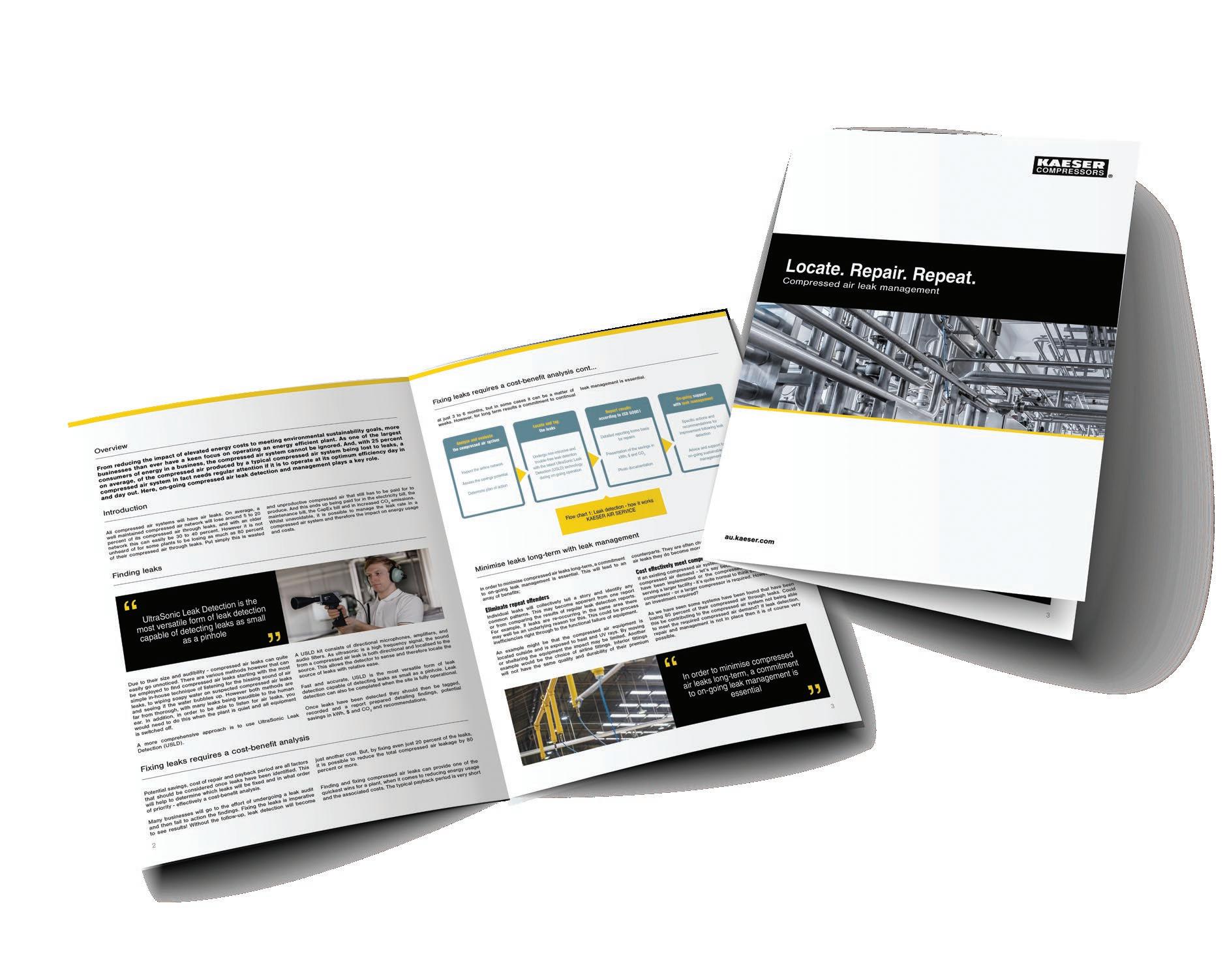
4 minute read
Locate. Repair. Repeat Compressed air leak management [whitepaper extract]
Locate. Repair. Repeat.
Hole diameter corresponding size
1 mm

