
3 minute read
Round Two for fle lng
EILEXIBLE moulding
l' seems to have kent a lower profile since bendable trim made its muchheralded introduction in the 1980s.
That doesn't mean the market hasn't continued to evolve and expand as more buyers and manufacturers catch on.
Change, in fact, has been a constant, says Rick Hemsworth, Profile Mouldings, Surrey, B.C. "Consumers are becoming far more choosy now that there are more suppliers compet- ing in this arena," he explains. "Producers of flexible mouldings that snap or break easily are being replaced by manufacturers with better flexible formulas."
He adds, "Some producers are now manufacturing flexible mouldings on large spools rather than specified custom lengths. While this works well for some commonly ordered profiles, 'special order' for individual pieces is still necessitated for the most part, owing to the number of profiles and required radiuses available. "
Research is ongoing even at veteran manufacturers. "Flex Trim is constantly developing and creating," says Billy Ward, Flex Trim Technologies, Rancho Cucamonga, Ca. "In 2003, we launched a brand new product called Xtrulinear. Prior to the introduction of Xtrulinear, the flexible moulding and trim industry were only delivering l2-foot lengths. We have developed the technology, Xtrulinear, to deliver our same product, with all the same sizes and shapes, in lengths up to 500 feet. Yes, that is 500 feet of continuous flexible moulding on a roll!" The product makes it easier to store and dispense trim on the job site, as well as at the lumberyard or home center. In addition, new this year is the XDisplay which, according to Ward, "takes the rolls and allows the distributor/home builder store to easily display, store, sell and dispense Xtrulinear in any length, with minimal floor space needed and the ability to maximize the square foot usage dollars." The display holds six reels.
Joe Morin, El & El Wood Products, Chino, Ca., adds, "New developments have occurred in a few-perhaps unnoticeable-areas, such as lighter weight and tear strength. Flexible moulding prices are determined by weight ani yield and then converted to a per foot price. If material can be developed
With flexible trim.
"imagination has been permitted to return to the architect's drawing board."
that weighs substantially less, it will reduce the cost of flexible mouldings. The problem with lighter weight systems is the integrity or strength of the material weakens causing the material to crack or split. We are in constant research and development to improve both the weight and strength of the flexible moulding."
As for other trends. Hemsworth notes, "In the flexible moulding market, crown mouldings are definitely picking up in popularity as architects learn more about their availability and ease of installation. With this knowledge, one's imagination is the only limitation. Rounded stair cases, drop ceilings and bulkheads can now be less square in appearance without limiting the extent of decor and adornment."
Dick Gorostiza, Ultra Flex Moulding, Escondido, Ca., sees growth due in part to "the ability to use urethane-based flexible moulding for exterior applications."
In addition, he notices "more and more applications to replaced curved wood millwork. Ultimate Flex is easily stained or painted to match up with the straight wood parts."
Ward forecasts: "We see (flexible trim) headed from the professional contractor venue to the do-it-yourself home center arena as we create more user-friendly technology."
Gary Uecker, ResinArt West, Costa Mesa. Ca." considers flexible moulding "stable and growing, to the tune of about l07o to 157o. All is based on higher-priced homes being built. The areas of growth seem to change among regions."
"We see continued growth, esPecially with restoration and new construction," predicts Michael Glicksman, Flex Moulding, Inc., Hackensack, N.J. "(Our) area has seen tremendous growth in new construction, and it is expected to continue. We expect to see continued growth with preformed arch moulding as window and millwork peoPle refer or resell our products."
