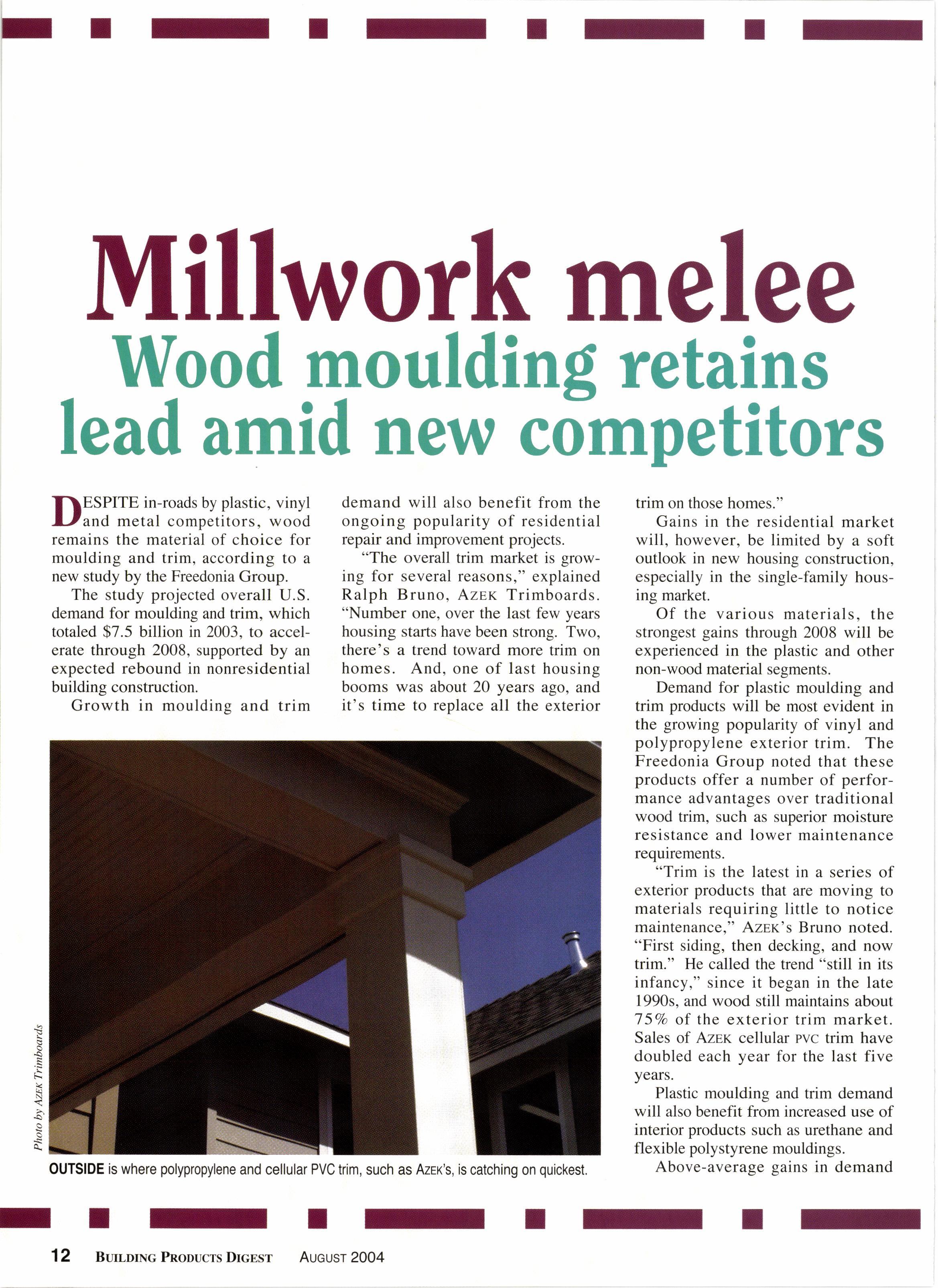
3 minute read
Millwork melee Wood moulding retains lead amid new competitors
IESPITE in-roads by plastic, vinyl Lf and metal competitors, wood remains the material of choice for moulding and trim, according to a new study by the Freedonia Group.
The study projected overall U.S. demand for moulding and trim, which totaled $7.5 billion in 2003. to accelerate through 2008, supported by an expected rebound in nonresidential building construction.