2 mm
4 mm
6 mm Example of the losses associated with compressed air leaks. In this example, the compressor operates at 6 bar. With a 1 mm hole it will consume an additional 0.39 kW/h. This equates to an annual cost of $512 - assuming the system has a power cost of 15 cents/kW/hr* .
Air consumption at 6 bar(g) m3/min
0.065
kW
0.39
Loss
$/year*
512
0.257
1.03
2.31 1.54
6.18
13.86 2,026
8,120
18,202 From reducing the impact of elevated energy costs to meeting environmental sustainability goals, more businesses than ever have a keen focus on operating an energy efficient plant. As one of the largest consumers of energy in a business, the compressed air system cannot be ignored. And, with 25 percent on average, of the compressed air produced by a typical compressed air system being lost to leaks, a compressed air system in fact needs regular attention if it is to operate at its optimum efficiency day in and day out. Here, on-going compressed air leak detection and management plays a key role.
Introduction
All compressed air systems will have air leaks. On average, a well maintained compressed air network will lose around 5 to 20 percent of its compressed air through leaks, and with an older network this can easily be 30 to 40 percent.
However it is not unheard of for some plants to be losing as much as 80 percent of their compressed air through leaks. Put simply this is wasted and unproductive compressed air that still has to be paid for to produce. And this ends up being paid for in the electricity bill, the maintenance bill, the CapEx bill and in increased CO emissions.
Whilst unavoidable, it is possible to manage the leak rate in a compressed air system and therefore the impact on energy usage and costs.
Finding leaks
Due to their size and audibility - compressed air leaks can quite easily go unnoticed. There are various methods however that can be employed to find compressed
Download the whitepaper today - just scan the QR code
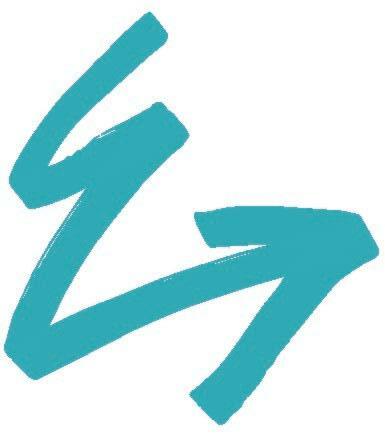

From reducing the impact of elevated energy costs to meeting environmental sustainability goals, more businesses than ever have a keen focus on operating an energy efficient plant. As one of the largest consumers of energy in a business, the compressed air system cannot be ignored. And, with 25 percent on average, of the compressed air produced by a typical compressed air system being lost to leaks, a compressed air system in fact needs regular attention if it is to operate at its optimum efficiency day in and day out. Here, on-going compressed air leak detection and management plays a key role.

air leaks starting with the most simple in-house technique of listening for the hissing sound of air leaks, to wiping soapy water on suspected compressed air leaks and seeing if the water bubbles up.
However both methods are far from thorough, with many leaks being inaudible to the human ear. In addition, in order to be able to listen for air leaks, you would need to do this when the plant is quiet and all equipment is switched off.
A more comprehensive approach is to use UltraSonic Leak Detection (USLD).
A USLD kit consists of directional microphones, amplifiers, and audio filters. As ultrasonic is a high frequency signal, the sound from a compressed air leak is both directional and localised to the source. This allows the detector to sense and therefore locate the source of leaks with relative ease.
Fast and accurate, USLD is the most versatile form of leak detection capable of detecting leaks as small as a pinhole. Leak detection can also be completed when the site is fully operational.
Once leaks have been detected they should then be tagged, recorded and a report prepared detailing findings, potential savings in kWh, $ and CO2 and recommendations.
Fixing leaks requires a costbenefit analysis
Potential savings, cost of repair and payback period are all factors that should be considered once leaks have been identified. This will help to determine which leaks will be fixed and in what order of priority - effectively a cost-benefit analysis.
Many businesses will go to the effort of undergoing a leak audit and then fail to action the findings. Fixing the leaks is imperative to see results! Without the follow-up, leak detection will become just another cost. But, by fixing even just 20 percent of the leaks, it is possible to reduce the total compressed air leakage by 80 percent or more. can provide one of the quickest wins for a plant, when it comes to reducing energy usage and the associated costs. The typical payback period is very short at just 3 to 6 months, but in some cases it can be a matter of weeks. However, for long term results a commitment to continual leak management is essential.
Minimise leaks long-term with leak management
In order to minimise compressed air leaks long-term, a commitment to on-going leak management is essential. This will lead to an array of benefits;
Eliminate repeat offenders
Individual leaks will collectively tell a story and identify any common patterns. This may become apparent from one report or from comparing the results of regular leak detection reports. For example, if leaks are re-occurring in the same area there may well be an underlying reason for this. This could be process inefficiencies right through to the functional failure of equipment. An example might be...