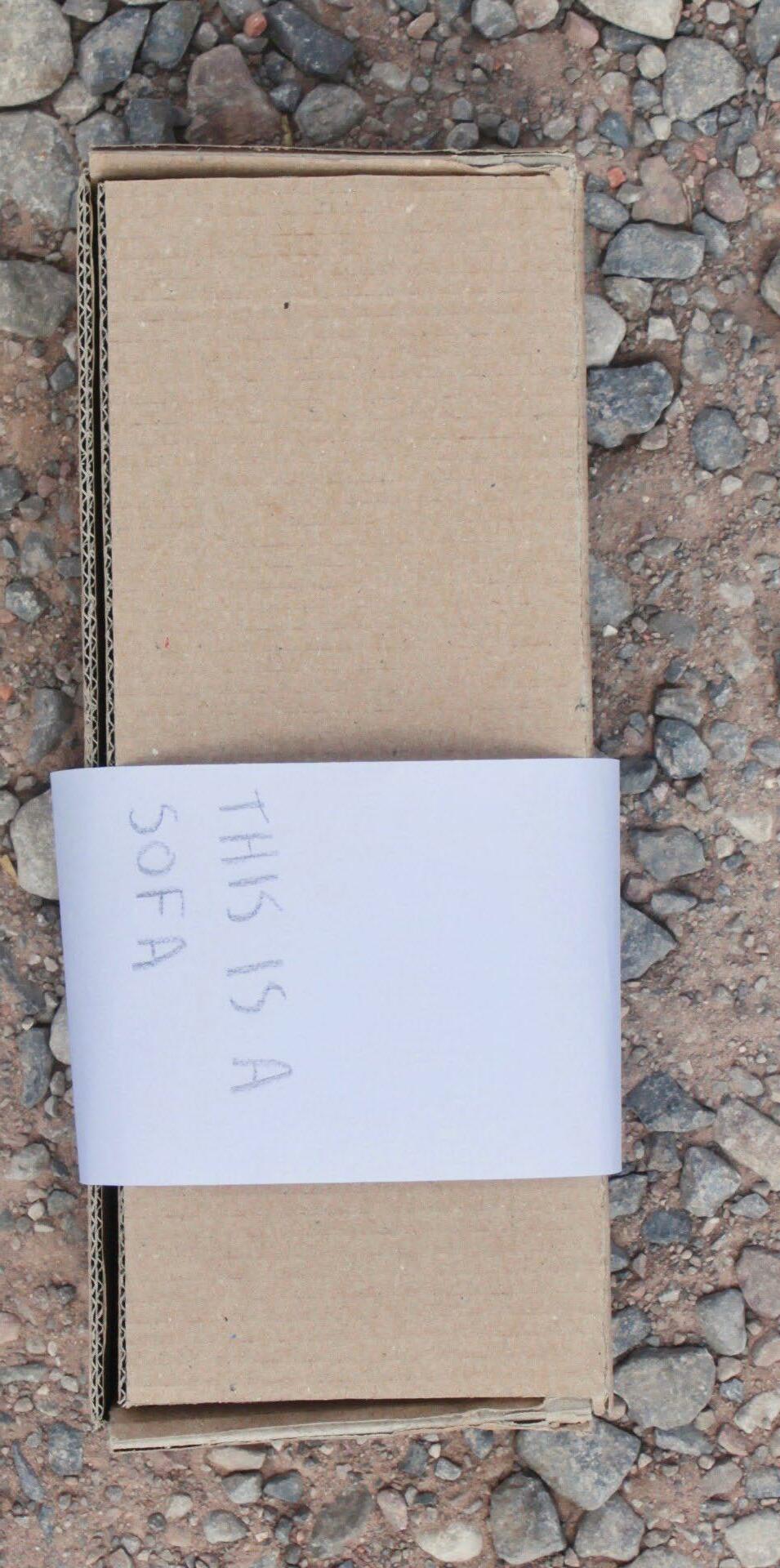


TheACCESSfinished manual has been designed as an open online source PDF, with the option to buy a physical copy alongside the straps, depending on what people Thisprefer.aims to give all people access to it, and promotes at-home making with no purchasing required. It takes into account the fact that some people may be less inclined to buy products due to worry of contamination.
