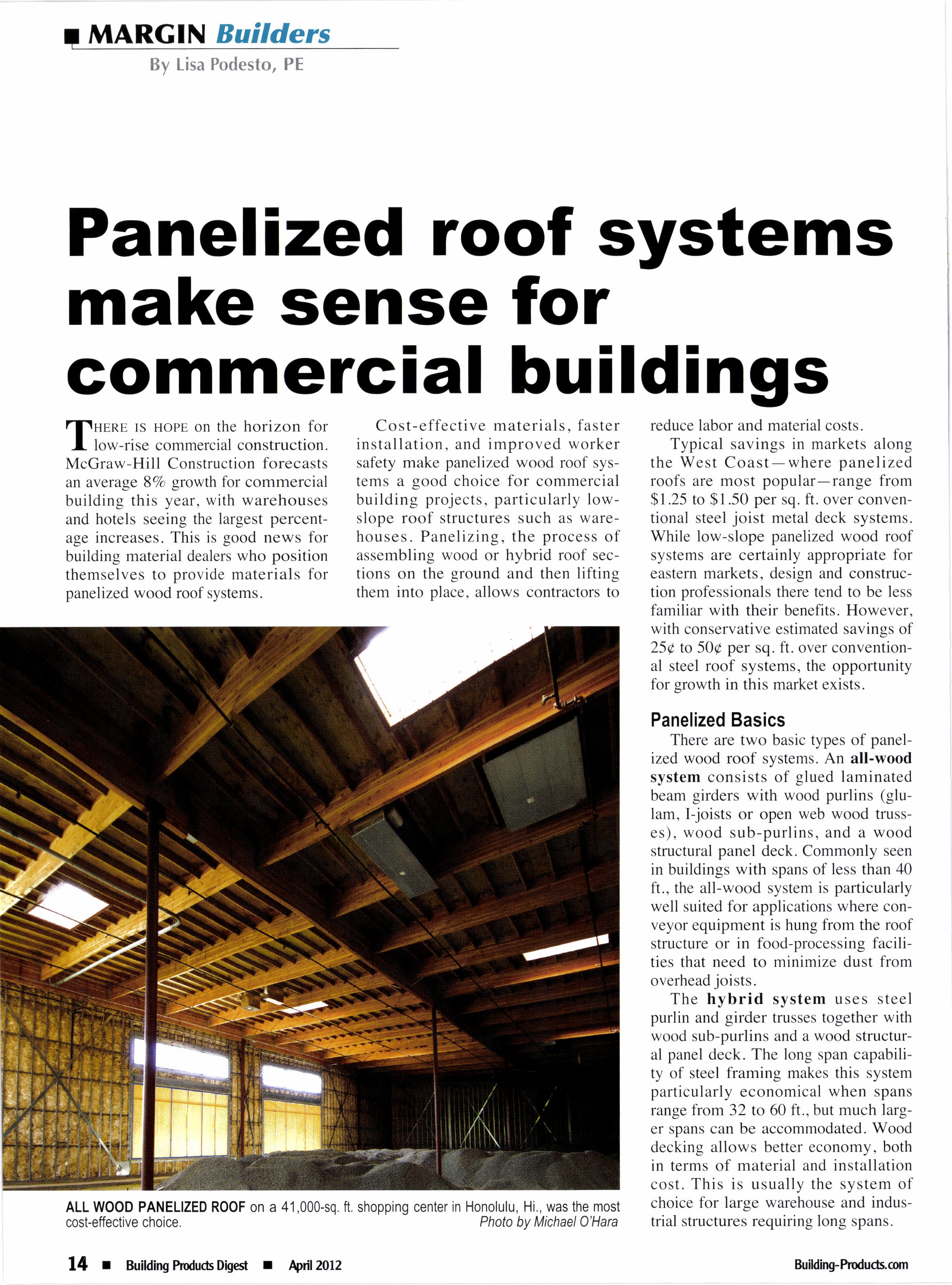
4 minute read
Panelized roof systems make sense for commercial buildings
fllHene IS HoPE on the horizon for I low-rise commercial construction. McGraw-Hill Construction forecasts an average 8% growth for commercial building this year, with warehouses and hotels seeing the largest percentage increases. This is good news for building material dealers who position themselves to provide materials for panelized wood roof systems.
