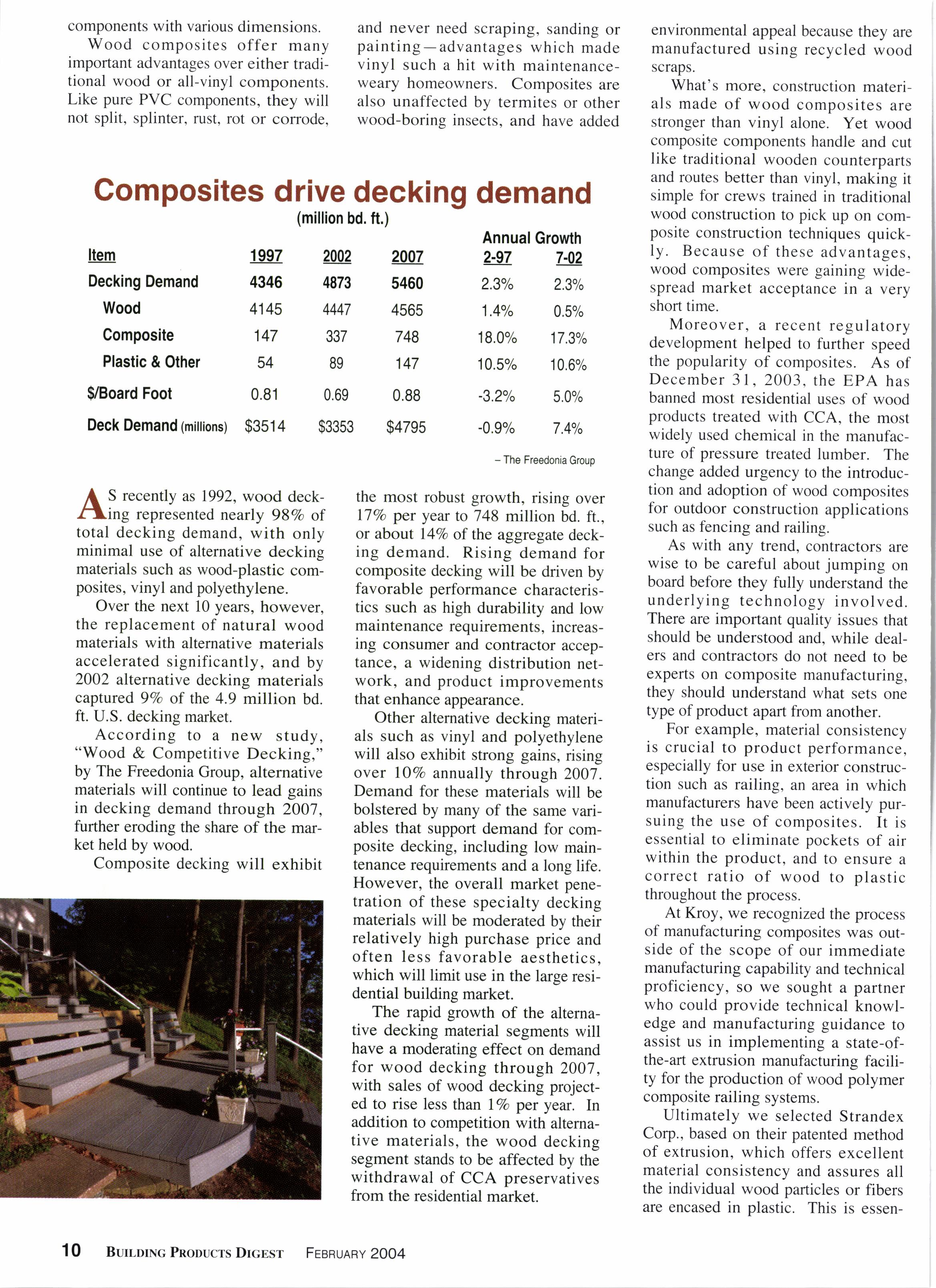
5 minute read
Composites drive decking demand
environmental appeal because they are manufactured using recycled wood scraps.
What's more, construction materials made of wood composites are stronger than vinyl alone. Yet wood composite components handle and cut like traditional wooden counterparts and routes better than vinyl, making it simple for crews trained in traditional wood construction to pick up on composite construction techniques quick- Iy. Because of these advantages, wood composites were gaining widespread market acceptance in a very short time.
f, S recently as 1992. wood deck.Cl,ing represented nearly 98Vo of total decking demand, with only minimal use of alternative decking materials such as wood-plastic composites, vinyl and polyethylene.
Over the next 10 years, however, the replacement of natural wood materials with alternative materials accelerated significantly, and by 2002 alternative decking materials captured 9vo of the 4.9 million bd. ft. U.S. decking market.