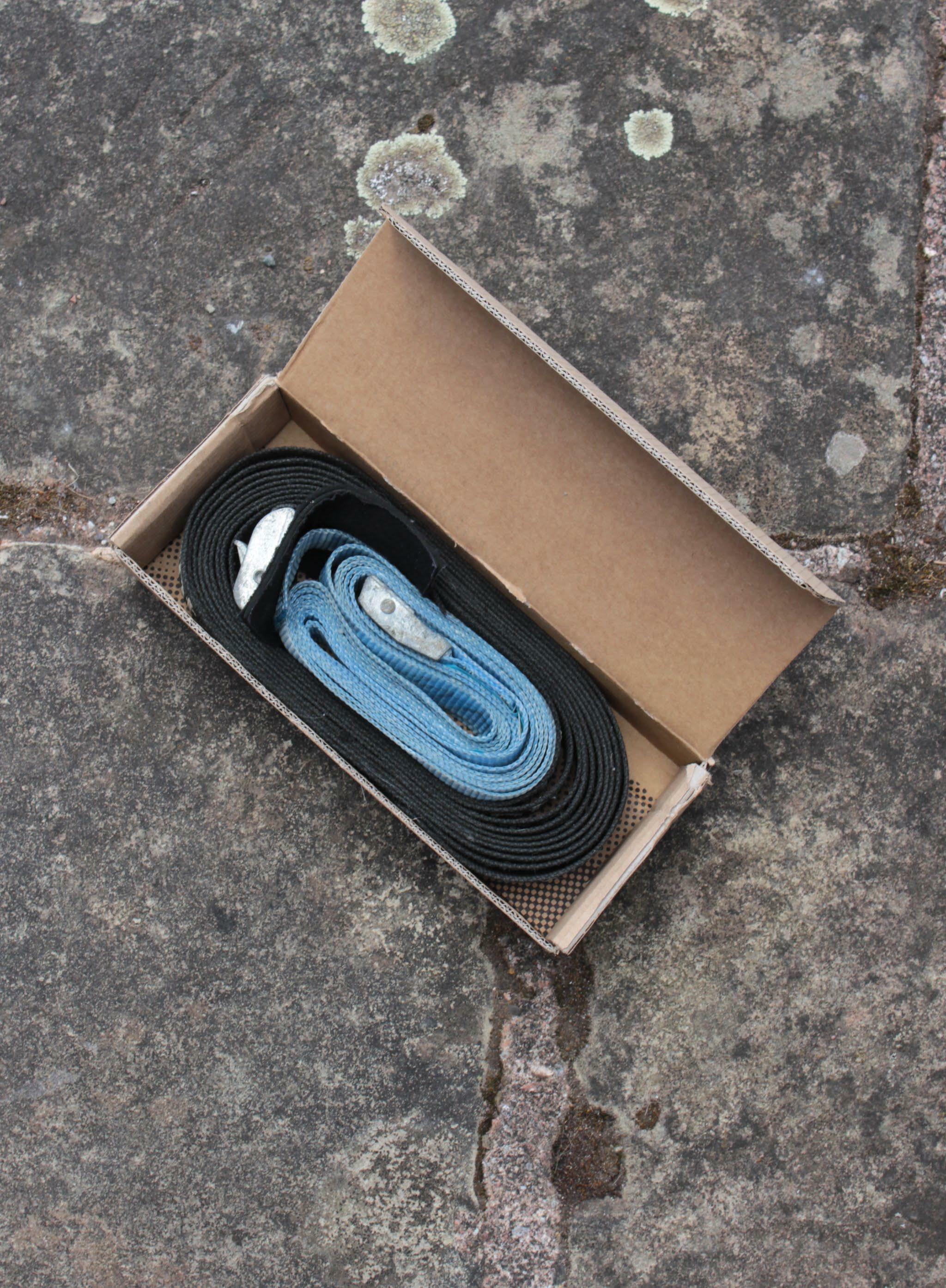
- I carried out design-based tasks such as building prototypes, testing products and designing graphics and moodboards that captured and responded to the clients narrative and aesthetic.
SUSTAINABILITY TEAM LEADER NTU Design Industries SEPT 2021 - JUNE 2022.
- I then helped organise and implement sustainable changes. This required clear, persuasive communication with a variety of different stakeholders.
NTU’s Extinction Rebellion Society. My role included listening and supporting members’ needs, organising and attending socials and national -demonstrations.Italsoincluded raising awareness for the climate emergency we are currently facing through nuanced and persuasive conversations both within the society and with members of the public.
WORKSHOP ASSISTANT Sebastian Cox Ltd, JULY 2020 - APR 2021.
SOCIETY PRESIDENT. NTU Extinction Rebellion Society, JULY 2018 – JUNE -2019.Ico-founded
PearsonINTERN.EXPERIENCELloyd,APR
- Worked as part of a multi-disciplinary design studio, helping to solve design problems, project specific primary and secondary research and industry wide insights and forecasting, all which required intuition, critical thinking and synthesising and presenting information.