Cost-effective materials, faster installation, and improved worker safety make panelized wood roof systems a good choice for commercial building projects, particularly lowslope roof structures such as warehouses. Panelizing, the process of assembling wood or hybrid roof sections on the ground and then lifting them into place, allows contractors to reduce labor and material costs.
Typical savings in markets along the West Coast-where panelized roofs are most popular-range from $1.25 to $1.50 per sq. ft. over conventional steel joist metal deck systems. While low-slope panelized wood roof systems are certainly appropriate for eastern markets, design and construction professionals there tend to be less familiar with their benefits. However, with conservative estimated savings of 25Q to 5O(, per sq. ft. over conventional steel roof systems, the opportunity for growth in this market exists.
Panelized Basics
There are two basic types of panelized wood roof systems. An all-wood system consists of glued laminated beam girders with wood purlins (glulam, I-joists or open web wood trusses), wood sub-purlins, and a wood structural panel deck. Commonly seen in buildings with spans of less than 40 ft., the all-wood system is particularly well suited for applications where conveyor equipment is hung from the roof structure or in food-processing facilities that need to minimize dust from overhead joists.
The hybrid system uses steel purlin and girder trusses together with wood sub-purlins and a wood structural panel deck. The long span capability of steel framing makes this system particularly economical when spans range from 32 to 60 ft., but much larger spans can be accommodated. Wood decking allows better economy, both in terms of material and installation cost. This is usually the system of choice for large warehouse and industrial structures requiring long spans.
While market share fluctuates with commodity steel and wood prices, about 707o of new low-slope, commercial roof projects in California are currently built with hybrid systems, l}Vo are all-wood, and the remaining 2OVo are built using all steel.
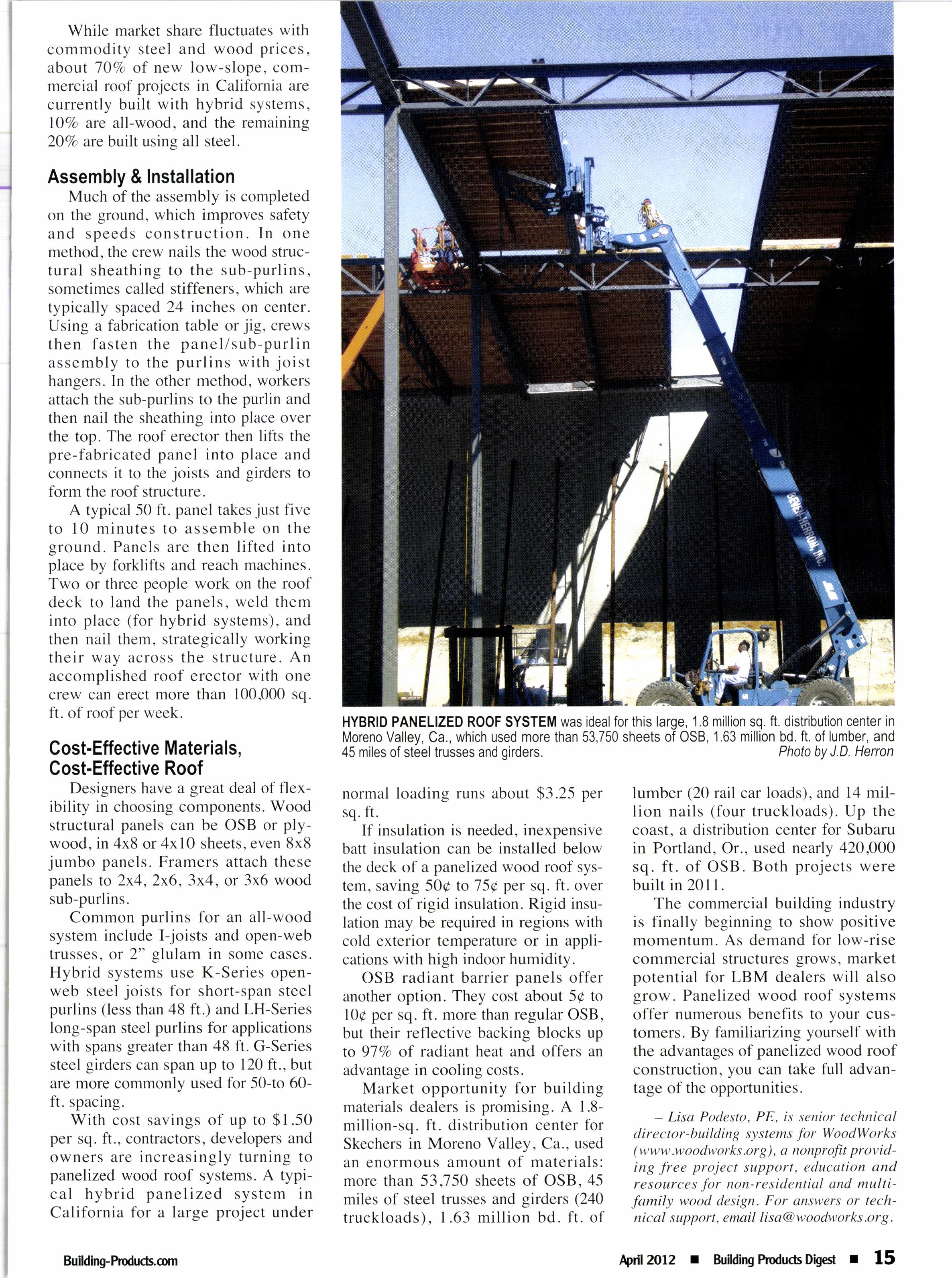
Assembly & Installation
Much of the assembly is completed on the ground, which improves safety and speeds construction. In one method, the crew nails the wood structural sheathing to the sub-purlins, sometimes called stiffeners, which are typically spaced 24 inches on center. Using a fabrication table or jig, crews then fasten the panel/sub-purlin assembly to the purlins with joist hangers. In the other method, workers attach the sub-purlins to the purlin and then nail the sheathing into place over the top. The roof erector then lifts the pre-fabricated panel into place and connects it to the joists and girders to form the roof structure.