According to a new study, "Wood & Competitive Decking," by The Freedonia Group, alternative materials will continue to lead gains in decking demand through 2007, further eroding the share of the market held by wood.
Composite decking will exhibit the most robust growth, rising over lTVo per year to 748 million bd. ft., or about l4Vo of the aggregate decking demand. Rising demand for composite decking will be driven by favorable performance characteristics such as high durability and low maintenance requirements, increasing consumer and contractor acceptance, a widening distribution network, and product improvements that enhance appearance.
Other alternative decking materials such as vinyl and polyethylene will also exhibit strong gains, rising over lOVo annually through 2007. Demand for these materials will be bolstered by many of the same variables that support demand for composite decking, including low maintenance requirements and a long life. However, the overall market penetration of these specialty decking materials will be moderated bv their relatively high purchase priie and often less favorable aesthetics, which will limit use in the large residential building market.
The rapid growth of the alternative decking material segments will have a moderating effect on demand for wood decking through 2007, with sales of wood decking projected to rise less than IVo per year. In addition to competition with alternative materials, the wood decking segment stands to be affected by the withdrawal of CCA preservatives from the residential market.
Moreover, a recent regulatory development helped to further speed the popularity of composites. As of December 31,2003. the EPA has banned most residential uses of wood products treated with CCA, the most widely used chemical in the manufacture of pressure treated lumber. The change added urgency to the introduction and adoption of wood composites for outdoor construction applications such as fencing and railing.
As with any trend, contractors are wise to be careful about jumping on board before they fully understand the underlying technology involved. There are important quality issues that should be understood and, while dealers and contractors do not need to be experts on composite manufacturing, they should understand what sets one type ofproduct apart from another.
For example, material consistency is crucial to product performance, especially for use in exterior construction such as railing, an area in which manufacturers have been actively pursuing the use of composites. It is essential to eliminate pockets of air within the product, and to ensure a correct ratio of wood to plastic throughout the process.
At Kroy, we recognized the process of manufacturing composites was outside of the scope of our immediate manufacturing capability and technical proficiency, so we sought a partner who could provide technical knowledge and manufacturing guidance to assist us in implementing a state-ofthe-art extrusion manufacturing facility for the production of wood polymer composite railing systems.
Ultimately we selected Strandex Corp., based on their patented method of extrusion, which offers excellent material consistency and assures all the individual wood particles or fibers are encased in plastic. This is essen- tial to protect the railing systems from rot, decay or termite damage.