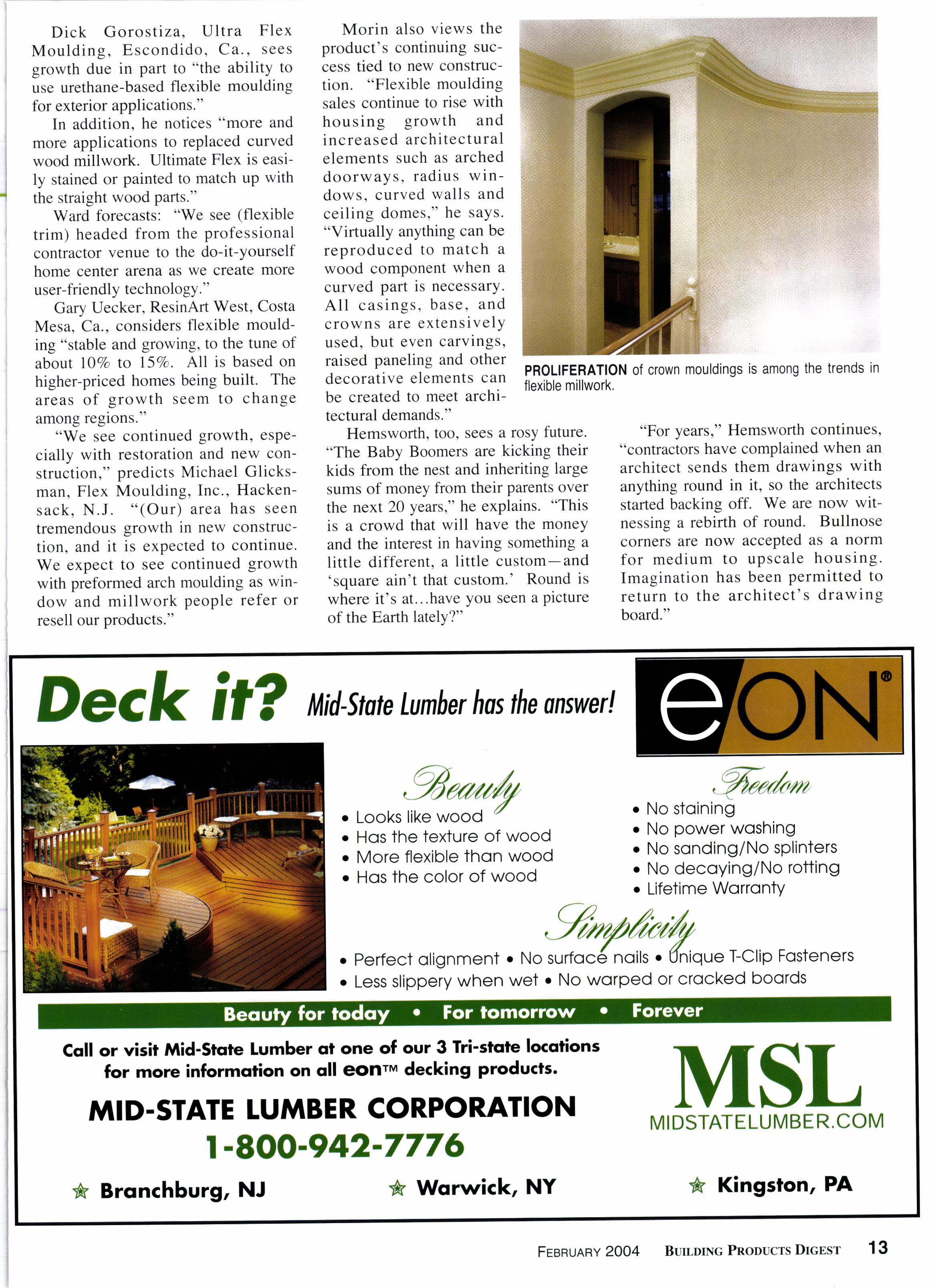
Morin also views the product's continuing success tied to new construction. "Flexible moulding sales continue to rise with housing growth and increased architectural elements such as arched doorways, radius windows, curved walls and ceiling domes," he saYs. "Virtually anything can be reproduced to match a wood component when a curved part is necessary. All casings, base, and crowns are extensivelY used, but even carvings. raised paneling and other decorative elements can be created to meet architectural demands."
Hemsworth, too, sees a rosY future. "The Baby Boomers are kicking their kids from the nest and inheriting large sums of money from their parents over the next 20 years," he explains. "This is a crowd that will have the money and the interest in having something a little different, a little custom-and 'square ain't that custom.' Round is where it's at...have you seen a picture of the Earth lately?"
"For years," Hemsworth continues, "contractors have complained when an architect sends them drawings with anything round in it, so the architects started backing off. We are now witnessing a rebirth of round. Bullnose corners are now accePted as a norm for medium to upscale housing. Imagination has been Permitted to return to the architect's drawing board."