A typical 50 ft. panel takes just five to 10 minutes to assemble on the ground. Panels are then lifted into place by forklifts and reach machines. Two or three people work on the roof deck to land the panels, weld them into place (for hybrid systems), and then nail them, strategically working their way across the structure. An accomplished roof erector with one crew can erect more than 100O00 sq. ft. of roof per week.
CoshEffective Materials, Cost-Effective Roof
Designers have a great deal of flexibility in choosing components. Wood structural panels can be OSB or plywood, in 4x8 or 4xl0 sheets, even 8x8 jumbo panels. Framers attach these panels to 2x4,2x6,3x4, or 3x6 wood sub-purlins.
Common purlins for an all-wood system include I-joists and open-web trusses. or 2" glulam in some cases. Hybrid systems use K-Series openweb steel joists for short-span steel purlins (less than 48 ft.) and LH-Series long-span steel purlins for applications with spans greater than 48 ft. G-Series steel girders can span up to 120 ft., but are more commonly used for 50-to 60ft. spacing.
With cost savings of up to $1.50 per sq. ft., contractors, developers and owners are increasingly turning to panelized wood roof systems. A typical hybrid panelized system in California for a large project under normal loading runs about $3.25 per sq. ft.
If insulation is needed, inexpensive batt insulation can be installed below the deck of a panelized wood roof system, saving 50@ to 75Q per sq. ft. over the cost of rigid insulation. Rigid insulation may be required in regions with cold exterior temperature or in applications with high indoor humidity.
OSB radiant barrier panels offer another option. They cost about 50 to lOp per sq. ft. more than regular OSB, but their reflective backing blocks up to 9l7o of radiant heat and offers an advantage in cooling costs.
Market opportunity for building materials dealers is promising. A 1.8million-sq. ft. distribution center for Skechers in Moreno Valley, Ca., used an enormous amount of materials: more than 53,750 sheets of OSB, 45 miles of steel trusses and girders (240 truckloads), 1.63 million bd. ft. of lumber (20 rail car loads), and 14 million nails (four truckloads). Up the coast, a distribution center for Subaru in Portland, Or., used nearly 420000 sq. ft. of OSB. Both projects were built in 201l
The commercial building industry is finally beginning to show positive momentum. As demand for low-rise commercial structures grows, market potential for LBM dealers will also grow. Panelized wood roof systems offer numerous benefits to your customers. By familiarizing yourself with the advantages of panelized wood roof construction, you can take full advantage of the opportunities.
- Lisa Podesto, PE, is senior technical director-building systems for WoodWorks (www.woodworks.or g), a nonprofit providing free project support, education and resources for non-residential and multifamily wood design. For answers or technical support, email lisa@ woodworks.org.