
5 minute read
rk trends: oulding rY awash ports
"If you're going to compete in fingerjointed moulding, you've got to import," says Bill Nathews, sales manager, MilfSource. Montevallo, Al. "Well over 9O7o of what we use now is imported."
Nathews points to the price advantages of imported species, as well as their maturing radiata pine plantations. It also helps that a few years ago, as MillSource was increasing its reliance on imports, the company was acquired by Woodgrain Millwork, Fruitland, Id.-which operates two mills in South America.
Butzelaar wonders, "Given the decline industrial pine supplies and surging imports, der that even diehard ponderosa pine users leader Sierra Pacific have made the move to ed radiata pine?"
Early this year, Sierra Pacific Industries, began buying surfaced lumber from New in domestic is it any wonlike industryusing importRedding, Ca., Zealand and rFHE ECONOMIC slowdown in the U.S. and the draI. matic influx of imported lumber and finished millwork items has braced the moulding and millwork industry for a potentially difficult year.
"With moulding consumption expected to level off in 2001 and 2OO2," explains Peter Butzelaar, associate editor of Wood Markets newsletter, "the battle fbr market share between import and domestic production will no doubt intensify."
Since 1990, domestic "shop & better grade" or cleartype lumber consumption dropped from 2.8 billion bd. ti. (6.6 million cu. meters) to 0.9 billion bd. ft. (2.l million cu. meters) in 2000. Output of shop & better ponderosa pine lumber, the main industrial grade species, plummeted by over 707o from 1.7 billion bd. ft. (4.0 million cu. ft.) in 1990 to approximately 0.5 billion bd. ft. (1.2 million cu. meters) in 2000. In contrast, imported shop & better grade lumber from pine-producing countries (excluding Canada) rose sevenfold to 561 million bd. ft. (1.3 million cu. meters) in 2000.
Chile to produce fingerjoint and solid moulding.
For a large timberland owner like Sierra Pacific, availability wasn't the issue. "There's plenty of lumber, but the gaps in price between domestic and imported pine got to be too wide," says sales manager Dan Wolter. He notes that customers, including window manufacturers, have been receptive, and radiata pine should continue to be about l5Vo of Sierra Pacific's moulding business.
"Today," says Butzelaar, "more than two-thirds of all mouldines consumed in the U.S. are from imported species, either as mouldings produced from imported lumber or as imported finished products."
Setzer Forest Products, Sacramento, Ca., imports lumber to produce mouldings, but not finished products. Mark Setzer notes that imported finished products have been extremely "strong in the Midwest to East, which has forced us to concentrate west of the Mississippi."
Imports, says Ron Middleton, sales manager, Southwest Moulding Co., Dallas, Tx., "have become much. much stronger in recent years. There's still a smattering of domestic production, but it's not anything like it was even five years ago."