@thebronblog07714651166bronwen.rees@outlook.com
- Taught me how to work to deadlines and think on my feet ; how to clearly communicate and listen within a close-knit team, and gave me first hand insight into the inner workings of a responsible and sustainable business.
- Trained in carpentry and gained knowledge on regenerative design and responsible, suitable wood uses.
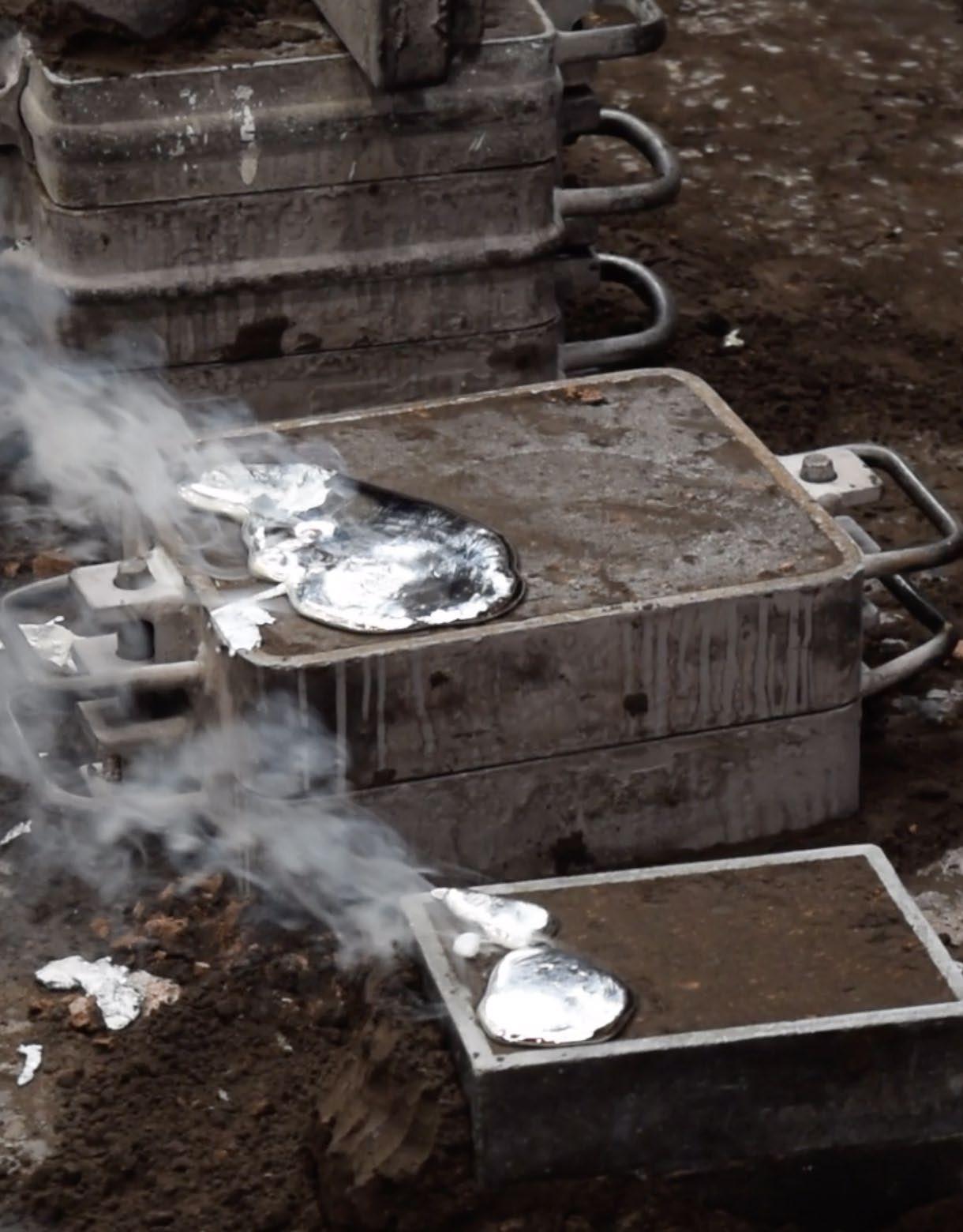
2021- AUG 2021.
- I created this team to tackle the negative impact created by our degree show, researching into a variety of problem areas, summarising the issues and presenting it to the rest of the degree show committee.
