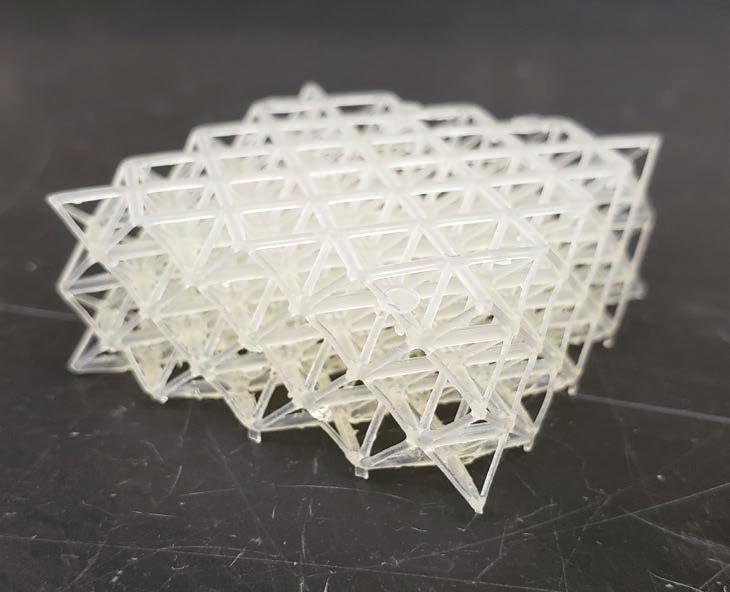
2 minute read
Getting Tough Fast
BROWN COMBINES MACHINE LEARNING, MECHANICS TO SPEED DISCOVERY OF IMPACT-RESISTANT MATERIALS
Designing materials for impact protection—think military helmets or a car’s crumple zone—is arduous and expensive. Engineers can’t simply model the impacts on a computer; they must physically subject the candidate materials to crashes.
Advertisement
Now, Associate Professor Keith Brown (ME, MSE, Physics) has figured out how to combine additive manufacturing with robotics and machine learning to test thousands of combinations of materials and designs with unprecedented speed—and no large-scale destruction.
“In the past year, our lab discovered a host of structured materials that were highly efficient in terms of absorbing mechanical energy, as the result of over 10,000 experiments,” says Brown. “We’re talking about big numbers—numbers it would be totally impractical, if not impossible, to reach without an automated system.”
That’s just one example of the advances in materials discovery that Brown and colleagues have shown are possible. The team published their findings in a recent paper in Matter and presented them at the first-ever Accelerate conference in Toronto, where Brown received a travel award.
“When nature builds materials and structures, it makes these exquisitely complicated things,” says Brown. “Our goal is to figure out ways to learn how to create similarly intricate structures that have really highly tuned and tailored properties for things like impact protection and mechanical performance—things that are hard to simulate.”
To catch up to nature, which has had “the benefit of hundreds of millions of years of evolution,” Brown says, “we build robots that do these experiments for us.”
That’s the first key component: Brown’s BEAR system, short for Bayesian experimental autonomous researcher. The engineers enter parameters into the system—say, properties of strength or toughness. The autonomous system rapidly designs one structure after another and, with a robotic arm and several 3D printers, manufactures samples.
Next, the researchers subject each sample to quasistatic compression in a kind of leaner stand-in for an impact test. Ultimately, once they find the sample structure—for example, a lattice—that meets the criteria, they can manufacture multiple copies of that lattice and knit them into a material with the desired toughness. “It’s like a box spring,” says Brown, “where you have a series of components arranged in a way that allows you to absorb energy effectively.”
Combining quasistatic and impact tests, the researchers trained a model that accurately predicted the impact performance in novel lattices. The results proved how relatively simple data, obtained without fullsize samples or complex measurements, can be used to accomplish bigger goals in materials discovery.
Along with his students Aldair Gongora (ENG’21) and Kelsey Snapp (ENG’25), Brown’s collaborators on the Matter study included Maysarah K. Sukkar Professor of Engineering Design and Innovation
Elise Morgan (ME, MSE, BME) and Emily Whiting, an associate professor of computer science in the College of Arts & Sciences. The team’s work is funded in part by the US Department of Defense. — PATRICK L.