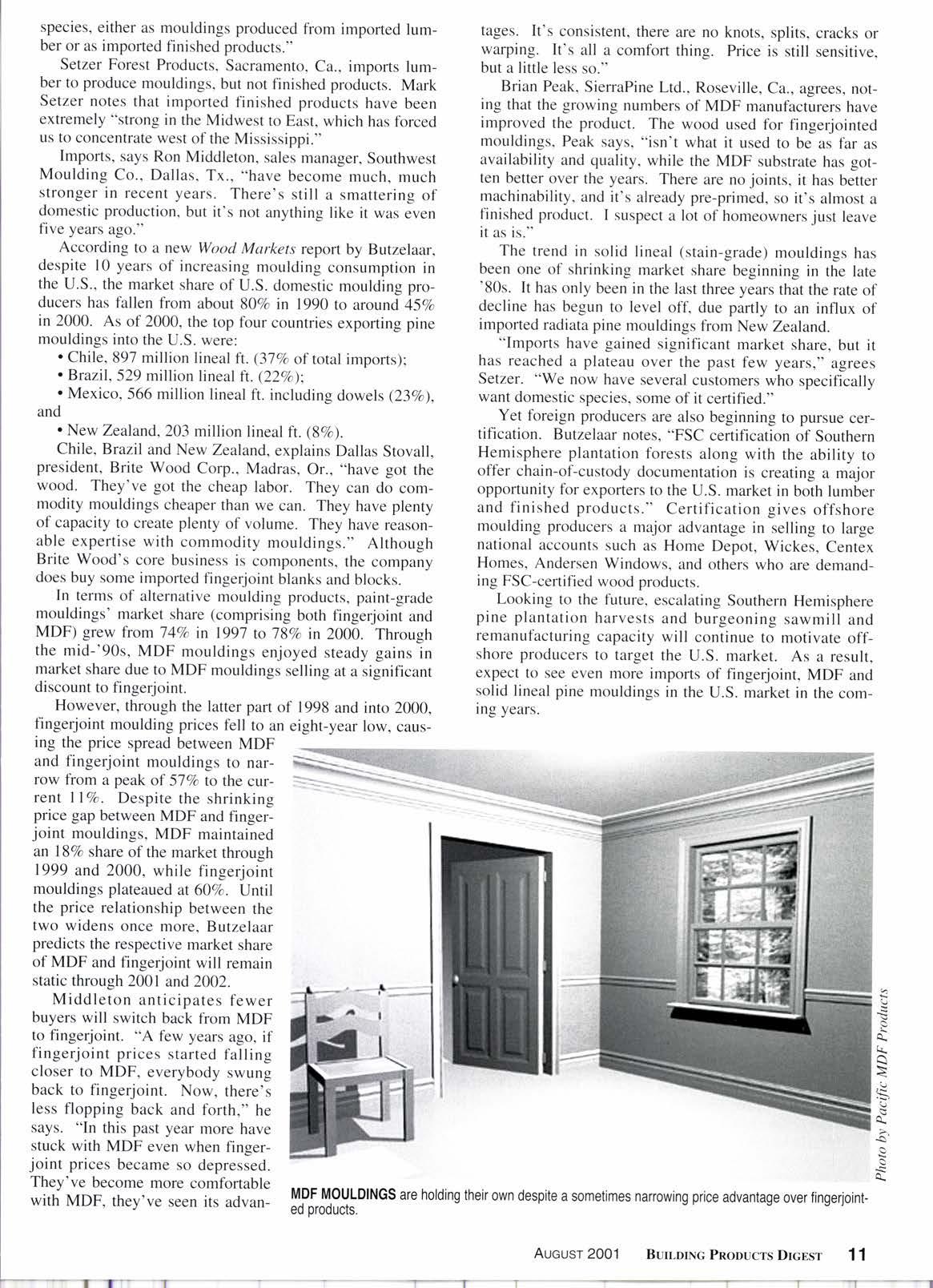
According to a new Wood Markels report by Butzelaar, despite l0 years of increasing moulding consumption in the U.S., the market share of U.S. domestic moulding producers has fallen from about 80Vo in 1990 to around 45Vo in 2000. As of 2000, the top four countries exporting pine mouldings into the U.S. were:
Chile, 897 million lineal ft. (37Vo of total imporrs);
Brazrl,529 million lineal ft. (22Va):
Mexico, 566 million lineal ft. including dowels (23Vo), and
New Zealand,203 million lineal ft. BVd.
Chile, Brazil and New Zealand, explains Dallas Stovall, president, Brite Wood Corp., Madras, Or., "have got the wood. They've got the cheap labor. They can do commodity mouldings cheaper than we can. They have plenty of capacity to create plenty of volume. They have reasonable expertise with commodity mouldings." Although Brite Wood's core business is components, the company does buy some imported fingerjoint blanks and blocks.
In terms of alternative moulding products, paint-grade mouldings' market share (comprising both fingerjoint and MDF) grew from 74Vo in 1997 to 78Vo in 2000. Through the mid-'90s, MDF mouldings enjoyed sready gains in market share due to MDF mouldings selling at a significant discount to fingerjoint.