Growth in mouldins and trim demand will also benefit from the ongoing popularity of residential repair and improvement projects.
"The overall trim market is growing for several reasons," explained Ralph Bruno, Azex Trimboards. "Number one, over the last few years housing starts have been strong. Two, there's a trend toward more trim on homes. And, one of last housing booms was about 20 years ago, and it's time to replace all the exterior trim on those homes."
Gains in the residential market will, however, be limited by a soft outlook in new housing construction, especially in the single-family housing market.
Of the various materials, the strongest gains through 2008 will be experienced in the plastic and other non-wood material segments.
Demand for plastic moulding and trim products will be most evident in the growing popularity of vinyl and polypropylene exterior trim. The Freedonia Group noted that these products offer a number of performance advantages over traditional wood trim, such as superior moisture resistance and lower maintenance requirements.
"Trim is the latest in a series of exterior products that are moving to materials requiring little to notice maintenance," Azsn's Bruno noted. "First siding, then decking, and now trim." He called the trend "still in its infancy," since it began in the late 1990s, and wood still maintains about 757o of the exterior trim market. Sales of Azex cellular pvc trim have doubled each year for the last five years.
Plastic moulding and trim demand will also benefit from increased use of interior products such as urethane and fl exible polystyrene mouldings.
Above-average gains in demand for moulding and trim made from other materials will be driven by a strong outlook for metal stairwork, as well as by growth in niche product segments such as mouldings made from engineered woods and woodplastic composites.
The substitute materials each seem to offer different advantages and disadvantages compared to wood. MBoss Inc., for example, produces pressed metal trim for interior and exterior applications. "Since our products are metal-either aluminum or solid copper-they are lighter in weight versus wood mouldings, generally cost less, and can be handtweaked during installation to accommodate imperfect and non-square surfaces," said Tracy Grygorcewicz.
Gossen Corp., for another, offers interior and exterior mouldings and trim made of vinyl for increased durability, flexibility, affordability and water resistance. Ultra-Flex uses syntactic polyurethane to increase strength and add flexibility.
Despite the growth of such substitutes, wood is forecast to remain the dominant material used for moulding and trim in the U.S. Freedonia attributes the widespread use of wood in molding and trim products to a variety of factors, including the familiarity of both builders and consumers with wood materials, and the well-established ties between woodworkers and the building industry.
In addition, wood materials are characterized by a number of performance characteristics that make them popular for molding and trim, including favorable aesthetics and easy workability.
"'Wood mouldings are always the best choice, because details and profiles can be cut into wood more delicately than any other product," said Craig A. Flynn, Windsor Mill, Windsor, Ca. "Wood mouldings allow for clean, crisp details-and allow for thick and wide patterns that help bring the right proportion and a natural scale to your room. Of
'oWhen to it, money being no issue, people would rather have real wood millwork in place rather than any substitute." course, alternative materials-composites like MDF-offer a price advantage in some instances, though any savings often means a sacrifice in quality. MDF, like any hardboard material, has a tendency to mushroom around nail heads, and in some cases reacts to and swells in contact with oil-based paint products."
Pioneer Millworks, Farmington, N.Y., specializes in wood because the material is sustainable and renewable. "People want to see wood in place for purely aesthetic reasons as well as from an environmental standpoint," stressed Ian Harrison. "With recycled millwork, we're keeping wood out of

Buyers continue to demand wood because, according to Jim Snodgrass, Contact Lumber Co., Clackamas, Or., "it's the real thing. It's the beauty and variety you get from that richness. There are a lot more species and looks available. With polystyrene, every piece is the same."
Snodgrass admitted solid wood does have some perceived weaknesses, such as limited availability, natural defects, random lengths, and the tendency to warp and crack. To compensate, Contact also veneer wraps virtually any softwood, metal or plastic substrate. "You get the best of everything-long lengths, no defects, many specieso" he said.
Most importantly, stressed Tom Williams, Jr., Yuba River Moulding & Millwork, Marysville, Ca., "Wood is real. When it comes down to it, money being no issue, people would rather have real wood millwork in place rather than any substitute. The character. charm. texture of real wood, it lasts, and it is a renewable, environmentally friendly product. Hands down, money being no object, people want real wood."