Another important quality issue is the selection of raw comPonents including the wood type, the wood mesh or particle size, the type of plastic and the source of plastic. The various wood or plastic choices are dictated by three factors: the specific manufacturing process that is being used, the desired performance of the end product, and its cost. The processes and technology options for manufacturing composite materials are abun- dant and growing-a sign that this new type of exterior building product will continue to evolve and improve over the next few years.
The wood flour used in comPosite material is manufactured by recycling the waste from other woodworking processes such as furniture and cabinet making. The process can Produce powder in a varying range of particle or mesh size, made from either softwood or hardwood.
In terms of the plastic binder materials, manufacturers use a broad range
Composite wood-not iust decking
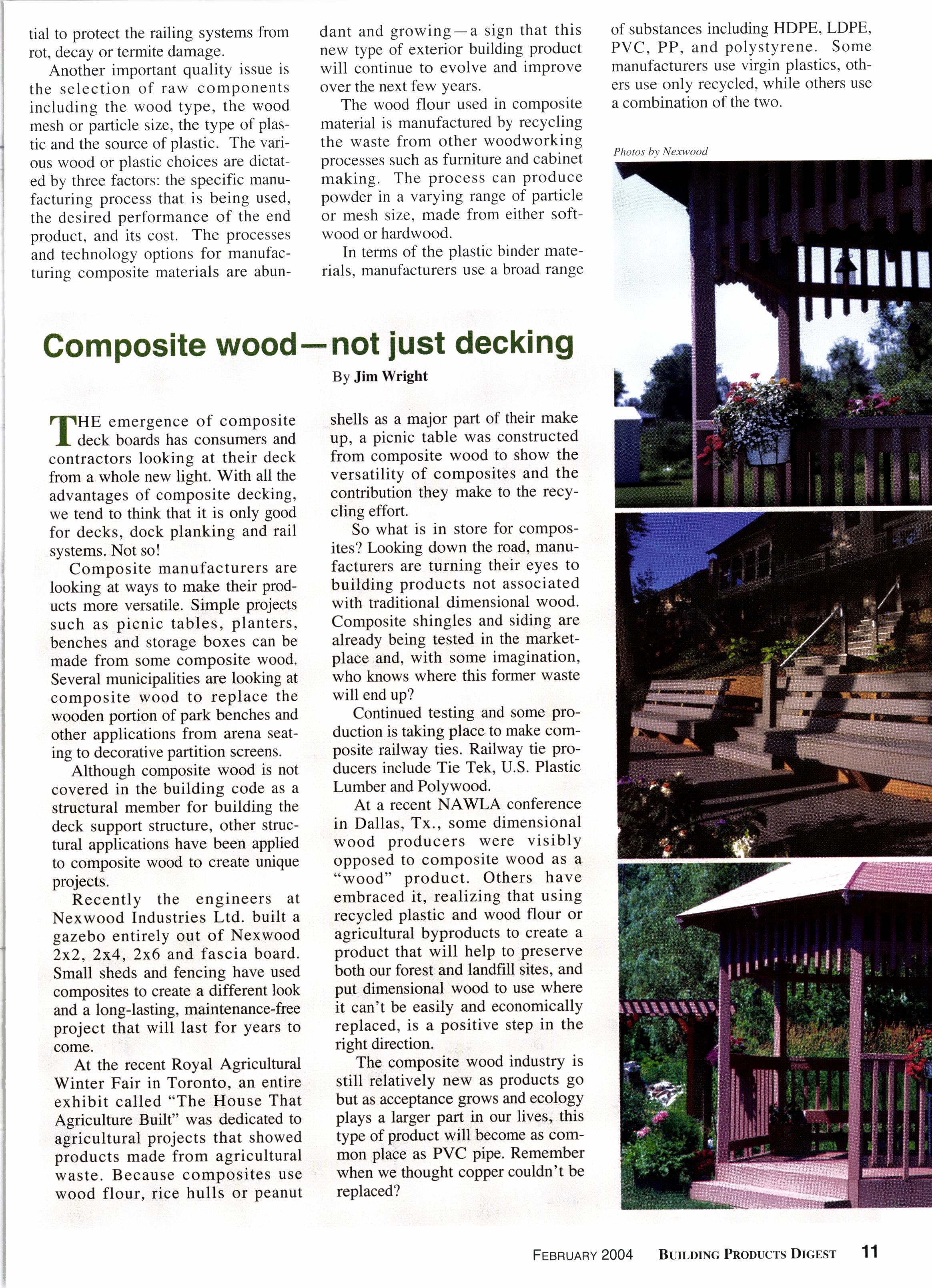
By Jim Wright
rnHE emergence of composite deck boards has consumers and contractors looking at their deck from a whole new light. With all the advantages of composite decking, we tend to think that it is only good for decks, dock planking and rail systems. Not sol
Composite manufacturers are looking at ways to make their products more versatile. Simple projects such as picnic tables, planters, benches and storage boxes can be made from some composite wood. Several municipalities are looking at composite wood to replace the wooden portion of park benches and other applications from arena seating to decorative partition screens.
Although composite wood is not covered in the building code as a structural member for building the deck support structure, other structural applications have been applied to composite wood to create unique projects.
Recently the engineers at Nexwood Industries Ltd. built a gazebo entirely out of Nexwood 2x2, 2x4,2x6 and fascia board. Small sheds and fencing have used composites to create a different look and a long-lasting, maintenance-free project that will last for Years to come.
At the recent Royal Agricultural Winter Fair in Toronto, an entire exhibit called "The House That Agriculture Built" was dedicated to agricultural projects that showed products made from agricultural waste. Because composites use wood flour, rice hulls or Peanut shells as a major part of their make up, a picnic table was constructed from composite wood to show the versatility of composites and the contribution they make to the recycling effort. of substances including HDPE, LDPE, PVC, PP, and polystyrene. Some manufacturers use virgin plastics, others use only recycled, while others use a combination of the two.
So what is in store for comPosites? Looking down the road, manufacturers are turning their eyes to building products not associated with traditional dimensional wood. Composite shingles and siding are already being tested in the marketplace and, with some imagination, who knows where this former waste will end up?
Continued testing and some Production is taking place to make composite railway ties. Railway tie producers include Tie Tek. U.S. Plastic Lumber and Polywood.
At a recent NAWLA conference in Dallas, Tx., some dimensional wood producers were visiblY opposed to composite wood as a "wood" product. Others have embraced it, realizing that using recycled plastic and wood flour or agricultural byproducts to create a product that will help to preserve both our forest and landfill sites, and put dimensional wood to use where it can't be easily and economically replaced, is a positive step in the right direction.
The composite wood industry is still relatively new as products go but as acceptance grows and ecology plays a larger part in our lives, this type of product will become as common place as PVC pipe. Remember when we thought copper couldn't be replaced?