However, through the latter part of l998 and into 2000, fingerjoint moulding prices fell to an eight-year low, causing the price spread between MDF and fingerjoint mouldings to narrow from a peak of 57Vo to the current llVo. Despite the shrinking price gap between MDF and finger- joint mouldings, MDF maintained an lSVo share of the market through 1999 and 2000, while fingerjoint mouldings plateaued at607o. Until the price relationship between the two widens once more, Butzelaar predicts the respective market share of MDF and fingerjoint will remain static through 2001 and20O2.
Middleton anticipates fewer buyers will switch back from MDF to fingerjoint. "A few years ago, if fingerjoint prices started falling closer to MDF, everybody swung back to fingerjoint. Now, there's less flopping back and forth," he says. "In this past year more have stuck with MDF even when fingerjoint prices became so depressed. They've become more comfortable with MDF, they've seen its advan- tages. It's consistent, there are no knots, splits, cracks or warping. It's all a comfort thing. Price is still sensitive, but a little less so."
Brian Peak, SierraPine Ltd., Roseville, Ca., agrees, noting that the growing numbers of MDF manufacturers have improved the product. The wood used for fingerjointed mouldings, Peak says, "isn't what it used to be as far as availability and quality, while the MDF substrare has gotten better over the years. There are no joints, it has better machinability, and it's already pre-primed, so it's almost a finished product. I suspect a lot of homeowners just leave it as is."
The trend in solid lineal (stain-grade) mouldings has been one of shrinking market share beginning in the late '80s. It has only been in the last three years that the rate of decline has begun to level off, due partly to an influx of imported radiata pine mouldings from New Zealand.
"Imports have gained significant market share, but it has reached a plateau over the past few years," agrees Setzer. "We now have several customers who specificallv want domestic species, some of it certified."
Yet foreign producers are also beginning to pursue certification. Butzelaar notes, "FSC certification of Southern Hemisphere plantation forests along with the ability to offer chain-of-custody documentation is creating a major opportunity for exporters to the U.S. market in both lumber and finished products." Certification gives offshore moulding producers a major advantage in selling to large national accounts such as Home Depot, Wickes, Centex Homes, Andersen Windows, and others who are demanding FSC-certified wood products.
Looking to the future, escalating Southern Hemisphere pine plantation harvests and burgeoning sawmill and remanufacturing capacity will continue to motivate offshore producers to target the U.S. market. As a result, expect to see even more imports of fingerjoint, MDF and solid lineal pine mouldings in the U.S. market in the comlns vears.
U.S. Department of Energy's Office of Building Technology, State and Community Program is partnering with the window industry to develop more energy efficient technologies. They have identified 65 different opportunities for innovation, including:
Advanced holograms - produce holographic images on windows
Aerogels - Incorporate nonopaque, highly insulating aerogel into insulating glass units
Alternative glazing methodsDevelop more durable and efficient glazing materials
Billet stock from recycleDevelop process for making billet out of recycled aluminum
Blast-resistant windowsDevelop new, cost effective, architecturally acceptable blastresistant window materials
Daylight rating - Provide a rating to measure the amount of daylighting provided by a window
Fire-rated windows - DeveloP lower-cost alternative materials for fire-rated windows
Glass/frame ratio - Increase vision area without a corresponding increase in framing
High-security windowsDevelop stronger, cost- effective, architecturally compatible materials for high security
Insulating coatings - Develop new colored architectural coatings that reduce conductive heat loss through window frames and sashes
Insulating componentsDevelop new alloys or composites that reduce conductive heat loss through window components
Integral smarts systemsDevelop self-contained power supplies, sensors, controllers and actuators to actively control heat and light transmission
Integral wind power recovery - Integrate components into windows to capture wind energy
Integral wiring - Incorporate wiring or wiring runs into the window
Interior lighting sourceTransmit light from spandrel through ceiling space
Interior passive lightingDevelop light shelves for curtain wall and window wall applications
(Continued in box at far right)