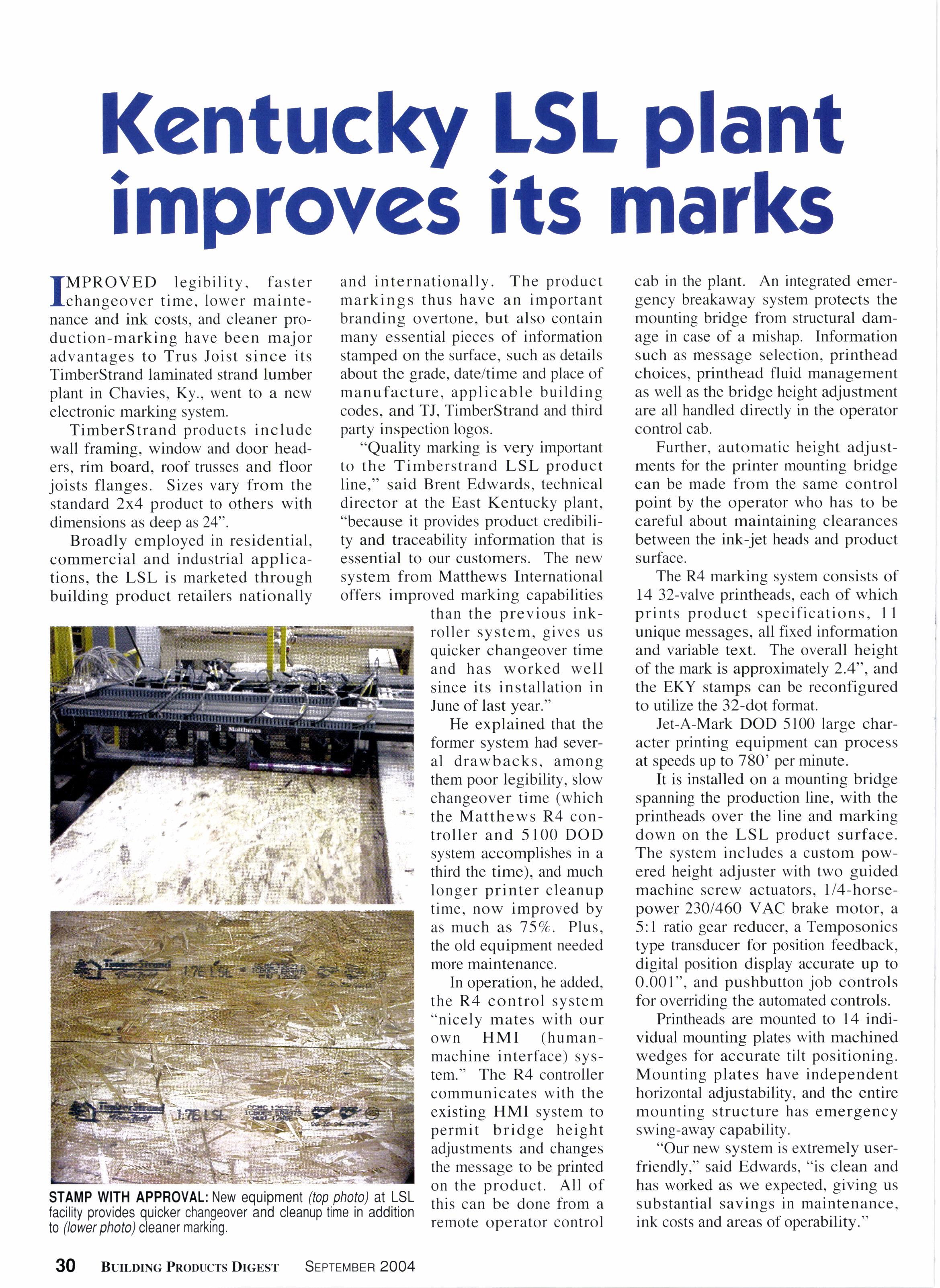
2 minute read
Kentuclry tSL plant a improves its marks
f MPROVED legibility. faster Ichanseover time. lower maintenun"" uid ink costs, and cleaner production-marking have been major advantages to Trus Joist since its TimberStrand laminated strand lumber plant in Chavies, Ky., went to a new electronic marking system.
TimberStrand products include wall framing, window and door headers. rim board. roof trusses and floor joists flanges. Sizes vary from the standard 2x4 product to others with dimensions as deep as 24".
Broadly employed in residential, commercial and industrial applications, the LSL is marketed through building product retailers nationally and internationally. The product markings thus have an important branding overtone, but also contain many essential pieces of information stamped on the surface, such as details about the grade, date/time and place of manufacture, applicable building codes. and TJ. TimberStrand and third party inspection logos.
"Quality marking is very important to the Timberstrand LSL product line," said Brent Edwards, technical director at the East Kentucky plant, "because it provides product credibility and traceability information that is essential to our customers. The new system from Matthews International offers improved marking capabilities than the previous inkroller system, gives us quicker changeover time and has worked well since its installation in June of last year."
He explained that the former system had several drawbacks, among them poor legibility, slow changeover time (which the Matthews R4 controller and 5100 DOD system accomplishes in a third the time). and much longer printer cleanup time, now improved by as much as 757o. Plus, the old equipment needed more maintenance.
In operation, he added, the R4 control system "nicely mates with our own HMI (humanmachine interface) system." The R4 controller communicates with the existing HMI system to permit bridge height adjustments and changes the message to be printed on the product. All of this can be done from a remote operator control cab in the plant. An integrated emergency breakaway system protects the mounting bridge from structural damage in case of a mishap. Information such as message selection, printhead choices, printhead fluid management as well as the bridge height adjustment are all handled directly in the operator control cab.
Further, automatic height adjustments for the printer mounting bridge can be made from the same control point by the operator who has to be careful about maintaining clearances between the ink-jet heads and product surface.
The R4 marking system consists of 14 32-valve printheads, each of which prints product specifications, I I unique messages, all fixed information and variable text. The overall height of the mark is approximately 2.4", and the EKY stamps can be reconfigured to utilize the 32-dot format.
Jet-A-Mark DOD 5100 large character printing equipment can process at speeds up to 780' per minute.
It is installed on a mounting bridge spanning the production line, with the printheads over the line and marking down on the LSL product surface. The system includes a custom powered height adjuster with two guided machine screw actuators, l/4-horsepower 2301460 VAC brake motor, a 5:1 ratio gear reducer, a Temposonics type transducer for position feedback, digital position display accurate up to 0.001", and pushbutton job controls for oveniding the automated controls.
Printheads are mounted to 14 individual mounting plates with machined wedges for accurate tilt positioning. Mounting plates have independent horizontal adjustability, and the entire mounting structure has emergency swing-away capability.
"Our new system is extremely userfriendly," said Edwards, "is clean and has worked as we expected, giving us substantial savings in maintenance, ink costs and areas of operability."