CERTIFIED CARBON LITERATE. The Carbon Literacy Project, MARCH 2022.
- Gained a comprehensive overview of topics such as carbon trends, carbon emissions, climate justice and policy - The training gave me the ability to create high impact solutions to reduce my carbon footprint , both individually and helping to introduce these steps in larger
- Awarded by the Materials and Design Exchange for both projects exhibited and the systemic thinking on which both are based: looking at life cycle design, the circular economy and efficient use of sustainable materials.
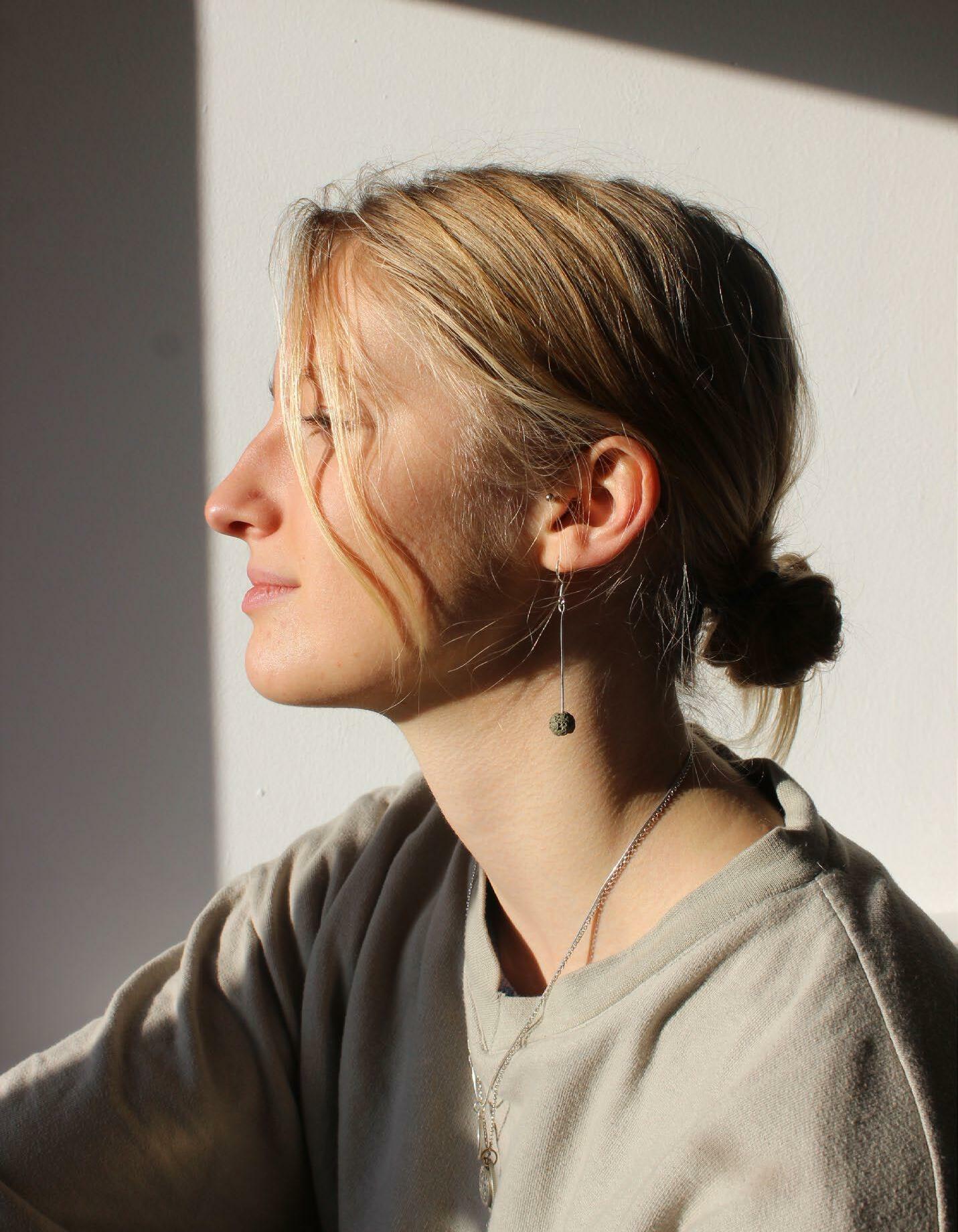
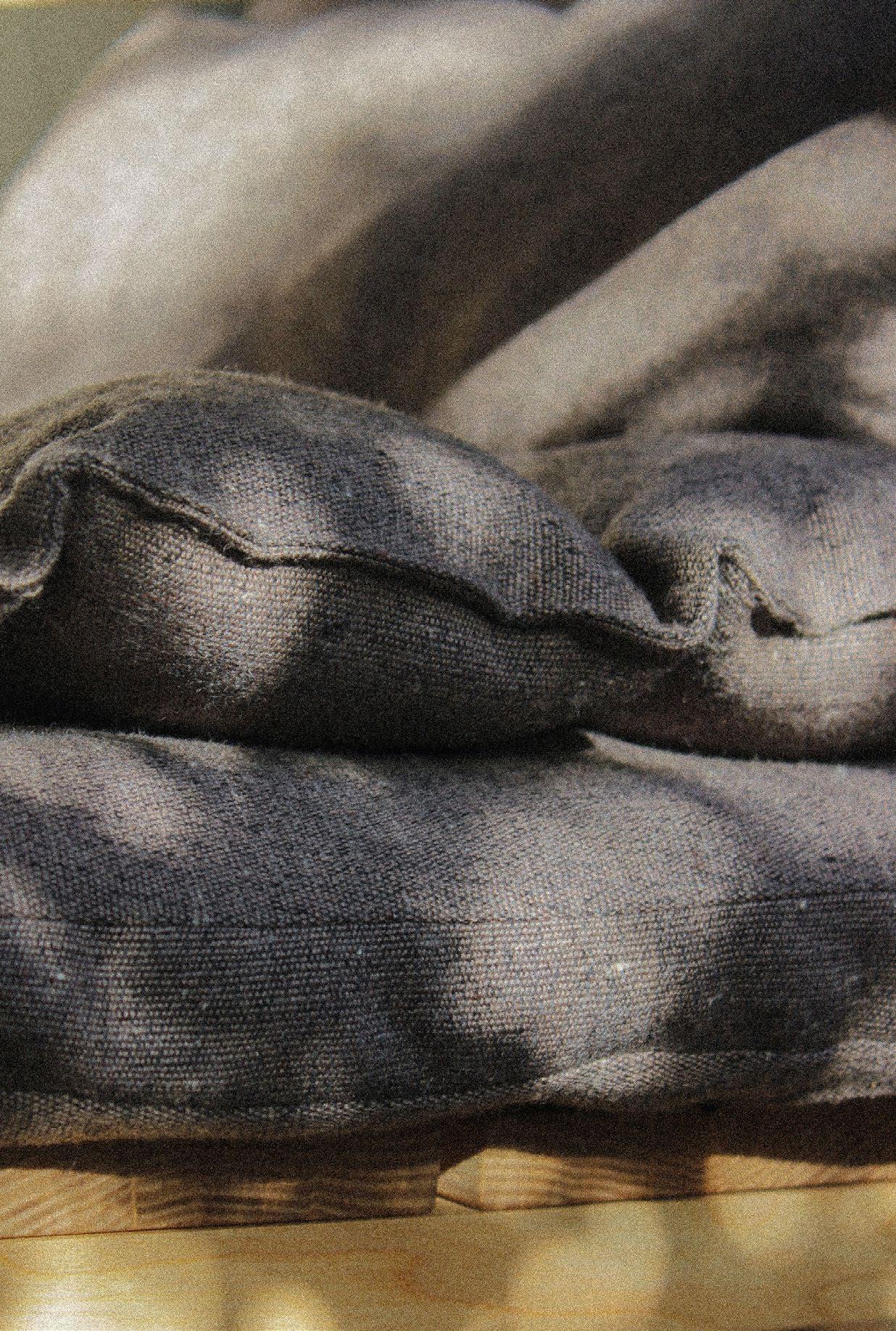
SUSTAINABILITY IN ENTERPRISE GOLD AWARD. NTU Green Awards, JUNE 2022.
- Awarded for completing a range of sustainabilityrelated extracurricular activities including working as part of a team, problem solving sustainabilitybased issues for SME’s and negotiating environmental agreements and advancements with different stakeholders. - Provided me with valuable skills in persuasion, bartering, and understanding sustainability in the workplace, and taught me how to use my own skills and knowledge to implement change professionally.
MaDEACHIEVEMENTS.CERTIFICATE
OF ACHIEVEMENT FOR EXCELLENT CONSIDERATION OF NewSUSTAINABILITY.Designers,JULY 2022.
BA(HONS)organisationsFURNITURE AND PRODUCT DESIGN BEST STUDENT. Nottingham Trent University, JULY 2022.
- An internal award given to a student who achieves outstanding academic grades and actively engages and contributes to the course.